Modeling Sheet Metal Parts: Techniques and Considerations
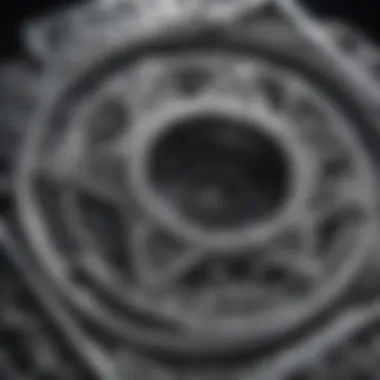
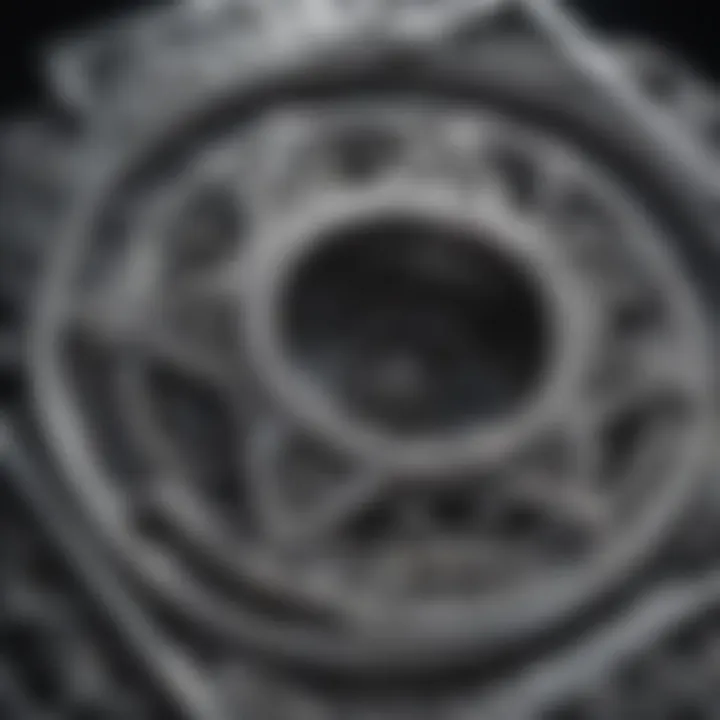
Intro
In the realm of engineering design, the modeling of sheet metal parts holds significant importance. As industries advance, the requirements for effective and efficient components become ever more demanding. Engineers must understand various techniques and considerations when designing parts to ensure they meet both functional and aesthetic needs.
This article aims to serve as an in-depth guide for students, researchers, educators, and professionals. It will explore key techniques and methodologies essential for modeling sheet metal parts, focusing on material properties, design considerations, and industry standards that influence the modeling process. By understanding these factors, one can enhance their ability to create components that not only function well but also adhere to the required specifications.
Key Concepts
Definition of Primary Terms
Modeling sheet metal parts involves creating a virtual representation of a component made from thin sheets of metal. The key terms in this process include:
- Sheet Metal: Thin and flat pieces of metal, which come in various thicknesses and materials.
- Bending: The process of deforming the sheet metal about a certain axis.
- Flanging: The turning of the edge of the sheet metal at a predetermined angle, increasing its strength.
- Cutting: The method of removing metal to achieve the desired shape, commonly using tools like lasers or shears.
- Forming: Techniques used to shape the metal into a specific configuration by applying force.
Related Concepts and Theories
The principles governing sheet metal modeling derive from various engineering and material sciences concepts. Important theories include:
- Manufacturing Processes: Understanding how different methods affect the final product's characteristics is crucial. Each process, from stamping to welding, influences material properties and tolerances.
- Material Science: Knowledge of how different metals react to heat and stress will determine the suitability of a material for specific applications.
- Finite Element Analysis (FEA): A computational technique used for predicting how components respond to physical effects, such as heat and stress, is essential in modeling.
"Effective modeling of sheet metal parts requires a holistic understanding of material properties, mechanical behaviors, and manufacturing intricacies."
Future Directions
Gaps Identified in Current Research
While considerable progress has been made in modeling sheet metal parts, notable gaps still exist. For instance, there is a need for more research on modeling complex geometries and their associated manufacturing challenges. The integration of intelligent algorithms for optimizing sheet metal designs is another area that merits further exploration.
Suggestions for Further Studies
To address the identified gaps, future studies should consider:
- Investigating new materials that could enhance the durability and functionality of sheet metal components.
- Exploring the application of advanced machine learning techniques in the modeling process to improve accuracy.
- Assessing the impact of environmental factors on the performance of sheet metal parts in real-world applications.
By delving into these areas, engineers and researchers can contribute to a more comprehensive understanding of sheet metal modeling practices. This knowledge not only enhances design capabilities but also promotes innovation in engineering solutions.
Foreword to Sheet Metal Modeling
Modeling sheet metal parts is a critical aspect of engineering design. It involves understanding the unique properties of metal sheets and how they can be manipulated to create complex shapes. Sheet metal modeling not only enhances the aesthetic qualities of products but also significantly impacts their functionality and manufacturability. The accuracy in design translates to reduced material waste and increased efficiency in production processes.
The techniques used in modeling require a comprehensive grasp of material behavior under different conditions, including bending, stretching, and cutting. Each aspect involves specific considerations that must be understood by engineers and designers alike. One key benefit of mastering these skills is the ability to develop designs that are both innovative and practical.
Effective sheet metal modeling can lead to significant advantages in various engineering applications. These include optimized assembly processes and improved performance characteristics of finished products. The result is a design outcome that not only meets the specifications but also adheres to industry standards.
In addition to enhancing manufacturing processes, proficient modeling can contribute to sustainability efforts. By optimizing designs, manufacturers can minimize waste and utilize resources more effectively.
Engaging with this knowledge equips professionals and students with important skills, paving the way for advancements in diverse fields such as automotive, aerospace, and electronics. Thus, understanding the foundations of sheet metal modeling is not just an academic exercise but a valuable investment in one’s career and in the industry as a whole.
Overview of Sheet Metal Parts
Sheet metal parts are fundamental components in many engineering and manufacturing sectors. These parts are created by cutting, bending, and assembling thin sheets of metal. Common materials used include steel, aluminum, and copper. Each type of metal has its own set of properties that affect the choice of material for specific applications.
The versatility of sheet metal allows for a wide range of applications, from automotive body panels to electronic casings. The ability to form intricate shapes and features contributes to the effectiveness and efficiency of these parts. By understanding the geometric possibilities, designers can push boundaries and create innovative structures.
Key features of sheet metal include:
- Bend radius: This refers to the curvature of the bend in the metal, impacting how the part performs once manufactured.
- Flange: A flat piece of metal that adds strength and rigidity to a design.
- Cutouts: Openings made for functional purposes, such as weight reduction or to allow for other components.
Importance in Engineering Applications
The relevance of sheet metal components in engineering cannot be overstated. From structural applications in buildings to precise mechanisms in machinery, sheet metal parts play a vital role. They offer critical functionality while maintaining a balance between strength and weight.
In fields like automotive engineering, the performance of vehicles often relies heavily on the use of sheet metal. Efficiency in manufacturing these parts translates to both cost savings and improved vehicle performance.
Moreover, the integration of advanced manufacturing techniques like laser cutting and CNC machining has revolutionized the production capabilities. With these technologies, complex designs can be realized more easily, making it crucial for engineers to keep pace with these advancements.
"The ability to create lightweight, strong components with intricate geometries makes sheet metal a preferred choice in modern engineering applications."
Finally, the adaptability of sheet metal also impacts sustainability initiatives. With proper design strategies, manufacturers can drastically decrease material wastage, aligning with green engineering principles. This holistic view of modeling sheet metal parts highlights not only their technical significance but also their contribution to the evolving landscape of manufacturing.
Understanding Sheet Metal Properties
Understanding the properties of sheet metal is essential for effective modeling and design in engineering applications. This section delves into various elements that define sheet metal properties, influencing both its performance and manufacturability. A comprehensive grasp of material types and their characteristics, along with thickness and gauge considerations, ensures that designers can create components that meet specific requirements in terms of strength, weight, and flexibility.
Material Types and Characteristics
The selection of material used in sheet metal fabrication is crucial. Different materials exhibit varying properties which can significantly affect the final product's performance. Common materials include steel, aluminum, brass, and copper.
- Steel is known for its strength and durability but may corrode unless treated.
- Aluminum offers a favorable strength-to-weight ratio, making it ideal for lightweight applications.
- Brass and copper provide good corrosion resistance and are often used in decorative and electrical components.
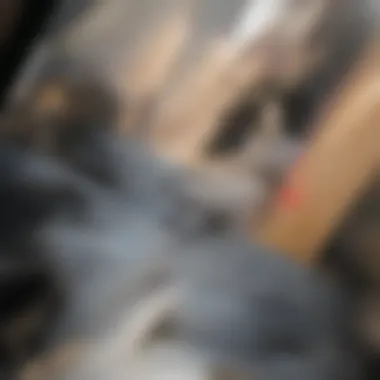
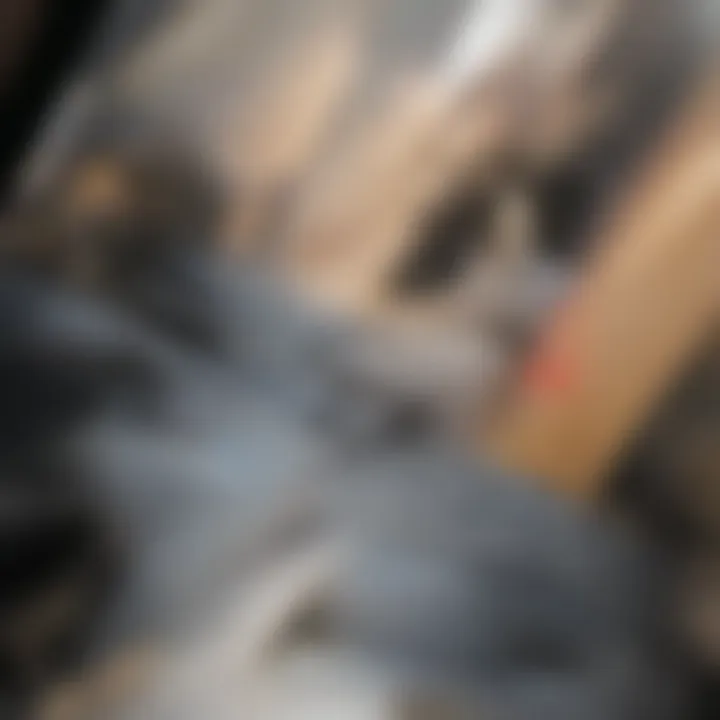
Each material has its unique characteristics:
- Mechanical Properties: These include tensile strength, yield strength, and ductility, all fundamental for determining how a material behaves under stress.
- Corrosion Resistance: The ability of a material to withstand environmental factors without deteriorating is a significant consideration.
- Thermal Conductivity: Important for applications where heat dissipation is a factor, materials with high thermal conductivity may be preferred.
When selecting a material, engineers must consider the intended application and the operating environment to ensure that the chosen material aligns with the project requirements.
Thickness and Gauge Considerations
The thickness and gauge of sheet metal have profound implications for both the design and functionality of the part. Gauge refers to the thickness of the material, with a lower gauge number indicating a thicker sheet. Understanding these factors leads to better design decisions.
- Strength: Thicker materials generally provide higher strength and can withstand greater loads. However, they also increase weight, which may be a limiting factor in some applications.
- Workability: Thinner sheets are easier to manipulate and form, but they may lack the robustness required for certain applications. Designers often face a trade-off between strength and workability.
- Cost: The cost of materials can also vary with thickness. Thicker materials typically are more expensive, influencing budget decisions during the design process.
It is vital to balance these considerations to arrive at an optimal choice as they impact the overall effectiveness and efficiency of the part. For instance, using a moderately thick aluminum sheet might combine both lightweight properties and sufficient strength for an aircraft component.
Principles of Sheet Metal Design
The principles of sheet metal design play a critical role in the effective modeling and manufacturing of components in various engineering fields. Understanding these principles ensures that designers create parts that are not only functional but also have optimal manufacturability and performance. Key elements include the considerations for manufacturing processes, material characteristics, and the anticipated stress and load conditions that the parts will encounter during their lifecycle.
Design for Manufacturability
Design for manufacturability involves creating a design that is easy to produce while minimizing costs and maximizing efficiency. This principle emphasizes the need to take into account the capabilities and limitations of production processes during the early stages of design. Here are some specific considerations:
- Process Compatibility: Designs must be compatible with the specific methods used for cutting, bending, welding, and assembling parts. Understanding the nuances of these processes is essential for a successful outcome.
- Material Selection: The choice of material can significantly influence manufacturability. Different materials respond uniquely to fabrication techniques. For instance, metals like aluminum are easier to work with than harder materials such as stainless steel.
- Simplicity in Design: Designs that use a minimal number of features and components not only streamline the production process but also reduce chances for errors. A simple design is usually more cost-effective to manufacture.
By emphasizing these factors, engineers can enhance efficiency and quality in sheet metal production, ultimately speeding up time to market.
Stress and Load Considerations
Stress and load considerations are imperative to ensure that sheet metal parts can withstand operational demands without failure. These factors influence the choice of materials, design methodology, and the overall performance of components. Important aspects include:
- Understanding Load Types: It is crucial to differentiate between static and dynamic loads. Static loads remain constant, whereas dynamic loads can change based on operational conditions. Each type requires different approaches in design and materials.
- Material Strength: The yield strength and tensile strength of the chosen material must be thoroughly evaluated. The design should aim to prevent stress concentrations which can lead to premature failure.
- Safety Factors: Establishing appropriate safety factors is essential in design. This involves designing parts to withstand loads above expected maximums, hence ensuring reliability in various applications.
The consideration of stress and load not only guarantees the reliability of a design but also significantly affects its lifespan and performance.
To summarize, grasping the principles of sheet metal design equips engineers and designers with the knowledge needed to create effective, manufacturable, and reliable components. By focusing on manufacturability and understanding the effects of stress and load, one can achieve superior outcomes in sheet metal modeling.
Modeling Software and Tools
In the domain of sheet metal modeling, the selection of appropriate software and tools is paramount. These tools serve as the backbone for accurately designing parts that meet specified requirements. Not only do they enhance productivity, but they also ensure that the end product is both functional and manufacturable. Understanding the capabilities of different software is essential for designers to make informed choices that align with project goals. Factors such as ease of use, integration with other systems, and the ability to conduct simulations contribute to the overall effectiveness of sheet metal design processes.
Popular Software Platforms
Various software platforms dominate the sheet metal modeling landscape. Each program offers unique features that can cater to different user requirements. Some of the most prominent tools include:
- SolidWorks: Renowned for its robust parametric design capabilities, SolidWorks allows engineers to create complex geometries with relative ease. Its sheet metal module supports features like bends, flanges, and cutouts, which are vital in sheet metal design.
- Autodesk Inventor: This tool excels in creating 3D models and is well-regarded for its assembly modeling features. It also has a dedicated sheet metal environment that enables the creation of parts with dynamic properties.
- CATIA: Used extensively in aerospace and automotive industries, CATIA offers advanced surface modeling capabilities. Its sheet metal design tools facilitate intricate parts that require high precision and advanced engineering techniques.
- NX by Siemens: NX is lauded for its integrated simulation tools, allowing users to validate designs early in the development process. Its parametric approach to sheet metal modeling helps streamline workflows and improve accuracy.
These platforms support various applications and industries, making them essential in the toolkit of today’s engineers.
Comparison of Features and Capabilities
When evaluating sheet metal modeling software, several features must be considered to determine which tool best suits particular needs. Key aspects include:
- User Interface: A clean and intuitive interface enhances productivity. Engineers should select software that allows for a smooth transition into sheet metal design without steep learning curves.
- Bend and Unbend Algorithms: Accurate algorithms are critical to ensure proper manufacturing outcomes. Some software efficiently calculates bend allowances, providing a more realistic representation of sheet metal characteristics.
- Sheet Metal Toolsets: The availability of specialized tools like automated lofting, punch design, and template creation can significantly reduce modeling time and increase efficiency.
- Simulation Capabilities: Advanced tools offer integrated simulation features that allow users to test designs under various conditions. For example, Finite Element Analysis (FEA) can predict how a part will behave once in use, offering insight into potential failures.
- Interoperability: The ability of software to exchange data with other platforms is another critical consideration. This ensures that design modifications can occur without disrupting entire workflows.
"Choosing the right software is not just about features but also ease of integration and future proofing for upcoming technologies."
In summation, exploring the realm of software tools is essential for anyone involved in sheet metal modeling. By understanding various capabilities, designers can make choices that will streamline their processes and enhance the quality of their work.
Geometric Features in Sheet Metal Parts
Geometric features are essential in the design and functionality of sheet metal parts. Understanding these features helps engineers create components that are not only accurate but also optimized for manufacturing and assembly. Each geometric feature, whether it be bends, flanges, holes, or cutouts, serves specific purposes within the overall design. These considerations can greatly influence the performance, strength, and manufacturability of the final product.
In modeling sheet metal parts, attention to geometric detail is crucial. Features need to be designed in a way that ensures the part will function correctly and meet the required specifications. Moreover, recognizing the constraints imposed by the material properties and the intended applications can lead to better design decisions.
Benefits of emphasizing geometric features include:
- Increased Structural Integrity: Properly designed features enhance the strength of the part while maintaining lightweight characteristics.
- Ease of Fabrication: Simplified features can reduce manufacturing time and costs, minimizing waste.
- Enhanced Performance: Features like bends can affect how a part behaves under load, affecting its overall performance in real-world applications.
Overall, a comprehensive understanding of geometric features aids in achieving precise models and successful outcomes in sheet metal design.
Simulation and Analysis in Modeling
The significance of simulation and analysis in modeling sheet metal parts cannot be overstated. These practices extend beyond mere modeling; they enhance the design process by providing critical insights into how materials will behave under various conditions. Such insights ultimately ensure that the manufactured products meet specifications and perform effectively in their intended applications.
Moreover, simulation assists engineers in visualizing complex interactions within the component. This assists in identifying potential points of failure, thus improving the reliability of the final product. The precision brought by simulation techniques allows for better decision-making throughout the design process.
Finite Element Analysis Applications
Finite Element Analysis (FEA) is a pivotal aspect of the simulation phase in sheet metal modeling. This method entails breaking down complex structures into smaller, manageable elements. Engineers can analyze each element under different loads and conditions. By doing so, precise calculations are made regarding stress, strain, and thermal responses.
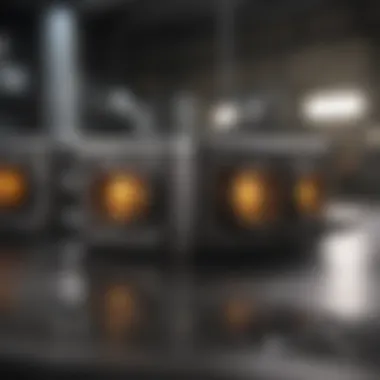
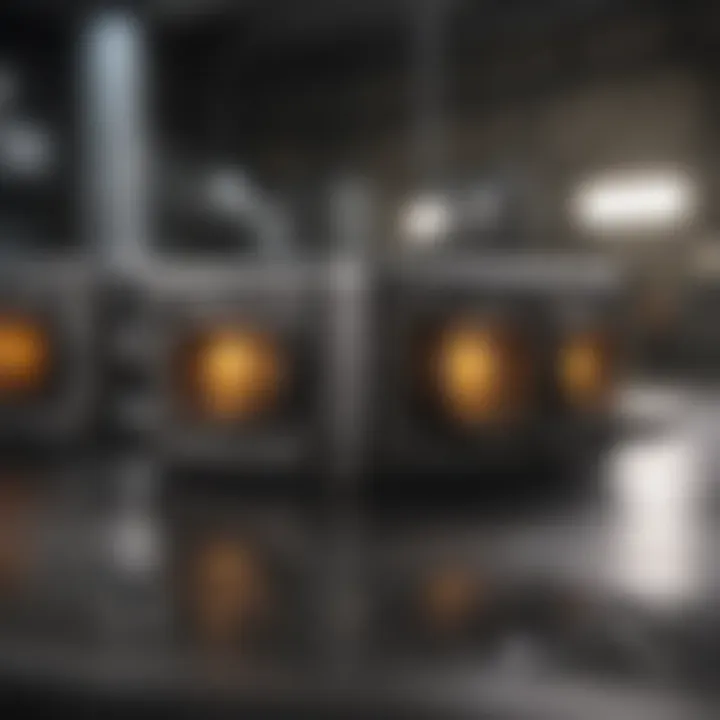
FEA enables quick iterations in design, which is essential for optimizing the performance of sheet metal components. Also, the graphical representation of deformation and stress distribution aids in understanding how parts will react to real-world conditions. Applications of FEA include:
- Predicting failure points in critical components
- Assessing the impact of geometric changes on performance
- Evaluating the effects of temperature variations
Through its extensive applications, FEA solidifies its role in ensuring efficient design modifications prior to production, thus saving time and costs.
Stress Testing and Performance Evaluations
Stress testing is another crucial component in the simulation and analysis phase. It involves applying various forces and conditions to a model to ascertain its durability and strength. By simulating stress scenarios, engineers can evaluate how sheet metal parts will endure operational demands.
Performance evaluations, conducted alongside stress tests, focus not only on material strength but also on functionality under diverse conditions. This can include:
- Evaluating fatigue over time
- Analyzing effects of impact loading
- Determining the factors of safety in different usage scenarios
Together, stress testing and performance evaluations provide an in-depth understanding of a component's reliability. Additionally, they offer insights into possible enhancements and alternative designs to address identified weaknesses.
Fabrication Processes for Sheet Metal
Fabrication processes are essential in transforming raw sheet metal into usable parts. Understanding these processes is vital for engineers and designers involved in sheet metal modeling. They must consider how each process will affect material choices, precision, and final product performance. The process not only defines the functionality but also the efficiency and cost-effectiveness of manufacturing.
When discussing fabrication processes, it is important to recognize two primary methods: cutting and forming. Both methods play a significant role in shaping and assembling parts, which ultimately influences the design phase.
Cutting Methods
Cutting methods are the first step in the fabrication process. This includes various techniques that can adjust the material dimensions and prepare the sheet metal for further processing. The significance of cutting cannot be overstated as accuracy directly affects subsequent steps. Common cutting methods include:
- Laser Cutting: This technique uses focused laser beams to create precise cuts. It offers high accuracy and minimal thermal distortion, making it suitable for complex geometries.
- Waterjet Cutting: A high-pressure stream of water, often mixed with abrasives, is used to cut through materials. This method is favorable for heat-sensitive materials since it avoids thermal-induced changes.
- Mechanical Cutting: Traditional methods like shearing and band saw cutting fall under this category. They are efficient for straightforward operations but may not handle intricate details well.
When selecting a cutting method, factors like material thickness, tolerance requirements, and production volume must be evaluated. Additionally, understanding the effects of each method on the material is crucial. For instance, laser cutting may introduce heat-affected zones that alter the material's properties, while mechanical cutting reduces stresses during the process.
Forming and Welding Techniques
After cutting, forming and welding techniques come into play. These processes shape the metal and assemble parts, which is a critical phase in fabrication.
- Bending: A common forming operation creates angle changes in sheet metal. It can be done using press brakes, which apply force at the bend point, or roll forming, which continuously rolls the material into desired shapes.
- Stamping: This method uses a die to produce parts from sheet metal. It allows for high-volume reproduction of identical components and can incorporate intricate designs.
- Welding: Joining is essential as it connects different sheet metal parts into a complete assembly. Various techniques, like MIG (Metal Inert Gas) and TIG (Tungsten Inert Gas) welding, each have unique advantages depending on the application.
Welding also presents risks, such as distortion and loss of material strength. Engineers must pay attention to the welding method relative to the type of metal used. Each technique requires specific settings and approaches which can influence the end product.
Understanding the importance of these processes facilitates better planning and execution in sheet metal projects. Therefore, integrating knowledge of cutting methods with forming and welding techniques helps in creating efficient and effective designs.
Industry Standards and Compliance
In the realm of sheet metal modeling, adhering to industry standards is not merely a formality; it serves as a crucial foundation that ensures quality, safety, and reliability in the final products. Compliance with established standards significantly impacts the modeling process, influencing design choices and material selection, and ultimately affecting manufacturability and cost efficiency. Understanding these standards is essential for professionals engaged in design, manufacturing, or quality assurance within the field of engineering.
Standards, particularly those defined by the International Organization for Standardization (ISO), provide guidelines that streamline processes and establish a common technical language. Integrating these standards into modeling practices assures that parts can be efficiently manufactured and those stringent quality measures are consistently met. This compliance mitigates the risk of costly errors and rework during the production phase.
Some of the prominent advantages of adhering to industry standards include:
- Enhanced Quality Control: Implementing ISO standards fosters systematic processes, ensuring high-quality output that meets customer expectations.
- Improved Safety: Standards often incorporate safety guidelines, reducing the risks associated with design and production defects.
- Market Competitiveness: Companies that demonstrate compliance are more likely to gain a competitive edge in the marketplace, as clients often prefer organizations that adhere to recognized standards.
- Global Recognition: ISO standards promote international trade by ensuring that products meet universally accepted criteria, simplifying the process of entering foreign markets.
Relevant ISO Standards
ISO standards for sheet metal fabrication define specific practices and criteria that guide engineers and manufacturers. The following are some key ISO standards relevant to sheet metal parts:
- ISO 9001: This standard focuses on quality management systems, ensuring consistent quality in products and services.
- ISO 1461: This standard specifies the requirements for hot dip galvanized coatings on fabricated iron and steel articles.
- ISO 10131: It outlines the standardized terms and definitions related to sheet metal products and their fabrication processes.
Each of these standards addresses different facets of the sheet metal modeling process, ensuring that practitioners have well-defined protocols to follow.
Regulatory Considerations for Manufacturing
Regulatory compliance in manufacturing is essential, particularly in high-stakes industries such as aerospace, automotive, and medical devices. Regulations imposed by government bodies ensure that products not only perform as intended but also uphold health and safety standards. For instance, in the United States, standards from organizations such as the Occupational Safety and Health Administration (OSHA) and the Environmental Protection Agency (EPA) directly influence the protocols adopted in sheet metal fabrication.
Key regulatory considerations can include:
- Environmental Impact: Manufacturers must be aware of their processes' environmental ramifications and follow regulations regarding waste disposal and emissions.
- Workplace Safety: Compliance with safety standards protects workers and reduces liabilities associated with workplace accidents.
- Product Certification: Certain industries require product certification to validate that components meet established standards.
Adhering to these regulatory requirements safeguards not only the company's reputation but also its legal standing. Effective compliance measures are vital in ensuring that all products meet necessary safety and performance benchmarks.
Challenges in Modeling Sheet Metal Parts
Modeling sheet metal parts can be intricate due to several challenges that need careful attention. These challenges are crucial because they can impact the quality, manufacturability, and performance of the final product. The modeling process requires a deep understanding of the interactions between design parameters, material properties, and manufacturing techniques. Each challenge presents its own set of implications for engineers and designers.
Common Mistakes in Design
Errors in sheet metal design often stem from a lack of awareness about the unique characteristics of the material. One common mistake is ignoring the properties of the sheet metal being used. For example, the thickness of the material should directly influence the design choices. If a designer overlooks this aspect, it can lead to structural weaknesses.
Other mistakes include improper tolerances and forgetting about the bend allowance. Tolerances need to be set with precision to avoid issues during the fabrication phase. Neglecting the bend allowance could result in misaligned parts and wasted materials. Additionally, failing to think about assembly processes can lead to designs that are difficult or impossible to fabricate.
Design calculations should also consider tools and equipment limitations. Relying on standard practices rather than tailoring approaches to specific projects can hinder optimal results. A thorough understanding of potential pitfalls can minimize mistakes, greatly improving the workflow and final outcomes.
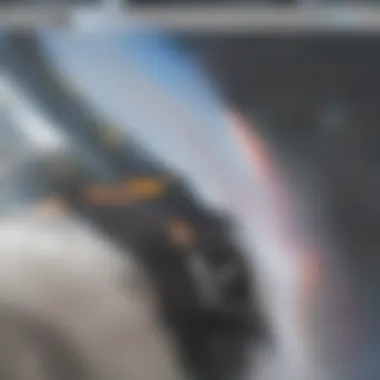
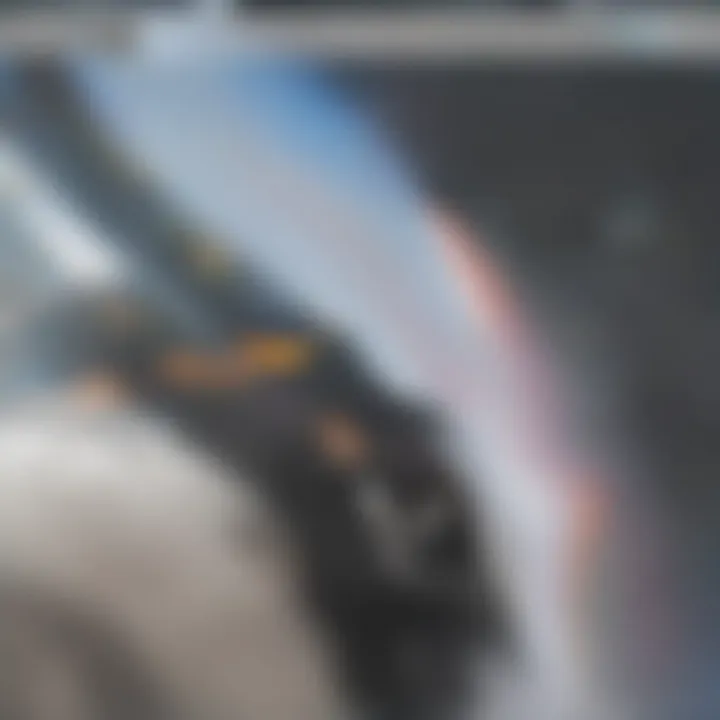
Overcoming Design Limitations
To tackle the design limitations in sheet metal modeling, several strategies can be employed. First, designers must engage in a continuous learning process to stay updated on the latest materials and technologies. Knowledge of advanced simulation tools can enhance their ability to predict how designs will behave under real-world conditions.
Collaboration between engineers and manufacturers is also essential. An open dialogue can bring insights that might not be immediately evident in the initial design stages. For instance, input from fabricators can highlight practical concerns that need consideration before production begins.
Prototyping is another effective method to test designs before full-scale production. Creating prototypes allows for adjustments and fine-tuning. This iterative process can save time and costs in the long run.
Finally, utilizing standardized practices while allowing for customization can help balance efficiency with creativity. Embracing these strategies can lead to more robust and manufacturable designs while ensuring high-quality outcomes in sheet metal fabrication.
"Anticipating challenges in sheet metal modeling is crucial for achieving success in the engineering process."
Overall, confronting the challenges in modeling sheet metal parts requires diligence and a proactive approach. Understanding the common mistakes and knowing how to overcome design limitations can lead to better outcomes in engineering projects.
Future Trends in Sheet Metal Modeling
In the rapidly evolving field of engineering, future trends in sheet metal modeling play a critical role. These trends directly influence how engineers and designers approach the development of effective solutions in the manufacturing process. The focus on emerging technologies and integration with automation signifies the shift towards increased efficiency and precision in the industry.
Emerging Technologies
Emerging technologies in the field of sheet metal modeling are reshaping traditional practices. Innovations such as 3D printing and computer-aided design (CAD) tools enhance the precision of modeling and fabrication processes.
- 3D printing allows for rapid prototyping, enabling designers to quickly test and modify designs before committing to production. This approach significantly reduces material waste and cuts down on time from concept to production.
- Advanced simulation software provides a deep insight into material behavior under various conditions. Tools like Siemens NX and SolidWorks are evolving to incorporate real-time feedback mechanisms, aiding in optimizing designs for manufacturability.
- Generative design employs algorithms to explore numerous design alternatives based on defined constraints. This fosters innovative configurations that would not be considered in conventional design.
As these technologies mature, they promise to deliver more sustainable solutions while maintaining strict tolerances and enhancing overall design quality.
Integration with Automation and AI
The integration of automation and artificial intelligence (AI) into sheet metal modeling signifies a profound leap forward.
Automation streamlines repetitive tasks, allowing engineers to focus on more complex design challenges. By automating the cutting and forming processes, production can be scaled effectively, minimizing human error and speeding up turnaround times.
On the other hand, AI will enhance decision-making within modeling. Machine learning algorithms analyze data from previous projects, suggesting optimal design modifications and predicting potential manufacturing challenges. Key benefits include:
- Increased accuracy: AI systems can analyze vast datasets, offering insights that improve precision in modeling.
- Predictive maintenance: By forecasting potential equipment failures, AI contributes to more reliable production environments.
- Customization capabilities: AI can help in designing customized sheet metal parts swiftly, aligning with specific client needs and requirements.
The convergence of automation and AI is fundamentally redefining how sheet metal parts are designed and produced—making future processes not just faster but smarter.
By understanding these future trends, professionals can prepare to adapt and leverage new tools and methodologies. Remaining agile in adopting these advancements will be essential for engineers and designers aiming to remain competitive in the field of sheet metal modeling.
Case Studies in Sheet Metal Design
Case studies in sheet metal design offer invaluable insights into real-world applications and challenges faced during the modeling and fabrication process. They serve as practical examples that demonstrate the successful implementation of techniques and the importance of careful consideration in various stages of design. Understanding these case studies allows engineers and designers to learn from others' experiences, refine methodologies, and avoid common pitfalls. It also illuminates how theoretical knowledge translates into practical results, ultimately enhancing the proficiency of professionals in the field.
Analysis of Successful Projects
Successful projects in sheet metal design often highlight best practices and innovative approaches that can be replicated in future work. For instance, one notable project involved the design of a custom airframe for aerospace applications. The key to success in this project lay in the thorough understanding of material properties, the use of advanced software tools, and effective communication among the design team.
- Material Selection: The team chose aluminum for its strength-to-weight ratio, crucial for aerospace components.
- Utilization of CAD Software: By employing SolidWorks, designers were able to visualize and simulate the assembly of the airframe before any physical work began. This helped identify potential manufacturing issues early.
- Iterative Prototyping: Rapid prototyping was pivotal in refining designs. Mock-ups allowed the team to test fit and function in real conditions, which led to design adjustments that improved overall performance.
These elements showcase the integration of cutting-edge technology and effective teamwork that drives successful outcomes in sheet metal design.
Lessons Learned from Failures
Examining failed projects provides critical lessons that guide future endeavors in sheet metal modeling. Consider a case where a manufacturing company attempted to produce a complex enclosure for electronic components but faced severe challenges.
- Design Oversights: Initial designs did not account for thermal expansion, leading to fit issues during assembly.
- Inadequate Testing: The prototype was not subjected to rigorous stress testing before production, which resulted in a high failure rate of the final product.
- Poor Documentation: Lack of clear documentation slowed down the troubleshooting process, complicating the inability to replicate success for future models.
This failed case underscores the importance of thorough testing, proper design validation, and effective documentation. Every design aspect must be methodically assessed to prevent similar mistakes, which could have significant financial repercussions and damage a company's reputation.
"Learning from failures is as critical as celebrating success. Each mistake is an opportunity to enhance competence and improve future designs."
End and Future Directions
The conclusion and future directions section encapsulates the essential findings of this article. It serves as a bridge connecting the current understanding of modeling sheet metal parts with the evolving landscape of engineering technologies. A clear understanding of both is crucial for advancing practices and methods in this field.
As we have seen, modeling sheet metal parts involves a nuanced grasp of material properties, design principles, and fabrication processes. The importance of precise models cannot be understated, as they directly relate to the functionality and manufacturability of engineered components. Moreover, the integration of simulation tools enhances the design process, allowing for more accurate predictions of physical behavior under actual conditions.
Looking ahead, the future of sheet metal modeling is tied to advancements in computational technology. Emerging techniques, such as machine learning and artificial intelligence, promise to redefine how engineers approach design. Automation is likely to reduce human error, streamline workflows, and even create more sustainable manufacturing practices. The synergy between these technologies will yield new opportunities alongside challenges that will require careful consideration.
Recap of Key Points
- The importance of precision in modeling sheet metal parts.
- Current technologies and methodologies utilized for effective design.
- The role of predictive modeling in improving manufacturability.
- Future technologies that promise to impact the field.
Understanding these elements builds a foundation for both practical application and theoretical exploration.
Implications for Engineers and Designers
Engineers and designers must consider these insights when approaching their work. The implications are significant. Firstly, real-world application is contingent on thorough understanding of modeling software. Having a solid grasp of tools like SolidWorks or AutoCAD can facilitate better project outcomes.
Secondly, the evolving landscape underlines the need for continual learning. As new technologies emerge, professionals in this field must adapt and upgrade their skills to remain competitive.
Finally, engineers should embrace collaboration across disciplines—integrating knowledge from other fields such as materials science and robotics can enhance innovation in sheet metal modeling. A multifaceted approach will yield improved and unexpected solutions in both design and production of sheet metal parts.
The necessity for rigorous testing and adaptation cannot be overstated in this rapidly changing environment. This will ensure that the engineering community remains at the forefront of advancements, capable of meeting future challenges with confidence.