Gala Pelletizers: Applications and Technologies Explained
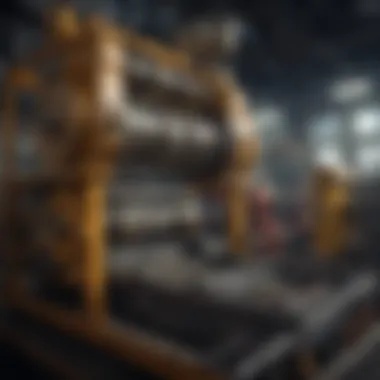
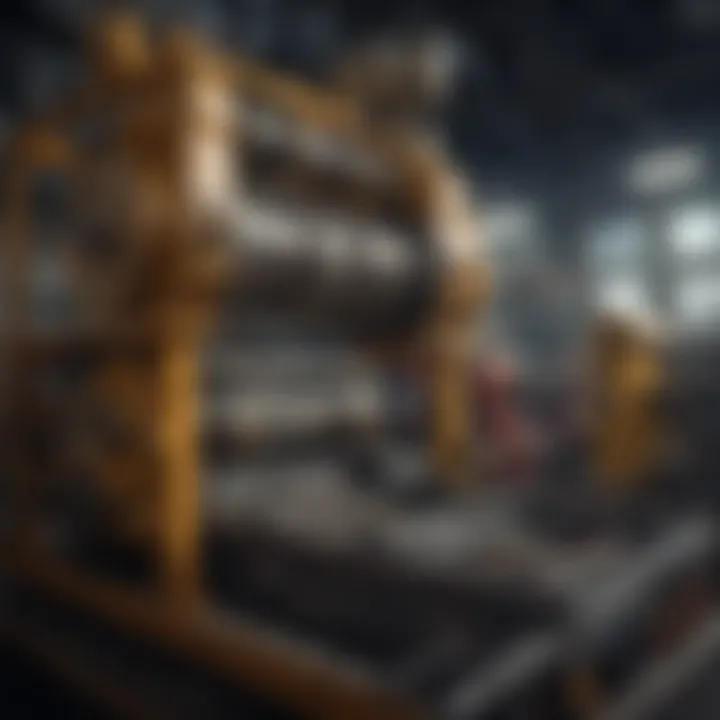
Intro
The field of manufacturing continues to evolve. This evolution brings forward new technologies and methods that enhance production efficiency. One such advancement is the gala pelletizer. Understanding its applications and technologies is crucial for professionals in the field. This article aims to unravel the complexities of gala pelletizers, exploring their operational mechanisms and various uses.
Key Concepts
Definition of Primary Terms
Gala pelletizers are specialized machines that convert raw materials into uniform pellets. These pellets are typically used for various applications, including food production, pharmaceuticals, and plastics. The core function of a pelletizer involves forming, drying, and cooling the pellets.
Key terms related to this topic include:
- Pelletization: The process of compressing or molding materials into the shape of pellets.
- Feedstock: The raw material supplied to the pelletizer.
- Extruder: A device that helps in forming the pellets by forcing the feedstock through a die.
Related Concepts and Theories
Gala pelletizers operate based on principles of mechanical engineering and material science. The principle of extrusion is fundamental in understanding how material shape changes occur. This principle plays a significant role in defining the consistency and quality of the produced pellets. Additionally, advancements in thermodynamics are relevant. They influence the temperature control during the pelletization process, impacting the physical properties of the final product.
Applications of Gala Pelletizers
Gala pelletizers serve a broad spectrum of applications across various industries. Some of the primary sectors include:
- Pharmaceuticals: In this industry, pelletization enhances drug delivery systems, offering controlled release of medication.
- Food Production: Here, pelletizers help create uniform feed for animals, ensuring consistent nutritional value.
- Plastics Manufacturing: Pellets of plastic materials can be easily processed in molding machines, streamlining production.
Each application benefits uniquely from the capabilities of gala pelletizers, making them indispensable in modern manufacturing.
Advantages and Disadvantages of Gala Pelletizers
While there are many advantages to using gala pelletizers, some disadvantages must be acknowledged.
Advantages include:
- Efficiency: The ability to produce uniform pellets minimizes waste.
- Flexibility: They can process a variety of feedstocks and adapt to different manufacturing needs.
- Cost-Effectiveness: Reducing the need for further processing can lower overall production costs.
Disadvantages can encompass:
- Initial Investment: The setup cost for advanced pelletizing machinery can be significant.
- Maintenance: Regular maintenance is essential to ensure consistent operation and product quality.
"Understanding both the advantages and disadvantages is essential for making informed decisions on the application of pelletizers."
Future Directions
Gaps Identified in Current Research
Despite the evidently transformative impact of gala pelletizers, there are gaps in current research. These include limited studies on the long-term effects of using different feedstocks and the environmental impact of pelletization processes.
Suggestions for Further Studies
Further investigation should focus on:
- Developing sustainable materials for pellet production to reduce environmental footprint.
- Exploring advanced data analytics in optimizing pelletizing processes for better product quality.
Understanding Gala Pelletizers
Gala pelletizers represent a crucial technology in modern manufacturing, crucially linked to various industries. Their significance lies in their ability to transform raw materials into usable products efficiently. This transformation not only enhances material handling and processing but also optimizes overall production processes. In an era where sustainability and efficiency are paramount, understanding gala pelletizers ensures that industries can leverage their capabilities fully.
Definition and Purpose
Gala pelletizers are machines designed to convert bulk materials into uniform pellets through compression and shaping. They serve an essential function across diverse sectors, including agriculture, energy, and recycling. The primary purpose of these machines is to create a product that is easier to transport and handle while ensuring consistency in size and quality.
These pelletizers function by utilizing a series of mechanisms to condense raw materials by applying pressure and heat. The resulting pellets often possess desirable characteristics such as uniformity, higher density, and improved combustion or digestibility. Such attributes make them suitable for various applications, thus expanding their utility and importance in different industries.
Historical Context
The development of pelletizing technology can be traced back several decades. Originally, the concept was applied to agricultural feed production, where fostering consistency and enhancing digestibility became critical. The inception of the gala pelletizer coincided with the need for more efficient waste management solutions, particularly in the agricultural sector. Over time, these machines evolved, incorporating automation and more sophisticated control technologies.
The industrial adaptation of gala pelletizers began to flourish with advancements in materials science. As awareness grew about the environmental impact of waste, industries sought ways to recycle and repurpose materials. This led to the introduction of new feedstocks, such as plastic and biomass, which fed the rapid evolution of gala pelletization techniques. The historical trajectory of gala pelletizers thus reflects an ongoing response to both market demand and technological innovation, which continues to redefine how materials are processed today.
Mechanics of Gala Pelletizers
Understanding the mechanics of gala pelletizers is crucial for grasping how these machines operate in various industrial sectors. The mechanics encompass the operational principles and the components that ensure their efficiency. This section looks into core mechanisms, emphasizing their roles and functions in the larger context of manufacturing.
Basic Operational Principles
Gala pelletizers are designed to convert raw materials into uniformly shaped pellets. The operational principle primarily revolves around the reduction and agglomeration of materials. The process begins with feedstock entering the system, where it is subjected to various forces that compress and shape it into pellets.
Key aspects include:
- Shear Forces: These forces play a vital role in breaking down feedstock into smaller particles.
- Pressure Application: Once the material is suitably prepared, pressure is applied in the pelletizing chamber to form solid pellets.
- Temperature Management: Maintaining optimal temperature is essential to ensure that the materials bond effectively without degrading their quality.
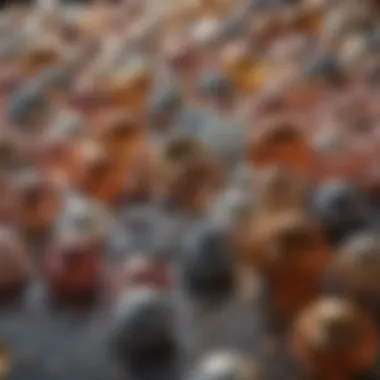
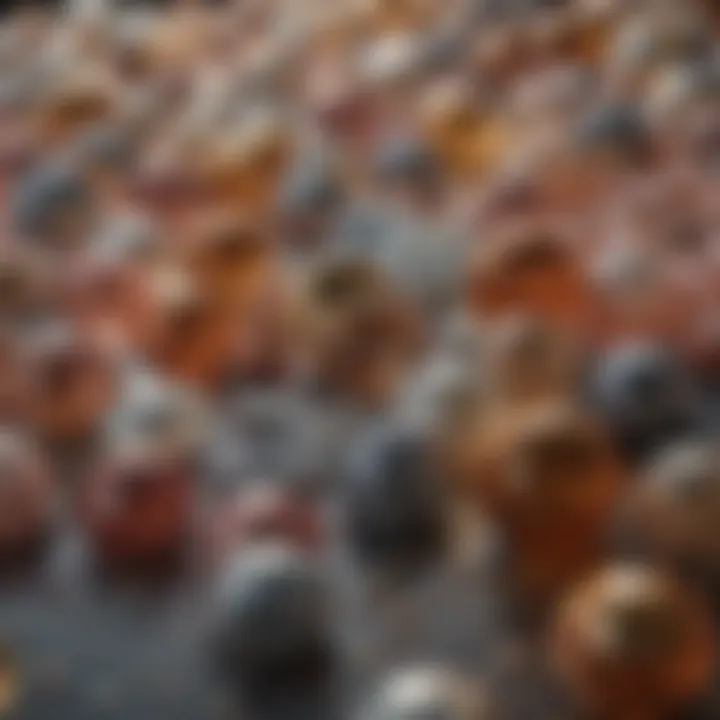
This systematic approach makes gala pelletizers extremely effective for a range of applications, from plastic recycling to biomass processing.
Component Analysis
A deeper examination of the components within gala pelletizers reveals how they contribute to overall performance. Key components include feeding mechanisms, pelletizing chambers, cooling systems, and control systems.
Feeding Mechanisms
Feeding mechanisms serve as the initial point where raw materials are introduced into the pelletizing process. They ensure a consistent flow of materials into the system, which is critical for uniform pellet production.
Characteristics of feeding mechanisms include:
- Variability Control: They allow operators to adjust the feed rate according to the properties of the material being processed.
- Integration Capability: Feeding systems can be integrated with other machinery, facilitating seamless workflows.
However, operating these systems requires careful calibration. Improper settings can lead to inconsistencies in pellet size and density.
Pelletizing Chambers
The pelletizing chamber is the heart of the gala pelletizer, where materials are compressed into pellets. Its design usually ensures an even distribution of pressure, which is vital for quality.
Key characteristics include:
- Enhanced Uniformity: High-quality chambers achieve uniform pellet dimensions and weight.
- Material Versatility: Well-designed chambers can handle various materials, from plastics to agricultural waste.
These advantages contribute significantly to the efficiency of the machine. Yet, wear and tear over time can affect performance, necessitating regular maintenance checks.
Cooling Systems
Cooling systems are essential for solidifying the pellets immediately after production. Proper cooling prevents the pellets from deforming, ensuring that they maintain their shape and durability.
Key features are:
- Controlled Temperature Reduction: Effective cooling systems employ controlled airflow or liquid cooling to strategically lower temperatures.
- Energy Efficiency: Modern cooling technologies consume less energy while providing effective cooling.
While advantageous, the integration of cooling systems must be planned with energy costs in mind.
Control Systems
Control systems oversee the operations of gala pelletizers, allowing for real-time monitoring and adjustments. These systems are vital for maintaining consistent output quality.
Characteristics include:
- Automation Features: Many control systems offer automation, reducing manual interventions and errors.
- Data Analytics: Modern systems can collect and analyze data to predict performance, enhancing operational efficiency.
Ultimately, a robust control system can maximize production while minimizing downtime, making it a crucial aspect in modern pelletizer technology.
Epilogue
The mechanics of gala pelletizers underscore their role in efficient manufacturing processes. By understanding the operational principles and analyzing key components such as feeding mechanisms, pelletizing chambers, cooling systems, and control systems, we gain insights that are fundamental for optimizing production in various industries. This knowledge not only aids in enhancing performance but also in addressing challenges that may arise in the operational environment.
Materials Processed by Gala Pelletizers
Gala pelletizers are vital in processing a variety of materials. This section focuses on the types of materials that are optimal for gala pelletizers and the implications of their use. The composition of materials processed is critical for ensuring the efficiency and performance of these machines. Different feedstocks bring unique characteristics, challenges, and benefits that affect production and end-use applications.
Types of Feedstocks
Biomass
Biomass serves as a highly versatile feedstock option for gala pelletizers. It encompasses organic materials from plants, animals, and biodegradable wastes. The key characteristic of biomass is its renewable nature, making it a sustainable choice for energy production and material processing. Biomass can significantly contribute to reducing waste and promoting eco-friendly practices. This feedstock is beneficial as it helps transition to greener energy solutions.
A unique feature of biomass is its ability to produce energy-dense pellets suitable for heating and energy generation. While it has many advantages, some disadvantages exist. For instance, the moisture content can significantly affect its pelletizing efficiency. High moisture levels may lead to operational challenges during the pelletizing process.
Plastic Waste
Plastic waste is becoming an increasingly important feedstock in addressing global waste management issues. The distinctive trait of plastic waste is its capacity to be reprocessed into usable products, thus reducing environmental pollution. Utilizing plastic waste in gala pelletizers allows manufacturers to convert discarded materials into value-added products while promoting recycling and circular economy concepts.
However, plastic waste has certain unique challenges. The variability in plastic types can lead to complications during processing. Different plastics require specific conditions for effective pelletizing. Additionally, certain types of plastics may release harmful emissions when heated, necessitating careful management of emissions and pollutants.
Mineral Materials
Mineral materials have their place in the realm of gala pelletizing. These materials include various inorganic components such as clays and ores, which can be transformed into pellets for multiple applications. The critical characteristic of mineral materials is their ability to provide stability and durability in the final product, making them suitable for construction and industrial uses.
A notable feature of mineral materials is their high melting point, which leads to unique challenges in the pelletizing process. This can sometimes create difficulties in achieving uniform pellet size and quality. Additionally, processing these materials often requires specialized equipment and higher energy consumption.
Quality Characteristics of Inputs
The quality of inputs is paramount when processing materials in gala pelletizers. Factors such as moisture content, particle size, and the composition of materials affect the efficiency of pelleting processes. Maintaining optimal quality characteristics can enhance machine performance and the overall quality of the finished pellets.
Key quality attributes include:
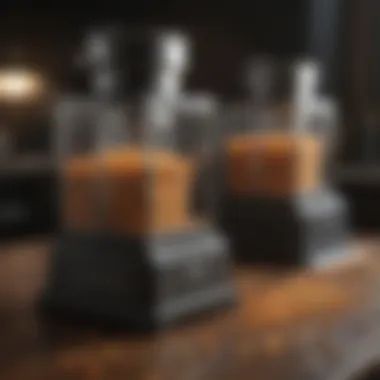
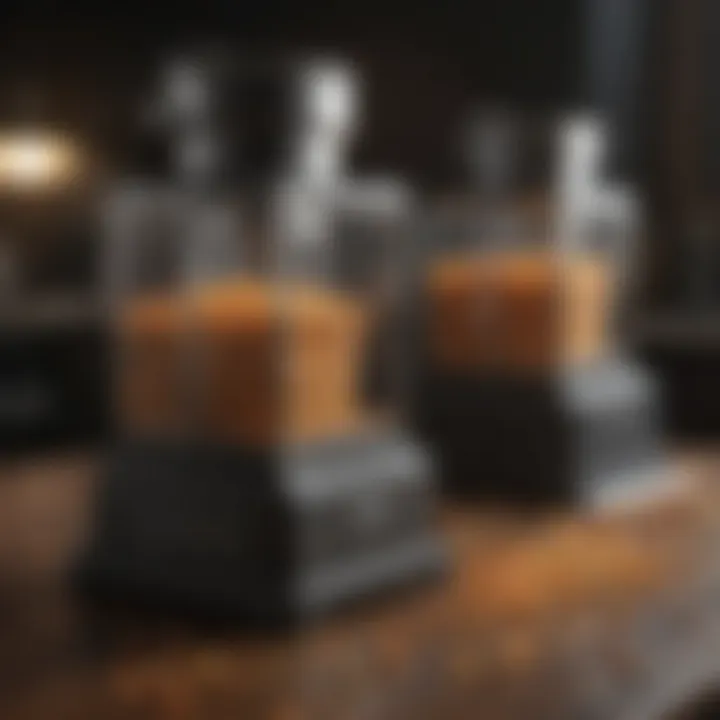
- Moisture Content: Affects pellet durability and energy consumption during production.
- Particle Size: Uniform particle size may improve compressibility and enhance pellet formation.
- Chemical Composition: Variability may lead to inconsistency in final product quality.
Therefore, it is crucial for manufacturers to implement stringent quality control measures to maximize productivity and ensure pellet integrity.
"Investing in quality inputs can directly influence the success of processing operations and the marketability of the final products."
Using proper guidelines and standards can foster better outcomes in the pelleting process. This aligns with the increasing demand for high-quality materials in various industries.
Advantages of Using Gala Pelletizers
Gala pelletizers are vital in several industrial contexts, and understanding their advantages provides clearer insights into their relevance. The benefits extend beyond mere operational efficiency, encompassing aspects such as production quality, cost savings, and environmental considerations.
Efficiency in Production
One of the primary benefits of gala pelletizers is their ability to enhance production efficiency. These machines are designed to optimize the conversion of raw materials into uniform pellets, which is crucial in various processes including energy production and animal feed formulation. The operational design allows for continuous processing, minimizing interruptions that could impact output. A well-tuned gala pelletizer can achieve a high throughput while maintaining tight tolerances on pellet specifications. This consistency in production quality is critical for businesses looking to meet specific standards in their markets.
"Efficiency in production is not merely about speed; it’s about consistency and quality in output."
Space Optimization
Another significant advantage of using gala pelletizers is space optimization. In industrial settings where floor space is a premium, these machines are compact and designed to fit into tighter layouts without sacrificing functionality. Their streamlined designs allow for efficient integration into existing production lines. Moreover, by converting bulk materials into smaller, denser pellets, they enable better storage options. This transition minimizes the spatial footprint of raw materials and product inventory, contributing to overall operational efficiency.
Reduced Environmental Impact
Gala pelletizers also play a crucial role in reducing environmental impact. The processing of materials into pellets often leads to more efficient combustion in energy applications, thus decreasing emissions. Additionally, by promoting the recycling of materials—such as plastic waste—gala pelletizers facilitate a move towards more sustainable manufacturing practices. Many modern pelletizing systems are engineered with energy-efficient technologies, which further reduces the carbon footprint associated with production processes. The implications of this are profound for industries facing stricter environmental regulations and growing public scrutiny over environmental practices.
Challenges and Disadvantages
Understanding the challenges and disadvantages of Gala pelletizers is crucial for industries considering their integration into production processes. While these machines offer various advantages, they also come with unique challenges that can affect operations. Awareness of these issues ensures more informed decision-making and effective management strategies.
Operational Downtime
Operational downtime represents a significant challenge in the use of Gala pelletizers. Every moment the machinery is not functioning translates into lost production time. Factors contributing to downtime include equipment failures, maintenance needs, and unexpected hazards. Manufacturers often face the dilemma of scheduling routine maintenance without disrupting production schedules. The balance can be tricky.
To minimize downtime, proactive measures such as regular inspections and timely repairs must be instituted. Implementing predictive maintenance techniques can also reduce the likelihood of unplanned outages. By employing technology to monitor performance metrics in real-time, operators can spot potential concerns before they turn into major failures.
Maintenance Requirements
Maintenance is a fundamental aspect of operating Gala pelletizers. These machines require routine check-ups and part replacements to maintain efficiency and ensure safety. Keeping up with maintenance needs can be resource-intensive. It involves not only time and labor costs but also the availability of replacement parts and qualified personnel for service.
Failure to adhere to a proper maintenance schedule can lead to more severe issues, resulting in costly repairs. Furthermore, extended downtimes may result from waiting for replacement parts, which can lead to delays in production and affect overall profitability. Therefore, effective maintenance planning is essential to mitigate these challenges.
Material Limitations
Material limitations present another challenge when using Gala pelletizers. Not all materials are suitable for the pelletizing process. Factors such as moisture content, size, and density can influence how well a feedstock can be processed. Some materials may not bind effectively, resulting in suboptimal pellet quality.
Incompatibility with certain materials may limit the functionality of a pelletizer. This necessitates careful selection of feedstocks before operation to ensure that only appropriate materials are used. Moreover, operators must be trained to recognize and address material limitations when choosing inputs. Doing so can prevent equipment strain and maintain product integrity.
"Understanding the challenges of pelletizing is as important as recognizing its advantages. The two aspects guide operational strategies and decision-making in manufacturing."
In summary, while Gala pelletizers are valuable assets in production, their challenges can impact efficiency and operations. Recognizing limitations due to operational downtime, maintenance requirements, and material choices is integral for maximizing productivity and minimizing costs.
Emerging Technologies in Pelletizing
The field of pelletization is experiencing significant evolution, driven by technological advancements. The importance of Emerging Technologies in Pelletizing lies in their ability to enhance efficiency and improve the quality of output while addressing environmental concerns. This section focuses on two key areas of development: advancements in machinery and the integration of smart technologies.
Advancements in Machinery
Modern machinery for pelletizing is being designed with enhanced features that optimize performance. These advancements aim to increase production rates and reduce energy consumption. For instance, high-capacity pellet mills have been developed, capable of handling large volumes of materials without compromising on quality.
Additionally, variable frequency drives (VFD) are becoming common in pelletizing machines. These drives allow the motors to run at varying speeds, providing more precise control and adaptability in different operational scenarios. Other innovations include improved die designs and material selections that enhance durability and efficiency.
- Key features of advancements in machinery include:
- Enhanced operational speeds.
- Better energy efficiency.
- Wider range of material handling.
- Improved durability of components.
This results in reduced operational costs and minimized downtime for maintenance, ultimately leading to higher profitability for manufacturers. As machinery continues to evolve, it opens new opportunities for various industries to utilize pelletizing effectively.
Integration of Smart Technologies
The integration of smart technologies brings another layer of sophistication to the pelletizing process. These technologies can monitor machines in real time and provide crucial data analytics for optimization. For example, Internet of Things (IoT) devices can track the performance of pelletizing systems, detecting inefficiencies and potential failures before they occur.
- Benefits of smart technology integration include:
- Predictive maintenance capabilities.
- Real-time monitoring of operations.
- Enhanced data collection for analysis.
- Improved decision-making based on data-driven insights.
By harnessing these smart technologies, companies can maintain higher production standards. The operational resilience provided by advanced data monitoring fosters a proactive approach to maintenance and increases the overall reliability of the pelletization process.
"As industries adapt to modern challenges, the implementation of emerging technologies in pelletizing ensures that quality and efficiency are not sacrificed."
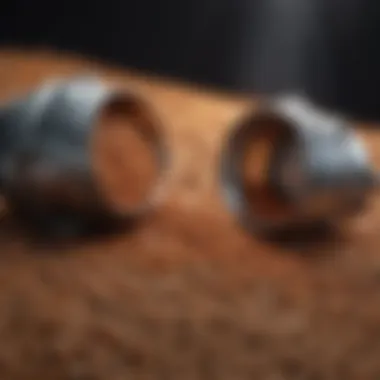
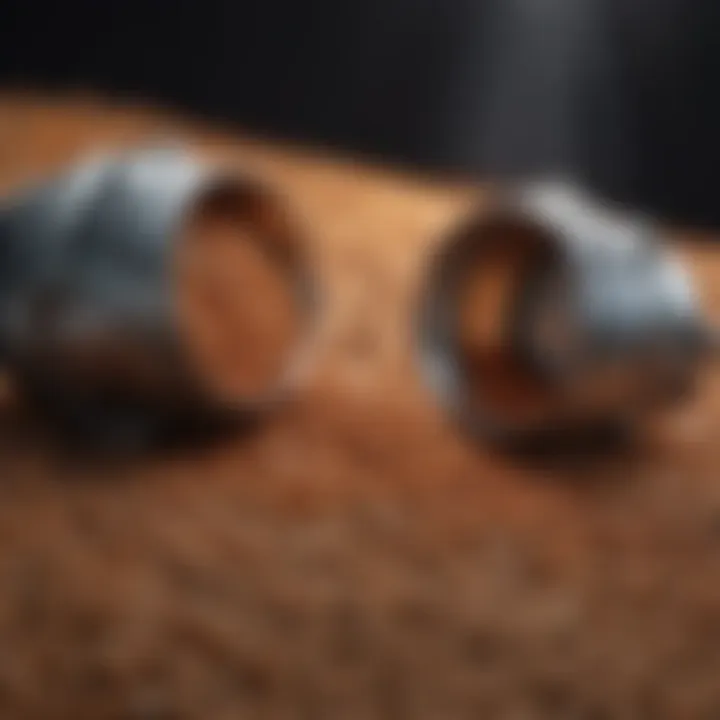
Industrial Applications of Gala Pelletizers
The utility of gala pelletizers extends far beyond mere processing; they have significant implications across various industries. The advancements in this technology have made it a cornerstone in how materials are transformed for specific applications. Understanding the industrial applications of gala pelletizers sheds light on their benefits, operational efficiencies, and the evolving landscape of material processing.
Energy Sector
In the energy sector, gala pelletizers play a vital role in enhancing the efficiency of biomass conversion. Biomass, often composed of agricultural residues, wood chips, and other organic materials, requires processing to be suitable for energy generation. Gala pelletizers effectively compress these materials into denser pellets, which optimize combustion during energy production. This not only increases the calorific value but also ensures better handling and transportation of biomass.
Moreover, by using gala pelletizers, energy producers can contribute to a more sustainable energy grid. The pellets produced can be utilized in various applications, including co-firing with coal, thus reducing greenhouse gas emissions.
"Efficient conversion and utilization of biomass through pelletizing underscores a significant step toward renewable energy solutions."
Agriculture and Animal Feed
In agriculture, gala pelletizers are integral to producing high-quality animal feed. The process of pelletizing feed enhances its digestibility, ensuring that livestock receive a balanced diet with the necessary nutrients. It also reduces waste generated during feeding, as pellets are easier for animals to consume compared to loose ingredients. This not only promotes better growth rates but also improves overall health in livestock.
Another critical advantage is the preservation of feed quality. Gala pelletizers apply heat and pressure during processing, which can help eliminate unwanted microorganisms. This contributes to a reduction in spoilage, extending the shelf life of feed products. Enhanced feed quality directly impacts agricultural productivity, making gala pelletizers a crucial technology in the sector.
Recycling and Waste Management
Gala pelletizers are gaining traction in the recycling and waste management arenas. They facilitate the conversion of plastic waste and other recyclable materials into usable pellets. These pellets can then be repurposed for various applications, including manufacturing new plastic products. The ability to transform waste into a valuable resource is critical in achieving sustainability goals and minimizing landfill contributions.
Furthermore, by improving the properties of recycled materials, gala pelletizers enable manufacturers to produce higher-quality products. This may lead to increased acceptance of recycled materials in different sectors, pushing the industry toward more sustainable practices.
In summary, the industrial applications of gala pelletizers significantly impact the energy, agriculture, and recycling sectors. Their ability to streamline processes offers not only operational efficiencies but also a path toward sustainability. As industries continue to recognize the value of pelletizing technology, further advancements are likely to unfold.
Regulatory and Environmental Considerations
The role of regulatory and environmental considerations in the operation of gala pelletizers is substantial. As industries today focus more on sustainable practices, adhering to regulations while minimizing environmental impacts becomes imperative. The discussion around compliance standards and sustainability initiatives highlights the ongoing efforts to align manufacturing processes with eco-friendly norms. By understanding these considerations, stakeholders can enhance their operational framework while promoting social responsibility.
Compliance Standards
Compliance standards are essential in the context of manufacturing, especially when discussing the use of gala pelletizers. Various regulatory bodies implement a range of guidelines aimed at ensuring safety, efficiency, and environmental protection.
- Safety Regulations provide protocols to safeguard operators and the surrounding community.
- Environmental Regulations ensure that pelletizing processes do not adversely affect air quality, water sources, or the surrounding ecosystems.
- Quality Standards guarantee that the pellets produced meet market demands and customer expectations, contributing to economic viability.
Fulfilling these standards often requires continuous monitoring of machinery and processes. For example, maintaining emissions at acceptable levels necessitates the use of advanced filtration and extraction systems within the pelletizers. Ultimately, abiding by these compliance standards can lead to a reduction in operational risks and enhance the overall viability of the production cycle.
Sustainability Initiatives
Sustainability initiatives are increasingly influencing the design and operation of gala pelletizers. These initiatives promote not only the use of renewable resources but also the implementation of processes that reduce waste and energy consumption.
- Efficiency Improvements are central to sustainability efforts. Modern gala pelletizers often integrate energy-saving technologies, reducing overall energy consumption without sacrificing output quality.
- Waste Reduction focuses on minimizing the byproducts created during pelletizing. Many companies are adopting closed-loop systems that recycle waste materials back into the production cycle.
- Use of Alternative Resources encourages the processing of biomaterials and recycled products, aligning with global sustainable development goals.
"Adopting sustainability initiatives not only addresses regulatory demands but also creates new opportunities for innovation in gala pelletizing technologies."
Engaging seriously with sustainability can end up being a competitive advantage in the marketplace. The holistic approach to sustainability can lead to significant shifts in how industries operate, fostering long-term operational resilience and improving public perception.
Future Trends in Gala Pelletizing
The realm of gala pelletizers is poised for significant transformations in the upcoming years. This section explores various trends that are shaping the future of pelletizing technology. Understanding these trends is vital for industry stakeholders aiming to optimize operations and enhance market competitiveness. Future trends are not solely about advancements in technology but also revolve around enhancing sustainability and adapting to evolving regulatory frameworks.
Market Projections
There is a growing demand for gala pelletizers across different sectors. Projections indicate that the pelletizing equipment market could experience substantial growth. According to recent industry analyses, this growth is primarily driven by the increased need for effective waste management and sustainable practices in various manufacturing processes.
- The global market is expected to expand at an approximate CAGR of 6–8% over the next five years.
- Increased awareness of recycling and environmental preservation is pushing manufacturers toward adopting pelletizing technologies.
- New applications in the energy sector, especially biofuels, are also anticipated to contribute to market growth.
Such growth underscores the potential of pelletizers in responding to global challenges, particularly regarding environmental sustainability and resource efficiency.
Innovations on the Horizon
Innovation will be a cornerstone of the future landscape of gala pelletizers. Several advancements are likely to emerge, transforming current operational methodologies and materials processing.
- Smart Automation: The integration of IoT (Internet of Things) technologies is poised to enhance operational efficiency. Smart systems can provide real-time monitoring, predictive maintenance alerts, and performance analytics, reducing downtime and increasing production rates.
- Advanced Materials: Innovations in materials science are paving the way for pelletizers to process a wider variety of feedstocks. For instance, developments in biodegradable plastics can lead to new opportunities in the recycling landscape.
- Energy Efficiency: Next-generation pelletizers may focus significantly on reducing energy consumption, potentially implementing energy recovery systems that utilize waste energy generated during operations.
- Environmental Compliance: Enhanced filtration and emission control technologies will likely become standard, aligning operations with stricter environmental regulations.
"The future of gala pelletizers lies in their ability to adapt and innovate in response to both market demands and environmental considerations."
These innovations will not only optimize production processes but also play a crucial role in mitigating the environmental impact of manufacturing practices. By understanding these trends, industries can prepare to harness the potential of gala pelletizers effectively.
The End
The conclusion of this comprehensive article on gala pelletizers encapsulates the various dimensions of these pivotal machines in modern industrial processes. Gala pelletizers serve as a cornerstone in the sectors of energy production, agriculture, and waste management. Their efficiency and versatility are paramount in addressing the growing need for sustainable manufacturing practices.
Summary of Key Insights
In summary, this article has highlighted several critical insights regarding gala pelletizers:
- Importance of Technology: The technology behind these machines showcases advanced engineering, designed to optimize the pelletizing process. This advancement offers not just efficiency but also adaptability to different materials.
- Diverse Applications: From energy production to recycling, gala pelletizers are applicable in a range of industries. They help in transforming various feedstocks into a more manageable and usable form.
- Environmental Considerations: Utilizing gala pelletizers contributes significantly towards reducing waste and promoting sustainability in industrial operations. By recycling materials and producing high-quality pellets, these machines lessen environmental impacts, which is becoming increasingly vital in today's economy.
- Current Challenges: Despite their advantages, challenges such as maintenance, operational downtime, and specific material limitations were acknowledged. Understanding these issues is essential for stakeholders aiming for optimized performance in their operations.
Implications for Industry Stakeholders
For industry stakeholders, the implications of using gala pelletizers are profound. The benefits outlined throughout this article not only present operational advantages but also underscore strategic importance in sustainability initiatives. It is crucial for businesses to consider the following:
- Investment in Technology: Adopting and integrating new pelletizing technologies can enhance production capabilities. Stakeholders should evaluate the potential return on investment and how technology can be tailored to their specific needs.
- Commitment to Sustainability: There is increasing pressure from consumers and regulatory bodies to adopt more environmentally friendly practices. Gala pelletizers, by virtue of their design, enable companies to bolster their sustainability credentials while remaining competitive in the market.
- Continuous Improvement: The landscape of pelletizing is dynamic. Ongoing research and development into advancements in machinery and materials processing techniques are essential. Staying informed about trends can provide a competitive edge and foster innovation.
- Collaboration Across Sectors: As industries work to improve their sustainability goals, collaboration may offer the best strategies for efficient use of gala pelletizers. Partnerships between suppliers, manufacturers, and regulatory bodies can lead to synergies that enhance the overall effectiveness of pelletizing processes.
Ultimately, gala pelletizers are not just machines; they are integral to a future where resource efficiency and environmental sustainability are paramount. The insights acquired from this analysis provide valuable guidance to stakeholders aiming to leverage these technologies effectively.