Understanding Inventory in Supply Chain Management
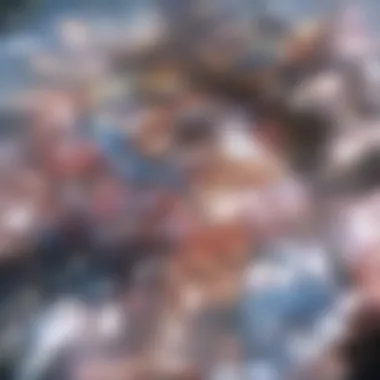
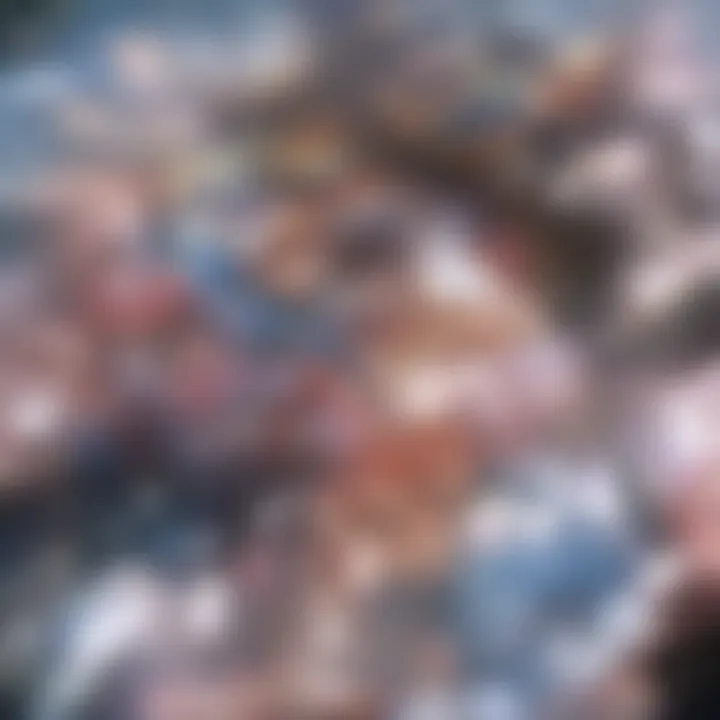
Intro
Inventory is a critical component in the realm of supply chain management. It serves as a bridge between production and consumption, ensuring that products are available when and where they are needed. Understanding inventory involves grasping its definitions, types, and underlying principles that influence supply chain operations.
The efficient management of inventory not only affects operational processes but also has significant implications for customer satisfaction and overall business performance. Successful inventory practices are essential for forecasting demand accurately and planning supply accordingly. This article delves deeply into various aspects of inventory within supply chain management, highlighting key concepts, challenges, and strategies that organizations can adopt to enhance their efficiency.
Key Concepts
Definition of Primary Terms
Inventory typically refers to the stock of goods and materials a company holds for the purpose of resale. This includes finished products, work in progress, and raw materials. Within supply chain management, several core terms are essential to understand:
- Lead Time: The time taken from placing an order until it is received and ready for use.
- Safety Stock: Extra inventory held to prevent stockouts caused by unforeseen demand changes or supply disruptions.
- Turnover Rate: A measure of how quickly inventory is sold and replaced over a period, indicating efficiency in inventory management.
Understanding these terms helps stakeholders analyze their inventory management practices effectively.
Related Concepts and Theories
Several concepts underpin the effective management of inventory in supply chains:
- Just-in-Time (JIT): An inventory strategy that aligns purchases with production schedules to minimize inventory costs.
- Economic Order Quantity (EOQ): A formula used to determine the optimal order quantity that minimizes total inventory costs, including ordering and holding costs.
- ABC Analysis: A method of categorizing inventory based on importance, with A items being the most valuable and C items the least.
These theories are instrumental in guiding organizations in their inventory strategies, helping to balance costs against customer service levels.
"Effective inventory management ensures that the right products are available at the right time, contributing significantly to customer satisfaction."
Future Directions
Gaps Identified in Current Research
Despite advancements in inventory management techniques, several gaps remain in research:
- The integration of artificial intelligence in predicting demand remains underexplored.
- There is limited understanding of how emerging technologies impact traditional inventory practices.
Suggestions for Further Studies
Future research can focus on:
- The role of big data and analytics in enhancing inventory accuracy and efficiency.
- Exploring the impact of economic fluctuations on inventory carrying costs and strategies.
By addressing these gaps, organizations can refine their inventory management approaches, aligning them more closely with modern supply chain dynamics.
Prelims to Inventory in Supply Chain Management
In today's business landscape, inventory management is a critical element of supply chain management. Understanding how inventory operates within this framework can significantly enhance operational efficiency. The management of inventory is not just about storing goods; it involves strategic planning and execution that impacts the entire supply chain.
Effective inventory management contributes to meeting customer demands promptly while minimizing holding costs. It requires balancing a delicate equation: having enough stock to satisfy demand without excess that ties up capital. This balance is crucial not only for profitability but also for maintaining competitiveness in the market.
Moreover, inventory's role stretches beyond simple storage. It acts as a buffer against uncertainties in both supply and demand, allowing companies to adapt to fluctuations. For instance, during peak seasons, adequate inventory can ensure sales opportunities are not lost due to stockouts. Conversely, in lean times, agility in adjusting inventory levels is vital.
"Effective inventory management can mean the difference between thriving and merely surviving for many businesses."
With these dynamics in mind, it is essential to explore the components of inventory in detail. This article will break down inventory definitions, objectives, different types, and their significant impact on overall supply chain performance. Adequate comprehension of these elements enables organizations to deploy effective strategies that optimize inventory and, in turn, enhance supply chain success.
Defining Inventory in the Supply Chain Context
Inventory refers to the goods and materials a business holds for the purpose of resale, manufacturing, or other operational needs. In the context of supply chain management, inventory serves multiple functions. It can include raw materials, work-in-progress items, and finished goods. Each category plays a unique role in the production process and overall supply chain efficiency.
Understanding inventory requires acknowledging it as a critical asset for businesses. Having the right amount of inventory at the right time can leverage production capacities, meet customer expectations, and maintain a smooth flow of goods through the supply chain.
The Objectives of Inventory Management
The primary objectives of inventory management include:
- Maintaining Optimal Inventory Levels: This objective focuses on ensuring that the stock aligns with customer demand and production requirements without creating excess.
- Reducing Holding Costs: Holding inventory incurs costs such as storage, insurance, and depreciation. Effective management aims to keep these costs in check.
- Enhancing Service Levels: Inventory management aims to provide customers with timely access to products, thus improving satisfaction and loyalty.
- Facilitating Production Planning: By ensuring raw materials and components are available when needed, companies can streamline their manufacturing processes.
Effectively pursuing these objectives not only safeguards a company’s financial health but also strengthens its reputation within the marketplace.
Types of Inventory
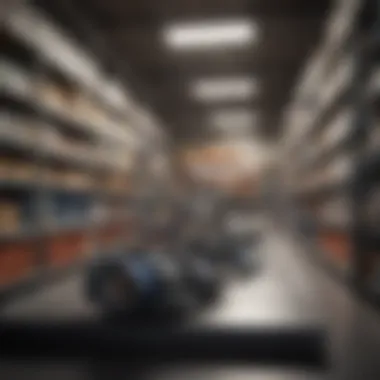
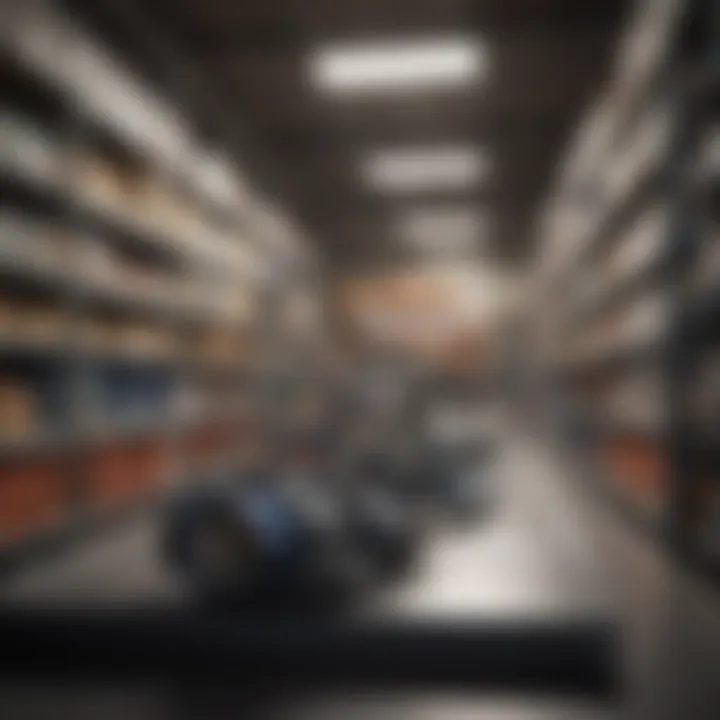
In supply chain management, understanding the various types of inventory is essential. Each category serves a distinct purpose and plays a critical role in the overall operational efficiency. Knowing these types helps organizations in their inventory planning strategies and assists in maintaining optimal levels.
Raw Materials Inventory
Raw materials inventory refers to the basic materials that a company uses to produce its goods. For manufacturers, this is the starting point of the production process. Managing raw materials effectively ensures that production can proceed without unnecessary delays.
Having an adequate supply of raw materials is important but keeping excess inventory can lead to higher holding costs. These costs include storage, insurance, and potential obsolescence. Thus, companies must balance their need for sufficient raw materials with the costs associated with holding them.
Work-in-Progress Inventory
Work-in-progress (WIP) inventory consists of items that are in the process of being manufactured but are not yet completed. This type of inventory includes materials that have been released for production but still need assembly or further processing.
WIP inventory helps to measure production efficiency. High WIP levels can indicate a bottleneck in the production process, signaling that improvements are needed. Therefore, managing this type effectively can lead to smoother operations and can help identify areas needing attention.
Finished Goods Inventory
Finished goods inventory comprises products that are fully manufactured and ready for sale. This inventory type is crucial for meeting customer demand. Companies must ensure that they have enough finished goods to satisfy orders while avoiding overproduction.
Optimizing finished goods inventory requires understanding the market demand and maintaining a flexible production schedule. A proper balance ensures that customers receive their products in a timely manner while minimizing excess stock that can tie up resources.
Maintenance, Repair, and Operations Inventory
Maintenance, Repair, and Operations (MRO) inventory includes items that support the production process but do not become part of the final product. This can involve tools, spare parts, and office supplies necessary for smooth operations.
While often overlooked, MRO inventory is essential for maintaining equipment and ensuring continuous production flow. Having the right MRO items on hand can prevent costly downtime and keep operations running efficiently. Organizations should regularly assess their MRO inventory to avoid shortages that might impact their overall productivity.
Effective inventory management involves recognizing the different types of inventory and strategizing accordingly. Each type presents unique challenges and opportunities that must be understood for optimal supply chain performance.
The Role of Inventory in Operational Efficiency
Inventory plays a crucial role in operational efficiency within supply chain management. Effective inventory handling not only ensures that organizations meet customer demand on time but also aids in cost management. When managed properly, inventory can thin margins yet provide a buffer against uncertainty in supply and demand. Therefore, understanding this aspect is vital for both students and professionals in the field.
One of the primary benefits of inventory in operational efficiency is its ability to act as a buffer. This buffer is essentially a safety net that enables businesses to handle fluctuations in demand and supply. When a demand spike occurs, a well-kept inventory allows a company to satisfy customers without delays. Conversely, in instances of reduced demand, having an inventory prevents stockouts, which could lead to lost sales and customer dissatisfaction.
Inventory as a Buffer
Inventory serves as a barrier against uncertainties in the supply chain. For example, businesses often face unpredictable changes, such as sudden spikes in customer demand or disruptions in production due to supply issues. In these scenarios, an adequate stock of products helps ensure that a business continues to operate smoothly.
This buffer function can be categorized into several types:
- Decoupling Inventory: This is particularly useful in manufacturing. By keeping certain levels of stock available, production can run without interruption even if there are delays in receiving raw materials.
- Seasonal Inventory: Businesses in sectors that experience seasonal fluctuations can pre-stock items to meet peak demand periods efficiently.
However, it is essential to balance this buffer capacity with the associated costs. Excessive inventory ties up funds that can be better utilized elsewhere, and can also lead to waste or obsolescence.
"Good inventory management leads to improved service levels and increased customer satisfaction, which are essential for long-term success in business."
Inventory and Supply Chain Resilience
The relationship between inventory and supply chain resilience is significant. Resilience refers to the ability of an organization to adapt to changes while maintaining operational continuity. An effective inventory strategy enhances this resilience. Companies can navigate disruptions more smoothly by maintaining various inventory types: raw materials, work-in-progress, and finished goods.
Having diverse inventory can allow organizations to respond effectively to varying market conditions. For instance, during unexpected economic downturns or crises, businesses with robust inventory systems are better equipped to handle reduced production capabilities or fluctuating customer needs.
Some key considerations for building resilience through inventory management include:
- Diversification of Suppliers: Having multiple sources for raw materials mitigates risks associated with supplier reliance.
- Flexible Inventory Practices: Organizations that adopt flexible inventory techniques, such as Just-in-Time, can respond quickly to changing market demands.
- Enhanced Visibility: Using technology such as real-time data analytics helps businesses monitor inventory levels and demand signals, thus improving decision-making.
Demand Forecasting and Inventory Planning
Demand forecasting and inventory planning are critical aspects of effective supply chain management. The ability to predict future demand accurately enables businesses to align their inventory levels with customer requirements. This alignment reduces not فقط the risk of overstocking, but also minimizes stockouts, which can harm customer satisfaction. When executed well, demand forecasting leads to optimized inventory levels, ensuring that a company can meet its operational needs while maintaining cost efficiency.
Utilizing Historical Data
Historical data serves as a foundational tool in demand forecasting. By analyzing sales patterns from past periods, businesses can identify trends and seasonality. This process involves collecting and analyzing various datasets, such as sales figures, inventory levels, and market conditions. Through this analysis, predictive models can be developed to forecast future demand.
Benefits of Utilizing Historical Data:
- Trend Analysis: Helps identify recurring patterns in demand over time.
- Seasonal Adjustments: Allows for adjustments based on known seasonal impacts, which can significantly affect sales.
- Enhanced Accuracy: Provides a data-driven approach, leading to increased accuracy in forecasting.
It is essential to note that while historical data is invaluable, it should not be the sole basis for forecasting. Market conditions are dynamic, and reliance solely on past data can lead to inaccuracies if not supplemented with other forecasting methods.
The Importance of Real-Time Data
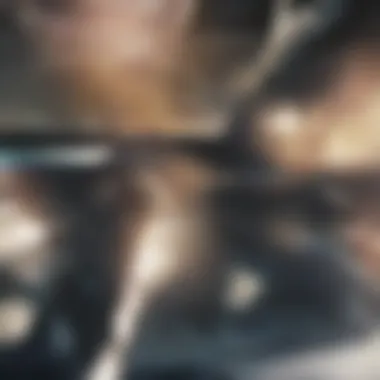
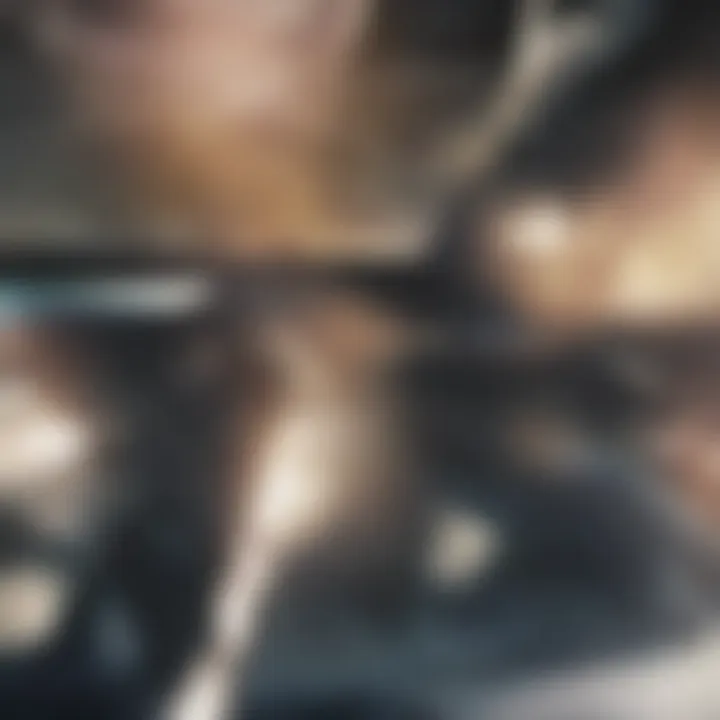
Real-time data introduces a layer of responsiveness in inventory planning that historical data alone cannot provide. In a rapidly changing market environment, being able to monitor demand in real-time enables companies to react swiftly to fluctuations. This is particularly vital for industries with volatile demand, such as retail and e-commerce.
Key Aspects of Real-Time Data Utilization:
- Immediate Response: Allows companies to adjust inventory levels dynamically based on current sales data.
- Reduced Lead Times: Helps in decreasing the time it takes to replenish stock.
- Improved Decision-Making: Gives managers access to up-to-date information, facilitating informed strategic decisions.
Companies that integrate real-time data tools, such as inventory management systems, can achieve a competitive advantage. Employing such systems allows for continuous monitoring of stock levels, sales trends, and supply chain disruptions, enhancing the overall efficiency of inventory management.
The integration of both historical and real-time data can lead to a more comprehensive outlook on future demand, thus aligning inventory levels more closely with market needs.
Inventory Management Techniques
Inventory management techniques are essential to efficient supply chain management. These techniques help businesses maintain the right level of inventory to meet customer demand without incurring excessive costs. When executed effectively, these strategies enhance operational efficiency, reduce waste, and improve customer satisfaction. In this section, we will explore three critical inventory management techniques: Just-in-Time (JIT) Inventory System, ABC Analysis, and Economic Order Quantity (EOQ).
Just-in-Time (JIT) Inventory System
The Just-in-Time (JIT) inventory system minimizes the amount of inventory on hand at any given time. This technique aims to synchronize production schedules with demand, ensuring that materials arrive just as they are needed in the production process. JIT reduces the carrying costs associated with holding large inventories and mitigates the risk of obsolescence.
The benefits of JIT include:
- Reduced Inventory Costs: Holding less inventory results in lower storage costs.
- Increased Efficiency: Production processes can be streamlined, reducing waste.
- Improved Cash Flow: Companies can allocate resources more effectively, using funds elsewhere.
However, JIT also presents challenges. It requires a high level of coordination with suppliers and can create vulnerability to supply chain disruptions.
ABC Analysis
ABC Analysis is a technique that categorizes inventory items based on their importance to the overall business operation. It often divides items into three categories:
- A items: High-value items with a low frequency of sales. These require tight control and accurate forecasting.
- B items: Moderate value with moderate sales frequency. Management is important, but not as stringent as A items.
- C items: Low-value items with a high frequency of sales. These items require the least control and management effort.
Implementing ABC Analysis allows companies to focus resources and efforts on managing the most critical items. This methodology provides insights on:
- Inventory Prioritization: Ensures that essential products are sufficiently stocked.
- Resource Allocation: Directs management attention based on the impact on revenue.
Economic Order Quantity (EOQ)
The Economic Order Quantity (EOQ) model determines the optimal order quantity that minimizes total inventory costs. These costs include ordering costs, holding costs, and stockout costs. By calculating EOQ, companies can achieve a balance that reduces the total cost of inventory management.
The formula for EOQ is:
Where:
- D is the demand rate (units per year)
- S is the ordering cost per order
- H is the holding cost per unit per year
The significance of using EOQ is:
- Cost Reduction: Helps avoid excessive order frequency, lowering overall costs.
- Operational Efficiency: Coordinates ordering and inventory levels for optimal management.
Effective inventory management is a significant contributor to operational success and customer contentment.
Technology in Inventory Management
In the evolving landscape of supply chain management, technology plays a pivotal role in inventory management. Leveraging the right tools not only streamlines operations but also enhances accuracy and efficiency. Businesses across various sectors are discovering that incorporating technology into their inventory processes can reduce costs and improve service levels. The benefits are substantial, as detailed below.
The Role of Inventory Management Software
Inventory management software serves as the backbone of modern inventory systems. It enables companies to keep a real-time track of stock levels, orders, sales, and deliveries. The precision and speed of data updates allow for prompt decision-making. Among its key features are:
- Real-time Monitoring: Businesses can monitor stock levels accurately, avoiding both overstocking and stockouts. This capability supports better strategic planning.
- Data Analytics: Many software solutions offer analytical tools that provide insights into customer purchasing behaviors, which in turn help refine inventory levels and order quantities.
- Integration: Quality inventory management software can integrate seamlessly with other systems, such as accounting software, CRM systems, and e-commerce platforms, creating a cohesive operational framework.
The choice of software depends on specific needs, such as whether a company requires cloud-based solutions or on-premise installations. Popular options include Fishbowl, TradeGecko, and Brightpearl, each offering unique functionalities tailored to distinct business needs.
Artificial Intelligence in Inventory Optimization
Artificial intelligence (AI) represents a groundbreaking shift in inventory optimization. By analyzing vast amounts of data quickly, AI helps organizations predict demand more accurately and optimize stock levels.
The potential advantages include:
- Enhanced Forecasting: AI algorithms can analyze historical sales data, market trends, and external factors, generating forecasts that are far superior to traditional methods.
- Dynamic Reordering: AI systems can automate reorder processes based on real-time data. This reduces human error and ensures that stock levels are maintained efficiently.
- Cost Reduction: By minimizing excess inventory and decreasing the likelihood of stockouts, AI leads to significant cost savings. This is crucial for maintaining competitive pricing and maximizing profitability.
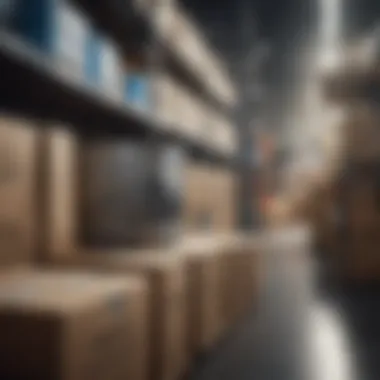
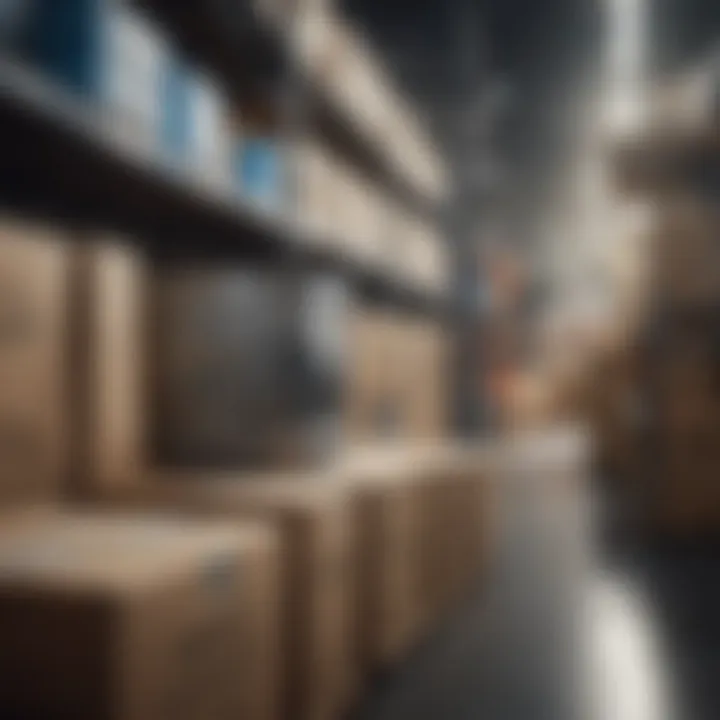
As companies embrace AI technologies, they unlock opportunities for greater efficiency and improved customer satisfaction. Businesses that seek to thrive must adapt to advancements like AI and sophisticated inventory management software, enabling them to stay ahead in a competitive market.
"Incorporating technology in inventory management is not merely an option, but a necessity for businesses striving for operational excellence."
Equipped with these technologies, organizations can approach inventory management with a more strategic mindset, ensuring that they meet customer expectations while optimizing operational performance.
The Impact of Inventory on Customer Satisfaction
Inventory management has a crucial impact on customer satisfaction. How well a company manages its inventory can directly influence its ability to meet customer demands. This section explores several key elements involved in this relationship, highlighting why maintaining an efficient inventory system is vital for businesses today.
One significant factor is stock availability. When products are readily accessible, customers feel valued and are more likely to complete a purchase. Low stock availability can result in frustration and dissatisfaction, leading to lost sales and potential long-term damage to a brand's reputation. It has been shown that when items are out of stock, many consumers will shift their purchase to competitors. Thus, businesses need to prioritize inventory management to ensure that they are prepared for customer demand at all times.
Additionally, effective inventory management can enhance the customer experience. This goes beyond simply having products in stock; it also involves the speed and accuracy of order fulfillment. Streamlined processes can ensure that customers receive their orders on time. According to studies, timely delivery boosts customer trust and loyalty. Therefore, companies must focus on improving their inventory and logistics processes to meet these expectations effectively.
"Efficient inventory management acts as a safeguard against customer disappointment and enhances the purchasing experience."
Stock Availability and Customer Experience
The concept of stock availability is fundamental in determining customer satisfaction. It refers to the readiness of products for sale when consumers are ready to buy. Insufficient stock can lead to a negative impression of a business. For instance, if a customer frequently finds that their desired item is out of stock, they might choose to shop elsewhere.
Some benefits of maintaining good stock availability include:
- Increased Sales: A consistent presence of products encourages purchases.
- Customer Retention: Satisfied customers are likely to return for future purchases.
- Market Competitiveness: Businesses that provide better availability can outperform their rivals.
Rather than relying solely on historical sales data, companies can use modern technology to project demand and adjust inventory levels proactively.
Inventory Turnover Ratio and Its Significance
Inventory turnover ratio is another critical component that affects customer satisfaction. This ratio measures how many times a company's inventory is sold and replaced in a specific period. A high ratio generally indicates efficient inventory management, suggesting that products are selling well and stock is refreshed regularly. Conversely, a low turnover ratio signals potential issues, such as overstocking or declining demand.
Understanding and managing this ratio is essential for several reasons:
- Resource Allocation: When turnover rates are high, resources can be allocated for restocking more efficiently.
- Cash Flow Management: High turnover leads to better cash flow, allowing businesses to invest in other areas.
- Customer Insights: Tracking turnover can provide insights into customer preferences, enabling better inventory decisions.
Challenges in Inventory Management
Inventory management is a critical element in supply chain operation. It shapes how businesses respond to demand fluctuations and manage resources efficiently. However, companies face multiple challenges in effectively managing their inventory. Understanding these challenges is essential for maintaining a competitive advantage and ensuring customer satisfaction.
One significant challenge is balancing the amount of inventory an organization holds. Companies must maintain enough stock to meet customer demand while avoiding excessive inventory that leads to higher carrying costs. This dual requirement makes inventory management a complex task. Effective strategies are necessary to reduce waste and streamline inventory processes.
Overstocking and its Consequences
Overstocking occurs when a business holds more inventory than needed. This situation often arises from inaccurate demand forecasting or a failure to respond quickly to market conditions. The consequences of overstocking can be severe.
- Increased Holding Costs: More inventory leads to higher storage costs. Businesses spend additional funds on warehousing, insurance, and management of excess stock.
- Decreased Cash Flow: Money tied up in surplus inventory cannot be used for other operational needs. This restriction can limit a business's ability to invest in growth opportunities.
- Risk of Obsolescence: Some products may become outdated or expire, especially in sectors like technology and food, leading to waste and loss of capital.
- Discounting Products: To clear excess stock, businesses may need to lower prices, thus diminishing their profit margins.
It is crucial for organizations to establish efficient inventory turnover strategies to mitigate overstocking.
Stockouts and Loss of Sales
On the flip side, stockouts occur when inventory levels drop below customer demand. This situation can be just as detrimental, if not more so, than overstocking. The implications of stockouts are significant:
- Lost Sales Opportunities: When customers cannot find the products they want, they often turn to competitors. This shift can lead to a permanent loss of customer loyalty.
- Damage to Brand Reputation: Frequent stockouts may convey unreliability to consumers, impacting the brand image negatively.
- Increased Operational Costs: The urgency of fulfilling backorders or rush orders can lead to increased shipping costs and strain resources.
- Inaccurate Demand Forecasting: Stockouts often stem from poor analytics. This oversight can perpetuate a cycle of inadequate supply and lost sales.
Ending
Inventory management serves a crucial role in the effective operation of supply chains. As outlined throughout this article, understanding inventory is essential for optimizing efficiency, enhancing customer satisfaction, and minimizing costs. The importance of managing inventory cannot be overstated; it is integral to the health of any supply chain. Proper inventory management ensures that companies can meet market demands without tying up excessive capital in unused stock. It also helps detect potential issues before they escalate, allowing businesses to adapt and respond swiftly.
Summarizing the Importance of Inventory Management
Inventory management is not just a function; it is a strategic advantage. Effective inventory practices allow companies to operate smoothly, ensuring product availability while maintaining cost-effectiveness.
- Balanced Stock Levels: Maintaining the right amount of inventory prevents overstocking, which can lead to obsolescence and increased storage costs. It also mitigates understocking, which can result in lost sales and disappointed customers.
- Informed Decision-Making: Through accurate tracking and analysis of inventory levels, businesses can make informed decisions regarding purchasing, sales forecasting, and production schedules. Using historical data, companies can tweak their approaches based on patterns and trends in customer demand.
- Operational Resilience: A strong inventory system enables an organization to respond quickly to unexpected disruptions. This flexibility creates a resilient operation that can withstand market volatility, supply chain interruptions, or changes in customer behavior.
In summary, businesses that prioritize inventory management can enhance their operational capabilities, leading to increased profitability and a competitive edge.
Future Trends in Inventory Management
Looking forward, several trends are shaping inventory management in supply chains:
- Increased Adoption of Automation: Businesses are increasingly utilizing automation technologies to manage inventory processes. Automated systems can reduce human error, streamline operations, and provide real-time data access.
- Integration of Predictive Analytics: Companies are harnessing the power of predictive analytics to improve forecasting accuracy. By analyzing large datasets, organizations can better anticipate market trends and adjust their inventory strategies accordingly.
- Sustainability Initiatives: As environmental concerns rise, companies are prioritizing sustainability in inventory management. This includes minimizing waste and selecting eco-friendly materials for packaging and shipping.
- Supply Chain Visibility: Enhanced technology will allow businesses to have clearer visibility throughout their supply chains. This visibility improves decision-making and fosters collaboration across different stakeholders.
These trends signal a shift towards more efficient, technology-driven inventory management practices. As organizations adapt to these changes, they will enhance their capabilities and maintain relevance in an evolving market.
"Inventory management is not merely about counting stock; it's about strategic management and planning to meet future needs."
By embracing these advancements, companies can navigate the complexities of supply chain management more effectively.