Pressed Board Plywood: In-Depth Analysis and Insights
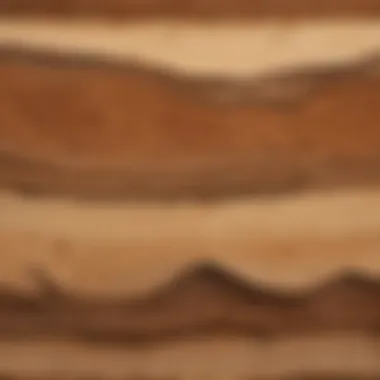
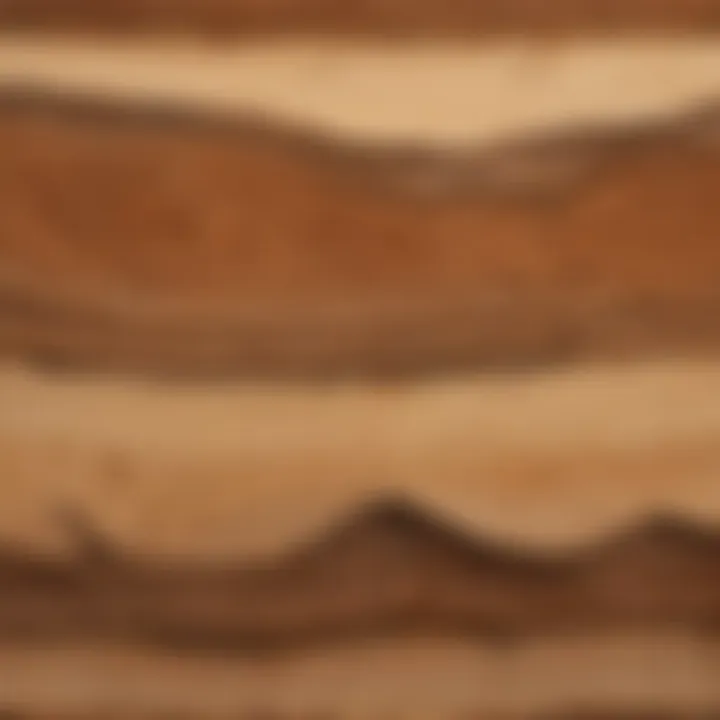
Intro
Pressed board plywood, a term that may not often grace the lips of casual conversation, stands as an underappreciated gem in the world of materials. This composite product, crafted primarily from wood fibers or chips, binds together under heat and pressure to create a sturdy, versatile panel. Given its unique composition and properties, it finds an array of applications that often go unnoticed in our daily lives.
Understanding pressed board plywood isn't merely about grasping its definition. It's about delving into the intricacies of its manufacturing, its applications, and the broader implications surrounding its use. With sustainability taking center stage in discussions about construction materials, this article aims to peel back the layers on pressed board plywood—to reveal its merits while considering its drawbacks.
In quizzing the merits of using this material, we will explore what makes it tick, the ways it can be employed in both industrial and domestic settings, and how it stacks up against its rivals. The push for innovation in manufacturing processes will also be highlighted, uncovering how technology shapes the efficiency and sustainability of this underrated material. As we position our lenses to focus on pressed board plywood, this article will cater to a diverse audience—students eager to learn, educators striving to teach, and professionals hunting for practical insights.
Let’s embark on this exploration, taking a closer look at the landscape surrounding pressed board plywood.
Intro to Pressed Board Plywood
Pressed board plywood has carved out a noteworthy niche in the construction and furniture industries. Understanding its characteristics and applications sheds light on why it is such a topic of interest. This segment introduces the concept of pressed board plywood, elucidating its importance, benefits, and the factors to consider when delving into this material.
Pressed board plywood is not just another building block; it's a versatile option that appeals to sectors ranging from interior design to sustainable construction practices. By emphasizing its unique properties, we can grasp the rationale behind its rising popularity and the need for informed discussions in educational and professional settings.
Definition and Overview
Pressed board plywood, also known as engineered wood or composite wood, is crafted by combining various layers of wood fiber or strands. These layers are glued together under immense pressure and heat, resulting in a product that boasts enhanced strength and stability compared to traditional wood. This composite nature allows pressed board plywood to be tailored to specific applications, making it a go-to material for many experts.
One striking feature of pressed board plywood is its surface finish. Manufacturers can produce a smooth surface that caters to aesthetic flexibility, allowing integration into a variety of design projects. In residential settings, it finds its way into cabinets, shelves, and flooring. In commercial use, it's often seen in partition walls and fixtures.
Historical Development
The history of pressed board plywood is a tale knitted with innovation and practicality. It traces its roots back to the early 20th century when wood was an abundant resource but utilizing it efficiently was a growing concern. The quest to maximize wood usage led to the development of pressed board plywood, an idea that emerged from the need to create strong, reliable material without the wastefulness associated with solid wood.
As technology improved, the processes for creating pressed board plywood became more refined. In the 1950s, the introduction of synthetic adhesives revolutionized the production process. This innovation not only boosted durability but also opened doors to a new range of potential applications. By the late 20th century, environmental considerations came to the forefront, urging manufacturers to adopt sustainable practices, such as responsible sourcing of raw materials and efficient production methods.
"The evolution of pressed board plywood underscores not just technological advancements but also a growing awareness of our environmental responsibilities."
Today, pressed board plywood stands as a cornerstone of modern construction and design, a testament to how far we've come in the realm of material science.
Composition of Pressed Board Plywood
Understanding the composition of pressed board plywood is crucial for grasping how it performs in various applications, from construction to furniture manufacturing. This section breaks down the primary components that make up pressed board plywood, shedding light on the raw materials and chemical additives involved. Knowing these elements can help one appreciate the material's strengths and weaknesses, guiding effective usage in your projects.
Raw Materials
Pressed board plywood primarily utilizes wood fibers or particles as its foundational building blocks. Commonly used raw materials include:
- Wood Shavings: These are small, thin curls produced during the cutting of wood. They can add to the bulk, offering a lightweight characteristic to the finished product.
- Wood Chips: Crafted from larger chunks of timber, wood chips enhance the structural integrity. Typically generated from the offcuts of lumber production, they are recycled into pressed board plywood, contributing to sustainability.
- Wood Fiber: This is derived from mechanically breaking down wood into fibers, providing a smooth, consistent texture for the final product.
The choice of raw materials notably affects the properties of the pressed board plywood. For example, high-density fiberboards use finer wood particles, resulting in a denser and more durable product. On the other hand, larger chips can impart a more rustic finish. In addition to wood sources, alternative materials like straw, flax, or recycled plastics are gaining traction, especially in eco-friendly initiatives. These alternatives not only reduce reliance on traditional timber sources but also showcase the innovative potential within pressed board technology.
Chemical Additives and Treatments
To enhance the performance and durability of pressed board plywood, manufacturers often incorporate various chemical additives and treatments. These substances can significantly influence the final product’s properties, including the following:
- Adhesives: Typically made from synthetic resins, adhesives bind wood particles together during the pressing process. Urea-formaldehyde is a common choice, offering good bonding properties at a lower cost. However, it raises concerns due to formaldehyde emissions. Alternatives like phenol-formaldehyde or soy adhesives are becoming more popular, catering to the market's growing demand for low-emission materials.
- Fire Retardants: These additives are necessary for applications requiring enhanced safety measures. They help to slow down combustion, granting valuable time for evacuation in case of emergencies.
- Anti-Fungal Agents: To combat moisture sensitivity, anti-fungal agents are applied to guard against mildew and decay. This treatment is especially important in humid environments where wood products face the risk of deterioration.
"In today's world, the balance between durability and environmental sustainability is key. Every choice, from raw material to chemical treatment, echoes this fact."
Ultimately, the careful selection of raw materials and chemical treatments not only improves the functional performance of pressed board plywood but also addresses environmental concerns. Making informed decisions about these components can lead to better products that meet ecological standards while still delivering on performance.
Manufacturing Processes
Manufacturing processes play a pivotal role in determining the quality and characteristics of pressed board plywood. Understanding these processes aids industries in choosing the right type of plywood for specific applications while ensuring efficiency and cost-effectiveness. Each stage in the manufacturing flow—from the preparation of raw materials to the pressing techniques—maps out the journey of how ordinary materials get transformed into high-performance products.
Preparation of Raw Materials
Before anything else, the raw materials must be appropriately prepared, as this significantly impacts the final product's durability, strength, and overall performance. The wood fibers or particles selected for pressed board plywood often come from various sources, like sawmill waste, wood chips, or even recycled wood. This choice isn't incidental; it provides the foundation for the plywood's properties.
The first step involves drying the raw materials, usually through a kiln. Drying reduces moisture content, which is crucial because excessive moisture can lead to mold growth or reduce adhesion during pressing. It is important to monitor this moisture closely. A wood particle that is even slightly too wet can deteriorate the glue's effectiveness, leading to eventual structural issues.
Once dried, the material undergoes a process called "screening." In this step, the materials are sorted according to size to ensure uniformity. Just like how a chef sifts flour before baking, this procedure ensures that all components are conducive to forming a strong bond. The variety of particle sizes is something to note, as different applications may require specific dimensions for optimal performance.
Pressing Techniques
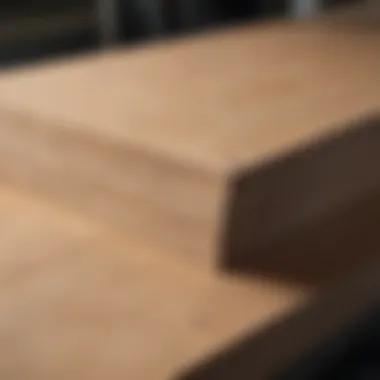
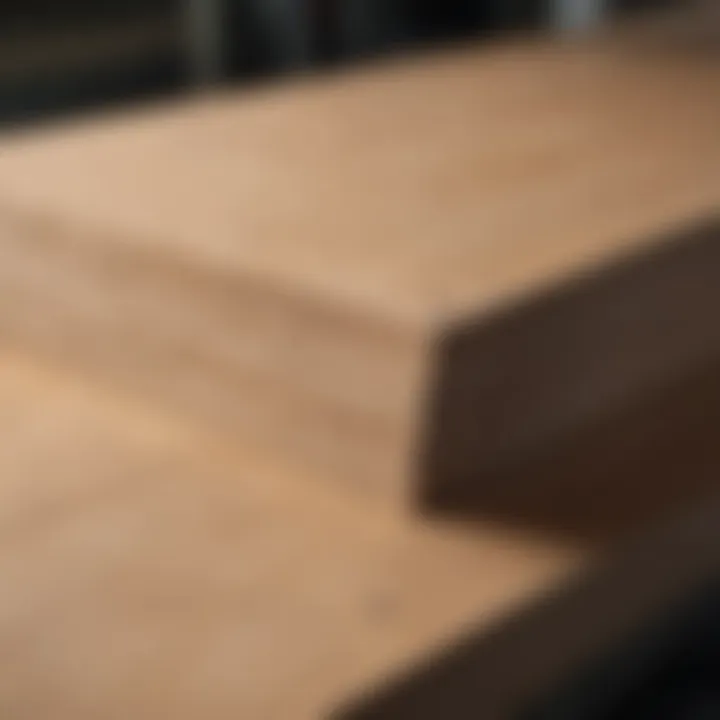
Next, we delve into pressing techniques, which are the heart of manufacturing pressed board plywood. Various methods can be employed during this stage, with the most common being hot pressing and cold pressing. The difference lies in the temperature and timing. Hot pressing involves applying heat and pressure simultaneously, which allows adhesives to cure faster and create a stronger bond. On the other hand, cold pressing uses lower temperatures with extended pressing times.
The choice of pressing method can hinge on several factors. For instance, hot pressing requires more complex machinery and may involve higher initial costs; however, it often leads to improved mechanical properties of the final product. Conversely, cold pressing could be seen as more energy-efficient, making it an appealing choice for smaller operations or environmentally conscious manufacturers.
Moreover, pressure levels and duration are tailored depending on the type of plywood being produced. A higher pressure applied for a shorter duration can yield different results than lower pressure maintained over a longer period. It’s a bit like cooking—time and temperature can make or break the dish.
Quality Control Measures
To ensure that the pressed board plywood meets both safety standards and performance expectations, quality control measures are indispensable throughout the manufacturing process. Various tests are conducted, evaluating parameters such as tensile strength, moisture resistance, and surface finish.
Inspections often begin with a thorough examination of the raw materials, checking for defects that might compromise the final product. After pressing, samples of the plywood undergo rigorous testing. For example, material thickness is checked consistently for uniformity, and adhesive bond strength is assessed using peel tests. These tests can even involve simulating conditions that the plywood will face in real-life applications.
Furthermore, an astute practice is to establish a feedback loop where data from the quality tests informs adjustments in the manufacturing process. If a particular batch doesn't meet guidelines, manufacturers can revisit stages such as raw material preparation or pressing methods without wasting time and resources.
"Quality isn't just an act; it's a habit that becomes rooted in the manufacturing culture." - An immediate understanding of this principle is what separates the leaders from the laggards in the plywood industry.
In summary, manufacturing processes encapsulate a series of critical practices in the journey from raw materials to pressed board plywood. Each step, from preparation to quality assurance, lays the groundwork for a product that can meet the varied demands of furniture, construction, and many other applications. Understanding these nuances gives manufacturers and consumers alike a much better grasp on the capabilities and limitations of pressed board plywood.
Applications of Pressed Board Plywood
Pressed board plywood, with its unique blend of properties, finds its way into various sectors, each showcasing its distinctive benefits and capabilities. Its utilization not only adds functionality but also brings aesthetic appeal across a wide range of materials. By diving deeper, we can explore specific applications like furniture manufacturing, construction, and packaging solutions—areas where pressed board plywood truly shines.
Furniture Manufacturing
In the realm of furniture manufacturing, pressed board plywood is a staple. It is prized for affordability and adaptability, allowing artisans and manufacturers to create varied designs without breaking the bank. With its layered structure, it mimics the natural grain of solid wood, enabling products that look luxurious yet remain budget-friendly.
Consider the versatile uses in this sector:
- Cabinets: Pressed board plywood provides the ideal base for kitchen and bathroom cabinets, offering durability while allowing for a range of finishes.
- Tables and Chairs: Its lightweight nature doesn’t hinder strength, making it a suitable choice for both heavy-duty dining and casual coffee tables.
- Shelving: Ideal for creating custom shelving solutions, it can be easily cut to size, providing flexibility for designers.
This material's ease of handling makes it a favorite among manufacturers. It can be shaped, finished, and assembled quickly, speeding up the production process. However, it’s crucial to be mindful of its constraints. Furniture exposed to extreme moisture can suffer damage, emphasizing the need for proper sealing and upkeep to increase longevity.
Construction and Interior Design
Pressed board plywood plays a noteworthy role in construction and interior design. Its structural strength and cost-effectiveness have made it popular among builders and designers alike. The material lends itself well to diverse applications, from flooring to wall paneling, enhancing both durability and aesthetics.
Key aspects in this application include:
- Wall Panels: Installed either for insulation or as design features, these panels can transform a plain space into an inviting environment.
- Flooring Systems: Pressed board plywood serves as an excellent foundation layer for various flooring options, offering both support and easy installation.
- Soundproofing: Due to its density, it also acts as a sound barrier, which can be beneficial in residential constructions, particularly in urban settings.
When it comes to interior design, pressed board plywood allows for flexibility in design while ensuring structural integrity. However, designers must consider its moisture sensitivity before using it in spaces with high humidity, such as bathrooms.
Packaging Solutions
Within the packaging industry, pressed board plywood is often an unsung hero. Its composition provides an excellent solution for protective packaging. Items needing shipment benefit from its strength and versatility.
Some notable applications include:
- Custom Crates and Boxes: Tailored packaging solutions protect products during transport while providing a sturdier option compared to traditional cardboard.
- Display Units: Retail environments utilize pressed board plywood for creating eye-catching display units, blending function with style.
- Eco-Friendly Options: As consumers grow more environmentally conscious, pressed board plywood presents itself as a more sustainable alternative to plastic packaging, considering its recyclability and lower ecological footprint.
While it delivers strength and durability, companies should remain vigilant about moisture exposure to maintain integrity during transit.
"Pressed board plywood stands as a multifunctional material that not only serves its purpose but also supports sustainability in various industries."
In summary, the applications of pressed board plywood extend far beyond mere utility. Each sector benefits from its unique characteristics while being cautious of its limitations. Understanding these applications can guide more informed decisions on usage and manufacturing processes, ultimately leveraging its strengths for effective outcomes.
Advantages of Pressed Board Plywood
Pressed board plywood brings a myriad of benefits to the table, making it an appealing choice for both industrial applications and personal projects. Exploring these advantages allows us to understand why many professionals and hobbyists alike favor this material in their work. Each advantage plays a crucial role in the decision-making process when selecting materials for specific requirements.
Cost-Effectiveness
One of the most compelling aspects of pressed board plywood is its cost-effectiveness. In an era where budget constraints often dictate project choices, this material stands tall. Not only is it cheaper to produce than traditional solid wood, but its affordability extends to the end-user as well. Given that it utilizes wood fibers which may otherwise go to waste, makers can provide a product that is both economical and environmentally considerate.
- Lower Material Costs: The raw material for pressed board plywood is often sourced from leftover wood chips, shavings, and sawdust, making it less expensive than sourcing high-quality lumber.
- Reduced Labor Costs: The manufacturing process, while highly technical, can be optimized to save labor hours. Automated processes minimize the need for specialized skills in many cases.
In summation, projects that choose pressed board plywood not only benefit financially but can also redirect the savings towards design and functionality enhancements.
Versatility and Customization
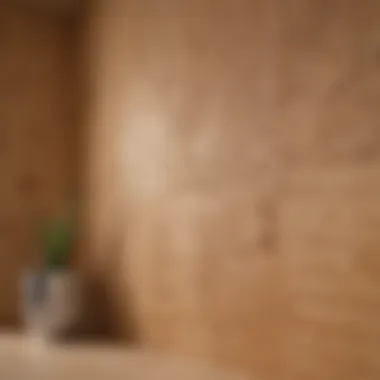
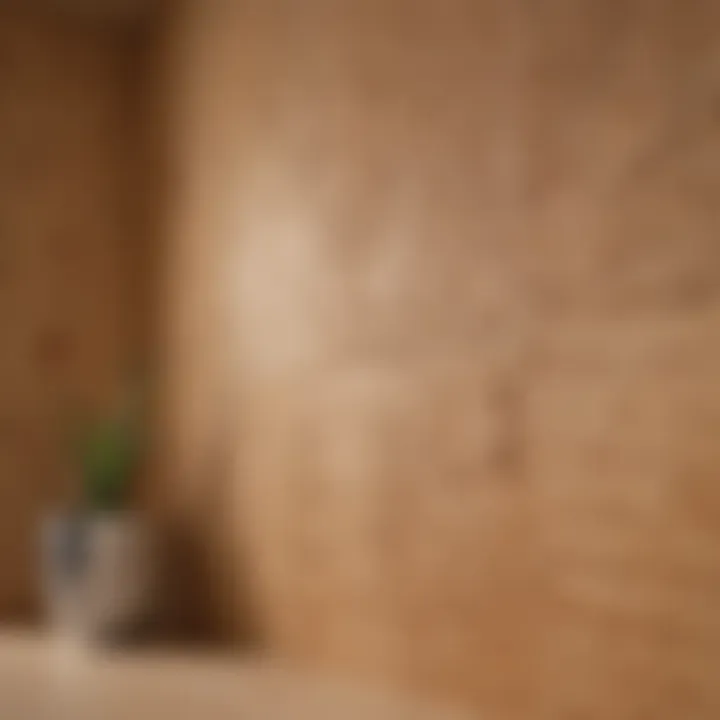
Pressed board plywood is synonymous with versatility. It serves many purposes, adapting to different styles, requirements, and environments with relative ease. Whether in schools, office spaces, or custom furniture design, its reach is extensive.
- Various Finishes: From sleek laminates to rustic veneers, pressed board plywood can be finished to match any aesthetic, be it modern or traditional.
- Dimensions and Thickness: It can be produced in a variety of thicknesses and formats, catering to any need from shelving to structural components.
Customization doesn’t stop at appearance; its capacity to be engineered to meet specific strength requirements means it can be tailored to those projects demanding extra resilience.
Ease of Handling and Processing
Working with pressed board plywood offers undeniable advantages in handling and processing. This feature makes it a preferred choice for builders and craftsmen, especially in trades where efficiency is non-negotiable.
- Lightweight: Compared to solid wood counterparts, pressed board plywood is considerably lighter. This quality facilitates easy transportation and installation, reducing fatigue on the job.
- Simplicity in Cutting and Shaping: Often described as user-friendly, it can be cut, drilled, or shaped without extensive tools or machinery. This accessibility empowers craftspeople, empowering even novice users to create with confidence.
Overall, the ease of use with pressed board plywood translates to time-saving efficiencies in projects, providing a smooth workflow from inception to completion.
"In a world that prioritizes efficiency and cost, pressed board plywood stands out as a favorable alternative, combining affordability with versatility and user-friendliness."
By leaning into these advantages, pressed board plywood not only meets a wide range of practical needs but also inspires creativity, allowing users to focus on design and quality without the associated burdens of traditional materials.
Limitations of Pressed Board Plywood
Understanding the limitations of pressed board plywood is crucial in evaluating its overall viability as a material. While it offers various advantages, this type of plywood is not without its drawbacks. Recognizing these limitations leads to informed decisions, whether you're in the furniture industry or planning a DIY project. Some limitations have implications for durability, sensitivity to moisture, and environmental impact, which deserve close examination.
Durability Concerns
When it comes to durability, pressed board plywood often raises eyebrows among seasoned professionals. Unlike solid wood, which has a natural resilience, pressed board plywood amalgamates smaller wood particles and adhesives under high pressure, resulting in a product that may not withstand wear and tear as well as its solid counterparts. For example, if you’re making an outdoor bench, pressed board plywood could warp or delaminate when exposed to the elements over time. This material is better suited for low-stress applications or indoor environments. If heavy-duty use is expected, solid wood or high-density composites might be a far better option.
Moisture Sensitivity and Maintenance
Moisture sensitivity is another glaring limitation of pressed board plywood. Its composition makes it particularly vulnerable to humidity and water, which can lead to swelling and decay if not properly maintained. A common scenario involves using pressed board plywood in kitchens or bathrooms, where moisture is prevalent. Without adequate sealing and protective measures, these sheets can quickly degrade, rendering them less functional and aesthetically pleasing. Furthermore, the maintenance required can be significantly higher than that of other materials, requiring regular checks and reapplication of sealants.
"A little prevention goes a long way; moisture is the enemy of pressed board plywood."
Environmental Impact
Environmental considerations also come into play with pressed board plywood. While it often utilizes smaller, faster-growing tree species — which can be seen as a sustainable choice — the adhesives and chemicals used in binding the particles can raise concerns regarding emissions and toxicity. Particularly in poorly ventilated spaces, these chemicals could off-gas and pose health risks. Additionally, the end of life for pressed board plywood isn't as simple as recycling. It often ends up in landfills, where its breakdown can release harmful substances into the soil.
Overall, awareness of these limitations is vital for making prudent choices in any project involving pressed board plywood. By carefully considering durability, moisture sensitivity, and environmental impact, one can better align their material choices with project needs and sustainability goals.
Sustainability and Environmental Considerations
In today's world, the call for sustainable practices is louder than ever, especially in industries that rely heavily on natural resources. When it comes to pressed board plywood, understanding the sustainability aspects is essential for manufacturers and consumers alike. This segment dives into both the sources of raw materials used and the lifecycle assessment of pressed board plywood, highlighting the broader environmental implications.
Sources of Raw Materials
Pressed board plywood mainly consists of various wood fibers, often sourced from fast-growing tree species such as pine, poplar, or eucalyptus. However, the sustainability of these sources can greatly vary. Ideal wood sourcing practices prioritize responsible forest management and often focus on:
- Recycling and Upcycling: Many manufacturers utilize waste wood fibers from other production processes, minimizing new timber extraction.
- Certified Forests: Using wood sourced from forests that adhere to environmental standards, like those certified by the Forest Stewardship Council (FSC), can help ensure that sourcing practices are ecologically sound.
- Alternative Biomass: Innovations are emerging that incorporate agricultural residues, such as straw or rice husks, as raw materials for pressed board plywood. This can reduce the demand for traditional logging and protect biodiversity.
Taking these practices into account is paramount as they not only contribute to a lower environmental footprint but also promote a circular economy.
Lifecycle Assessment
A lifecycle assessment (LCA) of pressed board plywood takes a comprehensive look at its environmental impact from production to disposal. This assessment is crucial for understanding the overall sustainability profile of the material. Key stages in the LCA include:
- Raw Material Extraction: This stage weighs the environmental effects of sourcing wood versus potential alternatives.
- Manufacturing Process: Here, considerations include energy consumption, greenhouse gas emissions, and waste generation during production. For example, utilizing more energy-efficient machinery and processes can significantly reduce the carbon footprint.
- Transportation: The impact of transporting raw materials and finished products is another factor. Local sourcing can help mitigate transportation emissions.
- Usage: The durability and maintenance requirements during the material's operational life play a vital role. Proper care can prolong the lifespan of pressed board plywood, decreasing the need for replacements.
- End-of-Life: Disposal methods must be evaluated to better understand their environmental effects, whether that means incineration, recycling, or landfill.
"Adopting effective lifecycle assessment methods allows manufacturers to identify critical areas where improvement can lead to significant environmental benefits."
In summary, focusing on sustainability and environmental considerations within the pressed board plywood sector reveals pathways to reduce ecological impact while promoting responsible use of resources. With the right sources and informed practices, the material can move towards a more sustainable future.
Technological Advancements in Production
In the contemporary landscape of pressed board plywood, technological advancements play a crucial role in shaping the efficiency and quality of production. The incorporation of innovative techniques not only enhances the manufacturing processes but also addresses several challenges that manufacturers face. Understanding these advancements can shed light on how they contribute to sustainability, cost-effectiveness, and overall product performance in both industrial and consumer markets.
Innovations in Material Bonding
Material bonding technologies have seen significant innovation in recent years. Traditional adhesives, while effective, have often raised concerns over toxic emissions and durability. New advancements focus on eco-friendly and high-performance bonding agents that minimize environmental impact while ensuring strength and longevity. For instance, the development of biobased adhesives has become prominent, derived from renewable resources like plant biomass. This shift fosters a healthier indoor environment because these adhesives tend to emit fewer volatile organic compounds (VOCs).
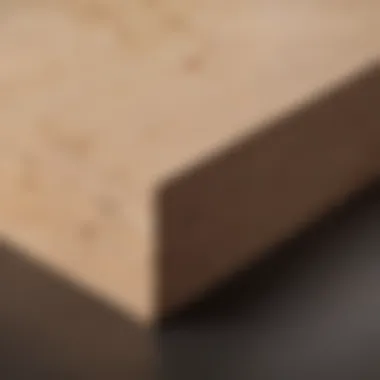
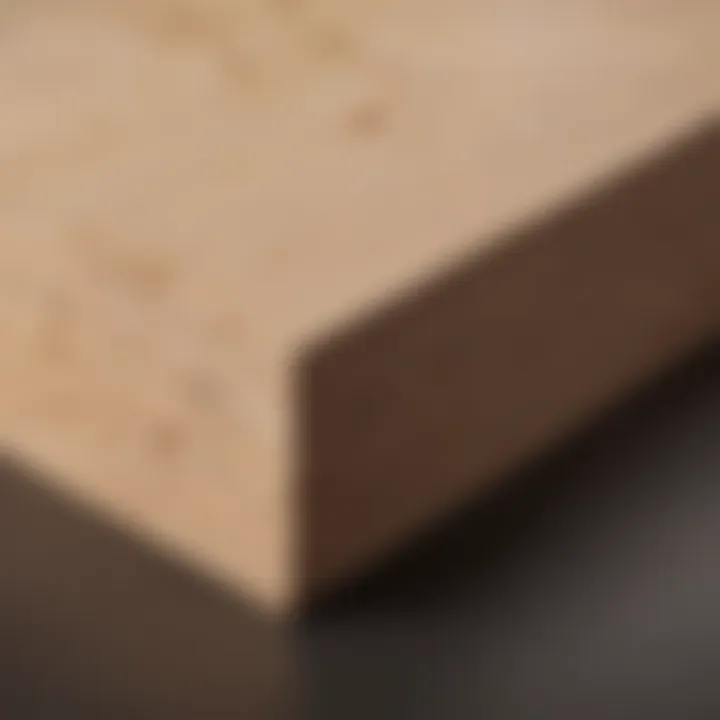
Moreover, advancements like cold pressing techniques have emerged as alternatives to traditional high-temperature processes. Cold pressing not only conserves energy but also helps maintain the integrity of the wood fibers. This results in finished products that are stronger and more resistant to moisture and other environmental factors. Companies like 3M and Henkel have been pioneering these advanced bonding solutions, which are becoming staples in pressed board plywood production.
Automated Manufacturing Processes
The automation of manufacturing processes in pressed board plywood signifies a leap towards efficiency, precision, and scalability. By integrating robotics and smart factory technologies, manufacturers can streamline operations and reduce labor costs. Automated systems can manage various tasks such as sorting, cutting, and assembling, enabling faster turnaround times without sacrificing quality.
Notably, the use of computer numerical control (CNC) machines has transformed how components are produced. These machines can intricately cut and shape materials with pinpoint accuracy, drastically reducing waste and errors in production. Moreover, automated quality control systems utilize sensors and imaging technology to detect defects in real-time, ensuring only top-quality products proceed to the next stages.
Adopting automation also allows for the flexibility that modern markets demand. Companies can quickly adapt their production lines to respond to shifts in consumer preferences or market trends without overhauling entire systems. This adaptability, combined with the ability to consistently produce high-quality materials, positions pressed board plywood as a competitive choice in the woodworking and construction industries.
The fusion of innovative bonding technologies and automated processes enhances not only the production efficiency but also contributes significantly to sustainability efforts.
Comparative Analysis with Other Materials
When discussing pressed board plywood, it’s essential to look beyond its own characteristics and consider how it measures up against alternative materials. This comparative analysis offers invaluable insights, revealing not just advantages and disadvantages of pressed board plywood, but also guiding potential users in their selection based on specific needs.
Solid Wood vs. Pressed Board Plywood
Solid wood has long been regarded as a classic choice for a wide range of applications, particularly in furniture manufacturing. However, pressed board plywood holds certain advantages that cannot be overlooked:
- Cost: Solid wood can be significantly pricier than pressed board plywood, making the latter a more budget-friendly option for many.
- Weight: Pressed board plywood tends to be lighter. This can be crucial for projects that require easily movable components.
- Uniformity: Pressed board plywood offers a consistent look and feel, unlike solid wood, which can sometimes vary dramatically in grain and coloration.
However, it's crucial to consider solid wood's durability. In certain scenarios, specifically high-end applications or where longevity is essential, solid wood often outshines pressed board plywood.
"Durability and aesthetics often take the spotlight when consumers make the case for solid wood; however, pressed board plywood shouldn’t be dismissed outright due to its versatility and affordability."
Composite Materials
A broader category includes composite materials, which combines different substances to achieve desired characteristics. Here’s where pressed board plywood faces both competition and opportunity:
- Material Synergy: Composites can be engineered for specific properties like moisture resistance or enhanced strength. Pressed board plywood, while versatile, inherently has limitations in terms of environmental stressors like humidity.
- Sustainability Factors: Many composite materials are designed with sustainability in mind, utilizing recycled components. While pressed board plywood can also be manufactured using recycled wood, it may not always be produced with the same eco-friendly focus as some composites.
- Performance Considerations: When it comes to load-bearing capabilities, certain composite materials can outperform pressed board plywood significantly, making them better suited for structural applications.
Both comparisons highlight the need to weigh the functional properties and suitability of pressed board plywood against solid wood and composites. Each material fills a niche, and understanding these distinctions enables smarter, more sustainable choices in various applications.
Future Outlook of Pressed Board Plywood
The discussion around the future of pressed board plywood is not just a passing fancy; it holds substantial weight in the timber and materials industry. With increasing emphasis on sustainability and efficient resource usage, understanding trends and projections in this sector can help stakeholders make informed decisions. Pressed board plywood combines practicality with versatility, which positions it well in an evolving marketplace.
Market Trends and Demand
The demand for pressed board plywood is on the rise, fueled by various factors that industries can scarcely ignore. Contemporary preferences lean towards materials that provide both economic and environmental benefits. Here are several trends influencing demand:
- Sustainable Products: With eco-conscious consumers in the driver's seat, manufacturers are pressed to offer sustainable solutions. Pressed board plywood, made from recycled wood fibers, fits this narrative, thus becoming increasingly popular.
- Lightweight and Strong: Users are continuously looking for options that are both lightweight and durable. Pressed board plywood meets this demand exceptionally well, often being lighter than solid wood while retaining adequate strength.
- Affordability: In a world where budgets are paramount, the cost-effectiveness of pressed board plywood cannot be overstated. It provides significant savings without skimping on quality, making it a go-to choice for furniture makers and constructors alike.
Spurred by these factors, demand for pressed board plywood continues to grow, leading to expansion across various markets and sectors. The construction sector, especially, is projected to witness a robust uptake as more builders lean towards composite materials over traditional wood.
Research and Development Directions
Looking ahead, the future of pressed board plywood also intertwines with innovations aimed at overcoming its current limitations. Research and development play a pivotal role in shaping materials that adapt to changing needs. Here are a few key areas of focus:
- Enhanced Resistance: Current studies aim to bolster moisture resistance characteristics of pressed board plywood. This would directly address durability concerns, making the material more versatile in different environments.
- Eco-Friendly Adhesives: The demand for non-toxic and sustainable adhesives is rising. R&D is focusing on developing adhesives that are as strong as traditional chemicals but derived from natural sources, ensuring that the end product remains environmentally friendly.
- Smart Technology Integration: Innovations such as smart sensors that monitor conditions affecting the plywood are becoming pertinent. This will open possibilities for functional furniture and applications that can adapt to user needs and environmental conditions.
In a nutshell, the future of pressed board plywood is bright, with market trends leaning toward sustainable, lighter, and more efficient materials. Research is driving innovations that will help ths material address its limitations effectively and cater to evolving market demands. By keeping an eye on these aspects, stakeholders can position themselves strategically in a competitive field, ensuring that pressed board plywood remains relevant for years to come.
"In a world increasingly marked by ecological concerns, pressed board plywood represents a promising blend of functionality and sustainability that resonates with the values of modern consumers."
Culmination
In summing up the profound impacts and implications of pressed board plywood, it becomes clear that this material stands at the crossroads of innovation and practicality within various industries. Through detailed examination, one can appreciate not only its structural capabilities but also the economic benefits it brings to the table. The discussion encapsulated in this article sheds light on quite a few specific aspects that can strongly influence choices regarding material selection in both industrial and personal projects.
Summary of Key Points
- Pressed board plywood is primarily composed of wood fibers bonded together through a mixture of resins and adhesives, resulting in a product that is both versatile and customizable.
- Applications span across furniture manufacturing, construction, and even packaging, showing its adaptability to different needs and settings.
- Its cost-effectiveness is another significant draw, allowing both manufacturers and consumers to achieve desired results without breaking the bank.
- On the flip side, limitations such as durability concerns, moisture sensitivity, and environmental implications compel stakeholders to weigh the options carefully.
- The analysis of market trends indicates a continual demand for pressed board plywood, suggesting its longevity within the industry.
The essence of materials like pressed board plywood goes beyond mere functionality; it embodies the opportunity for sustainable practices while meeting the demands of today’s fast-paced markets.
Final Thoughts
When considering the future of pressed board plywood, it becomes essential to stay informed about ongoing research and the advancements that continually reshape this material category. The dialogue on sustainability is crucial as it influences societal perspectives and regulations alike. There’s a budding interest in improved manufacturing processes that can lead to both enhanced durability and minimized environmental impact.
Ultimately, pressed board plywood serves as a stark reminder that in the tapestry of modern materials, choices aren't just about properties but also about decisions made for the greater good. As the landscape shifts, both consumers and producers must adapt while keeping a finger on the pulse of innovation and integrity in usage.
"The future is what we do today; it shapes the context in which we make our decisions tomorrow."
As we conclude, it’s clear this topic holds significance not merely as a study of materials but as a reflection on innovation, sustainability, and responsibility within every project. Individuals, researchers, and professionals alike should take these insights to heart, always striving for smarter and greener paths in their choices.