Exploring the Impact of Machine Tools Software on Manufacturing

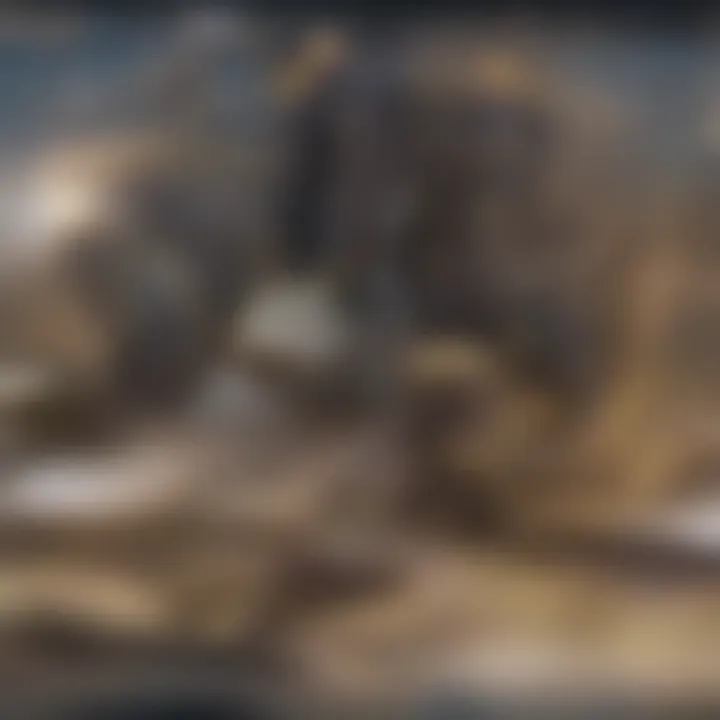
Intro
Machine tools software represents a critical component in the landscape of modern manufacturing and engineering. As the industry evolves, the capabilities and relevance of such software grow increasingly significant. Understanding this relationship between technology and manufacturing can provide insight into operational efficiencies and productivity improvements.
Increasingly complex machining processes require robust software solutions to enhance the functionality of machine tools. This article aims to offer an in-depth examination of machine tools software, focusing on its various applications, significance, and future trajectory.
Key Concepts
Definition of Primary Terms
Before diving further into specific applications and trends, it's essential to clarify some key terms:
- Machine Tools: These are machines used to shape or machine metal or other rigid materials. Examples include lathes, milling machines, and grinders.
- Software Applications: In the context of machine tools, software applications refer to programs that aid in the control, monitoring, and optimization of machinery. They can range from Computer-Aided Design (CAD) software to Computer Numerical Control (CNC) systems.
- Efficiency: This term describes how effectively resources are utilized to achieve a desired output. In manufacturing, higher efficiency often equates to reduced cost and waste.
Related Concepts and Theories
Machine tools software overlaps with several related concepts:
- Automation: This pertains to the technology that performs tasks with minimal human intervention. Automation improves consistency and speeds up production processes.
- Integration: The ability to seamlessly connect various software and machinery types is a growing area of focus. Integration facilitates better data exchange and enhances decision-making capabilities.
- Industry 4.0: This term encapsulates the surge in digital transformation in manufacturing, emphasizing smart manufacturing and the Internet of Things (IoT). Machine tools software plays a foundational role in this evolution.
"Incorporating advanced machine tools software is not just a trend; it is necessary for sustaining competitiveness in manufacturing."
Challenges in Integration
While the potential of machine tools software is immense, various challenges hinder its optimal integration into existing processes. Common issues include:
- Compatibility: New software may face difficulty working with legacy systems, causing disruptions.
- Skills Gap: As technology advances, workers may lack the necessary training to use new software efficiently.
- Cost: Initial expenditure on software solutions can be significant, deterring some companies from making the investment.
Future Directions
Gaps Identified in Current Research
Despite a wealth of knowledge surrounding machine tools software, certain areas remain under-researched. One such gap lies in the long-term effects of software integration on workforce dynamics. There is also limited understanding of how emerging technologies can synergize with existing tools for higher efficiency.
Suggestions for Further Studies
Future research should consider the following directions:
- Impact of AI: Investigating the role of artificial intelligence in optimizing machine tools can open new avenues for innovation.
- User Experience: Understanding how users interact with software can help developers create more intuitive solutions.
- Sustainability: Exploring environmentally sustainable practices in machine tool operations could yield beneficial insights for both industry and ecology.
With a rapidly evolving landscape, the significance of machine tools software continues to grow. Understanding its intricacies not only enhances operational efficiency but also aligns manufacturing practices with future technological advancements.
Intro to Machine Tools Software
Machine tools software serves as a cornerstone in the modern manufacturing landscape. Its integration into production processes enhances efficiency, precision, and overall productivity. In this age of rapid technological advancement, understanding machine tools software becomes vital not only for manufacturers but for researchers and educators aiming to grasp current trends and practices in the industry.
Definition and Overview
Machine tools software refers to a collection of applications that assist in the operation, design, and manufacture of machinery. These software solutions facilitate various functions, such as designing components, controlling machinery, and managing workflows. The scope of machine tools software can range from simple programs for basic design tasks to sophisticated systems that enable complex simulations and real-time data analytics.
Historically, machine tools have relied on manual processes, which were often slow and prone to human error. The advent of software has transformed this scenario significantly. Now, manufacturers can use tools like Computer-Aided Design (CAD) to create detailed models and Computer Numerical Control (CNC) systems to automate machining operations. This shift has not only streamlined operations but also opened new avenues for innovation in manufacturing.
Importance in Modern Manufacturing
The importance of machine tools software within contemporary manufacturing cannot be overstated. Here are several key benefits that highlight its relevance:
- Increased Efficiency: Automated operations reduce time spent on manual tasks, allowing for faster production cycles.
- Improved Precision: Software-driven machinery can achieve higher levels of accuracy compared to manual techniques, leading to reduced waste and better quality products.
- Data Integration: Many software solutions allow for seamless integration with other systems like Enterprise Resource Planning (ERP) and supply chain management tools, fostering a more cohesive operational environment.
- Flexibility: As market demands shift, machine tools software enables manufacturers to adapt their processes rapidly, implementing changes without significant downtime.
The impact of machine tools software extends beyond just efficiency and accuracy. It plays a crucial role in ensuring compliance with regulatory standards and offers insights for continuous improvement. In a world where competition is fierce and customer expectations are ever-increasing, leveraging such technologies becomes not just advantageous but necessary for survival in the manufacturing sector.
Types of Machine Tools Software
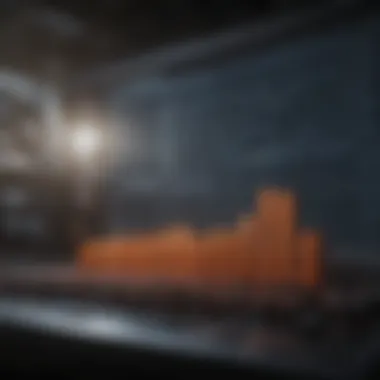
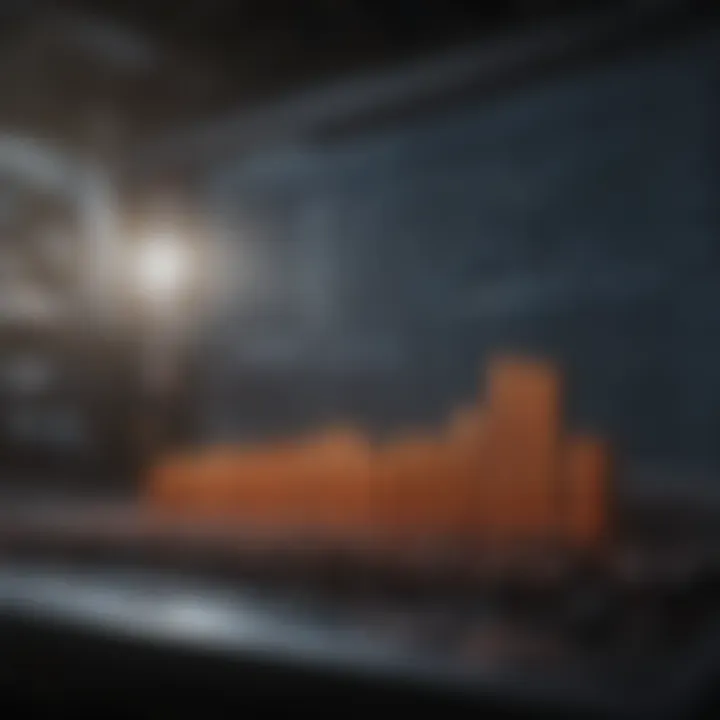
Machine tools software plays a vital role in the modern manufacturing landscape. It assists in enhancing efficiency, improving precision, and streamlining operations. Understanding the types of machine tools software is crucial for manufacturers looking to optimize their processes. This section delves into specific categories, outlining their functionalities, advantages, and contexts in which they are applied. These software types are instruments that can transform traditional manufacturing into more responsive and agile operations.
Computer-Aided Design (CAD)
Computer-Aided Design software is essential for designers and engineers. CAD allows users to create precise drawings and models of parts and assemblies. One of the main benefits of CAD is its ability to enhance visualization. Users can generate 2D drawings and 3D models, which facilitate a better understanding of the design before production begins.
CAD software also promotes collaboration among teams. Multiple users can work on the same project simultaneously, enabling feedback and iterative design processes. Common CAD programs, such as AutoCAD and SolidWorks, feature libraries of standardized components, which saves time and reduces design errors. The integration of CAD with CAM systems further allows seamless transition from design to manufacturing.
Computer-Aided Manufacturing (CAM)
Computer-Aided Manufacturing refers to the use of software to plan, manage, and control manufacturing processes. CAM is highly beneficial because it helps in directly converting CAD designs into actual products. This capability ensures higher productivity by minimizing manual input and reducing the likelihood of errors.
One notable aspect of CAM software is its ability to optimize machining processes. By simulating operations, manufacturers can identify inefficiencies and adjust parameters accordingly. Software solutions like Mastercam and Fusion 360 facilitate this optimization by providing tools for tool path generation, rendering, and validation. Overall, CAM enhances productivity, reduces costs, and delivers more consistent quality in manufactured parts.
Computer Numerical Control (CNC)
Computer Numerical Control software is crucial for operating CNC machines, which automate tools for cutting, shaping, and milling materials. CNC technology significantly improves production accuracy and repetition. It translates digital designs and commands into physical actions executed by machine tools.
CNC software enables real-time monitoring and control of production processes. Users can adjust settings on-the-fly, allowing for flexibility in manufacturing. Popular CNC software includes Mac and LinuxCNC. They provide functionalities such as programmability, tool management, and error reporting, which are vital for maintaining operational efficiency. With CNC, manufacturers can realize complex geometries and achieve high precision, which is often challenging with manual processes.
Enterprise Resource Planning (ERP)
Enterprise Resource Planning software integrates various functions within manufacturing companies into one unified system. ERP covers key operational areas such as inventory management, order processing, and supply chain logistics. The main benefit of ERP is its comprehensive approach to managing resources. It allows for better data visibility and coordinated decision-making.
Implementations like SAP and Oracle ERP enable manufacturers to align production schedules with customer demands. This alignment helps in minimizing excess inventory and reducing lead times. Furthermore, ERP systems often encompass advanced analytics, providing insights into performance metrics and trends. In doing so, manufacturers can enhance strategic planning and execution across the organization.
Functionalities of Machine Tools Software
Machine tools software serves as a fundamental component in the landscape of modern manufacturing. Its functionalities determine how companies design, produce, and manage products. Understanding these functionalities plays a pivotal role for students, researchers, and professionals interested in the interface between technology and manufacturing processes.
Design Simulation and Testing
The capability of design simulation and testing in machine tools software cannot be overstated. This functionality allows designers and engineers to create virtual representations of products before they enter production. By simulating manufacturing processes, teams can experiment with different material properties and design variations without incurring significant costs. The software aids in identifying potential flaws early in the development cycle. This minimizes the risk of expensive errors and rework later in the production phase.
Moreover, tools such as Autodesk Fusion 360 or Siemens NX offer advanced simulation features. These features include finite element analysis (FEA) and computational fluid dynamics (CFD). These analyses provide insights into how designs will behave under stress or when exposed to various environmental conditions. Successful simulation leads to improved product quality and a better understanding of material behaviors.
Production Scheduling and Optimization
Production scheduling and optimization form another crucial functionality of machine tools software. Effective scheduling enhances operational efficiency, reduces lead times, and maximizes resource utilization. Manufacturing operations involve numerous variables, from labor availability to machine uptime. Software applications like Epicor or Plex can automate scheduling tasks. Moreover, these tools can predict production bottlenecks and suggest optimal workflows.
Optimization algorithms help manufacturers make informed decisions regarding machine allocations and sequences of operations. By analyzing various data points, these solutions enable manufacturers to allocate resources effectively, resulting in cost savings. Additionally, leaning to adaptive production schedules helps industries respond swiftly to changes in demand.
Quality Control and Assurance
Quality control and assurance processes are critical in ensuring that manufactured products meet required standards. Machine tools software offers functionalities to maintain high-quality levels throughout the production lifecycle. Tools like Minitab or QI Macros assist in monitoring product quality through statistical process control (SPC).
These solutions can identify trends and outliers in production data, helping teams address issues before they escalate. This proactive approach to quality management fosters a culture of continuous improvement. Furthermore, integrating quality assurance functionalities within the software streamlines operations, reducing the need for separate quality management systems.
In summary, the functionalities encompassed within machine tools software significantly influence manufacturing efficiency. Each aspect, from design simulation to quality assurance, is a cornerstone that enhances productivity and innovation in manufacturing processes.
Impact of Machine Tools Software on Manufacturing Efficiency
The integration of machine tools software in manufacturing processes has significantly transformed the industry. It has enabled manufacturers to enhance efficiency through various means. Understanding the impact of machine tools software on efficiency is vital for businesses striving for competitiveness in a rapidly changing market.
Reduction of Lead Times
Reducing lead times has become a paramount focus for manufacturers aiming to meet customer demands quickly. Machine tools software plays an essential role in this regard. For instance, using Computer Numerical Control (CNC) systems allows for quicker setup times and adjustments. This software automates many processes traditionally done manually.
By automating design modifications and production scheduling, companies can accelerate production cycles. This leads to faster delivery of products to clients. Moreover, simulation tools integrated into these systems can predict any potential production roadblocks. As a result, manufacturers can address issues proactively rather than reactively.
Enhanced Precision and Accuracy
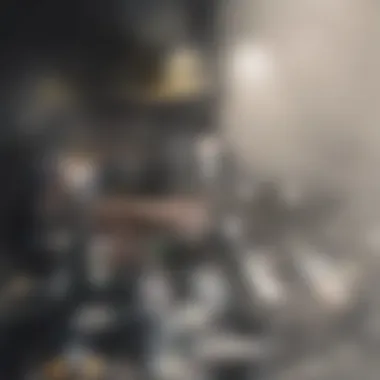
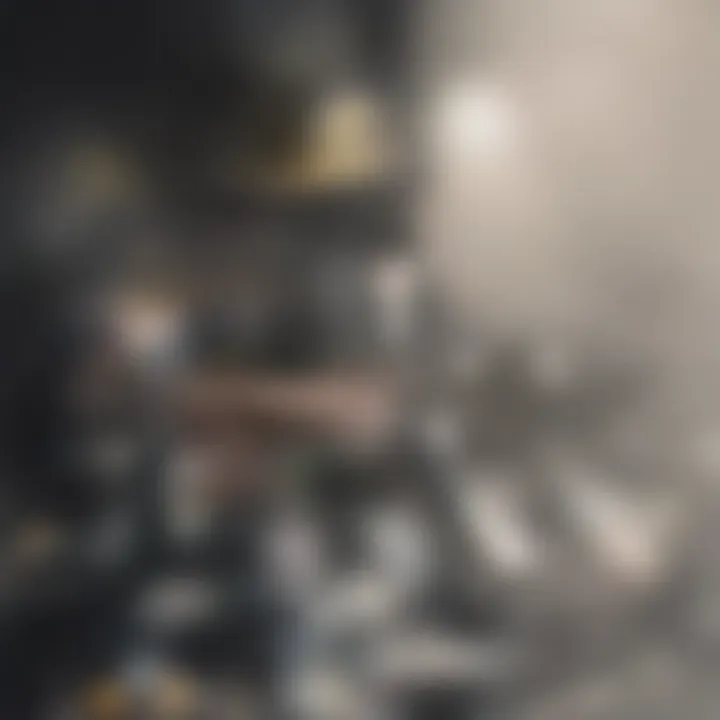
Precision and accuracy are crucial in manufacturing. Machine tools software provides advanced features that significantly improve these aspects. For example, CAD software helps in creating detailed models, ensuring that specifications meet exact requirements. With the use of digital simulations, the likelihood of errors during production can be minimized.
CNC machining further enhances this precision through its ability to follow complex designs with high accuracy. This leads to products that meet stringent quality standards. The consistent quality not only reduces wastage but also increases customer satisfaction, which is essential for long-term success.
Streamlined Workflows
Efficient workflows are vital for maximizing productivity. Machine tools software streamlines workflows by integrating various stages of production. For instance, ERP software can connect different departments, facilitating better communication between design, production, and logistics.
Additionally, proper scheduling and resource management ensure that machines are not idle. This enhances overall equipment effectiveness (OEE).
"Software integration can transform isolated tasks into cohesive processes, vastly improving operational efficiency."
Ultimately, the effective use of machine tools software translates to optimized resources and reduced downtime. This becomes essential for manufacturers focused on continuous improvement and operational excellence.
Trends in Machine Tools Software Development
The development of machine tools software is notably changing. These changes are not just minor updates or variations; they represent a significant evolution in how industries will function in the future. Understanding these trends is vital not only for manufacturers but for anyone engaged in the field of technology and engineering. New advancements help meet the growing demands for efficiency, precision and flexibility in manufacturing processes.
Integration with Artificial Intelligence
Integrating artificial intelligence (AI) into machine tools software is becoming more prevalent. AI enables automation of complex processes, enhancing the ability to predict maintenance needs for equipment. This minimizes unexpected downtime that can be financially burdensome for businesses. Additionally, AI assists in optimizing production schedules and even adjusts parameters in real-time based on operational data. For example, a CNC machine can use AI algorithms to analyze cuts and optimize for better accuracy and speed without human intervention.
Benefits of AI integration include:
- Improved operational efficiency
- Reduced labor costs
- Enhanced decision making through data analysis
Cloud-Based Solutions
Cloud-based solutions are rapidly transforming how software is deployed in manufacturing. Instead of relying on local servers, industries can access software through the internet. This offers a range of benefits including scalability and cost-effectiveness. Companies no longer need to invest heavily in infrastructure; they can simply subscribe to services as per need.
"Cloud computing offers unparalleled flexibility for machine tools software, allowing manufacturers to scale operations without heavy capital investment."
Intelligent data storage and processing are now possible, which means manufacturers can gather extensive data sets and analyze them efficiently. This development supports better decision-making and enhances innovation.
Mobile Applications in Manufacturing
The rise of mobile applications specifically for manufacturing is noteworthy. With a mobile application, operators are able to monitor and control machine tools from their smartphones or tablets. This flexibility increases productivity and allows technicians to address issues on the go.
Mobile apps also facilitate real-time communication between teams. As a result, this responsiveness can lead to quicker problem resolution and a more agile manufacturing environment.
Challenges in Implementing Machine Tools Software
Implementing machine tools software presents multiple challenges that industries must navigate to achieve optimal results. Understanding these challenges is essential for businesses looking to invest in technology that enhances manufacturing processes. These challenges not only affect the transition to upgraded systems but also influence the long-term satisfaction with software solutions.
Compatibility Issues
Compatibility is a critical consideration when adopting new machine tools software. This issue arises from variations in existing legacy systems alongside contemporary software needs. Companies often operate with a mix of older machines and newer technologies, which can hinder the seamless integration of new solutions like CAD or CAM systems.
When software solutions do not align with hardware specifications, companies may experience significant downtime. This disruption can affect production schedules and lead to financial losses. Therefore, a thorough assessment of compatibility is necessary before implementation to ensure that the new software can function alongside current systems. In some cases, modifications may be needed, which could involve additional costs and time investments.
Cost Implications
Financial considerations are another significant challenge. The investment required to implement advanced machine tools software can be substantial. Costs may include not only the software purchase but also hardware upgrades, licensing fees, and ongoing maintenance. For small and medium enterprises, these expenses can take a considerable toll on budgets.
Moreover, the return on investment (ROI) is not always immediate. Many companies may find themselves in a situation where the benefits of efficiency and productivity improvements take time to materialize. This uncertainty can put organizations in a difficult position, especially when under pressure to demonstrate immediate results. Careful financial planning and cost analysis are critical to ensure that the investment is sustainable.
Training and Skill Development
The need for training is often underestimated during the implementation of machine tools software. Employees must acquire new skills to operate modern software effectively. This requirement can lead to resistance, as seasoned workers may be reluctant to adapt to new systems. Furthermore, specialized training programs can be costly and time-consuming, creating additional hurdles.
To mitigate these challenges, companies should invest in comprehensive training programs tailored to different skill levels. Such initiatives not only facilitate smoother transitions but also help in maintaining employee morale. An equipped workforce ensures that the full potential of new software can be realized. As technology continues to evolve, continuous education must be a pillar of any successful machine tools software implementation strategy.
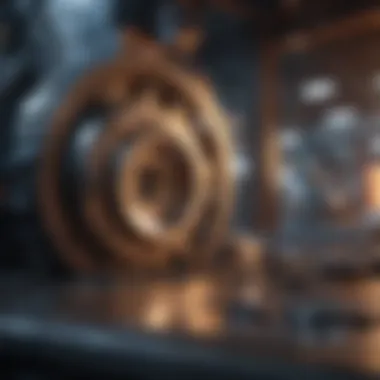
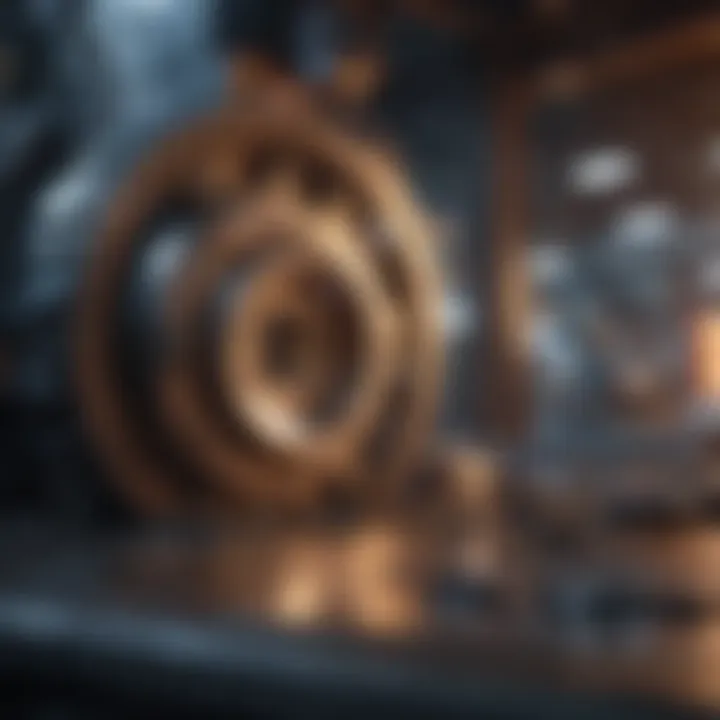
Case Studies of Successful Software Integration
Analyzing real-world applications of machine tools software provides valuable insight into its efficacy and relevance within various industries. Case studies illustrate how specific software solutions have been successfully integrated, the challenges faced during implementation, and the resulting benefits. Such examples not only highlight the power of leveraging advanced technology but also offer guidance for future applications in manufacturing and engineering.
Automotive Industry Examples
The automotive industry serves as a prime example of successful software integration, underscoring the necessity of precision and efficiency. Companies like Ford and General Motors have adopted a range of machine tools software to streamline production processes. By integrating Computer-Aided Design (CAD) and Computer Numerical Control (CNC) systems, manufacturers enhance design accuracy, reduce errors, and optimize machine performance.
For instance, Ford implemented Siemens' Solid Edge software to accelerate its design process. With this integration, they achieved a reduction in lead times, allowing for quicker vehicle prototyping. This change also enabled higher customization levels, meeting the diverse needs of consumers. Additionally, the use of CNC machines controlled by the latest software has improved consistency in manufacturing, leading to better overall quality.
In terms of benefits, automotive manufacturers experience:
- Increased design flexibility
- Lower material wastage
- Enhanced productivity
These elements collectively demonstrate the significance of software integration within the automotive sector.
Aerospace Manufacturing Applications
Meanwhile, the aerospace industry presents distinct challenges and requirements, making successful software integration critical to safety and performance. Companies such as Boeing and Airbus rely heavily on specialized machine tools software to maintain quality and adhere to strict regulations.
Boeing, for instance, utilizes CATIA software for advanced aerodynamic modeling. The integration of this tool with CNC machining helps ensure that all components meet FAA standards. Boeing's approach to combining software applications has significantly reduced production errors and improved efficiency.
The following advantages are noted in aerospace manufacturing applications:
- Streamlined compliance with safety regulations
- Improved aspect ratios in component production
- Enhanced collaboration across departments, simplifying communication
In summary, case studies from the automotive and aerospace industries not only demonstrate the successful integration of machine tools software but also shed light on the broader implications for improving manufacturing processes. By examining these examples, industries can draw lessons and strategies to optimize their operations moving forward.
"Successful software integration in manufacturing is not just about technology; it's about enhancing the human aspect of operations too."
Through careful study of these industries, other sectors may discover innovative ways to implement similar technologies and improve their own efficiency.
Future Outlook for Machine Tools Software
The future outlook for machine tools software is significant, impacting the manufacturing sector deeply. As technology evolves, so does the complexity and capability of software solutions. Understanding these trends and their implications become crucial for businesses looking to stay relevant in a competitive environment.
Predicted Technological Advances
Technological advances in machine tools software are poised to reshape the landscape of manufacturing. Predictive analytics, machine learning, and enhanced data integration are elements gaining traction. These innovations offer solutions to common operational challenges. For instance, predictive maintenance can anticipate equipment failures before they occur. This minimizes downtime and optimizes production processes.
Moreover, the integration of IoT technology can provide real-time data on machine performance. Such data allows manufacturers to make informed decisions instantly. With advancements like augmented reality, training personnel could become more efficient. Workers could receive virtual guidance directly on their tasks, reducing training time significantly.
"The merging of advanced algorithms and real-time data capabilities is driving a transformation in how we approach manufacturing."
Another notable trend is the growing importance of cybersecurity in machine tools software. As systems become more interconnected, protecting sensitive information becomes critical. Manufacturers will need to invest in robust security frameworks to safeguard intellectual property and operational data.
Implications for Workforce and Industry Structure
The advancements in machine tools software will inevitably affect the workforce and industry structure. As automation rises, the demand for skilled workers will shift. Traditional roles may decrease, while the need for data analysts, software developers, and automation specialists will increase. This evolution will require ongoing education and training programs.
The industry structure may also become more decentralized. With cloud-based solutions, smaller manufacturers can access cutting-edge technologies previously available only to larger firms. This democratization of technology allows for a more competitive market, where innovation drives success regardless of company size.
The End
The conclusion serves as a pivotal element of this article, summarizing the extensive insights gathered regarding machine tools software. This section emphasizes the profound impact that this software has on modern manufacturing processes. Its importance cannot be overstated, given how it enhances operational efficiency, improves precision, and fosters innovation across industries.
Summary of Key Points
Throughout the article, we have explored various facets of machine tools software. Key points include:
- Definition and Importance: Machine tools software is fundamental in modern manufacturing, facilitating design, production, and resource management.
- Types of Software: Software applications such as Computer-Aided Design (CAD), Computer-Aided Manufacturing (CAM), and CNC play distinct yet complementary roles in creating and managing manufacturing processes.
- Functionalities: Essential functionalities like design simulation, production scheduling, and quality control are indispensable for optimizing manufacturing workflows.
- Impact on Efficiency: We discussed how these tools reduce lead times, enhance precision, and streamline workflows, which ultimately leads to better productivity.
- Trends and Challenges: The integration of artificial intelligence, cloud solutions, and mobility in software development comes with challenges related to compatibility, cost, and the need for skilled personnel.
- Future Outlook: As technology continues to evolve, predictions regarding advancements in machine tools software point toward significant implications for workforce dynamics and industry structure.
Final Thoughts on Machine Tools Software
The future of machine tools software is promising, yet demands careful consideration. As industries continue to embrace advanced technologies, the successful integration of software solutions becomes crucial. It is essential to remain informed about the latest trends and adapt to emerging challenges.
"The advancements in machine tools software will directly influence the evolution of manufacturing techniques and systems, paving the way for smarter and more efficient industrial practices."