Exploring FFF 3D Printing: A Comprehensive Analysis
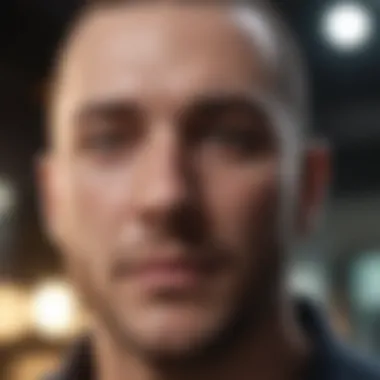
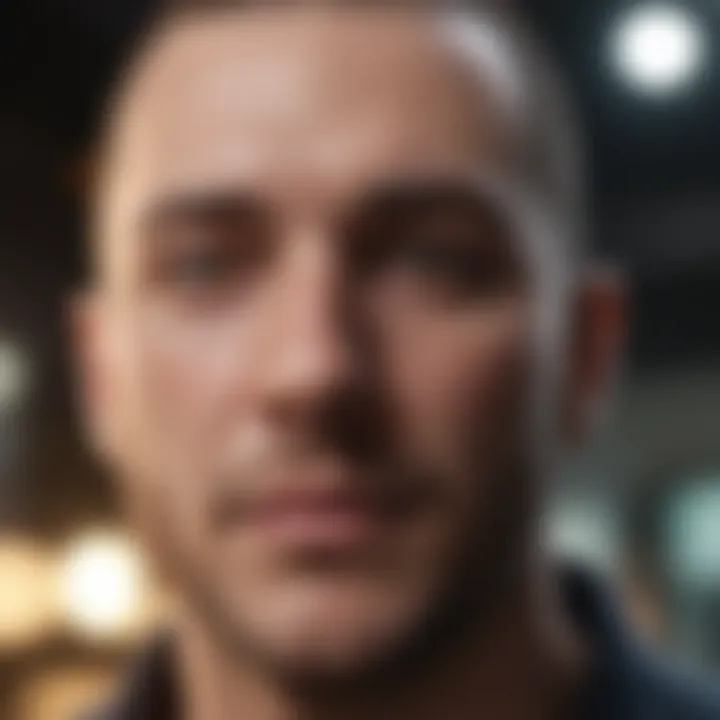
Intro
FFF 3D printing has emerged as a significant force in modern manufacturing. This technology allows for cost-effective and efficient production methods across a multitude of industries. Understanding the mechanics behind Fused Filament Fabrication is essential for grasping its wide-ranging applications and future potential.
In this article, we will explore various aspects of FFF 3D printing. We will define key terms, discuss related concepts, and examine the innovative materials that contribute to its functionality. Further, we will analyze the future directions of FFF 3D printing, identifying existing gaps and suggesting areas for further research. Through this exploration, we aim to deliver a well-rounded understanding suitable for students, researchers, educators, and professionals alike.
Preamble to FFF 3D Printing
FFF 3D printing, or Fused Filament Fabrication, is an important technology transforming how products are designed and manufactured. This process has significant implications for industries and individual users alike. The ability to create complex geometries and prototypes at a relatively low cost makes FFF an attractive option. In this section, we delve into its definition, basic principles, and the historical context that led to its development.
Definition and Basics
Fused Filament Fabrication is a form of additive manufacturing. In simple terms, it involves melting a thermoplastic filament, extruding it through a nozzle, and depositing it layer by layer onto a build platform. The process begins with a digital design, usually in the form of a CAD file. The material is heated until it reaches a semi-liquid state, allowing it to flow and bond with the previous layer.
The standard materials used in FFF include various thermoplastics, which are widely available and relatively inexpensive. This accessibility contributes to its growing popularity. The layers fuse together as they cool, creating a solid object. This method allows for more intricate designs compared to traditional subtractive manufacturing methods.
History and Development
The origins of FFF printing can be traced back to the late 1980s when Scott Crump, co-founder of Stratasys, developed a method known as Fused Deposition Modeling (FDM). This early technology laid the groundwork for subsequent advancements in 3D printing. During the following decades, the technology evolved, making devices smaller, more affordable, and accessible to a broader audience.
In 2005, FDM became obtainable for individual users when the RepRap project emerged. This initiative aimed to create a self-replicating 3D printer that would allow anyone to make their own machines. This marked a shift in the landscape of 3D printing, leading to the rise of numerous desktop printers and the FFF technology we recognize today.
Overall, understanding the definition and historical context of FFF 3D printing is crucial. It highlights not only the versatility of the technology but also the consistent innovations driving the field forward. This foundation sets the stage for the in-depth exploration of materials used, applications, advantages, challenges, and future directions that follow in this article.
Understanding the Technology
Understanding the technology behind FFF 3D printing is crucial for anyone involved in or studying this field. It allows for a better grasp of how various components work together to create complex objects from digital designs. The mechanism, as well as the phases of the print process, are essential for optimizing performance and achieving high-quality outputs. Moreover, knowing the technological intricacies can lead to innovative uses and improvements in workflows, making the technology even more relevant across different sectors.
Mechanism of FFF Printing
The FFF printing mechanism employs a relatively straightforward approach. At its heart, the printer uses a thermoplastic filament, which is melted and then extruded through a nozzle. The key components that make this process effective include:
- Hot End: This is where the filament is heated to a specified temperature. Precision in heating ensures that the material reaches the ideal viscosity for extrusion without degrading.
- Nozzle: The melted filament is pushed through a nozzle, which determines the width of the filament strand and, consequently, the level of detail in the print.
- Build Platform: This is the surface where the layers are deposited. It often requires a specific level of adhesion to keep the object in place during printing.
The movement of the extruder is controlled carefully, laying down the material layer by layer. Each layer is allowed to cool before the next is added. This layering process allows the creation of complex geometries that would be difficult to achieve through traditional manufacturing methods.
Different Phases of the Process
Understanding the different phases involved in FFF printing can make a significant difference in the results. Each phase has its considerations which can influence the overall quality of the output. The phases are:
- Preparation: This phase includes designing the 3D model using CAD software. It also involves slicing the model into layers, which is a critical step for determining print settings like layer height, infill density, and print speed. The slicer software converts the model into G-code, the language that the printer understands.
- Printing: During this phase, the printer follows the G-code instructions to produce the object. The printer moves the extruder along the required paths, depositing the filament. Consistent monitoring is essential to ensure that any issues, such as filament jams or misalignment, are addressed promptly.
- Cooling and Post-Processing: After the printing is complete, the object must cool down to solidify properly. Some users may choose to perform additional post-processing steps, such as sanding or painting, to enhance the surface finish and functionality of the printed piece.
Understanding these phases can lead to better management of the printing process, minimizing errors and improving final results.
Overall, being aware of the technology not only enhances the understanding of the printing process but also helps in making informed decisions regarding materials, designs, and applications.
Materials Used in FFF 3D Printing
The use of materials in FFF 3D printing plays a crucial role in the overall effectiveness and versatility of this technology. FFF enables the creation of complex geometries and prototypes, which heavily relies on the characteristics of the filaments used. The choice of material affects not only the mechanical properties of the printed objects but also their durability and suitability for specific applications. Therefore, understanding the types of filaments and their properties is essential for optimizing FFF printing processes.
Types of Filaments
PLA
PLA, or Polylactic Acid, is one of the most widely used filaments in FFF 3D printing. It is derived from renewable resources like cornstarch. Its key characteristic is its ease of use, making it a popular choice for beginners and professionals alike. PLA is known for its low warping and excellent adhesion properties, which enhances the printing experience.
This filament is also biodegradable, adding an environmental benefit. However, its lower temperature resistance compared to other materials limits its use in high-temperature applications. Nonetheless, PLA is a preferred material for educational purposes and prototyping, as it offers good detail and is available in many colors.
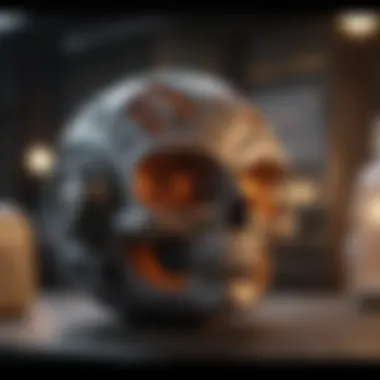
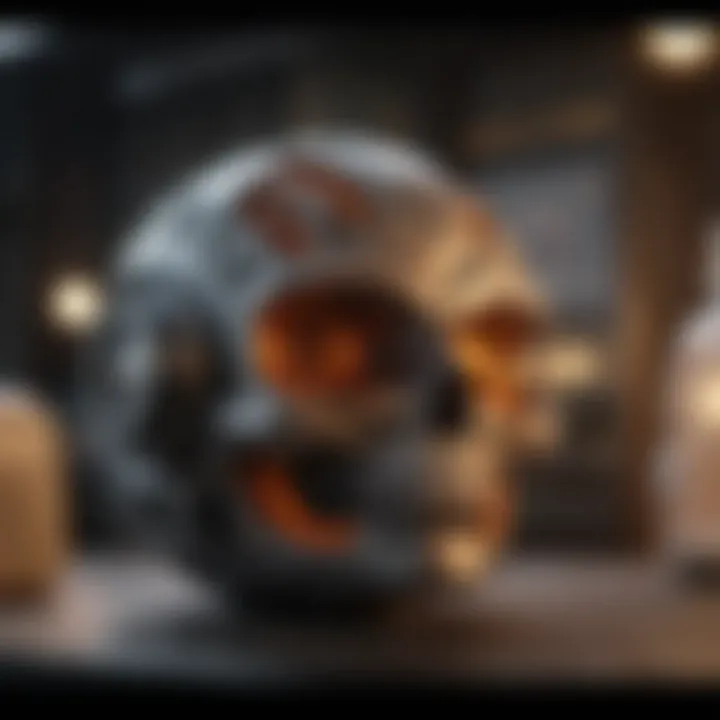
ABS
ABS, or Acrylonitrile Butadiene Styrene, is another popular filament known for its strength and durability. This material is often used for parts that need to withstand impact, making it an excellent choice for functional prototypes and end-use products. ABS has a higher temperature resistance than PLA, allowing for a broader range of applications.
However, one unique feature is its tendency to warp during printing, requiring a heated bed and proper handling. The strong fumes from ABS can also be a concern, so adequate ventilation is advised. Despite these disadvantages, its superior mechanical properties make ABS a staple in industries like automotive and aerospace.
PETG
PETG, which stands for Polyethylene Terephthalate Glycol, combines some of the best features of both ABS and PLA. Its key characteristic is excellent layer adhesion, resulting in strong and durable prints. PETG is also known for being easier to print than ABS due to its lower warping issues.
This filament has good chemical resistance and can withstand higher temperatures than PLA. However, it can be stringy and may need tweaks in printing settings to avoid oozing. The versatility of PETG makes it suitable for both prototyping and finalized parts, especially in industrial applications.
Nylon
Nylon is a tough filament that exhibits high flexibility and strength. Its key characteristic is its durability, making it ideal for parts requiring high impact resistance. The unique feature of nylon is its ability to handle stress and strain, which makes it suitable for functional prototypes and replacement parts.
However, nylon absorbs moisture readily, which can lead to issues during printing if not stored correctly. Additional requirements, such as a heated bed and specific nozzle sizes, may be necessary. Nonetheless, the advantageous properties of nylon make it a valuable material for various applications, notably in the automotive and specialized manufacturing sectors.
Material Properties
Strength
Strength is a critical property of materials used in FFF 3D printing. It influences the durability and performance of printed parts in various environments. PLA, while offering good rigidity, lacks the overall strength compared to ABS or nylon. This is crucial for applications where stress resistance is necessary.
In contrast, nylon offers the best strength-to-weight ratio, providing usage in demanding applications. Understanding strength characteristics assists designers in selecting the right filament based on project needs.
Flexibility
Flexibility refers to a material's ability to bend or compress without breaking. This property can signify how adaptable a printed part is to operational conditions. PLA is rigid, which limits its flexibility. However, nylon demonstrates excellent flexibility, enabling it to be used in applications requiring resilience against deformation or breaking.
This variability in flexibility is essential for engineers and designers as it dictates how a product interacts with its environment.
Temperature Resistance
Temperature resistance plays a vital role in determining a material's applicability. It refers to how well a material can endure high temperatures without deforming. PLA typically has lower temperature resistance, while ABS offers a more robust profile that can withstand more thermal stress.
Nylon excels in high-temperature environments, making it suitable for parts exposed to heat. Each filament possess unique thermal properties, and selecting the right material based on temperature requirements is essential for ensuring functionality.
In summary, the selection of materials used in FFF 3D printing significantly influences both the functionality and the overall utility of the printed products. By understanding their properties, designers can achieve optimal outcomes for various applications.
Applications of FFF 3D Printing
The applications of FFF 3D printing represent a critical area of exploration in this article. This technology has extended beyond mere prototyping; it is now fundamentally reshaping various industries. Key aspects, such as cost-effectiveness, accessibility, and design freedom, mark its relevance. FFF 3D printing delivers practical solutions that promote innovation, reduce material waste, and improve production speeds.
Whether in aviation, healthcare, or education, understanding these applications will shed light on the broader implications for manufacturing and technological advancement.
Industrial Applications
In the realm of industry, FFF 3D printing finds robust applications that transform traditional practices. From aerospace to automotive, companies are adopting this technology to streamline their workflows and enhance product quality.
Aerospace
Aerospace stands out as a significant beneficiary of FFF 3D printing. This industry is characterized by its need for precision and reliability, where even the smallest component can impact safety and performance. FFF methods enable the creation of complex geometries that are often impossible to achieve using conventional manufacturing processes. These custom parts can also be produced in smaller quantities, reducing inventory costs and speeding up the time to market. However, the downside is that not all materials meet the necessary regulatory compliances in aerospace applications.
Automotive
Similarly, the automotive sector leverages FFF 3D printing for creating prototypes and functional parts. This industry thrives on rapid innovation as consumer demands evolve continuously. One key characteristic is the ability to quickly iterate designs. Manufacturers can test new ideas without the need for expensive tooling. Nonetheless, while FFF allows for more flexible production methods, the strength and durability of parts may still be a concern for certain applications within the auto industry.
Manufacturing
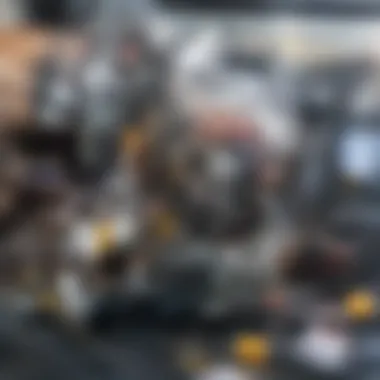
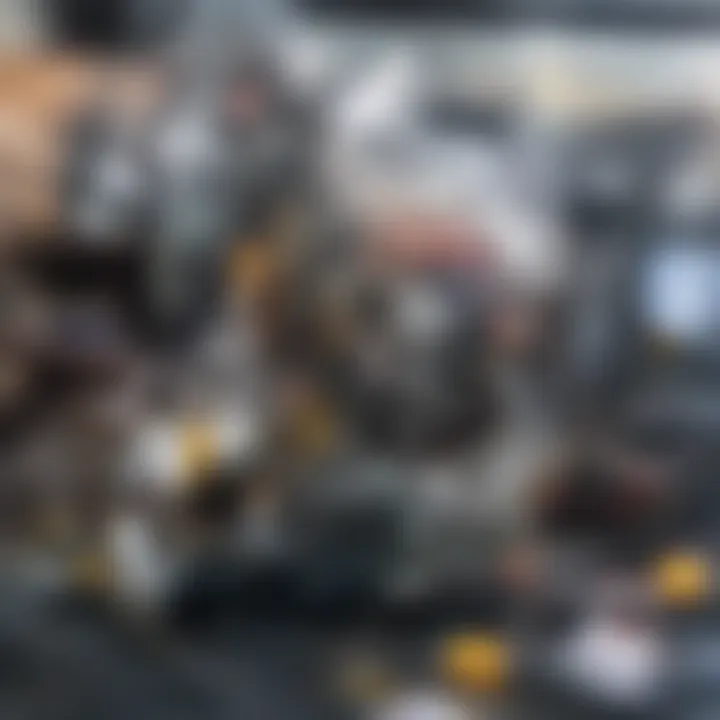
In the broader manufacturing field, FFF 3D printing excels by enabling customization at scale. The ability to produce on-demand reduces the need for large warehouses full of stock. This just-in-time manufacturing approach minimizes waste and optimizes resources. Yet, companies must consider the limitations of print speed compared to traditional methods to fully capitalize on these benefits.
Medical Applications
The medical sector is another domain where FFF 3D printing yields transformative possibilities. It encourages personalized solutions that enhance patient care and operational efficiency. The individual-centric approach holds significant promise.
Prototyping
Medical prototyping through FFF allows rapid iteration of device designs. The process accelerates the development cycle from concept to clinical trials. Designers can use patient data to create tailored prototypes, making it a popular choice in the medical field. However, while this method boosts productivity, it often requires further validation for regulatory compliance.
Implants
The use of FFF for creating implants represents an important leap forward in surgical practices. Custom implants can be printed to fit the unique anatomy of individual patients, leading to improved surgical outcomes. The biocompatibility of materials used is a crucial feature as it ensures safety during implantation. The significant challenge lies in ensuring material strength and durability in long-term use.
Patient-Specific Models
Patient-specific models produced through FFF offer a precise understanding of complex cases before surgery. These models assist surgeons in planning procedures effectively. The advantage lies in enhancing preoperative preparedness, potentially improving patient outcomes. However, considerations about production time and material costs remain essential for widespread adoption.
Educational Uses
In educational environments, FFF 3D printing serves as an invaluable tool that fosters experiential learning, particularly in STEM fields. The ability to visualize concepts through physical models aids in understanding complex subjects.
STEM Education
In STEM education, FFF technology empowers students to engage in hands-on learning. By creating prototypes, learners can see theoretical ideas come to life. This approach enhances problem-solving skills and creativity. Still, potential limitations like equipment access and material costs can affect its implementation in various institutions.
Research Prototyping
Research prototyping using FFF allows academic and industry researchers to push boundaries in their fields. Quick production of hypothesis-driven prototypes supports innovation and experimentation. Importantly, this method encourages collaboration across disciplines. However, ensuring the accuracy and precision of printed models can be challenging, especially when fine details are critical to research outcomes.
In essence, the applications of FFF 3D printing are vast and varied, providing profound enhancements across sectors while also presenting challenges that must be addressed for optimal utilization.
Advantages of FFF 3D Printing
FFF 3D printing offers several significant advantages that make it attractive for various applications. Understanding these advantages is crucial for those considering this technology for industrial, medical, and educational purposes. The key benefits are primarily in two areas: cost-effectiveness and design flexibility. These elements not only enhance usability but also broaden the scope of what can be achieved through FFF printing.
Cost-Effectiveness
Cost is a primary concern in any manufacturing process. FFF 3D printing is often more affordable than traditional methods. The material costs for filaments like PLA or ABS are relatively low compared to metals or specialized fabrication supplies. This makes it an appealing choice for small businesses and startups. Additionally, reduced waste during the printing process contributes to overall savings. Unlike subtractive manufacturing, which removes material from a solid block, FFF printing builds objects layer by layer, minimizing waste.
Efficiency is another key factor. Production times can be shorter, especially for prototypes. Considering the ability to quickly adjust designs and print them without extensive re-tooling, the financial benefits can stack up significantly.
"Cost savings in FFF 3D printing can lead to broader innovation opportunities, allowing for more experimental designs without the risk of excessive expenditure."
Design Flexibility
FFF 3D printing provides a level of design flexibility that is hard to match. Designers can create complex geometries that were previously impossible or too costly to produce. The additive nature of the technology allows for intricate designs that support functional purposes, such as lightweight structures or integrated features. This is particularly valuable in industries like aerospace and automotive, where reducing weight is crucial, and design plays an essential role in performance.
Moreover, the ability to customize products according to specific needs is enhanced with FFF. One can easily change designs without modifying the entire production setup. This capability opens doors to personalized solutions, making it possible to develop products that are tailored to individual requirements. The combination of these factors makes FFF a compelling option for both prototyping and final product manufacturing.
In summary, the advantages of FFF 3D printing—cost-effectiveness and design flexibility—position it as a vital technology in modern manufacturing. These benefits support innovation and practical applications across numerous sectors.
Challenges in FFF 3D Printing
The journey of FFF 3D printing is not without its hurdles. As this technology advances, it faces various challenges that can affect its efficiency, quality, and overall acceptance. Recognizing these challenges is essential for anyone involved in research, industry, or education related to this field. Addressing these problems can lead to improved practices, better outcomes, and ongoing innovation in the application of FFF 3D printing.
Material Limitations
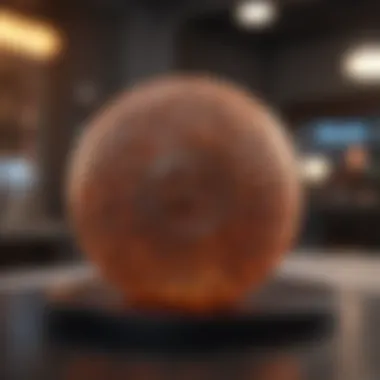
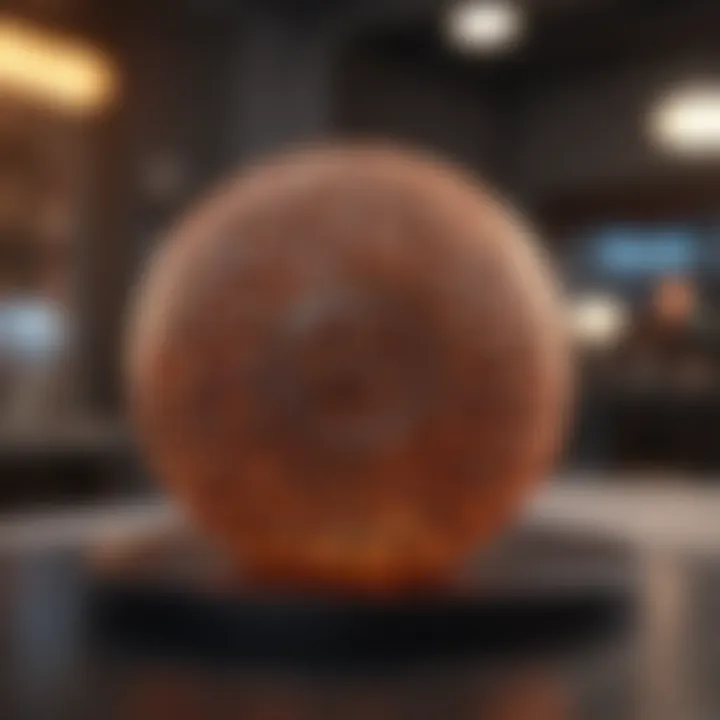
One of the foremost challenges in FFF 3D printing is material limitations. While there is a diverse range of filaments available, each material comes with its unique set of characteristics that may not always align with the desired application. For instance, polylactic acid (PLA) is easy to print and environmentally friendly, but it lacks the durability and heat resistance that other materials like acrylonitrile butadiene styrene (ABS) offer. This specificity can restrict designers and manufacturers in selecting the right material for their projects.
Additionally, some advanced materials require specialized printers or techniques which can be a barrier in implementing FFF 3D printing in certain environments. Companies may find it costly to upgrade equipment to keep pace with material innovations. Not all materials perform well under stress or temperature changes, which can affect the part's post-processing or long-term use. Even materials that are recognized for their strength, like nylon, can absorb moisture, changing their properties and printability.
The limitations in material capabilities often force users to compromise between performance, cost, and availability. The ongoing research and development in this area aim to discover and manufacture new composite materials that may alleviate some of these challenges.
Print Speed Constraints
The printing speed in FFF technology presents another significant challenge. Although FFF printers have improved significantly in speed, they still lag behind some traditional manufacturing processes. This slow printing speed can lead to longer lead times for production, which may not meet the demands of fast-paced industries.
Moreover, increasing the print speed can result in a decline in print quality. Faster speeds may lead to issues such as stringing, warping, or layer adhesion problems. This contradictory relationship between speed and quality can become a critical bottleneck, especially in industries where precision is vital.
Furthermore, the setup and calibration time for FFF printers contribute to the delay in the manufacturing process. Each material may require different settings, and improper configurations can lead to failed prints. Overall, these limitations necessitate careful planning and management, often impacting the production pipeline.
Future Directions in FFF 3D Printing
As FFF 3D printing continues to evolve, its future directions promise to reshape the landscape of manufacturing and prototyping. This section emphasizes the importance of understanding where the technology is headed. Innovations in this field will not only enhance production capabilities but also address existing challenges and leverage opportunities for sustainability. Key aspects such as technological advancements and sustainability considerations are crucial for researchers, educators, and industry professionals alike.
Technological Innovations
Technological innovations are pivotal in driving the growth and application range of FFF 3D printing.
Multi-Material Printing
Multi-material printing represents a significant advancement in the FFF 3D printing domain. This process allows for the simultaneous use of different materials during a single print job. The key characteristic of multi-material printing lies in its ability to combine contrasting properties in one object, such as stiffness and flexibility. This makes it a beneficial choice for creating complex models that require varied material properties.
A unique feature of multi-material printing is its capability to produce intricate geometries. By merging materials like PLA and TPU, for example, one can achieve a model with rigid structures in some areas and soft sections in others. However, implementation can be challenging. The precision required in aligning the different filaments can affect the final quality of the print, posing both advantages and disadvantages. While the potential for complex designs exists, users must consider the technical difficulties it introduces.
Improved Filament Types
Improved filament types are another area poised for growth in FFF 3D printing. Recent developments aim to enhance filament performance, addressing issues such as durability and environmental impact. Notably, high-strength composites and biodegradable options are gaining popularity.
The standout characteristic of improved filament types is their enhanced properties. Innovations like carbon fiber-infused filaments create stronger models suited for functional prototypes, while biodegradable alternatives like PLA offer a more environmentally friendly option. Such advancements make improved filament types a notable choice for industries focused on both performance and sustainability.
One unique feature of these improved filaments is their compatibility with various printers while often remaining easy to process. The advantages, including better mechanical properties and environmental considerations, must be weighed against potential limitations like cost or limited availability.
Sustainability Considerations
Sustainability is becoming an increasingly prominent topic in FFF 3D printing. As industries shift towards greener practices, evaluating the environmental impact of printing methods is crucial. This includes understanding the lifecycle of materials used and the possibility of recycling filaments after their intended use.
Furthermore, exploring the integration of renewable resources in filament production represents a forward-looking prospect. The adoption of sustainable practices can significantly influence the perception and acceptance of FFF 3D printing in various sectors, aligning it with broader industry goals for sustainability.
"The future of FFF 3D printing will not only be defined by technological advancements but also by our commitment to sustainability and responsible production practices."
End
The conclusion serves as a critical juncture in this exploration of FFF 3D printing, synthesizing the core elements discussed throughout the article. It reinforces the significance of understanding FFF technology in the context of its diverse applications and materials. Notably, FFF 3D printing is not just a method of creating objects; it represents a paradigm shift in manufacturing capabilities. Being cost-effective and versatile, it meets the needs of industries ranging from aerospace to education, making it an attractive option for many businesses.
Summary of Key Points
In reviewing the essential aspects, several key points emerge from the discussion:
- FFF 3D printing allows for a wide range of applications across industries. This includes prototyping and production in sectors like aerospace and medical fields.
- The types of materials utilized in FFF, such as PLA, ABS, PETG, and nylon, each offer unique properties, influencing the choice of filament depending on the application.
- Advantages including cost-effectiveness and design flexibility underscore the method's growing popularity.
- However, challenges remain, such as material limitations and print speed constraints, which researchers and practitioners must navigate.
- Future directions emphasize technological innovations and sustainability, highlighting the potential for progress in the field.
This summary encapsulates the breadth and depth of FFF 3D printing, illustrating its influence on modern manufacturing.
Implications for Future Research
Future research holds considerable potential in enhancing the effectiveness and sustainability of FFF 3D printing. Some potential areas for exploration include:
- Material Development: Investigating new filament materials that overcome existing limitations can open new avenues for applications. Biodegradable and recycled materials may also become significant factors in addressing environmental concerns.
- Process Optimization: Research aimed at improving print speeds and reducing errors can result in more efficient production methods. Optimizing the FFF printing process can lead to a broader acceptance in industrial applications.
- Integration of Smart Technologies: Incorporating elements such as artificial intelligence and machine learning into the FFF process presents opportunities for advancements in automation, precision, and design.
- Sustainability Practices: Developing methods that enhance the environmental responsibility of FFF printing will be crucial. Research into reducing waste and energy consumption aligns with global sustainability goals.
"The integration of advanced technologies into FFF 3D printing will shape its future with efficiency and eco-friendliness."
These research implications underscore the necessity for continued investigation and innovation within the realm of FFF 3D printing as it progresses and evolves.