Exploring Metal Forming: Techniques and Innovations
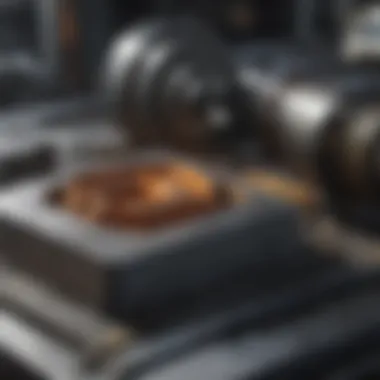
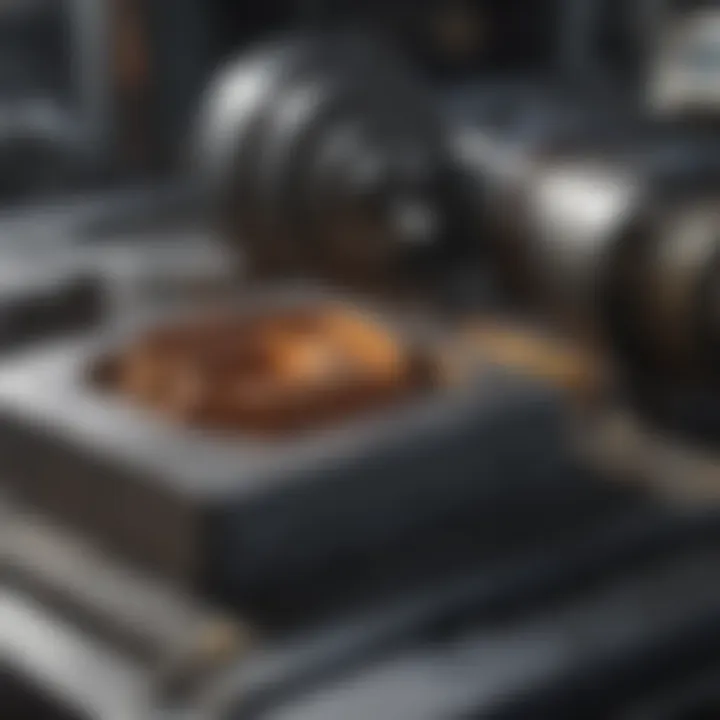
Intro
Metal forming is a vital aspect of manufacturing, influencing the production and performance of a wide range of products. Understanding its techniques and applications reveals the complexities of manufacturing processes and the impact of innovations. This article will provide detailed insights into various metal forming techniques such as forging, rolling, and extrusion while highlighting their applications in key industries like automotive, aerospace, and construction.
The journey through these topics will outline the importance of material properties and design considerations that directly affect production strategies. Additionally, it will delve into modern developments like 3D printing and digital fabrication, demonstrating their growing significance in the field.
The goal is to provide a comprehensive view of metal forming, making it accessible for students, researchers, educators, and professionals alike.
Key Concepts
Definition of Primary Terms
Metal forming refers to a group of industrial processes that change the shape of metal workpieces. These processes are essential in creating various components that come together to form larger systems. Key techniques within this domain include:
- Forging: This process uses compressive forces to shape metal, often resulting in high strength and durability. The metal is heated and then shaped by hammers or presses.
- Rolling: Involves passing metal through rollers to reduce its thickness. This method is common in creating sheets and plates.
- Extrusion: This technique forces metal through a die to create long shapes, like tubes and rods. It allows for the efficient production of complex cross-sections.
- 3D Printing: An innovative addition to metal forming, it builds components layer by layer from digital models.
Related Concepts and Theories
To understand metal forming comprehensively, it is also essential to consider related theories in material science and engineering design.
- Material Properties: The physical characteristics of metals, such as strength, ductility, and thermal conductivity play a crucial role in selecting suitable forming processes.
- Engineering Design: The principles guiding the design of components impact their manufacturability and performance. Design considerations should align with the chosen forming technique to ensure efficiency and effectiveness.
Applications
Industries such as automotive, aerospace, and construction rely heavily on metal forming processes for the production of critical components.
- Automotive: Metal forming is used extensively in vehicle bodies, frames, and engine parts. Each component must meet stringent safety and performance standards, demanding precision in forming techniques.
- Aerospace: In this sector, the lightweight and high-strength characteristics of forged and extruded components are paramount. Metal forming contributes significantly to the overall efficiency of aircraft.
- Construction: Structural components, like beams and reinforcements, utilize metal forming processes to ensure they can bear the loads they are subjected to.
Future Directions
Gaps Identified in Current Research
While metal forming techniques have existed for many years, certain areas require further exploration. Research on the integration of new materials and advanced forming technologies is lacking. Understanding the effects of new alloys on traditional processes could yield innovative applications and improve existing methods.
Suggestions for Further Studies
Future studies should focus on:
- The implications of integrating artificial intelligence and machine learning in metal forming processes.
- Analyzing sustainability in metal forming by exploring methods that reduce waste and energy consumption.
Prologue to Metal Forming
Metal forming is a critical process in manufacturing, influencing various industries through its ability to shape and manipulate materials. Understanding the dynamics and benefits of metal forming is essential for both production efficiency and product innovation. This section will explore the definition of metal forming, its significance, and its historical progression.
Definition and Importance
Metal forming refers to a collection of processes that alter the shape of metal materials through mechanical forces without removing any material. This method includes techniques like forging, rolling, extrusion, and stamping. The importance of metal forming lies in its efficiency and effectiveness in creating complex geometries that are often challenging to achieve with other manufacturing methods. Such processes are not only cost-effective but also improve the mechanical properties of the metals, leading to stronger and lighter products.
Metal forming is prevalent in sectors such as automotive, aerospace, and consumer electronics, where strength-to-weight ratios are critical. By enhancing the performance characteristics of metals, metal forming supports modern design innovations that require precision and durability.
Metal forming is vital for producing components that meet stringent engineering demands across various industries.
Historical Developments
The history of metal forming dates back to ancient civilizations, which utilized simple techniques to shape metal. Early blacksmiths would hammer and forge metal into various shapes for tools and weapons. Over centuries, metal forming evolved with technological advancements.
By the Industrial Revolution, mass production introduced new methods such as rolling and stamping, significantly improving the efficiency of producing metal components. The development of sophisticated machinery and computer numerical control (CNC) further transformed metal forming, enabling precise and repeatable processes. Today, advancements like additive manufacturing and digital fabrication further enhance the capabilities of metal forming, allowing for innovative designs and applications that were once thought impossible.
In summary, the evolution of metal forming reflects a blend of craftsmanship and technological innovation, solidifying its role as a fundamental practice in modern manufacturing.
Overview of Metal Forming Techniques
Metal forming is a pivotal aspect of manufacturing, involving the deformation of metals to create desired shapes without removing material. Understanding diverse techniques allows engineers to choose the proper method aligned with production requirements. The ability to efficiently manipulate metal makes these techniques fundamental in various industries, from automotive to aerospace.
Forging Processes
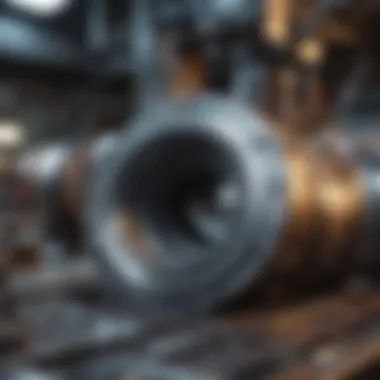
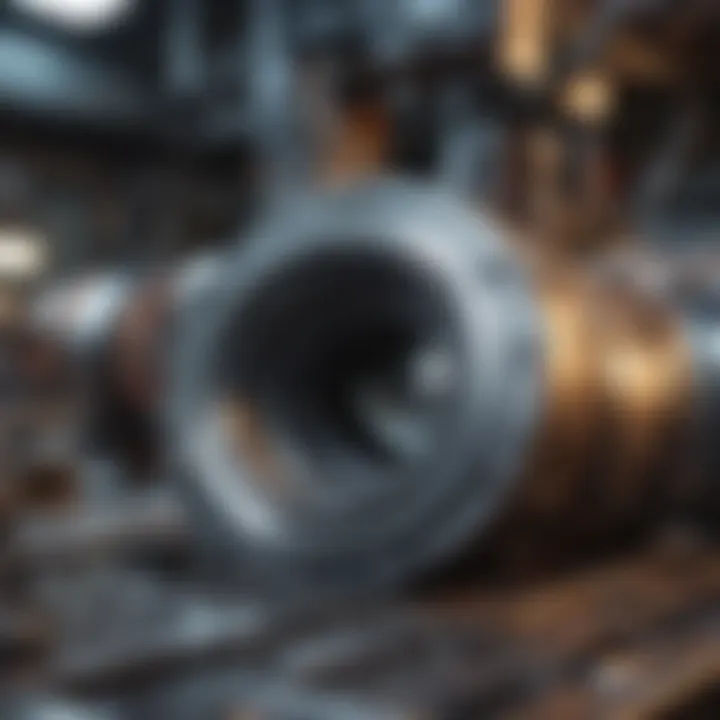
Forging is a technique that involves shaping metal through localized compressive forces. It can be done hot or cold, depending on the material properties desired. The primary advantage of forging is the enhancement of mechanical properties. When the metal is deformed, internal structure changes, improving strength and durability. Various forging methods exist, including open-die, closed-die, and impression-die.
Forging often results in superior mechanical properties compared to other processes, making it a preferred choice in critical applications.
Some common applications include aircraft components and automotive parts needing great resilience. However, this technique also has limitations, such as higher production costs and tool wear.
Rolling Techniques
Rolling involves reducing the thickness of metal by passing it through rollers. This method is invaluable for producing sheets and plates used in construction and automotive manufacturing. There are two main types of rolling: hot rolling and cold rolling. Hot rolling occurs above the metal’s recrystallization temperature, while cold rolling occurs at room temperature, resulting in increased strength and finer grain structure.
The benefits of rolling include uniform thickness and enhanced surface finish. However, the process can induce internal stresses in metals, which may require further treatments to alleviate.
Extrusion Methods
Extrusion is a process where metal is forced through a die to create long sections with uniform cross-sections. This technique is widely used for aluminum and other softer metals. Extrusion can be classified into direct and indirect methods. The primary advantage of extrusion is versatility in creating complex shapes that would be difficult to achieve through other methods.
This technique is particularly favorable in the production of pipes, tubing, and structural shapes. The uniformity in cross-section contributes to material efficiency and can significantly reduce waste in production processes.
Sheet Metal Processes
Sheet metal forming encompasses a variety of techniques that manipulate metal sheets into desired shapes. Common processes include bending, deep drawing, and stamping. These techniques are essential in industries such as automotive and electronics, where precision shapes are required.
The benefits of sheet metal processes lie in their efficiency and ability to produce complex geometries quickly. However, material properties can pose challenges, as certain metals may crack or lose integrity during forming. Understanding the limits of the material can enhance process selection and outcomes.
Metal Casting Techniques
Casting is a process involving pouring molten metal into a mold to create a desired shape. This technique allows for intricate designs that may be impractical with other forming methods. It includes processes like sand casting, investment casting, and die casting.
The key advantage of casting is the ability to create large and complex shapes without extensive material waste. However, defects such as porosity and shrinkage can arise, requiring careful control of the casting environment and process parameters.
In summary, an overview of metal forming techniques reveals critical methodologies, each with its unique benefits and drawbacks. The selection depends on various factors including material properties, design complexity, and production costs. Each method contributes to the rich landscape of engineering and manufacturing, shaping the products we use daily.
Materials Used in Metal Forming
The selection of materials in metal forming is of paramount importance. The characteristics of each metal directly influence the manufacturing process and the properties of the final product. Choosing the right material ensures that the formed product maintains structural integrity while also fulfilling its intended functional requirements.
Metal forming techniques require specific types of metals that can withstand and benefit from various processing methods. Understanding these materials allows engineers and designers to predict performance under different conditions, which is essential in sectors such as automotive, aerospace, and construction.
Types of Metals
In metal forming, several key types of metals are commonly utilized.
- Steel: Known for its strength and versatility. It is used especially in automotive and construction applications.
- Aluminum: Lightweight and resistant to corrosion, aluminum is popular in the aerospace sector.
- Copper: Highly conductive and malleable, copper finds its place in electronics and electrical applications.
- Titanium: Strong and lightweight, titanium is frequently used in aerospace due to its favorable strength-to-weight ratio.
- Nickel Alloys: These materials are resistant to high temperatures, making them ideal for specialized industrial applications.
Each of these metals presents unique properties that can be exploited during the forming process, ensuring the final products meet stringent performance expectations.
Alloys and Their Properties
Alloys often provide enhanced properties compared to pure metals. When metals are mixed, they can achieve a balance of strength, ductility, and corrosion resistance. Some notable alloys include:
- Stainless Steel: Offers excellent corrosion resistance and is used in various environments, especially in medical equipment.
- Brass: Combines copper and zinc; it is valued for its workability and aesthetic appeal in consumer products.
- Aluminum Alloys: By adding elements such as copper or silicon, aluminum can be tailored for specific applications, improving strength or resistance to wear.
The adaptability of alloys makes them essential for metal forming, as they provide engineers the toolset to optimize performance across different uses.
Material Selection Criteria
When selecting materials for metal forming, several criteria must be considered:
- Mechanical Properties: Strength, ductility, and hardness are critical to ensure that the metal can withstand forming operations without failing.
- Manufacturability: Consideration of how easily a material can be processed is important. Difficult-to-form materials can result in higher costs and longer production times.
- Cost: Budget constraints often dictate material choice, requiring a balance between performance and affordability.
- Environmental Impact: Sustainable practices require consideration of the ecological footprint of materials, from extraction to production.
- Application Specific Requirements: Each application may impose unique constraints; thus, the material must suit the specific use case.
Understanding these criteria allows stakeholders in metal forming to make informed decisions, which in turn affects product quality and manufacturability.
"Choosing the right material is not just about meeting specifications; it’s about aligning with the broader goals of sustainability and efficiency."
Exploring and selecting materials for metal forming involves evaluating the overall system, including intended use, manufacturing feasibility, and economic factors.
Applications of Metal Forming Products
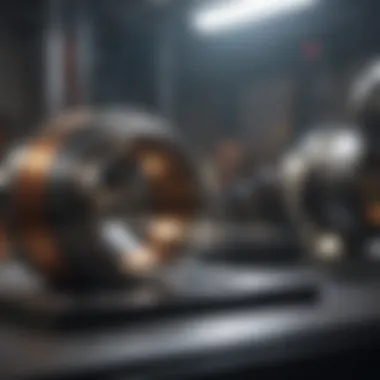
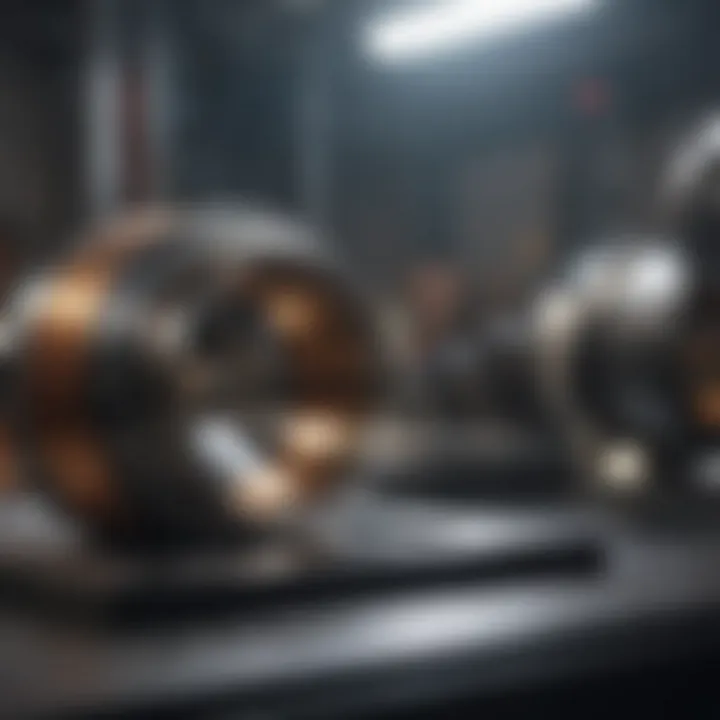
The applications of metal forming products are central to numerous industries, articulating their importance in engineering and manufacturing. Metal forming encompasses several techniques to shape materials into desired forms, which leads to a broad spectrum of applications. Industries leverage metal forming to enhance product performance, achieve design specifications, and meet safety standards. The benefits of using metal forming products include improved material properties, cost-effectiveness, and the ability to create complex geometries that would be difficult or impossible to achieve through other methods.
Automotive Industry
In the automotive industry, metal forming plays a pivotal role. Vehicles require numerous metal components, from body panels to structural supports. Techniques such as stamping and forging are prevalent in this field. Stamping, in particular, is used to create sheet metal parts with precise dimensions and a high level of repeatability.
Metal forming not only contributes to the structural integrity of vehicles but also aids in weight reduction, which enhances fuel efficiency.
The use of advanced high-strength steels allows manufacturers to produce lighter parts without compromising safety. Additionally, innovations such as hot stamping and hydroforming are gaining traction, providing manufacturers with more ways to produce complex shapes efficiently.
Aerospace Sector
The aerospace sector also heavily relies on metal forming to produce lightweight and durable components. The demand for materials that can withstand extreme conditions requires sophisticated techniques like superplastic forming. This method enables the creation of intricate shapes essential for aircraft design.
The use of titanium and aluminum alloys is common due to their favorable strength-to-weight ratios. These materials undergo forming processes to create parts like fuselage components and wing structures. The ability to seamlessly integrate various metal-forming techniques is crucial in meeting aerospace safety standards and optimizing performance.
Construction and Infrastructure
In construction and infrastructure, metal forming products are integral to structural framework and support systems. Products such as beams, columns, and reinforcements are often fabricated through processes like rolling and extrusion. Rolling techniques produce steel sheets and plates vital for building infrastructures, ensuring they can withstand various loads.
Another significant application includes the use of rebar, which is commonly formed to reinforce concrete structures. The strength and durability achieved through these processes are essential for the safety and longevity of buildings and infrastructure, making metal forming indispensable in this sector.
Consumer Electronics
Consumer electronics constitute another exciting area for metal forming. Products like casings, brackets, and internal components utilize metal forming techniques such as stamping and extrusion. Manufacturers aim for precision and aesthetic appeal. Moreover, with the trend of miniaturization in gadgets, forming techniques must adapt to create smaller, more complex components while maintaining functionality. These products often require tight tolerances and high-quality finishes, making metal forming an ideal solution.
Medical Equipment Manufacturing
The medical equipment manufacturing sector greatly benefits from metal forming as well. Instruments, implants, and devices demand high precision and biocompatibility. Processes like cold forming and machining are extensively used to create reliable and sterile medical devices.
Metal forming allows for intricate designs that are essential for certain applications like surgical instruments or orthopedic implants. The reliability and performance of these products depend heavily on the forming techniques employed, and thus, manufacturers invest significantly to innovate in this area.
In summary, the applications of metal forming products across various sectors highlight their versatility and importance. Understanding these applications offers a clear insight into how integral metal forming is to advancing technology and meeting industry standards.
Innovations in Metal Forming
Innovations in metal forming significantly shape the landscape of manufacturing. These advancements not only enhance traditional techniques but also introduce new possibilities that redefine production capabilities. Important elements of innovation include additive manufacturing, digital fabrication techniques, and automation and robotics. Each area contributes unique benefits, such as increased efficiency and improved design flexibility. Considering these innovations is crucial as industries seek to optimize processes and reduce waste while adhering to ever-evolving market demands.
Additive Manufacturing
Additive manufacturing, commonly known as 3D printing, revolutionizes the way metal products are created. By building components layer by layer, it allows for complex geometries that are often impossible with conventional methods. This technique reduces material waste and enables rapid prototyping. Industries like aerospace and medical benefit greatly from additive manufacturing, as it provides lightweight and custom-designed components efficiently.
Some key benefits include:
- Customization: Tailored designs specific to client needs.
- Reduced Lead Times: Faster production cycles compared to traditional methods.
- Environmental Benefits: Less material waste during production.
The implications for product development are vast. Companies can experiment with new designs without the hefty costs associated with traditional tooling processes. As the technology matures, we can expect broader adoption in various sectors.
Digital Fabrication Techniques
Digital fabrication techniques encompass a range of processes that merge computer-aided design (CAD) with manufacturing. This approach streamlines production and enhances precision. Techniques such as laser cutting, waterjet cutting, and CNC machining fall under this category.
With digital fabrication, engineers can:
- Achieve Higher Precision: Significantly improved accuracy in designs.
- Enhance Flexibility: Ability to change designs on the fly without extensive rework.
- Reduce Material Costs: Optimal material usage through precise cuts and designs.
Adopting these techniques leads to faster turnaround times and the capability to produce intricate designs. As industries push for more efficient practices, digital fabrication becomes increasingly relevant.
Automation and Robotics
Automation and robotics play pivotal roles in transforming metal forming operations. By integrating automated systems, businesses can reduce human error, lower labor costs, and enhance overall efficiency. Automated systems like robotic arms handle material movement, precision cutting, and assembly processes that typically require significant human effort.
Several advantages of automation include:
- Increased Productivity: Higher output rates due to reduced downtime.
- Consistency in Quality: Uniformity in product quality through precise control.
- Safety Improvements: Reducing human exposure to potentially dangerous work environments.
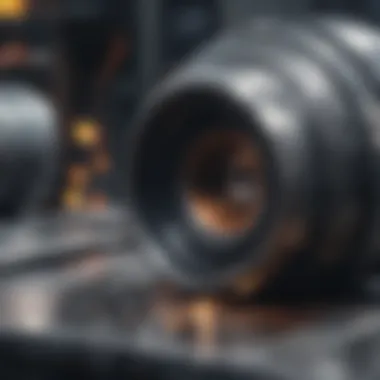
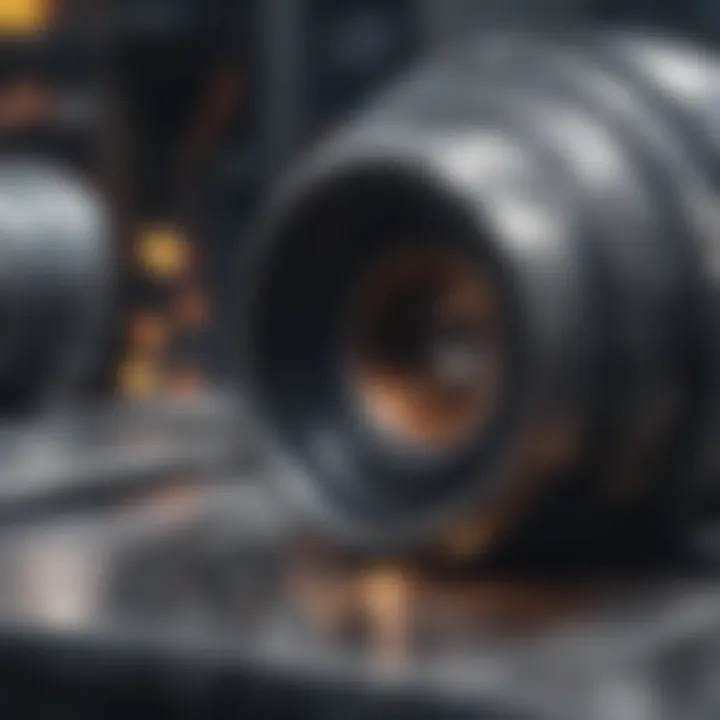
Non-typical sectors, such as custom metal forming firms, benefit immensely from scaling operations with robotics. As technology progresses, further integration of automation in metal forming is inevitable.
"Innovations in metal forming not only enhance traditional manufacturing processes but also pave the way for sustainable practices and advanced designs."
Challenges in Metal Forming
The field of metal forming encounters several complex challenges. These challenges play a significant role in the overall efficiency and effectiveness of the manufacturing process. Addressing issues related to economic factors, environmental concerns, and technical limitations is crucial for the future of metal forming. Unpacking these elements provides insights into the constraints faced by industries and suggests areas for innovation and improvement.
Economic Factors
Economic factors significantly influence the metal forming industry. The fluctuating costs of raw materials can affect production budgets. For instance, the prices of metals like steel, aluminum, and copper vary based on market demand and supply chain stability. These price instabilities can make it difficult for manufacturers to create precise financial projections. Manufacturers must adopt strategies to mitigate risks associated with these fluctuations.
Additionally, competition in the market leads to a constant push for cost reduction. Organizations aim to reduce expenses without compromising product quality. This often requires investments in new technologies and processes. For smaller companies, this can mean challenges in accessing capital for such advances. Larger entities can absorb costs better, potentially leading to market monopolization that can squeeze smaller competitors.
Lastly, the labor market presents another economic challenge. Skilled labor is required for intricate processes within metal forming, yet there is often a shortage in this area. This shortage can drive up wages and lead to increased operational costs. Companies may need to invest in training programs or technology that compensates for labor shortages.
Environmental Concerns
The environmental implications of metal forming are becoming increasingly critical. The manufacturing process can contribute to significant waste and emissions, which are now under scrutiny from both regulators and consumers. Metal forming techniques often involve high energy consumption, contributing to greenhouse gas emissions. As awareness grows around climate change, the pressure mounts on manufacturers to adopt more sustainable practices.
To address these concerns, companies must consider recycling and resource efficiency. Implementing systems that optimize resource usage, reduce scrap, and recycle waste can aid in lessening environmental impact. Furthermore, employing cleaner technologies in production processes can also contribute to sustainability goals. This is where innovation plays a crucial role. Companies exploring environmentally-friendly materials, energy-efficient machinery, or even biodegradable lubricants can position themselves favorably in the market.
In addition to regulations, consumer preferences are shifting towards sustainable products. Manufacturers that can demonstrate their commitment to environmental stewardship often gain competitive advantages. Engaging with eco-conscious practices is not just ethical; it is also a strategic business move.
Technical Limitations
Technical limitations present a constant challenge within the metal forming industry. These limitations can arise from both material properties and manufacturing technology. For example, some metals have inherent limitations on formability. The intricacies of certain alloys can lead to issues like cracking or slipping during processes such as stamping or bending.
Moreover, as technology evolves, keeping up with advancements becomes a hurdle for many manufacturers. The integration of new tools, machines, or software demands retraining staff and re-evaluating existing processes. This can lead to temporary setbacks or inefficiencies as companies transition. Failure to innovate can result in losing competitive ground to businesses that embrace technological advancements.
Manufacturers also face compatibility issues when integrating new technologies with legacy systems. This can slow down operations and increase costs as companies invest time and resources to bridge the gap.
Future Trends in Metal Forming
The field of metal forming is continually evolving as technologies and methods advance. Understanding the future trends in metal forming is vital for industries reliant on precision metal parts. It shapes strategies, influences product development, and enhances competitiveness. As companies strive for efficiency, quality, and sustainability, they must be aware of emerging trends, ensuring they remain relevant in a fast-paced environment.
Sustainable Practices
In recent years, sustainability has become a focal point for many businesses. In metal forming, this shift is influenced by the need to reduce waste and energy consumption. Sustainable practices involve a range of strategies, including the use of recyclable materials and energy-efficient technologies.
One simple approach is to leverage advanced manufacturing techniques such as near-net-shape manufacturing. This method minimizes material waste by shaping components closer to their final form. Additionally, companies can adopt green energy sources to power their operations, reducing their carbon footprint over time.
Moreover, many organizations are beginning to implement lifecycle assessments. This helps in evaluating the environmental impacts of products from production through disposal. By using this information, industry players can make informed decisions that align with sustainability goals.
Integration of AI and IoT
The role of Artificial Intelligence (AI) and the Internet of Things (IoT) in metal forming is expanding. These technologies offer unparalleled opportunities for increasing efficiency and improving accuracy. Smart sensors can be integrated into machinery, providing real-time data on performance and product quality.
With AI, predictive analytics can be employed to foresee potential issues in production lines. For example, failures can be predicted before they occur, reducing downtime and saving costs. Additionally, AI can analyze vast amounts of data, optimizing processes significantly.
On the other hand, IoT facilitates connectivity within machinery. It enables machines to communicate with one another, fostering an environment conducive to smart manufacturing. This integration also supports remote monitoring, allowing for prompt responses to any equipment irregularities.
In summary, as metal forming faces new challenges and opportunities, embracing sustainable practices and integrating advanced technologies like AI and IoT will be crucial. Adapting to these trends will not only improve efficiency and reduce environmental impact but also pave the way for innovative solutions that will define the future of the industry.
Finale
The conclusion of an article on metal forming products encapsulates the breadth of the subject covered. This section brings together the various discussions regarding techniques, applications, and innovations, which are paramount for understanding the landscape of metal forming. By iterating over key findings, it emphasizes the significance of metal forming within the engineering and manufacturing sectors.
A well-structured conclusion reinforces the benefits of these techniques and highlights their various applications in real-world scenarios. The insights highlighted lead readers to better appreciate the advancements in metal forming and their implications for industries such as automotive, aerospace, and construction.
Recap of Key Points
In summarizing the entire discourse, several key points emerge as focal elements in the field of metal forming:
- Diverse Techniques: Forging, rolling, extrusion, and casting each play distinct roles in producing metal components. Understanding their differences aids in selecting appropriate methods for specific projects.
- Material Selection: The choice of materials has a pronounced impact on the final product's performance and durability. Recognizing the properties of various metals and alloys is crucial to industrial applications.
- Innovations and Trends: The integration of technologies such as additive manufacturing and automation represents significant shifts in traditional practices. Keeping up with these changes is essential for industry professionals.
- Challenges and Future Directions: Economic and environmental factors continue to influence production methods. Research into sustainable practices will shape future developments in the field.
Implications for Future Research
Future research in metal forming should focus on the intersection of technology and sustainability. As industries seek to minimize their environmental impact, identifying methods to enhance efficiency and reduce waste will be critical. Additionally, exploring advancements in artificial intelligence and machine learning can facilitate better design and production processes.
Furthermore, interdisciplinary studies that incorporate materials science and engineering can yield new insights. Such collaborations may enhance the understanding of how different materials respond to various forming techniques, leading to more innovative applications.
Lastly, with ongoing globalization, research on international standards and practices can bolster competitiveness and collaboration among manufacturers across the globe. Engaging with these areas will be essential for fostering advancements and addressing the challenges faced within the sector.