Understanding Rectifier Heat Sinks in Electronics
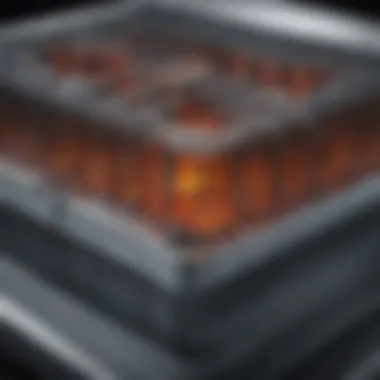

Intro
Rectifiers, the unsung heroes of electronic circuits, play a fundamental role in converting alternating current (AC) into direct current (DC). However, this transformation generates heat, which, if left unchecked, can lead to reduced efficiency and potential damage. This where heat sinks come into play.
Heat sinks are crucial for maintaining optimal operational temperatures. They help dissipate heat away from the rectifier, thereby ensuring the longevity and reliability of electronic systems. In this article, we will delve deep into the design, functionality, and applications of rectifier heat sinks, providing a thorough understanding of how they contribute to thermal management.
Key Concepts
Definition of Primary Terms
Before we embark on this exploration, it is essential to clarify a few terms:
- Rectifier: An electronic device that converts AC to DC.
- Heat Sink: A component designed to absorb and dissipate heat, maintaining the performance of the device it is cooling.
- Thermal Conductivity: A measure of a material's ability to conduct heat.
Understanding these fundamental concepts sets the stage for grasping how rectifier heat sinks function and their design considerations.
Related Concepts and Theories
The functionality of heat sinks is governed by principles of thermodynamics and heat transfer.
- Conduction: The transfer of heat through a material. Heat sinks often utilize materials with high thermal conductivity, such as aluminum or copper, to maximize heat dissipation.
- Convection: The process of heat transfer through a fluid, generally air in the case of heat sinks. This is why many heat sinks include fins or other structures to increase surface area and enhance airflow.
- Radiation: While less significant in practical heat sink design, it is still part of the heat loss mechanisms that can work alongside conduction and convection to manage thermal output.
By weaving these concepts into the fabric of our understanding, we can appreciate the intricate balance that heat sinks maintain within electronic devices.
Future Directions
Gaps Identified in Current Research
Although the field of thermal management has made significant strides, there are still gaps that warrant further investigation. For example, current research has primarily focused on traditional materials like aluminum and copper. There is a potential for innovative materialsâsuch as graphene compositesâthat might improve heat dissipation even further.
Suggestions for Further Studies
Future studies might explore:
- Nanotechnology: Investigating how nanomaterials can enhance thermal conductivity and efficiency.
- Smart Heat Sinks: Development of adaptive heat sink designs capable of responding to temperature changes in real-time.
- Environmental Impact: Assessing the sustainability of various materials used in heat sinks and their manufacturing processes.
Foreword to Rectifier Heat Sinks
In the realm of electronics, the role of rectifier heat sinks cannot be overstated. As electronic devices seek to enhance performance and efficiency, these components emerge as unsung heroes, working quietly behind the scenes to ensure that excessive heat does not wreak havoc on sensitive circuits. The relationship between heat generation and performance is profound, making understanding heat sinks vital for anyone involved in electronic engineering or applications.
Defining Rectifiers
Rectifiers are devices that convert alternating current (AC) to direct current (DC). They are fundamental in power supply circuits and are essential for numerous electronic applications, from household appliances to industrial machinery. When rectifiers operate, they inevitably generate heat. This heat can lead to failure and inefficiencies if not properly managed. Therefore, knowing what rectifiers are is just the starting point in grasping the significance of heat sinks. Not only do they address the heat produced, but they also enhance the rectifierâs reliability and lifespan, creating a crucial synergy between components and thermal management systems.
Importance of Thermal Management
Thermal management encompasses the strategies and methods used to control temperature, ensuring devices operate within optimal thermal limits. For rectifiers, effective thermal management is more than just a safety net; itâs a necessary aspect that enhances performance. Here are key factors worth noting:
- Preventing Thermal Runaway: High temperatures can lead to a condition known as thermal runaway, where increased heat generation leads to even more heat. This cycle can ultimately destroy the rectifier.
- Enhancing Efficiency: An effective heat sink can help maintain the operating temperature within acceptable limits, thereby optimizing the efficiency of power conversion.
- Ensuring Longevity: Consistent high temperatures can shorten the lifespan of electronic components. By managing heat, we extend operational life, reducing the need for replacements.
"Effective thermal management is not merely a preventative measure; it's a fundamental pillar of electronic device performance."
Principles of Heat Dissipation
The journey into the realm of rectifier heat sinks begins with understanding heat dissipation. Heat, an inevitable byproduct of electronic operations, needs to be effectively managed, or else components may fail under excessive thermal stress. The principles governing heat dissipation play a pivotal role in the overall efficacy of rectifiers in electronic circuits. In an electronic environment, the function of heat sinks cannot be underestimated; they are the unsung heroes that tackle heat build-up to ensure equipment longevity and reliability.
Thermal Conduction
Thermal conduction is the first fundamental mechanism by which heat transfers through a solid material. This process relies on the direct contact between molecules; warmer atoms transfer their energy to cooler atoms over time. When considering materials for rectifier heat sinks, thermal conductivity is key. Aluminum, for example, exhibits excellent conductivity at a fraction of the weight of copper, making it a popular choice despite copper's superior conductivity. Good thermal conductors ensure that heat doesnât linger in one location on the heat sink, but rather spreads evenly across the surface, allowing for effective dissipation.
Itâs imperative to recognize that the design also influences conduction. Surface roughness can create micro-cavities on the heat sink, which, although contributing to an increase in surface area, may also trap airâa thermal insulatorâif not optimally designed. Thus, finding the right balance between maximizing surface area while maintaining effective conduction is crucial for heat sink performance.
Thermal Convection
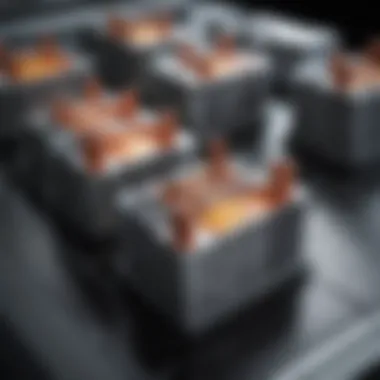
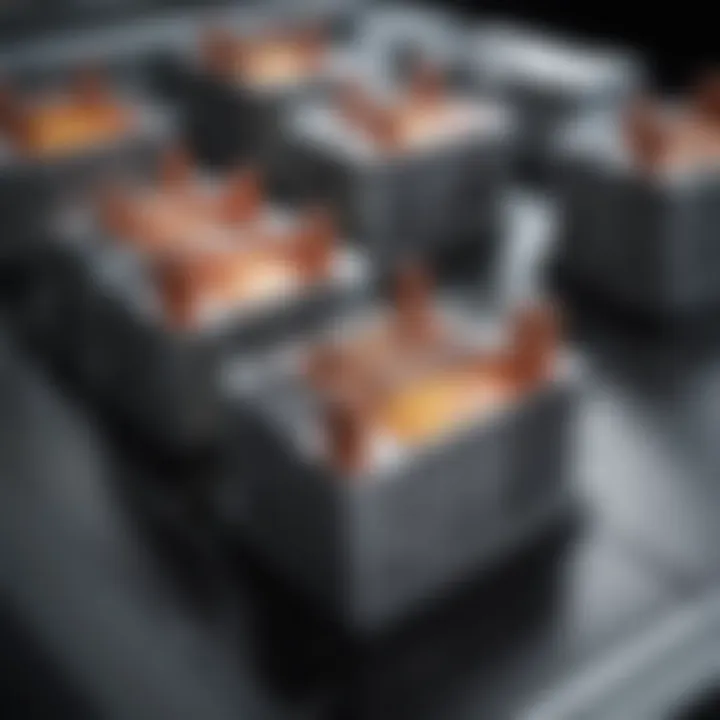
Once heat travels through a solid, it then disperses into the surrounding fluidâor airâvia convection. This is where things get interesting. Convection can be broadly classified into two types: natural and forced. Natural convection relies on the tendency of warmer air to rise, leading to a constant reshuffling of air near the heat sink surface. However, this is often a slow process and may not suffice for applications requiring rapid heat dissipation.
In contrast, forced convection utilizes fans or blowers to actively circulate air, dramatically enhancing heat removal. When designing rectifier heat sinks, it's essential to consider whether natural convection alone is adequate for the thermal load or if additional cooling methods are necessary. Proper airflow design can actually create a harsh but beautiful dance of thermal energy being swept away from delicate components.
Radiation in Heat Transfer
Lastly, we have radiation, the silent transfer of heat via electromagnetic waves. Unlike conduction and convection, radiation doesnât require a medium. In the context of rectifier heat sinks, radiation accounts for a smaller portion of overall heat dissipation, but still plays a role, especially at higher temperatures where the intensity increases significantly.
To enhance radiative heat transfer, surfaces can be finished with matte black coatings, improving emissivity. Something to consider: while shiny surfaces may look appealing, they reflect heat rather than emit it. If a heat sink's temperature hovers around a lethal point, a little tweak in surface treatment may prolong the life of components attached.
In essence, understanding the triad of thermal conduction, convection, and radiation illuminates the path toward efficient heat management in electronic designs. The effective interplay among these processes ensures that rectifier heat sinks uphold their critical role in maintaining thermal stability in various applications. As we dig deeper into design considerations and challenges, these principles will underpin the strategies employed to make rectifier heat sinks as efficient and reliable as they are.
Design Considerations for Rectifier Heat Sinks
In the realm of electronic engineering, the design of rectifier heat sinks is not merely an afterthought; it's a vital cog in the machinery of thermal management. Effective heat sink design directly impacts the performance and longevity of rectifiers, which are pivotal in converting AC to DC. As technology continues to advance, the electronic loads are becoming increasingly demanding, making heat dissipation more critical than ever. This section will unpack the essentials of designing rectifier heat sinks, emphasizing the key elements that contribute to efficient thermal management.
Material Selection
Aluminum
Aluminum stands out as one of the most popular materials for heat sinks. Its lightweight nature and excellent thermal conductivity make it a top contender in many applications. One major advantage of aluminum is its cost-effectiveness. This means engineers can achieve a good balance between performance and budget. Additionally, aluminum has a relatively high specific heat capacity which allows it to absorb more heat before its temperature rises significantly.
âThe right material can be the knifeâs edge in thermal management.â
However, while itâs easy to work with and can be extruded into various shapes, one downside is its susceptibility to oxidation. This can create a barrier that affects thermal conductivity, soaking up some performance benefits.
Copper
Copper is regarded as the gold standard for thermal conductivity among heat sink materials. It conducts heat better than aluminum, enabling efficient heat transfer away from the electronic components. This characteristic can be a game changer for high-performance applications, where every degree counts. The ductility of copper also allows for intricate designs, which can include fins and other geometric enhancements to maximize surface area and heat transfer.
However, the downside of using copper is its heavier weight and higher cost. These factors can limit its application in certain sectors like consumer electronics, where size and cost are critical.
Composite Materials
Composite materials are increasingly gaining traction for heat sink applications. They combine the favorable properties of different materials, tapping into the strengths of each. For instance, a composite made of metal matrix or polymer can offer a lightweight solution while still maintaining adequate thermal properties.
The main benefit of composites is their ability to be engineered for specific requirements. They can be tailored to specific thermal or mechanical needs which provides designers with flexibility. However, this bespoke nature can lead to higher manufacturing costs and complexities in production.
Geometric Configurations
Finned Designs
Finned designs have become synonymous with effective heat dissipation. By increasing the surface area significantly, these heat sinks can disperse heat more efficiently into the surrounding environment. Fins can be arranged in various orientations and densities, which affects airflow and thermal performance.
A critical aspect of finned designs is their ability to maintain a compact footprint while maximizing heat transfer. This makes them particularly advantageous in applications where space is at a premium. However, the challenge lies in ensuring that the design accommodates airflow well, as obstructed airflow can nullify the benefits they're meant to provide.
Flat Plate Heat Sinks
Flat plate heat sinks offer simplicity and are used widely in various applications. They provide a uniform surface area for heat dissipation and can easily be mounted to devices. The straightforward design enables manufacturers to incorporate them into tight spaces without fuss.
Flat plate designs can be enhanced by adding thermal interface materials (TIMs) to improve contact with the components they are cooling. Yet, their downside is often lower thermal performance compared to more complex designs like finned or active systems since they have less surface area exposed to ambient air.
Active Heat Sink Systems
Active heat sink systems incorporate fans or other active components to encourage airflow over the heat sink. This can drastically improve thermal performance, especially in environments with limited natural airflow. They are ideal for high-density applications where passive cooling may not suffice.
However, the power consumption and noise generated by active systems can pose challenges in specific applications, particularly in silent, compact designs. Balancing performance with operational noise and energy demands becomes a central design consideration for engineers.
Impact of Surface Area
Increasing surface area is fundamental to enhancing heat dissipative efficiency. The wider the surface area exposed to the air, the more heat can be transferred away from the heatsink. Finned designs are a prime example of how geometric alterations can manipulate heat transfer capacity. However, this increase in surface area must also be balanced against mounting constraints and aesthetic factors in product design, often leading to innovative design solutions that optimize both functionality and form.
Measuring Heat Sink Performance
Evaluating the performance of heat sinks is pivotal in the realm of electronics, particularly when it comes to maintaining the optimal functionality of rectifiers. The more effectively we can assess heat sink performance, the better we can ensure the longevity and stability of electronic components. Understanding various measurement methodologies, such as thermal resistance and benchmarking, provides engineers, educators, and researchers with essential tools to analyze and enhance heat sink efficiency.
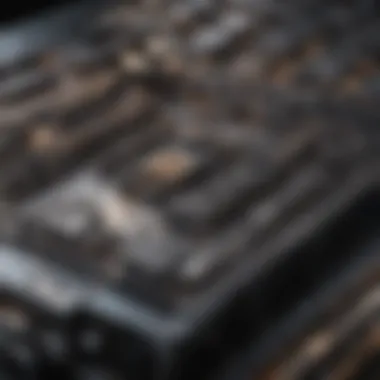
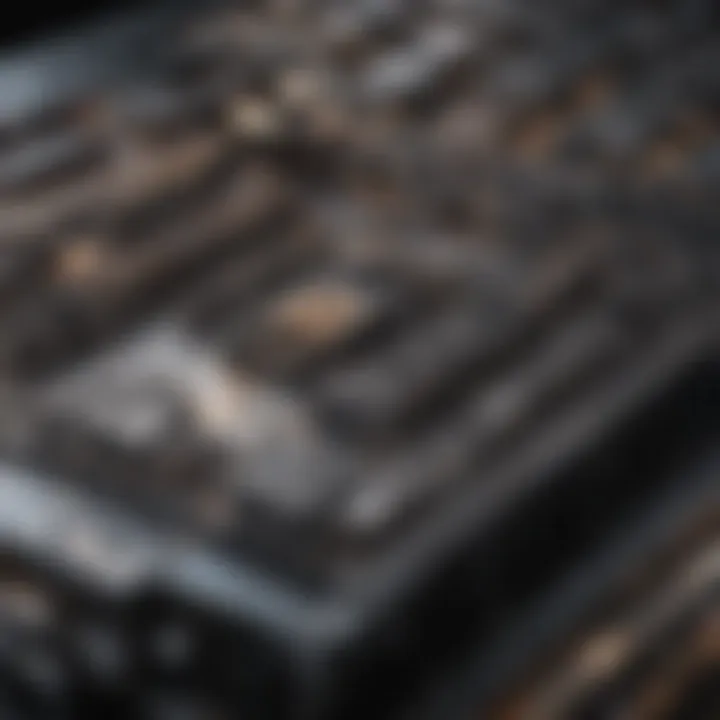
Thermal Resistance Parameters
Thermal resistance is a crucial parameter in heat sink design and performance assessment. It's essentially the opposition to heat flow, quantifying how effectively a heat sink can transfer absorbed heat away from the rectifier and into the surrounding environment. This parameter is usually represented in degrees Celsius per watt (°C/W).
Two primary aspects come into play when discussing thermal resistance:
- Junction-to-case resistance: This measures the resistance from the semiconductor junction, through the chip package, to the heat sink. A low value here indicates efficient heat transfer from the chip to the heat sink.
- Case-to-ambient resistance: This denotes the resistance from the heat sink to the ambient air surrounding it. Here again, lower values signify more efficient heat dissipation.
Understanding these thermal resistance parameters is vital because if they are too high, the heat sink will not effectively prevent the rectifier from overheating. With increasing demands on electronic circuitry, a poor thermal resistance rating may lead to device failure. Investing time in accurately measuring and interpreting thermal resistance can save not just components but potentially system failures down the line.
Benchmarking Techniques
Benchmarking is another key aspect of measuring heat sink performance. It provides a standard against which the effectiveness of a heat sink can be evaluated. This process involves testing heat sinks under controlled conditions and comparing their performance against known standards or similar products.
Some widely used benchmarking techniques include:
- Comparative Testing: This involves placing various heat sinks in identical conditions and measuring their thermal performance to find out which one excels. Experiments can help identify the best materials or designs under specific conditions.
- Steady-State Testing: In this method, a prolonged period is allowed for the heat sink to reach thermal equilibrium. By recording the steady-state temperature of the heat sink and the power dissipated, one can find a reliable thermal resistance value.
- Transient Testing: Unlike steady-state testing, this briefly assesses how a heat sink performs during sudden changes in power input. This method helps gauge how well a heat sink can handle spikes or dips in thermal loads, which are common in many applications.
"When evaluating the performance of heat sinks, itâs not just about the numbers; itâs about understanding the real-world scenarios where they will be deployed."
Benchmarking provides an empirical foundation upon which improvements can be built or changes can be justified. Awareness of varying performance across diverse conditions can guide researchers and professionals towards more refined designs that are better suited to specific applications, whether in consumer electronics, industrial power supplies, or electric vehicle systems.
The meticulous measurement of heat sink performance through thermal resistance parameters and benchmarking techniques holds significant potential. It is instrumental in sustaining the necessary heat management within electronic systems, which ultimately leads to enhanced performance and reliability.
Challenges in Heat Sink Design
The design of heat sinks is a crucial aspect when it comes to managing the thermal performance of rectifiers in electronic circuits. The efficiency with which a heat sink dissipates heat can significantly impact the reliability and longevity of electronic components. There are several challenges that engineers face in this domain, including rapidly evolving electronic loads, constraints in circuit space, and issues surrounding reliability and longevity.
Evolving Electronic Loads
As technology advances, the electronic devices we use are becoming more powerful yet compact. This shift towards high-efficiency rectifiers means they generate more heat in a limited space. For instance, modern power supplies and electric vehicles utilize sophisticated rectifiers that operate at higher frequencies and loads. This means the companion heat sinks must not only be effective but also adaptable to this increasing thermal output. Designers need a grasp on the thermal performance of materials under various operating conditions. New materials with better thermal conductivity, such as certain advanced composites, are being explored to address these rising demands.
Space Constraints in Circuit Design
When designing circuits, physical space often comes at a premium. The integration of heat sinks into compact environments presents various challenges that require creative solutions. For example, traditional heat sinks might not fit within the slim profiles of modern electronic devices. Therefore, engineers often turn towards more innovative designs that maximize the surface area without increasing size too much. Options like finned designs or heat sinks that incorporate cooling fans can address both space and thermal dissipation needs.
As thermal management becomes more critical, the idea of making the most of available space leads to creativity in heat sink design.
Reliability and Longevity Issues
The reliability of a heat sink is paramount in the overall performance of an electronic system. If a heat sink fails, the consequences can be dire, often leading to systemic component failure. Designers must consider the material's durability over time, which includes resistance to thermal cycling and oxidation. Copper, for instance, has excellent thermal properties but can be more prone to corrosion than aluminum if not properly treated. Manufacturers also have to consider the heat sink's operating environmentâextreme temperatures and humidity can greatly impact its longevity. Understanding the expected lifespan of a heat sink and its materials helps engineers make more informed choices to ensure system reliability.
In sum, navigating the challenges of heat sink design in the context of rectifiers requires thorough knowledge of the current technological landscape. Engineers must juggle evolving electronic loads, space limitations, and the imperative for reliable, long-lasting solutions. By staying ahead of these challenges, the impact on overall electronic performance can be significantly enhanced.
Applications of Rectifier Heat Sinks
Rectifier heat sinks serve a fundamental role in enhancing the performance and reliability of electronic systems across various sectors. Their ability to dissipate excess heat is crucial for ensuring efficient operation in devices where high currents are common. Without effective thermal management, rectifiers can overheat and fail, leading to decreased functionality or complete system breakdown. This section covers a few notable applications where this technology shines, illuminating its importance in modern electronics.
Industrial Power Supplies
In industrial settings, power supplies are at the heart of operation, powering everything from assembly lines to heavy machinery. Rectifier heat sinks are indispensable here due to the significant heat generated when converting alternating current (AC) to direct current (DC).
- Robust Performance: Efficient heat sinks can routinely withstand fluctuating loads, enhancing reliability.
- Extended Lifespan: By managing temperatures effectively, they prolong the lifespan of sensitive components, reducing maintenance costs.
- Safety Factors: In environments where machinery operates at high temperatures, heat sinks help mitigate risks associated with thermal runaway.
Industrial applications often involve larger rectifier systems where the heat sinking must be optimized for space and efficiency.Operations in factories where heat emission can lead to inefficient energy use must rely heavily on proper designs of rectifier heat sinks.
Power Electronics in Electric Vehicles
Electric vehicles (EVs) have garnered attention in recent years, and rectifier heat sinks play a pivotal role in electric drive trains. With advancements in technology, the electronics involved have become smaller yet more powerful, resulting in increased thermal output.
- Thermal Management: In EVs, effective thermal management is crucial for maintaining battery efficiency and longevity. Heat sinks ensure that rectifiers used in charging systems and DC-DC converters function optimally under stress.
- Weight Considerations: Because weight is a critical factor in EV design, choosing lighter materials for heat sinks can aid efficiency without compromising cooling capability.
- Integration with Other Systems: Effective design integrates heat sinks with other thermal management strategies, ensuring the entire system operates harmoniously.
Consumer Electronics Device Integration
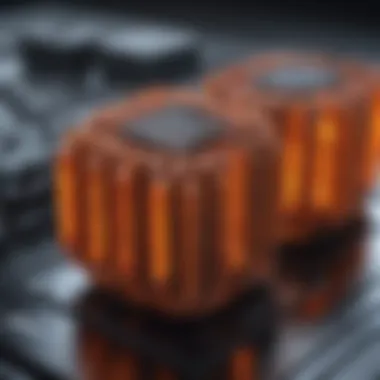
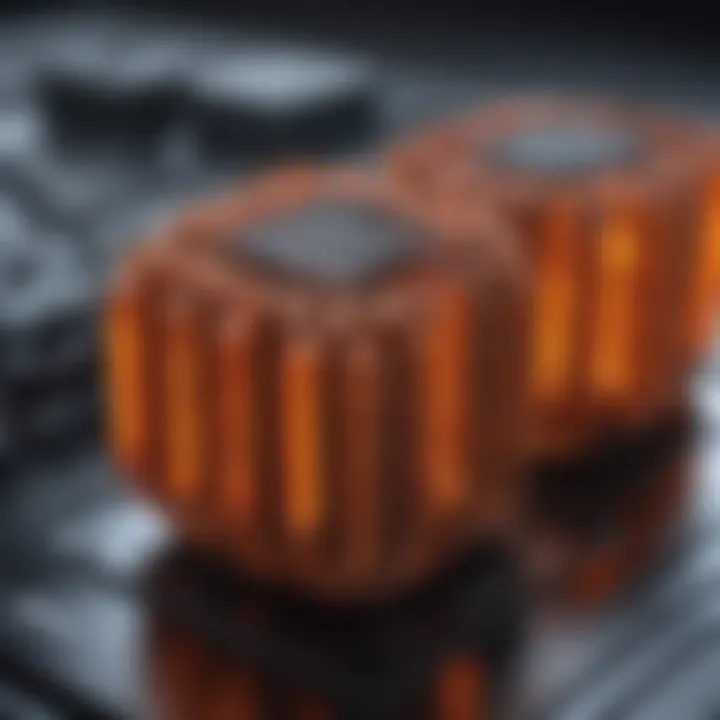
In the realm of consumer electronics, the drive for compact and lightweight devices presents unique challenges. Common gadgets like smartphones and laptops employ rectifiers for power conversion and system stability, making effective heat dissipation vital.
- Aesthetic Design: Engineers must consider not only functionality but also the aesthetics of heat sinks in sleek consumer devices.
- Miniaturization: The need for smaller yet efficient heat sinks has spurred innovation. Using advanced materials and innovative designs allows for maximizing thermal performance without increasing device bulk.
- User Experience: Ensuring a device doesnât overheat contributes significantly to user satisfaction, as warmer devices can lead to discomfort during use.
In summary, rectifier heat sinks are integral to various applications, helping to safeguard system performance through adept thermal management. As technology advances, the designs of these heat sinks must adapt, addressing ever-changing demands across diverse sectors.
Technological Innovations in Heat Sink Design
The realm of heat sink design has witnessed remarkable shifts as technology advances. These innovations are not merely enhancements but critical developments that cater to the rising demands of modern electronics. Efficient thermal management has become pivotal, particularly as electronic components shrink in size yet become more potent. The significance of this section will explore specific elements that contribute to the heightened performance of heat sinks and the benefits they present.
Advanced Materials and Coatings
A profound change in heat sink design arises from the use of advanced materials and specialized coatings. Adopting materials like graphite or ceramics has made a noticeable impact. Graphite, for instance, exhibits high thermal conductivity combined with lightweight properties, enabling effective heat dissipation without significant weight penalties.
Moreover, coatings play a vital role. These can bolster the performance of traditional materials like aluminum. A coating can improve heat transfer qualities or resist environmental degradation. The application of thermal interface materials can also reduce thermal resistance between the heat sink and electronic components. This attention to detail ensures optimal performance of the entire system.
For example, the use of nickel plating not only enhances corrosion resistance but can improve heat transfer by increasing the surface area. This attention to the intricate details of materials can lead to considerable gains in overall efficiency.
In the end, the choice of materials and coatings is about necessity and foresight. Itâs not just about what is available but what will stand the test of time.
3D Printing in Heat Sink Fabrication
Another game changer in the heat sink manufacturing landscape is 3D printing. This technology opens a world of possibilities, allowing for customized designs that could not be feasibly produced through traditional means. The ability to create intricate geometries leads to enhanced heat dissipation properties due to expanded surface areas.
With 3D printing, manufacturers can tailor designs specific to application needs. For example, a heat sink can be designed to fit snugly within a confined space, optimizing airflow and heat transfer, something mass-produced models struggle with. The freedom to iterate and improve designs quickly without the costs associated with traditional tooling means heightened innovation and flexibility in development processes.
Additionally, utilizing materials that can be 3D printed, like certain metals or polymers, ensures that manufacturers can iterate designs in response to evolving thermal demands. This real-time adaptability positions 3D printing as an essential method in future heat sink fabrication.
Ending
Technological innovations in heat sink design are not mere enhancements; they represent the convergence of efficiency, material science, and responsive engineering practices. From advanced materials that maximize performance to 3D printing capabilities that allow for unparalleled customization, these innovations are defining the future of thermal management in rectifiers. With the adoption of these technologies, the challenges of overheating in electronic components can be more effectively mitigated, laying the groundwork for more robust and reliable electronic systems.
Future Directions of Rectifier Heat Sinks
The future landscape of rectifier heat sinks promises to be both exciting and challenging. As electronic devices evolve and consumer expectations intensify, the demand for efficient thermal management systems continues to rise. Itâs undeniable that as the number of devices that require heat management increases, so does the complexity of designs that cater to their unique needs. In this light, understanding the upcoming trends is not just beneficial; it's imperative for staying ahead in the industry.
Integration with Smart Technologies
As we move forward, one of the key focal points will be the integration of heat sinks with smart technologies. This includes smart sensors that can monitor temperature fluctuations in real-time. The essence behind this integration is to create a more responsive and adaptive thermal management method. Imagine a heat sink that can adjust itself based on real-time temperature data! Such innovations could lead to systems that optimize their cooling capabilities, improving efficiency and perhaps even extending the lifespan of electronic components.
Moreover, the compatibility of these systems with IoT devices opens a whole new realm of possibilities. In an era where everything is connected, having heat sinks that can communicate with other components of an electronic system lays the groundwork for smarter operation. For instance, heat sinks that sync with a central computing unit to dynamically manage heat dissipation can minimize energy waste and enhance overall device performance.
This shift toward smart heat management is not merely a trend; it is a fundamental change in how thermal practices could be approached. The integration will necessitate consideration for both hardware adaptability and software algorithms that can efficiently manage heat dissipation according to usage conditions.
Sustainable Design Practices
Equally important is the shift toward sustainable design practices in the realm of rectifier heat sinks. With the increasing emphasis on sustainability, manufacturers are being pushed to rethink material choices, production processes, and end-of-life implications for their products. This means using more recyclable and environmentally-friendly materials in heat sink design, which can dramatically reduce the ecological footprint.
A few noteworthy points about sustainable practices in heat sink design include:
- Material Selection: Opting for materials such as aluminum and copper that not only provide excellent thermal conductivity but are also recyclable.
- Energy Efficiency: Innovations in design that require less energy in manufacturing. This might involve improving the manufacturing processes to minimize waste or energy consumption.
- Modularity: Creating heat sinks that can be easily upgraded or repaired rather than discarded when improvements or enhancements are needed.
- Lifecycle Assessments: Incorporating evaluations of the environmental impact from the design phase to disposal, allowing for a thorough understanding of the product's footprint.
Emphasizing sustainable practices will not only align the industry with global efforts toward environmental conservation but could also lead to cost savings in the long run. As manufacturers explore more sustainable pathways, the double benefit of efficiency and reduced environmental harm becomes an appealing proposition.
"The future of rectifier heat sinks is not just about managing heat better, it's about doing so sustainably."
In summary, the future of rectifier heat sinks lies in their ability to adapt to smart technologies while pursuing sustainability as a design principle. This dual focus opens up exciting new avenues for engineers and designers alike, creating an environment where innovation meets responsibility, ultimately leading to better heat management solutions.
The End
In summarizing the insights gained from our exploration of rectifier heat sinks, it becomes abundantly clear that these components are titans of thermal management within electronic systems. Their significance is not merely as add-ons, but as pivotal players that ensure operational efficiency and longevity. The interplay between rectifiers and heat sinks is at the heart of modern electronic design, where efficiency and reliability are king. Understanding the aforementioned factorsâsuch as thermal resistance, material selection, and geometic configurationsâilluminates the path toward optimizing both heat sinks and their integrated systems.
Summary of Key Points
- Defining Heat Sinks: Rectifier heat sinks dissipate excess heat, preventing system failure, and extending device life.
- Thermal Dynamics: Knowing how heat moves via conduction, convection, and radiation helps in crafting effective heat management strategies.
- Material Choices: Selecting the right material (like aluminum or copper) is critical for thermal performance and weight considerations.
- Design Innovations: Attention to geometryâfinned designs or active systemsâcan have significant effects on heat dissipation efficiency.
- Application Scope: From industrial power supplies to consumer electronics, the applications of rectifier heat sinks are vast and varied.
This summary draws attention to the essential points discussed and sets the stage for further insights into heat sink development and its future trajectory within electronic designs.
Final Thoughts on Rectifier Heat Management
As the electronic world continues to evolve at a breakneck pace, the importance of effective heat management through rectifier heat sinks cannot be overstated. The integration of smarter technologies and sustainable practices is paving the way for more efficient heat sinks that not only keep devices cool but also contribute positively to energy consumption outcomes. The emphasis on design innovations, such as advanced materials and techniques like 3D printing, illustrates an exciting frontier for future developments.