High Temperature Bearings: Comprehensive Insights

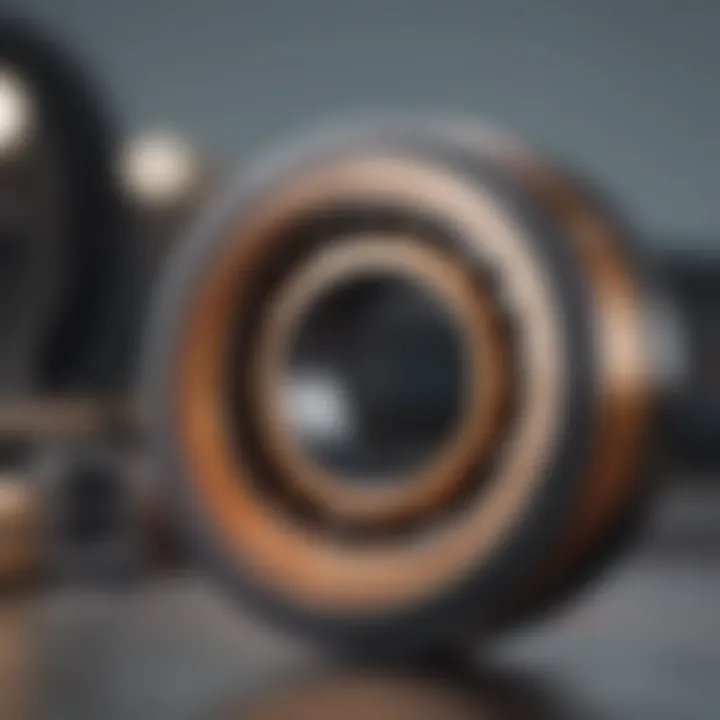
Intro
High temperature bearings are an unassuming yet critical component of many industrial applications. Often overlooked, they play a pivotal role in machinery that operates under extreme thermal conditions. Places like steel mills, aerospace, and power plants rely on these bearings to keep their operations running smoothly. This article takes a deep dive into high temperature bearings, exploring their construction, materials, operational advantages, and the innovative technology that puts them at the forefront of industrial applications.
Understanding high temperature bearings is paramount for professionals and researchers as it not only influences the design and operation of machinery but also impacts overall efficiency, safety, and longevity in various sectors. With a myriad of applications and the potential for cutting-edge advancements, this article aims to furnish readers with a clear and thorough grasp of this specialized subject.
Key Concepts
Definition of Primary Terms
High temperature bearings are specialized bearings designed to maintain performance when exposed to elevated temperatures, often exceeding 150 degrees Celsius. Common materials used include ceramics, advanced polymers, and high-performance steel alloys. These materials are engineered to withstand thermal expansion, oxidation, and wear under prolonged intense heat.
Related Concepts and Theories
Understanding high temperature bearings requires familiarity with several related concepts:
- Thermal Expansion: As temperatures rise, materials commonly expand. High temperature bearings must accommodate this factor to maintain functionality.
- Hydrodynamic Lubrication: This concept describes how lubricant forms a film between the bearing surfaces, preventing direct contact and wear under heat. Selecting the right lubricant is even more critical in high-temperature scenarios.
- Material Science Advances: Innovations in materials science have paved the way for the development of unique composites. These materials can offer not just heat resistance, but also increased durability and reduced friction.
"Advanced materials science is not merely a branch of engineering; it is the backbone of today’s efficient high temperature bearing solutions."
Advantages of High Temperature Bearings
Incorporating high temperature bearings into machinery provides numerous benefits:
- Increased Efficiency: These bearings maintain their performance in intense heat, helping machines function smoothly without interruptions.
- Extended Lifespan: The durability of advanced materials leads to less wear and tear, significantly boosting the lifespan of the machinery.
- Cost-Effectiveness: While the upfront costs of high temperature bearings can be significant, the reduced need for maintenance and downtime proves economical in the long term.
Applications in Various Industries
Common industries utilizing high temperature bearings include:
- Aerospace: Where extreme conditions are part and parcel of engine operations and control systems.
- Energy Production: Essential in turbine applications where high heat is a constant factor.
- Metal Processing: In manufacturing lines, where metal parts are generated and molded, bearings keep machinery efficient during high-temperature phases.
Maintenance Considerations
High temperature bearings demand careful maintenance. This can involve regular inspections to check for wear, ensuring that lubricant levels are adequate and evaluating temperature fluctuations that may signal abnormalities.
Best Practices
- Regularly monitor and replace lubricants, choosing those specifically designed for high temperature applications.
- Schedule periodic evaluations of bearings for signs of thermal fatigue or material degradation.
Future Directions
As technology continually evolves, so does the arena of high temperature bearings. Understanding both gaps in current research and innovations will be vital in the quest for efficiency and sustainability in industrial applications.
Gaps Identified in Current Research
There remains a need for deeper exploration into:
- The efficiency of newer composite materials under extreme duress.
- Long-term performance analysis of existing high temperature bearings across various sectors.
Suggestions for Further Studies
Future research could benefit from focusing on:
- Creating hybrid materials that combine the best features of different substances to further enhance performance.
- Investigating automated monitoring systems that could predict failure in high temperature-bearing assemblies before they occur.
Ending
As industrial operations demand higher tolerance to extreme conditions, high temperature bearings carve out their importance. They are often the unsung heroes of machinery, enabling industries to run continuously and efficiently despite significant challenges. A thorough understanding of these components—bolstered by ongoing research and development—will not only enhance machinery performance but also pave the path for technological evolution.
Foreword to High Temperature Bearings
Understanding high temperature bearings is crucial in today's industrious world where equipment operates in extreme thermal conditions. These bearings play a pivotal role in ensuring efficiencies, reliability, and longevity of machinery across various sectors. In this section, we will delve into their core definitions, the underlying functionalities, and explore how these components contribute to performance in high-stress environments. The use of high temperature bearings has become increasingly common in industries such as aerospace, energy production, and heavy manufacturing. This article serves as a comprehensive resource that emphasizes the attributes and advantages of these specialized bearings, arming students, researchers, educators, and professionals with invaluable insights into their workings.
Definition and Functionality
High temperature bearings are specifically designed to operate under elevated thermal conditions, which can often exceed standard tolerances found in regular bearings. These components are fundamental to reducing friction between moving parts while also supporting radial and axial loads. What sets high temperature bearings apart is their capacity to sustain performance levels at high heat, often utilizing advanced materials like ceramics and specialized alloys. Traditional lubricants may break down under intensive heat; hence, high temperature bearings are designed with mechanisms that facilitate proper lubrication without compromising structural integrity. This tailored functionality ensures sustained performance and reliability in demanding conditions, essential in multiple applications.
Historical Development
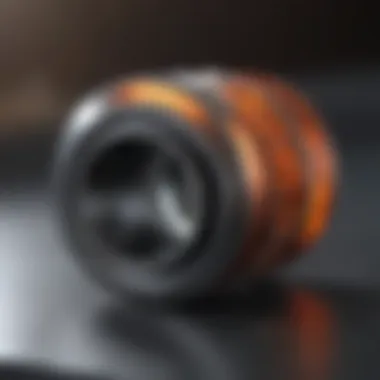
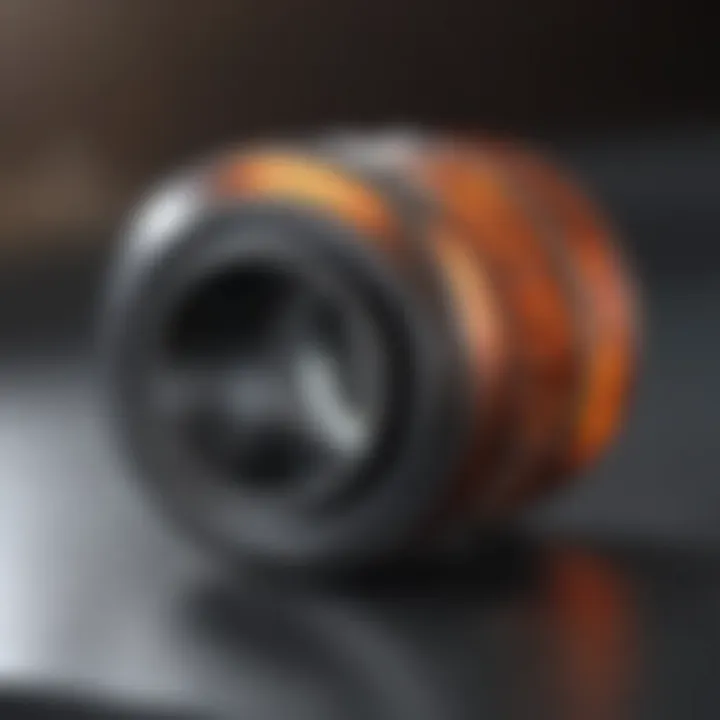
The evolution of bearings has a rich history rooted in human ingenuity. Initially, the concept traces back to simple wood or stone elements used in ancient carts. However, as industrialization surged in the 18th and 19th centuries, the necessity for more sophisticated and durable components arose. High temperature bearings particularly gained traction with the advent of machinery in environments where heat was an inherent byproduct. Early adopters of industrial-grade bearings began experimenting with materials that could withstand increased temperatures, leading to notable advancements by the mid-20th century when synthetic lubricants and new alloys became more commonplace. Today, research continues to push the boundaries of what is possible in bearing technology, emphasizing the ongoing need for innovation and adaptation to meet modern demands.
The journey of high temperature bearings mirrors the broader narrative of industrial progress — an enduring quest for perfection under pressure.
Understanding Bearing Technologies
When discussing high temperature bearings, it’s essential to grasp the foundational bearing technologies that form the basis of their functionality. These technologies not only dictate how bearings perform under strenuous conditions but also influence their durability and efficiency in varied applications. Understanding these technologies helps distinguish the efficient designs from the ineffective ones, illuminating options available for specific industrial needs.
Rolling Bearings
Rolling bearings are among the most prevalent types utilized across numerous industries. These bearings facilitate motion by utilizing rolling elements, such as balls or rollers, which move between inner and outer raceways. The core advantage of rolling bearings is their ability to reduce friction significantly compared to plain bearings. This reduction translates into less wear and tear, ultimately extending the lifespan of both the bearing and the machinery it supports.
The structure of rolling bearings can be relatively straightforward, yet they’re engineered to endure substantial loads and high speeds. Materials such as ceramics and advanced metallic alloys often play a pivotal role in their construction, enhancing their ability to withstand high temperatures.
- Key components of rolling bearings include:
- Inner ring: Connects to the shaft, facilitating rotation.
- Outer ring: Static part which the inner ring rolls against.
- Rolling elements: Balls or rollers that facilitate the motion.
"The choice of rolling bearing type can significantly impact efficiency and performance in high-stress applications."
In high-temperature scenarios, the selection of proper lubrication is critical since conventional lubricants may break down under extreme conditions. Advanced oils or even solid lubricants, like graphite, are often employed to maintain function without compromising structural integrity.
Plain Bearings
Contrary to rolling bearings, plain bearings operate without rolling elements. Instead, they rely on sliding contact between surfaces. While they might not be as efficient in terms of friction reduction as rolling bearings, plain bearings can be tailored to specific applications where space or load conditions dictate.
One distinct advantage lies in their simplicity and ease of maintenance. Plain bearings can often be made from composite materials or specially treated metals that enhance their performance at elevated temperatures. The design allows for the distribution of load over a larger area, reducing the risk of surface fatigue in high-stress environments.
- Common types of plain bearings include:
- Sleeve bearings: Where the shaft slides within a cylindrical tube.
- Thrust bearings: Designed to handle axial loads, preventing movement along the shaft’s length.
In high-temperature applications, ensuring that the bearing surface remains smooth and well-lubricated is crucial. This minimizes wear and allows the bearing to keep functioning despite the high levels of thermal expansion they may be exposed to.
Both rolling and plain bearings have their unique advantages and challenges in high-temperature settings. By selecting the right type based on specific needs, engineers can optimize machinery performance and longevity, ensuring reliable function despite the heat. Understanding these bearing technologies is essential for anyone involved in machinery design or maintenance.
Materials for High Temperature Bearings
In the realm of high temperature bearings, the materials utilized are of utmost importance. The right materials can drastically influence the performance, longevity, and reliability of bearings used in extreme thermal conditions. They must not only withstand high temperatures but also manage the stresses inherent in their respective applications. The selection process involves a meticulous analysis of thermal stability, mechanical properties, and environmental resistance, making it a cornerstone of high temperature bearing design.
Choosing high temperature bearing materials is not a one-size-fits-all scenario. Each application presents unique challenges, making it crucial to tailor material properties to specific needs. For instance, in environments where heat is coupled with corrosive elements, resistance to oxidation and wear becomes essential.
Ceramic Materials
Ceramic materials have carved a niche for themselves in high temperature applications. They boast several advantageous properties, including excellent thermal stability and lightweight characteristics. These materials can endure temperatures that would melt many metals, often exceeding 1000°C. The high hardness of ceramics minimizes wear and prolongs service life, reducing the frequency of replacements, which can save time and costs in a commercial setting.
Common ceramics like silicon nitride and zirconia demonstrate impressive fracturing toughness and provide a solution to heat-induced issues. They also exhibit low thermal expansion, which ensures dimensional stability. However, there are considerations to bear in mind; ceramic materials are typically brittle, so handling and structural design must be approached with care to prevent catastrophic failures.
Metallic Alloys
When discussing high temperature bearings, metallic alloys cannot be overlooked. These materials have evolved significantly to meet the demands of modern engineering. Superalloys, such as Inconel and Hastelloy, are particularly noteworthy for their exceptional strength and resistance to thermal degradation. They maintain their mechanical properties at elevated temperatures, ensuring that they can function effectively in challenging environments like turbine engines or industrial furnaces.
An asset of metallic alloys is their malleability, which allows them to be shaped into intricate designs for bearing architecture. Moreover, the availability of advancements in metallurgy has opened doors for even more refined compositions designed to resist wear and fatigue. However, at high temperatures, thermal expansion and potential reactions with lubricants can present potential risks, thus proper selection is vital.
Composites and Hybrid Materials
In recent years, the use of composites and hybrid materials has gained traction in high temperature bearings. These materials combine the best attributes of different components, resulting in enhanced performance characteristics. For instance, a hybrid that merges metal with a reinforcing ceramic can deliver both strength and improved thermal stability.
Such materials are not only lighter but often exhibit significant resistance to thermal shock, making them suitable for applications where typical metals might fail. They can also be engineered to offer tailored thermal expansion properties, thus fitting seamlessly into their specific bearing environments. Yet, it’s prudent to recognize limitations in terms of manufacturing costs and potential complexities in production processes.
"The materials selected for high temperature bearings not only define their operational capability but can also affect overall system efficiency and maintenance protocols."
In summary, selecting materials for high temperature bearings is a balancing act. The interplay of factors including maximum operating temperature, stress profiles, and environmental exposure underlines the absolute need for informed material choices. Only by addressing these aspects can the industry ensure reliability and operational success in applications exposed to high temperatures.
Design Considerations for High Temperature Bearings
When delving into high temperature bearings, it becomes evident that the design considerations are a linchpin for ensuring performance and longevity. These bearings frequently encounter harsh conditions that can drastically affect their operational efficiency. Thus, understanding the intricate details behind their design is not just beneficial, but essential. Key factors like load bearing capacity, thermal expansion, and lubrication challenges must not be overlooked if we want to optimize the usage of these advanced components.
Load Bearing Capacity
Load bearing capacity is arguably one of the most critical aspects in the design of high temperature bearings. Under high thermal conditions, the stresses on the bearing can increase, making it vital for the components to withstand those additional loads. For example, in an industrial furnace, where bearings might be exposed to temperatures topping 600 degrees Celsius, the materials must not only bear the weight of the machinery but should also maintain structural integrity under these extreme conditions. Traditional materials often falter under such demands, which is why advanced ceramics or specially formulated metallic alloys are commonly implemented.
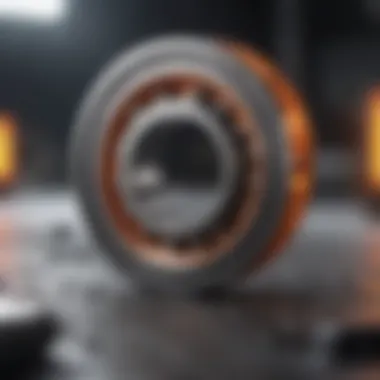
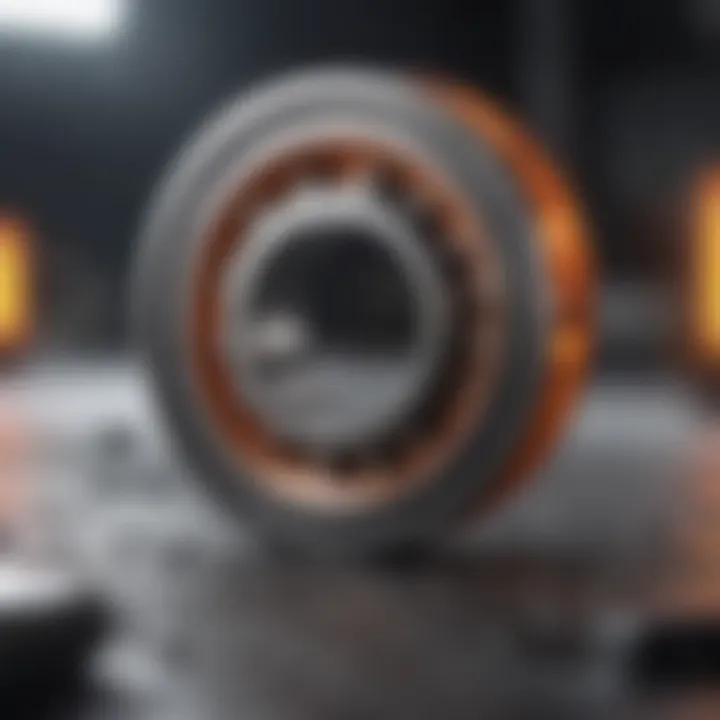
An effective strategy for enhancing load capacity involves using bearings designed with larger contact areas, minimizing localized stress concentrations. This can also be achieved through careful geometric configurations that help in distribution of load. As a general rule, the higher the load bearing capacity, the better the performance in critical applications, thereby reducing maintenance costs and downtime due to failures.
Thermal Expansion Factors
Thermal expansion is another pivotal consideration when designing high temperature bearings. As temperatures rise, most materials expand, which can lead to interference fit issues, tight clearances, or even misalignment. This phenomenon can wreak havoc on bearing performance.
Engineers typically need to account for the coefficient of thermal expansion of the materials used in their designs. For example, if a bearing made of steel is paired with a housing constructed from aluminum, their different expansion rates could result in a high level of stress, compromising the whole assembly. To counteract this, it’s prudent to choose materials with matched thermal expansion coefficients or employ design features such as floating mountings or specialized clearance tolerances that adapt to thermal fluctuations.
"In the world of high temperature bearings, neglecting thermal expansion can lead to premature failure and costly repairs."
By understanding and implementing adequate thermal expansion considerations, the overall reliability of high temperature bearings can significantly improve.
Lubrication Challenges
Lastly, one must never underestimate the lubrication challenges faced in high temperature bearings. At elevated temperatures, conventional lubricants often break down, leading to increased friction and wear. This creates a substantial risk for overheating and eventual bearing failure.
Using advanced lubricants suitable for high-temperature applications is paramount. Options include solid lubricants such as graphite or molybdenum disulfide, which can endure elevated temperatures far better than traditional oils. Alternatively, specially engineered synthetic oils can provide the necessary lubrication while also resisting breakdown.
In addition, the lubrication system design must ensure that the lubricant reaches all critical areas of the bearing. It is essential that engineers address these lubrication challenges proactively to assure the reliability and longevity of high temperature bearings.
Performance Metrics of High Temperature Bearings
Understanding the performance metrics of high temperature bearings is crucial for evaluating their effectiveness in high-stakes environments. These bearings must operate reliably under demanding conditions where standard materials may fail. This section delves into three key performance aspects: friction and wear analysis, thermal resistance, and mechanical stability.
Friction and Wear Analysis
When it comes to bearings, friction is a double-edged sword. On the one hand, a certain level of friction is necessary for effective function; on the other, excessive friction leeches energy and causes wear. High temperature bearings are designed to minimize this friction while withstanding elevated temperatures throughout their operating cycle.
The analysis begins with evaluating the coefficient of friction. This is a critical metric that measures the force resisting motion when two surfaces interact. In high temperature scenarios, materials that might be suitable at room temperature could behave differently when the heat is cranked up.
Some notables are:
- Ceramic vs. Metallic: Ceramics typically offer lower friction coefficients at high temperatures compared to metals, which can suffer from oxidation and other degradation.
- Surface Treatments: Employing advanced surface treatments can significantly reduce wear rates, thereby prolonging bearing life.
"Friction management is the name of the game in ensuring the long-term reliability of high temperature bearings."
In-depth study of materials and proper lubrication strategies directly influence energy efficiency and durability, making this clause a vital consideration in any application.
Thermal Resistance
Thermal resistance determines how bearings cope with heat generated from high operational speeds or environmental conditions. High temperature bearings are crafted with materials that can tolerate substantial thermal stresses without compromising their structural integrity.
Several factors come into play:
- Material Composition: As discussed in previous sections, ceramic materials tend to exhibit superior thermal resistance compared to traditional metallic alloys.
- Cooling Mechanisms: Some applications implement additional cooling methods, such as oil-jet or air cooling, to further enhance thermal resistance.
- Heat Dissipation: A well-designed bearing will have features that promote efficient heat dissipation, preventing hotspots that could lead to catastrophic failure.
In essence, thermal resistance is not just a measurement but a crucial design consideration for high temperature bearings.
Mechanical Stability
Mechanical stability refers to the bearing’s ability to maintain performance under load and thermal fluctuation. This metric encompasses aspects like creep resistance, fatigue strength, and overall structural integrity over time.
Key elements include:
- Load Capacity: There is a direct link between the material used and the load-bearing capacities. High temperature bearings often require materials that won't warp or deform under stress.
- Elasticity and Fatigue: Materials selected for high temperature applications are also evaluated for their elasticity, ensuring they can withstand cyclic loads without generating microfractures.
- Design Integrity: The geometric design of the bearing plays a vital role in ensuring stability. A well-calculated design can aid in evenly distributing loads.
In summary, these performance metrics are not mere numbers on a spec sheet. They reflect the real-world capacities of high temperature bearings to function under extreme conditions, fundamentally impacting reliability, efficiency, and longevity.
Applications of High Temperature Bearings
Understanding the applications of high temperature bearings is crucial for grasping their relevance and benefits across various industries. These specialized components are not just pieces of machinery; they are pivotal in ensuring the efficiency, reliability, and longevity of equipment subjected to extreme thermal conditions. The significance of high temperature bearings can be highlighted through their roles in three primary sectors: aerospace, energy production, and manufacturing processes.
In these applications, the bearings must maintain performance while enduring high loads, thermal expansion, and limited lubrication. Hence, the choice of materials and design play a vital role. Below, we take a closer look at each sector, exploring the unique challenges and advantages that high temperature bearings offer.
Aerospace Industry
The aerospace field is synonymous with high precision and performance under strenuous conditions. High temperature bearings find their place in various aircraft components, from engines to landing gear systems. The materials used in these bearings must withstand not only high temperatures but also vibrations and fluctuating loads.
- Efficiency in Flight: High temperature bearings enhance fuel efficiency by reducing friction in aircraft engines. This boost in performance translates to better fuel economy, which is paramount in aviation.
- Safety Considerations: In aerospace, failure is not an option. Bearings made from advanced ceramic materials, for instance, provide reliability and can function smoothly even in harsh conditions.
- Lightweight Design: The aerospace industry continually seeks to reduce weight. Ceramic bearings are significantly lighter than traditional metallic options, contributing to lower overall aircraft weight.
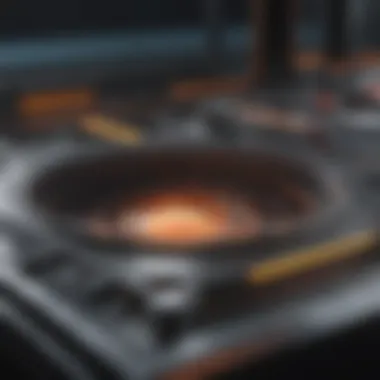
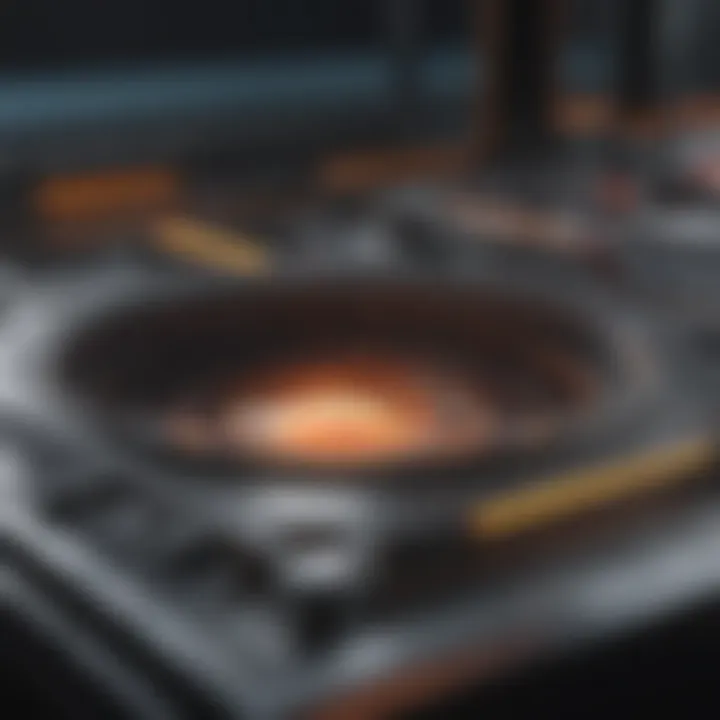
"High temperature bearings not only support the aerodynamic efficiency but also uphold safety standards imperative in aviation."
Energy Production
In energy generation, whether from fossil fuels, nuclear power, or renewables, the machinery often operates under high temperature and pressure. Here, high temperature bearings play an essential role.
- Efficiency in turbines: In gas and steam turbines, high temperature bearings ensure smooth operation, enhancing the overall energy output. This improved efficiency is crucial as energy demands continue to rise.
- Durability against conditions: Energy production machinery often encounters thermal extremes. Utilizing bearings that can withstand significant heat ensures that operations remain optimal, leading to reduced downtime for maintenance.
- Environmental Considerations: Many cutting-edge high temperature bearings are designed with environmental impact in mind. They help make processes more efficient and limit wastage, aligning with sustainable energy goals.
Manufacturing Processes
The manufacturing sector also benefits significantly from high temperature bearings. In processes like metal forging, die casting, and injection molding, machinery often reaches high operational temperatures.
- Increased Production Rates: High temperature bearings enable machines to run faster and for extended periods without overheating. This capability increases production rates and reduces costs.
- Maintenance Optimization: With the durability that high temperature bearings offer, maintenance schedules can be extended. This balance between operational efficiency and reduced shutdown time is beneficial for manufacturing plants aiming for the highest output.
- Versatility in Materials: High performance manufacturing processes often employ a variety of materials. Composites and hybrid bearings allow for a tailored approach, adapting to specific operational needs.
Maintenance and Reliability
In the realm of high temperature bearings, maintenance and reliability are nothing short of essential. Without regular upkeep, even the most advanced bearings can fall prey to wear and tear. High temperature environments place significant strain on these components, causing issues that can lead to failures. Therefore, understanding maintenance procedures not only prolongs their lifespan but also enhances operational efficiency. It's akin to ensuring a finely tuned engine runs smoothly; even a small oversight can lead to a cascade of problems.
Inspection Techniques
Regular inspection of high temperature bearings involves several techniques aimed at identifying early signs of wear or damage.
- Visual Inspection: It’s often the first line of defense. By examining the bearing surfaces for signs of discoloration or cracks, one can gauge the health of the bearing.
- Vibration Analysis: This technique monitors changes in vibration patterns, helping detect issues like imbalance or misalignment, which are common culprits in bearing failure.
- Temperature Monitoring: Keeping an eye on temperature variations is critical. Sudden spikes might indicate lubrication failure or excessive friction.
- Ultrasonic Testing: This non-destructive method uses high-frequency sound waves to identify internal defects. It's invaluable, especially where access is limited.
Through these inspections, operators can gather crucial data on the bearings' operational status.
Failure Analysis
When a high temperature bearing fails, understanding the underlying cause is pivotal. Failure analysis serves as a root cause investigation, aiming to spotlight the factors that led to the breakdown.
- Material Degradation: In high temperature environments, materials can degrade faster. Factors like oxidation and thermal fatigue can erode the integrity of bearings, impacting their reliability.
- Lubrication Issues: Insufficient lubrication can result in increased friction, leading to premature wear. An assessment of the lubrication strategy can reveal if it’s conquering the heat effectively.
- Operational Conditions: The workload and operating environment play significant roles in bearing performance. Overloading or incorrect mounting can precipitate failure.
- Contamination: External particulates, dust, or even improper handling can introduce contaminants that compromise bearing function.
Analyzing these factors not only informs adjustments for future applications, but also contributes to developing improved maintenance protocols.
In summary, the maintenance and reliability of high temperature bearings are fundamental to their functionality in demanding environments. Through diligent inspection techniques and thorough failure analysis, one can ensure that these crucial components perform optimally. Taking a proactive approach can save time and money while ensuring the longevity of the bearings.
Future Trends in High Temperature Bearings
Understanding the future trends in high temperature bearings stands at the crossroads of engineering innovation and evolving industrial needs. As industries push towards higher performance standards, the demand for bearings that can withstand extreme thermal conditions is greater than ever. This section delves into the pivotal developments and considerations that shape the future landscape of these critical components.
Innovations in Material Science
The backbone of advancements in high temperature bearings is the continuous evolution of material science. Researchers are constantly pushing the envelope to discover and develop materials that can resist thermal degradation while maintaining structural integrity.
- Ceramic Composites: One notable innovation is the use of advanced ceramic composites, which offer superior heat resistance and low thermal conductivity. They might be more expensive initially, but their longevity far outweighs the costs in high-stakes environments, such as aerospace applications.
- Self-Lubricating Polymers: Another emerging material trend is the development of self-lubricating polymers. These materials not only reduce friction but also extend the life of bearings under high operational temperatures. When temperatures soar, conventional lubrication tends to fail, leading to wear and tear. Self-lubricating options mitigate this concern effectively.
With these developments, we witness a shift in traditional manufacturing processes. High temperature bearings made from innovative materials allow industries to operate efficiently, with less downtime, even in scorching conditions.
Smart Bearings and IoT Integration
As technology evolves, high temperature bearings are no longer just passive components but are becoming integral parts of smart systems. The integration of the Internet of Things (IoT) into bearing design marks a new era in maintenance and operations, offering noteworthy benefits.
- Real-Time Monitoring: IoT-enabled sensors can provide real-time data regarding the condition of bearings. They track parameters like temperature, vibration, and load, allowing for proactive maintenance. Thus, potential failures can be addressed before leading to costly interruptions.
- Data Analytics: By analyzing data collected from smart bearings, companies can optimize their processes. This allows for tailor-made solutions tailored to specific operational conditions, enhancing both longevity and performance.
Incorporating IoT capabilities into high temperature bearings is not just about improving efficiency. It reshapes how industries perceive and manage maintenance, transitioning from reactive to proactive strategies, which is an invaluable shift in today's fast-paced industrial environment.
"The ongoing advancement in high temperature bearings, fueled by innovations in materials and IoT integration, is pivotal for maximizing performance and reliability in extreme conditions."
The road ahead for bearing technology is bright, replete with possibilities that promise to redefine industrial performance. As manufacturers prioritize longevity and functionality, the importance of understanding these future trends becomes undeniable.
Epilogue
In wrapping up this comprehensive examination of high temperature bearings, it is crucial to appreciate their significance not just in theory but in real-world applications. High temperature bearings play a vital role in ensuring that machinery operates smoothly even under the most trying conditions. Their development has seen significant advancements, bringing about materials and technologies that allow for enhanced performance and longevity.
Summary of Key Points
To recap some of the primary elements discussed:
- Definition and Functionality: High temperature bearings are specifically designed to maintain their structural integrity and functionality in extreme thermal environments.
- Materials: Innovative materials like ceramics and advanced metallic alloys are crucial in crafting bearings capable of withstanding high temperatures.
- Performance Metrics: Metrics like friction resistance, thermal stability, and mechanical resilience are vital for assessing the efficiency of these bearings.
- Applications: Sectors such as aerospace, energy production, and manufacturing benefit greatly from these specialized components which ensure reliable operation.
- Maintenance and Reliability: Understanding how to inspect and analyze failures helps in prolonging the life of these bearings and reducing downtime.
- Future Trends: The integration of technology, particularly smart systems, promise exciting advancements in monitoring and maintaining performance.
Implications for Industry
High temperature bearings are no longer just a niche component; they are becoming essential in various industries that rely on high-efficiency performance. The implications extend beyond manufacturing to sectors such as aerospace and renewable energy, where operational efficacy is paramount.
Organizations that adopt and invest in these advanced bearings can expect benefits like:
- Increased Efficiency: By withstanding extreme temperatures without performance degradation, businesses can enhance overall equipment effectiveness (OEE).
- Cost Savings: Reduced maintenance requirements and longer lifespan can lead to significant savings in operational costs.
- Enhanced Safety: Using reliable bearings minimizes the risk of mechanical failures that can lead to accidents.