Comprehending Lean Enterprise: Strategies and Implications
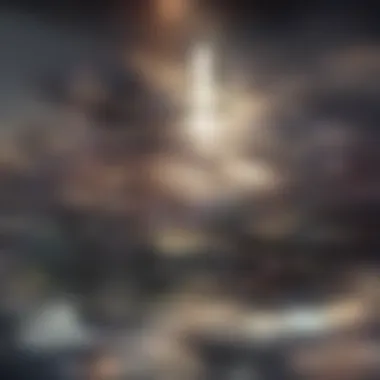

Intro
Lean enterprise is a multifaceted approach that aims to enhance organizational efficiency by streamlining operations, minimizing waste, and focusing on value creation. Understanding lean principles, methodologies, and tools is essential for anyone interested in improving business processes. This article aims to dissect the various aspects of lean enterprise, exploring its historical roots, practical applications, and the significant impact it has on modern organizations.
The concept of lean enterprise draws from its predecessor, lean manufacturing, which originated in the Toyota Production System. However, its application has expanded beyond manufacturing to various sectors including healthcare, service industries, and even technology.
Implementing lean practices requires a cultural shift within organizations, emphasizing a commitment to continuous improvement, employee empowerment, and customer satisfaction. This overview lays the groundwork for a detailed inquiry into lean methodologies, leading to a thorough exploration of effective strategies tailored to address organizational challenges.
Understanding Lean Enterprise
Understanding lean enterprise is crucial in today’s competitive business environment. Organizations face pressure to improve efficiency, reduce waste, and create value for customers. The lean enterprise framework offers a comprehensive approach to achieve these goals by focusing on continuous improvement and operational excellence.
The essence of lean enterprise involves minimizing waste while maximizing productivity. Waste can be defined as anything that does not add value to the product or service provided. In a lean environment, every process is analyzed to eliminate non-value-adding activities. This leads to better resource management and enhances overall effectiveness.
One key element is the emphasis on customer value. Organizations are urged to understand the needs and expectations of their customers and align their processes to meet these demands. This customer-centric approach is not only beneficial for the clients but also enhances employee satisfaction, fostering a culture of engagement and responsiveness.
Moreover, embracing lean principles necessitates a shift in organizational culture. It involves cultivating an environment where employees are empowered to identify issues and participate in problem-solving. This democratic approach not only enhances creativity but also increases accountability amongst team members.
In summary, understanding lean enterprise goes beyond merely adopting tools and techniques. It requires a holistic perspective on operations, where all layers of the organization are involved in the pursuit of excellence.
Definition and Key Principles
Lean enterprise is a methodology that focuses on eliminating waste while enhancing quality and efficiency. Key principles of lean include:
- Value: Determine what adds value from the customer’s perspective.
- Value Stream: Map out all actions and processes that contribute to delivering customer value, identifying waste.
- Flow: Ensure processes are smooth and continuous, reducing bottlenecks.
- Pull: Implement a system where production is driven by customer demand rather than planning forecasts.
- Perfection: Foster a culture of continuous improvement where organizations constantly strive for better methods and outcomes.
By understanding these principles, organizations can effectively create strategies that lead to operational improvement.
Historical Context
The concept of lean enterprise can be traced back to Toyota Production System developed in Japan during the 1950s. The aim was to improve quality while reducing production costs. After World War II, Japan faced significant economic challenges and adopted lean principles to rebuild its industries. This methodology helped Toyota enhance its manufacturing processes, setting a model that would influence global industries.
As lean practices evolved, various industries began to recognize their benefits. The core of lean enterprise has been adapted to fit manufacturing, healthcare, service sectors, and beyond. Its applicability across different contexts illustrates its versatility and effectiveness.
Today, organizations worldwide implement lean strategies not just for operational improvements, but also as a means to foster innovation and adaptability in a changing business landscape. The historical evolution of lean principles is a testament to its practicality and relevance.
The Lean Philosophy in Action
The Lean Philosophy serves as the backbone of a lean enterprise. It encapsulates a mindset focused on creating maximum value for the customer while minimizing waste. This philosophy is crucial for organizations seeking to improve efficiency and effectiveness. It affects various operational aspects, influencing workflows, employee engagement, and customer satisfaction.
Implementing the Lean Philosophy requires a clear understanding of its core elements. These principles guide organizations in their quest to identify and eliminate anything that does not add value to the customer. By doing so, businesses can enhance productivity and create sustainable growth.
Core Lean Methodologies
Core Lean Methodologies form the practical tools through which the Lean Philosophy is enacted in organizations. These include Just-In-Time production, which emphasizes producing only what is needed when it is required. This approach reduces inventory costs and improves cash flow.
Another methodology is 5S, a system that promotes organization and cleanliness in the workplace. It stands for Sort, Set in order, Shine, Standardize, and Sustain. 5S helps in establishing a disciplined workspace that fosters efficiency and focus.
Additionally, Total Productive Maintenance (TPM) is a strategy aimed at operational efficiency. It focuses on maintenance practices that maximize equipment effectiveness, significantly impacting production cycles.
Value Stream Mapping
Value Stream Mapping (VSM) is a valuable tool in the Lean toolkit. It visually represents the flow of materials and information through the production process. This method highlights both value-added and non-value-added activities. It serves as a basis for identifying areas for improvement. VSM allows organizations to see how their processes can be streamlined, promoting better efficiency.
By accurately mapping out an organization’s processes, teams can pinpoint bottlenecks and redundancies. This direct visualization aids in making informed decisions to enhance processes significantly. As a result, companies can improve delivery times and quality.
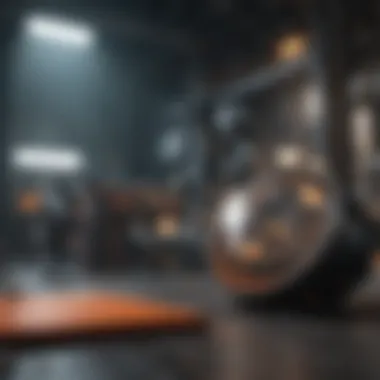

Kaizen Practices
Kaizen translates to "continuous improvement" in Japanese. It embodies the spirit of making small, incremental changes that lead to significant improvements over time. This practice involves all employees, encouraging them to contribute ideas and participate actively in problem-solving.
Implementing Kaizen practices cultivates a culture of collaboration and empowerment. Employees feel valued, leading to higher morale and productivity. Regular team meetings can help maintain momentum by offering a platform for sharing insights and progress.
Implementing Lean Strategies
Implementing lean strategies is crucial for organizations seeking to enhance operational efficiency and foster a culture of continuous improvement. This section will explore various elements and considerations integral to successful lean implementation.
Creating a Lean Culture
Creating a lean culture is foundational to the success of any lean initiative. It involves integrating lean principles into the very fabric of the organization. This culture promotes an environment where every employee understands their role in eliminating waste and optimizing processes.
Key aspects include:
- Employee Engagement: Employees must feel empowered to suggest improvements. Involving them not only boosts morale but also ensures that changes are practical.
- Open Communication: Establish clear channels for communication. This transparency nurtures trust and encourages collaboration.
- Shared Goals: Align the organization’s goals with lean principles. When everyone is focused on the same objectives, progress becomes evident and sustainable.
Fostering a lean culture may take time, but the long-term benefits, including increased employee satisfaction and improved productivity, are well worth the effort.
Training and Development Needs
Training and development are essential components of implementing lean strategies. Organizations must equip their workforce with the necessary skills and knowledge to apply lean principles effectively. A well-structured training program can significantly enhance understanding and execution of lean methodologies.
Key considerations include:
- Foundational Training: Provide basic training on lean concepts, tools, and methodologies. This ensures all employees share a common understanding.
- Role-Specific Development: Tailor training to address the unique needs of different roles within the organization. For instance, leaders may require advanced training in change management, while operational staff need hands-on experience with tools like Value Stream Mapping.
- Continuous Learning: Emphasize the importance of lifelong learning. Offer regular workshops, seminars, or resources that allow employees to deepen their knowledge of lean practices over time.
Investing in training leads to a more competent workforce that can independently drive lean initiatives.
Leadership’s Role in Lean Implementation
Leadership plays a pivotal role in the successful implementation of lean strategies. Leaders set the tone and direction for the organization. Their commitment to lean principles can make or break an initiative.
Essential roles that leaders must embrace include:
- Visionary: They should articulate a clear vision for the lean journey, explaining how it aligns with organizational goals. A compelling vision motivates employees to engage with lean practices.
- Role Models: Leaders must exemplify lean behaviors in their daily operations. By practicing what they preach, they build credibility and trust among the workforce.
- Support Network: Leaders need to provide the necessary support and resources for lean projects. This includes fostering a safe environment for risk-taking and innovation.
Measuring Lean Success
The success of lean enterprise initiatives is fundamentally linked to how effectively organizations can measure their outcomes. Defining the right performance metrics, utilizing robust data collection techniques, and establishing a continuous improvement feedback loop are crucial components in evaluating lean strategies. Ensuring that these elements are in place can lead to not only immediate benefits but also long-term sustainability of lean practices. The interplay of these components forms the backbone of successful lean implementations, driving efficiency and promoting a culture of accountability.
Defining Performance Metrics
Performance metrics are essential for assessing the effectiveness of lean strategies. These metrics should be specific, measurable, achievable, relevant, and time-bound. Common metrics in lean implementations include cycle time, lead time, defect rates, and overall equipment effectiveness (OEE). Each metric provides insights into different aspects of the operational process. For instance, tracking cycle time can help organizations identify bottlenecks, while analyzing defect rates can highlight areas needing quality improvement.
When organizations define their performance metrics, it's important to align them with overall business objectives. Metrics should reflect areas that impact customer satisfaction and financial performance. Furthermore, establishing baseline measurements before implementing lean strategies will allow organizations to evaluate changes more effectively.
Data Collection Techniques
Collecting data is pivotal in measuring success in lean practices. Various techniques can be employed to gather relevant data efficiently. Some effective data collection methods include:
- Manual Data Collection: Staff can record observations and metrics in real-time, though it can be time-intensive and prone to human error.
- Automated Data Collection: Utilizing technology, such as sensors and software, can streamline the data collection process and reduce errors. Systems like manufacturing execution systems (MES) are often used for this purpose.
- Surveys and Feedback: Gathering feedback from employees and customers can provide qualitative data on lean initiatives' effectiveness.
By adopting a combination of these techniques, organizations can ensure that data collection is comprehensive and accurate, providing a solid foundation for analysis and improvement.
Continuous Improvement Feedback Loop
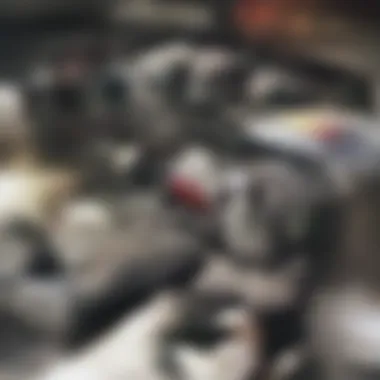

A continuous improvement feedback loop is integral to lean success. This concept revolves around the idea of constantly evaluating and refining processes. After collecting data and assessing performance metrics, companies should share findings with all relevant stakeholders. Collaboration across departments facilitates the identification of areas needing improvement.
The process typically follows a cycle of Plan-Do-Check-Act (PDCA). This iterative approach promotes active engagement in problems solving and fosters a culture of continuous improvement. Organizations that embrace this loop can adapt to changes quickly and effectively, leading to sustained gains in efficiency and productivity.
"Measuring success in lean enterprise is not just about hitting targets; it's about fostering a mindset of growth and continual improvement."
Challenges in Adopting Lean
Adopting lean principles presents various challenges that can hinder the transformation process in organizations. Recognizing these obstacles is crucial for successfully implementing lean practices. Understanding the nature of these challenges not only highlights the importance of strategic approaches but also shapes the learning and adjustments necessary for organizations.
Resistance to Change
Resistance to change is a primary challenge in adopting lean principles. Organizations often operate under traditional management practices, deeply ingrained in their culture. Employees may feel threatened by changes that lean practices propose. This resistance can manifest in various ways, including reluctance to adopt new processes, skepticism about leadership motivations, or anxiety related to job security.
To overcome this resistance, effective change management strategies are essential. Leadership must communicate the benefits of lean practices clearly, addressing employee concerns by involving them in the transformation journey. Cultivating an inclusive environment raises awareness about the positive impacts of lean principles on efficiency and job satisfaction.
Sustaining Lean Initiatives
Sustaining lean initiatives becomes a significant concern after the initial adoption phase. Organizations might experience initial success with lean methodologies, but maintaining momentum can falter over time. The integration of lean practices requires ongoing commitment from all levels of the organization.
One approach to ensure sustainability is regular training and development. By reinforcing lean principles and methodologies, organizations can prevent complacency. It also helps to monitor progress continuously. Setting clear and evolving goals for lean initiatives enables organizations to adapt to changes in their environment while remaining aligned with lean values.
Cost Considerations
Cost considerations play a critical role in the adoption of lean strategies. Implementing new practices may entail upfront investments in employee training, technology upgrades, or new processes. Organizations must evaluate these costs against potential long-term savings and efficiencies gained from lean practices.
A careful cost-benefit analysis can aid decision-making and highlight the financial rationale for lean adoption. This analysis should encompass not only tangible savings but also intangible benefits such as improved employee engagement and customer satisfaction.
"Investing in lean practices is not merely an expense; it is a strategic investment in efficiency and employee morale that pays dividends over time."
Comparative Analysis with Traditional Models
In the context of organizational management, understanding how lean enterprise strategies stand against traditional models is essential. This comparative analysis enables organizations to appreciate the strengths of lean principles and the potential limitations of conventional management frameworks. Moreover, discerning these dynamics aids in making informed decisions about strategic direction and operational efficiency.
Lean vs. Traditional Management
Lean management focuses on minimizing waste while maximizing value. Traditional management, in contrast, has often emphasized resource utilization, which can lead to inefficiencies. Some important elements to consider include:
- Focus on Value: Lean methodologies advocate for creating value from the customer’s perspective. Traditional models may concentrate on internal processes instead of what truly resonates with the consumer.
- Waste Reduction: Lean seeks to eliminate waste in all forms, including time, materials, and labor. Traditional management does not inherently prioritize waste reduction.
- Flexibility and Responsiveness: Lean organizations tend to be more agile, enabling faster adjustments to changing market demands. Traditional models can be slower due to hierarchical structures.
A thorough understanding of these contrasting perspectives can empower managers to implement practices that truly enhance efficiency.
Process Optimization Techniques
Lean methodologies utilize several process optimization techniques that differentiate them from traditional management models. The following are key techniques integrated into lean practices:
- Value Stream Mapping: This technique involves visualizing all steps in a process, identifying value-adding and non-value-adding activities. By eliminating the latter, organizations can streamline operations.
- Kaizen: The philosophy of continuous improvement, where employees at all levels suggest small incremental changes. Unlike traditional approaches that may require top-down directives, Kaizen thrives on grassroots participation.
- Just-In-Time: Lean emphasizes producing only what is needed, when it is needed. Traditional methods often involve producing in larger batches, which can lead to excess inventory and waste.
"Lean enterprise strategies are not merely operational techniques; they represent a shift in the understanding of how organizations can create and deliver value efficiently."
These tools and approaches underscore the adaptability and efficiency of lean enterprise, providing a compelling alternative to older, more rigid management styles. Understanding these distinctions is crucial for educators, students, and professionals seeking to appreciate the comprehensive implications of lean principles in various organizational contexts.
Lean Enterprise in Various Industries
Understanding how lean enterprise applies across different industries can offer compelling insights into its adaptability and benefits. Each sector faces distinct challenges, but they all can leverage lean principles to enhance efficiency, reduce waste, and foster a culture of continuous improvement.
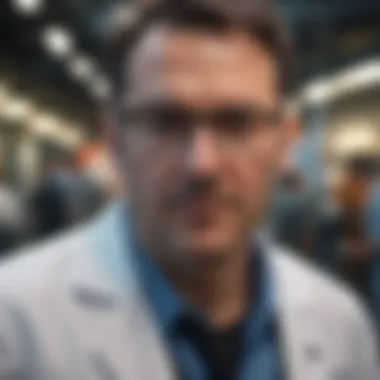

Manufacturing Applications
In the manufacturing sector, lean principles are often synonymous with efficiency. The objectives of lean manufacturing focus on maximizing productivity while minimizing costs. Key strategies include implementing Just-In-Time (JIT) inventory techniques, which ensure that materials are only procured as needed to avoid excess.
- Benefits of Lean Manufacturing:
- Reduces lead times
- Enhances product quality
- Lower production costs
Companies like Toyota have exemplified lean manufacturing through the Toyota Production System. This approach not only emphasizes waste reduction but also increases overall operational efficiency.
Service Sector Adoption
The service sector has also increasingly embraced lean methodologies. Unlike manufacturing, where physical products are the focus, the service industry aims to streamline processes. Lean principles can improve service delivery times, customer satisfaction, and employee engagement by simplifying workflows.
- Key Points for Service Sector:
- Mapping customer journeys to eliminate bottlenecks
- Employee training on lean practices
For example, banks implementing lean strategies might analyze loan processing to identify areas for improvement, leading to faster approvals and increased customer satisfaction.
Healthcare Sector Insights
The healthcare sector faces unique challenges, including high costs and stringent regulations. Lean management can help healthcare providers improve patient care and operational efficiency. Hospitals utilizing lean techniques can reduce patient wait times, manage inventory more effectively, and improve the quality of care.
- Lean in Healthcare:
- Focus on patient-centered care
- Streamlined administrative processes
Some health systems, such as Virginia Mason Medical Center, have successfully implemented lean strategies to enhance overall care quality while controlling costs.
Technology and Lean
The technology sector is another realm where lean enterprise thrives. Rapid changes in technology demand agility and quick responses to market needs. Lean strategies help tech companies eliminate waste in product development and accelerate time-to-market for new innovations.
- Technological Applications of Lean:
- Agile development methodologies
- Continuous feedback and iteration
Startups frequently adopt lean principles to pivot and adapt quickly, drawing from customer feedback to refine their offerings and reduce unnecessary development cycles.
Lean enterprise practices allow diverse industries to transform operations, driving both cost efficiency and innovation.
The Future of Lean Enterprise
The future of lean enterprise stands at a critical juncture. As organizations increasingly look for ways to enhance efficiency, drive innovation, and reduce waste, the principles of lean management continue to evolve. This section will explore the importance of understanding the future trajectory of lean frameworks, addressing how emerging trends and sustainability considerations shape the effectiveness of these methodologies.
Emerging Trends
Several emerging trends within the scope of lean enterprise warrant attention. Industry 4.0 brings a wave of digital technologies that lean methodologies can complement. Technologies like the Internet of Things (IoT), artificial intelligence (AI), and big data analytics provide unprecedented avenues for optimization.
- Integration of Digital Tools
Lean practices are increasingly leveraging digital tools for real-time data analysis. This enhances decision-making processes, allowing for quicker responses to operational inefficiencies. - Remote Work Adaptation
The significant shift to remote work calls for lean principles to be adapted to virtual environments. New strategies for collaboration and workflow design are emerging, ensuring productivity can be maintained beyond traditional office settings. - Agile Methodologies
Agile principles align closely with lean. The combination of lean and agile methodologies is fostering creativity in product development while maintaining efficiency. Companies can deliver solutions faster while remaining customer-focused, thus enhancing satisfaction. - Interconnected Lean Ecosystems
Lean enterprises will increasingly operate within broader ecosystems. Collaboration between various sectors and organizations can lead to shared best practices, contributing to enhanced value creation across the board.
These trends reflect the necessity for lean enterprises to remain dynamic and adaptable. Keeping an ear to the ground for these developments will equip organizations to better navigate the complexities of the modern business environment.
Sustainability and Lean
Sustainability is becoming a core tenet of lean enterprise thinking. It moves beyond mere efficiency to encompass environmental considerations. This shift is paramount as organizations face increasing pressure to operate sustainably while remaining competitive.
- Resource Optimization
Lean practices fundamentally advocate for the optimal use of resources. Integrating sustainability into these principles encourages organizations to minimize waste, not just in materials but also in energy consumption and emissions. - Circular Economy
The concept of a circular economy, which emphasizes the reuse and recycling of materials, complements lean thinking. Businesses that adopt circular practices not only enhance their sustainability credentials but also improve their economic resilience. - Stakeholder Engagement
There is a growing recognition of the importance of engaging stakeholders in sustainability efforts. Lean enterprises can utilize methods to understand stakeholder needs regarding environmental impact, thereby aligning operational practices with societal expectations.
"Sustainable lean practices are not merely a trend; they are an essential strategy for surviving in today's market."
In navigating this evolution, organizations can foster a culture that promotes continuous improvement and adaptability, ensuring their lean initiatives remain relevant and effective.