Advanced Wire Rope Clamping Techniques Explained
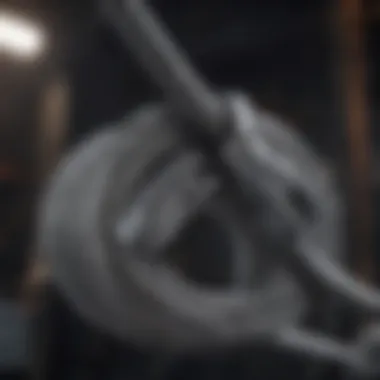
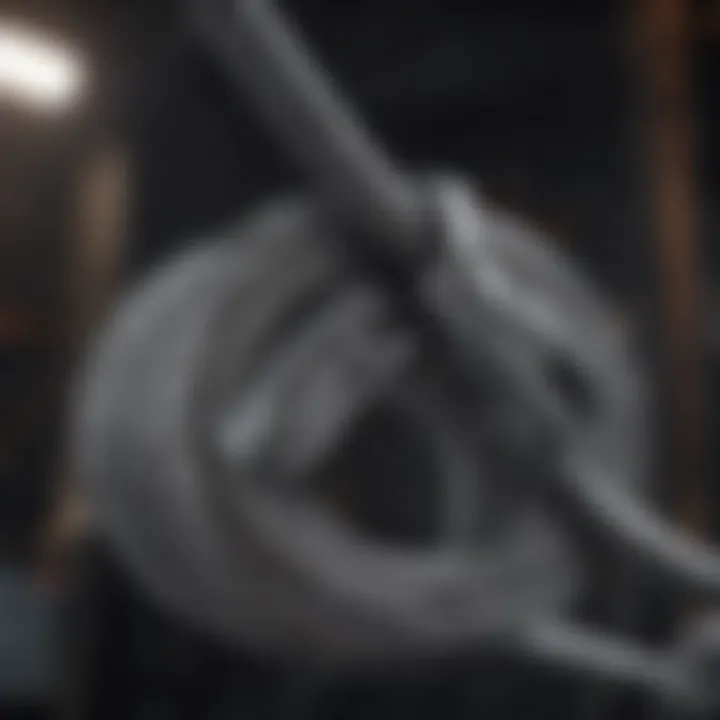
Intro
Wire rope is a complex yet essential component in various fields such as construction, maritime, and mechanical engineering. Its role in transferring loads and forces cannot be overstated. Yet, the efficiency and safety of wire rope usage hinge significantly on the clamping techniques applied. Understanding the nuances of these methods is crucial for anyone involved in the handling or application of wire ropes.
In this exploration, we dig into the approaches that professionals have developed over the years. We will navigate through the basic principles, delve into specific techniques, and examine their respective pros and cons. This discussion also opens the door to future advancements and ongoing research in the realm of wire rope clamping.
The interplay between mechanical principles and practical applications is intricate. Each method of clamping has its own merits and shortcomings, and understanding them in greater depth can lead to enhanced performance and safety. Therefore, it’s essential to unravel the technical aspects tied to wire rope clamping, which pave the way for informed decision-making on the job site.
"Understanding the key concepts behind wire rope clamping can make the difference between an effective solution and potential disaster."
From maintaining equipment to avoiding costly failures, the implications of clamping methods extend to all professionals operating in this space. Thus, by the end of this article, you will have a clearer grasp of how to optimize your wire rope applications through advanced clamping techniques.
Foreword to Wire Rope Clamping
Wire rope clamping is a crucial aspect of various industries ranging from construction to maritime operations. The reliability and integrity of wire rope applications rely heavily on effective clamping techniques. When we consider the multitude of forces that can be exerted on a wire rope, understanding the nuances of clamping is not just beneficial; it’s essential.
In this analysis, we will explore the fundamental principles behind wire rope clamping, as well as the intricate mechanisms and equipment involved. The importance of mastering these techniques cannot be overstated, as improper clamping can lead to catastrophic failures, resulting in significant safety hazards, costly downtime, and potential legal ramifications.
Definition and Importance
Wire rope clamping refers to the methodology of securing wire ropes to ensure that they hold the necessary tension and load without slipping or breaking. The definition is deceptively simple, yet embodies a complex interplay of mechanics, materials, and engineering principles. The effectiveness of a wire rope clamp can greatly influence the overall performance and safety of the system.
The implications of effective wire rope clamping are manifold. On one hand, it preserves the functionality and longevity of the equipment involved. On the other hand, it serves as a pivotal point of safety in operating environments where load-bearing elements must be absolutely secure.
Moreover, embracing advanced wire rope clamping techniques can aid in innovation within industries. It encourages engineers to rethink traditional designs and explore new materials and clamping methods, ultimately leading to performance enhancements.
Historical Context of Clamping Methods
To truly appreciate the significance of modern wire rope clamping techniques, one must look at their historical development. The use of wire rope traces back to the early 19th century. The introduction of clamping methods came as engineers began to recognize the limitations of knots and simple splicing methods. These early clamping techniques were rudimentary and often relied on basic mechanical principles, leading to a variety of challenges, especially under varying load conditions.
Over the decades, as technology advanced, so too did the methods of clamping. Steel clamps emerged as a popular choice, followed by the invention of more specialized clamps designed for specific applications. The enhancement of materials used in clamping grew alongside advancements in metallurgy, which enabled engineers to rely less on brute strength and more on clever design and load distribution.
Understanding these historical contexts helps frame the evolution of wire rope clamping methods. Each innovation built on the failures and successes of its predecessors, paving the way for the sophisticated techniques we analyze today.
Fundamentals of Wire Rope Mechanics
Understanding the fundamentals of wire rope mechanics is crucial. It sets the stage for the effective application of wire rope clamping techniques. This segment explores the intrinsic aspects associated with wire rope materials and the interaction of forces within the system, laying a foundation for practitioners and students alike.
Properties of Wire Rope Materials
Wire ropes are composed of numerous steel wires twisted together, thus creating a strong yet flexible structure. This construction is essential, as it dictates how the wire will behave under load. The material properties are pivotal in determining performance characteristics. Key factors include:
- Tensile Strength: This indicates the maximum stress a material can withstand while being stretched or pulled before failing. High tensile strength allows for greater load capacities.
- Elasticity: This is the ability of the rope to return to its original shape after stress is removed. An elastic material can absorb shocks and vibrations, preventing immediate fatigue.
- Corrosion Resistance: Over time, exposure to environmental factors can weaken wire ropes. Utilizing materials with higher corrosion resistance extends the life of the rope and ensures safety in various conditions.
A clear understanding of these properties is a must for selecting the appropriate wire rope for specific tasks. Inappropriate choices can lead to untimely failures, which not only pose significant safety risks but are also costly in terms of downtime and repairs.
Load Distribution and Tensioning
Load distribution and tensioning are among the most critical elements to consider when working with wire ropes. Proper tensioning maximizes efficiency and safety.
- Load Distribution: This refers to how forces are spread across the wire rope. Uneven distribution can lead to localized stress, increasing wear in specific areas. Ensuring even load distribution is vital for minimizing wear and prolonging the rope's lifespan.
- Tensioning: Correct tensioning balances the load without overstressing the rope. Too much tension can cause premature failure, while too little can result in slippage or disengagement.
It's also essential to be aware of external factors that can influence loading conditions, such as:
- Dynamic Loads: These arise from moving systems or fluctuating weights. Understanding the dynamic characteristics of loads will aid in effective clamping strategies.
- Environmental Conditions: Weather factors like wind or precipitation may exacerbate load effects, thereby requiring a review of the installation parameters and chosen techniques.
A well-designed wire system must accommodate variations in load conditions to ensure ongoing functionality and safety.
By comprehensively addressing the properties of wire rope materials and the intricacies of load distribution and tensioning, professionals can effectively choose and implement wire rope clamping techniques that meet both operational and safety standards.
Types of Wire Rope Clamping Methods
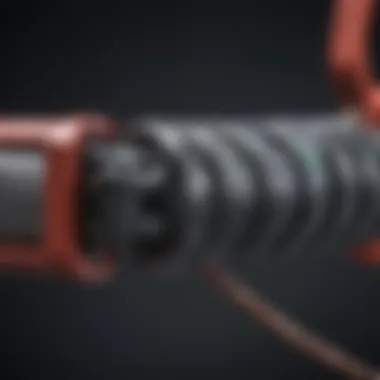
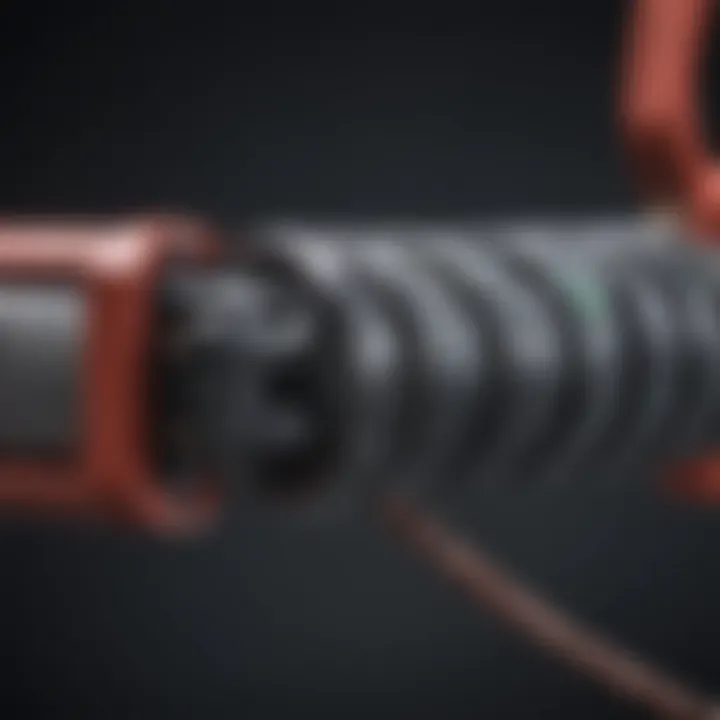
Understanding the various types of wire rope clamping methods is essential for ensuring the functionality and safety of applications involving wire ropes. Different methods offer distinct characteristics, advantages, and drawbacks, making their proper selection crucial depending on the intended purpose and environmental factors. The right clamping method can enhance performance, prolong the life of the rope, and meet safety regulations while ensuring that the load is adequately supported.
Mechanical Clamps
Overview and Functionality
Mechanical clamps represent a classic approach in wire rope clamping technology. These devices work by physically enclosing the wire rope and providing restrictive force, which ensures that the load is securely held in place. They typically consist of two or more pieces, including a base plate and a fastening mechanism, which may involve nuts and bolts or other similar hardware. A key characteristic of mechanical clamps is their adaptability; they can be used on various rope diameters and types.
Their design allows for straightforward installation and adjustment, making them a popular choice in construction and industrial settings. Mechanical clamps are lauded for their robustness, often providing an excellent balance between strength and simplicity. One unique feature is the option for various designs—like wedge or screw clamps—that cater to different operational needs. However, they can be heavier and bulkier than other alternatives, potentially posing challenges in weight-sensitive applications.
Common Applications
Mechanical clamps are versatile and find usage across diverse fields. They are commonly employed in construction, marine applications, and overhead lifting systems. Their ability to securely hold wire ropes in structures, like bridges or cranes, is invaluable. A significant characteristic of these applications is their demand for reliability under heavy load conditions.
The mechanical clamp's straightforward design also makes it economical, an advantage for large-scale operations. However, their tendency to require periodic checks and maintenance should not be overlooked. In demanding environments, such as harsh weather or corrosive atmospheres, they might need added protection or material upgrades to ensure longevity.
Friction-Based Clamps
Operating Principles
Friction-based clamps function on the principle of friction to hold the wire rope in place—when pressure is applied, the friction created between the clamp and the wire rope prevents slippage or movement. Unlike mechanical clamps, they do not rely on physical connectors but rather on the grip generated by the clamping force. This unique operation offers flexibility, making them an attractive choice in various settings.
One of the primary reasons for their popularity is that they often require minimal hardware, streamlining installation efforts. Additionally, the ease of adjustment allows for real-time modifications as loads vary. However, their dependency on proper friction levels now becomes crucial, as inadequate pressure can lead to slippage.
Advantages and Disadvantages
The advantages of friction-based clamps lie in their lightweight design and straightforward installation process. They can often accommodate adjustments without requiring the disassembly of surrounding components. This unique feature enhances operational efficiency.
However, these clamps can also exhibit disadvantages, particularly concerning their performance in adverse conditions. For instance, moisture or dirt can significantly impact the friction levels, leading to decreased effectiveness. Moreover, their applicability can be limited to specific weight ranges, as heavier loads can compromise their clamping ability. Thus, understanding the limitations of friction-based clamps is vital for selecting the right method.
Welded Clamps
Methodology and Usage
Welded clamps involve permanently welding the wire rope to the clamp, providing a strong and robust connection. This method is particularly beneficial in applications where the strength and stability of the joint are paramount. The key characteristic of welded clamps is their ability to resist high tension without compromising the clamping integrity.
Their unique feature is the elimination of movable parts, reducing the risk of mechanical failure, which is advantageous in high-stress environments. However, the limitations of welds, such as susceptibility to fatigue over time, should also be kept in mind.
Considerations for Selection
When selecting welded clamps, it's important to assess the anticipated loads and environmental factors. A key consideration is the terminal application; they are ideal for applications that don't require frequent adjustments or reconfigurations.
Welded clamps provide a permanent solution, making them a beneficial choice for long-term setups like in bridges or heavy machinery. However, they can limit flexibility in certain projects, which could require future modifications. Awareness of these factors helps in making informed decisions regarding clamp selection for specific applications.
Factors Influencing Clamping Method Selection
The selection of clamping methods is pivotal in ensuring the safety and performance of wire rope systems. This section highlights critical elements that professionals must deliberate on when choosing the right clamping method. Understanding these factors can significantly reduce failures and enhance operational efficiency in applications ranging from construction to marine engineering. Factors such as load conditions, environmental factors, and safety regulations are essential realms to explore, providing a robust framework for making informed choices.
Load Conditions and Environmental Factors
When considering clamping methods, load conditions play a central role. Load type, magnitude, and direction can impact how a clamped wire rope behaves under pressure. For instance, a wire rope subjected to dynamic loads—such as those encountered in lifting equipment—demands more robust clamping solutions than a static load scenario.
In addition, environmental factors can make a substantial difference in performance. For example:
- Temperature: Extreme heat or cold can affect the material properties of both the wire rope and the clamps. In some cases, materials may become brittle in low temperatures, while others may lose integrity in high temperatures.
- Corrosion: Exposure to saltwater or other corrosive environments will dictate whether to use stainless steel or other protective coatings on clamps.
- Moisture Levels: High humidity or water exposure can also lead to premature wear and tear on both wire rope and clamps.
Addressing these elements helps establish a solid foundation for selecting the appropriate mechanism that will perform well under specific working conditions.
Safety Regulations and Standards
Safety cannot be overstated when discussing wire rope clamping methods. Various regulations and standards exist to ensure safety in practice. Compliance with guidelines from organizations like the Occupational Safety and Health Administration (OSHA) and American Society for Testing and Materials (ASTM) is critical. Evaluating these requirements before selecting a clamping method helps reduce risks associated with wire rope failures.
Key regulations to consider include:
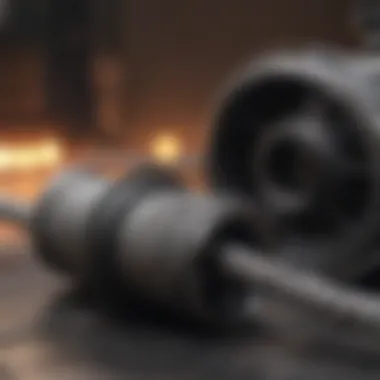
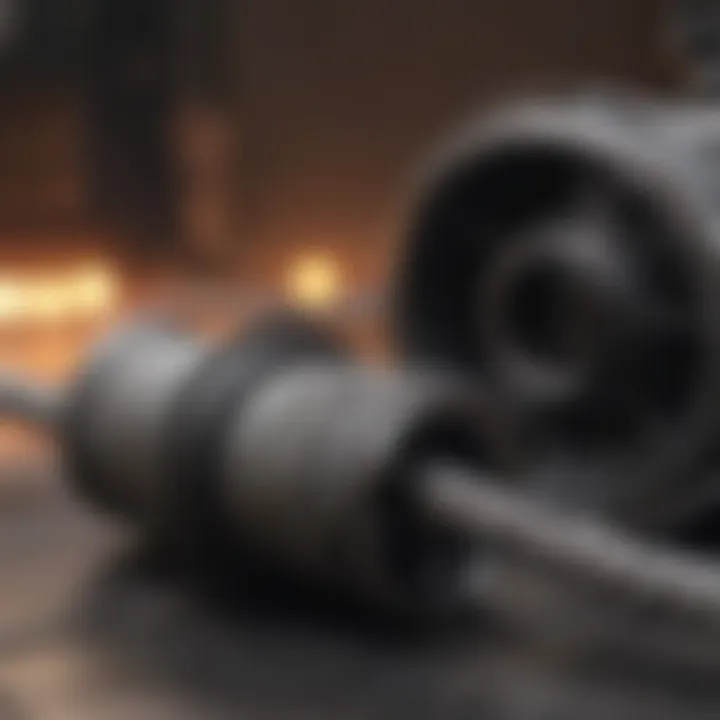
- Load Capacity Standards: Clamps must meet specified load capacities to prevent failures during operation. Better to be safe than sorry!
- Inspection Protocols: Standards set forth inspection intervals and procedures, ensuring ongoing performance and reliability.
- Worker Safety Measures: Inclusivity of safety design principles minimizes injuries in the event of a failure.
Understanding these regulations not only safeguards employees but also protects companies from potential liabilities that come with non-compliance. Thus, it paves the way for selecting a clamping method that is not just effective but also responsible.
"Choosing the right clamping method is not merely a technical decision—it's a responsibility toward safety and operational integrity."
In summary, the selection of wire rope clamping techniques is influenced by a myriad of factors. Professionals in the field must actively assess load conditions, environmental settings, and safety regulations in order to choose adequately. Making informed decisions can optimize performance, ensure safety, and comply with required standards.
Installation Best Practices
In the realm of wire rope clamping, installation best practices are not just a set of guidelines; they form the backbone of safety and efficiency. Proper installation can mean the difference between a secure setup and an impending structural failure, which is a risk nobody wants to take. Implementing best practices helps ensure that clamps function as intended, providing not only the expected performance but also extending the lifespan of the equipment.
Preparation of Wire Rope
Before diving into any clamping procedures, one must attend to the preparation of the wire rope itself. This involves cleaning the wire rope, checking it for any signs of wear, and ensuring it’s the right size for the intended application. A clean wire rope aids in achieving the needed friction, which is particularly crucial for friction-based clamps.
Key Steps in Preparation Include:
- Inspect for Damage: Look closely for frayed strands or broken wires. Damage compromises strength and can lead to failure during tensioning.
- Cleaning: Remove dirt, grease, and other contaminants that might interfere with the secure grip of the clamp. A clean surface ensures effective force transmission.
- Correct Sizing: Ensure that the wire rope diameter matches the clamp specifications. Using the right size prevents slippage and ensures the clamp performs effectively.
Clamping Procedure Recommendations
Step-by-Step Clamping
Following a methodical approach to clamping is crucial for ensuring a durable connection. During the step-by-step clamping process, attention is given to every detail to enhance both safety and performance. This method allows for systematic troubleshooting and adjustments as needed, ensuring nothing is overlooked.
When executing the clamping procedure, it is advisable to:
- Follow Manufacturer Guidelines: Every clamp type has specific instructions regarding torque settings and alignment that must be adhered to.
- Adjust Tension Gradually: Do not rush; gradually increase the tension to allow materials to settle.
- Double-Check Positioning: Ensuring everything aligns perfectly minimizes the likelihood of shifting or slippage.
This step-by-step process is beneficial not just in terms of operational integrity but also empowers technicians to troubleshoot any potential issues that arise during installation.
Quality Control Measures
Quality control measures serve as the safety net in any installation. Without thorough checks, the most intricate clamping systems could falter at an inopportune moment. As such, instituting quality checks during and after installation can't be overstated.
Key Elements:
- Verification of Load Seating: Ensuring that the wire and its clamp are seated correctly can significantly affect the strength of the assembly. This check is something professionals should never skip.
- Periodical Testing: After installation, conducting mechanical load tests can provide additional reassurance, essentially giving the installation a clean bill of health.
- Documentation: Keeping records of installation procedures and checks helps in understanding the system's history, making future assessments easier.
By instituting quality control measures, one can benefit from extended equipment life and potential savings in both repairs and downtime, issues that may arise from overlooking these kinds of precautions.
Proper preparation and systematic installation are not just ideal practices; they are essential for ensuring the longevity and safety of wire rope clamping systems.
Maintenance and Inspection Protocols
In the realm of wire rope clamping, maintenance and inspection protocols represent the unsung heroes that uphold safety and performance standards. The integrity of clamping techniques is paramount, as any oversight can lead to catastrophic failures during operations. Regularly scheduled maintenance routines not only extend the life of the clamping materials but also ensure they can handle the loads they’re subjected to without issue. An organized approach to maintenance is not merely a recommendation—it is a necessity that safeguards operational efficiency and personnel safety.
Routine Maintenance Procedures
Routine maintenance procedures comprise a variety of practices aimed at preventing unexpected failures and enhancing durability. Below is a brief overview of what these procedures might entail:
- Visual Inspections: Frequently examine the clamps for any visible signs of damage, cracks or corrosion. This initial step can often save considerable trouble down the line.
- Cleaning Protocols: Keep clamps and the wire rope free of debris and contaminants, as these can interfere with proper grip and functionality. Using brushes or compressed air for cleaning is often effective.
- Tension Checks: Ensure that the clamping techniques maintain appropriate tension specifications. Over time, wires can expand or contract, affecting the clamping system's effectiveness.
- Lubrication: If the clamps have moving parts, ensure they are properly lubricated to prevent wear, sticking, or jamming.
These procedures, while straightforward, lay a solid foundation for optimal clamping performance. Following through on them regularly can minimize unplanned downtime and improve overall safety in operational environments.
Signs of Wear and Tear
Identifying signs of wear and tear early can be the difference between a minor overhaul and a full-blown disaster. Various indicators point to the need for immediate attention:
- Corrosion and Rust: The presence of rust, especially around the clamp joints, signals exposure to moisture and can drastically weaken the structural integrity.
- Worn Surfaces: Inspecting surfaces for rounding or scoring can reveal excessive wear. This is often a precursor to failure.
- Unusual Sounds: Any grinding or squeaking noises during operation often suggest that components are not functioning smoothly, indicating the need for immediate attention.
- Looseness: If clamps feel loose or shift during load tests, it’s a clear indication that tightening or replacements are in order.
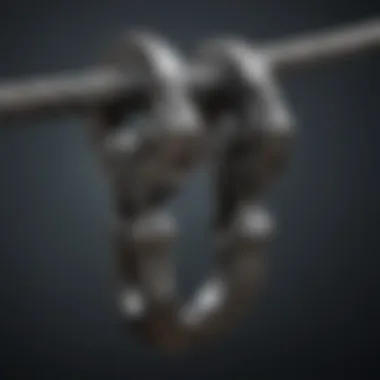
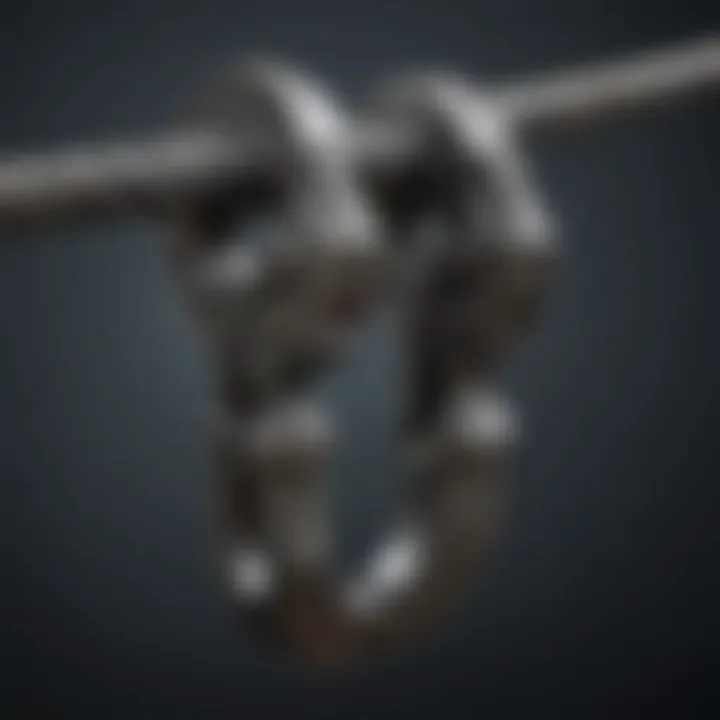
"Proactive maintenance isn’t just a best practice; it’s a critical aspect of preserving the safety and functionality of wire rope systems. Ignorance in this arena can have dire consequences."
Recognizing these signs before they escalate facilitates a proactive maintenance strategy that not only enhances safety but encourages a culture of vigilance in handling wire rope applications. With a deeper understanding of maintenance routines and the ability to spot wear and tear, professionals can better ensure the efficacy of their clamping systems.
Advancements in Wire Rope Clamping Technologies
As industries evolve, so do the techniques utilized in wire rope clamping. Recent advancements in this field have brought forth new technologies and materials that have transformed traditional approaches to clamping methods. This section discusses the significance of these advancements, emphasizing how they enhance performance, safety, and durability while being an essential part of modern applications.
New Materials and Their Benefits
In the ever-changing landscape of wire rope clamping, the introduction of cutting-edge materials stands out. Innovative materials such as high-strength polymer composites and advanced alloys are reshaping the way clamps are designed and function. The benefits of these materials include:
- Lightweight Construction: New materials often weigh less than traditional steel, which means that using them can reduce the overall load and stress on the installation environment.
- Increased Strength: Some synthetic materials can withstand higher loads and are less prone to deformation, ensuring stability under extreme conditions.
- Corrosion Resistance: Many modern materials exhibit superior resistance to corrosion, prolonging the lifespan of clamps in harsh environments.
- Lower Maintenance Needs: With improved durability, the frequency of inspection and maintenance can be reduced, allowing for more efficient operations.
By employing these advanced materials, professionals in the field can elevate safety standards while also optimizing the performance of wire rope applications.
Smart Technologies in Clamping
The integration of smart technologies into wire rope clamping represents a significant leap forward. These innovations not only push the envelope of traditional methods but also open doors to new capabilities. Some of the key aspects of smart technologies include:
- Monitoring Systems: Sensors embedded in clamps can provide real-time data on load, tension, and wear conditions. This allows operators to make informed decisions, enhancing safety and performance.
- Automated Adjustments: Certain smart clamps can automatically adjust tension depending on the applied loads, ensuring optimal performance without manual intervention.
- Predictive Analytics: Advanced data analytics can forecast potential failures before they happen. By analyzing trends, engineers can pinpoint when clamping methods might need adjustments or replacements, thus preventing unexpected downtimes.
"The future of wire rope clamping lies in the marriage of mechanical engineering and smart technology. This will not only boost performance but also ensure peace of mind for operators handling critical loads."
With these advancements, wire rope clamping is not just about holding things together; it's about creating a smart framework that enhances productivity and safety in various applications, from construction to heavy machinery operation.
Common Challenges and Solutions in Wire Rope Clamping
Wire rope clamping, while essential in various fields, is not devoid of its own set of challenges. Understanding these challenges is crucial for professionals who wish to ensure both safety and efficiency in their applications. By identifying common issues and applying suitable solutions, one can avoid costly setbacks and enhance the performance of wire rope systems. With this, engineers, technicians, and operators can be better prepared to tackle potential problems in real-world scenarios.
Identifying Challenges in Field Applications
In field applications, the challenges associated with wire rope clamping can vary significantly based on the environment and usage conditions. Some common challenges faced include:
- Environmental Impact: Factors like extreme temperatures, humidity, and exposure to corrosive materials can adversely affect the integrity of wire ropes. These environmental conditions may lead to premature wear or even catastrophic failure if clamping isn't properly managed.
- Load Variability: The loads placed on wire rope can be unpredictable. Changes in load conditions—such as those resulting from movement, vibrations, or shifts—can affect how clamps maintain their grip.
- Installation Errors: Improper installation is a common pitfall. If the clamps are not installed correctly, it can lead to slippage or an uneven distribution of stress, greatly reducing their effectiveness.
- Frequent Use and Maintenance: In industrial settings, wire ropes undergo heavy use and might not receive adequate maintenance. This neglect can result in unnoticed wear and potential failure.
"Understanding the challenges in the field is the first step toward making informed decisions regarding wire rope clamping. It's not just about the hardware; it's about the environment and conditions of use."
Recognizing these challenges enables professionals to take preventative measures and tailor their clamping techniques accordingly.
Engineering Solutions for Improved Performance
Addressing the challenges in wire rope clamping necessitates a multifaceted approach. Here are some effective solutions that can be adapted based on specific needs:
- Material Selection: Using corrosion-resistant materials for both ropes and clamps can extend their lifespan. For example, stainless steel or specially coated alloys might be ideal in harsh environments.
- Advanced Clamping Techniques: Incorporating innovative clamping designs such as hydraulic clamps can provide better load distribution and a more secure grip, essential for dynamic load conditions.
- Regular Inspections: Instituting a rigorous inspection schedule can help catch signs of wear early. This practice ensures that any defects are addressed before they escalate into serious issues.
- Training and Awareness: Providing comprehensive training for personnel involved in handling and installing wire rope systems is vital. When staff is well-informed about potential challenges and how to avoid them, chances of failure diminish significantly.
- Adaptive Solutions: Flexibility in application is also key. Utilizing clamps that can adjust to changes in load or environmental conditions can improve overall performance and safety.
By implementing these solutions, professionals can not only rectify existing issues but also enhance the durability and effectiveness of wire rope clamping systems. This proactive mindset helps ensure that both safety and performance are prioritized in any application.
The End and Future Perspectives
In synthesizing the rich discussion on wire rope clamping techniques, we can’t overlook the significance of reaching a well-informed conclusion. This section encapsulates not just a summary of insights, but also a forward-looking perspective on where these techniques may lead us in the future. Understanding the core principles of wire rope clamping is crucial for engineers and practitioners. It gives them the groundwork needed to innovate and adapt to upcoming challenges in their fields.
Wire rope clamping is not merely a matter of different techniques but is integrally linked to safety, efficiency, and the materials used. The rigors of field applications and the evolving demands of projects necessitate a critical re-evaluation of existing clamping methods. Thus, it becomes imperative to consider new advancements and best practices that can be integrated into current operations.
Summary of Key Insights
Upon reflecting on the previous sections, several key takeaways emerge:
- Mechanical Versatility: Different clamping methods offer various advantages depending on their specific applications. For instance, mechanical clamps often provide immediate security but may be more prone to slippage compared to friction-based options.
- Material Considerations: The evolution of materials used in wire rope and clamps themselves plays a fundamental role in durability and safety. Lightweight materials with high tensile strength are coming into play, allowing for greater load capacities while reducing overall weight.
- Safety Regulations: The strictness of safety standards in wire rope applications continues to escalate, calling for a more rigorous adherence to protocols and selection processes. Professionals must remain informed about regulatory changes to maintain compliance and ensure safe practices.
- Maintenance Importance: Regular inspections and maintenance of clamps and ropes are non-negotiable. Unattended wear and tear can lead not only to failures but also have catastrophic consequences.
"Continuous improvement is not only about maintaining quality but also about embracing innovations that shrink the gap between current practices and future potential."
Predictions for the Evolution of Clamping Techniques
Looking ahead, we can anticipate several rough trajectories in the evolution of wire rope clamping techniques, each shaped by both technological advancements and shifting industry needs:
- Increased Automation: The push towards automation is profound. Smart clamps, equipped with sensors that monitor load and secure grip, offer a glimpse into a tech-savvy future.
- Integration of AI: Incorporating artificial intelligence into clamping methods for predictive maintenance could revolutionize how we approach wire rope safety. Algorithms may soon analyze wear patterns and suggest timely inspections.
- Sustainable Materials: Environmentally friendly materials are likely to rise in the production of clamps. Innovations in biodegradable or recyclable substances can potentially reduce the environmental footprint of construction projects.
- User-Centric Design: As engineering becomes more inclusive, expect advancements that prioritize user experience. Ergonomically designed clamps that are lightweight yet durable can reduce operator fatigue, thereby enhancing overall safety.
These predictions suggest that the field of wire rope clamping is on the precipice of transformative change. Ongoing research and technological advancements will continue to refine these methods, optimizing performance, safety, and adaptability in various settings.