Mastering the Calibration of Fanuc Robots
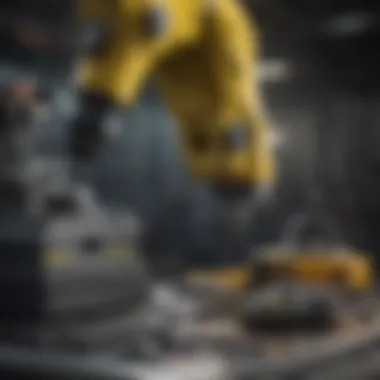
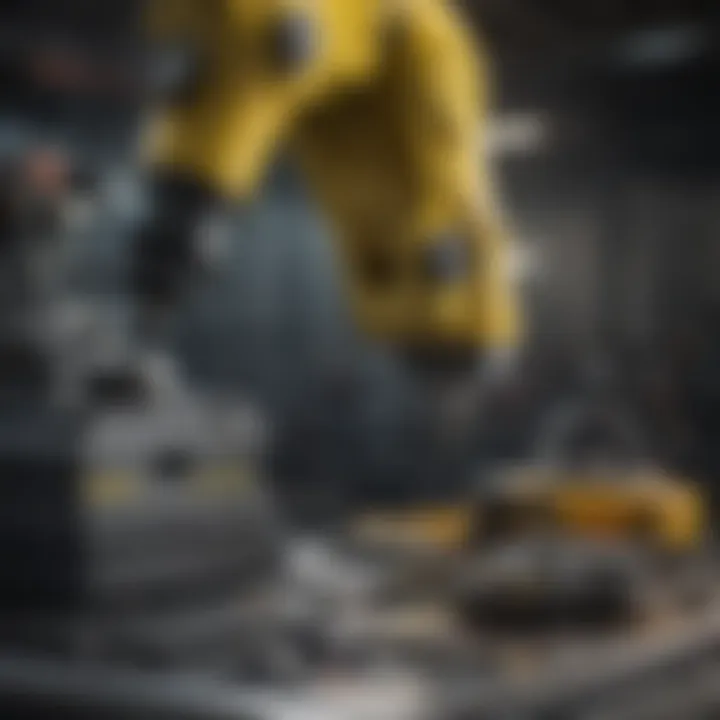
Intro
Calibrating Fanuc robots is an essential practice for ensuring their optimal performance in various industrial applications. This guide focuses on the calibration process, exploring every facet required to achieve precision and reliability while operating these advanced machines. In the following sections, we'll outline the key concepts involved in calibrating Fanuc robots, the methodologies that govern this process, and the challenges that may arise.
Understanding calibration is crucial. It is not merely a function of adjusting settings or aligning components, but a refined procedure that impacts the overall productivity of robotic applications. Each step must be carefully executed, keeping in mind the specific requirements of the task at hand. Next, we delve into the Key Concepts that form the backbone of this calibration process.
Intro to Fanuc Robots
Understanding Fanuc robots is crucial for anyone involved in industrial automation. These robots provide a quality solution for various tasks, including assembly, welding, and material handling. By recognizing the significance of Fanuc robots in the manufacturing landscape, users can leverage their capabilities effectively. This section will highlight the essentials of these machines, offering insights into the role they play within modern industry.
Overview of Robotics in Industry
Robotics has transformed the face of manufacturing and production. Automation has increased efficiency and productivity across various sectors. In many cases, robots perform tasks that are repetitive or hazardous to humans. The integration of robotics facilitates a faster production cycle while maintaining high standards of quality. Since 2020, the shift towards automation continues to grow strongly, driven by the need for precise and reliable production methods.
Robots enhance flexibility in manufacturing workflows. Industries can quickly adapt to changing demands or new products with reprogrammed robots. Moreover, the use of robots reduces labor costs over time. The investment in robotic technology sees a favorable return, especially for high-volume production.
"Robots can work 24/7 without breaks, leading to significant cost savings and increased output."
Specifics of Fanuc Robotics
Fanuc stands as a leader in robotic solutions known for their advanced technologies and innovations. Their offerings range from simple articulated robots to complex robotic systems with multiple configurations. Fanuc robots are recognized for their reliability, speed, and precision.
Some key features of Fanuc robots include:
- High payload capabilities: Fanuc robots can handle a broad range of weights, allowing for applications in heavy industries.
- Flexibility: The modular design enables customization for specific tasks.
- User-friendly programming: Fanuc uses intuitive interfaces, making it easier for operators to program and control the robots.
- Support and Resources: Fanuc provides extensive documentation and customer support, helping users troubleshoot and optimize their robotic systems.
In summary, the knowledge of Fanuc robots is vital. Their deployment leads to enhanced productivity and a competitive edge in manufacturing. Understanding their capabilities allows users to maximize the use of these robots, ensuring they serve their intended applications effectively.
The Importance of Calibration
Calibration is a crucial aspect of operating Fanuc robots effectively. It serves as the foundation for ensuring that the robots perform tasks with precision and repeatability. Without proper calibration, the robots may not function as intended, leading to unintended consequences such as product defects or operational inefficiencies.
Defining Calibration
Calibration can be defined as the process of adjusting the precision of a device. In the context of Fanuc robots, it involves setting the parameters and ensuring the accuracy of motion and operations. This process takes into account various factors such as the physical environment, the tools used, and the expectations of the tasks to be performed.
In practice, calibration involves not only verifying that the robot's mechanical components are functioning as needed, but also ensuring that the robot's software aligns with its physical capabilities. This dual focus on both hardware and software is what makes calibration particularly important for optimizing performance. Regular calibration checks can prevent drift in accuracy that might occur over time due to wear and tear or changes in operating conditions.
Impact on Performance
The impact of calibration on performance can't be overstated. When calibration is performed correctly, several benefits are observed:
- Increased Accuracy: Robots operate with enhanced precision, which is essential in applications requiring tight tolerances.
- Higher Efficiency: Calibrated robots can perform tasks faster without errors, leading to increased productivity.
- Minimized Downtime: Regular calibration can prevent breakdowns caused by misaligned parts or uncalibrated settings, thus reducing operational interruptions.
Failing to calibrate frequently can lead to compounded errors. Over time, even a small deviation from the desired parameters can result in significant discrepancies in output. As such, it is advisable to implement a routine calibration schedule, keeping in mind that various factors, including changes in tooling or environmental shifts, may necessitate more frequent checks.
"A robot's performance is only as reliable as its calibration. It is the difference between optimal function and operational failure."
Pre-Calibrating Considerations
Calibration is a crucial process for optimizing the performance of Fanuc robots. Before diving into the calibration tasks, certain pre-calibrating considerations must be addressed. These factors can greatly influence the effectiveness of the calibration process and the eventual performance of the robot. By focusing on the robot setup and ensuring access to necessary tools, users can avoid common pitfalls and enhance the precision of the calibration.
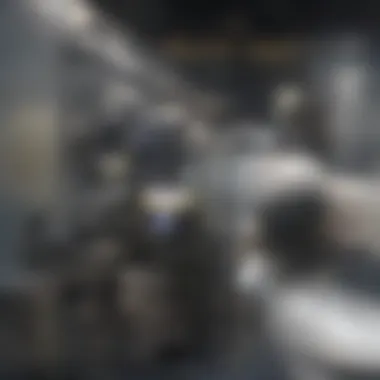
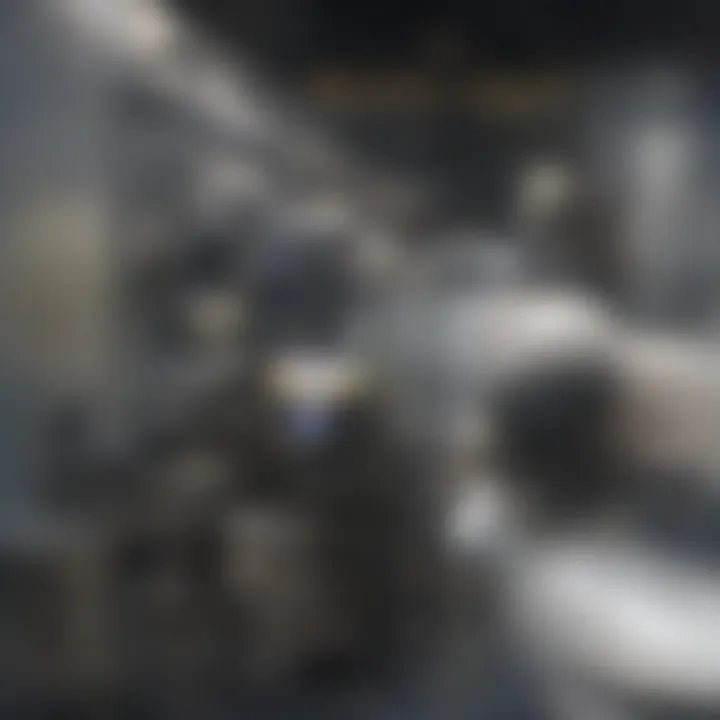
Assessing the robot setup is important as it ensures all components are correctly positioned and functioning. A well-prepared workspace helps in identifying potential issues that could arise during calibration. This phase can prevent time-consuming errors later in the process. Evaluating the current installation also aids in confirming that the robot's environment complies with safety protocols, thus ensuring the overall efficiency of the operations.
Identifying necessary tools is another vital pre-calibration step. The right tools can facilitate the calibration process and produce more reliable results. Utilizing calibration software, measuring instruments, and safety equipment each plays a significant role in the efficiency and safety of the entire calibration procedure.
Thus, taking the time to properly assess these pre-calibrating considerations can lead to smoother operations, greater accuracy, and ultimately, improved outcomes in robotic performance.
Assessing Robot Setup
Assessing the setup of the robot involves ensuring its physical configuration aligns with operational requirements. This process can include checking the base stability, ensuring that joint limits are appropriately set, and confirming connectivity to power sources and control systems. An adequately set up robot is less prone to errors during calibration. Any misalignment or unstable connection can lead to significant disruptions, making this step critical.
Identifying Necessary Tools
Identifying the tools required for calibration can streamline the process and ensure quality outcomes.
Calibration Software
Calibration software is the backbone of the calibration process. This type of software allows for real-time monitoring and control of the robot's movements. One key characteristic of robust calibration software is its user-friendly interface. This feature enables easy navigation, which is particularly beneficial for professionals less experienced with robotic systems. An example is Fanuc's RoboGuide, which not only provides simulation capabilities but also facilitates a smooth calibration workflow.
However, users must be aware of potential limitations regarding software compatibility with older robot models.
Measuring Instruments
Measuring instruments are essential for precision in calibration. These tools provide quantitative feedback necessary to achieve desired positions and movements. Commonly used measuring instruments include laser distance meters and precision gauges. The key characteristic of such instruments is their ability to deliver high accuracy. One advantage of laser meters is their non-contact measurement method, which minimizes the risk of interfering with the robot's operation. Nevertheless, their reliance on line-of-sight can be a disadvantage in certain settings.
Safety Equipment
Safety equipment cannot be overlooked when preparing for calibration. Using proper safety gear protects the personnel involved from accidents. Key pieces of safety equipment include safety goggles, gloves, and protective barriers. This equipment is critical in environments where the robot operates at high speeds or carries heavy loads. A unique feature of modern safety equipment is integration with sensor technology, which can trigger alerts if unsafe conditions arise. However, acquiring high-quality safety gear may involve higher costs.
Taking these pre-calibrating considerations into account sets the stage for a successful calibration process, ultimately enabling Fanuc robots to function at their fullest potential.
Calibration Procedures
Calibration procedures are a fundamental aspect of maintaining and optimizing the performance of Fanuc robots. Proper calibration ensures that a robot operates within its specified limits, enhancing accuracy and efficiency in various applications. This section will cover three critical phases of calibration: initial assessment, executing motion calibration, and fine-tuning end-effector position. Each of these phases plays a significant role in achieving precise results.
Initial Assessment
Before performing any calibration task, a thorough initial assessment is crucial. This involves evaluating the current state of the robot and understanding its operational environment. Factors to consider during this assessment include:
- Physical Condition: Check for any physical damage to the robot, such as bent arms or worn-out joints. Any such anomalies can significantly affect performance.
- Software Status: Ensure that the latest software version is installed. Outdated software may lead to inconsistencies in calibration.
- Environmental Factors: Temperature and humidity can influence the calibration process. Understanding the conditions where the robot operates will help in making necessary adjustments.
- Historical Data: Gather past performance metrics if available. This can provide valuable insights into the robot’s calibration history and any recurring issues.
Collecting this information lays the foundation for a successful calibration procedure. It helps to identify specific areas that require attention and sets realistic expectations for the calibration outcomes.
Executing Motion Calibration
Once the initial assessment is complete, the next step is executing motion calibration. This step involves adjusting the robot’s movements to ensure they align with programmed paths and tasks. It typically includes:
- Joint Calibration: Adjust each joint to their specified positions. This may require using tools such as calibration software and measuring instruments to verify the accuracy of each move.
- Path Verification: Run the robot through its intended paths and verify its response. Analyzing deviations will help in identifying underlying issues.
- Speed Adjustments: The speed at which a robot moves can impact its calibration. Consider adjusting speed settings based on the specific application requirements.
By executing motion calibration diligently, you ensure that the robot can perform tasks with precision. This is especially critical for applications requiring tight tolerances.
Fine-Tuning End-Effector Position
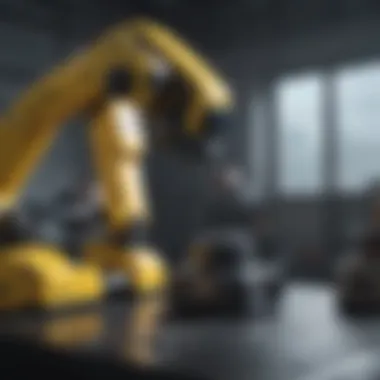
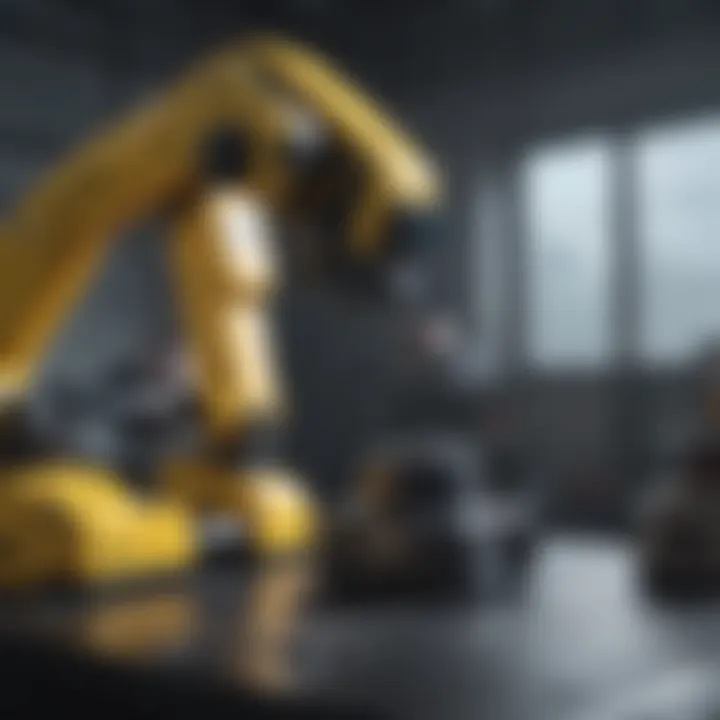
The final phase of the calibration procedure is fine-tuning the end-effector position. This step is essential, as the end-effector is the part of the robot that interacts with the external environment. Achieving accurate positioning can prevent errors in tasks such as assembly, picking, or welding. The key considerations include:
- Workpiece Alignment: Validate that the end-effector can access the targeted workpiece accurately. This may involve adjusting the parameters until the desired alignment is achieved.
- Testing Repetitions: Conduct multiple tests to ensure consistency in the end-effector’s positioning. Repeatability is crucial for maintaining quality in automated tasks.
- Feedback Systems: Utilize sensors to provide real-time feedback during this phase. This data can guide further adjustments as necessary.
Fine-tuning the end-effector ensures that the robot can operate effectively within its specified environment. Accuracy in this stage directly correlates with the robot's ability to perform designated tasks successfully.
Calibration is not a one-time task; it is an ongoing process to ensure optimal performance and precision.
This concludes the calibration procedures section. Following these steps not only enhances the overall functionality of Fanuc robots but also contributes significantly to the longevity and reliability of the robotic systems.
Advanced Calibration Techniques
In the constantly evolving field of robotics, advanced calibration techniques play a crucial role in enhancing the precision and efficiency of Fanuc robots. As industries increasingly rely on automation, understanding these methodologies is necessary for improving operational capabilities and achieving high-quality outputs. Advanced techniques are not just about ensuring functionalities; they help maintain a long-term competitive edge.
Using Isochronous Control
Isochronous control is an advanced technique that ensures precise timing in controlling movements of the robot. This method synchronizes various axes' actions within the robot, which is vital for applications where timing and speed are critical. By utilizing isochronous control, users can achieve smoother operations and reduced cycle times. With better timing, the robot's motions become more predictable.
This technique incorporates high-speed communication protocols, like CANopen or Ethernet, providing real-time data transmission. Optimal performance entails continuous monitoring and adjustments based on feedback. This control also allows seamless integration with other machinery, making it advantageous in complex environments.
To implement isochronous control effectively, consider the following factors:
- System Compatibility: Ensure that the robot and related systems support isochronous communication.
- Software Configuration: Properly set up the control software to recognize and execute commands accurately.
- Regular Updates: Keep software updated to access the latest functionalities and improvements.
"Advanced techniques like isochronous control are essential for optimizing the performance of Fanuc robots, particularly in high-speed environments."
Embracing Artificial Intelligence
Artificial Intelligence (AI) represents a transformative approach in robotic calibration, allowing for more intuitive and adaptive behaviors. AI technologies can learn from different processes and respond to varying conditions, thereby fine-tuning operational parameters dynamically.
One significant benefit of embracing AI in calibration is its ability to analyze large datasets quickly. This data-driven approach enables precise adjustments, ensuring robots consistently meet performance standards. Moreover, AI can predict wear and tear, allowing for proactive maintenance that minimizes downtime.
When integrating AI, consider:
- Learning Algorithms: Implement machine learning algorithms that can automatically adjust calibration based on historical data.
- Real-Time Data Analysis: Utilize sensors and data collection methods that feed information to AI systems for immediate adjustments.
- User Training: Ensure that users understand AI tools' functionalities to maximize the benefits of these innovations.
Troubleshooting Calibration Issues
Calibration issues can significantly affect the functionality of Fanuc robots. Identifying and resolving these problems not only ensures optimal performance but also prevents costly downtime in manufacturing processes. Addressing calibration issues promptly minimizes disruptions and preserves the efficiency of operations. This section discusses common errors and the significance of knowing when to seek professional assistance.
Common Errors and Solutions
Mistakes during the calibration process can occur due to various factors. Understanding these errors is the first step in troubleshooting. Here are some of the prevalent errors encountered in Fanuc robot calibration:
- Misalignment: This happens when the robot's reference points are not accurately set. It leads to positioning errors. The solution is to carefully review the setup and re-calibrate the reference points.
- Inaccurate Tool Parameters: Incorrect values of tool dimensions can distort the calibration. Always ensure the tool parameters match the actual tools being used.
- Software Configuration Errors: Problems in the calibration software can lead to incorrect commands being sent to the robot. Regularly update the software and verify settings against the manufacturer’s specifications.
- Communication Failures: If the robot fails to communicate with the controller, calibration cannot proceed. Check all connections and replace faulty cables if necessary.
Each of these errors requires careful analysis and a systematic approach to resolution.
When to Seek Professional Help
Even with the best practices in place, there may be situations where troubleshooting goes beyond basic checks. Recognizing when to call for professional help can save time and resources. Consider contacting a specialist in the following scenarios:
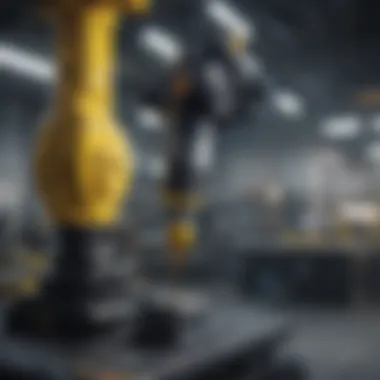
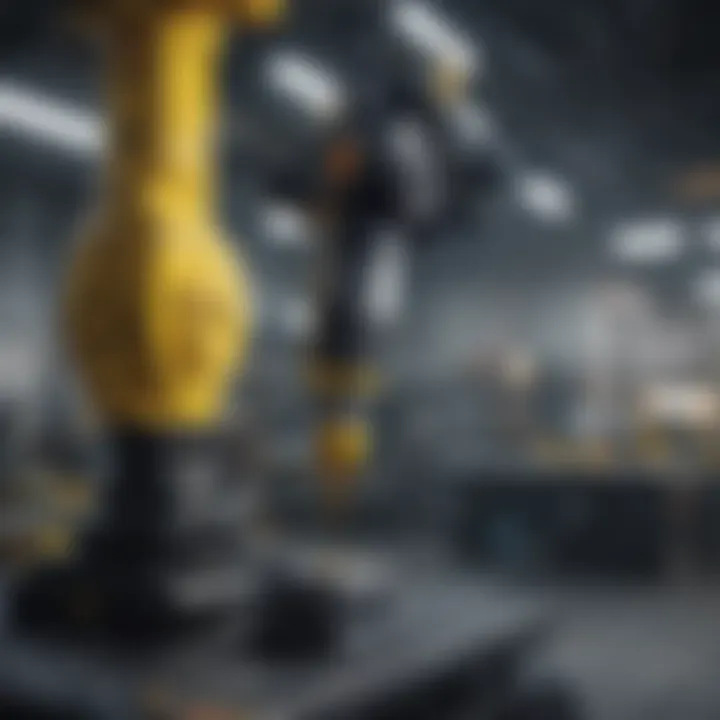
- Persistent Errors: If calibration issues continue after several attempts to correct them, it is advisable to seek help. Deeper issues may require advanced diagnostic tools.
- Lack of Expertise: If your team lacks experience with specific calibration procedures or Fanuc systems, it can lead to further complications. Professionals can ensure that calibration processes are conducted efficiently.
- Safety Concerns: If calibration poses any safety risks, especially when working with heavy machinery or complex systems, consultation with an expert is essential. Safety should not be compromised.
- System Upgrades: When introducing new equipment or transitioning to newer calibration technology, professional guidance can streamline the process and minimize errors.
Expert insight can often enhance the overall reliability of the calibration effort, reducing the potential for future issues.
The role of troubleshooting in the calibration process cannot be underestimated. By effectively identifying and addressing common errors, and knowing when to consult professionals, operators can greatly improve the efficiency and reliability of Fanuc robots.
Maintaining Calibration Integrity
Maintaining calibration integrity is crucial for ensuring the long-term performance of Fanuc robots. As industrial environments can be dynamic and often involve variations in factors such as temperature, load, and usage, regular maintenance becomes essential. Preserving the integrity of calibration helps in minimizing errors and optimizing operational efficiency.
One of the key aspects of calibration integrity lies in the regular checks that are performed to verify that the systems remain within acceptable tolerances. Regular calibration checks help identify potential drifts or deviations early on. This proactive approach allows for adjustments before significant issues arise, ultimately leading to reduced downtime and enhanced reliability in robotic operations.
Additionally, maintaining calibration integrity fosters trust in automated processes, particularly in industries where precision is paramount, such as automotive or aerospace manufacturing. The integrity of calibration not only serves as a technical requirement but also as a commitment to quality, which can enhance a company’s reputation in the market.
Regular Calibration Checks
Regular calibration checks are a systematic way of ensuring that Fanuc robots remain aligned with their performance standards. A well-established routine for checking calibration can help in identifying any inconsistencies that may occur over time due to wear and tear or environmental factors.
The frequency of calibration checks can vary depending on several factors, including:
- Usage intensity of the robot
- Environmental conditions
- Specific tasks that the robot performs
Setting up a schedule for these checks can include:
- Quarterly evaluations for standard usage
- Monthly assessments in high-demand environments
- Immediate recalibration after significant mechanical changes
Documenting results from these checks is equally important. Each assessment should be recorded, comparing current performance metrics against established benchmarks. This record can aid in trending issues that might need further attention or adjustment.
Documenting Calibration Results
Documenting calibration results is essential for transparency and accountability within an organization. A comprehensive record of each calibration session not only serves as a reference point for future checks, but it also complies with industry regulations that may necessitate rigorous documentation of equipment performance.
Key elements of documenting calibration results include:
- Date and time of calibration
- Personnel involved in the calibration process
- Specific tools used
- Results of the calibration tests
- Any adjustments made during the process
These records can be housed in a centralized data management system or maintained manually. Regular audits of these documents can help organizations identify patterns that may indicate issues requiring attention.
The maintenance of thorough documentation can also boost the organization's ability to conduct effective troubleshooting. By referring to previous calibration results, technicians can pinpoint inconsistencies and devise more informed strategies for resolving any emerging issues.
Regular documentation can streamline the troubleshooting process, ensuring efficiency in maintaining equipment integrity and performance.
Epilogue
The calibration of Fanuc robots is a crucial aspect of their functionality and effectiveness. It ensures that these machines operate at peak performance, which ultimately translates into better outcomes for industrial applications. Proper calibration isn't just a one-time procedure; it requires ongoing attention to maintain accuracy over time.
Recap of Key Points
In this guide, several key elements about calibrating Fanuc robots have been discussed:
- Importance of Calibration: Calibration is essential for improving the precision of robotic operations. It allows the robot to perform tasks with increased accuracy, reducing errors that could lead to costly downtime or waste.
- Calibration Procedures: Detailed procedures including initial assessments, motion calibration, and fine-tuning of end-effectors have been outlined to help users follow a systematic approach.
- Tools Required: An overview of necessary tools such as calibration software, measuring instruments, and safety equipment has been provided. These tools enable accurate calibration and help mitigate risks.
- Troubleshooting and Maintenance: Practical tips for identifying common issues during calibration and regular checks to maintain calibration integrity are also discussed.
Future of Robot Calibration
Looking ahead, as technology evolves, the future of robot calibration is likely to grow more sophisticated. Innovations in artificial intelligence and machine learning may simplify calibration processes significantly.
- Dynamic Calibration Systems: Future systems may allow for real-time adjustments based on feedback, enabling robots to self-calibrate, thereby increasing operational efficiency.
- Advanced Tools: The development of smarter software solutions can streamline the calibration process, making it accessible to users without extensive technical backgrounds.
- Integration of IoT: Internet of Things technologies could enhance data collection, allowing for more precise adjustments and proactive maintenance.
In summary, the landscape of robot calibration is poised for dramatic change, promising to enhance effectiveness and reduce the complexity of maintaining Fanuc robots.