Exploring Injection Moulding Materials and Their Uses

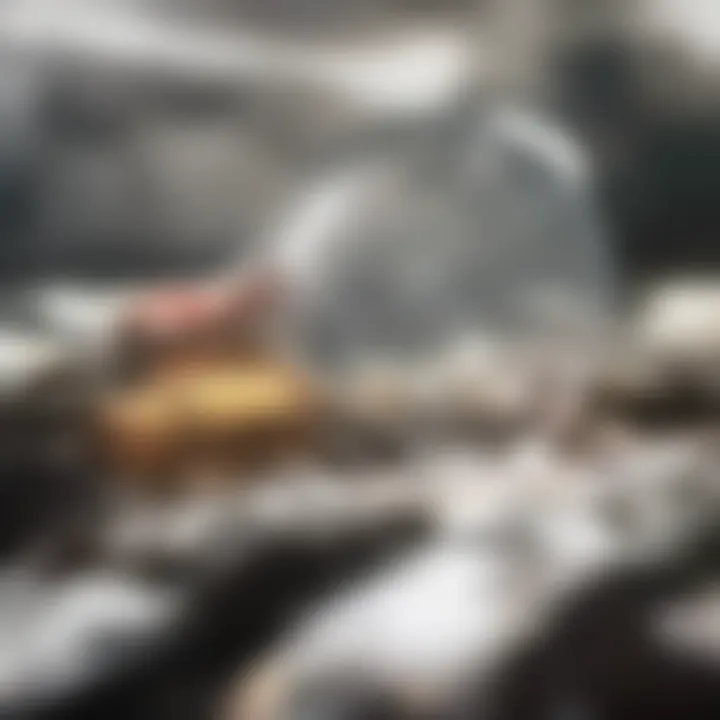
Intro
Injection moulding is a widely used manufacturing process for producing parts by injecting material into a mould. It is essential to understand the materials involved in this process as they significantly influence the final product's performance, durability, and aesthetic appearance.
In this exploration, we will analyze various types of materials used in injection moulding, including thermoplastics, thermosetting polymers, metal alloys, and composites. Understanding these materials is crucial for professionals in the manufacturing, engineering, and design fields.
Key Concepts
Definition of Primary Terms
To effectively engage with the topic, it is important to first define key terms related to injection moulding materials:
- Thermoplastics: These are polymers that become pliable or mouldable upon heating. They can be remoulded multiple times without losing their properties, making them versatile for various applications.
- Thermosetting Polymers: Unlike thermoplastics, these materials irreversibly harden when heated. Once formed, they cannot be remelted or reshaped. This property provides excellent resistance to heat and chemicals.
- Metal Alloys: These are mixtures of metals that offer enhanced properties such as strength, corrosion resistance, and improved durability. They are less common in injection moulding compared to plastics but have specific applications.
- Composites: Composites combine two or more materials, optimizing the strengths of each. They can offer tailored properties for specific applications.
Related Concepts and Theories
Material selection in injection moulding is influenced by various factors including cost, availability, and performance requirements. Understanding the interactions between these materials and the moulding process is critical. Different materials exhibit unique characteristics that affect processing times, cooling rates, and overall energy consumption.
Injection moulding designs require careful consideration of properties such as tensile strength, impact resistance, and thermal stability. This ensures that the selected material meets the intended performance standards.
Future Directions
Gaps Identified in Current Research
While significant research has been conducted on injection moulding materials, there remain areas needing further investigation. For example, the compatibility of new bioplastics with traditional injection moulding processes is an emerging field. There is also a lack of comprehensive data on long-term performance of new composite materials in various environments.
Suggestions for Further Studies
Future research should explore:
- Biodegradable Materials: Investigate the potential of new sustainable materials that can be used in injection moulding.
- Enhanced Processing Techniques: Study new methods to reduce cycle times and improve energy efficiency in the moulding process.
- Interdisciplinary Approaches: Collaborating with material scientists to develop hybrid materials that combine the best properties of existing options.
Advancements in material science could greatly enhance the injection moulding process, paving the way for more innovative products.
By addressing these gaps and pursuing promising avenues, we can continue to improve the efficiency and effectiveness of injection moulding materials.
Overview of Injection Moulding
Injection moulding is a central process in many manufacturing sectors, particularly in the production of plastic components. This technique has proven valuable for creating complex shapes with high precision and efficiency. It involves injecting molten material into a mould, where it cools and solidifies into the desired form. The significance of injection moulding lies in its ability to produce large quantities of identical parts, making it the preferred method for mass production.
Understanding the concept of injection moulding is vital for anyone involved in product design or manufacturing. By comprehending how the process operates, decision-makers can choose the best materials and designs that align with their production goals. The method has applications across various industries, including consumer goods, automotive, and healthcare. As the demand for innovative and sustainable products grows, the relevance of injection moulding continues to evolve, prompting discussions on materials used in this process.
Definition and Process
Injection moulding starts with selecting a suitable material, typically in granular form. The material is fed into a heated barrel, where it melts under controlled temperature. Once in a molten state, it is injected into a pre-designed mould under high pressure. This ensures that the material takes on the shape of the mould accurately. After the injection, the material is allowed to cool, solidifying and taking form. The mould is then opened, and the finished part is removed. The efficiency of this process allows for rapid production cycles, which is essential for meeting market demands.
Historical Development
Injection moulding has undergone significant evolution since its inception. The first patents date back to the late 19th century when processes involved basic materials and rudimentary machines. Early methods used materials like brownstone and later evolved to incorporate thermoplastics in the mid-20th century.
The development of thermoplastic materials revolutionized the industry, making it practical to create more complex and durable components. With advancements in technology, injection moulding machines have become more sophisticated, allowing for better precision and control over the process. Today, numerous materials are available for use in injection moulding, enabling designers to optimize performance and cost-effectiveness.
Material Selection in Injection Moulding
Material selection in injection moulding is a critical aspect of the entire molding process. The choice of material directly influences the product's performance, cost-efficiency, and environmental impact. Selecting the appropriate material ensures that the finished product meets functional requirements and has the desired durability and aesthetic appeal. Understanding the implications of material choice is essential for optimizing injection moulding operations and achieving high-quality outcomes.
Importance of Material Choice
The material choice in injection moulding encompasses various factors that can determine the success of a manufacturing project. It affects product properties such as strength, flexibility, and thermal resistance. Choosing the right material can enhance performance while reducing waste and production costs. Additionally, material choice plays a pivotal role in sustainability considerations, influencing whether products can be recycled or biodegraded.
Factors Influencing Material Selection
Material selection is not arbitrary; it involves a methodical assessment of several factors that govern the physical properties and usability of the final product. These factors include mechanical properties, thermal stability, cost considerations, and environmental impact.
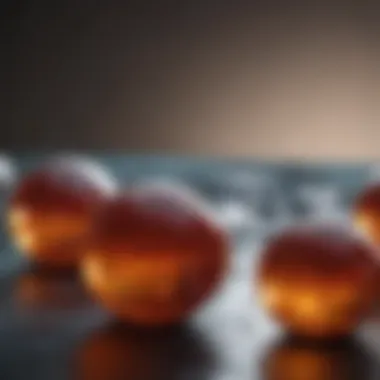
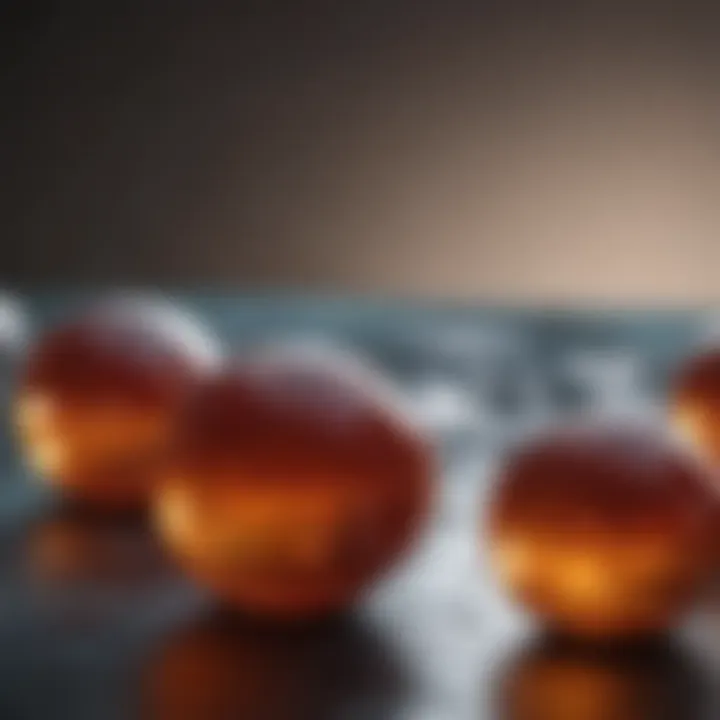
Mechanical Properties
Mechanical properties refer to how a material reacts under various stresses. These properties include tensile strength, impact resistance, and elasticity. Mechanical durability is paramount in applications where products will face physical stress. For instance, high tensile strength is essential for components in automotive or aerospace industries, making certain materials popular choices. Understanding these properties allows designers to predict how materials will perform under specific conditions, thus ensuring reliability in end-use applications.
Thermal Stability
Thermal stability is vital for materials that will experience high temperatures during processing or end-use. It defines a material's ability to maintain its properties over a range of temperatures. Typical examples where thermal stability is important include automotive and electrical components. Materials with high thermal stability resist deformation during processing and ensure that dimensional integrity is maintained in finished products. This characteristic is beneficial as it minimizes waste due to distortion and enhances product life, but it may also restrict the choice of materials to high-performance polymers.
Cost Considerations
Cost considerations involve evaluating not only the price of the raw materials but also processing costs and potential waste during production. Materials chosen must align with the budgetary constraints without sacrificing quality. Economical material options can be advantageous, particularly for high-volume production runs. However, lower costs might compromise the durability or functionality of the product, leading to higher long-term costs. Thus, achieving a balance between cost and quality is essential in decision-making.
Environmental Impact
Environmental impact is becoming increasingly important in material selection. The focus has shifted towards sustainability, prompting manufacturers to consider how materials affect the planet across their lifecycle. Choosing biodegradable plastics or recycled materials can significantly reduce a product's carbon footprint. Companies are now motivated to assess not only how they source materials but also how they affect ecosystems after their use. This consideration can enhance a brand's reputation and align with consumer demand for environmentally responsible products.
"Effective material selection is not just about performance; it also encompasses cost, sustainability, and future impact on the environment."
Thermoplastics in Injection Moulding
Thermoplastics play a central role in injection moulding due to their unique characteristics and versatility. These materials become pliable when heated and solidify upon cooling, which makes them suitable for intricate designs. Thermoplastics can be remelted and reshaped, providing manufacturers an opportunity to reuse materials effectively. This feature enhances sustainability in production processes, an increasingly important consideration in today's manufacturing climate. The variety of thermoplastics, along with their distinct properties, allows them to cater to diverse applications ranging from packaging to automotive parts.
Polypropylene
Properties
Polypropylene is widely recognized for its robustness and lightweight nature. It has a high melting point, allowing it to withstand heat better than many other thermoplastics. Its chemical resistance is another key property, making it suitable for environments where exposure to harsh substances is expected. Polypropylene's strength combined with flexibility is a beneficial characteristic for many applications. However, it can be brittle at lower temperatures, which may limit its effectiveness in cold conditions. This balance of pros and cons makes polypropylene a commonly preferred choice in various sectors, particularly in consumer goods.
Applications
The versatility of polypropylene translates into numerous practical applications. It is frequently used in packaging, automotive components, and household products. Its light weight and impact resistance allow it to excel in creating durable storage solutions, including containers and bottles. However, one must consider that while polypropylene is cost-effective, its lower resistance to UV rays can result in degradation when exposed to sunlight for extended periods. Therefore, appropriate application contexts are critical for maintaining product longevity.
Polyethylene
Types and Variants
Polyethylene is another prominent thermoplastic, known for its range of types, including Low-Density Polyethylene (LDPE) and High-Density Polyethylene (HDPE). Each variant displays distinct characteristics, such as flexibility and rigidity, affecting their suitability for different applications. For instance, LDPE is particularly flexible and used for film applications, while HDPE offers higher strength, making it ideal for containers and pipes. This variety allows manufacturers to select the right type based on specific needs and application requirements.
Applications
The applications of polyethylene are vast, extending from packaging materials to components in construction. LDPE is commonly used in plastic shopping bags and food packaging, where flexibility is crucial. Conversely, HDPE is utilized in items such as water bottles and toys due to its sturdiness. This adaptability underscores polyethylene's significance in both consumer products and industrial applications. Nonetheless, like other thermoplastics, careful consideration of environmental factors is necessary to prevent degradation in certain contexts.
Polystyrene
Characteristics
Polystyrene is recognized for its rigid structure and ease of processing. It is available in solid and foam forms, each catering to different needs in manufacturing. The lightweight nature of polystyrene contributes to its popularity, especially in packaging. Its low cost makes it accessible for large-scale production. However, it can be more fragile compared to other plastics, needing careful handling. Balancing its benefits and limitations is essential for effective use in products.
Common Uses
Common uses of polystyrene extend to disposable cutlery and packaging materials. Its foam variant, often referred to as Styrofoam, is widely utilized for insulation and in food containers. The material's properties make it especially well-suited for applications requiring lightweight and cushioning characteristics. On the flip side, its environmental impact due to non-biodegradability is a concern, prompting the need for more sustainable alternatives in specific applications. Utilizing polystyrene efficiently requires consideration of both its functional attributes and environmental responsibilities.
Thermosetting Plastics
Thermosetting plastics play a crucial role in the injection moulding process. These materials are distinct from thermoplastics due to their unique chemical structures. Once cured, they maintain their shape and don’t melt upon heating. This characteristic is essential in applications where high temperature resistance and durability are needed. Thermosetting plastics offer specific benefits that make them favorable for industries such as automotive, aerospace, and electronics.
Epoxy Resins
Chemical Structure
Epoxy resins are formed by the reaction of epoxide compounds with hardeners. The resulting three-dimensional cross-linked structure is notable for its rigidity and strength. This chemical arrangement means that epoxy resins can withstand significant stress and environmental conditions. Their enhanced adhesion properties also contribute to their popularity in the manufacturing of composite materials. Some unique features of epoxy resins include excellent moisture resistance and chemical stability.
Applications
Epoxy resins find their applications in various sectors. They are widely used in reinforcing materials, coatings, and adhesives. The strong bonding characteristics make them ideal for composites where durability is essential. Their resistance to heat makes them a popular choice for electronic components as well. However, they do have limitations in flexibility, which may restrict their usage in certain applications.
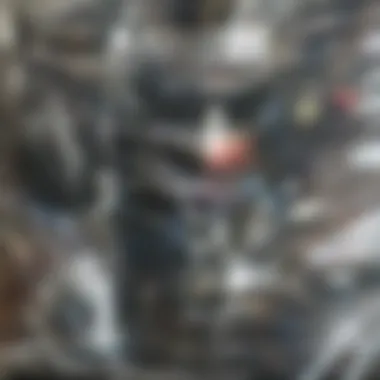
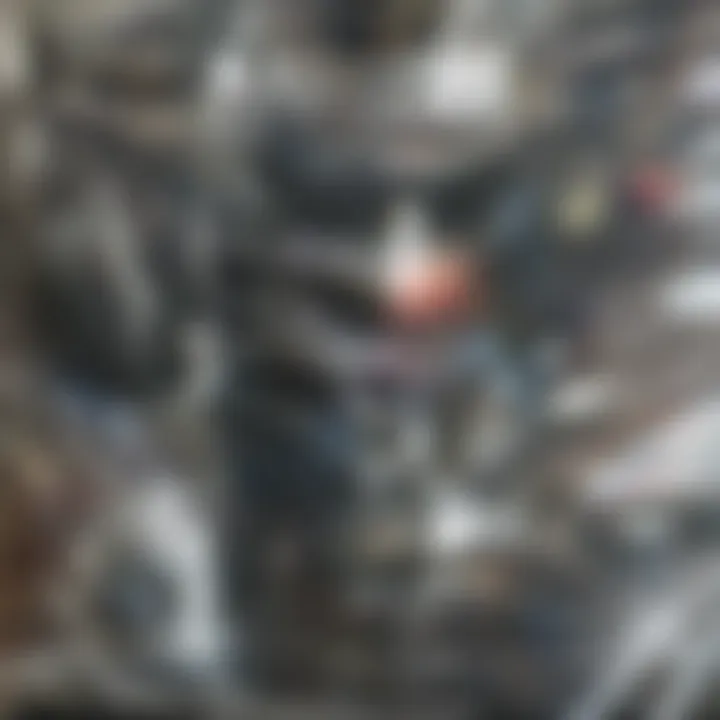
Phenolic Resins
Key Properties
Phenolic resins are known for their exceptional thermal stability and mechanical strength. These resins exhibit low flammability and resist degradation from UV exposure. Their rigid structure contributes to their gainful usage in various industries. One key characteristic of phenolic resins is their ability to withstand high temperatures without losing integrity, making them beneficial in critical applications requiring durable materials. However, their chemical resistance may be lower compared to epoxy resins.
Usage Scenarios
Phenolic resins are widely used in laminates, electrical insulators, and molded products. Their robust nature makes them suitable for construction materials in high-stress environments. They are also favored in the manufacturing of heat-resistant components. Despite their many advantages, the potential brownish tint can be a drawback in applications requiring aesthetic finish. Nonetheless, their performance in demanding scenarios often outweighs such concerns.
Metal Alloys in Injection Moulding
Metal alloys play a significant role in injection moulding, providing unique characteristics that distinguish them from common plastic materials. These alloys, primarily aluminium and zinc, offer advantages in strength, durability, and weight. Their use in various applications ranges from consumer products to complex industrial parts. Understanding metal alloys' properties and their implications in manufacturing can enhance product performance significantly. This section delves into the specific advantages, applications, and properties of these alloys in the injection moulding process.
Aluminium Alloys
Advantages
Aluminium alloys provide several notable advantages when used in injection moulding. One key characteristic is their light weight, which contributes to overall product efficiency. The low density of aluminium alloys reduces transportation costs and energy consumption, making them a popular choice in industries where weight is a critical factor. Additionally, these alloys display good corrosion resistance, extending the lifespan of products made from them.
Another essential advantage is their strength-to-weight ratio. This means that aluminium alloys can maintain structural integrity while being much lighter than their steel counterparts. This is particularly beneficial in industries such as automotive, where reducing weight directly correlates with fuel efficiency. However, it's important to note that while aluminium alloys are strong, they may not be suitable for all high-stress applications, where heavier metals may outperform them.
Common Applications
The common applications of aluminium alloys in injection moulding are diverse and impactful. They are frequently utilized in the automotive sector, where components such as engine parts and chassis are manufactured to reduce overall vehicle weight. Another significant area is in the production of consumer products, including housings for electronics and kitchen appliances.
One unique feature of aluminium alloys is their ability to be anodized, which enhances surface properties and aesthetic appeal. This process improves corrosion resistance by forming a protective oxide layer on the metal surface. Such advantages make aluminium alloys a preferred choice for many manufacturers aiming for both functional and visually appealing products.
Zinc Alloys
Properties
Zinc alloys present distinct properties that make them suitable for injection moulding. A key characteristic of these alloys is their excellent fluidity in the molten state, allowing for intricate designs and precise finishing. Zinc also has a relatively low melting point, which enables the use of lower energy in the moulding process, thus reducing costs.
Furthermore, zinc alloys show impressive mechanical properties, like good tensile strength and fatigue resistance. These qualities make them suitable for applications that require durability and longevity. However, it is crucial to be aware of the potential casting defects in complex geometries, which may limit production efficiency under certain conditions.
Industrial Uses
Zinc alloys have numerous industrial uses, particularly in the realm of die casting and architectural components. Common applications include automotive parts, such as housings for gears and switches, where precision is essential. These alloys are also frequently found in the manufacturing of hardware items, including fasteners and electronic components.
The unique feature of zinc alloys is their ability to be plated or coated, which enhances their resistance to corrosion while maintaining their aesthetic characteristics. This makes them a beneficial and popular choice for outdoor applications, where environmental exposure is a concern.
In summary, metal alloys bring distinctive qualities to injection moulding that can significantly impact product performance and manufacturing efficiency. Understanding their properties and applications will help guide decisions in material selection.
Composites in Injection Moulding
The integration of composites in injection moulding provides manufacturers with enhanced properties and performance characteristics not achievable with traditional materials. Composites, which combine two or more materials to create a composite material with unique benefits, have emerged as prominent contenders in various applications. Their versatility and adaptability allow for optimized performance in structural and aesthetic aspects of products.
As manufacturers increasingly focus on lightweight and durable components, composites have gained significance in industries such as automotive, aerospace, and consumer goods. They offer advantages like improved strength-to-weight ratios, resistance to environmental degradation, and enhanced thermal and electrical properties. Despite their benefits, composites also introduce certain complexities in processing and cost considerations, which warrant careful evaluation during material selection.
Fibreglass Reinforced Plastics
Material Composition
Fibreglass Reinforced Plastics (FRPs) consist primarily of a polymer matrix reinforced with glass fibres. The polymer used is often a thermosetting resin, such as epoxy or polyester, which provides excellent durability and heat resistance.
The inclusion of glass fibres significantly enhances the tensile strength and rigidity of the plastic. This combination is popular due to its lightweight nature and resistance to corrosion, making it suitable for demanding environments.
One major characteristic of FRPs is their low thermal conductivity, which is beneficial in applications requiring thermal insulation. However, challenges such as brittleness can limit their use in highly impact-sensitive applications.
Application Areas
The application areas for Fibreglass Reinforced Plastics are varied. They are commonly utilized in automotive components, industrial equipment, and sporting goods. The lightweight yet durable nature of FRPs allows for energy savings in transport and reduces overall production costs.
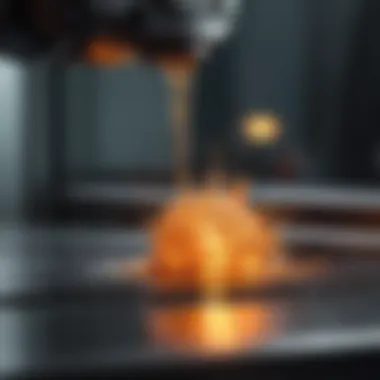
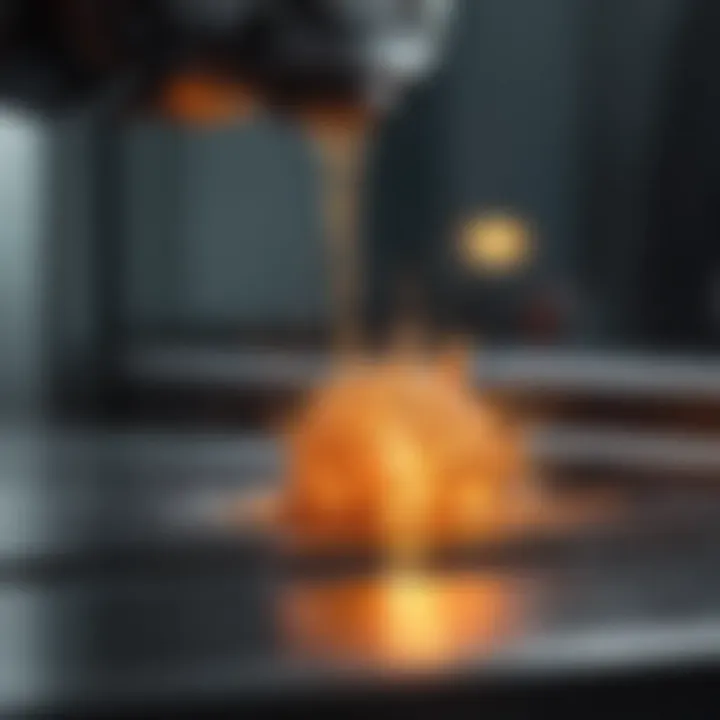
One notable feature of FRPs is their customization in terms of fibre orientation and resin type, enabling tailored solutions for specific applications. However, their higher initial cost compared to traditional materials may act as a disadvantage in some contexts.
Carbon Fibre Reinforced Plastics
Mechanical Performance
Carbon Fibre Reinforced Plastics (CFRPs) are notable for their exceptional mechanical performance. They possess a high strength-to-weight ratio, providing superior stiffness and strength compared to many metals. This unique characteristic makes CFRPs valuable in applications where performance is crucial, such as in aerospace and high-end automotive components.
CFRPs exhibit excellent fatigue resistance and lower thermal expansion, which means they maintain dimensional stability under varied temperature conditions. This stability is crucial in applications requiring precision. However, the potential for delamination under certain stresses can be a concern.
Advantages Over Traditional Materials
CFRPs present several advantages over traditional materials like steel and aluminium. Their lightweight properties result in significant weight reductions in constructed components, facilitating fuel efficiency in vehicles and aircraft.
Moreover, CFRPs resist corrosion and environmental degradation, extending the lifespan of products compared to their traditional counterparts. This resilience enables lower maintenance costs over time. However, the high cost of carbon fibre and the complex manufacturing methods can limit their widespread adoption, particularly in lower-end markets.
"The future of composites, especially those used in injection moulding, hinges on balancing performance with cost-efficiency to meet the industry's growing demands."
In summary, the role of composites in injection moulding signifies a shift towards more advanced and efficient manufacturing processes. Their properties allow for innovative product designs that meet increasing performance standards while addressing environmental concerns.
Emerging Materials for Injection Moulding
Emerging materials for injection moulding hold significant potential for the industry. With increasing demands for sustainability and advanced performance, these materials present innovative solutions that align with modern manufacturing needs. The importance of exploring this area includes understanding how these materials can reduce environmental impacts, enhance performance, and meet the evolving expectations of consumers. As technology progresses, the incorporation of new materials can lead to more efficient production cycles and better-end products.
Biodegradable Plastics
Types
Biodegradable plastics are crucial for sustainable manufacturing practices. They break down naturally in the environment, reducing plastic waste issues that traditional materials cause. There are several types of biodegradable plastics, such as polylactic acid (PLA), polyhydroxyalkanoates (PHA), and starch-based plastics. Each type has distinct properties and degradation timelines, which makes them suitable for various applications.
The key characteristic of biodegradable plastics is their ability to decompose under specific conditions, often in less than a year. This feature makes them a beneficial choice for industries aiming to lessen their environmental footprint. However, it is essential to consider the unique feature of these materials regarding their longevity and performance compared to conventional plastics, as some may not meet strict durability requirements.
Applications and Limitations
The applications of biodegradable plastics are varied, ranging from packaging to agricultural films. Their ability to break down offers an environmentally friendly alternative to traditional materials. However, there are limitations associated with their use. Not all biodegradable plastics decompose efficiently in every environment. For instance, many require industrial composting facilities to break down appropriately. Furthermore, their mechanical properties may not always match those of conventional materials, limiting their use in high-performance applications. This balance of benefits and limitations plays a crucial role in determining their viability in injection moulding processes.
Advanced Polymers
Properties
Advanced polymers represent a significant advancement in materials science, offering enhanced performance features. These materials often exhibit superior strength, heat resistance, and chemical stability. Many advanced polymers, such as polyetheretherketone (PEEK) and polyamide-imide (PAI), are engineered for high-performance applications, making them suitable for industries like aerospace and automotive. The unique characteristic of these advanced materials is their ability to perform under extreme conditions, thus broadening the scope for their application.
Their benefits include longer life spans and improved performance metrics, which often mitigate the higher initial cost of these materials. However, their processing can be more complex and may require specialized equipment.
Future Trends
Future trends in advanced polymers point towards increasing use in various sectors, driven by the need for sustainable and high-performance solutions. Innovations are likely to focus on enhancing recyclability and reducing manufacturing costs. As these materials become more mainstream, improvements in processing techniques and formulations are expected.
The key characteristic of these trends is the convergence of sustainability with performance. Companies will seek solutions that not only meet strict performance criteria but also align with environmentally responsible practices. However, the challenge remains in overcoming the cost barriers associated with high-performance polymers and ensuring consistent quality during manufacturing processes.
The advancements in polymer technology signify a pivotal shift towards more sustainable and high-performance materials in injection moulding.
The End
Understanding the various materials used in injection moulding is crucial for professionals in manufacturing and design. The selection of the right material directly affects the performance, durability, and overall quality of the final product. By exploring materials such as thermoplastics, thermosetting plastics, metal alloys, and composites, the article provides a broad perspective on their respective characteristics and applications. This grasp of material properties not only aids in cost-effective choices but also encourages sustainable practices in production.
Material selection is not just about meeting specifications but also about foresight in innovation and adaptability to changing market needs. Thus, knowledge gained from this article is not merely academic; it serves practical purposes that can influence future projects significantly.
"Choosing the right material is a vital step in the product development process that has far-reaching consequences for functionality and sustainability."
Summary of Key Points
- Diverse Materials: The article covers a range of materials suited for injection moulding, including thermoplastics like polypropylene and polyethylene, thermosets such as epoxy and phenolic resins, and various metal alloys and composites.
- Material Characteristics: Each material has distinct properties that make it suitable for specific applications. Understanding these properties is essential for optimizing the moulding process.
- Applications and Limitations: It is vital to recognize not only the advantages but also the limitations of each material, which can directly impact product performance and longevity.
- Emerging Trends: The discussion about biodegradable plastics and advanced polymers highlights ongoing developments and trends that shape the future of injection moulding.
Future Directions in Material Research
The landscape of material science is constantly evolving, driven by advancements in technology and changing industry demands. Future research is expected to focus on:
- Sustainability: There is a growing interest in developing eco-friendly materials, including biodegradable options that can reduce environmental impact. Research will likely explore the integration of recycled materials into mainstream injection moulding processes.
- Nanomaterials: Innovations involving nanotechnology could lead to the development of materials with enhanced properties. These materials could achieve higher strength, lighter weight, and improved thermal and electrical properties.
- Smart Materials: The exploration of intelligent materials that can respond to environmental stimuli is on the horizon. These materials can change properties based on factors such as temperature or light, opening new possibilities for product design.
- Testing and Refinement: Continued research will be important for improving testing methods and refining material processes. It will ensure that manufacturers can meet stringent regulations and quality standards while innovating products.
In summary, the future of injection moulding materials lies in the convergence of sustainability, advanced science, and innovation, presenting both challenges and opportunities for industry stakeholders.