API 653 Inspection Requirements Explained
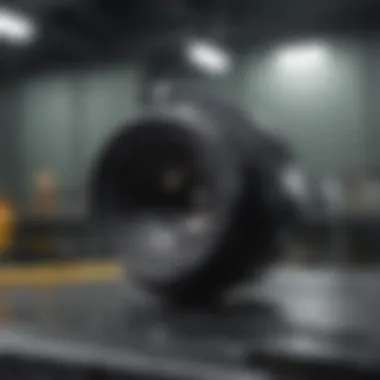
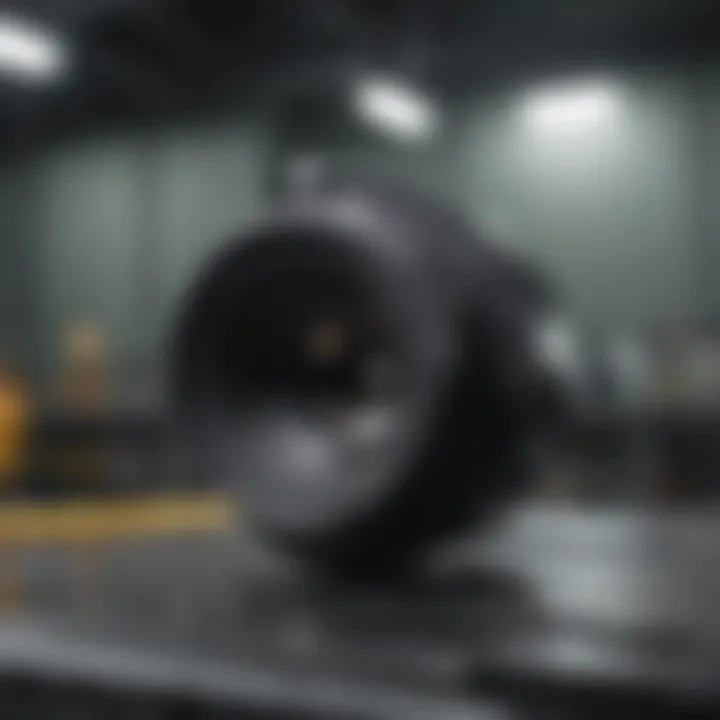
Intro
The inspection of aboveground storage tanks is a vital aspect of safety and environmental regulatory compliance. API 653, which stands for the American Petroleum Institute's standard for the inspection, repair, alteration, and reconstruction of aboveground storage tanks, sets forth critical guidelines for ensuring these structures maintain their integrity over time. Understanding API 653 requirements is essential for professionals in the industry, as non-compliance can lead to serious consequences.
In this article, we will explore the intricacies of API 653 inspection requirements. We will cover various protocols outlined by the American Petroleum Institute, detailing methodologies used in inspections and the significance of adhering to these standards. Furthermore, we will examine the essential roles of certified inspectors, necessary documentation processes, and the implications of failing to meet compliance standards. This comprehensive overview aims to provide valuable insights for students, researchers, educators, and professionals involved in the management of aboveground storage tanks.
Key Concepts
Definition of Primary Terms
Before diving deeper into the API 653 requirements, it is essential to clarify several key terms:
- Aboveground Storage Tanks (ASTs): Large containers used to store liquids, including petroleum products and chemicals, situated above the ground.
- API 653: The specific standard established by the American Petroleum Institute that outlines procedures for the inspection and maintenance of ASTs.
- Certified Inspectors: Professionals who are trained and certified to perform inspections according to API 653 standards. Their role is critical in evaluating the condition and safety of tanks.
Related Concepts and Theories
In addition to API 653, various related concepts enhance the understanding of tank inspection requirements. Key topics include:
- API 650: This standard focuses on design and construction techniques for welded tanks for oil storage and is foundational to API 653.
- Corrosion Control: Understanding the various forms of corrosion and their impacts on storage tanks is central to compliance with API 653, as inspections must address these issues thoroughly.
- Risk Management: The identification, evaluation, and prioritization of risks associated with inground operations influence inspection protocols and maintenance strategies.
Future Directions
Gaps Identified in Current Research
Research related to API 653 exists, yet certain gaps merit further exploration. These include:
- The impact of new materials and technologies on tank durability and inspection methods.
- Long-term effectiveness of current inspection techniques in preventing environmental hazards.
Suggestions for Further Studies
To advance the topic further, the following avenues of study could prove beneficial:
- Comparative studies of international tank inspection standards and their effectiveness mainly in regions with varying climatic conditions.
- Development of advanced monitoring technologies, such as real-time data analytics, to enhance inspection accuracy and compliance monitoring.
Prolusion to API
API 653 plays a vital role in ensuring the safety and reliability of aboveground storage tanks. This set of standards, developed by the American Petroleum Institute, outlines inspection protocols and requirements essential for maintaining the integrity of these storage facilities. Understanding API 653's provisions is not only crucial for compliance but also for operational efficiency. By adhering to these regulations, facilities can significantly reduce the risk of environmental incidents, enhance safety measures, and prolong the lifespan of their equipment.
Purpose of API
The primary purpose of API 653 is to provide criteria for the inspection and assessment of aboveground storage tanks. These standards ensure that tanks remain safe for continued use and comply with environmental regulations. By highlighting essential inspection practices, API 653 encourages proactive maintenance strategies. This leads to fewer failures and more effective management of risk associated with storage tanks. Additionally, these guidelines help facilities in identifying potential issues before they escalate, ultimately saving on costly repairs and safeguarding public health.
Scope of the Standard
The scope of API 653 encompasses various aspects of tank inspection, covering different conditions and situations that may affect the integrity of aboveground storage tanks. It is designed to apply to existing tanks, blending both in-service and out-of-service criteria. Notably, it mandates a systematic approach to monitoring tank conditions, addressing everything from construction and installation to maintenance and repair. This comprehensive scope allows stakeholders to make informed decisions regarding tank management, ensuring compliance with applicable regulations.
In summary, API 653 serves as a foundational standard that guides professionals in conducting thorough inspections. Its purpose focuses on enhancing safety and reliability, while its scope ensures that all relevant factors affecting tank integrity are taken into consideration.
Inspection Requirements Overview
Inspection requirements play a critical role within the API 653 framework. These rigorous guidelines are essential to ensure the safety, reliability, and longevity of aboveground storage tanks. Understanding these requirements allows facility operators and certified inspectors to systematically identify potential issues before they result in substantial risks or financial losses.
The significance of having a structured inspection process cannot be overstated. It promotes proactive maintenance, thereby extending asset life and optimizing operational efficiency. Moreover, adhering to these guidelines enhances regulatory compliance, which reduces the likelihood of legal ramifications due to non-compliance.
Types of Inspections
Inspection methods can broadly be categorized into three types: Visual Inspections, Internal Inspections, and External Inspections. Each type has its own unique considerations and advantages.
Visual Inspections
Visual Inspections serve as the initial step in assessing the condition of a storage tank. This method is straightforward yet effective. Inspectors visually examine the exterior of the tank for signs of corrosion, leaks, or structural damage. The main characteristic of visual inspections is their non-invasive nature, which means they can be performed without disturbing the asset's integrity.
This approach is beneficial for routine check-ups and allows for the quick identification of visible issues. One unique feature is that it often requires minimal equipment, making it a cost-effective choice. However, it has limitations; some internal defects may not be detected simply through visual assessment, thus necessitating further inspection procedures.
Internal Inspections
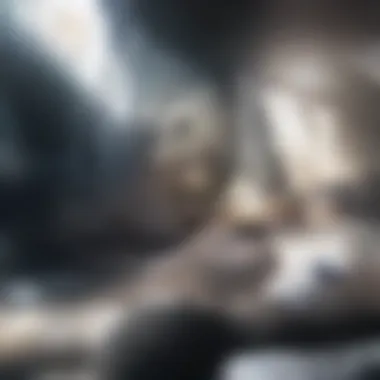
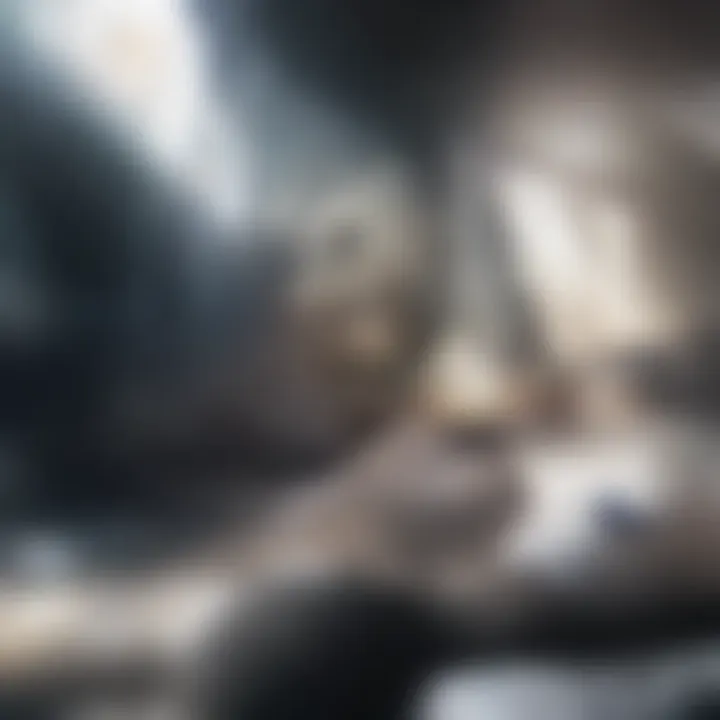
Internal Inspections are crucial in providing a deeper understanding of a tank’s condition. Unlike visual inspections, this method requires entering the tank to evaluate the interior thoroughly. This method allows for the detection of corrosion, sediment buildup, and other internal anomalies that could compromise the tank's integrity.
The key characteristic is that it offers a detailed view of the tank’s condition, which is vital for comprehensive maintenance planning. However, internal inspections require special safety measures and can lead to significant downtime, making them less convenient in terms of operation than other inspection types. Their thoroughness, however, often outweighs these disadvantages, especially for older or high-risk tanks.
External Inspections
External Inspections assess the tank from the outside, typically involving methods like ultrasonic testing and leak detection. This type of inspection is crucial for evaluating external surfaces and structural components. The primary advantage is its ability to identify issues that may not be visible to the naked eye, such as subsurface corrosion.
The unique feature of external inspections is their role in preventative maintenance strategies. They can often identify potential failures before they escalate. However, they may miss critical internal conditions, which is a significant disadvantage. Thus, external inspections should be viewed as part of a broader inspection strategy rather than a standalone solution.
Inspection Frequency
The frequency of inspections is pivotal to maintaining compliance and ensuring safety. Regulations stipulate specific timelines based on the tank's service conditions and past performance records. Businesses must analyze each tank’s risk profile and operational history to determine appropriate intervals for each type of inspection.
Adhering to a schedule for inspections not only aligns with regulatory requirements but also promotes an operational culture focused on safety and reliability. Frequent inspections may lead to early problem detection, thus avoiding costly repairs or environmental hazards. Regular reviews will enhance overall asset management, critical for sustaining operational efficiency.
Pre-Inspection Preparations
Pre-inspection preparations are crucial steps in ensuring the effective and efficient execution of API 653 inspections. These steps encompass the collection and organization of all relevant data and documentation needed to inform the inspection process. By thoroughly preparing ahead of time, organizations can reduce the likelihood of complications during the actual inspection and ensure compliance with the standards set forth by the American Petroleum Institute.
Documentation Required
Previous Inspection Reports
Previous inspection reports serve as essential records that detail the findings of past evaluations. Their contribution to the inspection process is significant as they provide insight into the historical condition of the storage tank. Understanding previous issues can help identify recurring problems that may need immediate attention. A key characteristic of these reports is their ability to reveal trends and changes in the tank's condition over time. This makes previous reports a popular choice for inspectors seeking to establish a baseline for current conditions and identifying areas that may require further scrutiny.
The unique feature of these reports lies in their historical data. They allow certified inspectors to assess whether prior recommendations were implemented and if any deterioration has occurred since the last inspection. The advantage of having previous reports readily available is that it streamlines the inspection process, allowing for a more focused assessment of the storage tank’s current state. However, if these records are incomplete or absent, it can lead to vulnerabilities in the inspection analysis.
Maintenance Records
Maintenance records document the routine upkeep and any repairs that have been performed on the storage tank. This documentation is vital as it contributes to the overall knowledge of the tank's operational history. The key characteristic of maintenance records is their detail in preventive actions taken, which can help predict future maintenance needs. They are beneficial in the API 653 context since they highlight the commitment of the facility operator to uphold safety and functionality standards.
The unique aspect of maintenance records is their function in establishing a timeline for repairs and maintenance interventions. This can help inspectors evaluate the effectiveness of past maintenance activities and prioritize areas that require attention. The advantage of diligent maintenance documentation is that it allows for proactive measures to be taken, potentially reducing risks of failure. A disadvantage, however, arises when maintenance is sporadic or poorly documented, making it challenging to assess the tank's true condition.
Regulatory Compliance Documents
Regulatory compliance documents are necessary to demonstrate adherence to applicable laws and standards during inspections. These documents contribute significantly to the goals of an API 653 inspection by ensuring that all regulatory requirements are met. A key characteristic of these documents is their role in maintaining safety and environmental standards, underscoring why compliance is a fundamental aspect of this inspection framework.
The unique feature of regulatory compliance documents is their requirement for continuous updates in response to evolving regulations. This characteristic leads to advantages like minimizing liability and ensuring a higher level of stakeholder trust. However, the downside can be the complexity involved in keeping such documents current, as this requires systematic oversight and frequent reviews by facility operators.
Site Assessment
Site assessments form the groundwork for any API 653 inspection as they evaluate the physical environment and tank conditions prior to the inspection. They encompass evaluating site safety, accessibility, and the presence of any environmental concerns. The assessment helps inspectors plan the inspection process effectively, ensuring all necessary tools and personnel are prepared for the task at hand.
The thoroughness of a site assessment can directly influence the efficiency of the subsequent inspection. Identifying potential obstacles or hazards, such as structural issues or environmental risks, allows inspectors to adapt their strategies accordingly. This proactive approach is essential, as overlooking site conditions can lead to delays or inaccurate evaluations during the actual inspection process.
Roles and Responsibilities
Understanding the roles and responsibilities involved in API 653 inspections is crucial for maintaining the integrity of aboveground storage tanks. These roles are divided primarily between certified inspectors and facility operators. Their collaboration ensures that storage tanks remain compliant with safety standards and operational guidelines.
Certified Inspectors
Certified inspectors play a vital role in the API 653 inspection process. Their main responsibilities include performing detailed evaluations of aboveground storage tanks. The inspectors must possess the necessary qualifications and certifications that demonstrate their knowledge of API standards and inspection practices. Their expertise is critical as they identify defects or weaknesses within the tank structures—issues that, if left unresolved, might lead to significant safety hazards or environmental concerns.
Key tasks of certified inspectors include:
- Conducting thorough visual inspections to check for surface degradation or other anomalies.
- Performing nondestructive testing methods, such as ultrasonic or radiographic testing, as appropriate.
- Documenting all findings accurately and ensuring that reports reflect the current state of the facility.
Benefits of having certified inspectors include:
- Assurance that inspections are carried out according to the latest standards.
- The ability to provide recommendations for repairs based on their findings, thus enhancing the safety and reliability of storage tanks.
Inspectors also must stay updated on regulatory changes and advancements in inspection technologies. The breadth of their responsibilities means continuous education and awareness of industry best practices are essential.
Facility Operators
Facility operators hold equally vital roles within the API 653 inspection framework. Operators are responsible for the ongoing maintenance and safe operation of aboveground storage tanks. Their familiarity with the facility's operations allows them to provide critical context for inspectors during the inspection process.
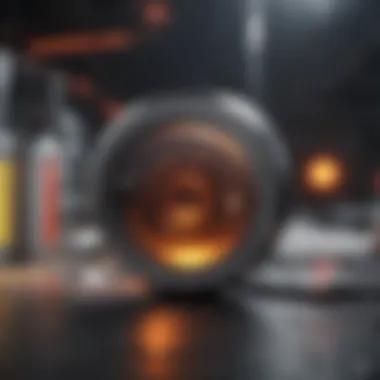
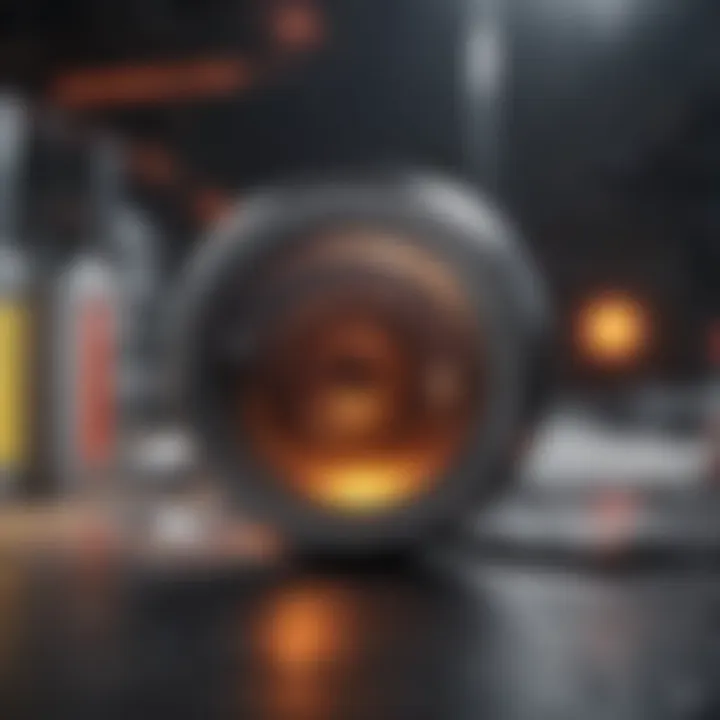
Key aspects of facility operators' responsibilities include:
- Ensuring that all necessary documentation, such as maintenance records and previous inspection reports, are readily available for review.
- Coordinating with certified inspectors to schedule inspections that interrupt operational flow minimally.
- Implementing recommended repairs or maintenance activities in a timely manner.
Considerations for facility operators involve:
- Understanding the inspection schedule to maintain compliance without disrupting workflows.
- Developing a culture of safety and compliance that encourages proper training and adherence to protocols among staff.
By fostering strong communication between inspectors and operators, facilities can effectively address potential issues before they lead to compliance problems. This teamwork is pivotal in creating a robust framework for safety and operational effectiveness.
Effective collaboration between certified inspectors and facility operators is essential to uphold the standards set by API 653, lead to safer operations, and protect prevailing environmental conditions.
Inspection Methods and Techniques
The section on inspection methods and techniques is crucial in understanding the comprehensive approaches used in API 653 inspections. The goal is to ensure the safety and integrity of aboveground storage tanks. Understanding different methods allows inspectors to select the most suitable ones based on the specific requirements of the tanks, the environment, and potential risks. Each inspection method has its distinct attributes and functions, contributing significantly to the overall assessment process.
Nondestructive Testing (NDT)
Nondestructive testing (NDT) plays a vital role in API 653 inspections. It enables professionals to evaluate the condition of storage tanks without causing any damage. This approach is valued for its ability to locate defects such as corrosion, cracks, and other structural concerns without compromising the tank's integrity. The following are key NDT techniques commonly employed:
Ultrasonic Testing
Ultrasonic testing utilizes high-frequency sound waves to detect internal and external flaws in tank materials. Its main characteristic is precision in measuring material thickness and identifying corrosion spots. This technique is highly beneficial due to its ability to provide real-time data without altering the tank's condition.
A unique feature of ultrasonic testing is that it is capable of inspecting complex geometries, making it versatile for various tank designs. Its advantages include high accuracy and the ability to gauge thickness at various depths. However, it requires skilled operatives to interpret the results accurately, which may pose a limitation.
Magnetic Particle Testing
Magnetic particle testing (MPT) is used primarily for ferromagnetic materials. This method involves applying magnetic fields to detect surface and slightly subsurface defects. One of its key characteristics is the simplicity in execution, allowing for quick checks during regular maintenance. MPT is advantageous because it can find very small surface cracks.
The unique aspect of MPT lies in its visual confirmation of flaws through colored particles that accumulate around defects. It is a quick and effective inspection method. However, it does have limitations; it is not suitable for non-magnetic materials and can only identify surface faults.
Radiographic Testing
Radiographic testing employs X-rays or gamma rays to examine the internal structure of materials. This method stands out for its ability to provide a permanent record of flaws detected inside the tank. Its principal advantage is detailed imaging that allows for a comprehensive analysis of the tank’s integrity over time.
The unique feature of radiographic testing is that it can reveal volumetric defects, such as voids or inclusions within the material. While it offers substantial insights, it requires significant safety precautions due to the use of radioactive materials, which could deter its frequent use in certain environments.
Dye Penetrant Testing
Dye penetrant testing is another established sensor technique for identifying surface-level imperfections. It involves applying a detectable dye to the tank surface, which will seep into cracks or voids. One primary characteristic of dye penetrant testing is its applicability to a wide range of materials, including metals and some plastics, and its low cost.
The unique part of this method is its simplicity and the ability to detect very fine surface defects. However, it offers no insights into subsurface issues, and rapid washout of the dye in wet environments can hinder efficacy.
Risk-Based Inspection (RBI)
Risk-based inspection (RBI) is a systematic approach that prioritizes resources and time based on the risk associated with specific assets. It allows for targeted inspections on tanks most likely to present integrity problems. This method combines inspection history, data analysis, and potential failure modes, making it essential in ensuring critical compliance with API 653 requirements.
Ultimately, each inspection method has its strengths and weaknesses. A solid understanding of these techniques supports safer, more efficient practices in maintaining aboveground storage tanks.
Post-Inspection Processes
Post-inspection processes are critical in ensuring that the findings from an API 653 inspection are effectively handled and acted upon. These processes consist of several key elements that help maintain the safety and integrity of aboveground storage tanks. Immediate actions following an inspection can prevent small issues from escalating into serious problems. The main focus here is to ensure compliance while also enhancing the overall safety and service life of storage facilities.
Reporting Procedures
Reporting plays a vital role in the post-inspection phase. Accurate and detailed reporting is necessary for documenting the findings of the inspection. The report should outline all observed conditions, whether they meet regulatory benchmarks, and any potential hazards identified during the inspection. A well-structured report typically includes:
- Executive Summary: Summarizes the inspection results clearly and concisely.
- Inspection Details: Provides specifics, including dates, times, and personnel involved.
- Findings: Lists all observations, categorized by criticality.
- Recommendations: Offers guidance based on the inspection findings.
Maintaining clear records aids in future inspections and can protect against legal issues. Furthermore, stakeholders can reference these reports to understand the tank's condition over time.
Follow-Up Actions
Follow-up actions are equally crucial post-inspection. They ensure that any identified issues receive the appropriate attention. Two major components of follow-up actions include immediate repairs and long-term monitoring.
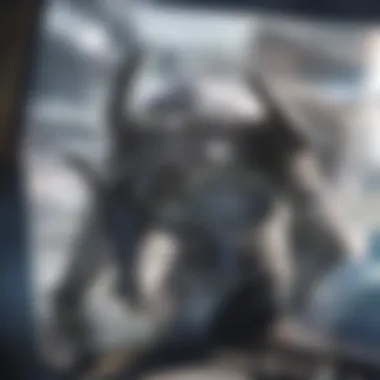
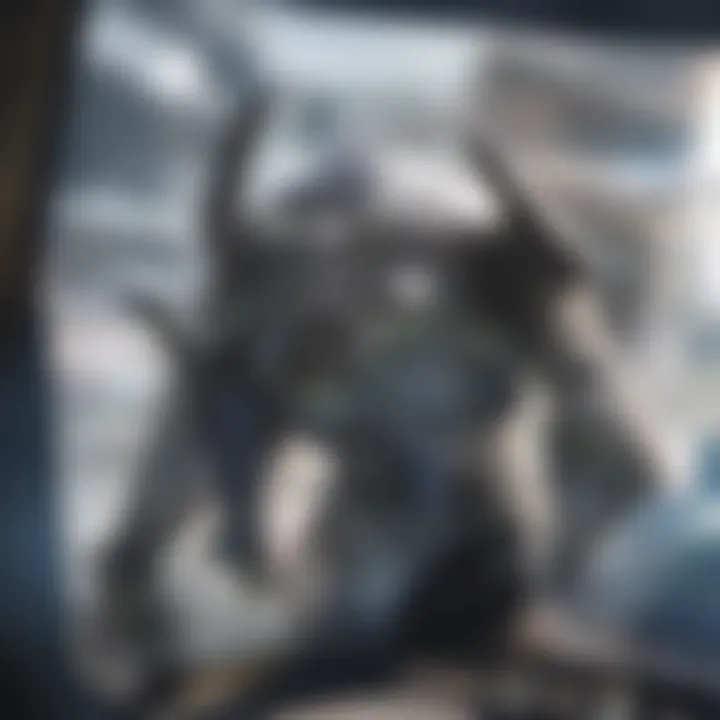
Immediate Repairs
Immediate repairs address critical deficiencies that jeopardize storage tank integrity. Acting on these issues as soon as possible is essential. Quick intervention prevents further deterioration and helps maintain safety standards. One key characteristic of immediate repairs is their priority status—they are essential to enforce compliance and protect the environment.
- Benefits: Immediate repairs can significantly reduce risks. In a high-stakes environment, these actions can prevent catastrophic incidents.
- Unique Feature: They are often reactive to urgent findings, allowing inspectors to address the highest priority issues first.
While immediate repairs are critical, they can involve higher costs and may require unplanned downtime for the facility. Thus, proper planning and budgeting during the inspection phase can mitigate these drawbacks.
Long-Term Monitoring
Long-term monitoring ensures ongoing compliance and health of the storage tanks. It involves setting up a framework to regularly assess tank conditions over time. This proactive strategy can identify issues before they require immediate repairs. A fundamental benefit of long-term monitoring is its ability to provide data that influences maintenance schedules and future inspections.
- Benefits: It ensures sustainability and helps in planning the lifecycle of the tank. Adopting a long-term view helps facilities in effectively allocating resources.
- Unique Feature: This approach is less reactive than immediate repairs and offers insights that can lead to improved operational practices.
Although lengthy processes may require resource allocation, they ultimately foster a more stable environment for operations. By committing to rigorous monitoring, facility managers position themselves to proactively maintain compliance and safety standards.
Regulatory Compliance and Standards
Regulatory compliance is essential in maintaining the integrity of aboveground storage tanks, as outlined by API 653. Compliance with regulations ensures that storage tanks meet safety and environmental standards, reducing the risk of leaks and environmental damage. Non-compliance can lead to significant penalties, including fines and operational shutdowns. Therefore, understanding the relevant standards and agencies involved is crucial for professionals in the field.
Relevant Regulatory Agencies
Several regulatory agencies oversee the implementation of API 653 inspections. Key agencies include:
- Environmental Protection Agency (EPA): The EPA regulates hazardous waste and enforces compliance with environmental laws. Their guidelines are crucial for facilities storing toxic or flammable materials.
- Occupational Safety and Health Administration (OSHA): OSHA ensures safe and healthy working conditions. They set standards that impact operational practices within facilities that use storage tanks.
- State Regulatory Agencies: Each state may have additional regulations pertaining to storage tanks, and professionals must be aware of these local requirements.
Staying informed about these agencies allows storage tank operators to maintain compliance, thereby preventing costly legal issues and environmental harm.
Overview of Related Standards
In addition to API 653, several other standards relate to tank inspection and compliance. These include:
- API 650: Covers the design and construction of aboveground storage tanks, laying the groundwork for safety and integrity.
- API 579: Focuses on fitness-for-service evaluations of pressure vessels and storage tanks, providing methodologies to assess structural integrity.
- NFPA 30: The National Fire Protection Association standard, which addresses flammable and combustible liquids storage.
Understanding these related standards is vital. They collectively contribute to a comprehensive framework that helps ensure safe operations in various environments. Through adherence to these guidelines, facility operators can better manage risks associated with aboveground storage tanks.
Challenges in API Inspections
Conducting inspections as per API 653 standards does not come without its hurdles. Understanding these challenges is essential for professionals engaged in maintaining aboveground storage tanks. Addressing the complexities of API 653 inspections not only helps in ensuring compliance but also significantly enhances the safety and integrity of storage systems. By grasping the common challenges and the evolving regulatory landscape, stakeholders can formulate more effective inspection strategies and make informed decisions, minimizing risks.
Common Inspection Challenges
Inspections under API 653 are subject to numerous challenges that can hinder efficiency and compliance. Here are some key aspects of these common challenges:
- Access limitations: Often, aboveground storage tanks are located in areas that are not easily accessible. This can make it difficult for inspectors to perform thorough evaluations.
- Environmental conditions: Unpredictable weather patterns and adverse environmental conditions can impact inspection activities. Heavy rain or extreme temperatures often results in delays or inadequate inspections which can compromise the quality of assessments.
- Equipment limitations: Not all inspection tools and technologies are equally effective. Some regions may not have access to advanced technologies like ultrasonic testing, which could limit the inspection scope.
- Inconsistent documentation: Proper documentation is vital. However, there might be gaps in previous reports or maintenance records, which can affect the risk assessment during inspections.
These challenges necessitate ongoing training for certified inspectors. They must stay informed about technological advancements and ensure their skill sets are updated to counter these obstacles effectively.
Evolving Regulatory Landscape
The regulatory environment surrounding API 653 inspections is dynamic, presenting continual challenges. Understanding this evolving landscape is crucial for compliance:
- New regulations: Regulatory agencies frequently update standards and guidelines. Inspectors must stay abreast of these changes to ensure compliance during inspections.
- Increased scrutiny: Agencies may implement more rigorous oversight on tank inspections, which can complicate processes for facilities that must demonstrate stringent compliance.
- Technological advances: As inspection technologies develop, the regulatory standards can shift, necessitating facility upgrades in both equipment and processes to align with new expectations.
It is essential for stakeholders to cultivate a proactive approach to regulatory changes. Staying educated about new standards can greatly minimize non-compliance risks and enhance operational safety.
Culmination
The conclusion of this article encapsulates the critical nature of API 653 inspection requirements for professionals in the petroleum industry. These inspections ensure that aboveground storage tanks maintain compliance and safety, safeguarding against potential failures that can result in severe environmental and economic repercussions. Understanding the protocols involved is essential for maintaining the structural integrity of tanks.
Summary of Key Points
- Inspection Types: Visual, internal, and external inspections provide different insights into the condition of storage tanks.
- Documentation: Accurate documentation, including previous reports and regulatory compliance documents, is vital for effective inspections.
- Roles: Certified inspectors and facility operators must collaborate closely to ensure thorough inspections and address issues that arise promptly.
- Methodologies: Utilizing Nondestructive Testing (NDT) techniques enhances the accuracy of inspections while reducing downtime.
- Challenges: Common inspection challenges include changing regulations and the need for consistent training of personnel.
- Regulatory Compliance: Adherence to standards set by regulatory agencies is essential for legal and operational success in tank management.
- Future Directions: Ongoing training and adaptation of new technologies are crucial for improving inspection processes, ensuring sustained compliance and safety.
By emphasizing these critical elements, the conclusion serves not only as a summary but also highlights the importance of a proactive approach in overseeing API 653 inspections. Each detail plays a role in a comprehensive risk management strategy that benefits both the organization and the environment.
Future Directions in API Compliance
Looking toward the future of API 653 compliance, several considerations emerge. The evolution of technology provides opportunities for enhanced inspection methodologies like advanced remote monitoring systems, which can reduce the frequency of manual inspections while ensuring continuous oversight.
Additionally, there is a growing trend towards integrating data analytics into inspection protocols. Such strategies could facilitate predictive maintenance, reducing costs, and improving safety outcomes. Training programs will need an evolution to encompass new technologies and regulatory changes to equip inspectors with necessary skills and knowledge.
Lastly, fostering collaboration among industry stakeholders can bring about innovative solutions that address common challenges in inspections. The collective effort can lead to industry-wide standards that not only comply with API 653 but also push the boundaries of compliance and safety.