Exploring the Unique Properties and Uses of Kapton
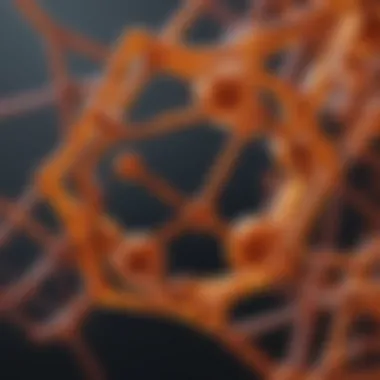
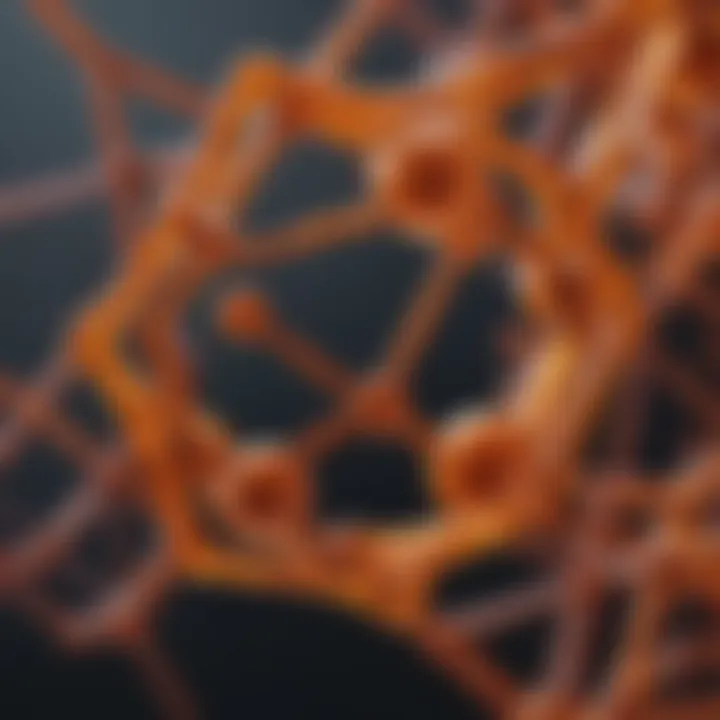
Intro
Kapton plastic, a polyimide film engineered for high-performance use, serves as a testament to human ingenuity in materials science. This remarkable material is celebrated for its exceptional thermal stability, impressive electrical insulation properties, and outstanding resistance to a variety of chemicals. Capable of operating in extreme environments, Kapton finds application in a diverse set of industries ranging from aerospace to electronics. With advancements on the horizon, understanding its properties and applications becomes increasingly relevant.
As our world races toward newer technologies and greener solutions, the versatility offered by Kapton serves as both a foundation and a springboard for innovation. But why has this seemingly humble plastic found a cozy niche in some of the most advanced fields? Our exploration begins with a closer look at the underlying characteristics that make Kapton unique.
Prelude to Kapton Plastic
Understanding Kapton plastic is crucial for anyone working in fields where high performance and reliability are non-negotiable. This unique polymer, known for its exceptional thermal and electrical properties, has carved out its niche in demanding environments, such as aerospace and electronics. Unlike other materials, Kapton offers an ideal combination of strength, insulation, and versatility, making it a frontrunner in advanced materials science.
Definition and Basic Composition
Kapton is a brand name for a polyimide film developed by DuPont. Its chemical structure primarily consists of imide monomers, which are polymers formed through a reaction between an anhydride and an amine. This basic composition bestows Kapton with remarkable characteristics including high temperature stability, chemical resistance, and electrical insulationāqualities that are indispensable in various demanding applications.
Furthermore, the polymer is known for its unique mechanical properties. It can withstand extreme temperatures ranging from -269°C to +400°C, which is something most conventional plastics cannot handle without significant degradation.
Historical Context
The journey of Kapton plastic began back in the 1960s when it was first introduced for use in the aerospace industry. The U.S. space program's increasing demands for materials that could operate effectively in harsh conditions propelled its development. Kapton's remarkable resistance to heat and chemicals led to its adoption in spacecraft, where it provided insulation for critical components. As the field expanded, so did the material's applicationsāfrom satellite equipment to circuit boards, Kapton's adaptability was proven time and again.
Initially, Kapton was seen as a specialty item, primarily reliant on its novelty to attract attention. However, over the years it has grown into a mainstream solution in many industries. Today, you'll find Kapton in medical devices, automotive components, and even consumer electronics. It has continuously evolved, meeting the industry's demand for innovative solutions to complex problems.
"Kapton not only meets the rigorous demands of industry applications but also speaks volumes about how materials science can improve efficiency in modern technology."
The importance of Kapton plastic cannot be overstated. It has not only facilitated advancements in technology but has also set a standard for high-performance materials. As we proceed through this article, we will explore in-depth its chemical and physical properties, applications, and the latest innovations surrounding this versatile material.
Chemical Properties of Kapton
Understanding the chemical properties of Kapton is crucial, as these attributes set the stage for its diverse applications across various industries. Kapton, a polyimide film, has unique characteristics that make it a standout material in the face of challenging environments. The remarkable thermal, mechanical, and chemical attributes contribute to its effective use in sectors like aerospace, electronics, and manufacturing.
Polyimide Structure
At its core, the polyimide structure of Kapton is what gives it the edge over traditional plastics. Polyimides are formed through the polymerization of specific monomers that create a complex network of imide linkages. This structure results in a semi-crystalline material known for its excellent thermal resistance and mechanical strength. Because of this unique arrangement, Kapton can maintain its form and functionality under extreme temperature fluctuations, often ranging from as low as -269°C to as high as 400°C.
In practical terms, the polyimide backbone contributes to its durability and performance in high-stress environments. Think of it as a robust backbone that keeps everything together while ensuring flexibility. This flexibility is not just physical; it also allows for various forms, such as thin films or thicker sheets, depending on the application's needs.
Thermal Stability
Thermal stability is one of the most notable properties of Kapton. It can endure prolonged exposure to high temperatures without degrading or losing its mechanical strength. To put it bluntly, when other materials might buckle and bend, Kapton stands firm. This remarkable stability is attributed to the stable chemical bonds formed in its polyimide structure, preventing thermal degradation.
Moreover, Kapton has a low coefficient of thermal expansion, which means it does not expand or contract significantly with temperature changes. This attribute makes it an ideal candidate for applications that face rapid temperature cycling. In simpler terms, it stays put when the heat is on, which is crucial for aerospace components that experience intense conditions during flight.
Chemical Resistance
Another area where Kapton shines bright is its chemical resistance. The material demonstrates impressive stability against a wide range of solvents, acids, and bases. This feature allows Kapton to be used in harsh chemical environments without significant degradation or performance loss.
For instance, in the aerospace industry, components made from Kapton can withstand exposure to fuels, oils, and other aggressive substances encountered in flight. Likewise, in the electronics sector, where devices come into contact with various chemicals during assembly or use, Kapton provides the necessary durability.
As a testament to its resilience, Kapton films can be found in applications requiring prolonged exposure to corrosive materials, such as packaging for sensitive electronics or insulation in high-temperature environments. Listening closely to how these properties play out tells a story of reliability and robustness in the face of adversity.
While these attributes paint a promising picture, the understanding of Kapton's capabilities lays a potent groundwork that brings us closer to its various applications and innovations.
Physical Properties of Kapton
The physical properties of Kapton plastic are not just technical specs; they demonstrate why this material shines brightly in so many demanding applications. Understanding these properties, such as mechanical strength, flexibility, and dimensional stability, uncovers the layers of versatility that Kapton offers to industries ranging from aerospace to electronics.
Mechanical Strength
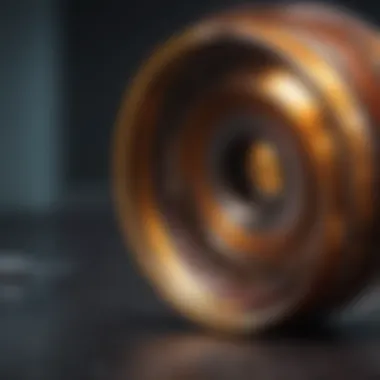
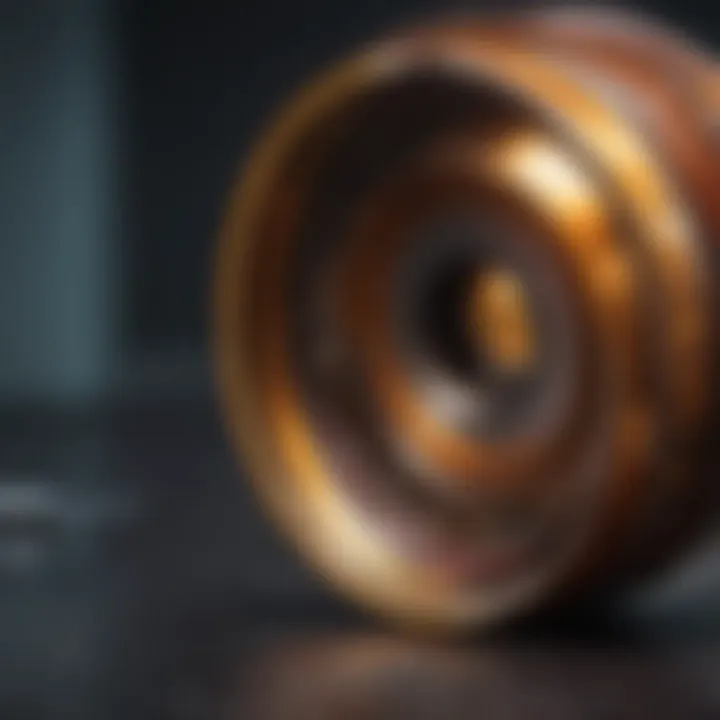
Mechanical strength is perhaps one of the most critical aspects when evaluating any engineering material, and Kapton does not disappoint. This polyimide film exhibits exceptional tensile strength, allowing it to retain its form and function under severe stress. In instances where materials might bend or break, Kapton stands strong, effectively withstanding significant forces. Its capability to maintain integrity in extreme environments is a game-changer.
For example, think about a satellite orbiting the Earthāsubjected to harsh conditions, including radiation and vast temperature variations. Kaptonās mechanical resilience ensures that components remain intact even when faced with vibrations and mechanical loads during launch and operation. Companies such as NASA and Boeing often rely on Kaptonās strength in their aerospace projects, proving its worth.
"Mechanical strength is not just a number; it's the backbone of reliability in critical applications."
Flexibility and Thickness Variability
When it comes to flexibility, Kapton is a standout performer. Its inherent flexibility allows it to be deployed in various forms, making it suitable for applications that require bending and shaping. This characteristic is vital in sectors like consumer electronics, where flexible circuits are increasingly common. Kapton can be manufactured in multiple thicknesses, offering tailor-made solutions for specific needs. The ability to cut film thickness means that designers can choose just the right level of flexibility, whether they need a thicker gauge for durability or a thinner one for lightness.
This adaptability is particularly advantageous in automative designs where components often require a degree of flexibility due to movement and vibration. The thickness variability supports engineers in achieving the right balance between performance and weight, ultimately boosting efficiency.
Dimensional Stability
Dimensional stability refers to the ability of a material to retain its original dimensions, despite changes in temperature, moisture, or other environmental factors. Kapton excels in this area as well. Its low coefficient of thermal expansion means it doesnāt warp or deform easily under temperature fluctuations, something critical in the precision-driven industries.
In practical terms, this translates into reliable performance for applications like high-speed computing, where even minute changes in size can lead to catastrophic failures. Components that depend on tight tolerances find peace of mind in Kapton, as its stability supports overall system integrity.
In summary, the physical properties of Kapton plastic, particularly its mechanical strength, flexibility, and dimensional stability, highlight its importance in modern technology. As industries continue to evolve and demand more from their materials, Kapton stands at the forefront, showcasing qualities that not only meet but exceed expectations.
Thermal and Electrical Properties
Understanding the thermal and electrical properties of Kapton plastic is essential as they significantly influence its applications across various industries. Kapton's exceptional thermal stability makes it a top choice in environments that require materials to withstand extreme temperatures. Moreover, its electrical insulation capabilities ensure that it is safe to use in high-voltage applications, reducing the risk of electrical failures. As industries evolve, the relevance of these properties continues to shape innovations and applications in a variety of fields.
Insulation Performance
Kapton demonstrates remarkable insulation performance, which is a hallmark of its many uses in electrical and electronic applications. The material's ability to maintain its integrity when exposed to high temperaturesāup to 400°Cāensures consistent performance in demanding scenarios. This capacity to insulate prevents the unwanted flow of current, effectively safeguarding sensitive components from electrical damage.
- Benefits of Kapton Insulation:
- Exceptional thermal resistance.
- High dielectric strengthāthis means it can withstand high voltages without breaking down.
- Light weight compared to traditional insulating materials, which is critical for applications where weight matters, like in aerospace.
Its use is commonplace in the manufacturing of electric motors, wiring, and circuit boards. For example, satellites often utilize Kapton as a protective layer for wiring and circuitry, showcasing its necessity in high-stakes environments.
Dielectric Properties
The dielectric properties of Kapton are fundamental to its ability to serve effectively as an insulator. With a high dielectric strength and low dielectric constant, Kapton excels in minimizing energy loss through electric fields, making it efficient for various electronic devices. This characteristic allows materials to be layered tightly together without risking interference or failure due to shorts, which is vital in compact electronic designs.
"Kaptonās low dielectric loss ensures high-fidelity signals in communication devices, reducing attenuation."
Applications in radio-frequency (RF) circuits further emphasize Kapton's significance; the material plays a crucial role in telecommunications, where signal clarity is paramount. In many ways, its performance in this area sets the bar for what high-quality dielectrics should achieve.
Thermal Management Applications
The versatile thermal management capabilities of Kapton are invaluable, particularly in environments that experience rapid temperature fluctuations. In electronics, managing heat is critical to maintain device longevity and operational efficiency. Kapton films serve as heat shields, effectively dissipating heat and protecting sensitive components.
- Areas of Application:
- Aerospace: Insulation in spacecraft, where temperatures can vary drastically.
- Automotive: In electric vehicles, Kapton films safeguard batteries by regulating temperature.
- Consumer Electronics: Used in devices like smartphones and laptops to protect against thermal overload.
By employing a Kapton layer in thermal management applications, manufacturers benefit from enhanced reliability and performance. It directs heat away from critical components, ensuring processes remain unimpaired under thermal stress. The combination of insulation and thermal control illustrates why Kapton remains a trusted material in modern engineering.
Applications of Kapton Plastic
Kapton plastic has made its mark across various industries due to its unique properties and reliability. Its adaptability to extreme conditions sets it apart from other materials, making it a favored choice for engineers and manufacturers. The applications of Kapton are not just functional but often vital to the success of high-tech projects. By integrating keywords such as "Kapton applications," "high-performance solutions," and "versatile material," we can keep this discussion relevant both in terms of content and search engine optimization.
Aerospace and Defense
In aerospace and defense, reliability can make or break a project, and thatās where Kapton excels. This material is known for its resistance to extreme temperatures, ranging from -269°C to over +400°C. In spacecraft technology, where components must withstand the harshness of space, Kapton is often used as insulation in wiring and electronic boards. Its light weight, coupled with outstanding thermal stability, allows it to fit seamlessly into spacecraft design without adding unnecessary bulk.
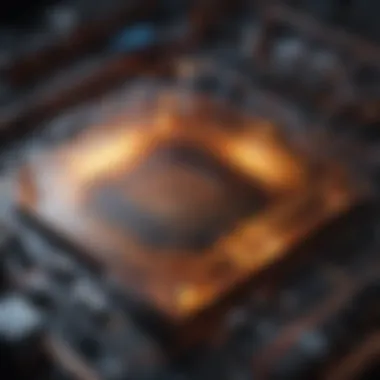
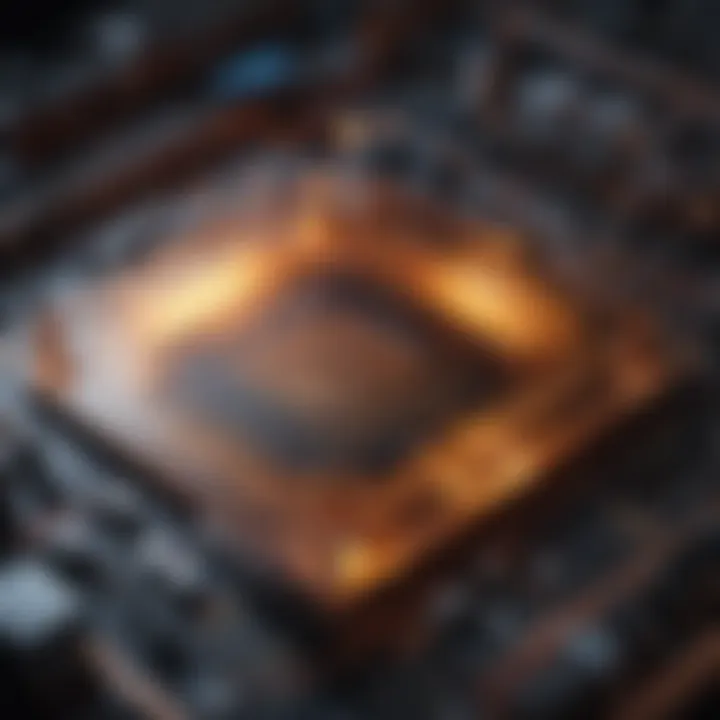
Key benefits of using Kapton in aerospace applications include:
- Thermal resistance: Protecting sensitive components from thermal surges.
- Lightweight properties: Important when every gram counts in flight.
- Durability: Able to endure the stresses of launch and re-entry.
"In mission-critical aerospace applications, using Kapton is not just an option; it is often a necessity to ensure safety and reliability."
Electronics Industry
The electronics sector thrives on innovation and efficiency, and Kapton plays an essential role here. Flexible circuits, which are becoming increasingly important in modern electronics, utilize Kapton for its excellent dielectric properties and flexibility. With the trend leaning towards miniaturization of technology, the need for thin, lightweight, and flexible materials makes Kapton indispensable.
Some of its notable applications in electronics include:
- Flexible Printed Circuits (FPC): Ensuring reliable conduction in limited spaces.
- Electrical Insulations: Protecting sensitive electronic components.
- High-frequency cables: Enhancing performance in telecommunications equipment.
Medical Device Manufacturing
In healthcare, the reliability and quality of materials can directly impact patient outcomes. Kapton is ideal in this field for its biocompatibility and chemical resistance. Commonly used in devices that require precision and durability, it ensures operational safety and integrity.
Examples of Kapton applications in medical devices include:
- Insulation for sensors: Providing protection in sterilization and high-temperature environments.
- Packaging materials: Quick adaptability to various forms for customized devices.
- Wearable technology: Its flexibility makes it suitable for skin-adhering applications.
Automotive Applications
The automotive industry continuously pushes the envelope for performance and safety. Kapton supports this drive, ensuring that various components perform well under high-stress situations. From wiring harnesses to heat shields, its properties allow it to function optimally in bustling environments like automobiles.
In the automotive sector, Kapton can be seen in:
- Wiring Insulation: Reliable performance to prevent shorts or failures.
- Heat Shields: Protecting critical areas from engine heat.
- Gaskets and Seals: Long-lasting material that withstands chemicals and wear.
Overall, the applications of Kapton plastic not only highlight its versatility but also underline its critical role in advancing technology in various sectors. Each industry leverages its strengths to enhance product performance, reliability, and efficiency to stay competitive in ever-evolving markets.
Recent Innovations and Developments
In the rapidly evolving landscape of materials science, the significance of recent innovations in Kapton plastic cannot be overstated. This section delves into key advancements and emerging trends that not only enhance the performance of Kapton but also expand its array of applications. As research leads to breakthroughs, understanding these developments is crucial for students, researchers, and professionals keen on deploying this versatile polymer effectively.
Advancements in Processing Techniques
The processing methods for Kapton plastic have reached new heights, focusing on improving efficiency and precision. Traditional techniques have been reevaluated in the light of new technologies that reduce waste and increase output quality.
- Film Production: Innovations in film extrusion processes are notable. New techniques enable the creation of thinner, stronger films without compromising the material's integrity, making it suitable for applications where space and weight are at a premium.
- Coating Technologies: The advent of advanced coating techniques allows for tailored properties. Companies are experimenting with surface treatments that improve adhesion and enhance durability, offering greater resilience to wear and tear.
- Additive Manufacturing: The integration of 3D printing into Kapton processing opens up new possibilities. This allows for manufacturing intricate designs that were previously unfeasible, paving the way for customized solutions in industries like aerospace and electronics.
Enhancements in processing not only improve performance characteristics like heat resistance but also lead to cost-efficiency. As manufacturers adopt these advanced practices, they align projects with sustainability goals by minimizing the ecological footprint of production.
"Innovation is not just about technology; itās about improving processes that empower applications to reach their full potential."
Emerging Applications
As processing techniques advance, so too do the applications of Kapton plastic. Hereās a closer look at some promising directions where this material is making waves:
- Space Exploration: Kapton's lightweight and heat-resistant properties are increasingly being applied in the design of heat shields and insulating blankets for spacecraft. Missions to Mars and beyond see the benefits of reducing weight while ensuring thermal protection at extreme temperatures.
- Wearable Technology: The rise of wearable devices brings forth a need for flexible and durable materials. Kapton films are particularly suited for these applications due to their thinness and robustness, allowing integration into various electronic devices without sacrificing comfort or function.
- Flexible Solar Panels: The renewable energy sector is turning to Kapton for flexible solar panel solutions. Its capability to withstand outdoor conditions while being lightweight makes it essential for developing technologies that can adapt to various applications in energy collection.
- Electronics Miniaturization: In the realm of electronics, Kapton is becoming more prominent for circuit substrates and flexible printed circuits. As devices shrink yet demand grows for functionality, Kapton serves as a reliable solution, offering significant electrical insulation without added bulk.
As these applications unfold, the knowledge surrounding Kaptonās benefits and limitations enhances, guiding engineers and developers in making informed decisions about this vital material.
Challenges and Limitations
In the contemporary landscape of material science, it is paramount to scrutinize the challenges and limitations associated with Kapton plastic. While it boasts remarkable properties that make it a go-to material in various high-tech fields, not every application can take full advantage of these qualities. Discussions around its cost implications and environmental concerns are crucial, as both factors can greatly influence its adoption in emerging technologies.
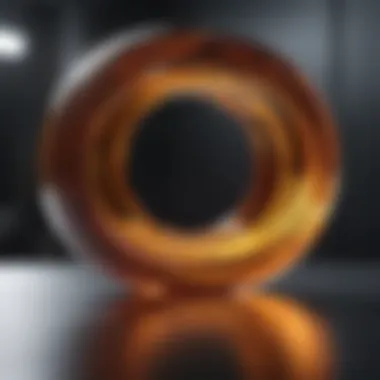
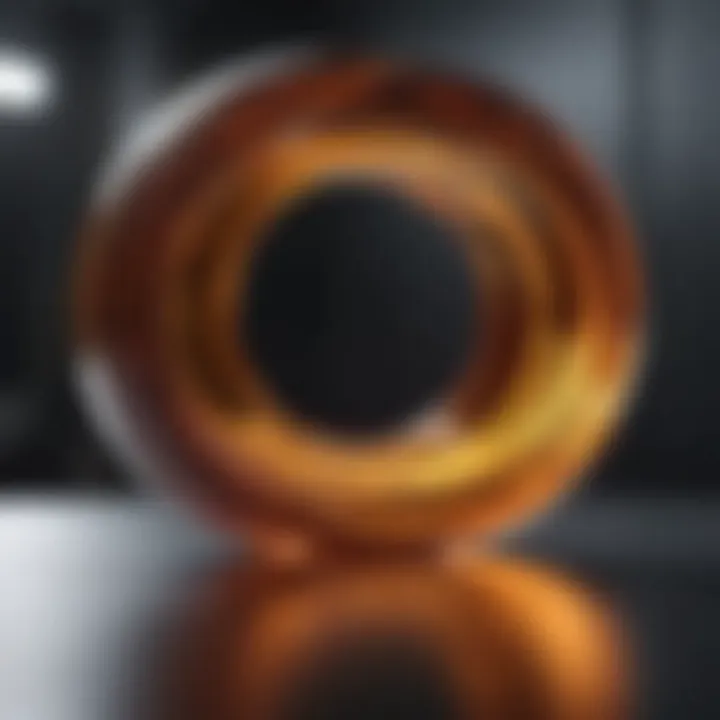
Cost Implications
Cost remains a significant barrier when it comes to the broader adoption of Kapton plastic. The intricate processes involved in its manufacturing often translate into higher prices compared to more conventional plastics. This premium cost can hinder its use in applications where budgets are tight. Organizations looking to integrate Kapton into their production lines must weigh these financial implications against the benefits it provides.
- Initial investment can be steep, demanding careful budgeting and planning.
- Long-term savings, however, might offset these initial costs, especially in high-performance applications.
- For instance, aerospace and defense sectors might find Kapton worth its weight in gold, owing to its exceptional thermal resistance and durability.
Potential buyers should conduct a comprehensive cost-benefit analysis, evaluating whether the enhanced performance justifies the financial outlay. Not all sectors will find the investment feasible, especially in cost-sensitive industries such as consumer goods.
Recycling and Environmental Concerns
Another key area of discussion is the recycling and environmental impact of Kapton plastic. As countries and industries strive for sustainability, the recyclability of materials has become a hot-button issue. Unfortunately, Kapton does not lend itself easily to conventional recycling methods. This characteristic poses challenges not only for manufacturers but also for end-users who are increasingly conscious of their ecological footprint.
- While the material is highly resistant to wear and degradation, its non-biodegradable nature presents environmental challenges.
- The lack of recycling facilities capable of processing Kapton exacerbates waste management issues.
- In this light, innovators are actively exploring ways to develop greener alternatives, aiming to combine the strong points of Kapton with eco-friendly properties.
Ultimately, addressing these concerns about cost and environmental sustainability will be essential for the future of Kapton plastic. As the debate continues, industries are pressured to find solutions that balance performance with ecological responsibility. This evolving landscape could push researchers towards developing new formulations that mimic the great attributes of Kapton but with higher recyclability and lower cost.
Future Directions in Kapton Research
The potential future of Kapton plastic research is nothing short of exciting. As industries continually seek materials that align with a growing emphasis on sustainability and innovation, Kapton's adaptability places it in a prime position to meet these challenges. Future directions in this area hold the promise of creating not only improved materials but also refining existing applications, thus allowing for better performance and environmental stewardship.
Sustainable Alternatives and Innovations
The conversation around sustainability in materials science is gaining momentum. In the context of Kapton, there are explorations underway to create more sustainable production processes or even biodegradable alternatives. For instance, research is venturing into biopolymer composites that could mirror some of Kapton's key features, to lessen the environmental impact of traditional production methods.
As we look ahead, collaboration between scientists, universities, and industries will play a vital role. New methods, such as using agricultural by-products in the synthesis of polyimides, could help not only in reducing waste but also scaling up production sustainably.
Environmental initiatives often come with regulatory benefits as well. Companies focused on sustainable practices may find themselves gaining access to incentives or favorable public perception, creating a win-win scenario. Here are some key areas to focus on in sustainable Kapton research:
- Recycled materials: Investigating how recycled Kapton could be reprocessed and repurposed.
- Energy-efficient methods: Looking at green chemistry principles to reduce energy consumption during manufacturing.
- Lifecycle assessments: Assessing the environmental impact across all stages from production to disposal.
"Innovating isn't just about machine parts and making things; it's about understanding the big picture - the impact on our planet and communities alike."
Integration with Other Materials
An intriguing avenue for future research lies in the integration of Kapton with other materials. By blending Kapton with metals, ceramics, or other polymers, researchers can leverage the strengths of each component to create hybrid materials with enhanced properties. This fusion can lead to solutions that are not only lighter and stronger but also exhibit improved temperature resistance and insulation characteristics.
One such example is the use of Kapton in multi-layered composites for aerospace applications, where engineers combine it with carbon fiber or aluminum to achieve optimal structural integrity while managing weight.
Moreover, there is the potential of incorporating smart technologies into Kapton composites. As industries push towards smarter products, the fusion of Kapton with conductive materials could enable the development of flexible sensors or electronic components.
To summarize:
- Enhanced performance: Combining materials can lead to new functionalities and advanced performance metrics.
- Customizable properties: Tailoring materials for specific applications broadens their usability.
- Future-proofing: Making materials that adapt to the ever-changing technological landscape ensures longevity in their applications.
Moving forward, the integration of Kapton with various materials signifies a transformative step in material science, opening the doors to innovative applications that were once thought impossible.
Finale
In wrapping up our exploration of Kapton plastic, itās vital to recognize the profound significance this material holds within various industries. From its unique thermal and electrical resistance qualities to its versatile applications, Kapton's attributes underpin its integral role, especially in cutting-edge fields like aerospace and electronics.
Summary of Key Findings
A few key points emerge from our discussion:
- Exceptional Thermal Stability: Kapton can withstand extreme temperatures, making it ideal for high-stress environments.
- Chemical Resistance: Its resistance to many chemicals ensures longevity and reliability in tough conditions.
- Versatile Applications: From aerospace to the medical field, Kapton's application spectrum is extensive, showcasing its adaptability.
These findings not only highlight the current use of Kapton but also signal its continued relevance as industries evolve and demand more from materials.
Implications for Industry and Research
The implications of this material are far-reaching. For industries, especially those involved in high-tech manufacturing, the adoption of Kapton translates to enhanced efficiency and better product performance. Moreover, the ongoing research into Kapton and its composites promises advancements in material science that could lead to innovative solutions addressing current challenges.
- Encouragement for Sustainable Practices: As environmental awareness grows, thereās a push to develop more sustainable forms of Kapton, incorporating eco-friendly practices in its production.
- Integration with Emerging Technologies: The future points toward a fusion of Kapton with newer materials to create composites that push boundaries further, potentially leading to lighter, more efficient products.
"The innovation in processing techniques and the integration of Kapton with other materials will undoubtedly redefine its applications in the coming years."