Forging Nickel: Methods, Applications, and Trends
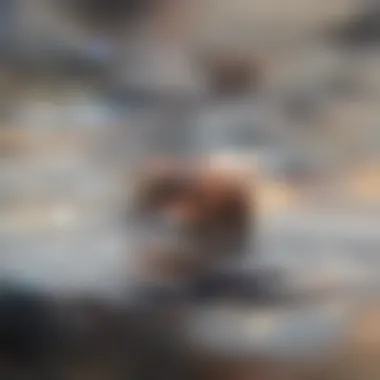
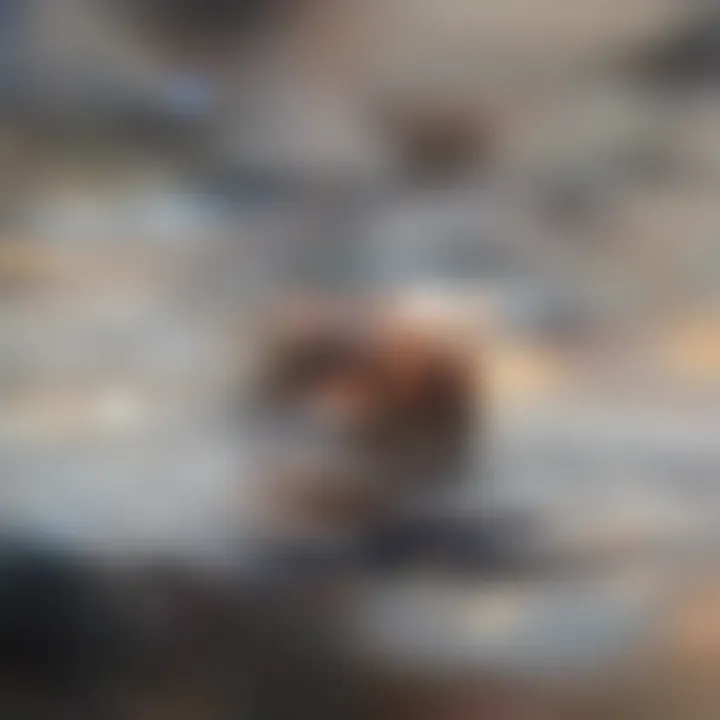
Intro
The study of forging nickel unveils a significant facet of materials science and engineering. Nickel, a versatile metal, plays a crucial role in a wide array of applications, ranging from aerospace components to automotive technologies. The process of forging this metal combines both artistry and science, molding raw materials into sophisticated designs that meet demanding specifications. Understanding the intricacies of forging nickel not only offers insights into its applications but also highlights its unique material properties, making it an essential element in modern industry.
In this article, we will explore the various methodologies involved in forging nickel, the challenges that engineers face, and the transformative applications that this metal supports. By examining these elements, we aim to provide a well-rounded understanding of how nickel enhances engineering outcomes across multiple sectors.
Key Concepts
Definition of Primary Terms
When discussing forging, it is essential to clarify some key terms:
- Forging: The process of shaping metal by applying compressive forces, often through hammering or pressing.
- Nickel: A silvery-white metal known for its corrosion resistance and strength, typically alloyed with other metals.
- Alloy: A combination of two or more elements, at least one of which is a metal. Nickel alloys are used to enhance strength and durability.
Related Concepts and Theories
In forging nickel, several theories come into play. The detailed understanding of heat treatment processes and deformation mechanics is relevant here. Heat treatment influences the mechanical properties of nickel alloys, affecting hardness, ductility, and tensile strength. Other concepts include:
- Thermal Processing: A method to change the properties of metals through controlled heating and cooling.
- Deformation Theory: Explains how materials behave under various stresses, aiding in predicting how nickel will respond during forging.
These concepts lay a foundation for comprehending the complexity of forging processes and their resulting material properties.
Future Directions
Gaps Identified in Current Research
While substantial knowledge exists regarding forging nickel, certain gaps remain. Research often overlooks specific alloys of nickel and their performance under extreme conditions. Further studies are crucial to filling these voids in understanding.
Suggestions for Further Studies
More research into additive manufacturing techniques could also be beneficial. The integration of traditional forging with modern technology presents possibilities for creating more durable and innovative designs. Future studies should focus on:
- Analyzing the long-term performance of nickel in aerospace applications.
- Exploring environmentally sustainable practices within the forging process.
Such investigations will not only broaden the current knowledge base but also pave the way for advancements in relevant industries.
Foreword to Nickel Forging
Nickel forging represents a critical area in materials science and engineering. As industries increasingly demand materials with enhanced properties, the significance of forging nickel cannot be overstated. This process affects the overall performance, durability, and reliability of components used in high-stress applications.
Definition of Forging
Forging is a manufacturing process that involves shaping metal using localized compressive forces. This can be accomplished through various methods such as hammering, pressing, or rolling. The primary goal is to improve the material's strength and refine its microstructure. Unlike casting, forging promotes grain flow and enhances mechanical properties, making components more suited for rigorous environments. The understanding of forging is essential for anyone engaging in materials engineering, as it lays the groundwork for producing high-performance items.
Role of Nickel in Forging
Nickel plays a vital role in forging, particularly due to its unique properties. It is known for its excellent corrosion resistance, high-temperature stability, and remarkable strength. These characteristics make nickel alloys highly desirable in places where components experience extreme conditions.
Nickel is often alloyed with other metals like chromium and molybdenum to further enhance these attributes. By understanding how nickel interacts during the forging process, manufacturers can create materials that meet the stringent requirements of various applications. The role of nickel in forging is not merely functional; it is foundational to the development of modern engineering solutions.
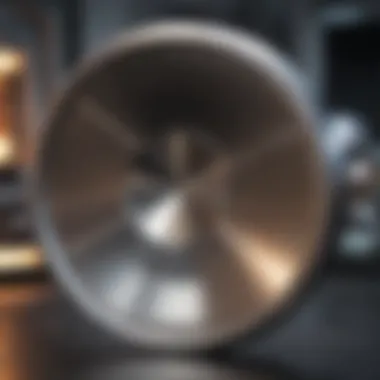
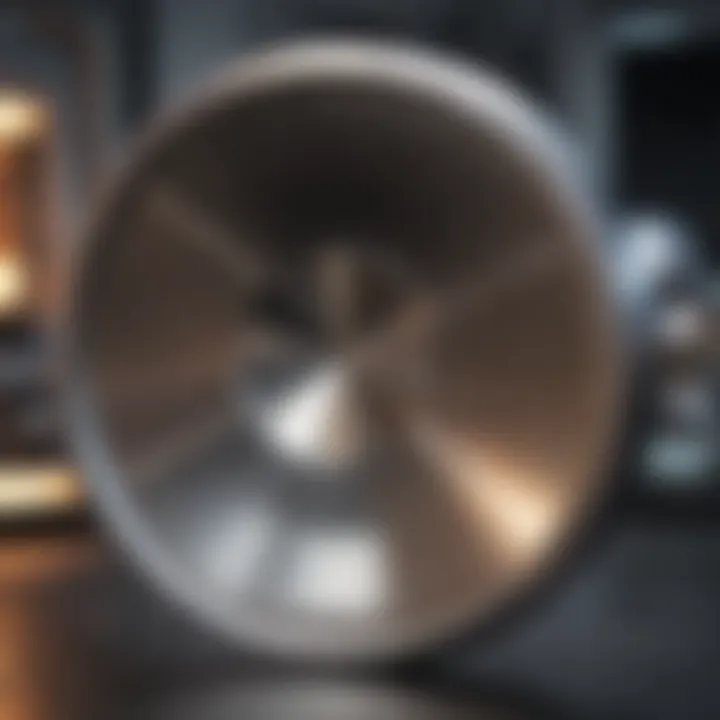
"Forging nickel-based alloys yields superior material performance, essential for critical applications."
Through careful analysis and methodical application, the contribution of nickel to forging processes becomes clear. It transforms raw materials into high-performance components capable of withstanding the challenges of modern engineering.
Properties of Nickel Alloys
Nickel alloys are significant in the forging process due to their unique properties, which enhance their suitability for various applications. These alloys not only improve the product's performance but also contribute to the longevity of components made from them. Understanding the properties of nickel alloys is essential for anyone involved in forging or utilizing forged components.
Mechanical Characteristics
Mechanical characteristics of nickel alloys make them an ideal choice for high-stress applications. They exhibit excellent mechanical strength and ductility, allowing for deformation without fracture. These two properties play a critical role in processes such as forming and shaping, making nickel alloys robust in demanding environments.
- Strength: Nickel alloys maintain their strength even at elevated temperatures. This trait is crucial for applications like aerospace and automotive engineering where high performance is vital.
- Ductility: Ductility refers to the ability of a material to deform under stress. Nickel alloys are known for their good ductility, which allows them to be easily forged into different shapes without losing integrity.
- Toughness: The toughness of nickel alloys also contributes to their resistance against impact and fatigue. This property is particularly important for components subjected to cyclic loading, as seen in machinery and tools.
Corrosion Resistance
Corrosion resistance is another critical feature of nickel alloys. These alloys can withstand harsh environments, with many applications requiring materials that resist oxidation and corrosion.
- Oxidation Resistance: Nickel forms a protective oxide layer on its surface, which significantly improves its ability to resist oxidation. This characteristic is especially beneficial for parts exposed to high temperatures.
- Chemical Resistance: Nickel alloys demonstrate good resistance against various chemicals, including acids and bases. This makes them valuable in industries like chemical processing and marine environments, where exposure to corrosive substances is common.
- Longevity: The corrosion-resistant nature of nickel alloys typically leads to an extended lifespan for components. This results in less frequent replacements and lower maintenance costs, enhancing overall efficiency in industrial applications.
Thermal Conductivity
The thermal conductivity of nickel alloys is another important aspect. In engineering applications, heat transfer can significantly affect performance. Nickel alloys possess favorable thermal properties that contribute to their versatility.
- Conductivity: Nickel has relatively high thermal conductivity, allowing heat to move through the material efficiently. This is beneficial in applications where rapid heat dissipation is required, such as in engines or heat exchangers.
- Thermal Stability: In combination with their mechanical properties, nickel alloys maintain structural integrity at elevated temperatures. This stability is essential for components that operate under conditions of extreme heat.
- Applications Impact: This attribute makes nickel alloys suitable for a wide range of applications, from aerospace components that encounter fluctuating temperatures to industrial machinery operating under continuous heat.
The properties of nickel alloys, including mechanical characteristics, corrosion resistance, and thermal conductivity, establish them as a material of choice for industries requiring durability and performance under demanding conditions.
In summary, understanding the properties of nickel alloys highlights their advantages in engineering and manufacturing. This knowledge illustrates why nickel remains a critical material in forging applications across varied industries.
Forging Processes Involved
The topic of forging processes is crucial in the exploration of nickel as a material in various industries. Forging is a key manufacturing process that involves shaping metal using compressive forces. When it comes to nickel, understanding the different techniques of forging aids in maximizing its impressive properties while minimizing the risks associated with its use. This section aims to shed light on the specific forging processes that are essential in working with nickel, focusing on hot forging, cold forging, and precision forging methods.
Hot Forging Techniques
Hot forging is a popular technique used to shape nickel alloys, especially at high temperatures. The significant benefit of hot forging is the reduced flow stress of the material when it is heated. This makes the shaping process easier and allows for complex geometries. In this technique, metal is heated above its recrystallization temperature which decreases its strength and increases ductility.
The steps involved in hot forging are relatively straightforward:
- Heating the nickel alloy to a specific temperature.
- Applying compressive force to shape it into the desired form.
- Cooling the shaped component at a controlled rate.
During hot forging, care must be taken to avoid overheating, as it may lead to unwanted grain growth, affecting the final properties of the product. This method is particularly beneficial for applications requiring components that need to endure high-stress environments, such as in the aerospace sector.
Cold Forging Techniques
Cold forging differs from hot forging in that it is performed at or near room temperature. This process is advantageous in producing parts with superior surface finish and tighter tolerances without the need for machining. Cold forging utilizes higher strength and improved material properties due to the strain hardening effect. When nickel alloys are put through cold forging, their mechanical properties can greatly enhance, making them suitable for several applications.
Some advantages of cold forging processes include:
- No heating required, which results in lower energy consumption.
- Improved surface finish, reducing the need for subsequent machining.
- Better dimensional accuracy due to lower thermal expansion during processing.
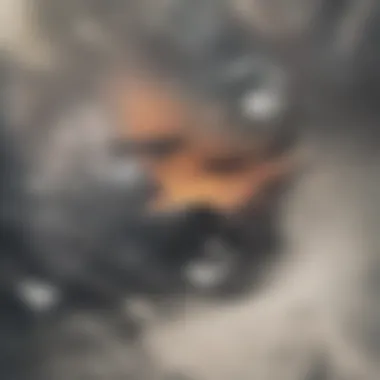
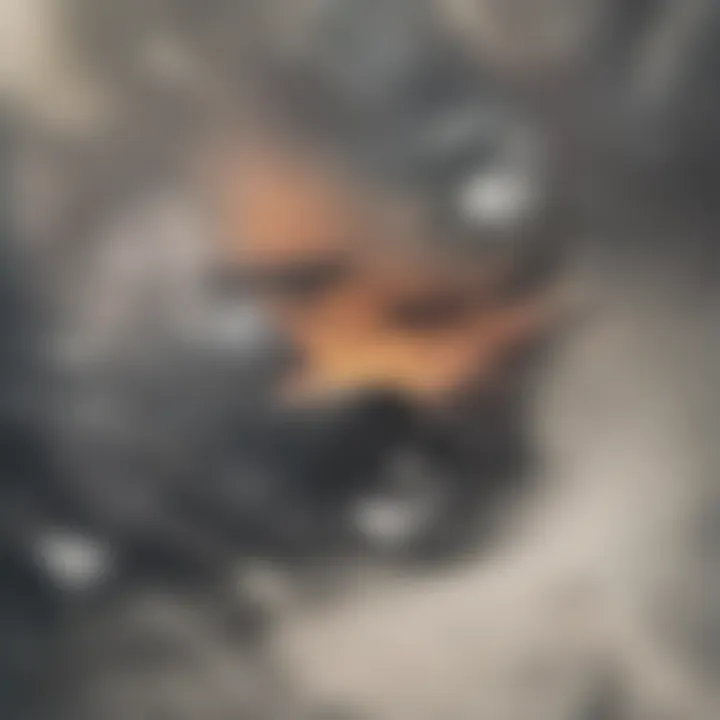
However, cold forging may not be suitable for all shapes and sizes due to material limitations. Notably, brittle materials should be avoided in this process.
Precision Forging Methods
Precision forging involves advanced techniques that enable the production of high-accuracy components. This process often incorporates the use of computer numerical control (CNC) technology and can achieve tolerances as tight as ยฑ0.01 mm. The principal objective of precision forging is to reduce post-forging machining operations, leading to cost savings and efficiency.
Precision forging typically employs two common techniques: near-net shape forging and intricate design forging. Both allow manufacturers to design components that fit specific application requirements, particularly in sectors demanding high precision, such as medical device manufacturing and aerospace components.
Precision forging not only assures dimensional accuracy but also optimizes material utilization, reducing waste during production.
Applications of Forged Nickel Components
Forged nickel components play an essential role across multiple industries, showcasing unique properties that make them indispensable. The applications vary widely, reflecting the versatility of nickel as a material. Both the inherent properties of nickel alloys and the specific requirements of each sector influence the choice of nickel components.
Nickel's strength, durability, and resistance to corrosion render it particularly beneficial in demanding environments. As industries continually seek to improve efficiency and performance, the use of forged nickel components is increasingly prominent. This section explores four prominent sectors where these components are crucial.
Aerospace Industry
In aerospace, the requirements for materials are stringent. Components must withstand extreme conditions, including high temperatures and pressures. Forged nickel alloys are favored in this sector due to their exceptional strength-to-weight ratio and fatigue resistance.
Forged nickel parts such as turbine discs and fan blades are fundamental to aircraft engines. These components must endure cyclical stresses while providing reliable performance. Moreover, the resistance to oxidation and corrosion in high-temperature environments greatly enhances their longevity. This allows manufacturers to focus on performance and safety without compromising weight.
Automotive Engineering
The automotive industry is another major user of forged nickel components. Here, the emphasis is on performance, durability, and safety. Nickel alloys are commonly used in a variety of car components, including crankshafts, connecting rods, and transmission gears.
These components often operate under significant stress and need to withstand wear. The use of forged nickel improves overall vehicle performance and extends the lifespan of engine parts. Additionally, these materials can help reduce vehicle weight, contributing to better fuel efficiency.
Energy Sector
Forged nickel components are vital in the energy sector, especially in renewable energy applications. Wind turbines and power plants require parts that can resist various environmental factors and stresses. For instance, nickel-based alloys are commonly used in turbine blades and valve components in power generation facilities.
The corrosion resistance of nickel also makes it suitable for use in oil and gas applications, where equipment is frequently exposed to corrosive substances. Forged nickel components help ensure operational reliability and safety, thus enhancing overall efficiency in energy production.
Medical Devices Manufacturing
In the medical field, the demand for reliability and safety is paramount. Forged nickel components are used in various medical devices, including surgical instruments and implants. The biocompatibility of nickel, along with its resistance to corrosion, makes it an ideal choice for these applications.
In implants, forged nickel alloys can provide strength and durability, supporting loads in joint replacements or dental applications. The precision and reliability of forged components ensure that medical devices perform optimally over time. This usage underlines how critical material selection is in enhancing patient care and outcomes.
Forged nickel alloys facilitate advancements across several high-stakes industries, aiding in intensive applications that prioritize strength and reliability.
Challenges in Nickel Forging
Nickel forging presents a distinct set of challenges that can affect the overall efficiency and effectiveness of the manufacturing process. Understanding these issues is vital for professionals engaged in metallurgy and engineering. Problems such as material deformation, fracture risks, and the high costs associated with nickel materials create barriers to optimization and innovation. Each challenge demands attention and requires specific strategies to mitigate risks. Addressing these concerns enhances not only the viability of nickel forging but also its applications in various industries.
Material Deformation Issues
Material deformation is a significant challenge in the forging of nickel. The unique properties of nickel alloys can often lead to unexpected changes in shape during the forging process. Factors such as temperature, strain rate, and the specific forging method used can all contribute to these deformation issues.
When heated, nickel alloys exhibit different responses compared to other metals. Inconsistencies in temperature control can lead to uneven thermal expansion. As a result, it can generate stresses that cause the material to warp or twist. This can lead to components failing to meet precise specifications. Engineers must find optimal temperature ranges and techniques to minimize deformation, ensuring the integrity of the final product.
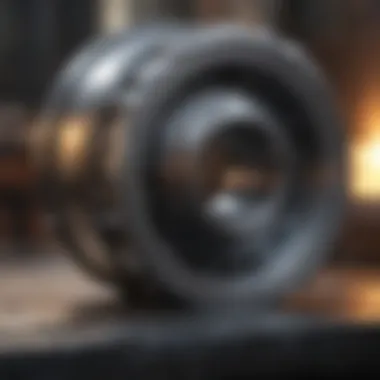
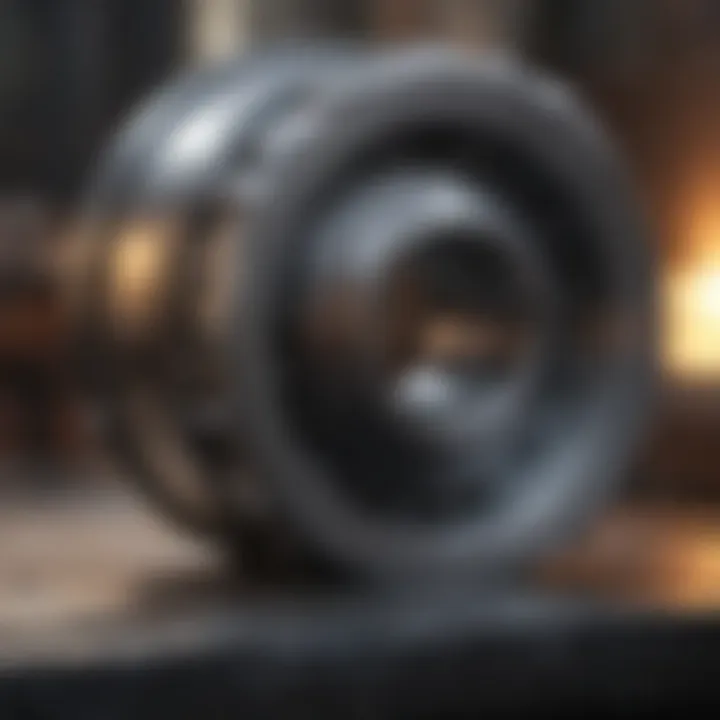
Fracture and Defect Formation
Fracture and defect formation is another major challenge faced during nickel forging. The mechanical properties of nickel alloys can be influenced by various factors, such as impurities in the material or inadequate processing techniques. These can lead to microstructural flaws that compromise the strength and reliability of the forged components.
Improper forging processes can induce stress concentrations, resulting in cracks or voids. High temperatures necessary for the forging process might also lead to grain growth and adversely affect mechanical performance. Therefore, rigorous testing and quality control measures are essential. Proper handling and inspection reduce the likelihood of defects, ensuring that forged components meet industry standards.
High Cost of Nickel Materials
The economics of nickel forging is heavily influenced by the high cost of nickel materials. Nickel is a critical alloying element, prized for its strength, corrosion resistance, and thermal stability. Nonetheless, its price can fluctuate significantly based on market trends and availability. This creates a challenge for manufacturers trying to maintain profitability while offering competitive products in the marketplace.
To address cost concerns, companies often explore ways to enhance efficiency in their forging processes. Investing in advanced forging technologies and optimizing material usage can prove beneficial. Recycling scrap nickel and reducing waste in the production cycle can also mitigate financial burdens.
"The increasing costs of nickel materials necessitate innovative solutions in forging practices to sustain industry growth."
This comprehensive understanding of the challenges in nickel forging will guide industry stakeholders in developing effective strategies. By tackling these obstacles, stakeholders can improve product quality and ensure the continued relevance of nickel in advanced applications.
Future Trends in Nickel Forging
The realm of nickel forging is undergoing a significant transformation influenced by advancements in technology, sustainability efforts, and increased focus on recycling. As industries evolve and demand for high-performance materials grows, understanding these future trends is essential for professionals and researchers alike. This section will uncover specific elements reshaping nickel forging, highlighting benefits and considerations that accompany these trends.
Advancements in Technology
Technological advancements play a critical role in the future of nickel forging. Innovative techniques, such as additive manufacturing and computer simulation, are enhancing traditional forging methods. For instance, numerical modeling allows for better understanding of die behavior and material flow during the forging process. This leads to improved precision and reduced wastage. Moreover, machine learning is gradually being integrated, offering predictive maintenance solutions that can extend the lifespan of forging equipment.
The use of robotics is another notable development. Automated systems can execute complex forging tasks, which minimizes human error and increases productivity. Enhanced sensors and monitoring tools permit real-time quality control throughout the forging process. This integration of technology provides opportunities for higher efficiency and cost-effectiveness, ultimately benefiting manufacturers and consumers alike.
Sustainable Practices in Forging
Sustainability has become a focal point in many manufacturing sectors, including nickel forging. As global awareness regarding environmental impact rises, companies are adopting sustainable practices to reduce their carbon footprint. One approach is to optimize energy consumption in forging operations. By incorporating energy-efficient machinery and utilizing renewable energy sources, companies can significantly decrease greenhouse gas emissions.
Furthermore, manufacturers are exploring the potential for bioplastics and other eco-friendly materials in conjunction with nickel forging. This not only aligns with environmental goals but also meets the growing consumer demand for green products. Companies implementing such strategies are likely to gain a competitive advantage in the marketplace.
Recycling and Material Recovery
The importance of recycling and material recovery in nickel forging cannot be overstated. As resources become scarcer, the focus on reusing materials is intensifying. Nickel alloys are particularly amenable to recycling, maintaining their fundamental properties through repeated cycles. This allows manufacturers to reclaim significant portions of scrap material generated during the forging process.
Organizations are investing in advanced recycling technologies that facilitate the recovery of nickel and other valuable metals from waste products. These efforts not only contribute to sustainability but also help mitigate the high costs associated with nickel acquisition. As such, the emphasis on recycling will likely continue to grow within the industry, leading to a positive impact on both the economy and the environment.
"Investing in recycling and sustainable practices in nickel forging is not just a compliance measure; it is a strategic necessity for future competitiveness."
Closure
In the realm of engineering, the forging of nickel emerges as an essential process. It involves shaping metal through compressive forces, which results in enhancements to the material's structural integrity. Many industries rely on forged nickel components due to their mechanical properties and durability. This article has explored various facets of nickel forging, from its fundamental definitions to the challenges faced in production.
Summary of Key Points
The following points summarize the crucial aspects discussed in this article:
- Defining Forging: Forging is a manufacturing process that forms materials into desired shapes by applying significant pressure.
- Nickel's Role: Nickel is integral to producing strong, corrosion-resistant alloys, enhancing mechanical properties across applications.
- Forging Techniques: Different methods such as hot forging and cold forging cater to specific needs, optimizing efficiency and output.
- Applications: Key fields like aerospace, automotive, and energy utilize forged nickel for its reliability and strength.
- Challenges: Difficulties such as material deformation and high production costs cannot be overlooked and need effective strategies.
- Future Trends: Emerging technologies and sustainability efforts play a significant role in shaping the future landscape of nickel forging.
Each of these points showcases the complexity of the process and its wide-ranging implications for industry.
The Importance of Continued Research
Research into nickel forging is vital for several reasons. First, addressing the existing challenges can lead to improved manufacturing practices. For instance, advancements in forging technology can help lower costs and enhance efficiency. Additionally, research can identify innovative alloys and techniques that increase performance in extreme conditions. Furthermore, focusing on sustainable practices can aid in reducing environmental impact while maintaining the quality of products.
Investments in research can yield breakthroughs that not only benefit current industries but also open doors to new applications. As global demand for high-quality materials grows, continuous exploration in nickel forging becomes increasingly important. This ongoing dialogue will ensure that the industry evolves, keeping pace with technological advances and changing market needs.