Exploring Galvanised Conduit: Applications and Benefits
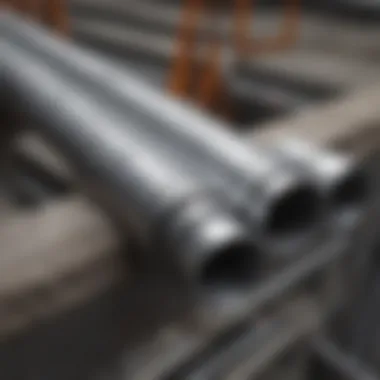
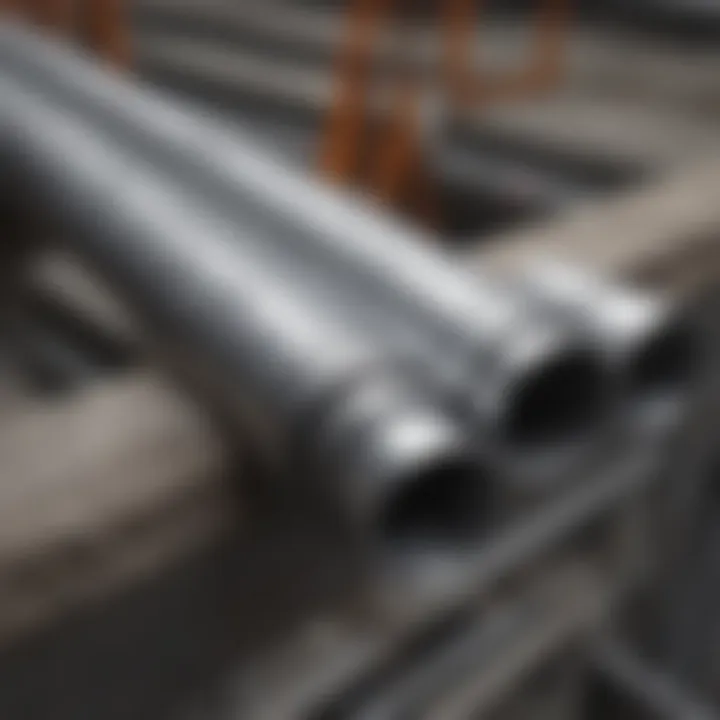
Intro
Galvanised conduit serves as an important component in a variety of electrical and construction applications. Understanding this material is essential for professionals and researchers in the field. This guide will delve into its properties, uses, and installation aspects.
Key Concepts
Definition of Primary Terms
Galvanised conduit is a type of metal tubing coated with zinc to protect against corrosion. It is commonly used to house and protect electrical wires. The galvanising process involves coating the base metal with zinc to enhance its durability. This property is crucial in outdoor and industrial settings where exposure to moisture and elements is frequent.
Related Concepts and Theories
The application of galvanised conduit is often associated with the broader subject of electrical safety and efficiency. Its use is grounded in standards set by various regulatory bodies, which emphasize the importance of protecting electrical systems from damage and potential hazards. Understanding the risks of corrosion is vital when considering any construction materials, especially those intended for electrical applications.
Applications of Galvanised Conduit
Galvanised conduit finds usage across various domains:
- Electrical Wiring Protection: It serves to protect wiring systems from physical damage and environmental factors.
- Institutional Buildings: Durable structures often prefer its use in wiring to ensure longevity and compliance with safety standards.
- Industrial Settings: Manufacturing plants regularly use this material due to its resilience in harsh conditions.
Benefits
The advantages of using galvanised conduit are several:
- Corrosion Resistance: The zinc coating enhances resistance, prolonging the lifespan of electrical installations.
- Durability: It can withstand heavy usage and impact, making it suitable for demanding environments.
- Cost-Effectiveness: While initial costs might be higher than other materials, its long-term value is significant, reducing replacement and maintenance costs.
Considerations
When selecting galvanised conduit, there are some factors to keep in mind:
- Weight: Its density can make installation more challenging, requiring appropriate tools and techniques.
- Compatibility: Ensure that it is compatible with other materials in your system to prevent issues like galvanic corrosion.
- Local Regulations: Familiarize yourself with local building codes and regulations that govern conduit installation to ensure compliance.
Installation and Maintenance
Proper installation of galvanised conduit is critical for safety and performance. Here are some key steps:
- Planning: Assess the environment to determine the route and type of conduit needed.
- Cutting and Joining: Use appropriate tools for precise cuts. Ensure connections are tight to prevent moisture ingress.
- Support and Securing: Ensure that the conduit is adequately supported to prevent sagging or stress on connections.
Regular maintenance is also necessary. Checking for signs of wear, damage, or loosening will ensure continued protection and functionality of the electrical system.
Future Directions
Gaps Identified in Current Research
There are still unresolved questions regarding the long-term effects of environmental factors on galvanised conduit systems. Research could explore areas such as:
- Corrosion Performance: Understanding how various environments impact coating effectiveness.
- Material Innovation: Exploring new materials that maintain durability while improving weight efficiency.
Suggestions for Further Studies
Future studies could focus on:
- Advanced Material Coatings: Investigating alternative coatings that may enhance performance further.
- Case Studies: In-depth analysis of specific installations to demonstrate best practices and challenges associated with galvanised conduit.
Galvanised conduit plays a crucial role in ensuring electrical safety. Its properties make it a vital choice for professionals in the field.
Preface to Galvanised Conduit
Galvanised conduit plays a crucial role in both electrical and construction sectors. Its design and material characteristics make it a preferred choice for housing wiring and protecting electrical systems. Understanding galvanised conduit is essential for industry professionals, researchers, and educators alike, as it forms the backbone of numerous projects where safety and durability are key.
The process of galvanisation involves coating steel or iron with a layer of zinc. This protective layer prevents rust and corrosion, enhancing the longevity of the conduit. Therefore, galvanised conduit is not only functional but also cost-effective in the long run. The brand reputation of materials in construction and electrical installations largely rests on their reliability. Here, galvanised conduit stands out due to its resilience against environmental factors.
Key Elements of Galvanised Conduit
When discussing the significance of galvanised conduit, the following elements should be highlighted:
- Corrosion Resistance: The zinc layer ensures that the interior and exterior of the conduit are protected against moisture and other corrosive substances.
- Mechanical Strength: Galvanised conduit is known for its ability to withstand physical impacts and impacts from installation processes. This makes it a robust option in various applications.
- Flexibility in Application: It is widely used in electrical systems, including residential, commercial, and industrial settings. This versatility makes it a vital component in many construction projects.
Benefits and Considerations
Given the properties of galvanised conduit, here are some advantages:
- Durability: The lifespan of galvanised conduit is much longer than other conventional options. This reduces the frequency of replacements, ultimately saving costs.
- Cost-Effectiveness: Though initial investment might be higher, the long-term savings in maintenance and replacement make it an economical choice.
- Safety Compliance: Galvanised conduit meets various safety standards, ensuring that installations are up to regulatory requirements.
The sustainability aspect of using galvanised conduit cannot be overlooked, especially in an era where environmental considerations are paramount.
Understanding Galvanisation
Galvanisation is a crucial process in enhancing the longevity and performance of metals, specifically steel and iron. It involves the application of a protective zinc coating to prevent corrosion. This not only ensures the integrity of the material but extends its lifespan significantly. In the context of galvanised conduit, understanding galvanisation is essential as it lays the groundwork for the conduit’s effectiveness and reliability in various applications.
The process can be complex, often encompassing different methods. Recognizing these methods enables better selection of materials based on specific needs. A comprehensive understanding of this topic will help industry professionals and researchers make informed choices regarding the use of galvanised conduits in electrical and construction undertakings, maximizing their benefits while minimizing risks.
Chemical Process of Galvanisation
The chemical process of galvanisation primarily involves immersing steel in molten zinc. This immersion creates a metallurgical bond between the zinc and the steel. As a result, it forms a protective layer which acts as a barrier against environmental factors like moisture and oxygen that typically contribute to corrosion.
Key steps in the chemical process include:
- Surface Preparation: Steel surfaces must be cleaned thoroughly to remove dirt, rust, and oils. This is often achieved through methods like sandblasting or acid pickling.
- Zinc Bathing: After preparation, the steel is dipped into a vat of molten zinc, usually around 450 degrees Celsius. The zinc bonds with the iron in the steel, forming various zinc-iron alloy layers.
- Cooling: Once removed from the zinc bath, the galvanised conduit must cool, which solidifies the zinc coating and ensures durability.
This process is not only effective but also economical, offering a robust solution to corrosion resistance in various environments.
Purpose and Benefits of Galvanisation
The purpose of galvanisation goes beyond just the surface appearance of the conduit. The primary aim is to enhance the lifespan of metal structures, especially in challenging environments prone to corrosion.
Benefits include:
- Corrosion Resistance: The zinc coating acts as a sacrificial layer, meaning it will corrode before the underlying steel, thereby protecting it. This is vital in scenarios where conduits are exposed to moisture.
- Cost Efficiency: By decreasing the frequency of replacements and repairs, galvanised conduit can lead to significant cost savings over time.
- Mechanical Strength: Galvanisation does not compromise the strength of steel; it reinforces it while providing resistance to impact and abrasions.
- Low Maintenance: Galvanisation requires minimal upkeep. This quality is especially beneficial for installations in hard-to-reach areas where maintenance might pose further challenges.
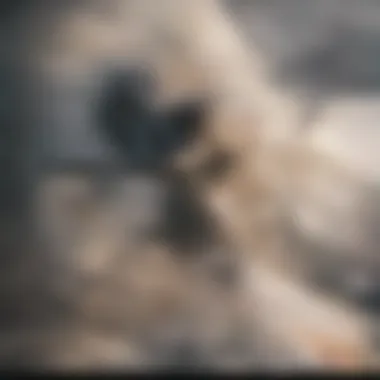

"The extended lifespan of galvanised materials can significantly reduce overall project costs and ensure consistent performance over time."
In essence, understanding galvanisation contributes immensely to realizing the full potential of galvanised conduit in its various applications. It supports informed decision-making, ensuring that the advantages offered by this method are fully leveraged.
Manufacturing of Galvanised Conduit
The manufacturing of galvanised conduit is a subject of significant importance in this exploration of galvanised conduit. This process covers everything from raw material selection to production methods. Understanding these elements is crucial because they determine the quality and efficacy of the end product. Therefore, insights into the manufacturing intricacies also reflect on the conduit’s overall performance in various applications.
Raw Materials Used
The raw materials for galvanised conduit are vital to its construction and performance. The primary component is steel, which provides the structural integrity needed to handle various environments and loads. The steel often goes through a process to ensure it possesses adequate strength and rigidity.
In addition to steel, a number of additives are sometimes included. These can enhance properties like corrosion resistance. Commonly used alloying elements may include manganese and silicon, which effectively strengthen the steel and facilitate galvanisation. This selection of raw materials significantly influences the reliability of the conduit in practical settings. It can affect the conduit’s life span in demanding environments, thus playing a vital role in deciding the material’s suitability for specific applications.
Production Techniques
The production of galvanised conduit generally involves two main stages: the preparation of steel and the galvanisation process itself. Firstly, the steel is cut and shaped into the desired conduit form. This sometimes includes bending and threading to meet specific installation requirements. Precision in these early stages is important. Even slight inaccuracies can lead to complications in installation later on.
Once the conduit shape is achieved, the galvanisation process begins. This typically involves hot-dip galvanisation, where the steel conduit is submerged in molten zinc. This method ensures a thick, even coating of zinc is deposited onto the steel surface. The chemical reaction creates a metallurgical bond, ensuring that the conduit remains protected against rust and other corrosive elements.
An alternative to hot-dip galvanisation is electro-galvanisation, although this method usually results in a thinner layer of zinc. This reduces the durability in harsh environments. Thus, the selection of galvanisation technique also influences the conduit’s future applications.
Effective manufacturing processes ensure galvanised conduits are reliable for both electrical and construction purposes.
Key Properties of Galvanised Conduit
Understanding the key properties of galvanised conduit is essential for anyone involved in electrical or construction fields. These properties, namely corrosion resistance and mechanical strength, significantly affect the conduit’s performance, longevity, and reliability in various applications.
The construction and electrical industries demand materials that can withstand harsh environments while maintaining structural integrity. Galvanised conduit stands out due to its unique combination of these properties. The following sections delve deeper into each property and their relevance.
Corrosion Resistance
Corrosion resistance is one of the most critical characteristics of galvanised conduit. The galvanisation process involves coating steel with a layer of zinc, which serves as a protective barrier against rust and corrosion. This protection is vital, especially in environments exposed to moisture, chemicals, and harsh weather conditions.
- Longevity: Galvanised conduit can last significantly longer than standard steel conduit due to its corrosion-resistant properties. This aspect reduces maintenance costs over time.
- Safety: Using corrosion-resistant materials minimizes the risk of system failures, as corrosion can lead to leaks and short circuits in electrical systems.
- Variety of Applications: The enhanced durability allows for its use in versatile environments, including outdoor settings where exposure to the elements is a concern.
"The right choice of materials can affect long-term performance and reliability in electrical and construction projects."
Mechanical Strength
Mechanical strength is another paramount property of galvanised conduit. This material provides robustness that is essential for both electrical installations and structural applications.
- Load-Bearing Capability: Galvanised conduit can withstand significant mechanical stress without failure. This capability makes it suitable for high-load applications, such as in commercial and industrial constructions.
- Impact Resistance: In addition to load-bearing, galvanised conduit offers considerable impact resistance, which protects electrical wiring and equipment from physical damage.
- Stability: The structural integrity of galvanised conduit ensures stability in various installations. This is critical when considering safety and regulatory compliance in construction and electrical projects.
In summary, the key properties of galvanised conduit—corrosion resistance and mechanical strength—play a crucial role in its effectiveness and longevity in various applications. Understanding these properties is essential for anyone involved in the selection or installation of this material.
Applications of Galvanised Conduit
Galvanised conduit serves as an essential component in various industries, particularly in electrical and construction applications. This section will detail how galvanised conduit is utilized, outlining its role in electrical systems and construction projects. Understanding these applications is crucial for professionals seeking to implement effective and durable solutions.
Electrical Systems
In the realm of electrical systems, galvanised conduit is crucial for protecting wiring from environmental hazards. It ensures safety and compliance with electrical codes. The use of galvanised conduit often helps to prevent moisture and corrosion from affecting electrical installations. This material contributes to minimizing risks such as short circuits and electrical fires.
Moreover, its robust mechanical properties allow it to support wiring in a way that is both secure and efficient. The conduit can be installed in various locations, including indoor and outdoor settings. For example, in industrial settings, it is common to see galvanised conduit used to encase high-voltage wiring. This not only protects the wiring but also ensures easy identification during maintenance work.
Many electrical engineers favor galvanised conduit due to its longevity and reliability. The typical life span can exceed decades, providing cost efficiency over time.
"Electrical systems benefit significantly from the durability and protective qualities of galvanised conduit, making it a go-to choice for safety-minded installations."
Construction Projects
In construction, galvanised conduit finds its importance in both structural and electrical applications. This material is commonly employed for routing and protecting electrical wires in commercial and residential buildings. Its strength and resistance to various environmental factors make it ideal for long-term installations.
One key advantage is its ability to maintain integrity in harsh weather conditions. In fact, galvanised conduit often withstands moisture, chemicals, and physical impacts better than alternatives.
In addition, galvanised conduit provides a clean, professional appearance for exposed wiring. This is particularly relevant in aesthetic-driven plans where visibility of utility conduits is a concern.
When considering installation, galvanised conduits are relatively straightforward to work with, allowing construction teams to save time and resources. Common practices include using connectors and fittings that are also galvanised, ensuring a uniform protective layer against corrosion.
Through these applications, galvanised conduit plays a pivotal role in ensuring safe and efficient construction practices. Its reliability and industry compliance continues to make it a preferred choice among professionals.
Advantages of Using Galvanised Conduit
The value of galvanised conduit arises from its unique properties and functionalities that cater to an array of applications in various fields. From electrical installations to structural applications, understanding the advantages is critical for professionals seeking robust and reliable solutions.
Durability
Durability is one of the foremost qualities of galvanised conduit. The galvanisation process provides a protective layer that shields the metal from external environmental factors. Over time, exposure to moisture, chemicals, and other elements can degrade metallic materials. However, galvanised conduit effectively resists corrosion, ensuring longevity in installation.
Factors influencing durability include:
- Coating Thickness: A thicker galvanised coating provides better protection against wear and tear.
- Installation Environment: In harsh environments, such as coastal areas or areas with high humidity, galvanised conduit performs exceptionally well.
This durability means fewer replacements or repairs over time, thus reducing operational downtimes and enhancing project efficiency.
Cost-Effectiveness
Cost-effectiveness is another significant advantage. While the initial investment in galvanised conduit may be higher relative to alternative materials, the long-term savings become apparent quickly. The longevity and reduced need for maintenance translate into lower overall costs over the lifespan of an installation.
Benefits contributing to cost-effectiveness include:
- Reduced Maintenance: The corrosion-resistant qualities lead to less frequent maintenance work, saving both labor and material costs.
- Energy Efficiency: In electrical applications, the longevity of the conduit can contribute to enhanced energy efficiency, reducing utility costs.
- Availability: Galvanised conduit is widely available, which can minimize supply chain costs.
In summary, while galvanised conduit requires a measured upfront investment, the robustness and endurance it offers ultimately yield significant savings and justify its use across various applications.
"Investing in high-quality materials like galvanised conduit pays off in the long run through resilience and lower maintenance needs.”
Challenges and Drawbacks
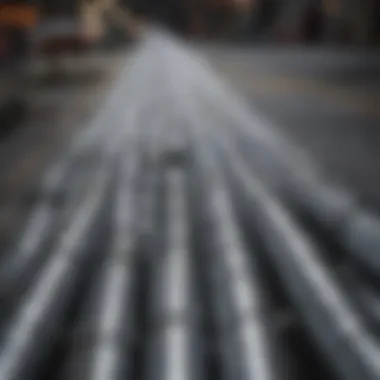
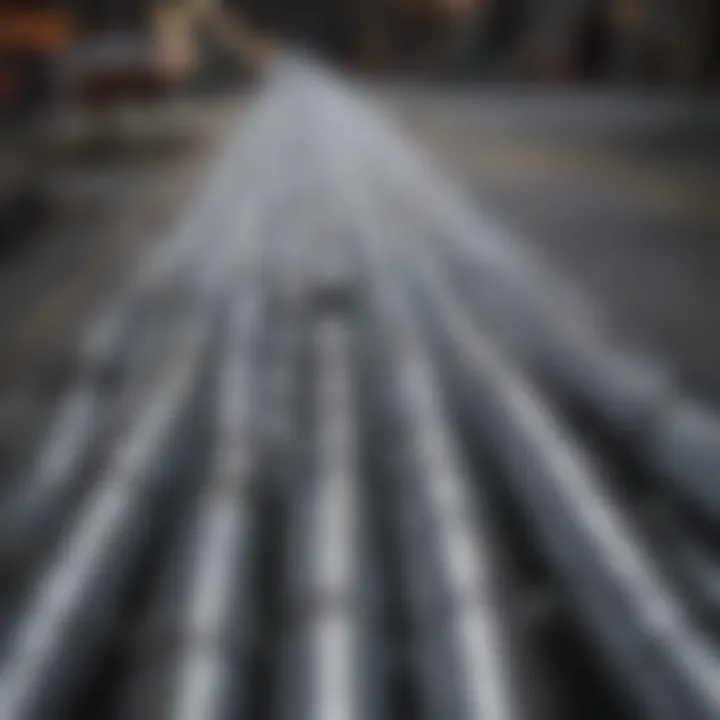
In any material usage, including galvanised conduit, understanding the challenges and drawbacks is essential. Despite its benefits in construction and electrical applications, galvanised conduit presents several considerations that professionals must evaluate carefully. These factors can influence project timelines, budgets, and overall effectiveness.
Weight Considerations
One of the most prominent challenges with galvanised conduit is its weight. Compared to alternatives, such as PVC or EMT, galvanised conduit is significantly heavier. This added weight can affect various aspects of installation and handling.
- Installation Difficulty: Heavy materials require more manpower and equipment to manage and install properly. This can lead to increased labor costs and project timelines.
- Structural Support: The weight can necessitate additional structural support, especially in installations involving long runs or high ceilings. Designing around this need may complicate the overall project.
- Transportation Logistics: Transporting galvanised conduit to job sites can be more complicated and costly due to its weight. Consideration of transportation logistics is crucial for budgeting.
These factors call for conscious planning during the design phase. Understanding how to plan for the weight and its implications can mitigate potential issues during installation.
Thermal Expansion
Another significant drawback of galvanised conduit is related to thermal expansion. As a metal, it expands and contracts in response to temperature changes. This property can influence installation layouts and long-term usability.
- Expansion Gaps: Depending on the installation environment, professionals must account for thermal expansion by including appropriate gaps. Failing to do so can lead to stress on joints and connectors, resulting in potential failures over time.
- Material Integrity: With excessive thermal expansion, there is a risk of the conduit warping or distorting, weakening its overall structural integrity. Proper installation and securing techniques must adjust to environmental conditions to avoid issues.
Effectively managing thermal expansion is critical to maintaining the performance and reliability of galvanised conduit in various applications.
In summary, while galvanised conduit offers many advantages, it is important to recognize the challenges associated with its weight and thermal expansion. Proper planning and consideration can make these drawbacks manageable, allowing professionals to take full advantage of galvanised conduit's properties in their projects.
Installation Techniques for Galvanised Conduit
The installation of galvanised conduit is an essential aspect of its application, influencing both functionality and durability. Proper techniques ensure that the conduit serves its purpose within electrical and construction projects effectively. Understanding installation methods not only contributes to safety but also maximizes the lifespan of the conduit. Each project has its unique demands, wherein planning and layout play a crucial role, alongside the various joining methods utilized for effective integration into systems.
Planning and Layout
Planning is a critical step in the installation of galvanised conduit. This phase involves identifying the route the conduit will take, determining the number of conduits required, and ensuring the layout complies with local regulations. Notably, a well-structured plan can help in minimizing material wastage and reducing installation time. Key considerations during the planning process include:
- Load Requirements: Understanding the electrical load that the conduit will need to support is vital. This directs the selection of the appropriate size and type of conduit.
- Environmental Conditions: Installation sites may have different factors such as moisture or temperature extremes. These impact the choice of conduit and its installation approach.
- Accessibility for Maintenance: Ensuring that conduits are easily accessible for future repairs or inspections is an important consideration.
- Supporting Structures: Depending on the configuration, proper support brackets should be planned into the layout to prevent sagging or misalignment.
Evaluating these elements can culminate in a smoother installation, leading to enhanced performance over time. The planning phase should also include comprehensive documentation of the design, which can be beneficial for future maintenance or upgrades.
Joining Methods
Once the planning is complete, the next step involves the joining of galvanised conduits. Several methods exist for connecting pieces of conduit. Choosing the right joining method is paramount to ensure safety and functionality. The most common techniques include:
- Threaded Connectors: This method involves threading the ends of the conduits. It provides a secure connection and is often employed in scenarios requiring disassembly for maintenance.
- Compression Fittings: Compression fittings are applicable where quick connections are important. They allow for flexibility and ease of installation without the need for special tools.
- Welded Joints: This method is most suited for permanent installations. Welding creates a strong bond between the conduit pieces but requires skilled labor and appropriate safety measures.
- Screw Connectors: Using screws to fasten conduit sections is another viable option. This method is simple and provides ample strength while allowing for easy disassembly when needed.
Proper joining techniques are crucial for ensuring the integrity and safety of electrical installations.
Maintenance of Galvanised Conduit
Maintaining galvanised conduit is essential to ensure its longevity and optimal performance in various applications. Regular maintenance can help prevent potential issues that arise from wear and tear, environmental exposure, or improper installation. The focus here is on the two critical aspects of maintenance: inspection protocols and repair techniques. By understanding these processes, professionals working with galvanised conduit can maximize its lifespan and efficiency.
Inspection Protocols
Inspection is a proactive step in maintaining galvanised conduit. It involves a detailed examination of the conduit installations to identify any signs of damage, corrosion, or other issues that might affect their integrity. Here are some key components of effective inspection protocols:
- Regular Scheduling: Establish a routine inspection schedule. Regular reviews can catch problems early, reducing repair costs and ensuring safety.
- Visual Inspection: Conduct thorough visual assessments of the conduits, looking for scratches, corrosion, and any physical deformities. Any visible damage should be noted for further investigation.
- Environmental Factors: Pay attention to the environment around the conduits. Environmental contamination, excessive moisture, and exposure to chemicals can lead to accelerated corrosion.
- Testing for Insulation Integrity: An important consideration is ensuring that the conduit’s insulation remains intact. This involves checking for any signs of overheating or electrical insulation degradation.
- Documentation: Keep detailed records of inspections and any discovered issues. This documentation is crucial for long-time maintenance planning and provides information for troubleshooting future problems.
Regular inspections not only prevent future damage but also ensure compliance with local safety standards.
Understanding the importance of inspection protocols can greatly influence the performance and safety of galvanised conduit installations.
Repair Techniques
When faults are detected during inspections, prompt and effective repair techniques must be implemented. Here are some common approaches to repairing galvanised conduit:
- Cleaning: Before any repair, it is vital to clean the affected area. Using a wire brush or chemical cleaners can help remove rust, dirt, or other contaminants from the surface.
- Rust Treatment: For corrosion issues, applying a rust-inhibiting primer or paint after cleaning can help prevent further deterioration. Ensure the surface is dry and free from grease before application.
- Patch Repair: Small holes or cracks can be patched using galvanised metal patches. These should be securely attached and sealed to avoid moisture infiltration, which can exacerbate corrosion.
- Replacement: In cases where damage is extensive, replacement of sections of conduit may be necessary. It is important to match the new conduit’s specifications with the original to maintain system integrity.
- Reinstallation: If the conduit was improperly installed, re-evaluation of the installation techniques and methods may be necessary. This ensures that the conduits are properly secured to withstand potential physical disturbances and environmental factors.
Maintenance of galvanised conduit is not merely a recommendation; it is a requirement for safety and efficiency in both construction and electrical applications. Adhering to proper inspection and repair methods can extend the useful life of galvanised conduit, supporting its crucial role in various applications.
Regulatory Standards and Compliance
Understanding the regulatory standards and compliance requirements surrounding galvanised conduit is essential. Compliance ensures safety, functionality, and durability in installations. Such standards dictate how conduit should be used in various applications, safeguarding both users and infrastructure.
National Electrical Code (NEC) Compliance
The National Electrical Code (NEC) sets the foundation for safe electrical design, installation, and inspection. It covers several aspects of conduit usage. For galvanised conduit, the NEC specifies requirements for size, type, and installation methods. Compliance ensures that installations are safe from hazards such as electrical shocks and fire risks.
A few key points include:
- Material Standards: The NEC outlines the acceptable materials for conduit installations—galvanised steel must meet specific grades. This ensures consistency in quality and performance.
- Installation Guidelines: The NEC provides detailed installation procedures that must be followed to ensure safety and effectiveness. These guidelines help prevent issues like water accumulation and corrosion.
- System Compatibility: The NEC emphasizes that conduit systems must be compatible with electrical systems. This aspect ensures that galvanised conduit can handle intended loads without failure or degradation.
Adhering to NEC guidelines not only promotes safety but also helps in passing electrical inspections, which can impact a project's timeline and costs.
Safety Regulations
Safety regulations focus on the protection of personnel and the environment. These regulations govern how galvanised conduit should be employed in various settings. Several key considerations are involved:
- Health Risks: Working with galvanised materials does come with health risks. Workers should wear appropriate personal protective equipment (PPE) to avoid inhalation of zinc dust during cutting or welding. Ensuring compliance with occupational health standards is paramount.
- Installation Safety: Following safety protocols during installation decreases the chances of accidents. For instance, proper handling techniques help prevent falls or equipment damage.
- Emergency Preparedness: In the case of an electrical fault or failure, safety regulations often require that emergency measures are in place. This includes well-defined protocols for dealing with electrical fires or injuries.
Understanding and following safety regulations is crucial. Neglect can lead to serious injuries or accidents.
In summary, both the NEC and safety regulations play vital roles in ensuring that galvanised conduit installations are conductive, safe, and reliable. Professionals involved in these projects must remain updated on these standards and continuously assess their compliance. This vigilance not only enhances safety but also contributes to the longevity and effectiveness of the installed systems.
Future Trends in Galvanised Conduit Usage
The relevance of future trends in galvanised conduit usage cannot be understated. As the world moves towards more sustainable practices, innovations in material science and an increased focus on environmental considerations will shape the future of this essential commodity. Understanding these trends will equip professionals to make informed choices, ensuring that they remain relevant in a rapidly evolving landscape.
Innovations in Material Science
Material science is continuously evolving and has a profound impact on the production and application of galvanised conduit. Recently, researchers have focused on developing enhanced galvanisation techniques that improve the lifespan of conduits without compromising their core functions. New alloys and coatings can promote better resistance to corrosion, making conduits safer and longer-lasting in various environments.
Additionally, advancements such as nano-coatings are becoming more prevalent. These coatings can provide an extra layer of protection while maintaining lightweight characteristics. Such innovations not only improve the durability of galvanised conduit but also contribute to its adaptability in different sectors. For example, highly resistant conduits are crucial in offshore projects where exposure to saltwater can lead to significant degradation.
"Innovation in material science is key to enhancing performance and longevity of galvanised conduits in critical applications."
This evolution in material technology also means improved manufacturing processes. Automated systems and robotics are streamlining production, reducing waste and allowing for a more efficient use of resources. As these technologies integrate into the industry, the market may become more competitive, leading to better pricing and availability.
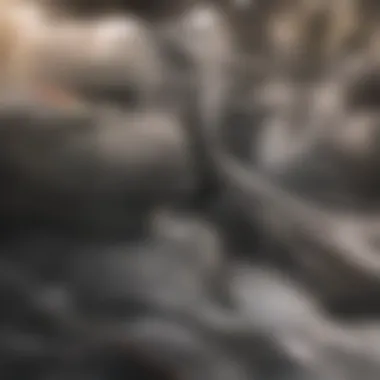
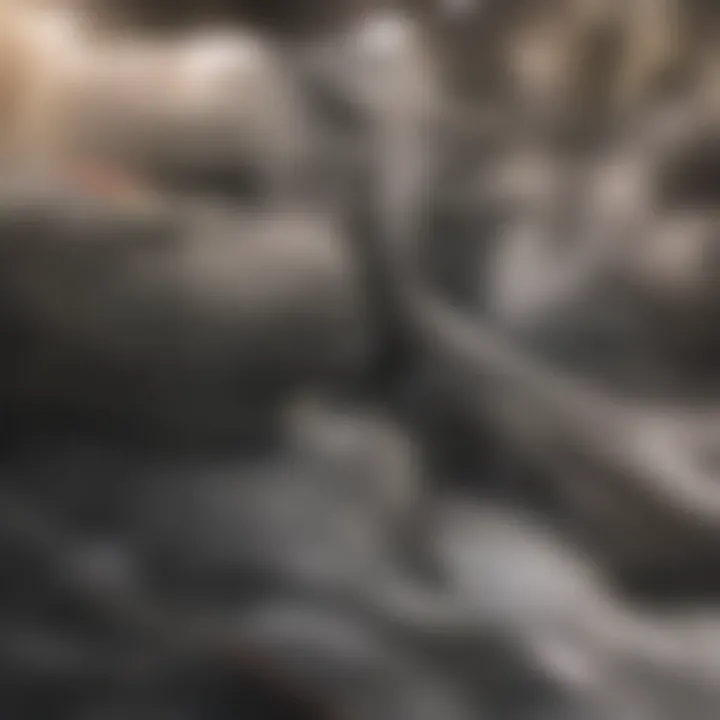
Environmental Considerations
An increasing demand for environmental friendliness is influencing the future landscape of galvanised conduit. With concerns about climate change and sustainability taking center stage, manufacturers are revisiting their production methodologies. This includes practices that minimize waste and utilize recycled materials. For example, employing recycled steel in the production of galvanised conduit not only conserves resources but can also lower carbon footprints associated with manufacturing.
Furthermore, the focus on lifecycle assessments is making its way into the industry. This means examining the impacts of galvanised conduit from production through to end-of-life, ensuring that materials can be disposed of or recycled correctly. This holistic view prompts the development of conduits that can be reused or repurposed rather than contributing to landfill overflow.
The transition to more eco-friendly practices can also enhance the reputation of brands within the industry. Companies dedicated to sustainability are likely to attract partnerships and investments, fostering growth in sectors sensitive to these global trends.
Comparative Analysis with Alternative Materials
A comprehensive understanding of galvanised conduit necessitates a comparative analysis with alternative materials. This section focuses on comparing galvanised conduit with commonly used options such as PVC conduit and EMT (Electrical Metallic Tubing). Each material has its properties, advantages, and drawbacks, which impact their use in electrical and construction applications.
In evaluating these options, one can discern how galvanised conduit stands against its counterparts in terms of durability, corrosion resistance, and cost-effectiveness. This comparison is not just about choosing one over the other; it's about understanding the specific scenarios where each material excels, thereby allowing professionals to make informed decisions.
PVC Conduit vs. Galvanised Conduit
PVC conduit is often used as a lightweight and cost-effective alternative to galvanised conduit. One of the primary benefits of PVC is its resistance to corrosion, which makes it suitable for environments exposed to moisture. Its flexibility can simplify installation, especially in spaces requiring intricate bends. However, PVC conduit has limitations in terms of temperature resilience. It may deform or melt in high-temperature environments, which can create safety hazards.
On the other hand, galvanised conduit is known for its robust mechanical strength and ability to withstand harsher conditions. It does not warp or bend as easily as PVC, which can be an advantage in commercial settings.
Some critical differences include:
- Material Composition: PVC is plastic, while galvanised conduit is metal coated with zinc for corrosion resistance.
- Temperature Resistance: Galvanised conduit performs better under heat, maintaining structural integrity in high temperatures.
- Fire Resistance: Being non-combustible, galvanised conduit offers better fire safety compared to PVC.
In applications where durability and fire resistance are paramount, galvanised conduit is often the preferred choice despite its heavier weight.
EMT (Electrical Metallic Tubing) vs. Galvanised Conduit
Electric Metallic Tubing (EMT) is another alternative to galvanised conduit, often favored for indoor applications due to its lightweight and ease of installation. EMT is typically thinner than galvanised conduit, which can make it easier to handle and install. However, this lightness comes at the cost of some structural integrity and durability, particularly in outdoor or high-impact environments.
Conversely, galvanised conduit provides superior protection for wiring in harsh environments, thanks to its thicker walls. This additional mass contributes to better protection against physical damage and impact. EMT lacks the corrosion resistance that galvanised conduit offers, specifically in humid, salty, or highly polluted areas.
Consider the following points for comparison:
- Weight: EMT is lighter, making installations easier, whereas galvanised conduit provides stronger protection.
- Cost: EMT can be more economical initially, but galvanised conduit’s durability may lead to lower long-term costs due to fewer replacements.
- Installation Technique: EMT's ease of bending can make it faster to install, but galvanised conduit necessitates more robust joining methods to ensure safety.
"Understanding the comparative strengths and weaknesses of materials like galvanised conduit, PVC, and EMT allows for smarter, safer choices in installation and application."
In summary, understanding the distinctions between galvanised conduit, PVC conduit, and EMT is crucial for professionals aiming to choose the appropriate material for specific contexts. The choice often boils down to the unique demands of the project, including exposure to elements, fire safety needs, and budgetary considerations.
Case Studies of Galvanised Conduit in Practice
Case studies provide a critical lens through which we can analyze the practical applications of galvanised conduit in real-world scenarios. They elucidate the effectiveness and versatility of this material in both industrial and residential settings. By examining specific instances, we can not only validate our earlier discussions about galvanised conduit but also discover new insights into its usage. Furthermore, case studies highlight the considerations that need attention during the planning, installation, and maintenance stages.
Industrial Applications
In industrial settings, galvanised conduit serves a fundamental role in protecting electrical wiring from external elements. One notable example can be found in large manufacturing facilities where the environment is often dusty, humid, or even corrosive. In these conditions, the durability of galvanised conduit provides a significant advantage. A case study conducted in a manufacturing plant showcased how installing galvanised conduit reduced instances of wiring failure, which often stems from exposure to moisture and chemical substances.
Moreover, galvanised conduit is preferred for its seamless support for wiring systems, which can often be extensive. It allows easy access for future modifications without requiring extensive rewiring. These features result not only in substantial cost savings but also enhance operational efficiency.
"The ability to adapt and maintain electrical systems is crucial in today’s fast-paced industrial environment, making galvanised conduit a reliable choice."
Residential Installations
When it comes to residential installations, the applications of galvanised conduit are also noteworthy. In one case, a new housing development used galvanised conduit for all its electrical wiring needs. Benefits included significant long-term savings due to the reduced risk of corrosion, which can often be a serious concern in basements and other moisture-prone areas. This particular installation highlighted the ease of maintenance and inspection, as galvanised conduit allows for straightforward access to wiring without compromising structural integrity.
Another interesting aspect to consider is that galvanised conduit also contributes to aesthetic values. Homeowners in this case study appreciated the neat appearance since the conduit can be run along walls and ceilings without detracting from the home’s design.
Regarding safety, galvanised conduit positions itself as a defensible choice, minimizing fire hazards linked to improper wiring.
International Perspectives on Galvanised Conduit
Understanding the international context of galvanised conduit is essential for several reasons. Different countries have unique applications, standards, and market dynamics concerning this material. By examining these perspectives, we can identify best practices, common challenges, and innovative solutions that have emerged across the globe. This knowledge not only enhances our comprehension of galvanised conduit but also informs various stakeholders about the potential for its use in different regulatory climates.
Standards Across Different Countries
The standards governing galvanised conduit differ significantly around the world. In the United States, for instance, the National Electrical Code (NEC) outlines specific requirements that ensure safety and performance in electrical installations. This code emphasizes the importance of using conduit that can withstand environmental challenges, which is particularly relevant in regions with harsh climates.
In Europe, standards are influenced by both the EN (European Norm) directives and local regulations. The ISO (International Organization for Standardization) plays a role in establishing guidelines that promote safety and interoperability among electrical components.
The reliance on local building codes and safety regulations means that users of galvanised conduit need to be aware of the specific requirements in their locale. Key aspects often include:
- Material specifications – Different grades of galvanised steel may be mandated, based on local corrosion resistance requirements.
- Installation practices – The methods of installation may be dictated by both safety regulations and efficiency concerns specific to each region.
- Testing and certification – Conduit must often pass rigorous testing to ensure compliance with local standards before it can be used in projects.
Market Trends in Global Context
The market trends for galvanised conduit are shaped by various factors, including economic conditions, technological advancements, and changing regulations. In many developing countries, the demand for galvanised conduit is rising, driven by increased infrastructure projects and urbanization. As cities expand and electrical systems become more complex, the need for reliable conductors is critical.
Conversely, in developed markets, there is a focus on sustainable building practices. As such, galvanised conduit is often compared with alternative solutions, such as PVC or EMT. However, its long lifespan and low maintenance needs make it a favorable choice for many contractors and engineers.
Furthermore, the integration of smart technologies within electrical systems is influencing conduit market dynamics. For example, conduit that can accommodate the installation of fiber optics alongside electrical wiring is gaining popularity.
Key market trends include:
- Sustainability – Growing emphasis on environmentally friendly materials is leading to increased scrutiny of galvanising processes.
- Innovation – Smart IT and installation solutions are integrating with traditional materials to meet modern demands.
- Globalisation – The international trade of galvanised conduit is expanding, providing access to different markets and innovations from across the globe.
"Understanding international perspectives on galvanised conduit is crucial for leveraging its applications in various sectors. Standards and market trends provide insights into practical and regulatory considerations vital for successful implementation."
Finales and Recommendations
Summary of Key Findings
The exploration of galvanised conduit has revealed several key findings:
- Corrosion Resistance: The galvanisation process enhances the conduit’s ability to resist corrosion, making it suitable for a variety of environments, especially where exposure to moisture is common.
- Mechanical Strength: Galvanised conduit exhibits substantial mechanical strength, offering durability and safety in installation which is crucial for electrical and structural integrity.
- Wide Range of Applications: Its versatility allows for application across numerous sectors including industrial installations, residential wiring, and construction projects.
- Cost-Effectiveness: The long lifespan and lower maintenance needs of galvanised conduit contribute to its overall cost-effectiveness over time.
- Regulatory Compliance: Adhering to national codes and regulations safeguards the quality and safety of installations, highlighting the importance of compliance for practitioners.
Taking these findings into account should inform strategic choices regarding materials and installation practices, ensuring both efficiency and safety in projects involving galvanised conduit.
Future Directions for Research
As galvanised conduit technology evolves, several avenues for further research emerge:
- Innovations in Coating Techniques: Examining newer galvanisation techniques might enhance corrosion resistance, making galvanised conduit even more suitable for extreme environments.
- Environmental Impact Studies: Understanding the ecological implications of using galvanised conduit, from production to disposal, will be crucial in promoting sustainable practices in the industry.
- Comparative Material Studies: Continued research comparing galvanised conduit with alternative materials can yield insights into performance, cost, and application-specific advantages.
- Advancements in Joining Techniques: Investigating new methods for joining galvanised conduit to improve installation efficiency and robustness could significantly benefit the industry.
By addressing these potential research areas, professionals and academics alike can facilitate advancements in the field, ensuring that galvanised conduit continues to meet the evolving demands of both electrical and construction applications.
"The understanding of materials like galvanised conduit paves the way for innovation and improved practices in industrial standards."