Logistics and Reverse Logistics: Roles and Impact
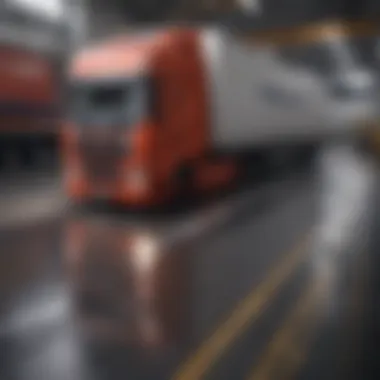
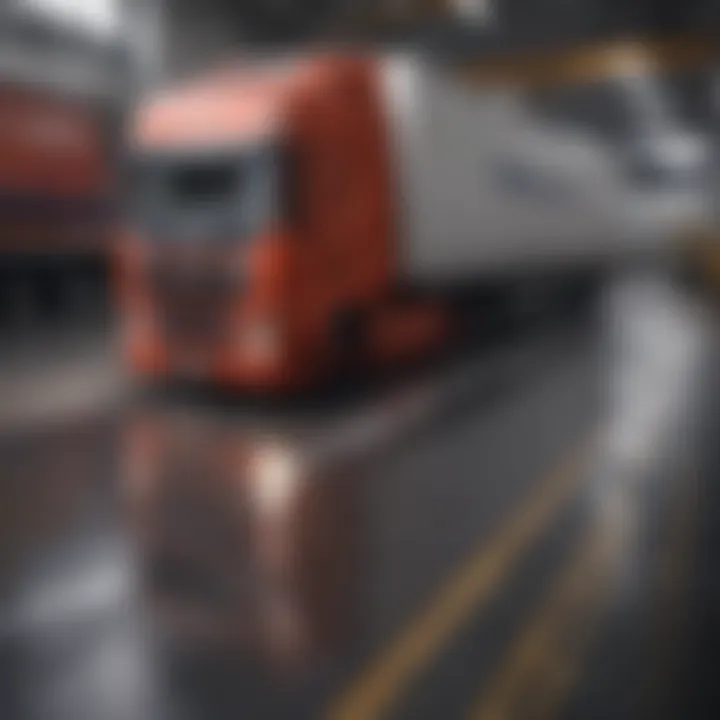
Intro
In today's fast-paced economic landscape, logistics has emerged as a cornerstone of effective supply chain management. While often viewed as a traditional domain focused on moving goods from point A to point B, it has evolved into a complex field that encompasses a myriad of components, each playing a significant role in overall efficiency.
Simultaneously, reverse logistics has gained traction, especially concerning sustainability and cost-effectiveness. These two areas, logistics and reverse logistics, intertwine, shaping not only operational efficiency but also impacting customer satisfaction, brand reputation, and environmental responsibility.
To fully appreciate their significance, it is essential to dive deep into these concepts, examining their definitions, key components, and the growing interdependencies that affect modern businesses.
Key Concepts
Definition of Primary Terms
- Logistics refers to the process of planning, implementing, and controlling the efficient flow and storage of goods, services, and related information from point of origin to point of consumption. It includes various functions such as transportation, warehousing, and inventory management.
- Reverse Logistics, on the other hand, encompasses all operations related to the reuse of products and materials. It involves processes such as returns management, repair, refurbishment, recycling, and disposal of waste. This sector is gaining importance due to rising consumer awareness about sustainability and the increasing focus on environmental stewardship.
Related Concepts and Theories
Understanding logistics and reverse logistics necessitates connecting several related theories and concepts:
- Supply Chain Management (SCM): This broader concept includes the flow of goods, information, and finances from suppliers to manufacturers to consumers. A good grasp of SCM helps in understanding how logistics and reverse logistics fit into the greater picture.
- Just-in-Time (JIT) Inventory: This philosophy emphasizes reducing waste and increasing efficiency by receiving goods only as they are needed. It closely relates to logistics in maintaining minimal inventory levels, impacting storage and transportation.
- Lean Manufacturing: This approach focuses on minimizing waste within manufacturing systems while simultaneously maximizing productivity. Both logistics and reverse logistics play a role in optimizing these practices.
"Success in logistics transformations hinges on collaboration and integration across supply chain entities, breaking down silos and fostering resilience."
Future Directions
Gaps Identified in Current Research
Upon reviewing current literature, some gaps emerge:
- Insufficient empirical data on the return on investment (ROI) associated with reverse logistics initiatives.
- Lack of comprehensive studies linking logistics efficiency directly to customer satisfaction metrics.
Suggestions for Further Studies
Future research could focus on:
- Developing standardized metrics to evaluate the performance of reverse logistics systems across industries.
- Exploring the technological advancements that can enhance transparency and tracking in both logistics and reverse logistics processes, such as blockchain or IoT systems.
Understanding Logistics
Understanding logistics is paramount in today's fast-paced and interconnected world. The very backbone of supply chains, logistics facilitate the smooth flow of goods, services, and information from origin to destination. This section will unfold the multi-faceted nature of logistics, illustrating its key importance in achieving overall business objectives.
Definition of Logistics
Logistics is essentially about managing the movement of products and materials to deliver them efficiently to the appropriate place at the right time. It combines various activities, including transportation, warehousing, inventory management, and sometimes, even after-sales service. Framing logistics within the broader context of supply chain management, it is about ensuring that every piece fits neatly into the puzzle, optimizing resources and ensuring customer satisfaction simultaneously.
Key Components of Logistics
Each element of logistics plays a unique role in ensuring that products reach consumers effectively. Taking a closer look:
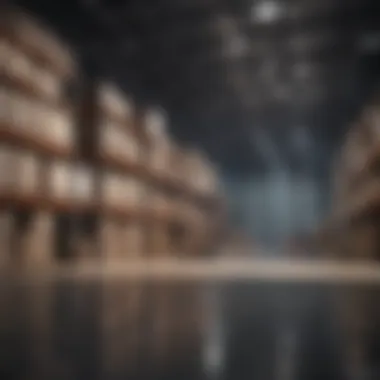
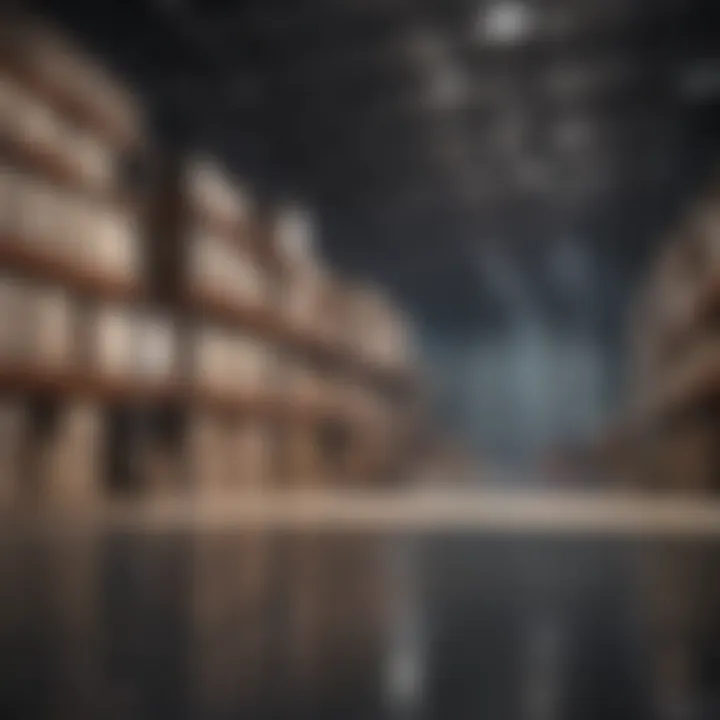
- Transportation: The lifeblood of logistics, transportation encompasses all modes of moving goods, whether by road, rail, air, or sea. It connects manufacturers, suppliers, and consumers. The choice of transportation can drastically affect the speed, cost, and reliability of delivery.
- Warehousing: This involves storing products until they are needed. The design of a warehouse can impact how quickly items can be retrieved and sent out to customers. Efficient warehousing reduces costs and improves service levels, making it essential in today's logistics strategy.
- Inventory Management: This is all about balancing supply with demand. Effective inventory management means knowing what products are in stock, what needs ordering, and what can be shipped to customers immediately. Poor inventory management can lead to stock-outs, excess inventory, or missed sales opportunities.
- Order Fulfillment: This includes every step from receiving the order to delivering it to the customer. The effectiveness of order fulfillment processes can influence customer satisfaction and loyalty, thus holding significant importance in logistics management.
The Role of Technology in Logistics
Technology drives efficiency in logistics like oil lubricates machinery. From automated storage systems to sophisticated routing software, technology shapes how logistics is executed.
- Automation: One cannot overlook automation in logistics. It helps in speeding up processes, reducing errors, and cutting down costs. For example, automated sorting systems in warehouses can quickly identify where goods need to go, greatly streamlining operations.
- Data Analytics: This has become crucial for decision-making. Organizations can analyze trends in logistics operations, customer preferences, and supply chain efficiencies, shaping strategies effectively. Data helps predict issues before they become problems, making logistics more responsive.
- Supply Chain Management Software: Using software like Oracle SCM Cloud or SAP Integrated Business Planning can transform how logistics is handled. These solutions offer insights into all aspects of the supply chain, ensuring a more coordinated approach to logistics management.
Logistics Strategies for Efficiency
Strategic approaches within logistics are key to improving efficiency and effectiveness.
- Just-in-Time (JIT): Aimed at reducing inventory costs, JIT ensures goods are produced or delivered just as they are needed. This strategy minimizes waste but requires precise coordination across suppliers and logistics partners.
- Lean Logistics: This methodology focuses on minimizing waste throughout the logistics process. By streamlining operations, companies can enhance efficiency, reduce unnecessary costs, and improve customer satisfaction.
- Integrated Logistics Management: This takes a holistic view by coordinating logistics across various functions, facilitating better communication and collaboration, which often leads to enhanced service levels and reduced costs.
Challenges in Logistics Management
Logistics management faces several obstacles that can hinder efficiency.
- Cost Control: Keeping operational costs down while trying to maintain service levels is a tightrope walk for logistics managers. Coordination is vital to avoid overspending while meeting customer demands.
- Regulatory Compliance: Varying regulations across countries and regions can complicate logistics. Understanding and adhering to these rules is essential to avoid hefty fines and disruptions.
- Globalization: As companies expand globally, managing logistics across borders introduces complexity. Cultural differences, varying market demands, and logistical challenges can make this a tough nut to crack.
Understanding logistics is not just about knowing the definitions; it involves grasping the complexities, strategies, and challenges that come with managing the flow of goods. This knowledge sets the stage for exploring reverse logistics and how it interrelates with traditional logistics functions.
Exploring Reverse Logistics
The landscape of supply chain management is rapidly evolving, and one of the integral components that has gained traction in recent years is reverse logistics. Understanding and implementing reverse logistics is not just an operational necessity; it is a strategic advantage that businesses can leverage to enhance efficiency, improve customer satisfaction, and contribute to sustainability goals. As companies focus on becoming more agile and responsive to consumer demands, entering the realm of reverse logistics becomes indispensable.
Definition and Importance of Reverse Logistics
Reverse logistics refers to the process of moving goods from their final destination back to the manufacturer or retailer for reasons such as returns, repairs, refurbishments, or recycling. Unlike traditional logistics, which focuses on forward flowādelivering products from suppliers to customersāreverse logistics emphasizes the backward flow.
This concept is critical because it addresses several modern-day challenges. A well-functioning reverse logistics system can significantly cut costs associated with returns, enhance brand loyalty by providing excellent customer service, and boost overall sustainability efforts. Companies that grasp the importance of this area are better positioned to manage their supply chains effectively while also catering to the environmentally conscious consumer.
Key Processes in Reverse Logistics
Return Management
Return management is a cornerstone of reverse logistics. It concerns handling returned products from customers, a process which can involve various steps such as authorization, inspection, refurbishing, and restocking.
A key characteristic of effective return management is its ability to streamline the process, thus minimizing the time and resources spent on handling returns. Efficient systems ensure that not only are products processed quickly, but also that customer interactions are smoothāleading to higher satisfaction rates. A unique feature of return management is its integration with customer service; a simple return can turn a potential negative experience into a loyal customer relationship. However, managing returns is not without its challenges, as increased volume can lead to complexities that strain resources.
Repair and Refurbishment
Repair and refurbishment involve assessing returned goods to determine whether they can be repaired and resold. This process is particularly relevant for electronics or furniture, where refurbished items can be offered at a lower price point while still retaining value.
The crucial aspect of repair and refurbishment is its potential for cost savings. Companies can recuperate losses by investing in repairs instead of writing off returned items as losses. This approach not only supports sustainability initiatives by reducing waste but also offers customers an affordable alternative. Still, these processes can require sophisticated logistics, as maintaining an efficient system to handle repairs can be resource-intensive.
Recycling and Disposal
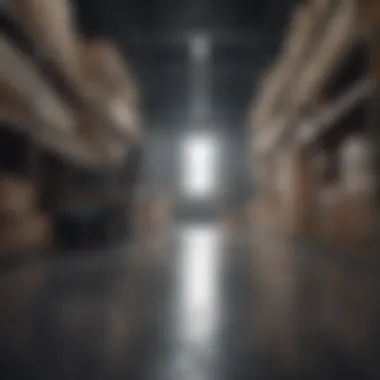
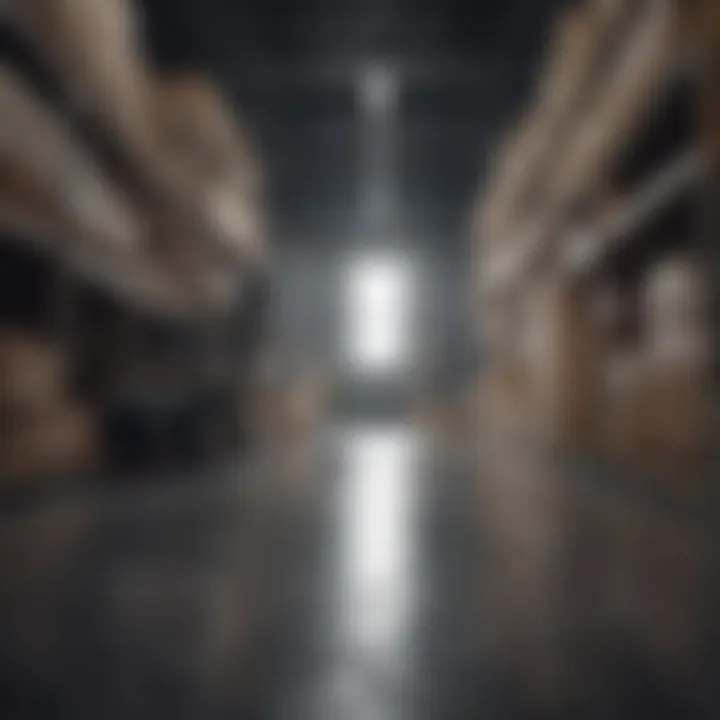
Recycling and disposal pose another significant aspect of reverse logistics, focusing on the responsible handling of products at the end of their lifecycle. With increasing regulations around waste and a strong push towards sustainable practices, companies are finding it in their best interest to develop systems for recycling and proper disposal.
A key characteristic of recycling is its capacity to reclaim valuable materials from worn-out products, significantly minimizing the need for new raw materials. The unique feature here is the environmental impact; businesses can boost their sustainability image while also adhering to governmental regulations regarding waste management. However, the complexities of establishing a recycling chain can often lead to additional costs, especially if adherence to regulations is not met.
The Economic Benefits of Reverse Logistics
Cost Recovery
Cost recovery is one of the significant economic benefits offered by effective reverse logistics. This practice allows companies to reclaim value from returned or unused products through refurbishing, reselling, or recycling.
This aspect stands out primarily due to its immediate impact on the bottom line. Instead of incurring losses from unsold or returned inventory, businesses can convert these assets back into cash flow. It is especially crucial during economic downturns, as recovering costs can help safeguard profitability. However, it is essential to have a structured process in place to measure the potential recovery against the associated logistical costs.
Inventory Optimization
Inventory optimization focuses on maintaining the right levels of stock throughout the supply chain, thus ensuring that the right products are available when needed. In reverse logistics, it pertains to how returned items are managed and reintegrated into inventory systems.
The key characteristic of this process is proactive management. By having a clear understanding of return patterns and inventory levels, companies can make educated decisions on stocking policies. This approach also enables firms to minimize excess stock that might lead to financial losses. Yet, the challenge lies in effectively forecasting returns, as unpredictability in return rates can complicate inventory management.
Customer Retention
Customer retention involves fostering long-term relationships with consumers and can significantly be influenced by effective reverse logistics practices. When a customer experiences a hassle-free return process, they are more likely to make repeat purchases.
The unique element of customer retention in reverse logistics is the relationship-building potential. Companies that provide seamless returns build trust and loyalty among their customers, translating to a competitive advantage in a saturated market. However, if not executed well, complicated return policies can lead to a loss of customers, making it essential to strike a balance.
Integration of Reverse Logistics into Supply Chains
Integrating reverse logistics into existing supply chain frameworks is paramount. Companies must view reverse logistics not as an afterthought but as a vital component from the onset. This integration ensures that resources are allocated effectively and creates a responsive system that adapts to consumer needs.
Challenges in Reverse Logistics Implementation
Implementing reverse logistics is not without its hurdles.
Complex Return Processes
Complex return processes often overwhelm both businesses and customers. A convoluted return policy can lead to frustration and discourage customers from shopping with a brand again.
A crucial characteristic of tackling this complexity is simplifying return procedures while ensuring compliance with company standards. A unique challenge here is balancing simplicity with thoroughness; while ease of returns can enhance consumer experience, it must not come at the cost of operational integrity, which can lead to losses.
Tracking and Documentation
Effective tracking and documentation are essential for managing reverse logistics. Every returned item needs a reliable tracking system to ensure accountability and visibility in the process.
One of the significant aspects of tracking is that it allows decision-makers to identify trends and optimize operations for the future. Proven methods, however, can sometimes lead to overhead in maintaining the documentation, particularly for small to mid-sized enterprises that might not have adequate resources.
Resource Allocation
Resource allocation is critical in ensuring an efficient reverse logistics process. Allocating too many resources towards this component can detract from other areas, while insufficient resources can lead to bottlenecks and inefficiencies.
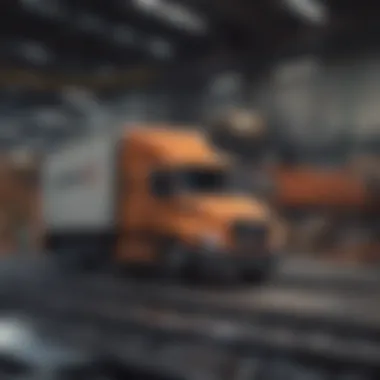
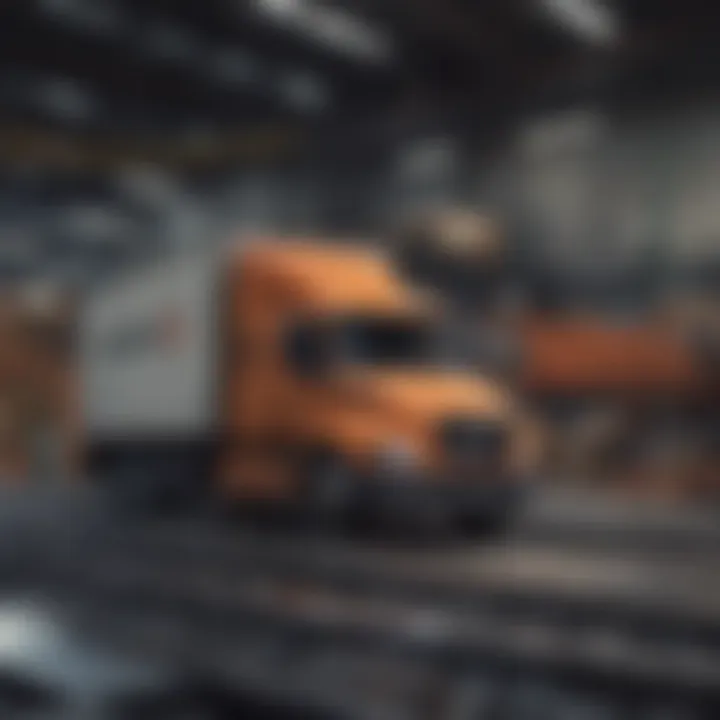
The important takeaway here is that firms need to establish clear priorities when it comes to resource distribution. A well-balanced approach can sustain a functional reverse logistics system while maximizing overall operational efficiency, but it requires careful attention and planning to get right.
In the ever-changing dynamics of supply chains, the interplay between logistics and reverse logistics can no longer be overlooked. By understanding and optimizing these processes, businesses stand to gain beyond just operational efficienciesāthey can enhance customer experiences and promote sustainable practices.
The Interrelationship Between Logistics and Reverse Logistics
Understanding how logistics and reverse logistics interconnect is crucial for any modern supply chain, making both operations smoother and more efficient. The relationship between these two domains is like the flip side of a coin. Efficient logistics can make reverse logistics less burdensome and vice versa, thereby optimizing overall operations, reducing costs, and improving customer satisfaction. When businesses recognize the synergy between these functions, they can implement strategies that enhance productivity.
How Logistics Supports Reverse Logistics
Logistics serves as the backbone of reverse logistics. When a product is returned, logistics systems are activated to ensure efficiency in product handling. This involves not just the transport of goods back to warehouses but also managing returns in a way that minimizes delays.
For instance, if a customer decides to send back a pair of shoes they bought online, the logistics team is responsible for coordinating the return shipment. They track the returned item, update inventory status, and ensure itās processed swiftly. By optimizing transportation routes and warehouse space, logistics can significantly reduce return processing times, making the process seamless for both the customer and the company.
The Feedback Loop: Customer Experience and Return Policies
A solid feedback loop exists between customer experience and return policiesāone that can ultimately enhance customer loyalty. Businesses that maintain a straightforward return process tend to encourage repeat purchases. Logistic systems that support easy returns express a commitment to satisfied customers. This, in turn, reflects positively on the brand.
Customers feel more confident making purchases knowing they wonāt be stuck with a product they donāt want; this can increase the average order value. A clear return policy, coupled with efficient logistics to handle returns, creates a win-win situation. The smoother this process is, the more likely customers are to leave favorable reviews or refer friends, thereby enhancing the companyās reputation.
Case Studies of Successful Integration
Retail Industry Examples
A prominent example can be found in the online retail giant Amazon. Their well-known return process is a key aspect of their business model. When customers decide to return items, Amazon has enabled logistical mechanismsāsuch as drop-off points at local storesāthat make returns as easy as pie. This ease of return not only drives customer satisfaction but also fosters loyalty. The ability to handle returns quickly and effectively enhances their logistical efficiency.
One unique feature of Amazonās approach is the simplicity of their return instructions. The clarity with which they communicate return steps ensures customers experience minimal frustration, thus reinforcing their global position in online retail.
Manufacturing Sector Insights
In the manufacturing sector, a noteworthy case is that of Dell. Dell integrates reverse logistics into its supply chain by recycling old parts from used computers, which are then refurbished and reused. This not only reduces waste but also saves cost in parts procurement. The companyās focus on reverse logistics helps them stay sustainable while meeting customer satisfaction.
The unique aspect here is Dellās proactive approach to include customers in the process of recycling their products. This initiative is two-facetedāenhancing Dellās corporate responsibility and boosting consumer engagement, thus aligning with contemporary ethical marketing trends.
Future Trends in Logistics and Reverse Logistics
Looking ahead, the fields of logistics and reverse logistics are set for significant evolution. To stay ahead, businesses must recognize future trends that influence their operations.
Sustainability Practices
Sustainability will play an increasingly integral role in logistics. Companies adopting green policies are becoming more popular among consumers who seek to lessen their environmental footprint. Through the integration of sustainable practices in logistics, businesses can not only reduce waste but also appeal to a more eco-conscious customer base.
A unique feature of sustainability practices in reverse logistics is their dual purpose; they help the environment while polishing a companyās image as a responsible brand. This can result in increased sales and customer loyalty.
Technological Advances
Technology is marching forward at a rapid pace. Innovations like artificial intelligence and machine learning are redefining how logistics and reverse logistics are managed. These technologies help in orchestrating more precise inventory levels and predictive analytics, making the logistics process faster and more accurate.
The unique feature here is the adaptability of these technologies; companies can tailor them according to specific operational needs, thus maximizing their efficiency.
Customer-Centric Approaches
Lastly, placing the customer at the heart of both logistics and reverse logistics operations tends to yield fruitful results. Creating tailored experiences based on customer data can optimize the service provided. For instance, analyzing purchase patterns can help companies adjust their return processes or inventory management strategies accordingly.
In summary, the interrelationship between logistics and reverse logistics propels organizations toward smoother operations, but it also calls for adaptation to emerging trends that shape the industry. Each function plays a vital role in achieving overall supply chain success. As businesses increasingly prioritize customer satisfaction and sustainability, understanding this delicate balance will become more essential.