Exploring Information Technology's Impact on Manufacturing
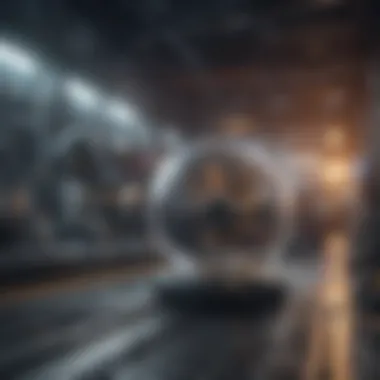
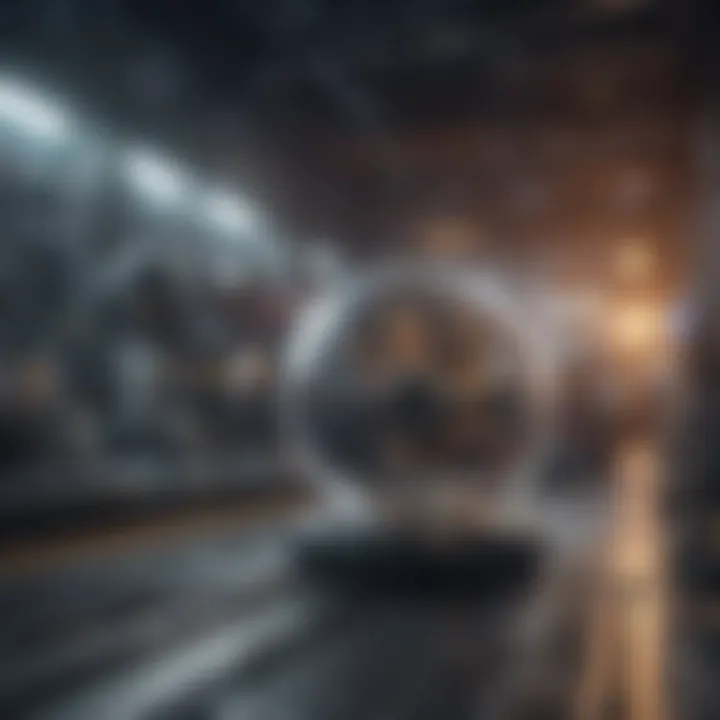
Intro
In today's fast-paced industrial environment, the role of information technology in manufacturing cannot be overstated. With an increasing reliance on digital tools, the landscape in which manufacturers operate is reshaping at an unprecedented rate. From big data analytics to the Internet of Things (IoT) and artificial intelligence (AI), technology is not just an auxiliary facet of operations; it has become a driving force behind efficiency, productivity, and profitability.
The integration of these technologies isn't merely a fad; it's a response to the growing demands of global markets, which expect faster production times, greater customization, and enhanced quality assurance. As traditional manufacturing methods evolve, the relevance of information technology continues to escalate.
Key Concepts
Definition of Primary Terms
To grasp the implications of information technology in manufacturing, it's important to define key terms that are often used interchangeably but have distinct meanings:
- Information Technology (IT): Encompasses all technologies used to create, store, exchange, and utilize data. In manufacturing, this includes hardware, software, networks, and databases that facilitate communication and processing.
- IoT (Internet of Things): Refers to interconnected devices that communicate with each other, collecting and sharing data from the manufacturing floor to improve processes and decision-making.
- Artificial Intelligence (AI): In manufacturing, AI refers to systems that analyze data and execute tasks typically requiring human intelligence. This includes predictive maintenance and quality control automation.
- Big Data: Encompasses large volumes of structured and unstructured data that can be analyzed to reveal patterns, trends, and associations in relation to human behavior.
Related Concepts and Theories
Several theories underpin the application of information technology in manufacturing. Some of these include:
- Industry 4.0: This concept refers to the fourth industrial revolution, characterized by a fusion of advanced manufacturing techniques with cutting-edge technologies such as cyber-physical systems, IoT, and smart factories.
- Lean Manufacturing: This philosophy emphasizes efficiency by reducing waste, and it can benefit from digitization that provides real-time data and analytics to track performance.
Understanding these concepts creates a foundation for delving deeper into how these technologies are applied and their overall impact on modern manufacturing practices.
Current Landscape of Information Technology in Manufacturing
The Benefits of IT Integration
The integration of information technology can yield significant advantages for manufacturing operations. Some noted benefits include:
- Increased Efficiency: Enhanced automation and streamlined processes lead to faster production cycles.
- Data-Driven Decision Making: Access to real-time analytics allows manufacturers to make informed decisions quickly, minimizing downtime.
- Cost Reduction: By automating tasks and processes, companies can reduce labor costs and waste.
Nevertheless, it's crucial to consider the challenges that accompany these advancements. Issues such as cybersecurity risks and the need for ongoing technology training should not be overlooked.
The Future Directions
Gaps Identified in Current Research
While there's a wealth of information on the benefits of information technology in manufacturing, several gaps remain in understanding its long-term implications, especially in terms of sustainability and workforce impact.
Suggestions for Further Studies
Future research could delve into:
- The ethical implications of AI in manufacturing jobs and worker displacement.
- The long-term sustainability impacts of heavily relying on technology in production processes.
- How emerging technologies will shape collaboration in manufacturing sectors.
Foreword to Information Technology in Manufacturing
In an era where practically every aspect of our lives is influenced by technology, the manufacturing sector stands as a prominent example of transformative change driven by information technology. This particular intersection is not merely about automation or enhanced efficiencies; it showcases a profound shift in how manufacturing operations are conducted, monitored, and optimized. The integration of information technology into manufacturing processes has reshaped traditional methods and expanded the horizon of possibilities.
Definition and Scope
When discussing information technology in manufacturing, it is crucial to grasp what this entails. Essentially, it encompasses the entirety of technologies used to manage and process information in manufacturing settings. From sophisticated software that governs production scheduling to cutting-edge hardware, like smart sensors, that gather operational data, the scope of information technology in this field is vast.
Moreover, it's not just about the technology itself but also about the systems and processes that support the flow of information. Data management, communication, and control systems are integral to optimizing production lines, maintaining product quality, and responding swiftly to market changes.
Evolution of Information Technology in Manufacturing
To appreciate the present landscape, one must look back at the evolution of information technology in manufacturing. Early manufacturing relied heavily on manual processes and basic mechanization. However, the introduction of computers in the late 20th century marked a turning point. This technological leap enabled manufacturers to adopt computerized control systems. The rise of enterprise resource planning (ERP) systems further revolutionized the industry by facilitating the integration of disparate processes into a cohesive framework. Today, we observe the adoption of cloud computing and artificial intelligence, which push the boundaries even further, enabling predictive capabilities and real-time decision-making that were unfathomable a few decades ago.
Importance of Integration
Integrating information technology into manufacturing is not just beneficial—it is essential. The interconnectedness of devices and systems allows for a seamless flow of information from the factory floor to decision-makers. This integration fosters improved communication and collaboration between different departments, enhancing operational efficiency.
- Increased Transparency: When systems are interconnected, stakeholders can easily access real-time data, which provides transparency in operations.
- Enhanced Responsiveness: With immediate access to vital information, businesses can respond to issues promptly, preventing small problems from escalating.
- Data-Driven Decisions: Integration enables companies to leverage big data insights, thereby making informed decisions that drive continuous improvement.
Key Technologies Shaping Manufacturing
In the current manufacturing landscape, technology plays a pivotal role in redefining processes and improving efficiency. With a vast array of tools available—from artificial intelligence to cloud computing—each technology brings its own set of advantages and transformative potential.
When discussing key technologies in manufacturing, it’s crucial to understand not only the innovations themselves but also how they integrate within the larger ecosystem of production. This interconnectedness often leads to gains in productivity, cost savings, and enhanced quality. These benefits are not merely theoretical; they are observed through real-world applications that have redefined how industries operate.
Artificial Intelligence in Manufacturing
Artificial Intelligence (AI) is setting the stage for significant improvements in the manufacturing sector, driving organizations toward smarter, more efficient processes.
Machine Learning Applications
Machine Learning (ML) is a subset of AI that enables systems to learn from data and improve over time without human intervention. In manufacturing, ML applications can predict equipment failures before they occur, significantly reducing downtime. The ability to analyze vast datasets makes ML an invaluable tool for manufacturers. A unique feature of these applications is their adaptability, allowing them to refine algorithms based on real-time data, which leads to optimizing production lines continuously.
However, not all is rosy; a challenge with ML is the need for high-quality data. Inconsistencies can lead to erroneous predictions, hence organizations must invest in robust data management strategies.
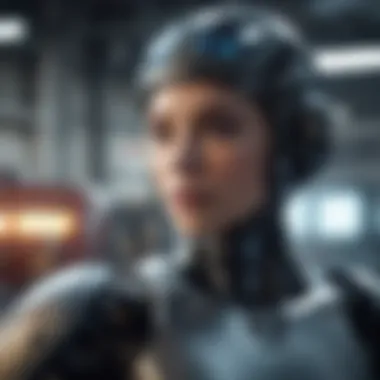
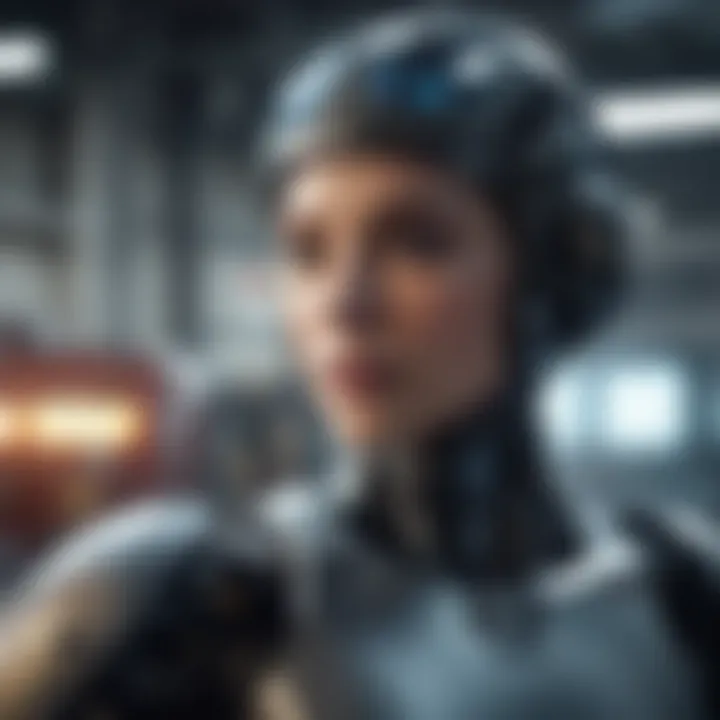
Predictive Maintenance
Predictive Maintenance (PM) employs AI algorithms to analyze machine data and forecast potential malfunctions. The beauty of PM lies in its preventive approach, which helps manufacturers act before issues become critical. This method proves to be a popular choice as it saves both time and resources.
One unique aspect of PM is its reliance on historical data alongside real-time analytics to develop a comprehensive maintenance schedule. The upside is reduced downtime, while the drawback includes the initial costs of implementing such systems.
Quality Control Automation
Quality Control Automation leverages technology to monitor and manage the quality of products throughout the manufacturing process. This technology not only reduces human error but also ensures consistent standards. In this regard, one notable characteristic is its ability to integrate vision systems that can quickly assess defects in production.
The major advantage here is the acceleration of quality checks; however, it requires upfront investment and skilled personnel to manage the technology effectively.
Internet of Things and Connectivity
The Internet of Things (IoT) is another cornerstone in modern manufacturing. It connects devices, sensors, and machinery to facilitate real-time data sharing, which is invaluable in optimizing operations.
Smart Sensors
Smart Sensors collect data from equipment and feed it back to centralized systems. The primary contribution of these sensors is the ability to monitor machinery across various parameters, such as temperature and operating speed. Their deployment leads to informed decision-making, making them a hot commodity in manufacturing.
Their unique feature is the ability to communicate data seamlessly through wireless networks. On the flip side, concerns about data overload and the need for adequate processing power can hinder their effectiveness.
Connected Machinery
Connected Machinery refers to equipment equipped with IoT technology that communicates data between machines and systems. This interconnectedness is essential for creating a cohesive manufacturing environment. A key advantage is the improvement in operational efficiency as machines learn from one another to optimize processes.
The disadvantage lies in the complexities involved in integrating various machines that might utilize different communication protocols, potentially leading to compatibility issues.
Real-Time Data Analytics
Real-time Data Analytics provides insights as events unfold, allowing manufacturers to react quickly to any changes or issues in production lines. The core benefit it offers is enhanced responsiveness, leading to improved operational decision-making and crisis management.
One exceptional feature of this technology is its forecasting ability, which can predict possible future trends based on current data, helping in strategic planning. However, in implementing real-time analytics, there often lies the challenge of managing and interpreting large streams of data effectively.
Big Data and Analytics
Big Data is a defining trend in manufacturing processors, as organizations harness large sets of data to glean meaningful insights.
Data Collection Techniques
Data Collection Techniques are essential in gathering information from various stages within the manufacturing process. These techniques range from automated sensors to manual entry systems. One of their critical characteristics is the ability to capture diverse datasets, which can be analyzed for various purposes.
The unique feature of these techniques is their flexibility, allowing different methodologies based on specific needs. However, managing and storing such diverse data may present challenges, particularly regarding security and accessibility.
Data-Driven Decision Making
This approach emphasizes making decisions based on data insights rather than intuition or guesswork. It signifies a shift towards more analytical thinking within organizations. The advantage here is the ability to back decisions with hard evidence, leading to enhanced performance outcomes.
Yet, one must tread carefully, as an over-reliance on data could overshadow human intuition and experience, which also hold significant value.
Case Studies in Manufacturing
Examining real-world examples of how data analytics has impacted manufacturing can illuminate its practical applications. Such case studies often showcase how specific companies improved efficiencies or quality by incorporating analytics, which serves as a guideline for others looking to adopt similar technologies. However, challenges around replication and scalability can also arise from these unique cases.
Cloud Computing and Manufacturing
Cloud Computing has transformed how manufacturing companies manage their resources and applications.
Platform as a Service (PaaS)
PaaS provides a foundation for developers to build applications without worrying about the underlying infrastructure. This service is gaining traction in manufacturing as it allows for rapid development and deployment of applications at a lower cost. The characteristic of reduced complexity in development processes is a key attraction.
Unique to PaaS is its scalability; as demand increases, manufacturers can expand their resources without heavy investments in physical infrastructure. Nevertheless, ongoing concerns about data security and compliance persist.
Software as a Service (SaaS)
SaaS is becoming increasingly popular among manufacturers for offering applications over the internet. This model minimizes the need for local installations and maintenance, simplifying the IT landscape for many organizations. A significant edge of SaaS is its cost-effectiveness, especially for small to medium enterprises.
However, relying solely on SaaS could lead to challenges, including data privacy issues and lack of control over the software used.
Scalability and Cost-Efficiency
These aspects are crucial for the continued growth of manufacturing businesses. Scalability ensures that as a company's operations expand, technology resources can grow alongside, thus maintaining performance while keeping costs manageable. The main advantage of being scalable is adaptability.
On the downside, there can be added costs associated with scaling operations, particularly if systems are not designed with flexibility in mind.
By carefully examining the key technologies shaping modern manufacturing, organizations can better position themselves to harness the potential of digital transformation, navigate challenges, and drive future growth.
Benefits of Information Technology in Manufacturing
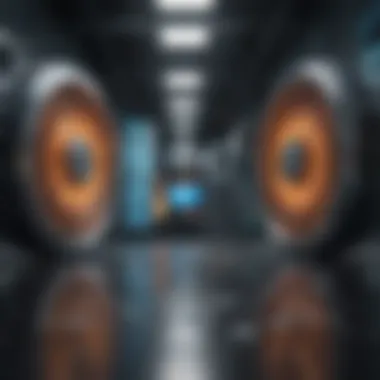
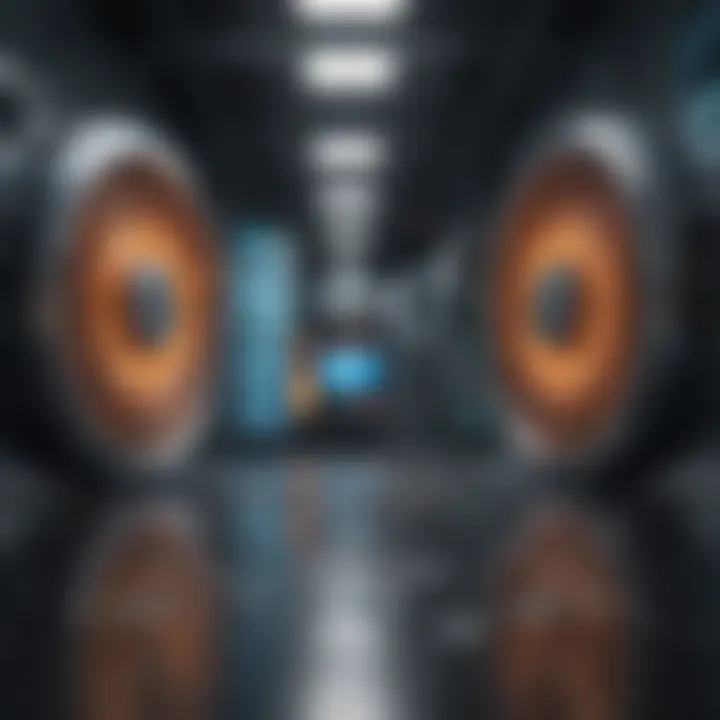
Introducing Information Technology in manufacturing is akin to flipping a switch on efficiency, innovation, and productivity. Inside factories and manufacturing plants, technology weaves itself into every process, transforming traditional approaches into finely-tuned systems that operate with remarkable precision. Here, we explore the specific benefits that come when information technology is embedded into the manufacturing framework, enriching both the workflow and the bottom line.
Enhanced Operational Efficiency
At the heart of modern manufacturing lies operational efficiency, a principle that means getting the job done right while using the least amount of resources. With information technology, manufacturers can streamline processes in ways that were previously unimaginable.
For example, utilizing real-time data analytics enables teams to identify bottlenecks in a production line almost instantly. By examining the flow of materials and information, companies can adjust processes on-the-fly. This flexibility allows for a smoother operation with minimal downtime.
Moreover, automation tools help in scaling production without the complications of human errors. Sensors and smart devices connected through the Internet of Things (IoT) give manufacturers insights unavailable in the past.
- Key Aspects of Enhanced Operational Efficiency:
- Real-time monitoring of production processes
- Decreased lead times in product delivery
- Higher throughput without sacrificing quality
Improved Quality Control
Quality control is no longer just about inspecting the end product; it starts from the supply chain to production and finally to distribution. Information technology plays a critical role in maintaining and improving quality standards. Automated systems continuously monitor processes. They can detect deviations from predefined standards immediately—a task that would be tedious and time-consuming if done manually.
Additionally, employing machine learning algorithms helps predictive maintenance. Predictive maintenance schedules maintenance activities before a machine breaks down, reducing unexpected downtime. When problems arise, they are addressed preemptively instead of reactively. This shift not only protects the quality of the output but also prolongs the lifespan of the equipment involved.
- Elements of Improved Quality Control:
- Continuous feedback loops between production and quality assurance
- Data-driven decisions for better accuracy
- Reduction in waste from faulty products
Cost Reduction Strategies
When you delve into the soups and nuts of manufacturing, one can't help but notice the impact of information technology on cost reduction. Advanced technologies make it feasible to minimize expenses in several ways. First off, automating repetitive tasks cuts labor costs. Manufacturers can reallocate workers to areas of higher skill demand, adding value to the organization.
Additionally, by employing big data analytics, manufacturers can predict market trends more accurately. This predictive ability helps companies avoid overstocking or stockouts, optimizing supply chain management and conserving cash flow.
Let’s also not overlook simply keeping energy costs low. Systems that monitor energy consumption can detect and rectify inefficiencies, contributing to significant savings over time.
- Cost Reduction Strategies Include:
- Streamlined supply chain processes
- Minimized wastage through smart inventory metrics
- Energy-efficient production methods
"The integration of information technology is not merely a trend but a necessity for manufacturers striving for competitiveness in today's market."
As we can see, the benefits of integrating information technology into manufacturing are multifaceted. From enhancing operational efficiency to improving quality control and implementing savvy cost-reduction strategies, the role of technology is indispensable. Not only does it lead to immediate gains, but it also sets the stage for sustainable growth and excellence in the long run.
Challenges Associated with Information Technology
In the modern landscape of manufacturing, information technology plays a pivotal role in shaping how organizations operate. However, as integration becomes more prevalent, several challenges surface that can hinder progress. Addressing these obstacles is essential not just for immediate success but for the long-term sustainability of manufacturing enterprises. When considering challenges associated with information technology, organizations must take a closer look at the specific elements that can affect their operations and performance.
Implementation Obstacles
The dream of a fully integrated manufacturing system can quickly turn into a nightmare if implementation hurdles aren't carefully navigated. One fundamental issue is the sheer complexity of modern IT systems. Manufacturers often grapple with integrating new technologies alongside legacy systems, creating a tangled web of compatibility concerns. This integration isn't as cut and dried as one might think; it involves not just chores of technology but also human factors.
Moreover, companies frequently face resistance from employees who are comfortable with existing practices. Training staff to adapt to new software can be a heavy lift. If the workforce resists or is inadequately trained on the new systems, it can lead to inefficiencies and errors, costing both time and money. An additional hurdle stems from budget constraints. High costs of state-of-the-art technologies can deter organizations from undertaking upgrades or full-scale implementations, which leads to a vicious cycle of outdated tools that cannot compete in today's fast-paced market.
Data Security Concerns
As smiles spread across the factory floor from improved efficiency, a shadow lurks behind—data security. With the rise of interconnected devices and systems, the risk of cyber threats escalates. Each sensor and machine that connects to a network can serve as a potential entry point for malicious actors. Thus, maintaining data integrity and security is not just a technical requirement; it's a must-have safeguard to bolster confidence in a manufacturer’s operations.
Utilizing robust data encryption methods and regularly updating firewalls are essential steps in this ongoing battle. Still, some companies overlook the importance of creating an organizational culture focused on cybersecurity. Employees who unintentionally click on phishing links or fail to follow security protocols are often the weakest links.
"As organizations lean more on technology, their security stances must evolve - a breach is not just a statistic; it's a potential disaster."
Skill Gaps in the Workforce
The introduction of advanced technologies, from AI to robotics, demands a workforce that can keep pace, yet many manufacturers face glaring skill gaps among their employees. Traditional skills are becoming obsolete and must be replaced with an entirely new set of competencies. It's like trying to run a marathon in business-casual shoes—utterly impractical.
Interestingly, these gaps can be traced back to educational systems not keeping up with industry needs. Despite there being a wealth of online learning resources, manufacturers often find it difficult to direct staff towards relevant courses. The result? A workforce that struggles to fully harness the power of technology—missing out on the advantages it brings to productivity and innovation.
To address these gaps, organizations need a dual approach. First, they should invest in training programs tailored to their specific technology stack. Second, partnering with educational institutions can help bridge the gap, preparing the next generation for a more technology-centric manufacturing landscape.
In summary, tackling these challenges associated with information technology within the manufacturing sphere requires more than just a technical solution. It demands a holistic approach that considers human factors, security protocols, and continuous skill development to ensure that manufacturers can not only adapt but thrive in an ever-changing market.
Future Trends in Manufacturing Information Technology
The world of manufacturing is in a constant state of flux, driven largely by advancements in information technology. Understanding the trends shaping this landscape is critical for stakeholders at all levels—from the factory floor workers to the strategic decision-makers. Embracing these trends can provide significant advantages, such as enhanced productivity, improved operational efficiency, and better quality assurance.
Emergence of Smart Factories
Smart factories represent the epitome of the digital transformation in manufacturing. These facilities leverage technologies like IoT and AI to create interconnected networks of machines, enabling them to communicate, self-optimize, and adapt in real-time.
- Benefits of Smart Factories:
- Increased Flexibility: Adapt production lines quickly in response to changing demand.
- Real-time Monitoring: Insights from machines allow for immediate adjustments, thus reducing waste.
- Predictive Maintenance: Utilizing AI, machines predict failures before they occur, thus minimizing downtime.
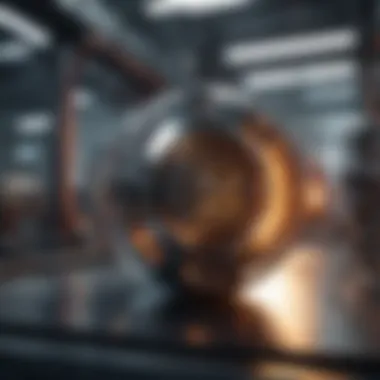

The future of smart factories lies not only in efficiency but also in sustainability. By implementing green technologies, manufacturers can minimize their environmental footprint while enhancing their operational capabilities.
Role of Blockchain in Manufacturing
Blockchain is no longer just a buzzword in finance; it’s making waves in manufacturing too. Its core principle of decentralized and transparent data management has the potential to transform supply chain operations.
- Key Considerations:
- Enhanced Traceability: Each transaction or product movement can be securely logged, making it easy to trace back sources and verify authenticity.
- Improved Collaboration: Stakeholders across the supply chain can share real-time data, reducing misunderstandings and improving efficiency.
- Cost Reduction: Lower administrative costs through automated processes, reducing the need for intermediaries.
As manufacturers begin to implement blockchain, the complexities of data handling in supply chains could largely diminish, leading to smoother operations and better accountability.
Increasing Automation and Robotics
Automation has been a fervent topic in the manufacturing sector for years, but the integration of advanced robotics is reaching new heights. Robots are becoming more intelligent, capable of performing complex tasks with precision.
- Impact on Workforce:
- Trends to Watch:
- Job Evolution: While automation may replace certain manual jobs, it also creates opportunities for higher-skilled positions, such as robot maintenance and programming.
- Safety Improvements: Robots can take over dangerous tasks, minimizing workplace injuries and promoting safer environments.
- Collaborative Robots (Cobots): Designed to work alongside humans, cobots enhance productivity without fully replacing human labor.
- Artificial Intelligence Integration: Robots armed with AI can learn from their tasks, making them more adaptive and efficient over time.
In closing, the future of information technology in manufacturing is not merely about implementing the latest gimmicks; it’s about creating an integrated, smart environment that marries technology with human ingenuity. As these trends continue to evolve, they promise to revolutionize how products are made, resulting in unprecedented levels of efficiency and innovation.
Case Studies: Successful Implementations
Exploring successful implementations of information technology in manufacturing offers an insightful lens to view its transformative potential. This section is important as it illustrates tangible outcomes and practical applications of theoretical concepts discussed previously. By diving into case studies, we can understand how companies leverage technology to overcome challenges, improve operational efficiency, and foster innovation in their processes.
The significance of these stories cannot be overstated. They serve as blueprints, providing not only inspiration but practical lessons for other businesses aiming to enhance their operations through technology. Each case study emphasizes unique elements, revealing the benefits and considerations necessary for successful integration of IT into manufacturing.
Thus, case studies function as not just examples, but educational resources illuminating routes to success for future endeavors in the industry.
Case Study: Automotive Industry
The automotive sector has seen remarkable transformations thanks to the integration of information technology. A classic example would be the American automotive giant Ford. By adopting advanced manufacturing technologies like IoT and AI, Ford streamlined its production lines.
Through smart sensors, vehicles are monitored in real-time from the factory floor to ensure everything runs smoothly. This implementation has decreased downtime significantly, allowing Ford to meet rising consumer demand without compromising quality.
Moreover, predictive maintenance technologies enable engineers to preemptively address potential issues in machinery before they lead to costly breakdowns, further enhancing productivity. In this case, integrating IT not only optimized operations but also enhanced the customer satisfaction due to timely production and delivery.
Case Study: Electronics Manufacturing
The electronics manufacturing sector often demands rapid innovation and precision, making it a prime candidate for information technology applications. Take Samsung, for instance, which has heavily invested in big data analytics and cloud computing to refine its manufacturing processes.
By utilizing data-driven decision making, Samsung anticipates market trends and adjusts production schedules accordingly. The results have been impressive. They managed to significantly cut waste and enhance product quality. The company's ability to track product defects in real time has led to faster recalls and more satisfied customers overall.
As they integrate these technologies, Samsung demonstrates how combining big data with traditional manufacturing practices can drive significant improvements in efficiency and accountability, setting a high standard in the electronics field.
Case Study: Food and Beverage Sector
In the food and beverage industry, Nestlé stands out with its innovative use of technology to address challenges related to supply chain management and quality assurance. By employing IoT devices within its operations, Nestlé now monitors temperature and freshness levels throughout the supply chain, ensuring products remain within safe consumption limits. This adaptation not only safeguards consumer health but also minimizes waste, driving sustainability efforts forward.
Moreover, the company has turned to automation to expedite production lines, ultimately reducing labor costs and enhancing product throughput. This case study exemplifies how strategic implementation of IT can lead to not just increased profitability but also positive environmental impacts.
Integrating information technology in manufacturing can lead to substantial improvements in efficiency, safety, and customer satisfaction, as illustrated in these case studies.
Through these real-world instances—from automotive to electronics and food production—we grasp a clearer picture of the potential achieved by harnessing the capabilities of information technology. Each sector showcases unique adaptations driven by specific challenges yet converges on a common impact: enhanced operational excellence.
Epilogue and Implications
The application of information technology in manufacturing processes cannot be overstated. As industries continue to adapt to the rapid pace of technological advancements, the role of IT becomes increasingly central. Embracing these technologies is not merely a matter of keeping up with competitors; it is a crucial strategy for survival and growth in a landscape that's constantly evolving.
Information technology acts as a backbone for various manufacturing processes. It facilitates communication, data sharing, and analysis, helping businesses to make informed decisions quickly. The benefits span across multiple facets of manufacturing, from improving operational efficiencies to enhancing product quality.
One cannot overlook the importance of integrating advanced technologies. For instance, using artificial intelligence allows companies to leverage predictive analytics, which can alert managers to potential equipment failures before they happen, thereby avoiding costly downtimes. Similarly, utilizing the Internet of Things (IoT) equips machinery and devices with sensors, enabling real-time data collection and management. This integration leads to greater transparency and helps streamline operations.
However, along with these advantages come significant challenges. Security remains a key concern, especially as more devices become interconnected. A cyber-attack can cripple operations, exposing sensitive data to theft or misuse. Therefore, implementing robust cybersecurity protocols is no longer optional but essential. Moreover, the skill gap in the workforce presents further hurdles. As manufacturing relies more on tech-savvy employees, ongoing training and development must take precedent.
Overall, the implications of incorporating information technology in manufacturing extend beyond immediate benefits. They suggest a paradigm shift whereby traditional manufacturing approaches give way to smarter, more agile operations. For industry leaders, this means re-evaluating not just processes but also workplace culture and employee engagement.
"To thrive in this digital landscape, businesses must recognize IT as a strategic asset rather than just a tool."
Summary of Findings
The exploration of information technology in manufacturing reveals several key takeaways. Foremost, enhanced operational efficiency through automation and analytics has become a hallmark of modern manufacturing. This transformation allows for more streamlined workflows and reduced waiting times.
Improved quality control methods have emerged from integrating technology, including the utilization of big data for analyzing production processes. This not only helps in identifying defects earlier but also in making iterative improvements more effectively.
It's also clear that cost reduction strategies through technology adoption are significant. By minimizing waste, optimizing supply chains, and maintaining predictive maintenance schedules, organizations can realize substantial savings.
Future Perspectives on Manufacturing
Looking ahead, the future of manufacturing intertwined with information technology is promising yet complex. The emergence of smart factories is set to redefine what manufacturing looks like. Environments where machines autonomously communicate with each other and adapt in real-time will soon be commonplace.
Blockchain technology may also introduce more secure and transparent supply chains. This could significantly reduce fraud and enhance traceability in product sourcing.
Furthermore, we see an increase in automation, with robots taking up more repetitive and dangerous tasks, thus elevating the human role to more creative and supervisory positions. The workforce will be challenged to adapt and shift towards tech-driven skill sets.