In-Depth Guide to Powder Coating Formulation
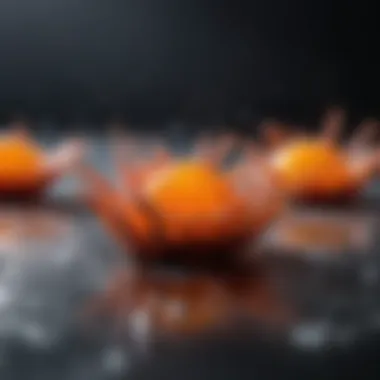
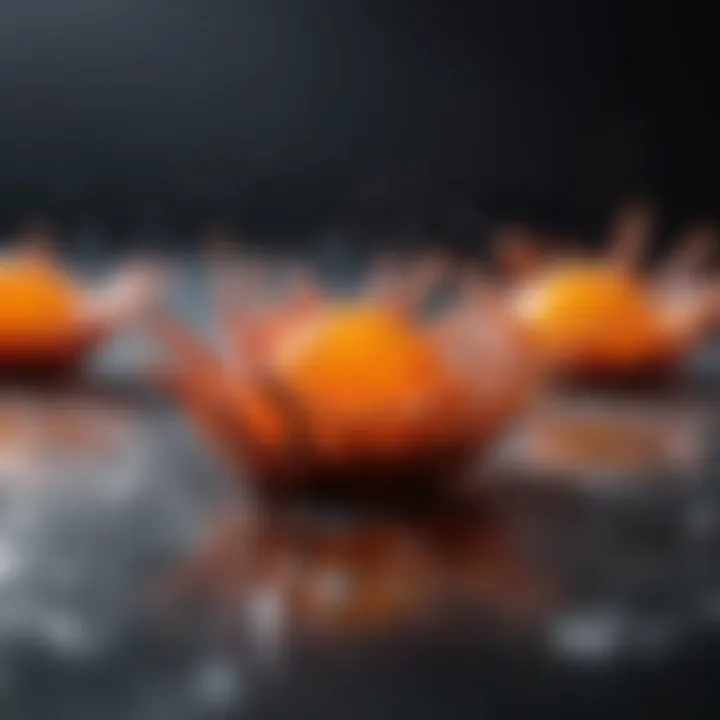
Intro
Powder coating is not just an art; it's a science. As a durable and versatile coating method, it is favored across various industries for its resilient finish. Unlike traditional liquid paints, which need solvents to keep the paint liquid, powder coating uses finely ground particles that form a dry film when heated. But what goes into the making of this innovative coating solution? That’s what we will delve into.
Key Concepts
Definition of Primary Terms
At the heart of powder coating lies a unique blend of chemical components. Generally, they include:
- Resins: These are the primary binding agents that give the coating its strength and durability. Common types include epoxy, polyester, and urethane.
- Pigments: These offer color and opacity to the powder. The pigment choices can dramatically affect the coating’s appearance and characteristics.
- Additives: Designed to enhance the performance, additives can improve flow, prevent settling, or enable quicker curing times.
- Curing Agents: These chemicals facilitate cross-linking when the powder is heated, thus setting the finish.
With these components, a variety of formulations can be designed to meet specific needs. Each component contributes uniquely to the coating's final properties, making formulation an intricate process.
Related Concepts and Theories
To fully appreciate powder coating, it’s essential to understand related concepts:
- Electrostatic Spraying: A key application technique where charged particles adhere to the substrate, providing an even coating.
- Thermal Curing: The heat process that solidifies the powder coating, allowing it to bond permanently to the surface.
- Environmental Impact: Unlike traditional systems, powder coating is environmentally friendly, emitting fewer volatile organic compounds (VOCs) and being easily reclaimable.
The formulation process is more than just mixing ingredients. It's about achieving harmony between these components to produce a coating that meets heat resistance, corrosion resistance, and aesthetic appeal.
"The quality of the finish often lies in the unseen details of formulation and application."
Future Directions
Pacing towards the future of powder coating reveals both challenges and opportunities for innovation.
Gaps Identified in Current Research
While there’s considerable progress in the field, several gaps remain:
- Sustainability: More work is needed to develop fully sustainable raw materials. Aside from the eco-friendliness of the process itself, the source of resins and pigments can further enhance the overall environmental footprint.
- Adhesion Mechanisms: A deeper understanding of adhesion at a molecular level is warranted, emphasizing how coatings adhere under different conditions.
Suggestions for Further Studies
Taking these gaps into account, the following directions could be promising:
- Evaluation of New Materials: Research into alternative bio-based resins and pigments could open new avenues for innovation.
- Application Techniques: Studies focusing on newer application methods that reduce waste and enhance uniformity would be beneficial.
By addressing these areas, we could impact industries from automotive to consumer goods, whereby innovation and sustainable practices can redefine powder coating’s role in modern manufacturing.
Intro to Powder Coating
Powder coating is an often overlooked process that plays a pivotal role in enhancing the durability and aesthetic appeal of various products. Understanding this surface finishing technique is crucial for students, researchers, and professionals in the field. Gaining a solid grasp of powder coating not only opens doors to advanced material sciences but also offers insights into sustainable manufacturing practices. This introduction aims to illuminate why powder coating formulation must not be dismissed as just another technical process, highlighting key elements and benefits that are worth considering.
Definition and Overview
Powder coating involves applying a dry powder to a surface, which is then cured under heat to form a hard, protective layer. Unlike traditional liquid paint, powder coating is free from solvents, making it both environmentally friendly and efficient. In practical terms, this technique results in a finished product that boasts a tough surface. Depending on the specific formulation, powder coatings can provide a range of finishes—from high gloss to matte—a flexibility rivaled by few other methods.
The powder itself is primarily composed of finely ground particles of pigment and resin, which may be thermoplastic or thermoset in nature. The choice of resin is intrinsic to achieving desired properties like weather resistance, adhesion, or chemical resistance. Furthermore, this method is often favored for its ability to create a uniform coating, which ensures that even intricate shapes gain an even layer.
History and Evolution
Diving into the historical context, powder coating has its roots tracing back to the 1940s when it was first utilized in the United States. It was invented by a German chemist who devised a way to spray dry powder onto objects, revolutionizing how coatings were applied. Initially, the process was rather rudimentary and limited to industrial applications. However, as technology advanced, the method saw its share of innovations.
By the late 1960s, with the rising consciousness around environmental issues, powder coating gained momentum as a cleaner alternative to traditional liquid coatings. The technology saw significant enhancements during the 1980s with the introduction of electrostatic spraying, allowing for improved efficiency and transfer efficiency rates. Over the decades, enhancements in curing processes and cross-linking techniques has catapulted its usability in various sectors, rendering it a staple in many production lines today.
Current Applications
In today's industry, powder coating is not just a yes-man to decorative needs; it stretches applications far and wide. Consider the automotive industry, where it's used to coat car parts for increased durability and to achieve a durable finish that withstands harsh environmental conditions. Similarly, appliances such as refrigerators and ovens benefit immensely from the protective layer provided by this coating.
Additionally, the architectural sector leverages powder coatings for aluminum and steel structures, offering aesthetics alongside robust protection against corrosion and wear. It's also worth noting that companies are increasingly turning to this method for consumer goods, furniture, and sporting equipment, enhancing product integrity without compromising design.
The environmental advantages cannot be overstated; many manufacturers have switched to powder coating to minimize pollution and waste. > "With burgeoning interest in green technologies, powder coating stands out as a practical choice for environmentally-conscious enterprises."
In summary, as the powder coating process has evolved, its significance and applicability have expanded substantially, influencing not just manufacturing, but also considerations around sustainability. Recognizing its history and current relevance provides a firm foundation for understanding its formulation complexities.
Key Components of Powder Coating Formulation
Understanding the key components of powder coating formulation is crucial for grasping how this surface finishing technology works. These components not only define the coating's characteristics but also influence its performance and aesthetic qualities. By comprehending the specific elements that make up powder coatings, the reader can better appreciate how to achieve desired results in various applications, from industrial to decorative uses.
Resins: Types and Functions
Resins play a pivotal role in the formulation of powder coatings, functioning as the primary binding agents that provide adhesion and durability to the finished surface. The most commonly used types of resins in powder coatings include epoxy, polyester, and acrylic resins, each bringing unique characteristics to the table.
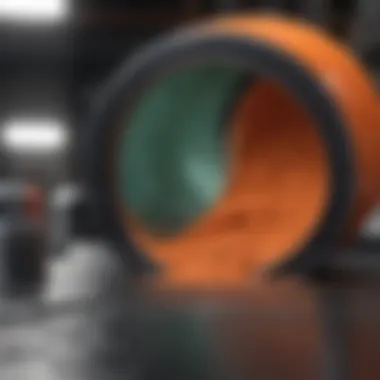
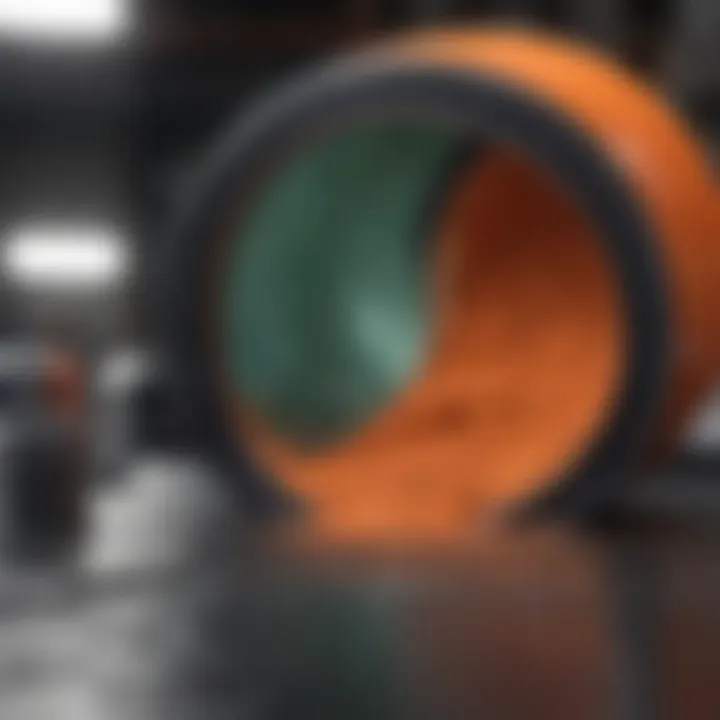
- Epoxy Resins: Known for their excellent adhesion and chemical resistance, epoxy resins are often used in applications where durability is necessary, such as automotive and industrial coatings. They provide hard coatings that withstand mechanical wear and environmental challenges. However, their UV stability can be a limitation, leading to yellowing or degradation when exposed to sunlight.
- Polyester Resins: These resins are a popular choice due to their good weather resistance and color retention. They are widely used in architectural applications and outdoor furniture finishes. The durability against UV rays makes polyester formulations a reliable option for products exposed to harsh environmental conditions.
- Acrylic Resins: Acrylic resins offer exceptional gloss and color retention, making them ideal for decorative applications. They are known for their clarity and brightness, which enhances aesthetic appeal. However, they may not provide the same level of chemical resistance as epoxy or polyester.
The function of these resins is not limited to mere adhesion; they also impact various performance aspects such as scratch resistance and overall hardness. Selecting the right resin is fundamental in achieving a powder coating that meets specific performance criteria.
Pigments: Color and Performance
Pigments are not just about color; they are integral to a powder coating's overall performance, influencing visual appeal as well as protective qualities. The choice of pigments directly affects both aesthetic and functional attributes of the coatings.
- Color Pigments: These are crucial for achieving the desired hue in the final product. They can be organic or inorganic, with organic pigments often providing bold colors while inorganic pigments are generally known for better stability and durability. Some small manufacturers are exploring natural pigments to replace synthetic ones, which is an emerging trend in sustainability efforts.
- Functional Pigments: Beyond just color, functional pigments can impart particular properties to the coating. For instance, some pigments can enhance UV protection, corrosion resistance, or antimicrobial properties. This incorporation of functional pigments expands the possibilities for application in demanding environments.
In understanding pigments, one must also consider the processes for achieving uniform dispersion within the resins, as poor dispersion can lead to inconsistencies in color and performance.
Additives: Enhancing Properties
Additives are the unsung heroes of powder coating formulations. While resins and pigments grab the spotlight, it’s often the additives that fine-tune a coating’s performance and versatility. These may include accelerators, flow agents, anti-foaming agents, and many others, each serving distinct purposes.
- Flow Agents: These materials help in achieving a smooth application, ensuring that the powder flows easily and evenly during the electrostatic spraying process. A well-flowing powder reduces the likelihood of clogging and defects in the coating.
- Curing Agents: Essential for initiating the crosslinking process during curing, these additives determine how quickly and effectively the coating adheres and sets. For example, a fast-curing agent can speed up production times, but it may require careful evaluation against potential impacts on flexibility or hardness.
- Stabilizers and Surfactants: These additives help control the stability of the coatings before application, preventing settlement and improving homogenization. The right choice of stabilizer can ensure that the coating retains its properties over time without deteriorating.
In sum, every additive has a specific role that enhances the final product, making it key to consider their functions when developing a powder coating formulation. Efficient and thoughtful integration of these components ultimately leads to superior performance and versatility of the powder coating.
Formulation Techniques
When it comes to powder coating formulation, understanding the techniques involved is crucial. This practice is like cooking a delicate meal; the right combination of ingredients and processes can yield a perfect finish, while a single misstep can ruin everything. Formulation techniques are essential because they determine the flowability, adhesion, and overall performance of the powder coating. Furthermore, these techniques help in maintaining consistency and quality, which are non-negotiable in an industrial setting.
Blending and Mixing
Blending and mixing are the foundational steps in the powder coating formulation. This involves combining different components such as resins, pigments, and additives to create a uniform powder. Imagine trying to make a cake batter; if the flour isn't mixed properly with the eggs and sugar, the result will be uneven. Similarly, in powder coating, inconsistency in blending can lead to variations in color, gloss, and texture.
In the mixing stage, the equipment used plays a pivotal role. High-speed mixers, for instance, can facilitate a thorough blend of materials, but they need to be monitored closely to prevent overheating. After mixing, achieving a uniform quality may require recalculating the ratios of various components, ensuring that the final product meets required specifications.
- Importance of Even Distribution: Even dispersion of pigments ensures that the final coat exhibits consistent color.
- Impact on Performance: Proper blending can significantly enhance the adhesion properties of the powder, impacting its durability.
- Quality Control: Regular sampling during this process can help in identifying any issues early on, paving the way for immediate corrective actions.
Extrusion Processes
Extrusion processes are where the mixture of powders gets transformed into a usable form. This technique, akin to squeezing toothpaste out of a tube, forces the blended powder through a heated barrel. As it passes through, it melts into a viscous liquid, creating uniform profiles. The significance of this step lies in the conversion of the powdered materials into a solid form that can be easily handled and stored.
The extrusion process is not without its considerations; temperature control is key. If the temperature runs too high, it can degrade sensitive components like resins or pigments, resulting in poor performance. Conversely, if it’s too low, the mixture may not melt completely, leading to clogs and inefficiencies in production.
- Equipment Choices Matter: The choice of extruder affects the quality of the output.
- Key Variables: Parameters like speed, temperature, and pressure need to be optimally adjusted for the desired outcome.
- Recycling Potential: Extrusion also allows for recycling excess powder, which is an economic benefit.
Grinding and Sifting
Once the extruded material has cooled and solidified, it undergoes grinding and sifting. This stage is comparable to refining a rough diamond; it polishes the finished powder to ensure that it has the right particle size needed for application. Fine powders tend to create smoother finishes and better coverage, but excessive milling can also lead to degradation of the materials.
Grinding techniques vary from mechanical grinders to cryogenic grinding, each with its unique set of pros and cons. After grinding, sifting or sieving is undertaken to separate undesirable larger particles from the mix. This ensures that only uniform sizes make it to the final product, providing a consistently high-quality coating.
- Particle Size's Role: Different applications may require different particle sizes; fine particles can enhance smoothness while coarser ones may increase texture.
- Control Techniques: Sifting also provides an opportunity to incorporate quality control measures, ensuring the powder meets industry standards.
Effective formulation techniques are the backbone of successful powder coating applications. Without attention to blending, extrusion, and grinding, achieving the desired finish becomes a matter of luck, rather than skill or science.
Application Methods
Application methods represent a crucial aspect of the powder coating process, acting as the bridge between formulation and the final aesthetic and performance characteristics of the coated surfaces. Utilizing the right method can optimize the adhesion, coverage, and ultimately, the durability of the coating. Furthermore, these methods are not merely about application; they are also intertwined with factors such as material efficiency, energy consumption, and the overall quality of the finished product. Different techniques offer unique benefits and spell out distinct operational considerations that influence a wide range of industries, from automotive to appliance manufacturing.
Electrostatic Spraying
Electrostatic spraying is one of the most widely adopted methods for applying powder coatings. This technique takes advantage of the principles of electrostatics, where the powder particles are given a charge while the substrate is grounded. The charged particles are then drawn toward the substrate, ensuring an even and thorough coating. This method stands out for several reasons:
- Efficiency in Material Use: Electrostatic spraying minimizes overspray, allowing for greater transfer efficiency. This means that more of the powder reaches the surface, reducing waste.
- Versatility: It can be used for a diverse range of shapes and sizes, making it favorable for intricate parts where every nook and cranny needs coverage.
- Quality of Finish: The technique results in a smooth, even finish that is generally free from imperfections, which is vital for both aesthetic and functional aspects.
Nevertheless, while electrostatic spraying has its upsides, operators need to be mindful of humidity and temperature, as extreme conditions can affect the powder's properties and the overall quality of the application.
Fluidized Bed Coating
Fluidized bed coating provides a different approach where powdered coating materials are suspended in the air by a flow of gas, creating a bed that behaves like a liquid. This method involves heating the substrate before immersion into the fluidized powder bed, which allows the powder to adhere effectively as it melts and forms a coating. Key aspects of fluidized bed coating include:
- Uniform Thickness: It provides consistent coating thickness, which is especially important for heavy industrial parts that require robust finishes.
- Complex Shapes: This method is advantageous for complex geometries, as the fluidized bed can envelop all surfaces uniformly.
- Reduced Need for Overspray Controls: Because of how it works, there's less need for extensive overspray management systems, which can save both time and cost.
However, operators must be cautious about the temperature control; if too high, it can lead to excessive melting and dripping.
Tribostatic Techniques
Tribostatic techniques employ the principle of friction to enhance the adhesion of powder coatings. In this method, both the substrate and the powder particles are electrically charged through frictional contact. As a result, the powder is propelled toward the substrate and sticks more effectively. Tribostatic techniques are appreciated for several reasons:
- High Transfer Efficiency: Similar to electrostatic spraying, tribostatic methods provide high coating efficiency, reducing waste and improving material yield.
- Adaptability to Different Powder Types: This method can be used with various kinds of powders, including those that are challenging to apply with other techniques.
- Effective for Small Particles: Smaller powder particles gain charge more readily, which can enhance application for specific projects.
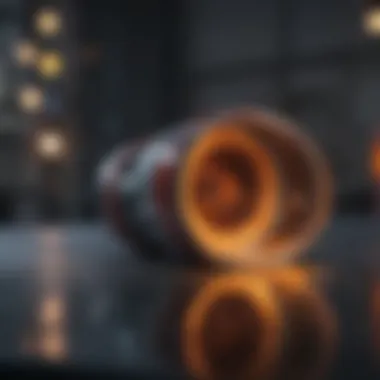
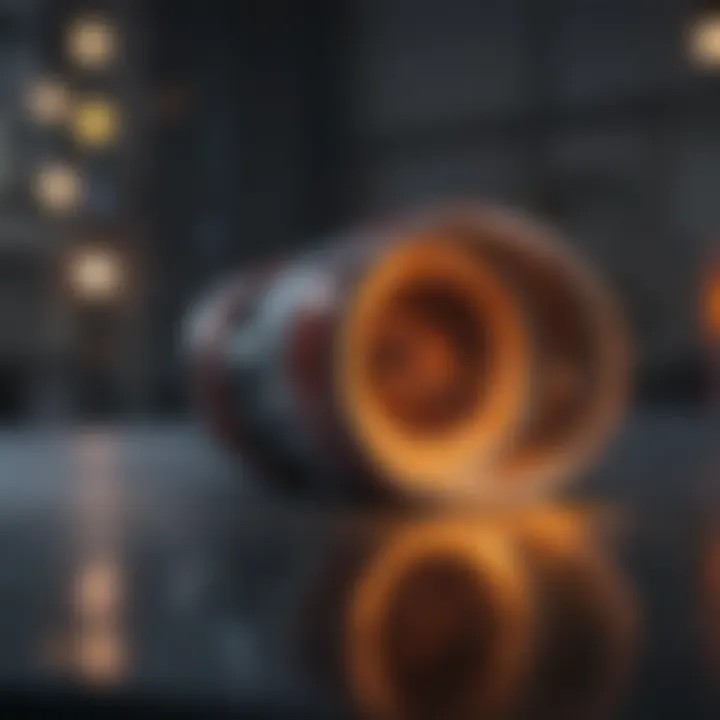
On the flip side, training and proper technique are essential for achieving optimal results, especially because this method relies heavily on the operator's skill and understanding of the materials involved.
"Understanding these application techniques not only sheds light on how coatings are applied but also highlights the intricacies of ensuring a high-performance finish that meets industry standards."
In summary, the choice of application method significantly influences the final quality and functionality of powder-coated items. Each technique has its merits and challenges, making it essential for professionals to match the method with the specific requirements of their projects.
Curing Process
The curing process is vital in powder coating, acting as a definitive step that transforms a coated object from a mere application of powder into a fully functional, durable finish. Understanding the nuances of this process is essential for anyone working in the field or studying the technology. Curing not only ensures the coating adheres effectively but also enhances its long-term performance and aesthetic qualities.
Role of Temperature
Temperature plays a pivotal role in the curing process. Each type of powder coating comes with its own specified temperature range that must be adhered to for optimal results. When the coated piece is heated, the powder melts and flows, allowing it to form a continuous film. Typically, temperatures can range between 350°F to 400°F (about 180°C to 200°C), depending on the material.
Higher temperatures tend to accelerate the curing reaction, resulting in a harder and more resistant finish. However, pushing temperatures too high may lead to undesirable effects, such as degradation of the coating or distortion of the substrate material. Hence, it's crucial to balance the temperature to achieve a robust finish without compromising the integrity of either the coating or the base material.
"If the heat's too high, it might turn into a hot mess. Yet, if it's too low, it’ll just sit there, lacking the necessary cure to perform well."
Curing Time Considerations
Alongside temperature, curing time is another critical aspect. Generally, the duration of curing varies based on many factors, including the powder type, the thickness of the coating, and the material being coated. A common guideline might dictate a range of 10 to 30 minutes at the specified temperature, but it’s not a one-size-fits-all rule.
Various applications may require different durations. For instance, thicker coats need more time to cure completely as the heat penetrates the layers. Additionally, some formulations might have specific instructions for extended curing times to achieve particular performance metrics, like enhanced chemical resistance.
Factors affecting curing time do not end there; humidity and air flow in the curing oven can also play a role. More humid conditions can sometimes extend the time needed for the process to complete effectively. Thus, knowing your materials and their requirements is paramount in fine-tuning the curing time.
Oven Types and Their Impact
The type of oven used for curing can also significantly influence the outcome of the powder coating. Several designs exist, including convection ovens, infrared ovens, and combination ovens, each with its advantages and nuances.
- Convection Ovens: These ovens use heated air to transfer heat to the coated object. They ensure an even temperature throughout the chamber, which is crucial for uniform curing. This is particularly vital for complex shapes where heat might not penetrate evenly.
- Infrared Ovens: Using infrared radiation to heat the surface of the coating, these ovens can provide faster and more concentrated heating. It can be beneficial for thin coatings or when time efficiency is critical. However, there’s a risk of uneven curing if not monitored closely.
- Combination Ovens: By integrating both convection and infrared heating, these ovens aim to capitalize on the benefits of each method, offering robust performance for a range of applications.
In summary, the impact of curing processes lies at the intersection of temperature management, appropriate timing, and the right oven selection. Each decision in this phase dictates not just the immediate quality of the finish but also the longevity and functionality of the coated item. By mastering the art of curing, one can unlock the true potential of powder coating technology.
Performance Metrics
In the world of powder coating, performance metrics are essential parameters that determine the effectiveness and applicability of the coating. These metrics gauge how well the coating performs under different conditions, influencing everything from manufacturing choices to customer satisfaction. By focusing on aspects like adhesion strength, durability, resistance, and aesthetic qualities, industry professionals can articulate the value of their products and make educated decisions in formulation and application. Not to mention, high-performance coatings often translate to competitive advantage in market scenarios. As the saying goes, "you can't manage what you don’t measure." Hence, understanding and applying these metrics equips stakeholders with tools that not only enhance quality but also meet regulatory standards.
Adhesion Strength
Adhesion strength is arguably the cornerstone of any successful coating, including powder coatings. This characteristic reflects how well a coating sticks to a substrate. A high adhesion strength minimizes the likelihood of peeling or blistering over time, thereby extending the lifespan of the coated surface. Factors influencing adhesion strength consist of surface preparation, the nature of the substrate, and the chemical composition of the powder itself.
For example, imagine coating a metal component that hasn't been properly prepped; the surface may have dirt, oxidation, or other contaminants that can create a barrier, affecting adhesion. Worse yet, if an inferior quality powder is chosen, it may simply not bond effectively. Adhesion tests are routinely conducted to measure this strength, ensuring that it meets or exceeds industry standards, usually expressed in units like psi (pounds per square inch).
Durability and Resistance
Durability and resistance denote how well the powder coating can withstand environmental stresses and everyday wear and tear. A good powder coating should resist fading, cracking, and chipping, which are essential for both aesthetics and functionality.
Chemically, coatings are often formulated with different resins and additives to enhance these qualities. For instance, epoxy resins are known for their robust adhesive properties and superior chemical resistance, making them perfect for industrial applications. On the flip side, polyester resins offer better UV stability, making them suitable for outdoor applications. Manufacturers have to strike a balance to tailor durability characteristics that meet specific end-use expectations.
To ensure that a product meets durability requirements, various testing methodologies are employed. These can include weathering tests, salt spray tests for corrosion, or even abrasion resistance testing. By employing such protocols, manufacturers ensure that their products don't just look good on the surface but also stand the test of time.
Aesthetic Qualities
While performance is crucial, a coating also requires aesthetic qualities that appeal to consumers. Aesthetic qualities include color, gloss, texture, and finish. The Color can play a significant role in attracting customers, while the gloss affects how light interacts with the coated surface.
For instance, matte finishes can give a contemporary look to certain machinery, whereas high-gloss coatings may lend a shiny and polished touch to automotive parts. The texture can range from smooth to rough, impacting both visual appeal and functionality, since some textures can also hide surface imperfections.
Aesthetic quality is closely interlinked with performance metrics as well. For example, a color that fades quickly under sunlight is not just an aesthetic failure; it also signals that the durability of the coating may not be up to par. Therefore, industry players must ensure that aesthetic choices align with performance metrics, enriching the product's appeal without compromising on essential qualities.
"When it comes to performance metrics, marrying aesthetics with durability is akin to finding the harmony between art and engineering."
A meticulous approach to assessing these performance metrics allows businesses to constantly evolve and refine their powder coating formulations, paving the way for enhanced products that meet consumer demands and industry standards.
Environmental Considerations
The realm of powder coating operations can no longer afford to sidestep the broader implications of their activities on the environment. As concerns about sustainability continue to seep into public consciousness, industries are increasingly held accountable for their environmental footprint. In powder coating, focusing on sustainable practices not only aligns with regulatory compliance but also enhances brand value and customer loyalty. It’s an intricate dance—balancing efficiency, quality, and ecological responsibility.
"Engaging in eco-friendly practices does more than just comply with regulations; it can drive innovation and open up new markets."
Sustainable Practices in Powder Coating
Modern powder coating practices are incorporating sustainability at their core, recognizing that ecological responsibility and business viability can go hand in hand. A few key strategies in this domain include:
- Recycling Overspray: Unlike traditional liquid paints, where excess material often becomes waste, the electrostatic nature of powder coating allows for the collection and reuse of overspray. This dramatically reduces material waste, which is a win-win for both the environment and cost management.
- Low-VOC Formulations: Many powders are now designed with lower volatile organic compounds (VOCs), which contribute to air pollution. Companies like Aegis Coating Solutions have developed specialized formulations that minimize these emissions while maintaining performance metrics.
- Energy-Efficient Curing Systems: As curing is a significant part of the powder coating process, investing in energy-efficient ovens can have substantial environmental benefits. Systems equipped with advanced technologies, such as infrared heating, can decrease energy consumption at significant scales.
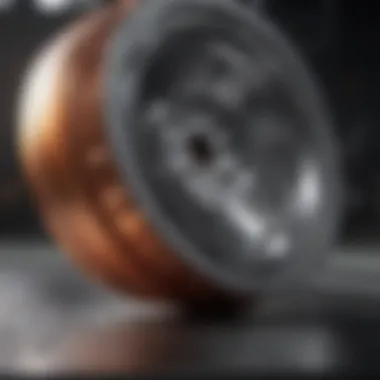
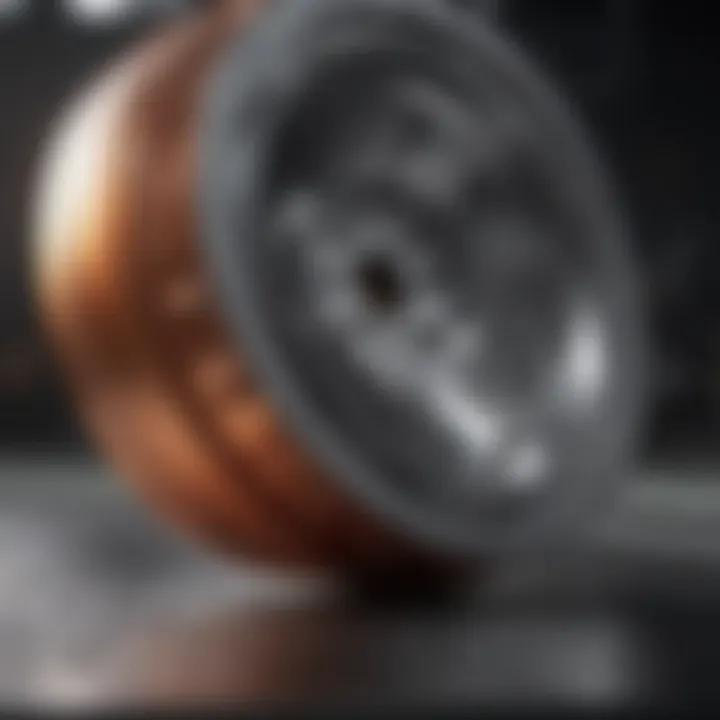
By employing these practices, companies are turning the spotlight on their operational methods, demonstrating that going green may not be just an ethical choice but also a pragmatic one that enhances their competitive edge.
Regulatory Compliance
Regulatory compliance serves as a guiding light for environmental considerations in powder coating. In many regions, powder coating operations are subject to regulations that aim to limit environmental damage. Compliance isn’t simply a matter of ticking boxes; it requires staying abreast of evolving legislation that can impact operational protocols. Understanding and adopting regulatory frameworks can offer several benefits:
- Reduction of Fines: Non-compliance can lead to significant fines and repercussions that burden a company financially and reputationally. Staying updated helps mitigate these costs.
- Marketability: Being compliant can also offer a unique selling proposition. Customers are often more inclined to engage with companies that showcase their commitment to environmental stewardship.
- Innovation: Embracing regulatory challenges can spark innovation. Companies often find new solutions or practices that not only meet compliance but also elevate their product offerings.
In summary, awareness of the ecological implications and regulatory landscape is paramount in the powder coating industry. A conscientious approach not only preserves our environment but also ensures long-term viability and progress in the industry.
Innovations and Trends
Innovations in powder coating formulation represent a dynamic intersection of technology, environmental awareness, and market demands. As industries evolve, the need for advanced surface finishing solutions becomes paramount. Staying abreast of new developments in this field can lead to improved product performance, cost efficiencies, and environmental sustainability—factors that increasingly influence purchasing decisions.
In this section, we will explore two significant aspects of this topic: new formulation technologies and emerging market applications. These insights will help professionals grasp the shifting landscape of powder coating and its ever-growing relevance in various industries.
New Formulation Technologies
The advent of novel formulation technologies in powder coating opens up a world of improved performance and versatility. Companies are now looking to harness cutting-edge methods to enhance their products, making them not only more durable but also more adaptable to specific requirements.
For example, the development of hybrid powder coatings merges multiple formulations to bring forth coatings that exhibit enhanced mechanical properties and resist degradation better than traditional options. These hybrid formulations are particularly useful in applications where materials must endure harsh environments, such as automotive or aerospace parts.
Another noteworthy trend involves low-temperature curing technologies. These formulations allow coatings to cure at lower temperatures, significantly reducing energy consumption during the curing process. This is not just a win for the environment but also for manufacturers looking to streamline operations and cut costs.
Benefits of New Formulation Technologies:
- Enhanced Durability: New materials resist wear and tear more effectively.
- Lower Energy Usage: Technologies like low-temperature curing trim down energy consumption.
- Customization Potential: Hybrid formulations facilitate tailored solutions to meet distinct needs.
Emerging Market Applications
Emerging applications of powder coating signify not just a trend but a fundamental shift in how industries utilize coatings. As sectors diversify and innovate, they provide further avenues for powder coating materials to shine.
- Architectural Coating: Contemporary architecture often emphasizes aesthetic appeal alongside functionality. Powder coatings can now be customized to provide a wide range of textures, colors, and finishes that enhance the building's visual impact while offering protection against environmental elements.
- Electronics Coating: With electronic devices becoming increasingly compact and powerful, powder coatings are finding a niche in electronics. Coatings that provide electrical insulation as well as thermal resistance are being actively developed to protect delicate components from various operational hazards.
- Furniture Finishing: The furniture industry has embraced powder coating for its ability to deliver vibrant, long-lasting finishes. New formulations are being designed to withstand scratches, stains, and fading, making them ideal for both indoor and outdoor furniture.
The evolution of powder coating applications demonstrates its versatility and adaptability, ensuring long-term relevance in numerous industries.
Key Emerging Markets:
- Automotive: New formulations designed for scratch resistance and appeal.
- Aerospace: The need for high-performance materials.
- Consumer Goods: A push for more durable and aesthetically pleasing finishes.
In summary, the realm of innovations and trends in powder coating formulations encompasses a variety of advancements that promise improved performance and broader application possibilities. Staying updated with these trends is crucial for professionals seeking to leverage new opportunities and stay competitive in an ever-evolving market.
Challenges in Powder Coating
Understanding the challenges faced in powder coating is crucial, especially as industries continue to seek more efficient and sustainable finishing methods. This section takes a close look at two significant issues: quality control and cost-effectiveness. Addressing these challenges not only affects the final product but also influences overall operational efficiency.
Quality Control Issues
Quality control is the backbone of any production process, and powder coating is no exception. Inconsistent quality can lead to problems that go beyond aesthetics. Several factors contribute to quality control issues within powder coating formulations:
- Material Variation: Variability in raw materials can significantly impact the final product. When resins or pigments are sourced from different suppliers, inconsistencies may arise. This inconsistency can cause differences in appearance and performance, leading to increased waste and operational bottlenecks.
- Environmental Factors: Factors such as humidity and temperature play a vital role during the application process. Fluctuations in these environmental conditions can affect adhesion and curing. For instance, if the coating is applied on a humid day, the moisture can interfere with the adhesion, leading to defects.
- Equipment Calibration: Failing to maintain and calibrate application equipment leads to uneven powder distribution, resulting in areas that are either overcoated or undercoated. An extensive quality control process must be established to minimize these risks.
Proper techniques for quality assurance should include routine inspections, systematic testing of batches, and strict adherence to specifications during production. By implementing a robust quality control framework, manufacturers can mitigate issues before they arise, improving both performance metrics and customer satisfaction.
"Effective quality control in powder coating processes is not just a best practice; it's a necessary component for long-term success."
Cost-Effectiveness Concerns
Every industry is always looking at bottom lines. In powder coating, delivering a quality product at competitive prices challenges many manufacturers. Cost-effectiveness plays a pivotal role in determining the choice between powder coating and other finishing methods, like liquid coatings. Here are a few aspects where costs come into play:
- Initial Investment: Setting up a powder coating system can be costly. The purchase of application equipment, curing ovens, and the space required for operation can be high initial hurdles for smaller businesses. This might push some to opt for cheaper alternatives, despite powdered coating's superior advantages in durability and finish.
- Material Efficiency: While powder coating is generally more efficient in terms of material usage than liquid painting, improper application techniques can lead to overspray waste. This not only leads to increased material costs but also necessitates additional processing steps to reclaim that powder, which could increase operational costs.
- Long-Term Benefits vs. Short-Term Gains: While powder coatings may necessitate a higher initial investment, they are durable and resistant to corrosion and scratches, translating to lower costs in repairs and replacements over time. Evaluating the balance between initial costs and long-term benefits is critical to achieving cost-effectiveness.
Closure
The conclusion serves as a critical linchpin in our exploration of powder coating formulation. It encapsulates the critical insights gleaned throughout this discourse, tying together threads from the various aspects we've examined. Understanding these formulations offers a profound appreciation not only for the science behind them but also for their tangible impact across multiple industries.
Recap of Key Insights
In revisiting the key insights, it's vital to highlight several essential elements:
- Chemical Components: From resins to pigments, each ingredient plays a specific role that affects both the application process and the durability of the final product.
- Application Techniques: The methods used to apply powder coatings significantly determine the efficiency and effectiveness of the coating process. Techniques such as electrostatic spraying and fluidized bed coating lend themselves to varied applications, catering to different needs and environments.
- Curing Process: Understanding the nuances of temperature and time in the cure process underscores the importance of these factors in achieving the desired coating characteristics.
- Performance Metrics: Metrics such as adhesion strength and durability are paramount in assessing the success of a powder coating application, influencing everything from customer satisfaction to regulatory compliance.
Each of these points interlinks, aiding professionals in making informed decisions about powder coating applications, and highlighting how critical it is to grasp the intricacies involved in formulation.
Future Directions
As we look ahead, several future directions are noteworthy for the field of powder coating:
- Innovation in Formulation Technologies: There's a noticeable trend towards developing more sophisticated formulation technologies that enhance performance and reduce environmental impact. This could include bio-based resins and zero-VOC (volatile organic compounds) formulations.
- Emerging Market Applications: Industries such as automotive and aerospace are increasingly looking for advanced coating solutions that provide not only aesthetic appeal but also superior durability under various conditions.
- Sustainable Practices: As environmental regulations become more stringent, the industry is facing pressure to adopt more sustainable practices. Future formulations could focus on recyclability and reduced energy consumption during application and curing.
"The future is not something we enter. The future is something we create."
In aligning with this sentiment, industry professionals must actively engage with the latest advances in powder coating formulations, ensuring they remain at the forefront of coating technology.