Bending Copper Sheets: Techniques and Applications
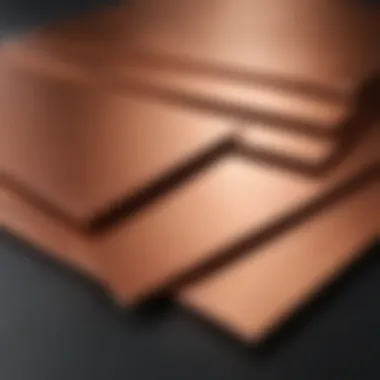
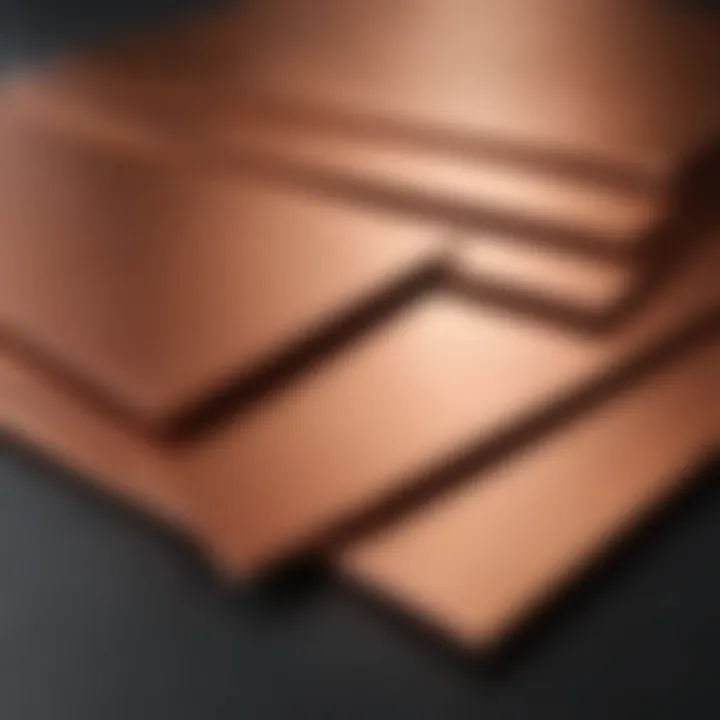
Intro
Bending copper sheets is a skill that melds creativity with practical application. Whether in crafting intricate art pieces or engineering reliable components for machinery, understanding how to shape copper efficiently is essential. This process isn’t merely about yielding to physical forces; it’s a dance between the properties of copper and the techniques we employ to manipulate it.
Copper, a metal with a long history, is prized for its excellent conductivity and malleability. These characteristics make it suitable for a wide array of applications, from electrical wiring to decorative art. This guide aims to equip you with the knowledge on the best practices, tools, and techniques in bending copper sheets, all while addressing potential challenges you may face.
Let’s delve deeper into the key concepts that underlie this craft, marrying theory with practical wisdom.
Key Concepts
Definition of Primary Terms
Before diving into the techniques, it's important to iron out some terminology that commonly surfaces in discussions about bending copper sheets. Here are a few definitions:
- Bending Moment: The force applied to a metal sheet that causes it to bend. It’s critical to calculate this accurately to avoid snapping or over-stressing the copper.
- Sheet Metal Gauge: The thickness of the copper sheet. A lower gauge means a thicker sheet; understanding this influences the choice of tooling and bending techniques.
- Springback: The tendency of copper to return to its original shape after bending. This phenomenon must be taken into account to achieve the desired angle.
Related Concepts and Theories
Several theories can help contextualize the bending of copper sheets. Understanding material science is vital since it reveals how copper responds to stress and strain during the bending process. For example, the concept of plastic deformation signifies when a material can be bent without returning to its original shape.
Another essential theory is mechanical advantage, which guides how tools leverage force to bend metal effectively. Knowing this can save considerable effort and improve accuracy during the bending task.
When bending copper sheets, practical applications can often draw upon principles from both physics and engineering. The applied forces must be calculated carefully, ensuring that the operation aligns with the physical properties of the metal.
"Understanding the science behind the materials is as crucial as the skills of execution. Without this comprehension, every bend risks becoming a break."
As we continue, we will examine the necessary tools to bend copper sheets efficiently and the safety measures to ensure a smooth process.
Understanding Copper as a Material
Copper is often lauded as a cornerstone material in various industries, and for good reason. Its unique attributes not only facilitate its bending but also underscore its value in numerous applications. One could say copper is like the Swiss Army knife of metals; versatile and indispensable. To appreciate why bending copper sheets is such an important topic, it's essential to understand some specific aspects of this metal.
Physical Properties of Copper
Copper has several physical properties that govern how it behaves during bending processes. First off, its malleability stands out; copper can be easily shaped without breaking, which is crucial when considering the bending techniques discussed later. In terms of conductivity, copper ranks among the best, making it an optimal choice for electrical components.
It's also relatively ductile, which allows it to stretch and deform without failure. The thermal expansion of copper is another property to bear in mind, as it can expand when subjected to heat, affecting the bending technique. These characteristics play a pivotal role when understanding the precision required during the bending process, ensuring that the final product meets high standards of performance and reliability.
Applications of Copper in Industry
Copper's multifaceted nature means it's everywhere in industrial applications, from electronics to construction materials. In electrical application, for instance, its excellent conductive property makes it a staple in wiring. Buildings often showcase copper in their roofing or plumbing, not to mention the decorative aspects of copper fixtures.
Additionally, the automotive industry leverages copper for its heat resistance in various components. Here are a few sectors that benefit greatly from copper:
- Electronics: Circuit boards, connectors, and other hardware depend on copper's conductivity and versatility.
- Construction: Copper is used in pipes, roofing, and gutters because it resists corrosion.
- Art and Design: Artists use copper for sculpture and decorative elements due to its aesthetic appeal.
Despite its many applications, specific techniques must be employed for the bending to ensure that the end products fulfill their intended purpose effectively.
Common Copper Alloys
Copper alone holds great strength, but when alloyed with other metals, its properties can be even more fine-tuned. Some common copper alloys include bronze and brass.
- Bronze: A mixture of copper and tin, bronze is known for its durability and resistance to wear, making it perfect for bearings and bushings.
- Brass: Copper combined with zinc creates brass, a metal that exhibits brilliant colors and high resistance to corrosion. It's often used in decorative items and musical instruments.
- Copper-Nickel: Combining copper with nickel can improve strength and corrosion resistance, ideal for marine applications.
These alloys open doors to extended uses of copper in bending processes, providing opportunities to target specific characteristics that enhance performance in those additional applications. Understanding these materials is fundamental for anyone seeking to manipulate copper sheets effectively and accurately.
Techniques for Bending Copper Sheets
The techniques used for bending copper sheets play a pivotal role in ensuring that the end product meets desired specifications and quality standards. This section delves into various methods of bending copper, acknowledging that each technique has its own set of advantages, limitations, and intricacies. Understanding these methods helps craftsmen and engineers select the appropriate approach based on the project requirements, sheet thickness, and desired bend characteristics.
Mechanical Bending
Mechanical bending is a widely accepted method for shaping copper sheets. This technique utilizes a mechanical press or bending machine to exert force onto the copper, thereby changing its shape.
The key benefit of mechanical bending is the consistency it offers. With preset machinery settings, one can achieve precise angles and repeatable results, making it invaluable in a production setting. Additionally, this method is well-suited for thicker sheets and larger production runs, providing strength and durability to the final product. However, mechanical bending requires proper knowledge and skills to set up the machinery correctly, as improper adjustments can lead to unwanted deformation.
Thermal Bending
Thermal bending involves the application of heat to the copper sheet at the bend area. By heating the metal, it becomes more malleable, allowing for smoother shaping. This method is particularly useful when working with thicker or larger pieces that may be difficult to bend mechanically.
Special considerations include:
- Temperature Control: Maintaining the right temperature is crucial; too much heat can cause damage, while too little can make bending ineffective.
- Safety Measures: Using heat sources requires utmost care, ensuring that workers are protected against burns or heat exposure.
This technique can yield unique design possibilities, enabling bends that other methods might struggle to achieve. However, one must consider the cooling process after bending, as rapid cooling can introduce stresses into the material, potentially impacting its structural integrity.
Roll Bending Techniques
Roll bending is particularly useful for creating large, cylindrical shapes from copper sheets. This technique utilizes rollers to gradually form the sheet around a pre-determined radius. It stands out in its ability to work with large sheets and achieve gentle curves that might be challenging with other methods.
This process is ideal for creating components like pipes or tanks, and here are some aspects to keep in mind:
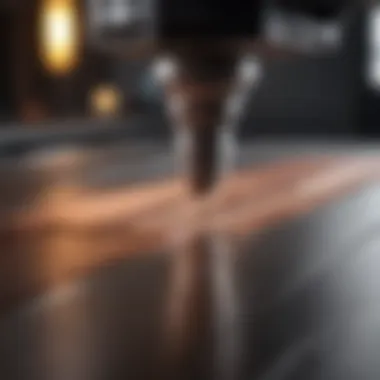
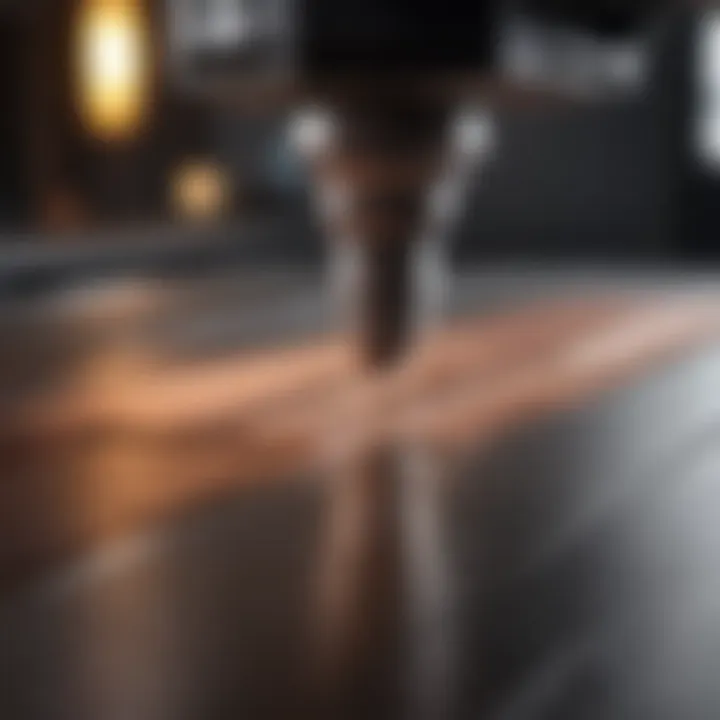
- Roller Setup: Correct alignment of rollers is critical; even slight misalignments can lead to unwanted shapes.
- Material Thickness: The thickness of the copper sheet plays a direct role in how it can be rolled; thicker sheets may require more powerful machinery to achieve desired results.
Overall, roll bending is a versatile method, allowing a variety of configurations that are essential in industries ranging from construction to art.
Manual Bending Methods
Manual bending methods involve hands-on techniques and tools to shape the copper sheets. While often seen as less sophisticated than mechanical methods, manual bending offers unmatched control and the ability to create bespoke designs. This technique is especially favored by artisans and hobbyists who appreciate the tactile experience of working with the material directly.
Some common manual bending tools include:
- Bending Brakes: Allow for precise bends by securing the sheet while applying force with a lever.
- Hammers and Blocks: Useful for more intricate designs, where finesse is key.
- Vise Grips: Help stabilize the material while bending, providing additional support and safety.
Though manual methods may not provide the efficiency of mechanical bending, they offer significant advantages in terms of precision and artistic expression. They are invaluable in small-scale projects or delicate tasks where machine methods might overcomplicate the process.
Essential Tools for Bending Copper Sheets
When involved in the world of metalworking, particularly with materials like copper, having the right tools isn't just a perk; it's essential. The tools used for bending copper sheets play a pivotal role in achieving precision, efficiency, and ultimately, quality in the work produced. Whether one is a hobbyist or a professional in the field, understanding these tools can make a significant difference in the outcome of any project.
Bending Dies and their Uses
Bending dies are fundamental in shaping copper sheets into desired forms. These tools provide the necessary structure to ensure consistent and accurate bends. They come in various styles, designed for specific types of bending tasks, such as box bending, angle bends, or custom shapes.
- Material Composition: Most bending dies are made from hardened steel or other durable materials, as they must withstand constant pressure without deforming.
- Customization: Many fabricators choose to invest in custom dies for unique projects. This investment can drastically reduce the time taken to achieve precise bends, helping to save both time and material.
Equipped with the right die, one can create brackets, panels, and many other components with ease. The craftsmanship that goes into fabricating these dies reflects directly in the final product.
Press Brakes: Types and Functions
Press brakes are specialized machines that incorporate two heavy beams and use hydraulic or mechanical power to perform bending operations. Their design aids in achieving high levels of accuracy and efficiency.
- Hydraulic Press Brakes: These are versatile and are most commonly used in industrial settings. The hydraulic system is effective in bending thicker sheets and provides significant force.
- Mechanical Press Brakes: They rely on a mechanical system to perform the bending. These are typically used for lighter materials and jobs that do not require much force.
- Pros: Higher bending force, better control, suitable for heavy-duty tasks.
- Cons: Higher upfront investment.
- Pros: Lower maintenance, quicker setup times.
- Cons: Limited in force capacity compared to hydraulic models.
Understanding the different press brake types can help enhance workplace efficiency, leading to quicker turnaround times and fewer errors in production.
Hand Tools for Sheet Bending
For those who prefer a hands-on or smaller-scale approach, hand tools for bending copper sheets are invaluable. These tools are not only budget-friendly but also allow for more direct manipulation of the material. Common hand tools used include:
- Hand Benders: Simple yet effective, these tools help achieve precise bends on thinner sheets.
- Bending Brakes: These are versatile hand-operated tools that let users create accurate bends across various angles. They offer flexibility in small workshops or home setups.
- Angle Finders and Calipers: Precision is key when bending. Utilizing tools like these ensures that each bend meets exact specifications, which can be vital in professional settings.
Using hand tools may require more physical labor compared to machines, but the skill and attention to detail can yield excellent results.
Safety Equipment for Metal Work
Safety should never take a backseat when bending copper sheets. The right safety measures protect not just the metal, but also yourself. Effective safety equipment includes:
- Safety Goggles: Protect your eyes from flying debris during bending.
- Gloves: Cut-resistant gloves guard against sharp edges, which can be a hazard when handling copper sheets.
- Aprons and Steel-toed Boots: Protect your body and feet from potential falling objects or splashes from tools.
Remember, safety is as much about the environment you work in as it is about the tools you use. Good safety practices make for a more efficient workflow and minimize accidents.
In summary, the arsenal of tools for bending copper sheets must be chosen wisely. Recognizing what each tool brings to the table, from dies and press brakes to hand tools and essential safety gear, can not only streamline the process but also enhance the quality of the work produced. This can be a stepping stone in developing skills and excelling in metal fabrication.
Preparation for Bending Copper Sheets
Preparing to bend copper sheets is a critical phase in the overall bending process. This step can often be underestimated, but doing it right can make all the difference in achieving a high-quality bend. By laying a solid groundwork through careful preparation, the likelihood of errors and subsequent need for rework diminishes considerably. Moreover, proper preparation ensures that the bending process flows smoothly and efficiently, conserving both material and time.
Measuring and Marking Techniques
Measuring accurately and marking the copper sheet is paramount before bending begins. Precision here helps avoid mishaps down the line. A reliable method is to use a steel ruler along with a permanent marker for clear lines. The goal is to measure twice, mark once—this age-old axiom holds true, especially when working with materials like copper, which can be costly and difficult to source.
Considerations include:
- Measuring for Accuracy: Always reference the specifications required for the bend, ensuring that any tolerances are taken into account.
- Scribe Lines: Using a scribe can also be beneficial to create precise lines that won’t smudge or rub off.
- Take Notes: It may be useful to jot down measurements to double-check later during the bending process.
Adhering closely to your measurements sets the tone for the entire operation.
Cleaning and Preparing the Copper
Cleaning the copper sheet prior to bending can’t be overlooked. Any grime, oxidation, or debris can impact the quality of the bend, possibly leading to fractures or an uneven curve. It’s essential to handle the copper carefully while cleaning, avoiding any harsh chemicals that might etch the surface.
A recommended approach includes:
- Washing: Using warm, soapy water helps in removing surface dirt. Make sure to rinse it thoroughly and dry it with a soft cloth.
- Degreasing: If the sheet has oil or grease, a degreaser or isopropyl alcohol will do the trick without damaging the metal.
Taking the time to clean and prep the copper allows for improved adhesion in any shapes or additional finishing processes that may follow.
Determining Bend Radius and Angle
Calculating the bend radius and the angle is essential to ensure that the bending process will yield the desired shape without compromising the metal's integrity. Both radius and angle will dictate how the copper behaves during and after bending. Crucial points to consider include:
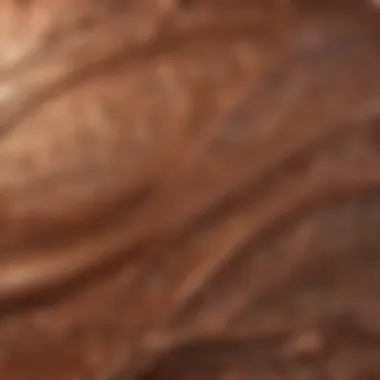
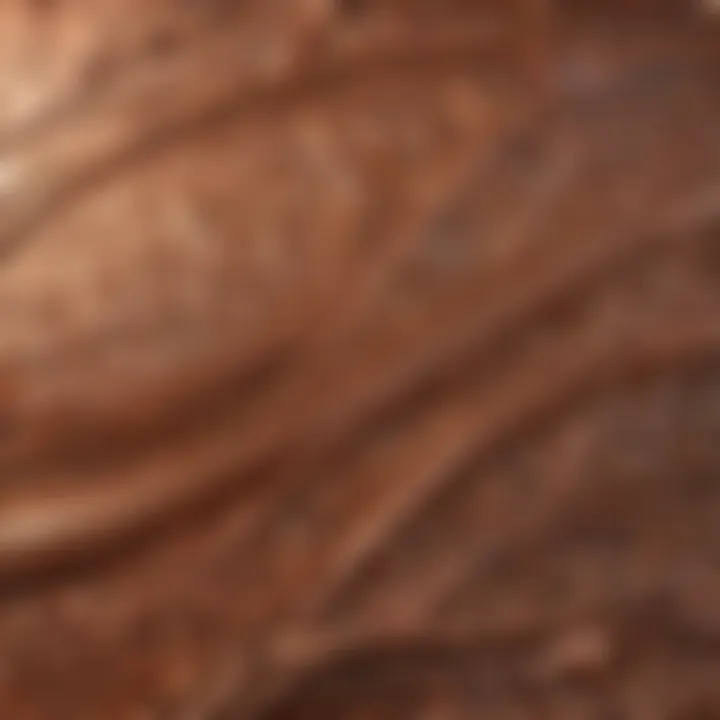
- Bend Radius: The bend radius is the distance from the inside curve of the bend to the center of the copper sheet. Generally, a larger radius minimizes the chances of cracking. A good rule of thumb is to ensure your radius is at least equal to the thickness of the sheet.
- Angle Measurements: The angle of the bend is determined by the application. For a 90-degree bend, for example, you could use a protractor to ensure precision.
- Material Thickness: Always account for the thickness of the copper sheet. This affects how tight or loose your bend can be.
This preparatory phase not only aids in achieving aesthetic results but also affects the functionality of the end product. As you can see, taking the proper steps in preparation is a matter of ensuring overall quality in the bending process. It’s an investment that pays dividends down the line.
"An ounce of prevention is worth a pound of cure."
Taking time in preparation can save colossal headaches in the end.
Executing the Bending Process
Executing the bending process is a pivotal phase in the manipulation of copper sheets. Understanding each step, from the initial setup to the final finishing touches, is crucial for ensuring the integrity of the material and the success of the overall project. It involves various techniques, each with its own merits and considerations, allowing professionals and amateurs alike to shape this versatile metal effectively.
The importance of this section cannot be overstated. A well-executed bending process leads to optimal results, reducing the potential for defects and wastage. It also enhances the efficiency of production, ensuring that time and resources are utilized wisely.
Steps in Mechanical Bending
Mechanical bending is often the go-to method for professionals looking to achieve precise angles and figures. The primary steps involved can typically include:
- Setup: Ensuring the bending tool (such as a press brake) is calibrated to the specifications outlined in your project.
- Positioning the Copper Sheet: Aligning the copper sheet to ensure that it's correctly placed for the bend. Misalignment can lead to unnecessary tension and eventually deformity.
- Engaging the Bender: Activating the bender mechanism to commence the process, while ensuring the desired force is applied uniformly.
- Monitoring: Observing the bending as it occurs, making fine adjustments as necessary to prevent excess strain on the material.
- Release: Gradually releasing the pressure once the bend is achieved, profoundly ensuring the shape remains unaltered.
Each of these steps requires attention to detail and expertise, emphasizing the skill involved in successful mechanical bending.
Understanding Thermal Dynamics
Thermal bending relies on manipulating the copper's properties through heat. The science behind it is not just about applying heat but understanding how it affects the metal's structure. When copper is heated, it becomes more malleable, making it easier to achieve sharper bends.
Here’s a simplified breakdown of what to consider:
- Heating Temperatures: Typically, copper needs to be heated to around 600–800 degrees Fahrenheit to become workable.
- Cooling Techniques: Gradual cooling can be just as crucial as heating. Sudden temperature drops can lead to cracking or shifting.
- Heat Distribution: Ensuring that heat is evenly distributed over the bend area will result in a smoother, more uniform shape.
Getting a firsthand grasp on these thermal dynamics can prevent common pitfalls, such as warping or brittleness later in the process.
Roll Bending Procedures
Roll bending is a highly efficient technique often used in industrial settings for creating large radius curves. This method employs a series of rollers to bend the copper flat sheet into the desired shape. The process involves specific procedures, which generally include:
- Material Selection: Choosing the appropriate gauge of copper sheet for the intended application.
- Roll Setup: Positioning the rollers to the desired curvature. The initial gap between rollers will determine the radius of the bend.
- Feeding the Copper: Carefully feeding the copper sheet into the rollers while ensuring proper alignment and speed.
- Multiple Passes: Often, achieving the desired curve requires several passes, each adjusting the infile gap slightly to finesse the radius further.
Utilizing these procedures effectively will lead to consistent and appealing results in your bends.
Monitoring the Bending Process
The monitoring phase is often overlooked but is essential to achieving high-quality bends in copper sheets. Throughout the bending process, continuous observation can avert many complications. Things to keep an eye on include:
- Tool Functionality: Regular checks on the bending equipment for any signs of malfunction.
- Material Condition: Observing the copper sheet during bending to catch early signs of stress like warping or fracturing.
- Production Consistency: Ensuring that each bend maintains the specifications set out in the initial stages of the project.
"An ounce of prevention is worth a pound of cure.” Monitoring is key to avoiding mistakes that can lead to costly rectifications.
Common Challenges in Bending Copper Sheets
Bending copper sheets is not a walk in the park; it comes with its own set of hurdles. Understanding these challenges is key for those involved in metalwork or manufacturing. It’s important to recognize that without proper attention to these issues, one can end up with poor quality results or a stripped project. Each of these problems presents not just a hindrance but an opportunity for improvement and skill enhancement.
Deformation and Wrinkling Issues
Deformation and wrinkling are two of the most notorious adversaries in the bending of copper sheets. When the bending process is rushed or improperly executed, the metal is likely to warp, creating unsightly and structurally unsound results. Some potential causes include:
- Wrong tools or pressure settings: Utilizing inappropriate tools or incorrect pressure can lead to uneven bends.
- Inadequate planning: Failing to adequately plan the bends, such as not calculating the bend allowance, can also contribute to these deformities.
Preventing deformation requires adequate preparation and understanding of the material’s properties. When a technician knows how much force to apply and what angle to achieve, it greatly reduces the chance for error.
"Engaging with the material and mastering the calculation for bend allowance ensures the smoothest path in avoiding deformation issues."
Stress and Fatigue in Copper Sheets
Stress and fatigue in copper sheets are often overlooked but can lead to significant failures in both appearance and structural integrity. Copper, while malleable, is not immune to stress concentrations that occur during bending. Factors to consider include:
- Thickness of the sheet: Thicker sheets often experience more stress during bending than thinner ones.
- Bend radius: A tighter bend radius can amplify stress, potentially leading to cracks or fractures over time.
It’s crucial to monitor the stress levels throughout the bending process. A more gradual bending approach, along with the correct radius, can greatly alleviate undesired strain on the materials.
Avoiding Cracking During Bending
Cracking is perhaps the most detrimental outcome one could face when bending copper sheets. Such failures often invalidate the work and call for a complete redo. The risks of cracking increase significantly under certain conditions:
- Too much force: Applying excessive force can lead to cracks almost instantly. It’s all about finding that sweet spot; excessive force leaves no room for error.
- Cold temperatures: Copper behaves differently when it’s cold; it loses some flexibility. Bending at lower temperatures increases the risk of cracking.
- Inadequate lubrication: Not using proper lubrication during bending can create friction that contributes to cracking.
To mitigate the risks associated with cracks, it's advisable to use heating or appropriate lubrication methods before executing bends. This assists in keeping the copper sheet flexible and able to withstand the forces being applied.
Understanding these challenges allows for better planning and execution, enhancing both the efficiency and quality of work with copper. Taking the time to address deformation, stress, and cracking will lead to more successful outcomes and an overall stronger end product.
Post-Bending Procedures
After the process of bending copper sheets is complete, there are crucial steps to follow that ensure the results meet required standards. Engaging in post-bending procedures is key; it impacts the quality of the finished product, the usability in various applications, and even the longevity of the copper itself. Each stage of this process caters to specific elements such as thorough inspection, deciding on surface finishes, and proper storage techniques. When executed correctly, these follow-up actions mitigate issues that can arise post-manufacturing and enhance the overall outcome.
Inspection and Quality Control
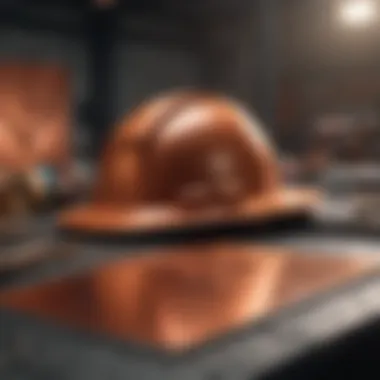
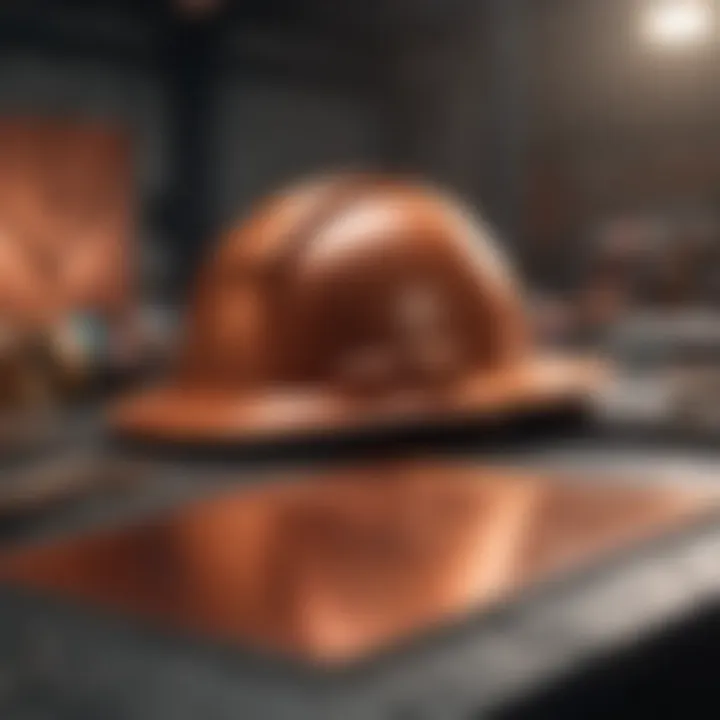
Once the bending process is done, inspection takes center stage. This isn't merely a cursory glance; it’s a detailed examination that checks for any imperfections. These could include issues like uneven edges, warping, or cracks that might not be visible at first. One effective method to perform this inspection is through the use of gauges and calipers that measure dimensions accurately.
Implementing a quality control protocol ensures that each batch of copper sheets meets industry standards. This might involve setting up checkpoints at various stages prior to final usage. Here’s a quick look at what a solid inspection routine might look like:
- Visual Inspection: Look for surface blemishes or inconsistent bends.
- Dimensional Checks: Measure thickness, width, and bend angles.
- Non-Destructive Testing: Techniques like ultrasonic testing can reveal hidden discrepancies without damaging the material.
By investing time in rigorous inspection, manufacturers can avoid costly errors down the line, further securing the integrity of their projects.
Finish Options for Bended Copper
After making sure everything is in order with the inspection, the next point of consideration is deciding on the finish for the bended copper. This plays a crucial role in determining the aesthetic appeal and functionality. Quite a few options can be explored:
- Natural Finish: Leaving the copper in its natural state leads to it developing a patina over time, a favored look in certain architectural applications.
- Lacquer Coating: Applying lacquer provides a clear finish that protects against oxidation and tarnishing, keeping the copper looking pristine.
- Electroplating: This involves coating the copper with a layer of another metal. It's a great way to improve durability and corrosion resistance.
- Anodization: Involves chemical processes that enhance the oxide layer, allowing for additional colors and improved resistance.
Each finish option brings unique properties that suit different needs, affecting everything from aesthetics to longevity, it's wise to choose the one that aligns with the intended application.
Storing and Handling Bended Copper Sheets
Finally, once the inspection and finishing options are sorted, storage becomes a priority. Proper handling and storage techniques are essential in preventing damage and preserving the quality of the bended copper sheets. Some considerations include:
- Flat Storage: Store sheets flat, avoiding stacking that can lead to warping or bending.
- Controlled Environment: Ideally, maintain stable temperature and humidity levels to reduce oxidation risks.
- Use of Protective Covers: Covering sheets with a plastic or tarpaulin can shield from dust and moisture, especially in outdoor environments.
- Handling Protocols: When moving sheets, it’s essential to use gloves to avoid transferring oils or dirt, which can compromise quality.
Remember: Taking these precautions ensures that the integrity of the work is maintained. Copper is expensive, and caring for it reduces waste and enhances sustainability in practices.
Thus, post-bending procedures are not just about wrapping things up; they are an integral part of the whole process. From inspection through to storage, it’s the details that set good work apart from excellent work.
Applications of Bended Copper Sheets
The applications of bended copper sheets stretch far and wide, encompassing a broad spectrum of industries and creative endeavors. Understanding these applications not only highlights the practical utility of the material but also reveals the intricate connection between engineering, art, and technology. Copper's excellent conductivity, malleability, and resistance to corrosion make it an ideal choice in various fields. Here, we will dive into three specific areas: architectural elements, electrical conductive components, and artistic uses, each bringing unique challenges and benefits into focus.
Architectural Elements
In architecture, bended copper sheets serve both functional and aesthetic purposes. From roofing to decorative facades, the versatility of copper allows designers to explore innovative forms.
- Durability: One of the endearing qualities of copper is its long lifespan. With natural resistance to degradation, architectural components made from copper not only look striking but can also endure the harshest weather conditions.
- Patina Development: Over time, copper develops a patina that adds value to architectural aesthetics. This greenish hue is not just beautiful; it serves as a protective layer, further extending the life of the material.
- Sustainability: The recyclability of copper makes it an environmentally friendly choice. Structures utilizing bended copper sheets contribute to sustainable architectural practices.
Architects and builders striking the right balance between beauty and functionality often choose copper, especially in projects where an iconic or historical appearance is desired.
Electrical Conductive Components
Moving into the realm of electricity, the bending of copper sheets is crucial for various conductive components. Due to its exceptional electrical and thermal conductivity, copper remains unsurpassed in multiple electrical applications. Whether for residential wiring or industrial machinery, bent copper sheets facilitate:
- Effective Heat Dissipation: The ability to manage heat effectively is vital in electrical components. Copper ensures that excess heat generated in devices is distributed and dissipated adequately, maintaining efficiency.
- Compact Designs: With the advent of modern electronics demanding smaller, more efficient components, bended copper sheets can be tailored to fit snugly into tight spaces without sacrificing performance.
- Connectivity: Bended copper sheets form connections in circuit boards and other hardware, proving essential in ensuring reliable electric conduction.
In summary, the electrical applications of bended copper sheets underline the material’s critical role in modern technology.
Artistic and Decorative Uses
On the creative side, copper's aesthetic qualities shine in artistic applications. Artists and craftsmen frequently choose bended copper sheets for:
- Sculptures and Installations: The malleability of copper allows artists to create intricate designs and sculptures. Its ability to be bent and shaped without breaking often leads to unique forms that captivate viewers.
- Home Decor: From wall art to bespoke furniture pieces, bended copper sheets contribute a touch of charm and sophistication to interior spaces. Their warm tones and textures blend well with various design styles.
- Craftsmanship: In metalwork, skilled artisans utilize copper's properties for making jewelry and other decorative items. The bendability of sheets can lead to complex shapes that enhance the intricacy of the final product.
Ultimately, amber sunsets and intricate roofing are only the tip of the iceberg. In realms of both function and art, bended copper sheets resonate through practical utility and creative expression, where the only limit is the imagination.
"Copper's appeal lies in its dual nature: both a workhorse material in industry and a canvas for artistic expression."
Through understanding the diverse applications and relative merits of bended copper sheets, we gain insight into why this enduring material remains popular across various fields.
Future Trends in Copper Sheet Bending
As industries continue to evolve, the future of bending copper sheets becomes a topic of significant importance. Addressing how technology, sustainability, and marketplace dynamics shape bending practices not only prepares practitioners for upcoming changes but also ensures they remain relevant in an ever-competitive environment. With copper being a pivotal material in various sectors such as electrical, construction, and art, understanding future trends is essential for maximizing both efficiency and innovativeness.
Innovations in Technology
The advancements in technology are transforming how copper sheets are bent. High-precision CNC machines now allow for unprecedented accuracy in bending. With these machines, manufacturers can achieve complex shapes that were once thought impossible.
- Programmable Bending: This technology enables operators to program specific bending angles and parameters into the machine, ensuring consistency and reducing waste. This is especially important in large-scale productions where uniformity is crucial.
- Laser Cutting: Before bending, sheets can be precisely cut using lasers, minimizing the need for secondary processes. This method is valued for its clean cuts and reduced lead times.
Further, the emergence of 3D printing techniques is paving the way for new designs in copper applications, giving artists and engineers the freedom to explore realms of creativity that were previously constrained. As these technologies develop, the overall productivity and capabilities in bending copper sheets will continue to improve, pushing boundaries.
Sustainability in Copper Production
The spotlight on sustainability is not just a passing trend; it’s becoming a staple practice in the manufacturing world. The copper industry is adapting by embracing greener practices.
- Recycling Initiatives: The recycling of copper has been an industry norm, but enhanced techniques are being developed to reclaim more materials from waste effectively. Bended copper products often find themselves back into the production cycle, reducing the environmental impact.
- Eco-Friendly Processing: New methods are being explored such as cold bending, which minimizes thermal processes and energy use. These innovations align with global initiatives to lower carbon footprints in manufacturing activities.
By adopting these sustainable practices, companies engage in ethical responsibility while furthering economic growth through efficiency gains and reduced costs.
Emerging Applications and Markets
As society progresses, so does the need for bended copper sheets in emerging applications and markets. This material's versatility makes it adaptable in various fields:
- Renewable Energy: The demand for copper in solar panel production and wind turbines is on the rise. As these technologies expand, so does the necessity for specialized copper sheets.
- Smart Technology: The integration of copper sheets in consumer electronics is growing. With the proliferation of smart devices, there's increased demand for components that require bending to fit intricate designs.
The global exploration of copper markets is expanding, particularly in regions focusing on developing infrastructure. These trends point to a flourishing future where copper sheet bending becomes integral to advancing technology and improving quality of life.
"In a world that is embracing technology, those who adapt to the changes in material processing will not just survive; they will thrive."
By understanding these trends and adapting accordingly, practitioners in the field can position themselves to harness the full potential of bending copper sheets, ensuring success in and beyond the factory walls.