Comprehensive Guide to NX Solid Modeling Techniques
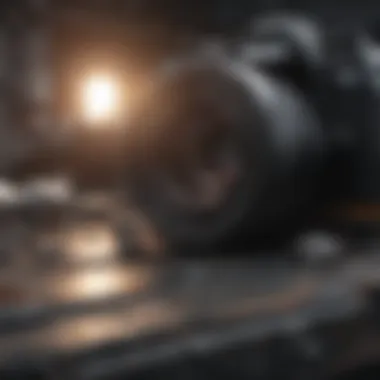
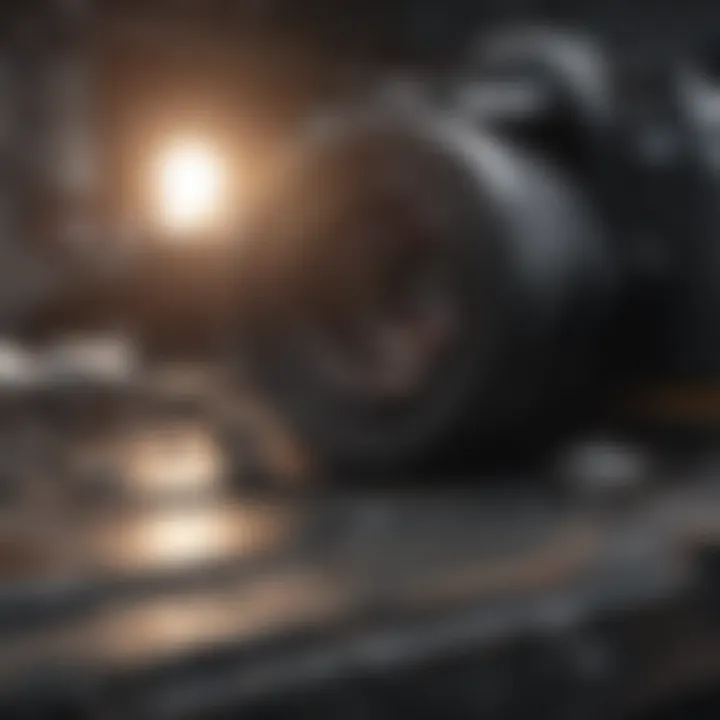
Intro
In the rapidly evolving landscape of computer-aided design, NX solid modeling stands as a pillar of modern engineering and design methodologies. This powerful software not only enhances the precision of three-dimensional representations but also streamlines workflows across various industries. From aerospace to automotive, NX solid modeling provides a sophisticated platform for professionals to bring their innovative ideas to life.
As we embark on this insightful journey, we'll explore the many facets of NX solid modeling. We will uncover its core functionalities, practical applications, and the underlying theories that shape this indispensable tool. A well-rounded understanding of NX solid modeling empowers professionals to navigate its advanced features effectively, thereby optimizing their design processes and bolstering accuracy.
By breaking the content down into digestible sections, this article serves as both an introduction for newcomers and a reference for experienced users. Let's dive into the key concepts that form the backbone of NX solid modeling, setting the stage for a comprehensive exploration of this essential CAD software.
Prelude to NX Solid Modeling
In the realm of computer-aided design (CAD), NX Solid Modeling stands as a cornerstone for creating detailed three-dimensional (3D) representations of products. The significance of this modeling technique cannot be overstated; it merges the worlds of engineering and creativity, providing tools that are not just functional but also innovative. Understanding this approach is vital for anyone involved in design, engineering, or manufacturing.
Investing time to grasp NX Solid Modeling opens doors to enhanced accuracy in designs. This process is not merely about making things look pretty. It's about making them work effectively in real-world applications. The precision that comes with solid modeling is a game changer, whether you're dealing with intricate components for aerospace or simple fixtures in a workshop.
When we talk about the benefits, itās impossible to overlook the efficiency that solid modeling offers. Designers can quickly iterate on ideas, modifying parameters and instantly seeing changes. This flexibility far outweighs the traditional methods where alterations often meant starting from scratch. With NX, the ability to create complex forms and simulate how they'll perform under stress is invaluableāa real feather in the cap for professionals looking to push boundaries.
However, beyond the practical benefits lies a wealth of knowledge regarding its historical context and development. The leap from 2D drafting to sophisticated 3D modeling has transformed the landscape of design. Familiarity with this evolution helps in appreciating the robust features that NX Solid Modeling brings to the table.
The following sections will delve deeper into defining what NX Solid Modeling encompasses, its historical roots, and how it has carved its niche in both education and industry practices. Understanding these factors not only enriches the user's capabilities but also equips them with an essential skill set suitable for today's fast-paced engineering environment.
"Innovation distinguishes between a leader and a follower." āSteve Jobs
What is NX Solid Modeling?
NX Solid Modeling is a specialized CAD software that enables the creation of 3D solid models using a parametric modeling framework. Unlike basic modeling tools, NX allows users to define their designs with dimensions and constraints that can be easily modified. This means you can change one aspect of a model, and all associated features will adjust accordingly.
The solid models created using NX encompass not just the visual aspects but also the physical properties that provide insights into performance. Features include solid geometry construction, Boolean operations, and surface treatmentsāall of which can be manipulated in real-time. The software also integrates seamlessly with various simulation tools, making it a versatile choice for engineers.
Historical Context and Development
To appreciate the current capabilities of NX Solid Modeling, itās essential to consider its historical backdrop. The evolution began in the late 1960s and early 1970s when computer-aided design tools started transitioning from 2D drafting to 3D modeling. Initially, the focus was on geometric modeling, emphasizing how objects could be represented using mathematical equations.
As technology advanced, so did NX. Originally developed by McDonnell Douglas in the 1980s, this software was one of the first to implement a fully integrated CAD environment. Over the subsequent decades, continual improvements were made, including advancements in user interfaces, better algorithms for rendering, and more sophisticated simulation functionality.
In today's context, NX Solid Modeling is celebrated not just for its technical prowess but also its collaborative capabilitiesāenabling teams across various locations to work together seamlessly.
Thus, by examining the foundations and development trajectory of NX, we see how this software has reshaped the landscape of design, standing out as an essential tool in engineering and manufacturing today.
Core Concepts of Solid Modeling
Understanding the core concepts of solid modeling is like laying the foundational bricks for a sturdy building. It sets the stage for everything that follows, providing essential knowledge that designers, engineers, and CAD professionals rely on to create effective models. This section dives into the fundamentals that underpin solid modeling, with emphasis on solid geometry, parametric modeling, and the distinctions between solid and surface modeling. Each of these components plays a critical role in developing sophisticated designs and improving overall productivity.
Understanding Solid Geometry
Solid geometry forms the backbone of 3D modeling. It refers to the study of three-dimensional figures and their properties. In the realm of CAD, understanding solid geometry ensures that designers can accurately represent physical objects in a digital space. The essence of solid geometry lies in its ability to convey physical characteristics, such as volume, mass, surface area, and spatial relationships. Designers often utilize basic geometric shapesālike cubes, spheres, and cylindersāas building blocks, which can be manipulated to create complex structures.
For example, when you create a simple cube in NX, the software translates this geometric shape into mathematical representations that define its edges, faces, and vertices. This mathematical foundation allows for intricate operations, such as rotations and transformations, thus enabling users to visualize how different components interact within a model.
In essence, a solid understanding of solid geometry not only boosts modeling precision but also enhances a designer's ability to visualize end products before they even hit the manufacturing floor. As the old adage goes, "measure twice, cut once," and in solid modeling, understanding geometry is akin to doing that necessary measuring first.
The Role of Parametric Modeling
In the world of CAD, parametric modeling stands out as a game changer. It allows users to build models based on parameters or constraints. Instead of manually adjusting features, users define relationships between different elements to create a model that can adapt to changes dynamically. This adaptability means that if one dimension changes, the entire model recalibrates automatically, saving time and reducing errors.
For instance, if a designer is working on a mechanical part that requires a specific diameter, by setting that diameter as a parameter, they can quickly adjust it as per requirements without having to redraw the entire part. This flexibility not only speeds up the design process but also significantly enhances accuracy since any alterations propagate through the model with consistency.
Moreover, parametric modeling encourages design iteration. Designers can showcase multiple variations quickly, making it easier to evaluate alternatives during the development phase. This functionality is invaluable; in industries where products must be fine-tuned for performance or manufacturability, the ability to pivot based on feedback is paramount.
Differences Between Solid and Surface Modeling
While both solid and surface modeling are integral to CAD, they serve distinct purposes and hold different implications for design.
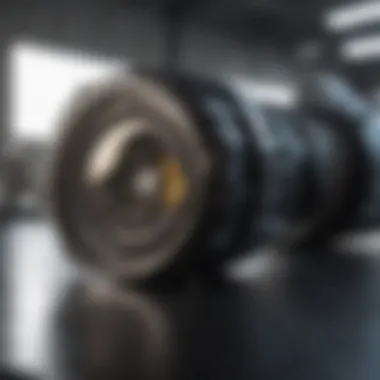
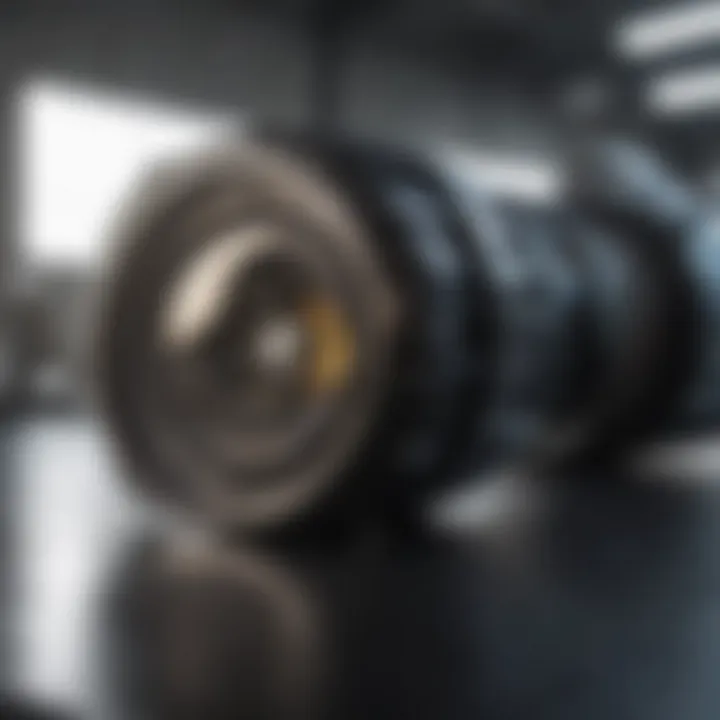
- Solid Modeling
- Surface Modeling
- Represents volumes and solid forms. It defines physical characteristics applicable in real-world scenarios.
- A solid model can support features like mass properties, volumetric calculations, and collision detection, which are crucial for engineering analysis.
- Focuses mainly on the surface geometry of a design. It does not inherently convey information about mass or volume.
- Useful for creating complex shapes, especially when aesthetics or surface continuity is a priority, making it a favored choice in industries like automotive and aerospace for styling purposes.
One might say that solid modeling is like crafting a robust statue from marble, where every cut adds substance and volume, while surface modeling acts more like a finely detailed fabric, concentrating on the textures and visual surface appearances.
Understanding these differences is fundamental for selecting the appropriate modeling technique based on project requirements. Remember, the choice between solid and surface modeling often comes down to the goals of the design. The implications of this choice reverberate throughout the entire development process, influencing both the technical aspects and the eventual aesthetics of the final product.
Key Features of NX Solid Modeling
The landscape of computer-aided design (CAD) is riddled with tools and technologies that serve the needs of designers and engineers, but NX Solid Modeling stands as a prominent pillar. Its key features cater to a variety of requirements, providing an array of advantages that enhance the process of design and development. With a foundation rooted in advanced engineering principles, NX Solid Modeling excels in offering functionalities that are both adaptable and intuitive. This section dives into its essential components, underscoring how they contribute to efficient workflows, improved accuracy, and collaborative potential among stakeholders.
Sketching Tools and Techniques
Sketching in NX goes beyond mere lines and curves; itās about laying the groundwork for future designs with precision and clarity. The software offers a suite of sketching tools that allow designers to create detailed 2D sketches which serve as the blueprint for their 3D models. Features such as constraints, dimensions, and geometric relationships enable users to control the shape and size of sketches, promoting consistency and accuracy in the modeling process.
Additionally, the use of parametric sketching provides a significant tactical edge. For instance, when one dimension is changed, all related dimensions update automatically. This bi-directional referencing serves to save time and reduce errors, making it simpler to iterate on designs without starting from scratch each time.
3D Modeling Techniques
Once the sketches are completed, transitioning to 3D modeling requires not only skill but also effective tools. NX Solid Modeling has a diverse range of 3D modeling techniques, enabling designers to transform their sketches into intricate models. With functionalities such as extrusion, revolution, and sweeping, users can create complex geometries that meet their design specifications.
Furthermore, the use of synchronous technology in NX simplifies the process of editing models. Modifications can be made directly on the 3D geometry, without needing to revert to the original sketches. This flexibility is essential for design teams working on iterations based on client feedback or engineering revisions.
Assembly Modeling and Management
In the realm of product design, the ability to model assemblies accurately is crucial. NX facilitates this process through its assembly modeling capabilities. Users can assemble multiple parts together, defining how they fit and interact in a cohesive unit. This is not just about visual representation; it extends to understanding how components behave under different conditions.
With assembly constraints and motion studies, teams can analyze the dynamics of their assemblies. This foresight helps identify potential design flaws before moving into production. Additionally, version control features aid in managing changes over time, ensuring that all collaborators remain aligned on the latest updates.
Advanced Simulation Capabilities
Simulation is a vital part of the design process, allowing users to test the performance of their designs under various conditions. NX Solid Modeling integrates advanced simulation tools that provide feedback on factors such as stress, heat, and motion. These simulations are not just theoretical; they mirror realistic scenarios, giving insight into how a model will perform in the real world.
Tools such as finite element analysis (FEA) and computational fluid dynamics (CFD) enable engineers to make informed decisions about materials and design configurations. This capability to simulate real-world behavior leads to products that are more reliable, ultimately enhancing customer satisfaction.
"The features of NX Solid Modeling do not merely improve efficiency; they fundamentally alter the trajectory of product development by integrating testing and modeling in a streamlined manner."
Through these key features, NX Solid Modeling not only addresses the immediate requirements of designers but also sets the stage for innovation in product development and engineering. As firms look to stay competitive, embracing the full functionality of NX ensures that they are not just keeping pace but leading the charge into the future of design.
Applications of NX Solid Modeling
In the realm of computer-aided design (CAD), NX solid modeling proves to be a game changer. Its applications stretch across various industries, providing robust solutions that cater to the intricate needs of engineering, manufacturing, and product development. From crafting complex geometries to fostering seamless collaboration among team members, the significance of NX solid modeling cannot be overstated. This section delves into the core applications that make NX an indispensable tool in modern design processes.
Engineering Design
Engineering design is one of the primary arenas where NX solid modeling shines brightly. The sophisticated tools within NX empower engineers to transform abstract ideas into concrete designs with remarkable precision. This involves not just creating basic shapes, but intricately detailed models that encapsulate intricate design specifications. When engineers use NX, they can leverage features like parametric modeling, which allows modifications to propagate through all associated elements. This capability ensures that if a change is required, it can be cascaded through the design without needing to redo each individual part.
Moreover, the simulation tools integrated with NX allow engineers to visualize how their designs will perform under various conditions. This predictive power leads to smarter, safer, and more cost-effective designs before they hit the production floor. In a rapidly evolving industry, the ability to quickly prototype and test is invaluable.
Product Development
Product development, much like engineering design, benefits significantly from NX solid modeling. As products evolve from concept to market, maintaining coordination across departments becomes imperative. NX facilitates this by providing a unified platform where design, documentation, and manufacturing considerations are intertwined.
With NX, teams can create comprehensive 3D models that serve not just as visual representations, but as real-world validation tools. For example, when developing a new consumer electronic device, designers can model every component, analyze the assembly process, and even simulate user interactions. This results in a product that is not just innovative but aligns perfectly with consumer expectations and manufacturability.
Manufacturing Processes
In manufacturing, efficiency often dictates success. NX solid modeling allows manufacturers to refine their processes by providing an accurate digital twin of the end product. This means potential issuesābe it in assembly line configuration or material compatibilityācan be identified and addressed early in the design process.
Consider how an automotive manufacturer utilizes NX. Before production, engineers can simulate the welding process for car components. By understanding potential weaknesses, adjustments can be made to both design and manufacturing procedures to enhance product durability and reduce costs. Consequently, applications in this sector not only streamline operations but also enable companies to remain competitive in a saturated market.
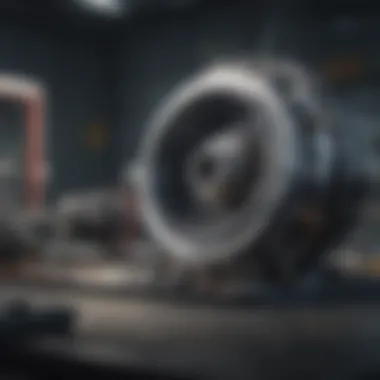
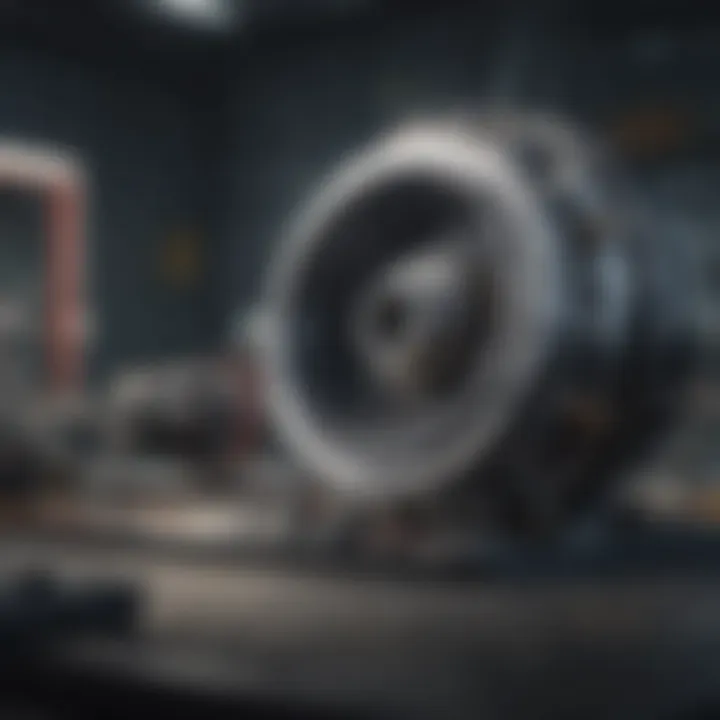
Collaborative Projects
The collaborative dimension of NX solid modeling is another key aspect that enhances its utility in various projects. In an age where remote teamwork is becoming the norm, NX provides tools that enable real-time collaboration. Designers and engineers can work simultaneously on the same model, with changes reflected instantly for all users. This is a breath of fresh air in project management, reducing the likelihood of miscommunications and errors.
Furthermore, integrating tools like Teamcenter within NX ensures that all teams are up to speed on the latest project developments. Documentation, revisions, and communication all come together seamlessly, making the entire process much more efficient. As workflows become more fluid, teams can tap into their collective expertise, driving innovation and leading to superior outcomes.
"The more collaborative the approach, the richer the final outcomeāNX solid modeling embodies that principle."
In summary, the applications of NX solid modeling span from engineering design to complex manufacturing scenarios and collaborative project work. Each facet showcases how NX not only enhances the design process but also fortifies the capacity for teams to work together effectively, ensuring that the end product meets the highest standards.
Theoretical Foundations of Solid Modeling
Understanding the theoretical foundations of solid modeling is crucial for anyone looking to leverage NX solid modeling to its fullest potential. Not only does it establish the groundwork upon which solid modeling techniques operate, but it also equips users with the knowledge to innovate and troubleshoot effectively. When users grasp these concepts, they can navigate challenges with confidence and think critically about their modeling choices. This section delves into the mathematical principles and geometric techniques that underpin this essential CAD tool.
Mathematical Principles in Solid Modeling
Mathematics serves as the backbone of many engineering disciplines, and solid modeling is no exception. At the core of solid geometry are various mathematical principles that dictate how shapes and volumes are defined and manipulated. Understanding these principles can enhance oneās ability to create accurate models.
- Coordinate Systems:
- Transformation Operations:
- Topology and Set Theory:
- Calculus in Modeling:
- NX solid modeling employs Cartesian coordinate systems, which create a reference framework. Knowing how these coordinates influence the placement and dimensions of objects is key.
- Users can define points in space using coordinates, allowing for precise modeling.
- Transformation techniques, like translation, rotation, and scaling, are essential for modifying geometric shapes.
- Each transformation can be mathematically described, allowing for consistent reproductions of shapes in different contexts.
- Topological concepts are often applied in solid modeling to understand how different components fit together within a design.
- Knowledge of set theory helps in managing groups of geometric entities, which becomes important during complex design processes.
- While basic calculus is often not explicitly used in the daily functions of NX, understanding rates of change and limits allows designers to create dynamic models that respond to varying parameters.
- For instance, parametric modeling revolves around these principles, letting modifications flow through the design seamlessly.
The interplay of these mathematical principles enhances both the creativity and functionality of solid modeling. Therefore, investing time in mastering these can pay dividends in accuracy and efficiency.
Geometric Modeling Techniques
Geometric modeling techniques provide the practical tools to implement theoretical knowledge into actual designs. Understanding geometric modeling is vital for successful application in NX solid modeling. Here's a closer look at fundamental techniques:
- Primitive Shapes:
- Boolean Operations:
- NURBS and B-Splines:
- Surface versus Solid Modeling:
- Most geometric designs begin with primitive shapesācubes, spheres, cylinders, and cones. These shapes form the base for more complex designs.
- By combining and modifying these basics, a modeler can explore various geometric configurations.
- Essential for modeling, Boolean operations involve combining two or more solid models through union, intersection, or subtraction.
- For designers, mastering these operations enables environmental adaptation of models to fulfill specific requirements or resolve space limitations.
- Non-Uniform Rational B-Splines (NURBS) provide more flexibility in designing freeform shapes.
- This technique is essential for industries like automotive design, where aerodynamic properties and aesthetics are critical.
- Understanding the difference between surface and solid modeling is crucial as they serve different purposes.
- Surface modeling focuses on creating complex shapes without necessarily defining their volume, while solid modeling captures both geometry and space.
"In the world of design, comprehension of geometric techniques lies at the heart of all successful projects."
By mastering these geometric modeling techniques, designers can better utilize NX solid modelingās capabilities. The investment in understanding these foundations prepares users to tackle more advanced modeling challenges with ease and precision.
Advantages of Using NX Solid Modeling
NX Solid Modeling brings a myriad of advantages that enhance design practices and streamline workflows. It serves as a catalyst for increasing productivity in various industries, enabling the creation of detailed and precise models. Letās delve into its main benefits and discern why it continues to be a preferred choice among professionals.
Increased Efficiency and Accuracy
When it comes to CAD applications, efficiency and accuracy are not just desirable; they are essential. NX Solid Modeling equips users with a set of tools that automate repetitive tasks, allowing for quicker iterations and better use of time. Utilizing parametric features supports designers in making changes without starting from scratch. For instance, if an engineer decides to modify a design's dimensions, NX automatically updates interconnected components. This ensures consistency throughout the model, reducing errors and rework.
Moreover, the softwareās precise geometry capabilities support the creation of highly accurate models. This is crucial in fields such as aerospace or automotive design, where even the slightest deviation can lead to significant safety concerns. Engineers can trust that the specifications they set get translated perfectly into the final product.
Enhanced Design Collaboration
In a world where teamwork defines success, NX Solid Modeling shines as a powerful collaborative platform. It allows multiple users to work on the same project simultaneously, a feature known as concurrent engineering. Designers, engineers, and manufacturers can easily share and access model updates in real time. This tends to minimize misunderstandings and the back-and-forth that typically slows down projects.
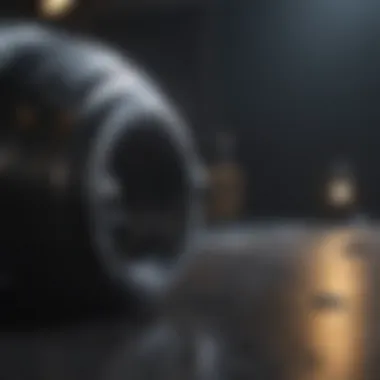
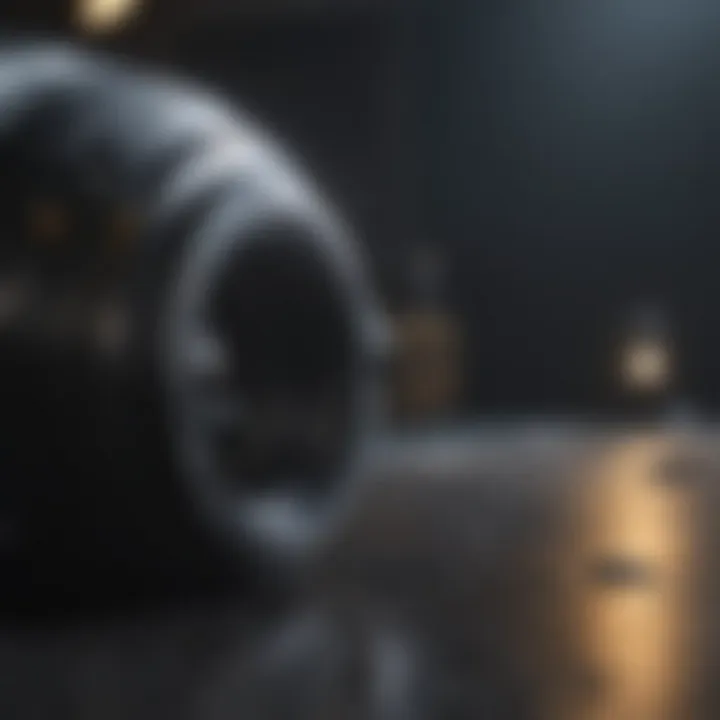
Furthermore, the integration of various tools within the NX ecosystem enables seamless communication across departments. An aspect worth noting is how data can be exported to other formats effortlessly, making it easier for teams using different software to still work together effectively.
Key features that facilitate collaboration include:
- Version Control: Keeps track of changes, ensuring everyone's on the same page.
- Team Reviews: Allows for feedback and adjustments, fostering a collaborative atmosphere.
- Cloud-Based Sharing: Gives teams the flexibility to work from anywhere, which is a boon for remote setups.
"In the age of collaboration, NX Solid Modeling isn't merely a tool; it's a bridge between visions and realizations."
In summary, the advantages of using NX Solid Modeling lie fundamentally in its ability to boost efficiency and accuracy while promoting a collaborative environment. These factors not only enhance the quality of designs but also help in meeting stringent deadlines without sacrificing the integrity or performance of products. As industries continue to evolve, embracing tools like NX becomes not just beneficial, but vital for sustaining a competitive edge.
Challenges and Considerations
When it comes to NX Solid Modeling, it's essential to recognize the hurdles that users might face. Understanding challenges and considerations is as crucial as mastering the tools themselves. This segment addresses both the practical difficulties users may experience and the limitations inherent in the software, providing a clearer picture for those who are diving into this advanced space.
Learning Curve for New Users
Getting up to speed with NX Solid Modeling can be quite a task, especially for new users. The initial engagement with the software can feel like learning a new language. The interface is rich with features, but this complexity can be overwhelming. Key areas where new users may struggle include:
- Navigating the User Interface: While powerful, the layout is not especially intuitive. Users may find themselves lost among menus and options, hindering their learning process.
- Understanding Core Concepts: Newcomers should grasp solid modeling principles beforehand. Without this foundation, it's easy to make mistakes that could set back their learning journey.
- Practice Orientation: Like riding a bike, mastering NX requires practice. Hands-on experience plays a big role. However, many users might not have enough real-world tasks to build their skills initially.
Due to these factors, organizations should consider implementing thorough training programs. Such offerings can help shorten the learning curve, ensuring that new users can fully leverage NX's capabilities.
Software Limitations
Despite its robust features, NX Solid Modeling does have its quirks and shortcomings. Understanding these limitations is vital to avoid potential frustrations later on. Here are some common challenges users might face:
- Performance Issues: As the complexity of models increases, so can the demands on system resources. Users might encounter slow response times or lag, particularly with large assemblies. Ensuring that hardware meets NX's specifications is critical.
- Limited Compatibility: While NX is compatible with many standards, it may not support every format one encounters. This can restrict collaboration with teams using other CAD software, causing extra conversion steps that could lead to errors.
- High Costs: NX is not the most budget-friendly option out there. For individuals or smaller companies, these costs can be a significant consideration, especially when weighing features against price.
"Understanding the challenges of NX Solid Modeling is not just about recognizing stumbling blocks but also about preparing to navigate them strategically."
Future Trends in Solid Modeling
In an ever-evolving landscape of technology, solid modeling is poised for significant advancements. The relevance of discussing future trends in this domain cannot be overstated. As industries demand increasingly complex designs that harmonize with the latest technological innovations, solid modeling tools, particularly NX, must adapt to these emerging expectations. This section not only highlights the elements shaping future developments but also underscores the benefits of incorporating these trends into practical applications.
Integration with Emerging Technologies
One of the most exciting aspects of future solid modeling lies in the integration with emerging technologies. As we navigate through the fourth industrial revolution, the blending of Internet of Things (IoT), Augmented Reality (AR), and Virtual Reality (VR) into CAD processes is becoming more prevalent.
- IoT and Solid Modeling: With the surge of IoT, solid models can be augmented with real-time data. For instance, imagine designing a smart bridge that adjusts its structural integrity based on sensor feedback. This synergy enhances safety and can lead to more efficient maintenance strategies.
- AR and VR Applications: Augmented and virtual realities offer immersive environments for testing designs. Engineers and designers can visualize and interact with their models in a more intuitive way. For example, simulating a vehicle's design in a virtual space allows for immediate feedback on ergonomics and function. This iterative process is crucial in refining designs before any physical prototypes are built.
Impact of Artificial Intelligence and Machine Learning
The ramifications of artificial intelligence (AI) and machine learning (ML) on solid modeling are profound. By leveraging the analytical power of AI and ML algorithms, designers can unlock a new realm of automation, making model revisions and optimizations more intuitive.
- Predictive Design Adjustments: Imagine that an AI-driven tool could anticipate performance issues based on initial designs, suggesting alterations before any errors occur in the manufacturing phase. This shift can drastically reduce costs and time spent on revisions.
- Enhanced Customization: Machine learning can analyze user patterns to provide tailored suggestions for design improvements. It can streamline workflows by learning from past projects and informing the designer of the best practices and potential pitfalls.
In summary, the convergence of solid modeling with cutting-edge technologies like IoT, AR, VR, AI, and ML is set to revolutionize the design and engineering landscape, making it crucial for professionals to stay abreast of these trends.
As these technologies continue to mature, the future of NX solid modeling will not only enhance functionality and user experience but will also propel industries towards innovative solutions that meet the demands of tomorrow. The ongoing engagement with these trends will be vital for anyone looking to thrive in the world of design and engineering.
Culmination
In the rapidly evolving landscape of computer-aided design (CAD), NX solid modeling stands out as an essential tool, intricately blending creativity with precision. The importance of this software lies not only in its robust functionalities but also in its role as a facilitator for various industries, enabling them to innovate and improve their design processes.
Summarizing the Importance of NX Solid Modeling
NX solid modeling plays a transformative role in engineering, manufacturing, and product development. Its importance can be boiled down into several key elements:
- Enhanced Precision: The software utilizes parametric design principles that allow for high levels of accuracy. Designs can be easily modified without starting over, saving valuable time.
- Versatile Applications: Whether itās for aerospace, automotive, or consumer goods, NX solid modeling adapts to diverse market needs, ensuring that it remains relevant across sectors.
- Seamless Integration: It integrates well with other tools and technologies, making collaboration among different teams more efficient. The ability to share resources aids in cross-discipline projects.
- Advanced Simulation Features: With sophisticated simulation capabilities, users can foresee potential issues in design and address them before they escalate into costly problems.
These aspects illustrate the software's significance in shaping the future of design.
Encouraging Adoption of Advanced Modeling Techniques
For organizations and individuals entrenched in outdated modeling methods, the shift to NX solid modeling can appear daunting. However, the benefits far outweigh the temporary discomfort of transitioning to new practices. Here are a few persuasive points for adoption:
- Future-proof Skills: By embracing NX solid modeling, designers and engineers enhance their skill set, making them more valuable in a competitive job market.
- Streamlined Workflows: Advanced modeling techniques simplify complex tasks, allowing teams to focus on innovation rather than getting bogged down in mundane processes.
- Cost Savings: In the long run, the precision and efficiency gained from using NX can lead to significant cost reductions due to less material waste and fewer errors, which could otherwise derail projects.
- Improved Collaboration: Shared platforms foster better communication among team members, leading to richer ideas and stronger outcomes.
By fostering an environment that encourages the use of NX solid modeling, organizations can not only enhance their productivity but also unlock potential that stagnant methods canāt offer.