Mastering the Techniques for Polishing Cast Iron
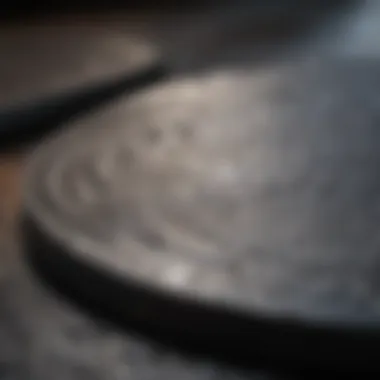
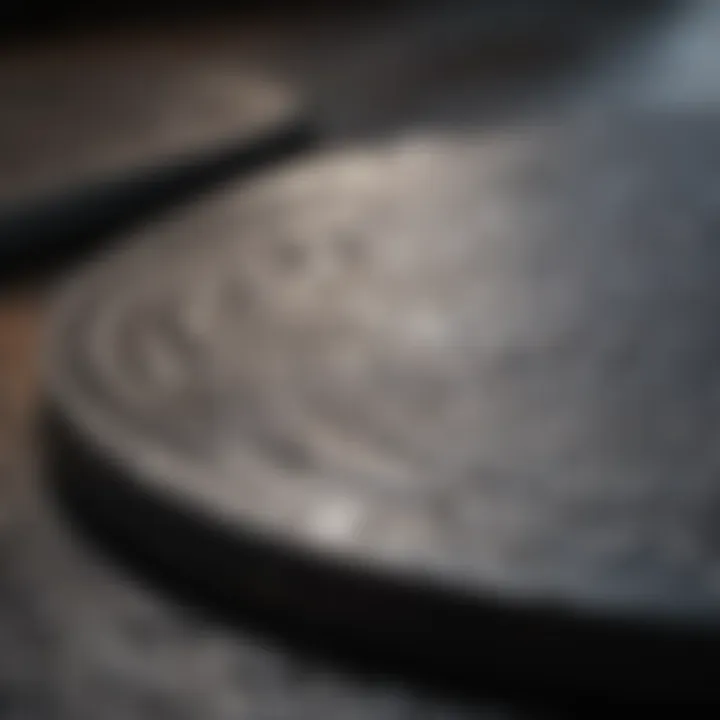
Intro
Cast iron, often considered a workhorse of materials, has been a staple in kitchens, workshops, and artisanal crafts for centuries. Its durability and heat retention make it invaluable, especially in cookware. However, the journey to achieving a smooth, polished finish on cast iron is both an art and a science. With the right techniques and tools, anyone can enhance its aesthetic and functional qualities. This article will take a closer look at the processes involved and the subtleties that can transform rough edges into a polished masterpiece.
Key Concepts
Definition of Primary Terms
To delve into polishing cast iron effectively, it is essential to define some key terms:
- Cast Iron: A group of iron-carbon alloys with a carbon content greater than 2%. It is known for its excellent castability and resistance to wear and deformation.
- Polishing: The act of refining a surface to make it smooth and shiny, typically involving an abrasive process.
- Abrasives: Materials used to grind and polish the surface by removing small amounts of material.
Related Concepts and Theories
Understanding the theory behind polishing can elevate your approach:
- Material Composition: The different types of cast iron, such as gray, ductile, and white cast iron, all exhibit unique behaviors when polished. Each type responds differently based on its composition and intended use.
- Grain Structure: The internal structure of cast iron that can affect how it responds to polishing; finer grains yield smoother finishes.
- Heat Treatment: Sometimes, the properties of cast iron can be altered through heat treatment, which can make the polishing process easier or more effective.
Techniques and Tools to Polish Cast Iron
Polishing cast iron requires a delicate balance of the right tools and techniques. Here’s a snapshot of what one typically involves:
Tools for Polishing
- Sandpaper: Different grades (from coarse to fine) serve various purposes. Coarse grades remove material quickly, while fine grades refine the surface.
- Angle Grinder: A powerful tool, particularly for large cast iron pieces, that allows for quick removal of rust or roughness before finer polishing.
- Polishing Compound: Specific compounds designed for metal polishing help create a high gloss finish.
Techniques
- Cleaning the Surface: Before polishing, wash the cast iron to remove grease and debris. This can be done using soapy water and a scrub brush.
- Applying Abrasives: Start with a coarse sandpaper to remove imperfections, gradually working towards finer grades.
- Polishing: Use a polishing compound on a cloth or buffing wheel, moving in circular motions for even coverage.
Important Considerations
When engaging in this process, one must keep certain considerations in mind:
- Safety First: Always wear protective gear including gloves and goggles as cast iron can produce sharp shavings.
- Work Environment: Ensure a clean, dust-free space while working to avoid contamination of the surface.
- Patience is Key: Take your time through each stage to ensure quality results rather than rushing through the process.
"A little patience can often lead to astonishing results in polishing cast iron, turning dull into dazzling with careful touch."
Future Directions
Looking toward the future of polishing cast iron reveals potential gaps and avenues worth exploring.
Gaps Identified in Current Research
Currently, there's limited research specifically addressing the environmental impact of polishing materials and methods used. As sustainability becomes increasingly paramount, understanding new, eco-friendly abrasives could pave the way for greener practices.
Suggestions for Further Studies
- Innovative Materials: Scientists could explore the development of new polishing compounds that effectively minimize waste.
- Automation in Polishing: Studying how automation could enhance the consistency and speed of polishing processes could help industries looking to optimize production.
In light of these insights, polishing cast iron is not only about technique; it's about understanding the nuances that make each piece unique while being mindful of future implications. The intricate dance of artistry and technicality in this process elevates it well beyond the mere act of refining surfaces.
Understanding Cast Iron
Cast iron plays a pivotal role in the world of metalworking and manufacturing. As a material, it offers an exceptional blend of durability, strength, and versatility, making it ideal for varied applications—from cookware to machinery parts. Understanding cast iron isn’t just about grasping its characteristics; it’s about appreciating its unique properties, which set the stage for the art of polishing. Polishing cast iron can elevate its aesthetic appeal and enhance its functionality. The surface finish can determine how well it withstands wear and corrosion, thus making the knowledge of cast iron fundamental to mechanists, metalworkers, and hobbyists alike.
Composition and Properties
At its core, cast iron is primarily composed of iron, carbon, and silicon, typically containing about 2-4% carbon and 1-3% silicon. This composition grants cast iron its distinct properties. The presence of carbon forms graphite, which contributes to cast iron's good machinability and also impacts its brittleness and strength. Notably, cast iron’s ability to dampen vibrations is a characteristic that makes it preferable for machinery bases and tools.
Understanding these variables aids craftsmen in selecting the right cast iron type for their specific polishing projects and intended uses.
Types of Cast Iron
Cast iron comes in various forms, each with its own array of properties and potential applications. The three most common types that one should familiarize themself with are gray cast iron, ductile cast iron, and white cast iron.
Gray Cast Iron
Gray cast iron is known for its excellent wear resistance and machinability. Its high graphite content gives it a characteristic gray color when broken, hence the name. One of the key benefits of gray cast iron is its ability to absorb shock loads, which is crucial in many applications where durability is essential.
- Advantages:
- Excellent castability and machinability.
- Good wear resistance, making it ideal for engine blocks and machine tools.
However, it can be brittle, which might not be favorable for all applications, especially those involving heavy impact.
Ductile Cast Iron
Ductile cast iron stands out because of its unique microstructure, which gives it remarkable ductility and toughness. This type of cast iron is achieved through the addition of small amounts of alloying elements like magnesium during production. Its ability to deform under stress without fracturing makes it a popular choice for components subjected to high fatigue loads, such as automotive and heavy industrial applications.
- Advantages:
- Enhanced strength and flexibility.
- Suitable for high-stress applications.
Nevertheless, it can often be more expensive than gray cast iron, which may restrict its use in certain cost-sensitive projects.
White Cast Iron
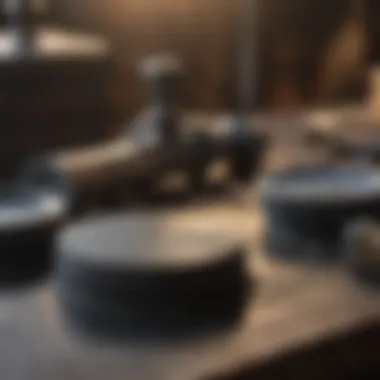
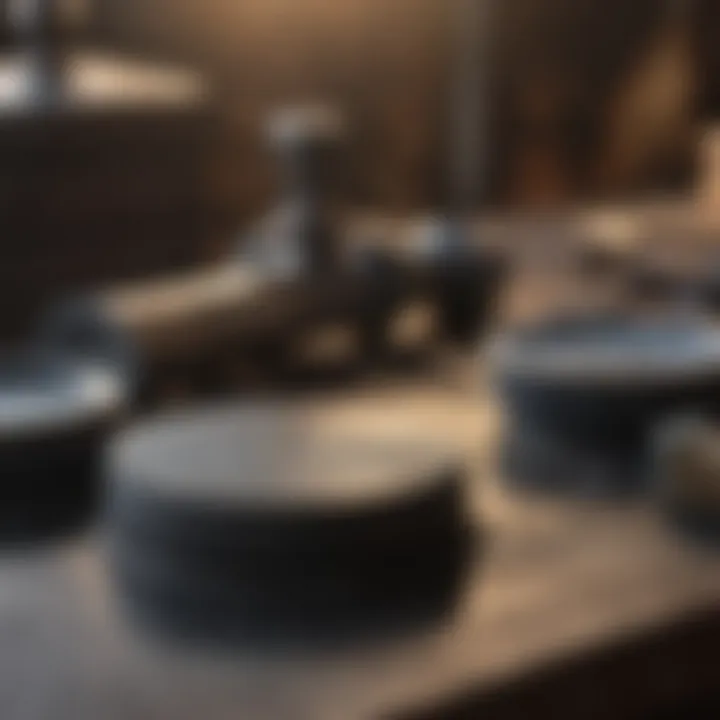
White cast iron is characterized by its hard and brittle structure due to minimized carbon in graphite form. This uniqueness makes it ideal for wear-resistant surfaces, such as in mills and crushers. Its hardness is one of its key features, often leading to its use in applications where abrasion resistance is paramount.
- Advantages:
- Outstanding hardness, suitable for extreme wear scenarios.
- Good for creating hard thin-walled shapes.
However, the brittleness of white cast iron can pose challenges. Special care is needed during handling and processing to prevent breakage, impacting its desirability for some end applications.
Understanding these types equips individuals with the insight needed to choose the right cast iron for tasks, especially in the polishing process where different metals demand tailored techniques and tools. Each type's intrinsic qualities contribute to the overall effectiveness and end results in polishing, making this knowledge crucial for successful applications.
The Importance of Polishing
Polishing cast iron not only serves aesthetic purposes but also has far-reaching implications for its functionality and longevity. In this section, we delve into why polishing is paramount, recognizing its dual role in enhancing appearance and ensuring optimal performance. It becomes evident that polishing is an essential aspect of working with cast iron, and ignoring it could lead to pitfalls later in the usage or maintenance of these items.
Aesthetic Appeal
The visual aspect of polished cast iron cannot be overstated. A well-polished piece can transform a rugged, industrial object into a stunning centerpiece. When light reflects off a smooth surface, the object seems to glow, drawing eyes and creating a lasting impression. A piece that glistens under light demonstrates the care and quality of craftsmanship involved in its creation; it signifies durability and reliability to those who observe it.
Take, for example, a cast iron skillet. An unpolished skillet can appear dull and unattractive, while a polished one reveals intricate details and character, showcasing the metal's unique texture and patterns. This enhancement not only sparks interest but also adds value. Collectors often seek out pieces that demonstrate meticulous care, and a brightly polished item can fetch a higher price or serve as a treasured heirloom.
Functional Benefits
Reducing Friction
Reducing friction is a crucial aspect of polishing that directly contributes to the functionality of cast iron items. When the surface of cast iron is polished, the smoothness allows for reduced resistance during use. For instance, in cooking, a polished cast iron skillet will allow food to move more freely, preventing sticking and achieving a better sear.
The key characteristic here is the increased glide of the surface, which enhances user experience—be it in cooking or in machinery settings where cast iron components are in constant motion. The smoother a surface, the less likely it is for materials to wear down, which is a significant advantage, especially in applications demanding high precision and reliability.
However, one must be mindful of the balance here. Over-polishing can lead to an overly smooth surface that may diminish some of the desirable properties, particularly for cookware that benefits from a slight roughness for seasoning retention. So, finding the sweet spot in polishing is essential for preserving functionality.
Improving Corrosion Resistance
Improving corrosion resistance is another vital contribution of polishing. When the surface of cast iron is polished, it becomes less absorbent to moisture and contaminants, factors that contribute to rust formation. The smooth layer acts as a barrier, reducing the number of nooks and crannies where water can gather and lead to degradation over time.
The key aspect of this benefit is the enhanced longevity of cast iron items, making them more resilient to the ravages of environment and use. A well-polished piece could potentially last years longer than its unpolished counterpart, offering not just a practical advantage but also justifying the time and resources invested in its care.
Additionally, polished surfaces are generally easier to clean, as food particles and grime tend to wash away more easily, leading to improved maintenance and a better overall experience. However, it should be noted that polishing does not eliminate the need for regular maintenance; protective coatings should still be applied to preserve the surface.
Preparing for the Polishing Process
Before diving into the realm of polishing cast iron, it's crucial to lay the groundwork with adequate preparation. This stage can significantly influence the outcome of the polishing process, affecting not just the visual appeal but also the longevity and functionality of the cast iron surface. Proper preparation means better results, fewer headaches down the road, and can even optimize the effort you put into polishing.
Gathering Necessary Tools
Sandpaper and Abrasives
Sandpaper and abrasives are the backbone of manual polishing. These tools vary in grit size, and choosing the right one is key.
- Key Characteristic: The gritty texture helps remove imperfections and provides the necessary friction for effective polishing.
- Beneficial Choice: Sandpaper, particularly with a grit of around 400 to 600, is popular because it balances aggressiveness with finish quality.
- Unique Feature: They come in different forms—sheets, sponges, or rolls—allowing for versatility in tackling various surface shapes.
Advantages and Disadvantages: One of the main advantages of sandpaper is its accessibility and ease of use. However, it can wear out quickly, requiring frequent changes, which may slow down the process.
Polishing Compounds
Polishing compounds play a vital role in achieving a smooth and shiny surface. These substances work by filling in microscopic scratches left from abrasives.
- Key Characteristic: They are designed specifically to buff and polish through chemical or mechanical means.
- Beneficial Choice: These compounds, particularly those formulated for metals, are effective because they offer a fine finish and enhance the overall appearance.
- Unique Feature: Available in various formulas for different effects, some can even contain wax to add an additional layer of protection.
Advantages and Disadvantages: While polishing compounds can provide an impressive sheen, they might require specific techniques and applications to get the best results. Moreover, using the wrong compound can lead to damage.
Protective Gear
Using protective gear is non-negotiable in the polishing process. Safety should always come first.
- Key Characteristic: Protective gear includes items like gloves, goggles, and masks to shield yourself from dust and particulate matter.
- Beneficial Choice: This gear is vital because it minimizes injuries and health risks, particularly from fine particles that can irritate your lungs or eyes.
- Unique Feature: High-quality gear often provides better comfort and a more secure fit, which can be crucial when working for extended periods.
Advantages and Disadvantages: Investing in proper protective gear is fundamental. While it may add to your initial cost, the safety it provides is invaluable. The downside can be the potential discomfort of wearing gear for long durations or in warmer conditions.
Surface Assessment
Before you pick up that sandpaper, assessing the surface of the cast iron is fundamental. This pre-polishing check can save a lot of time and improve final results.
Identifying Imperfections
Before polishing, identifying imperfections on the surface is essential. They can include scratches, dents, or uneven areas.
- Key Characteristic: Spotting these issues allows you to strategize on how much effort will be required to fix them.
- Beneficial Choice: Factors like light reflection and feel can help in assessing imperfections, especially those that might not be visible.
- Unique Feature: Focusing on larger defects first can streamline the process, making it less tedious overall.
Advantages and Disadvantages: Being thorough in this stage allows you to avoid pitfalls later. However, if not done correctly, it could lead to overlooking major issues that might complicate the polishing.
Checking for Rust or Contaminants
Rust and contaminants can create significant problems during polishing. If they are present, they must be dealt with prior to the polishing process.
- Key Characteristic: Rust can eat away at the metal and lead to uneven surfaces, dramatically impacting the final appearance.
- Beneficial Choice: Regular checks for contaminants ensure that the surface is as clean as possible, reducing any potential damage.
- Unique Feature: The use of a magnet can help identify areas that might be suffering from rust or other forms of deterioration.
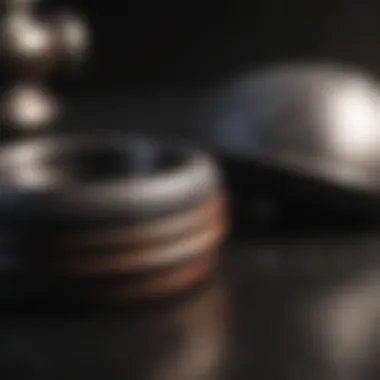
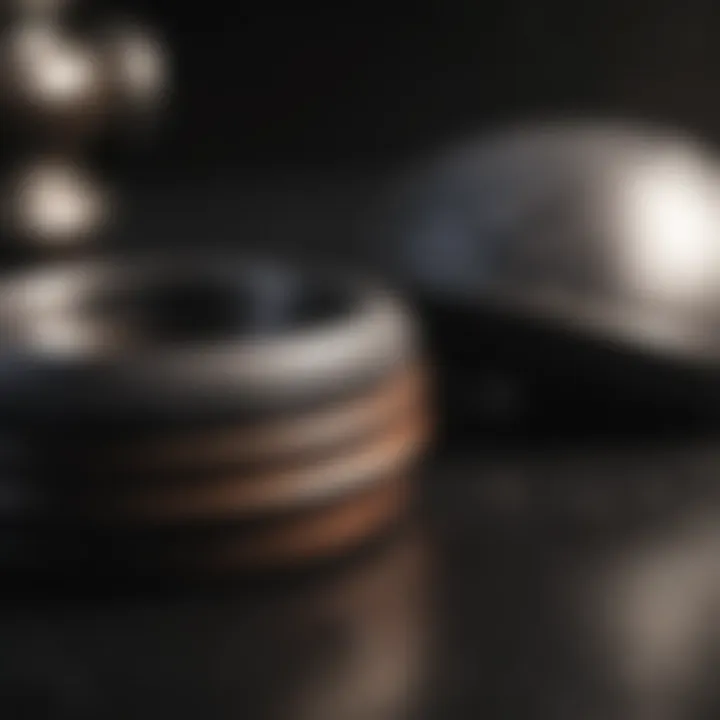
Advantages and Disadvantages: While examining for rust may seem tedious, tackling it beforehand ultimately saves time and resources. On the flip side, not addressing it can result in a poor finish, undoing all the hard work you put into polishing.
Remember, preparation isn’t just half the battle; it often defines the outcome.
Techniques for Polishing Cast Iron
Polishing cast iron is more than just a cosmetic endeavor; it combines art and craftsmanship with real practical benefits. When looking at the process, there are two primary strategies: manual polishing techniques and machine polishing methods. Each approach brings its own flavor to the task and caters to different needs and skill levels.
Mastering these techniques is essential for achieving a polished surface that not only looks good but also performs well in various applications. Attention to detail during polishing ensures the longevity of the cast iron piece while also preserving its functional qualities.
Manual Polishing Techniques
Use of Hand-Held Abrasives
Hand-held abrasives serve as the go-to choice for many when starting the polishing journey of cast iron. They offer an intimate connection to the material, allowing users to gauge the feedback more closely as they work. This technique involves using various grits of sandpaper or abrasive pads, making it versatile for different surface conditions.
A key factor that sets hand-held abrasives apart is their ability to target specific areas. For instance, if there are rough patches, a coarser grit can be employed to scrape those areas back to a smoother finish. Plus, user control over pressure and direction plays a significant role in how the surface appears in the end.
However, the trade-off is that manual polishing can be time-consuming, especially for larger or heavily pitted areas. Patience is essential, and having the right technique matters significantly. If done wrong, it can lead to uneven surfaces, undermining the entire polishing effort.
Applying Polishing Compounds
Once the abrasive phase is well underway, bringing in polishing compounds can elevate the outcome. These compounds, often wax or paste-based substances, fill in minor scratches and enhance the shine of the cast iron. Moreover, applying a polishing compound is akin to an artist adding the final details to their masterpiece—it transforms the mundane into something remarkable.
Selection of the right compound is also crucial, as there are those specifically designed for metals which can offer superior results. Unique to this approach is the buffing process, typically requiring a clean cloth or pad to work in the compound seamlessly into the surface. The right compound, when matched with effective manual techniques, can significantly diminish the residue of the polishing phase that came before.
However, these compounds need to be used in moderation; excessive application can lead to build-up in corners or crevices. Therefore, it’s necessary to know when to stop and inspect the surface regularly, ensuring consistent quality.
Machine Polishing Methods
Belt Sanders
For those who crave efficiency coupled with power, belt sanders present a solid option. These machines can quickly tackle broad surfaces, making them ideally suited for larger cast iron pieces. Operating a belt sander is relatively straightforward—just guide it over the surface, maintaining a steady hand. The primary benefit here lies in its speed: you can remove a significant amount of material in a shorter period.
Moreover, belt sanders can accommodate various grit belts, making it easy to transition from coarse to finer grit. However, an important aspect to remember is the risk of overheating the material. If pressed too hard, it can warp the cast iron or create uneven spots, so moderate pressure is key.
Rotary Buffers
Another machine polishing method worth mentioning is the rotary buffer. This device is particularly popular among those seeking high gloss finishes on their cast iron. The rotating movement can cover wider areas and achieve a smooth surface quickly. The key characteristic that makes rotary buffers appealing is their dual functionality; they can be used for both sanding and polishing, streamlining your workflow.
When compared to other methods, rotary buffers can produce an exceptionally shiny finish, capturing the hallmark look sought after by many professionals and hobbyists alike. However, one must be cautious with the buffer's speed settings. Excessively high speeds can leave swirl marks or even burnish the iron. Balancing the speed with the material's needs is crucial for obtaining the desired result without compromising the integrity of the cast iron.
To really nail the polishing process, combining both manual and machine techniques often yields the best results, allowing you to take advantage of each method's strength.
Best Practices in Polishing
Polishing cast iron is not just about achieving a shiny surface; it’s a meticulous process that requires a methodical approach to truly enhance the material’s characteristics. Understanding and applying best practices in polishing can make the difference between a lackluster finish and one that reflects diligent craftsmanship. These practices are not just recommendations; they’re essential steps that lead to effective and efficient polishing, ensuring that the integrity of the cast iron is maintained while improving its aesthetic appeal and functionality.
Working in Sections
The mantra of ‘divide and conquer’ holds true in the world of polishing cast iron. Working in sections not only makes the task more manageable but also ensures a uniform finish. If you attempt to polish the entire piece in one go, it’s easy to miss spots or apply uneven pressure, leading to inconsistent results.
Here are some key points to consider when working in sections:
- Select a Manageable Area: Begin with a small section that’s easy to handle. This could be a square foot, or even less if the piece is large.
- Mark Your Boundaries: Use painter’s tape or a marker to delineate the areas you’ll polish. This visual guide keeps you focused and helps to avoid overlap.
- Consistent Technique: By focusing on one section at a time, you can apply a consistent technique. This means that you can ensure the same pressure, speed, and motion across your polishing.
"A small, controlled zone can turn a tedious task into a detailed work of art."
Polishing in sections also allows you to step back and inspect your work as you go. This evaluation can be valuable for determining whether further work is needed before moving to the next area.
Maintaining Consistent Pressure
One of the core principles in polishing cast iron is maintaining consistent pressure throughout the process. Inconsistent pressure can create fluctuations in the surface finish and can even lead to damage in certain areas. Here’s why that’s critical:
- Surface Flatness: When pressure is uneven, it can affect the flatness of the polished surface, leading to a wavy or mottled appearance.
- Effective Material Removal: Even pressure ensures that the abrasive material works uniformly. If you push harder in some areas, you risk removing too much material, affecting the overall integrity of the cast iron.
- Durability of Finish: A uniform surface achieved with consistent pressure will be smoother and more resilient over time, reducing the need for frequent re-polishing.
To maintain consistent pressure, follow these tips:
- Keep Your Hand Steady: If manual polishing, focus on keeping your hand steady, using your whole arm rather than just your wrist for movement.
- Use a Pressure Gauge: If you’re using a machine for polishing, consider employing a gauge that can help you monitor and maintain the pressure applied.
- Regularly Check Your Progress: Periodically step back and check the surface. If you notice areas that look different, reassess your technique and pressure.
By weaving these best practices into your polishing routine, you set the stage for exceptional results. Paying attention to the details, like sectioning your work and maintaining even pressure, can transform the entire polishing experience from a simple chore into a rewarding craft.
Post-Polishing Care
In the quest for a refined and smooth finish on cast iron, the work doesn’t just end once the polishing is done. Post-polishing care is as vital as the polishing process itself. This phase ensures that the surface remains in pristine condition and maximizes the longevity of the polished metal. It entails meticulous cleaning and the application of protective coatings. Let’s explore these essential steps in more detail.
Cleaning the Surface
Removing Residual Compounds
Once the polishing is complete, it's crucial to eliminate residual compounds left on the surface. These might include polishing oils or abrasive particles that, if left unchecked, can tarnish the appearance of the cast iron. Using a soft cloth or mild soap and water solution to gently scrub the surface is a good practice. The key benefit comes from ensuring that the finish achieved remains unblemished and that any potential for future corrosion is minimized. A unique aspect of this step is its ability to maintain the luster of the cast iron while significantly reducing the risk of patches developing on the surface over time.
However, it's worth noting that while removing compounds, care must be taken not to scratch the newly polished surface. This step is incredibly beneficial because it preserves the hard work invested during the polishing process.
Inspecting the Finish
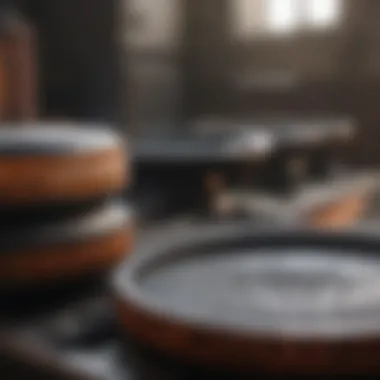
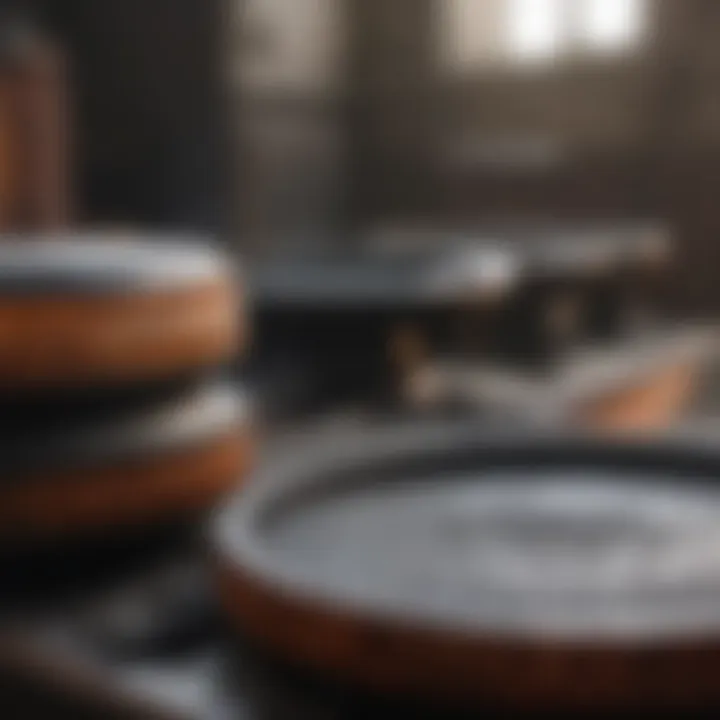
After cleaning, inspecting the finish is a natural next step. It’s all about scrutinizing the polished surface for any imperfections that may have gone unnoticed. The primary characteristic of a thorough inspection is vigilance. If something seems off, it’s better to catch it early rather than your beautifully polished iron becoming a source of frustration later. This inspection can reveal flaws, dull spots, or areas needing a touch-up.
The unique feature of this step lies in its proactive approach. By identifying flaws right away, one can prevent much larger issues down the line, such as rusting or pitting. Although it might seem tedious, the advantages of this practice cannot be overstated in achieving the desired quality. A polished finish not only adds to the aesthetic appeal but also prolongs the lifespan of the cast iron, making this a crucial component of post-polishing care.
Applying Protective Coatings
Oiling Techniques
The application of protective coatings is like putting a cherry on top to finish off the polishing process. Oiling techniques stand out among these coatings. When applied correctly, oiling can create a barrier protecting the cast iron from moisture and other environmental factors that can cause rust. A common choice for oiling may include mineral oil or specialized cast iron oils, which significantly enhance the durability of the finish.
The unique feature of this step is that it not only protects but also enhances the appearance of the cast iron, giving it a richer look. Many find this practice beneficial because it requires minimal effort for maximum protection. However, it does necessitate periodic reapplication to maintain effectiveness, and depending on the environment where the cast iron is used, this frequency can vary.
Alternative Sealants
For those looking beyond oil, alternative sealants offer valuable protection for polished cast iron. These can include clear coatings that seal the surface against oxidation. This approach has a dual benefit: it not only makes the surface easy to clean but also provides a shinier finish compared to traditional oiling methods.
A significant characteristic of using sealants is their variety; choices can range from acrylic sprays to wax finishes. This flexibility allows users to opt for the method that suits their personal preferences or requirements best. However, caution is warranted since certain sealants may alter the appearance of the cast iron. It's essential to choose alternatives designed for use on metal surfaces to avoid potential complications.
In summary, post-polishing care embodies a critical part of maintaining the work put into polishing cast iron. By addressing cleaning and protective steps conscientiously, one can ensure that their metal not only dazzles with a refined finish but stands the test of time as well.
Challenges in Polishing Cast Iron
Polishing cast iron poses its own suite of challenges that can seem daunting, especially for those new to the craft. Each unique hurdle can impact the final quality of the finish, and addressing them is paramount for achieving both an aesthetic and functional outcome. Recognizing these challenges is not just about overcoming obstacles; it’s about understanding the material's nature and how to work with it effectively. This knowledge can save both time and resources, allowing for a smoother process overall.
Dealing with Pitting and Damage
Pitting is a common issue in cast iron surfaces, caused by corrosion or improper storage conditions. It manifests as small, depressions on the surface that can be both unsightly and problematic for polishing. Repairing these pits is crucial because they can trap moisture and impede the effectiveness of the polished finish.
To tackle pitting, a few steps can be followed:
- Assessment: Thoroughly inspect the surface for pitting and other imperfections. Identifying areas needing repair is the first step.
- Surface Preparation: Use coarse sandpaper or a file to even out the surface around the pitting. This requires a gentle touch to avoid creating more damage.
- Filling Gaps: A metal filler might be useful here. Select a filler compatible with cast iron for best results.
- Sanding: After filling, re-sand the area to blend it seamlessly into the surrounding surface. Use finer grits as you work towards getting a smooth finish.
By specifically addressing pitting and damage, one can significantly enhance the overall outcome of the polishing process, ensuring that the final shine is not just skin-deep but structurally sound and durable.
"Taking care of pitting early on can save a world of hassle down the line."
Understanding Material Limitations
Every material comes with its own set of limitations that dictate how it can be worked with. Cast iron is no exception. Understanding its properties can prevent frustration during the polishing process.
First and foremost, cast iron is brittle. While this gives it excellent wear resistance, it increases the risk of cracking if handled improperly. Here’s what to keep in mind:
- Tool Selection: Using the wrong tools can exacerbate issues. Ensure all tools are suited specifically for cast iron.
- Pressure Observation: Applying too much pressure during polishing can lead to chipping or cracking. A gentler approach is necessary.
- Heat Management: Excessive heat can cause warping. Keep the work area well-ventilated and use techniques that minimize heat buildup.
Embracing these limitations is not about being resigned to them; it’s about using this knowledge to refine techniques. Knowledge of limitations empowers users to choose suitable approaches, tools, and methods that respect the integrity of the material while achieving the desired polished finish.
Sustainability Considerations
When it comes to polishing cast iron, the conversation doesn’t just revolve around achieving a flawless finish. An equally important aspect in today's world is sustainability. It focuses on being mindful of not just the processes involved in polishing but also the materials we use and the impact they leave behind. From selecting eco-friendly supplies to understanding recycling options, sustainability considerations are pivotal for reducing waste and promoting responsible craftsmanship.
Environmental Impact of Polishing Supplies
The tools and materials employed during the polishing process often come with a hefty environmental footprint. Most traditional polishing compounds and abrasives are derived from non-renewable resources and can contribute significantly to pollution. For example, many commercial polishing compounds contain harmful chemicals that not only pose risks to human health but also to aquatic ecosystems when washed away.
Considering this, opting for greener alternatives can make a real difference. Here are some ways to minimize environmental impact:
- Eco-Friendly Abrasives: Seek out alternatives made from natural materials, such as walnut shells or corncobs, which degrade naturally instead of causing pollution.
- Water-Based Polishing Compounds: These compounds typically have fewer volatile organic compounds (VOCs) compared to their solvent-based counterparts. Using them can greatly reduce harmful emissions into the atmosphere.
- Bulk Purchasing: Reducing packaging waste when sourcing polishing materials can lessen your carbon footprint. Buying in bulk minimizes the reliance on plastics and wrappers that end up in landfills.
By being Selective with polishing supplies, artisans can take proactive steps towards fostering a healthier planet.
Recycling Cast Iron
The journey of cast iron doesn't end with its initial use. Recycling is not just a sustainable practice; it's an efficient way to ensure that valuable materials aren't wasted. Recycling cast iron can bring significant environmental advantages, such as:
- Conserving Natural Resources: Recycling reduces the need to mine and process raw iron ore, which in turn conserves energy and preserves ecosystems.
- Reducing Waste: Cast iron products that are no longer used can be repurposed, cutting down on the volume of waste in landfills.
- Circle of Life: The iron that is recycled can be transformed into new products or even reintroduced to the manufacturing cycle, creating a closed-loop system.
Key Steps for Recycling Cast Iron:
- Local Recycling Programs: Identify local facilities or programs that accept metal recycling. Many areas have designated drop-off points or scheduled pickups for cast iron.
- Upcycling: Consider creative ways to reuse cast iron products rather than discarding them. This can include repurposing for garden features or making art.
- Community Resources: Engage with forums or local community groups that focus on sustainability to learn more about recycling initiatives and ways to participate.
"One man's trash is another man's treasure." This old saying rings especially true in the context of sustainability in cast iron polishing. A shift towards thinking of end-of-life materials as resources rather than waste can revolutionize how we approach the craft.
Future Trends in Cast Iron Treatment
As the industrial landscape continues to evolve, the future of cast iron treatment stands at a crossroads of tradition and innovation. The importance of this topic cannot be overstated; it reflects the need for adaptability in an ever-changing market. Advances in technology and materials science are not just reshaping casting but also refining how we polish and maintain cast iron. A solid understanding of these trends gives manufacturers and artisans the edge needed to meet modern demands while preserving the charm and utility of cast iron.
Advancements in Materials Science
Materials science is making significant strides, shaping the future of cast iron treatment. One emerging trend is the development of specialized alloys that enhance the properties of cast iron. For instance, newer composite materials with improved wear resistance and reduced brittleness are becoming more prevalent. These advancements not only improve durability but can also increase the lifespan of cast iron products.
Furthermore, researchers are investigating eco-friendly materials that reduce harmful emissions during the production and polishing processes. By embracing these innovative materials, companies can contribute to sustainable practices without sacrificing performance.
- Composite Materials: The blend of cast iron with materials such as polymers enhances flexibility and resistance.
- Eco-Friendly Options: Materials that lower environmental impact can reshape industry standards.
Innovative Polishing Techniques
In the realm of polishing, techniques are rapidly evolving as well. Where once manual methods ruled the roost, machinery and technology now offer enhanced efficiency alongside precision. Laser polishing is perhaps one of the most transformative innovations. This new method affords a level of detail and smoothness that traditional techniques struggle to achieve. Plus, it minimizes the need for extensive manual labor.
Moreover, advancements in abrasive materials are changing the game. For example, diamond abrasives are now being incorporated into polishing kits, yielding superior finishes with less effort. As we strive for efficiency, the old adage "work smarter, not harder" rings truer than ever.
Polishing isn't merely about aesthetics; it is about enhancing functionality and longevity of the cast iron objects.
To summarize, the future trends in cast iron treatment hinge on the integration of innovative materials and polishing techniques. In an industry where durability and quality remain paramount, adopting these advancements will likely lead to better performance and a smaller carbon footprint. This balance might just hold the key to maintaining the legacy of cast iron while stepping boldly into the future.