Calculating Gear Reduction: Principles and Applications
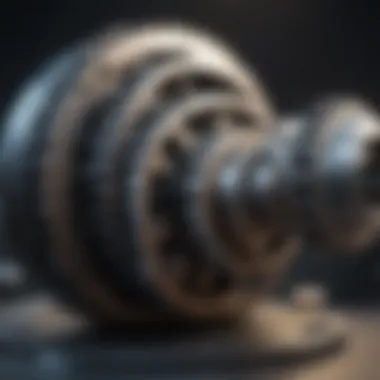
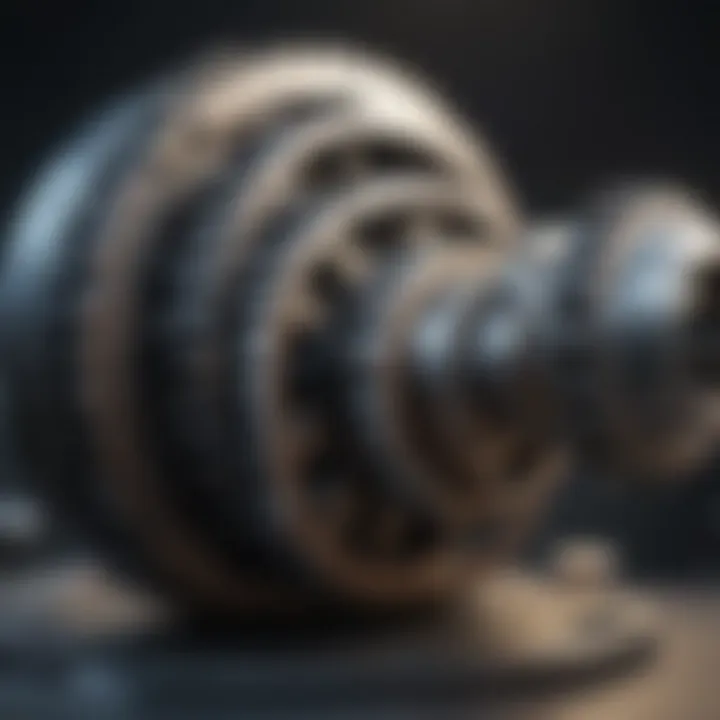
Intro
In the realm of mechanical engineering, the concept of gear reduction emerges as a pivotal principle. This section serves as a preamble to understanding how gears operate within various systems. Gear reduction translates to the relationship between the speed and torque of rotating objects linked by gears. This relationship is fundamental for designing effective machinery, allowing engineers to optimize performance based on desired output.
The intricacies of gear reduction span various applications, from automotive engineering to robotics. A firm grasp of this principle demands clarity on terms, calculations, and implications. As we delve into the associated calculations and theory, it is essential to appreciate how these elements integrate to yield practical solutions in engineering design.
Key Concepts
Understanding gear reduction necessitates a clear definition of primary terms involved, alongside an exploration of related concepts and theories.
Definition of Primary Terms
- Gear Ratio: This term refers to the ratio of the number of teeth on two meshing gears. A higher gear ratio signifies that the driving gear has more teeth than the driven gear.
- Torque: A measure of rotational force. Torque produced by a gear system is affected by the gear ratio, influencing the system's overall performance.
- Speed: The measure of how quickly a gear rotates, often expressed in revolutions per minute (RPM).
Related Concepts and Theories
The foundations of gear reduction align with several mechanical principles:
- Mechanical Advantage: This concept indicates the ratio of output force to input force in a mechanism, crucial for understanding load capacities.
- Kinematics of Gears: The motion of each gear affects the system's performance. The study of these motions allows predictive modeling for system behavior under various conditions.
- Efficiency: This relates to the degree of energy loss in a gear system, often expressed in percentage. Understanding efficiency can guide design choices for optimal performance.
"Mastering the art of gear reduction is essential for any aspiring engineer looking to innovate and enhance mechanical systems."
Future Directions
As the field of gear reduction evolves, several gaps remain in current research and application practices. Future studies could focus on:
Gaps Identified in Current Research
- Limited understanding of new materials affecting gear performance.
- Insufficient research on the long-term effects of wear in gear systems.
Suggestions for Further Studies
- Investigating advanced alloys and composites for gear manufacturing.
- Analyzing the impact of lubrication and maintenance on gear longevity.
In wrapping up, appreciating the principles of gear reduction extends beyond mere calculations. It involves a comprehensive understanding of the interconnected principles that govern mechanical systems. As we explore practical applications and detailed calculations, a thorough grasp of these concepts ensures one can harness the full potential of gear systems.
Understanding Gear Reduction
Gear reduction is a critical concept in mechanical engineering. It defines how much a gear decreases the speed and increases the torque of a machine. Understanding gear reduction is fundamental for students, researchers, educators, and professionals in engineering fields. It influences design decisions in various applications, from automotive engineering to robotics. By grasping the principles of gear reduction, one can optimize machine performance, enhance efficiency, and achieve desired operational outcomes.
Definition of Gear Reduction
Gear reduction refers to the ratio between the number of teeth on two gears engaged in a meshing relationship. This ratio determines how much the speed of the driven gear (the output) is decreased compared to the driving gear (the input). Essentially, when a smaller gear turns a larger gear, the output speed decreases while the torque increases. This principle is leveraged in various machines, allowing for better control over power delivery and speed management.
Key Components of Gear Systems
Gear Types
Different gear types serve unique purposes in machines. For instance, spur gears are common for simple applications, while bevel gears adapt rotation between shafts at different angles. Their specific shapes and configurations allow engineers to address various mechanical needs. The choice of gear type impacts efficiency, space, and performance, making it crucial to select wisely.
Key Characteristics:
- Spur Gears: Most popular and straightforward for direct applications.
- Bevel Gears: Effectively change the axis of rotation.
Each gear type has its advantages and disadvantages. For example, while spur gears are efficient at transferring rotational motion, they generate more noise compared to helical gears.
Gear Teeth
The configuration of gear teeth is essential in determining how gears interact. The number of teeth, their shape, and pitch all affect how smoothly and efficiently gears mesh. A common characteristic is that larger gears with more teeth will generally reduce speed more than smaller gears.
Unique Feature:
- Tooth Profile: The design impacts wear and shifting performance.
- Material: Materials affect durability and performance under load.
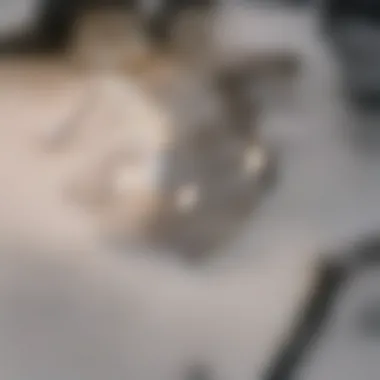
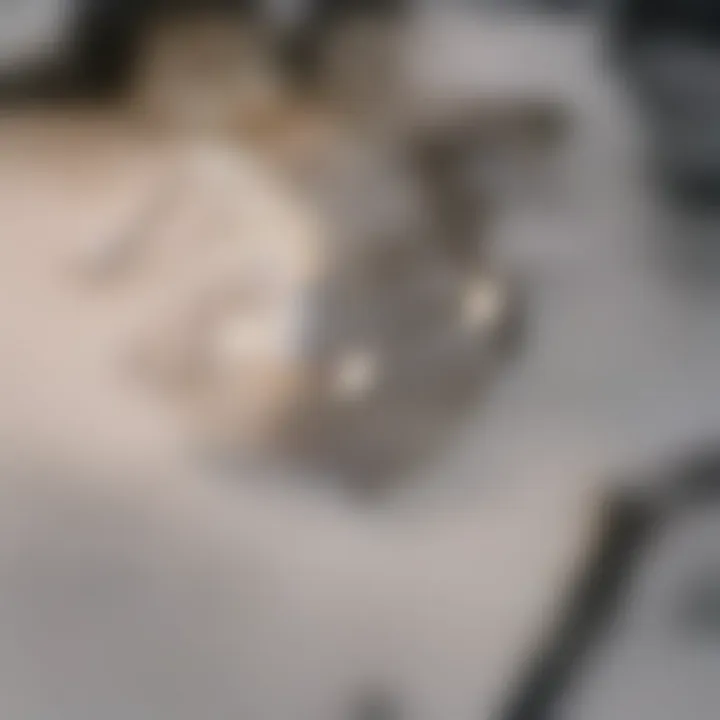
Understanding gear teeth helps engineers design systems that function correctly over long periods. Choosing the right tooth profile can reduce noise and enhance reliability.
The Importance of Gear Reduction
The principle of gear reduction plays a vital role in various fields. In automotive engineering, it is crucial for managing engine power. Effective gear ratios can lead to better fuel efficiency and performance. In robotics, it ensures precision in movements. These applications highlight the necessity of understanding gear reduction. Failing to consider gear reduction can limit a machine's effectiveness, underscoring its importance in design and engineering.
Fundamental Principles of Gear Mechanics
Understanding the fundamental principles of gear mechanics is essential for grasping how gear reduction operates within various mechanical systems. Gear systems are at the core of many machines, providing the necessary alterations in speed and torque that enable efficient operation. This section focuses on significant elements like the relationship between torque and speed, the calculation of gear ratios, and their implications for practical applications.
Torque and Speed Relationship
Mechanical Advantage
Mechanical advantage is a crucial aspect of how gear systems function. It represents the factor by which a mechanism multiplies the force put into it. In gear systems, this means that by using gears, one can efficiently amplify the torque. This characteristic makes mechanical advantage highly beneficial for applications needing significant force, such as starting motion in heavy equipment.
One unique feature of mechanical advantage in gear systems is its capacity to create a balance between torque and speed. For instance, if a smaller gear drives a larger gear, the torque increases while the speed decreases. Thus, mechanical advantage becomes popular in design choices where high torque output is necessary while controlling speed.
However, engineers must consider the trade-offs. While high mechanical advantage can provide powerful forces, it usually results in lower rotational speeds, which may not suit all applications.
Speed Reduction
Speed reduction plays another vital role in the functionality of gear systems. Speed reduction refers to decreasing the rotational speed of an output gear compared to its input gear. This feature is indispensable in applications where precise control of movement is essential, such as in robotics and automotive systems.
A distinctive characteristic of speed reduction is its direct impact on enhancing torque. The more speed is reduced, the more torque is generated on the output side. Therefore, it is often the choice for engineers aiming to optimize power transmission in a way that balances speed and force.
The primary disadvantage of speed reduction is that while it augments torque, it also reduces the system's responsiveness. This can be a concern in applications requiring quick changes in speed or direction.
Gear Ratio Calculation
Simple Ratio Calculation
Simple ratio calculation is fundamental for understanding gear systems. It involves a straightforward formula that shows the relationship between the number of teeth on two or more gears. By knowing the number of teeth on the driving gear and the driven gear, one can easily derive the gear ratio. This simplicity makes it very beneficial for initial designs and analysis.
A unique feature of this method is that it can directly inform engineers about how the system will behave in terms of speed and torque. For example, a gear ratio of 2:1 indicates that the driving gear is twice as fast as the driven gear. This information is crucial for developing balanced systems with predictable performance.
However, while it is simple and effective, it may not cover the complexities often found in compound gear systems where multiple gears interact.
Compound Gear Systems
When dealing with compound gear systems, the calculations become slightly more complex. These systems involve multiple gears interacting, which makes the overall gear ratio depend on the product of the individual ratios. This feature allows for greater flexibility in design, enabling engineers to achieve specific speed or torque outcomes tailored to unique applications.
The strength of utilizing compound gear systems lies in their ability to achieve large reductions in speed or increases in torque without requiring disproportionately large gears. This makes them beneficial for compact designs in fields like robotics or power transmission.
On the flip side, the complexity in understanding and calculating the ratios can lead to challenges. Maintenance and alignment of multiple gear systems may also introduce additional factors to take into consideration when designing gear mechanisms.
Understanding these principles is vital for engineers and designers aiming to optimize gear systems for efficiency and performance.
Methods to Calculate Gear Reduction
Calculating gear reduction is a critical aspect in designing efficient mechanical systems. The methods covered in this section help engineers and designers understand how to manipulate speed and torque to achieve desired performance. Accurate calculations ensure that machinery operates smoothly. Furthermore, these calculations help in preventing failures and optimizing resource use. The steps to calculate gear reduction will be examined closely. This includes understanding the formulas involved and applying them to various systems.
Formula for Gear Reduction
To understand gear reduction, one must first recognize the underlying formulas. The primary formula operates on the principle of comparing input and output values. This is essential for determining how much speed is sacrificed for increased torque.
Input and Output RPM
Input and output RPM, or revolutions per minute, are crucial for evaluating gear performance. The input RPM reflects how fast the motor drives the gears, while output RPM indicates what speed the driven gear operates at. The role of these values is significant, as they form the basis of performance assessment. Monitoring input RPM can assist in determining the system's efficiency. Higher input RPM often leads to greater output speeds, but at a cost to torque. In many applications, this characteristic is beneficial because it allows flexibility in design, accommodating variable speeds. Utilizing input and output RPM calculations can help identify the best configurations for specific applications. However, simplifying to these two metrics can also gloss over more complex interactions in multifaceted systems.
Gear Teeth Count
Gear teeth count serves as another vital parameter in gear reduction methods. The count directly correlates with the gear ratio in a system. A gear with more teeth will reduce speed more than a gear with fewer teeth when paired together. This easy calculation can significantly influence gear performance. The unique feature of gear teeth count is its influence on overall mechanical advantage. A larger teeth count can enable finer control of motion, an appealing aspect for precise applications. In contrast, a lower count can lead to higher output speeds but reduced torque. Balancing these factors is key in any engineering design.
Using Gear Ratio for Calculations
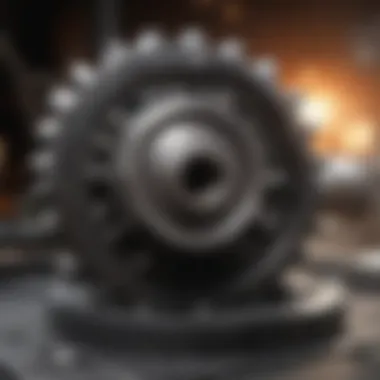
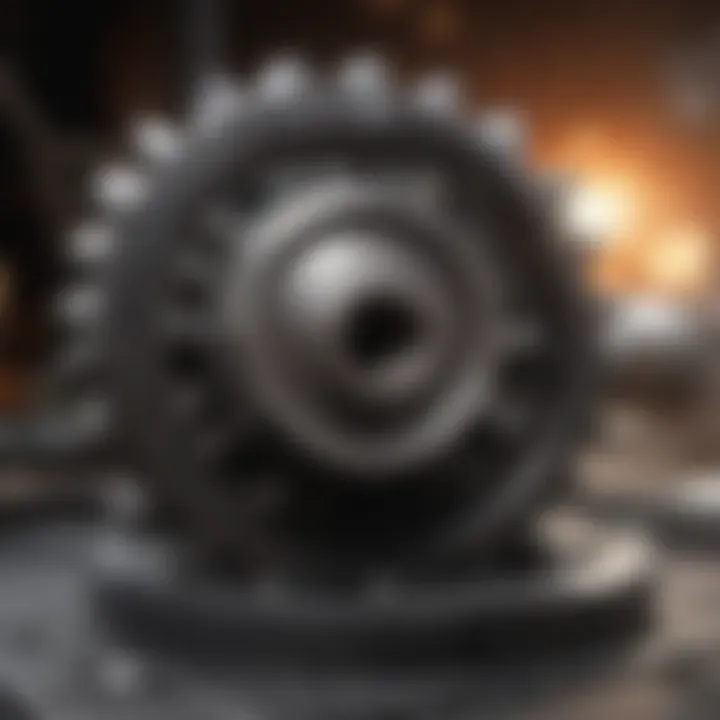
Employing gear ratios paints a broader picture of how gears interact when engaging. An understanding of gear ratio helps reveal not only how speed and torque adjust but also their overall effects on system dynamics. It is pivotal for system efficiency.
Single Gear Calculations
Single gear calculations focus on the straightforward relationship between two gears. This method is often the first step in gear design. The simplicity of these calculations is a major advantage; they provide quick insights into performance. This is especially beneficial in preliminary design stages. However, the limitation of impact analysis arises from their simplification. They do not account for potential compound effects introduced by multiple gear stages. Nevertheless, knowing single gear performance is essential for building more complex systems.
Multi-Gear Systems
In contrast, multi-gear systems involve several gears functioning together. This approach allows for more nuanced calculations concerning torque and speed. Each gear in the system affects the next. The collective impact of each gear can lead to unique behaviors, enhancing overall performance. Multi-gear calculations offer the benefit of optimizing complex mechanical systems to achieve the best efficiency possible. However, the complexity can also become a disadvantage, requiring more thorough analysis and understanding. Balancing system performance across varying configurations is vital for successful implementation.
Practical Applications of Gear Reduction
Understanding practical applications of gear reduction is essential for grasping its significance in various fields. Gear reduction serves different industries by enhancing efficiency, improving performance, and enabling machines to fulfill complex tasks that require precise movements. The importance of gear reduction lies in its ability to provide the necessary power amplification, manipulate speed, and facilitate control over machinery, specifically in automotive engineering, robotics, and industrial applications.
Applications in Automotive Engineering
Transmission Systems
Transmission systems are fundamental to automotive engineering. They play a role in delivering power from the engine to the wheels effectively. Gear reduction in transmission systems is crucial because it allows vehicles to start moving from a standstill and to maintain power while navigating various terrains. Notably, these systems enable optimum torque and speed adjustments, making driving smoother and more responsive. A key characteristic of transmission systems is their adaptability to changing driving conditions, which makes them a reliable choice for vehicles of all types.
The unique feature of transmission systems is their ability to change gear ratios seamlessly. This capability results in improved fuel efficiency and enhanced vehicle performance, although they may incur additional complexity and maintenance requirements. Moreover, the advancements in automatic transmission technology, such as CVTs, highlight the ongoing evolution within gear reduction applications in cars.
Auxiliary Gear Units
Auxiliary gear units are accessories that complement primary systems within vehicles. Their purpose is to manage secondary functions, such as powering additional equipment like winches, pumps, or other tools utilized in various vehicles, especially in off-road or specialized applications. The key characteristic of auxiliary gear units is that they provide enhanced versatility and can be tailored to specific needs. This makes them beneficial for machinery that requires additional power without overly consuming space or resources.
These units often feature customizable gear ratios, which allow for higher torque outputs for specialized tasks. Although they augment the machine's functionality, one downside can be increased weight and potential complexity that may arise from additional components. Nevertheless, their ability to enhance capabilities across various vehicles is significant in many sectors.
Role in Robotics
Motor Integration
Motor integration in robotics emphasizes the connection between motors and gear systems to achieve desired motions. Effective gear reduction contributes significantly to this integration, providing the necessary torque to move robotic limbs or navigate complex terrains smoothly. The vital aspect of motor integration is its function in controlling the speed and precision of movements in robots. This is essential, especially in tasks requiring fine motor skills or high-speed operations.
A notable feature of motor integration is the ability to have feedback mechanisms that adjust performance in real-time. This impact enhances the reliability of robotic systems but can introduce coordination challenges, especially when multiple motors are in play. The reliance on gear reduction makes motor integration a valuable focus in robotics, resulting in advanced functionality and applications across different fields.
Movement Precision
Movement precision in robotics relies heavily on gear systems for accurate positioning and control. By using gear reduction, robots can achieve exact orientations and speed adjustments necessary for delicate operations, such as assembly tasks in manufacturing. The main characteristic of movement precision is its dependency on consistent feedback from the environment, allowing robots to make informed decisions based on real-time data.
The unique feature of movement precision systems is their capability to perform intricate tasks autonomously. However, this complexity can lead to challenges, including system calibration and potential disruptions in feedback loops. Despite these issues, the incorporation of gear reduction to enhance movement precision represents a significant advance in robotic capabilities.
Industrial Applications
Conveyor Systems
Conveyor systems are prevalent in industrial settings where the movement of materials is vital. Gear reduction is part of these systems, enabling efficient transport of goods across production lines. The central characteristic of conveyor systems is their reliability and adaptability to various materials and conditions. Their use reduces workforce strain, thereby enhancing efficiency in material handling operations, which is vital for productivity.
A unique feature is the ability to incorporate multiple gear ratios to accommodate different types of loads and speeds. While this versatility is an advantage, the potential for mechanical failure or overcrowding can disadvantage large systems. Nonetheless, their integration with gear reduction systems increases overall operational effectiveness.
Machinery Drives
Machinery drives encompass a range of equipment used across various industries for tasks such as manufacturing, construction, and material handling. Gear reduction within machinery drives allows for efficient energy transfer, which is crucial for maintaining operational output. The defining characteristic of machinery drives is their capacity to handle significant loads while optimizing performance, ensuring speed and torque remain balanced according to the task demands.
An essential feature of machinery drives is their ability to integrate with automation systems to enhance operational capabilities. However, they may face challenges such as wear and tear from continuous use and the need for regular maintenance. Still, their importance in gear reduction applications cannot be underestimated, as they provide the backbone for crucial industrial operations.
Challenges and Considerations in Gear Design
The realm of gear design must address numerous challenges and considerations to achieve effective and reliable performance. These challenges are not merely technical; they encompass a range of factors that can influence efficiency, durability, and overall success of mechanical systems. Understanding these considerations can lead to significant improvements in design practices and operational capability.
Efficiency Calculations
Friction Loss
Friction loss is a critical concept in gear design. It refers to the energy lost due to friction between the moving parts of a gear system. This aspect is essential to balance, as excessive friction can lead to overheating and decreased efficiency. In terms of gear design, minimizing friction loss is prioritized to enhance performance in various applications. One of the key characteristics of friction loss is that it usually increases with the load on the gear.
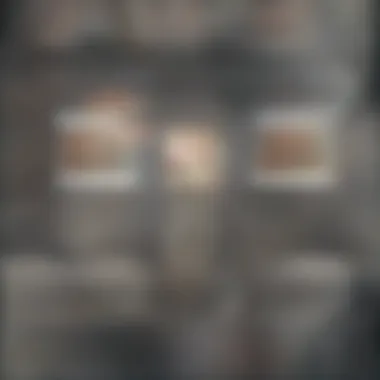
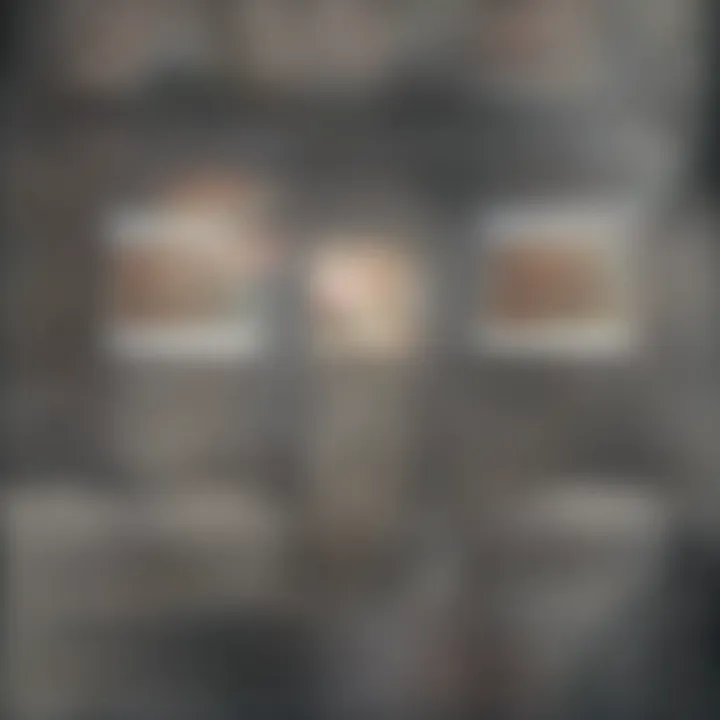
In this aspect, friction loss becomes a popular topic because of its direct impact on operational cost. For instance, gears with lower friction can operate cooler and require less energy, saving on operational costs. However, one must note the trade-offs: reducing friction excessively may compromise the gear's ability to handle loads and lead to increased wear and tear.
Thermal Considerations
Thermal considerations have a significant role in gear design. These principles guide how engineers calculate and manage temperature impacts on gear systems. Gears generate heat during operation due to friction, and understanding this heat generation is vital. If temperatures exceed safe levels, it can lead to material degradation or failure of the gear system.
The key characteristic of thermal considerations is the focus on heat dissipation. Effective cooling methods must be employed to prevent adverse effects on performance. This makes thermal considerations a beneficial aspect in gear design. However, it introduces complexity, as designers must integrate thermal management systems while maintaining the simplicity of the mechanical design. Its unique feature also includes the potential for thermal expansion, which can change the fit between gear components and affect operation.
Common Design Flaws
Misalignment
Misalignment is another common challenge encountered in gear systems. This problem arises when gears are not properly aligned with each other, leading to uneven wear and potential failure. The key characteristic of misalignment is that it can often go unnoticed until significant damage is done, making it a critical issue in design and maintenance. This flaw is particularly relevant in discussions about gear design because it can drastically affect reliability and increase operational costs.
To prevent misalignment, precise manufacturing processes and installation techniques are essential. However, even minor imperfections can lead to misalignment, creating a challenge in design and maintenance efforts. Thus, awareness of alignment during the early stages of design is critical.
Material Selection
Material selection plays a pivotal role in gear durability and performance. The right materials must withstand the operational loads and environmental conditions. A key characteristic of material selection is considering mechanical properties such as strength, hardness, and corrosion resistance. This is vital in gear design as choosing the wrong material can result in premature gear failure.
Selecting high-quality materials is a beneficial choice for designers as it enhances the reliability of the gears. However, there are trade-offs, such as cost and availability. Each material brings its unique features and challenges. For example, while metals like steel are strong, they can also be heavy. Composites, on the other hand, may offer weight savings but often at the expense of strength.
Future Trends in Gear Technology
The landscape of gear technology is evolving rapidly, driven by advancements in digital methods and innovative materials. Understanding these trends is not only important for engineers and designers but also enhances the overall efficiency and capabilities of mechanical systems. Embracing these changes can lead to more effective designs, reduced costs, and improved performance in a variety of applications.
Digital Methods in Gear Design
Simulation Software
Simulation software plays a crucial role in modern gear design. It allows engineers to test and optimize gear performance virtually before any physical prototypes are made. The key characteristic of simulation software is its ability to predict how gears will behave under different conditions. This predictive capability is beneficial as it minimizes the trial-and-error process, which can be time-consuming and costly.
One unique feature of simulation software is its capacity for real-time adjustments. Engineers can modify parameters, such as load conditions or material properties, during simulations to view immediate effects on gear performance. This adaptability is a notable advantage in reducing development time and ensuring designs meet specific requirements.
However, there are also some disadvantages. The accuracy of results often depends on the quality of the input data, and sometimes complex simulations require considerable computational resources, which can be a barrier for smaller firms.
3D Printing of Gears
3D printing technology has erupted in its application for creating gears. This method allows for rapid prototyping and production of custom gears with complex geometries that traditional methods may struggle to replicate. A significant benefit of 3D printing is that it reduces the lead time for manufacturing and can accommodate low-volume production runs effectively.
The unique ability to create lightweight and intricate designs makes 3D printing a favorable choice in gear design. This technology also enables engineers to play with different designs and materials, leading to more innovative outcomes. One considerable disadvantage, though, is that not all printed materials can withstand high operational loads, which may limit their applications in more demanding environments.
Innovative Materials and Configurations
Composite Materials
The use of composite materials is transforming the approach to gear construction. Composite materials combine the advantages of different substances to create lightweight parts with enhanced strength. The key characteristic that makes composite materials appealing is their high resistance to fatigue and corrosion.
For gear design, using composites can lead to significant weight reductions while maintaining functionality. This feature is particularly valuable in applications such as aerospace or automotive engineering, where reducing weight can enhance performance and fuel efficiency. However, the downside is that composite materials can be more expensive than traditional metals, which may deter some manufacturers.
Custom Gear Shapes
Custom gear shapes are becoming more popular with advancements in design software and manufacturing processes, such as CNC machining. A notable aspect of custom gear shapes is their ability to be precisely tailored for specific applications. This customization can lead to optimized performance, improved efficiency, and longevity of the gear system.
The flexibility in design is a significant advantage. Engineers can create gears that better fit the unique requirements of their projects, providing solutions that standard gears might not adequately address. Still, one disadvantage may arise in the complexity of producing custom gears, as this can sometimes lead to increased production costs and extended time frames for delivery.
Epilogue
Understanding gear reduction is crucial for various engineering fields. It plays a vital role in maximizing efficiency and performance in machinery. This article has outlined the principles and applications of gear reduction, providing insights into its calculations and design.
Summary of Key Points
- Gear Reduction Defined: Gear reduction occurs when gears are configured to decrease output speed while increasing torque. This mechanism is essential in applications requiring high power from low speeds.
- Core Calculations: The relationship between input speed, output speed, and gear ratio is fundamental. Knowing how to calculate these values enables design optimization in various systems.
- Practical Applications: Industries like automotive, robotics, and manufacturing heavily rely on gear reduction. Applications range from transmission systems to conveyor belts, highlighting its versatility.
- Challenges in Design: Issues like efficiency loss through friction and material selection are critical factors in gear design that require careful consideration.
Implications for Future Research
Future research on gear reduction might explore several avenues, including:
- Enhanced Materials: Innovations in materials can lead to more efficient and durable gear systems, which are critically needed in high-demand applications.
- Digital Design and Simulation: Utilizing simulation software could streamline the design process, allowing for more complex and optimized gear systems.
- Sustainable Practices: Research into eco-friendly manufacturing methods for gear production may become increasingly important as industries move towards sustainability.
By deepening the understanding of these areas, researchers and engineers can improve existing technologies and develop new solutions that enhance the functionality and efficiency of mechanical systems.