In-Depth Analysis of Gas Cooler Heat Exchangers
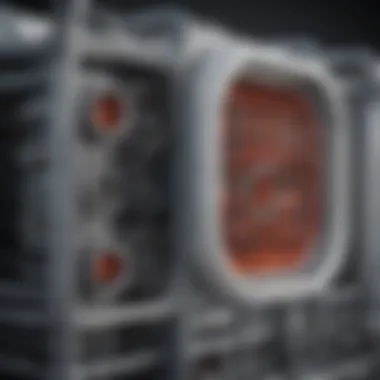
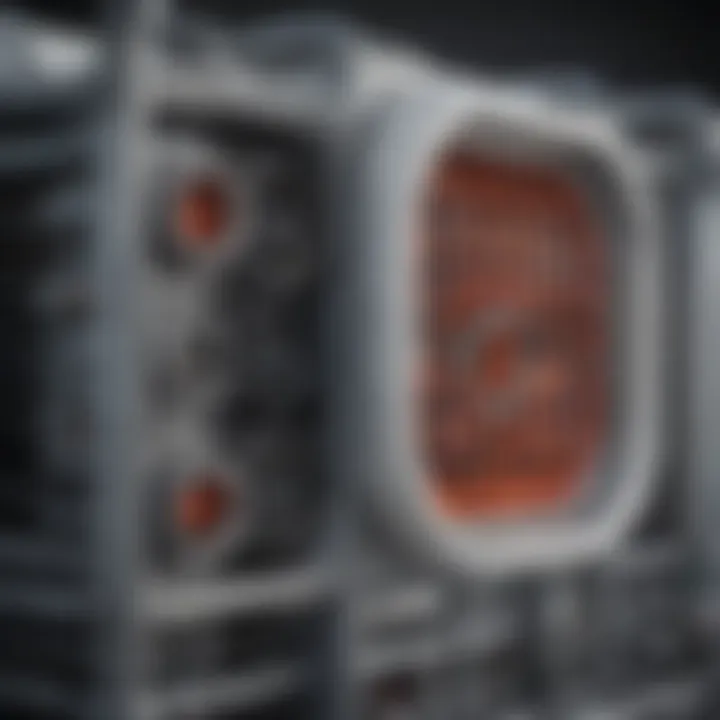
Intro
Gas cooler heat exchangers are critical components in a variety of industrial systems. Their primary role is to efficiently transfer heat from one medium to another, usually facilitating the cooling of gases in different processes. Understanding their functionality, design specifics, and practical applications can lead to enhanced operational efficiency and energy savings. This section serves as an introductory overview to frame the subsequent analysis.
Key Concepts
Definition of Primary Terms
To effectively grasp the intricacies of gas cooler heat exchangers, it is essential to clarify several key terms:
- Heat Exchanger: A device designed to transfer heat from one fluid to another without mixing them. It is a crucial tool in various heating and cooling systems.
- Gas Cooler: A specific type of heat exchanger used to cool gaseous substances.
- Thermal Efficiency: This refers to the effectiveness with which a heat exchanger transfers heat, affecting its overall performance.
These terms lay the groundwork for understanding how gas cooler heat exchangers operate and their significance in industrial contexts.
Related Concepts and Theories
The discussion of gas cooler heat exchangers is intertwined with several engineering principles, including thermodynamics and fluid mechanics.
- Thermodynamics: The laws governing energy transfer and conversion are vital to understanding the efficacy and performance of heat exchangers.
- Fluid Dynamics: The behavior of fluids in motion plays a significant role in designing effective cooling systems.
As we delve deeper into the functionality of gas cooler heat exchangers, these concepts will recur throughout the analysis, reinforcing the idea of integrated knowledge across disciplines.
Future Directions
Gaps Identified in Current Research
While there are substantial studies on heat exchangers, there are still gaps that merit further investigation:
- The impact of variable operational conditions on the performance of gas coolers remains underexplored.
- There is a lack of comprehensive data on the long-term efficiency of novel materials used in heat exchangers.
Suggestions for Further Studies
Future research should consider:
- Developing more advanced materials that can withstand high thermal stresses while maintaining efficient heat transfer.
- Investigating novel designs or configurations of heat exchangers that could improve efficiency in specific applications.
In sum, as the demand for energy efficiency rises, understanding the operation and design of gas cooler heat exchangers becomes increasingly vital. The insights gained will be crucial for both present and future developments in this field.
Prelude to Gas Cooler Heat Exchangers
Gas cooler heat exchangers play a critical role in thermal management systems across various industrial applications. Their primary function is to reduce the temperature of gases, ensuring efficient performance in processes such as refrigeration, HVAC, and power generation. Understanding these systems is essential, as they influence both energy consumption and operational effectiveness.
Definition of Heat Exchangers
Heat exchangers are devices designed to transfer heat between two or more fluids without mixing them. The principle relies on the second law of thermodynamics where heat flows from a hotter to a colder medium. They are widely utilized in engineering to improve energy efficiency. Common types of heat exchangers include shell and tube, plate, and air-cooled designs. Each type serves specific needs and varies in construction, making proper definition crucial.
Overview of Gas Coolers
Gas coolers, a specific category of heat exchangers, utilize ambient air or water to extract heat from gases. These systems are paramount for industries that require precise temperature control. Typically, a gas cooler operates by circulating a fluid that absorbs heat from the gas stream, which then releases this heat to the environment.
The advantages of gas cooler systems are significant. Not only do they contribute to the overall efficiency of thermal processes, but they also help in reducing operational costs. By managing the temperature effectively, gas coolers minimize energy waste, thus aligning with modern sustainability goals. This efficiency is especially pertinent in large installations where cooling requirements are substantial and the impact on energy consumption is pronounced.
Principles of Operation
Understanding the principles of operation for gas cooler heat exchangers is crucial in grasping how these systems function within industrial settings. The efficiency and effectiveness of cooling applications hinge on these principles. A solid comprehension helps ensure optimal performance and application in various scenarios. The principles focus primarily on thermodynamics and the modes of heat transfer, both essential aspects to effectively utilize gas cooler heat exchangers.
Thermodynamics of Heat Exchange
Thermodynamics concerns the transfer of energy from one form to another. In heat exchangers, this involves the flow of heat energy between two media. The first law of thermodynamics states that energy cannot be created or destroyed, only transformed. This principle is paramount in explaining the operation of gas cooler heat exchangers.
In essence, the hot gas enters the cooler and transfers heat to a secondary fluid, typically air or water, thus lowering its temperature. This exchange takes place while ensuring both liquids retain their distinct properties. The efficiency of this exchange largely depends on the temperature gradient between the fluids. The larger this gradient, the higher the rate of heat transfer.
Key factors affecting thermodynamic performance include:
- Heat capacity of the fluids
- Flow rate of the hot and cold media
- Surface area of the heat exchanger
These factors are essential for optimizing the process, ensuring maximum energy transfer and minimal energy waste.
Modes of Heat Transfer
Modes of heat transfer signify how heat is exchanged within a system. There are three primary modes: conduction, convection, and radiation. However, in gas cooler heat exchangers, conduction and convection are the most relevant.
- Conduction is the process through which heat transfers through materials. In a gas cooler heat exchanger, heat moves from the gas to the metal walls and then to the cooler fluid. The effectiveness of conduction depends on the materials used in the heat exchanger, as well as the thickness of those materials.
- Convection occurs when heat is exchanged between a solid surface and a fluid in motion. It can be natural or forced, depending on how the fluid moves across the surfaces. For instance, in an air-cooled heat exchanger, ambient air moves over the fins or coils through a fan, enhancing the cooling effect. The rate of convection significantly influences the overall efficiency and is influenced by:
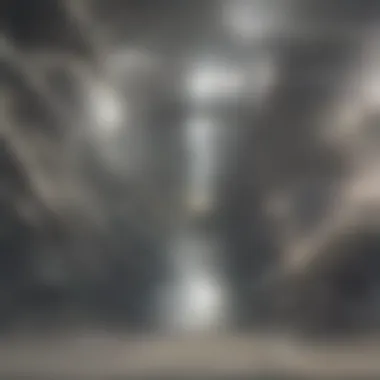
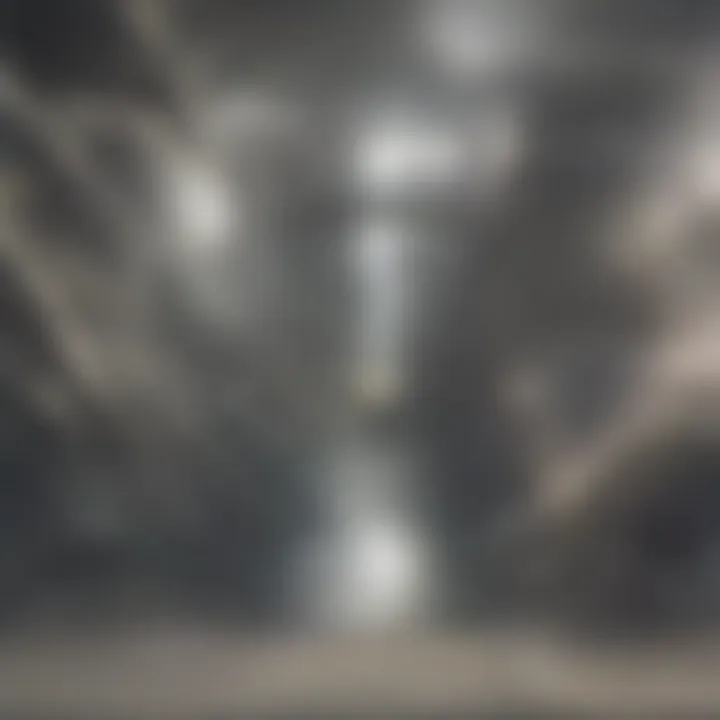
- Fluid velocity
- Temperature difference between the surfaces
- Surface area of contact
"Maximizing efficiency in heat exchangers relies heavily on optimizing heat transfer modes and understanding the underlying thermodynamics."
These modes of heat transfer play a vital role in determining the performance of gas cooler heat exchangers. Knowledge of these principles allows engineers and professionals to design better systems suited for specific applications.
Design Considerations
Design considerations are critical when creating efficient gas cooler heat exchangers. These considerations ensure optimal performance, reliability, and durability. Focusing on the right materials, configurations, and size helps in meeting specific application requirements while also maximizing efficiency.
Material Selection
Choosing the correct materials for gas cooler heat exchangers is essential for their longevity and function. Materials need to withstand various stresses, including thermal expansion and corrosion.
- Corrosion Resistance: Stainless steel and titanium are often selected for their resistance to corrosion in harsh environments. These materials can endure the chemical interactions in refrigerant applications effectively.
- Thermal Conductivity: Copper is known for its high thermal conductivity, making it a great candidate for maximizing heat transfer efficiency. However, it may not be ideal for all applications due to cost or potential corrosion issues.
- Weight and Structure: Lightweight materials can reduce the overall weight of the system, leading to easier installation and less structural support needs. This is especially important in HVAC systems where space is often limited.
Design Configurations
Design configurations of gas cooler heat exchangers play a significant role in their operational efficiency. The main types include shell and tube, plate, and air-cooled designs.
Shell and Tube
Shell and tube heat exchangers consist of a series of tubes, one set carrying the hot gas and the other the cooling medium. This configuration is well-suited for applications requiring robust construction. One key characteristic of shell and tube designs is flexibility; they can be built in various sizes and configurations to fit specific needs.
- Advantages: They are durable and can handle high pressures and temperatures. The design allows for easy maintenance, as individual tubes can be accessed for cleaning or replacement.
- Disadvantages: However, they can be more expensive to manufacture and install compared to other designs.
Plate
Plate heat exchangers utilize thin plates to create channels for the heat exchange process. This design efficiently maximizes surface area while minimizing the volume of the unit. A significant advantage of plate exchangers is their compact nature, making them a popular choice for installations with limited space.
- Advantages: They have excellent thermal transfer rates and are relatively easy to clean, as plates can be disassembled.
- Disadvantages: On the downside, they are typically less effective at handling high pressures compared to shell and tube designs.
Air-Cooled
Air-cooled heat exchangers use ambient air to dissipate heat, making them a suitable choice when water sources are limited or where water conservation is necessary. This type highlights simplicity and efficiency, as it often requires no additional cooling fluid.
- Advantages: Their design minimizes water usage and is easier to maintain since there are fewer parts that could become clogged or corroded.
- Disadvantages: However, they may have lower heat transfer efficiencies in conditions with low air velocity or high ambient temperatures.
Size and Capacity Determination
Determining the size and capacity of gas cooler heat exchangers is crucial. The size has to align with the operational demands of the system. Factors impacting size and capacity include:
- Flow Rates: Calculating the maximum flow rate of gas is essential to ensure the unit can handle the operational requirements.
- Temperature Requirements: Understanding the inlet and outlet temperatures of the fluids will guide the selection process.
- Pressure Drops: Analyzing pressure drops through the system can prevent inefficiencies and potential equipment failures.
In summary, design considerations encompass material selection, configurations, and size determination. Each element contributes to the overall performance and efficiency of gas cooler heat exchangers. By understanding these factors, one can better design systems that meet the necessary operational standards and expectations.
Types of Gas Cooler Heat Exchangers
In the context of gas cooler heat exchangers, understanding the various types is crucial for optimizing their applications. Each type of heat exchanger possesses unique characteristics that influence performance, efficiency, and suitability for specific industrial needs. By dissecting the primary types, one can make informed decisions regarding design and implementation.
Air-Cooled Heat Exchangers
Air-cooled heat exchangers rely on ambient air to remove heat from a gas. This method is particularly advantageous in applications where water is scarce or unavailable.
Benefits of Air-Cooled Heat Exchangers:
- Simplicity: Many air-cooled models require less maintenance compared to water systems.
- Cost-Effective: They do not necessitate water treatment or pumping systems.
- High Reliability: Air-cooled units can function under various environmental conditions without the risk of freezing related to water-cooling.
However, these exchangers may have less efficiency in areas with high temperatures or when the ambient air temperature is close to the desired cooling temperature. Engineers must consider air velocity and density to optimize heat transfer.
Water-Cooled Heat Exchangers
Water-cooled heat exchangers utilize water as a cooling medium. These systems are widely recognized for their efficiency and effectiveness in heat transfer.
Considerations for Water-Cooled Heat Exchangers:
- High Efficiency: Water can absorb and transport heat better than air, especially in applications with high heat loads.
- Adaptability: These systems are often suitable for various processes, including industrial refrigeration and HVAC applications.
Nonetheless, water-cooled systems come with caveats. They involve substantial water usage and may require elaborate water circulation systems. Maintenance is essential to avoid issues such as scaling or corrosion over time.
Refrigerant Heat Exchangers
Refrigerant heat exchangers specifically use refrigerants to facilitate heat transfer between systems, integral to refrigeration and air conditioning systems. They work efficiently within closed-loop systems, enabling precise temperature control.
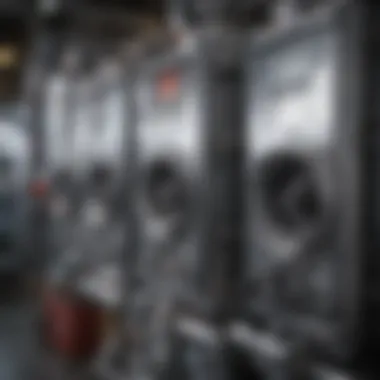
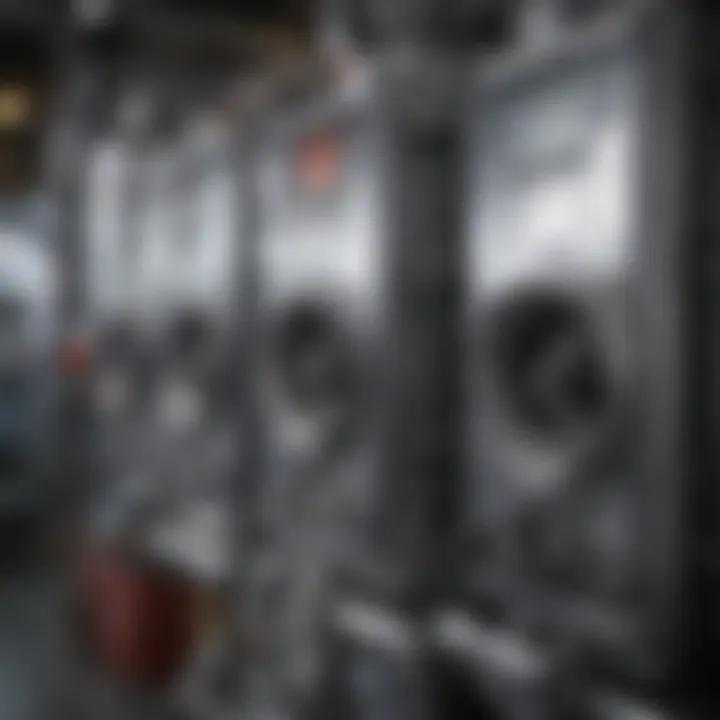
Key Features of Refrigerant Heat Exchangers:
- Enhanced Performance: They provide rapid heat exchange, which is beneficial for environments demanding rapid cooling.
- Versatile Design: Adaptable designs mean these exchangers can be tailored to fit specific systems, optimizing space and efficiency.
On the downside, careful handling of refrigerants is necessary due to their environmental impact if they leak. Regulatory considerations regarding refrigerant use are also important for compliance with laws like the Montreal Protocol.
Each type of gas cooler heat exchanger plays a vital role in efficiency and application scope. A clear understanding of their distinct characteristics aids in optimal system selection and implementation.
Efficiency Metrics
Understanding the efficiency metrics of gas cooler heat exchangers is vital for evaluating their performance in various applications. These metrics provide insights into how effectively a heat exchanger operates, helping to identify areas for improvement and optimizing energy consumption. Efficiency metrics are essential for engineers and technicians as they design systems that require reliable and efficient heat management. The following sections will discuss two key components: the Coefficient of Performance and Heat Transfer Rates.
Coefficient of Performance
The Coefficient of Performance (COP) quantifies the efficiency of a heat pump or cooling system. It is a ratio that compares the useful heating or cooling provided by the system to the energy consumed. For gas cooler heat exchangers, a higher COP indicates greater efficiency, meaning more cooling per unit of energy input. The formula for COP is given by:
[ \textCOP = \fracQ_cW ]
Where:
- Q_c is the amount of heat removed (in kW or BTU).
- W is the work input (in kW or BTU).
A higher COP not only lowers operating costs but also contributes to reduced environmental impacts by displacing fossil fuel usage in energy generation.
Selecting a gas cooler with a high COP is crucial for applications requiring intensive cooling, such as industrial refrigeration and HVAC systems. Furthermore, advancements in materials and design configurations can lead to improved COP ratings over time, thus enhancing the overall energy efficiency of systems with gas coolers.
Heat Transfer Rates
Heat transfer rates refer to the volume of heat transferred in a specific period, which is a critical factor in evaluating the performance of gas cooler heat exchangers. This metric is usually expressed in watts (W) and is influenced by several factors, including surface area, temperature difference, and the flow rate of the working fluid.
The effectiveness of a heat exchanger can often be assessed by the following equation:
[ Q = U \times A \times \Delta T ] Where:
- Q is the heat transfer rate (in watts).
- U is the overall heat transfer coefficient (in W/m²·K).
- A is the surface area available for heat transfer (in m²).
- \Delta T is the temperature difference between the hot and cold fluids (in K).
A higher heat transfer rate indicates more efficient cooling performance. Engineers must carefully design heat exchangers to optimize these rates while considering factors such as fluid dynamics, fouling, and scaling that can hinder performance over time.
Applications of Gas Cooler Heat Exchangers
Gas cooler heat exchangers serve vital roles in several industrial processes. Their primary purpose is to remove heat from gases, setting them up for safer, more efficient processing. This application extends to various important sectors. In this section, we examine the relevance of these exchangers in industrial refrigeration, HVAC systems, and power generation, highlighting specific benefits and designs.
Industrial Refrigeration
In industrial refrigeration, gas cooler heat exchangers are essential. They manage refrigerant temperatures that can fluctuate dramatically. A well-functioning gas cooler enhances the efficiency of refrigeration cycles by condensing and cooling gases before their use. This process has significant benefits:
- Energy Efficiency: Lower temperatures lead to reduced energy consumption.
- Enhanced Performance: Efficient cooling improves the overall performance of refrigeration systems.
- Equipment Longevity: By minimizing excess heat within systems, the chances of premature failure are less likely.
For example, in food storage, maintaining a constant temperature is critical. The gas cooler heat exchanger ensures that the environment remains optimal, which is vital for health regulations and product quality.
HVAC Systems
Gas cooler heat exchangers also play a crucial role in HVAC systems, which are necessary for climate control in buildings. These systems benefit from their ability to regulate temperatures effectively. Consider these aspects:
- Temperature Regulation: Gas coolers maintain desired indoor climates by balancing heat removal.
- Air Quality: Enhanced heat exchange contributes to better air quality by filtering contaminants.
- Cost-Effectiveness: Efficient operation means reduced operational costs for HVAC systems.
Choosing the right type of gas cooler is key. For instance, air-cooled models may be preferred for smaller systems, while water-cooled models are more efficient for larger installations.
Power Generation
In power generation, gas cooler heat exchangers are vital for maximizing efficiency. Their primary role in this sector involves cooling and condensing exhaust gases from turbines or other machinery. Here are points to consider:
- Cycle Efficiency: Cooling exhaust gases enhances the overall thermodynamic cycle efficiency.
- Lower Emissions: Efficient heat removal contributes to reduced greenhouse gas emissions.
- Operational Stability: Maintaining optimal operating conditions leads to fewer interruptions.
Gas coolers are integrated into systems like combined cycle plants, where their performance can significantly influence energy output and reliability.
Properly designed and maintained gas cooler heat exchangers can lead to substantial operational savings across multiple industries.
Maintenance Practices
Regular maintenance of gas cooler heat exchangers is essential for their efficient operation and longevity. This section will explore the significance of maintaining these systems, highlighting routine inspections, appropriate cleaning methods, and troubleshooting common issues that may arise.
Routine Inspections
Routine inspections are critical to ensuring that gas cooler heat exchangers operate effectively. During inspection, technicians look for signs of wear, corrosion, and potential leaks. Commonly, these inspections should occur on a schedule determined by the system's usage and the manufacturer's guidelines.
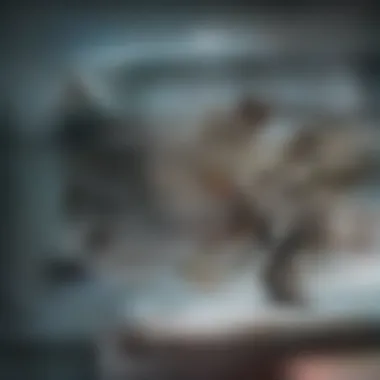

Here are key factors considered during routine inspections:
- Visual checks: Inspect for any visible damage or corrosion on the surface.
- Performance monitoring: Evaluate heat exchange efficiency through temperature and pressure readings.
- Component integrity: Examine joints, seals, and gaskets for structural integrity, as these are common failure points.
Conducting these inspections regularly can prevent small issues from escalating into costly repairs, thereby enhancing the reliability of the heat exchanger.
Cleaning Methods
Cleaning is another vital aspect of maintenance. Over time, gas cooler heat exchangers can accumulate dirt, debris, and other contaminants that hinder performance. Cleaning methods should be chosen based on the type of heat exchanger and the nature of the buildup. Common methods include:
- Chemical cleaning: Using specific solvents or acids to dissolve scale or fouling that accumulates within the heat exchanger.
- Mechanical cleaning: This includes brushing or scrubbing the surfaces to remove debris manually.
- Flushing: Circulating a cleaning solution through the system to dislodge and remove deposits.
Regular cleaning not only improves efficiency but also extends the lifespan of the equipment by preventing damage from corrosion and buildup.
Common Repairs and Troubleshooting
Repairing gas cooler heat exchangers requires a systematic approach to identify and resolve issues effectively. Common problems may include:
- Leaking joints or seals: These can often be repaired by tightening connections or replacing seals.
- Blocked flow paths: If the flow path is restricted, it can cause overheating; resolving this may require cleaning or unblocking.
- Pressure fluctuations: These can signify underlying problems in the system, such as compressor issues or obstructions that need troubleshooting.
By addressing these common repairs with urgency, operators can maintain peak performance and avoid extended downtimes.
Regular maintenance practices for gas cooler heat exchangers ensure not only optimal performance but also contribute to sustainable operational practices.
Environmental Considerations
The importance of environmental considerations in gas cooler heat exchangers cannot be overstated. In today's industrial landscape, sustainability has become a priority. Companies now recognize that the operational efficiency of their systems can significantly impact both energy budgets and the environment. Therefore, a detailed exploration of environmental elements related to gas cooler heat exchangers yields valuable insights.
Energy Consumption and Efficiency
Gas cooler heat exchangers play a vital role in the broader context of energy consumption. Their design influences the overall efficiency of systems in which they are employed. Efficient heat exchange processes not only minimize waste but also lower operational costs.
- Energy Efficiency: It’s critical to select heat exchangers that optimize thermal performance. Advanced designs reduce energy use and maintain desired outcomes in heating and cooling processes.
- Use of High-Performance Materials: Development in materials, such as alloys and composites, can enhance thermal conductivity. These innovations lead to more efficient systems, requiring less energy to operate effectively.
- Operational Strategies: Implementing control strategies, like variable frequency drives, can enhance efficiency. These methods adjust energy use according to operational demands, lowering energy losses.
Emissions and Sustainability Practices
As industries aim to minimize their carbon footprints, the role of gas cooler heat exchangers extends to emissions reduction. While they help in cooling gases, the design and operation of these systems play a crucial part in managing emissions.
Effective integration of gas cooler heat exchangers supports sustainability, reducing greenhouse gas emissions through optimized processes.
- Reducing CO2 Emissions: Utilizing efficient heat recovery techniques helps decrease reliance on fossil fuels, subsequently lowering carbon emissions.
- Sustainable Practices: To achieve sustainability, industries can adopt best practices, including:
- Monitoring Technologies: The use of advanced monitoring systems for emissions helps industries remain compliant with environmental regulations. Investing in such technologies proves beneficial for operational transparency and environmental protection.
- Regular maintenance to ensure optimal function.
- Upgrading to energy-efficient models.
- Implementing recycling programs for materials at end-of-life.
In summary, environmental considerations surrounding gas cooler heat exchangers are significant. Emphasizing energy consumption and emissions inspires both operational improvements and strategic practices that enhance sustainability. Companies must embrace these practices to contribute to a healthier planet while remaining economically viable.
Future Trends in Gas Cooler Heat Exchanger Technology
The evolution of gas cooler heat exchangers is vital due to their key role in improving energy efficiency and reducing emissions. In various industries, there is a pressing demand for systems that not only optimize performance but are also environmentally sustainable. This section explores two prominent trends currently shaping this technology: advancements in materials and the integration with renewable energy systems. Understanding these trends helps industries stay competitive and compliant with modern energy expectations.
Advancements in Materials
Recent innovations in materials science have significantly influenced the design and functionality of gas cooler heat exchangers. The industry is moving towards the use of advanced alloys and composite materials. These materials offer enhanced thermal conductivity and corrosion resistance, which are crucial for maintaining efficient operation over time.
- High-Strength Alloys: These alloys can withstand higher pressures and temperatures, leading to smaller, more efficient designs.
- Polymer Blends: Advanced polymers are lighter and can be molded into intricate shapes, improving airflow and heat transfer efficiency.
The emphasis on sustainable materials is also growing. Manufacturers are researching the use of recyclable materials. This consideration aids in reducing the overall environmental impact of heat exchangers after their lifecycle ends. The trend towards nanomaterials is also noteworthy. They provide benefits like improved heat transfer rates and overall efficiency.
Integration with Renewable Energy Systems
Another significant trend is the integration of gas cooler heat exchangers with renewable energy systems. As industries strive for greener operations, the synergy between these technologies is becoming increasingly relevant.
- Solar Energy Utilization: Gas coolers can interface with solar thermal systems, leveraging the sun's energy for heating and cooling cycles, optimizing energy use throughout the day.
- Wind Energy Applications: Coupling gas coolers with wind energy systems can provide efficient heat dissipation methods, especially in offshore turbines where excess heat management is critical.
This integration not only enhances the overall efficiency of energy systems but also supports the transition towards a low-carbon future. The increasing pressure to meet regulatory standards surrounding emissions renders these trends essential for modern engineering practices and strategies. By investing in these advancements, organizations can better position themselves to optimize performance while meeting environmental goals.
"The future of gas cooler heat exchangers lies in their ability to adapt and integrate with renewable technologies, setting the stage for innovation and sustainability across industries."
These future trends paint a promising picture for the efficiency and effectiveness of gas cooler heat exchangers in industrial applications. The relevance of these trends will continue to escalate as technology develops and the world transitions towards more sustainable practices.
End
The examination of gas cooler heat exchangers culminates in understanding their critical position in various sectors. These systems excel in enhancing thermal efficiency while minimizing energy loss, which is essential for sustained productivity in industrial settings. They play a significant role in facilitating cooling processes, essential for preserving the integrity of equipment and products across multiple applications.
Summary of Key Points
- Role in Efficiency: Gas cooler heat exchangers are pivotal in improving the overall efficiency of cooling systems through effective thermal exchange. The optimization of heat transfer rates is crucial in sectors such as HVAC and refrigeration.
- Design Considerations: Various design configurations, such as shell and tube and plate heat exchangers, cater to specific needs. The choice of materials directly impacts longevity and performance.
- Application Wide Impact: These heat exchangers find applications not only in industrial refrigeration but also in HVAC systems and power generation. Their adaptability is a considerable advantage, making them a preferred choice across sectors.
- Environmental Benefits: By enhancing energy efficiency, gas cooler heat exchangers contribute to reduced emissions, aligning with sustainability goals. Their incorporation into renewable energy systems marks a significant trend toward eco-friendly solutions.
- Future Advancements: Emerging technologies indicate a shift towards advanced materials and integration with smart systems, suggesting a progressive future for gas cooler systems.
Final Thoughts
The interplay between evolving technologies and traditional practices dictates future trends. Awareness of these factors equips stakeholders to innovate and adapt in a fast-changing industrial landscape. As industries continue to prioritize energy efficiency and environmental considerations, mastery of gas cooler heat exchangers will remain essential.