Understanding Recuperative Thermal Oxidizers: Efficiency and Applications
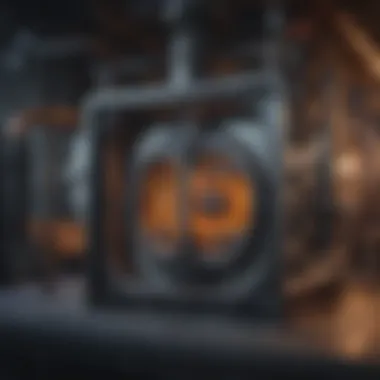
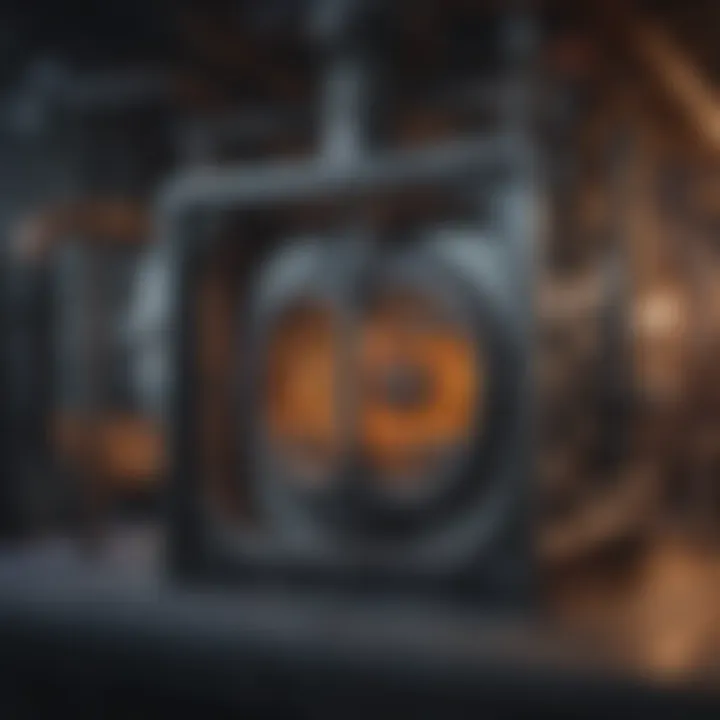
Intro
In today’s industrial landscape, the increasing awareness around air quality and environmental impact is leading many organizations to take a closer look at their emissions control strategies. A significant player in this domain is the recuperative thermal oxidizer. These systems extend beyond mere compliance with regulations; they represent a proactive approach towards sustainable operations. To fully grasp the implications of adopting such technologies, it’s essential to set the stage with fundamental concepts.
Key Concepts
Definition of Primary Terms
To understand recuperative thermal oxidizers, one must first familiarize themselves with some key terminology:
- Thermal Oxidation: This refers to the process of combusting hazardous air pollutants at high temperatures, resulting in their conversion into less harmful substances, primarily carbon dioxide and water.
- Recuperative System: This term denotes a system that captures waste heat from the exhaust gases and returns it to the combustion process. The primary goal here is to improve overall energy efficiency.
- Hazardous Air Pollutants (HAPs): These encompass a range of volatile organic compounds and other chemicals known to pose risks to human health, necessitating effective management.
Each term is more than just jargon; they’re pieces of a larger puzzle that illustrates both the operation and significance of recuperative thermal oxidizers.
Related Concepts and Theories
To further comprehend this technology, it’s valuable to consider related notions that shape its application. For example:
- Energy Recovery: This concept is central to recuperative thermal oxidizers. The energy harvested by using waste heat not only increases efficiency but frequently decreases operational costs. Businesses are realizing that saving energy translates directly to saving money.
- Emissions Regulations: Understanding the regulatory context is crucial. Policies such as the Clean Air Act drive the urgency for industries to invest in advanced emissions control technologies.
- Lifecycle Analysis: In evaluating any emissions control technology, it’s essential to consider the entire lifecycle from production to disposal. This broader perspective can often reveal unexpected benefits or drawbacks associated with different technologies.
"The true measure of technology’s value lies in its ability to integrate seamlessly into existing frameworks while minimizing both costs and environmental footprints."
Future Directions
Gaps Identified in Current Research
Despite the advancements, there remain unexplored territories within the field of recuperative thermal oxidizers. Most notably:
- Data on Long-Term Performance: There’s a lack of comprehensive performance data over extended periods, making it difficult for industries to evaluate the systems' durability and reliability.
- Integration with Emerging Technologies: While there's an increasing interest in hybrid systems that combine recuperative thermal oxidizers with other technologies—like scrubbers or biofilters—research is still catching up with market applications.
Suggestions for Further Studies
To forge ahead in the realm of emissions control, stakeholders should consider:
- Innovative Cooling Techniques: Exploring ways to enhance the heat transfer process could lead to improved energy recovery.
- Adaptation to Varied Industries: As industries differ, studies assessing how recuperative thermal oxidizers can be customized might yield fruitful results.
- Real-World Case Analysis: Investigating operational experiences can offer valuable insights into best practices and efficiency metrics.
These perspectives could lay the groundwork for future innovations, driving further development in emissions control technologies.
Foreword to Recuperative Thermal Oxidizers
In the face of modern environmental challenges, the importance of recuperative thermal oxidizers becomes ever more pronounced. These systems play a crucial role in mitigating hazardous air pollutants, ensuring that industries can continue their operations while adhering to stringent environmental regulations. By capturing and converting harmful emissions into less toxic substances, recuperative thermal oxidizers not only contribute to air quality improvement but also offer significant energy savings. Understanding this technology is paramount for professionals navigating the complex landscape of industrial emissions control.
Definition and Overview
A recuperative thermal oxidizer is a specialized device designed to oxidize volatile organic compounds (VOCs) and other hazardous air pollutants. When these pollutants enter the oxidizer, they are subjected to high temperatures, typically exceeding 700 degrees Celsius. This process breaks down harmful substances into benign gases like carbon dioxide and water vapor, effectively reducing their environmental impact.
The recuperative aspect refers to the system’s method of heat recovery. In this design, the heat generated from the combustion process is captured and used to preheat the incoming exhaust gases. Consequently, this can result in reduced fuel consumption and operational costs, making the technology both environmentally friendly and economically advantageous. This two-pronged benefit is a major selling point for industries looking to balance cost and compliance with environmental policies.
Historical Development
The journey of recuperative thermal oxidation technology can be traced back to the mid-20th century, when industries began facing increasing scrutiny over air emissions. As environmental awareness grew, so too did the need for effective air pollution control technologies. Early systems primarily revolved around simple incineration processes, which were blunt and often inefficient.
The transition to recuperative thermal oxidizers marked a significant evolution in emissions control. By the late 1970s, with the advent of more sophisticated heat recovery methods and advances in combustion technology, recuperative thermal oxidizers began to gain traction in various industrial sectors. Firms noticed that by implementing these systems, they could not only comply with regulations but also lower their operating costs through energy efficiency. This led to a broader acceptance of recuperative thermal oxidation technology, culminating in its integration into various manufacturing practices and waste management approaches.
Looking towards the future, developments in materials science and automation will likely play a key role in further enhancing the efficiency and effectiveness of recuperative thermal oxidizers, ensuring they continue to meet the evolving demands of both industry and regulation.
Principles of Operation
Understanding the principles of operation for recuperative thermal oxidizers is crucial, as this knowledge forms the backbone of how these systems effectively reduce harmful emissions. The operation of these oxidizers is pivoted on several key elements that, when combined, harness energy efficiently while effectively managing hazardous pollutants. By exploring these operational principles, we unpack the benefits they confer and the considerations necessary for effective implementation in varied industrial scenarios.
Basic Mechanisms
At its core, a recuperative thermal oxidizer functions through the oxidation of volatile organic compounds (VOCs) and other hazardous air pollutants. The basic mechanism involves a series of steps:
- Preheating Process: Incoming contaminated air is first preheated using heat exchangers. The energy recovered from the exhaust heat significantly enhances energy efficiency.
- Combustion Chamber: After preheating, this air enters the combustion chamber, where it's mixed with fuel to ensure complete oxidation. This stage features burners that ignite the mixture, generating high temperatures that facilitate the conversion of pollutants into harmless byproducts.
- Exhaust Management: Finally, the clean gases exit through the exhaust system. The design of the system allows for minimal energy loss, ensuring that most of the heat is recovered and reused.
This sequential operation not only maximizes the energy derived from combustion but also manages emissions effectively. Such mechanisms ensure that pollutants are treated before being released into the atmosphere, aligning with regulatory compliance demands.
Heat Recovery Process
The heat recovery process stands as a pivotal function of recuperative thermal oxidizers, significantly enhancing their energy efficiency. Heat exchangers play a vital role here; they capture the thermal energy from hot exhaust gases and transfer that heat to the incoming polluted air.
- Efficiency Gains: By recovering heat, these systems can achieve thermal efficiency rates between 85% to 95%. Such improvement considerably reduces operating costs and minimizes the environmental impact.
- Types of Heat Exchangers: Various technologies are available to serve this purpose, including:
- Plate Heat Exchangers: Known for their compact size and high efficiency.
- Shell and Tube Heat Exchangers: These are often favored for their reliability and maintainability.
The design choices made in the heat recovery setup can dramatically affect both the operational costs and the effectiveness of pollutant reduction strategies.
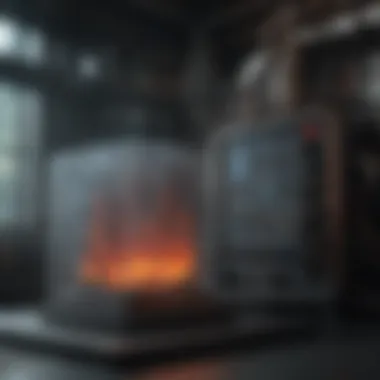
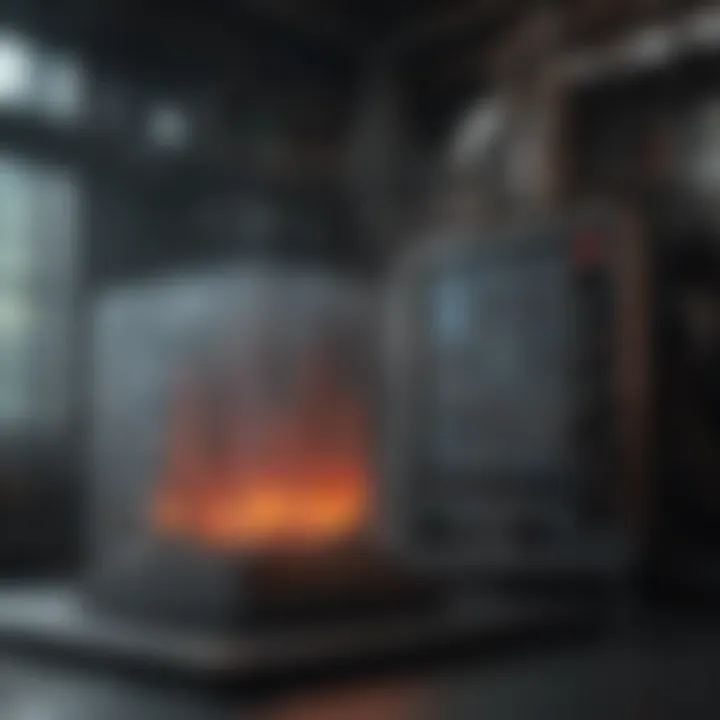
Combustion Chemistry
Delving into the combustion chemistry provides further insights into the oxidation process within recuperative thermal oxidizers. It's essential to grasp the chemical reactions that take place during combustion to appreciate the operational efficiency of these systems fully.
- Oxidation Reactions: The primary goal of combustion is facilitating oxidation. Hydrocarbons present in VOCs react with oxygen under high temperatures, resulting in water vapor and carbon dioxide.
- Temperature Control: Effective control of combustion temperature is paramount; too low can lead to incomplete oxidation, while too high might increase the formation of nitrogen oxides (NOx), a concern for air quality.
- Stoichiometry: Achieving an optimal air-fuel ratio ensures that all VOCs are converted. Deviations can lead to unburned hydrocarbons entering the atmosphere, undermining the oxidizer's effectiveness.
In summary, understanding these principles allows for a more nuanced view of recuperative thermal oxidizers and their operational processes. By unraveling the basic mechanisms, heat recovery techniques, and combustion chemistry, we start to appreciate not just their technology but also the significant advantages they confer in emissions control.
Key Components of Recuperative Thermal Oxidizers
In the world of recuperative thermal oxidizers, the effectiveness and efficiency hinge significantly on the key components that comprise these systems. Each element plays a pivotal role in ensuring optimal performance, facilitating not just the processing of hazardous pollutants but also maximizing energy savings. Understanding these components can empower industries to make informed decisions, particularly when adhering to environmental regulations and striving for sustainability. Let’s delve into the core elements: burner systems, heat exchangers, and control systems.
Burner Systems
Burner systems serve as the heart of recuperative thermal oxidizers. They are the initiators of the combustion process, transforming chemical energy into thermal energy, which is essential for oxidizing volatile organic compounds (VOCs) in waste gases. The design of these burners affects their operational efficiency and emissions output.
Different types of burners may be employed, each tailored to specific requirements. For instance, low-NOX burners are designed to minimize nitrogen oxides released into the atmosphere, thus complying with stringent environmental regulations. These systems not only impact emissions but also influence overall energy usage. A significant consideration is the fuel type, with options ranging from natural gas to propane, depending on availability and cost-effectiveness.
Heat Exchangers
Heat exchangers function as the bridge between the heat generated during combustion and the incoming waste gas stream. Their primary role is to recover thermal energy, allowing it to preheat the incoming air or gases. This process can significantly improve the inefficiency of thermal oxidizers by utilizing latent heat that would otherwise be wasted.
Two prevalent types of heat exchangers are the regenerative heat exchanger and the plate heat exchanger. Regenerative systems alternate between hot and cold flows, capturing heat with ceramic materials that can withstand high temperatures. Plate heat exchangers, on the other hand, utilize metal plates to transfer heat efficiently but may not handle high thermal volumes as effectively. By incorporating these systems, industries not only minimize energy costs but also contribute to lower greenhouse gas emissions.
"A well-designed heat exchanger can improve the efficiency of a recuperative thermal oxidizer system by up to 90%, showcasing the importance of this component."
Control Systems
Control systems integrate all components of the recuperative thermal oxidizer, serving as the nervous system of the operation. They enable real-time monitoring, data collection, and adjustments to maintain optimal conditions. These systems can include basic on-off controls or sophisticated software solutions that ensure automated adjustments based on operating conditions and emissions levels.
Using advanced control algorithms, these systems can analyze variables such as temperature, airflow, and emissions in real-time, ensuring that the system operates within its efficient range. This responsiveness is crucial, especially in industries where process variability can affect emissions significantly. Investing in robust control systems not only aids in regulatory compliance but also enhances the overall reliability of thermal oxidizers, leading to lower operational costs in the long run.
Understanding these components provides industries with a clearer perspective on how to optimize their operations. Each one supports the overarching goal: to effectively combat air pollution while maintaining efficiency and compliance. By focusing on burner systems, heat exchangers, and control systems, organizations can leverage the strengths of recuperative thermal oxidizers to achieve better outcomes.
Advantages of Recuperative Thermal Oxidizers
Recuperative thermal oxidizers are not just wind in the sails of pollution control; they’ve carved out an essential niche in industrial emissions management. Understanding their advantages offers a glimpse into why they’re becoming increasingly popular across various sectors. What lies beneath their operational framework equips industries with the tools needed to tackle regulations while simultaneously managing cost and environmental impact effectively.
Emission Control Efficiency
The cornerstone of recuperative thermal oxidizers is their ability to achieve high levels of emission control. These systems burn hazardous air pollutants at elevated temperatures, transforming them into less harmful substances. For instance, volatile organic compounds (VOCs) experience combustion at temperatures reaching 1,500°F, which facilitates a remarkable reduction in harmful emissions.
"In terms of performance, recuperative thermal oxidizers can achieve destruction efficiency rates typically exceeding 95%."
Not only do these rates satisfy regulatory standards set by environmental agencies, but they also provide companies with a bulletproof defense against potential fines or sanctions. Enhanced efficiency translates to less waste and cleaner air, making them a logical choice for many businesses committed to corporate social responsibility.
Energy Savings and Cost Effectiveness
When it comes to energy efficiency, recuperative thermal oxidizers deserve a nod of appreciation. The incorporation of heat recovery systems allows these units to reclaim thermal energy produced during the oxidation process. By recycling this energy, facilities can significantly reduce their natural gas consumption compared to traditional thermal oxidizers.
The economic benefits are palpable. Companies can observe a::
- Reduction in monthly utility bills.
- Decrease in fuel costs, which can account for a substantial fraction of operational expenses.
- Lower overall operating costs by extending equipment lifespan through reduced thermal stress.
Specific case studies in industries like plastics manufacturing indicate that energy savings of over 30% are achievable, making a strong financial case for these systems. Such outcomes epitomize the blend of environmental stewardship with fiscal prudence.
Sustainability Factors
In today’s world, sustainability isn’t just a buzzword; it’s an expectation. Recuperative thermal oxidizers rank highly in this regard. They not only satisfy emission control needs but also support broader sustainability goals. By minimizing the discharge of greenhouse gases and other harmful pollutants, these systems contribute positively to local and global environments. Their operational framework encourages effective waste management practices, promoting the betterment of air quality metrics.
Furthermore, companies leveraging recuperative thermal oxidizers often find themselves positioned favorably in the eyes of consumers and regulatory bodies alike.
- Firms can enhance their brand image by showcasing commitment to sustainability.
- Engagements in socially responsible practices boost consumer trust and loyalty.
The long-term impact of implementing these systems transcends immediate gains; it fosters a culture of innovation toward greener alternatives in industrial operations.
In summary, recuperative thermal oxidizers provide compelling advantages that surpass operational norms, merging efficiency with regulatory compliance while driving sustainability efforts. Businesses that implement these systems are not merely adhering to guidelines— they’re taking a proactive stance toward a cleaner and more cost-effective future.
Applications Across Industries
The utilization of recuperative thermal oxidizers is marked by their wide-ranging applications across various industries. This section investigates how these systems play a crucial role not only in enhancing operational efficiency but also in meeting regulatory demands regarding emissions control. Each sector takes advantage of the heat recovery capabilities, thus turning potential pollutants into usable energy. The added benefit? They contribute to sustainable practices, which are becoming increasingly essential in today’s industrial landscape.
Chemical Manufacturing
In the chemical manufacturing sector, the need for effective emissions control systems is paramount. Chemical processes often produce hazardous air pollutants (HAPs), which can pose serious environmental and health risks. Recuperative thermal oxidizers are particularly effective here. They can destroy organic compounds with high oxidation efficiency, thus decreasing the emission of harmful substances into the atmosphere.
- Cost-Effectiveness: By capturing the heat from the exhaust and using it to preheat the incoming air, these systems can significantly reduce energy costs, providing a return on investment that is appealing to manufacturers.
- Regulatory Compliance: The sector is often subject to stringent environmental regulations. Therefore, using recuperative thermal oxidizers helps ensure compliance with these regulations, mitigating potential fines and enhancing operational reputation.
Oil and Gas Sector
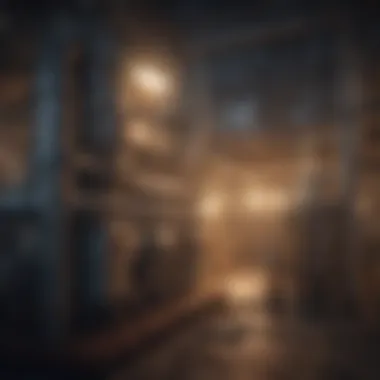
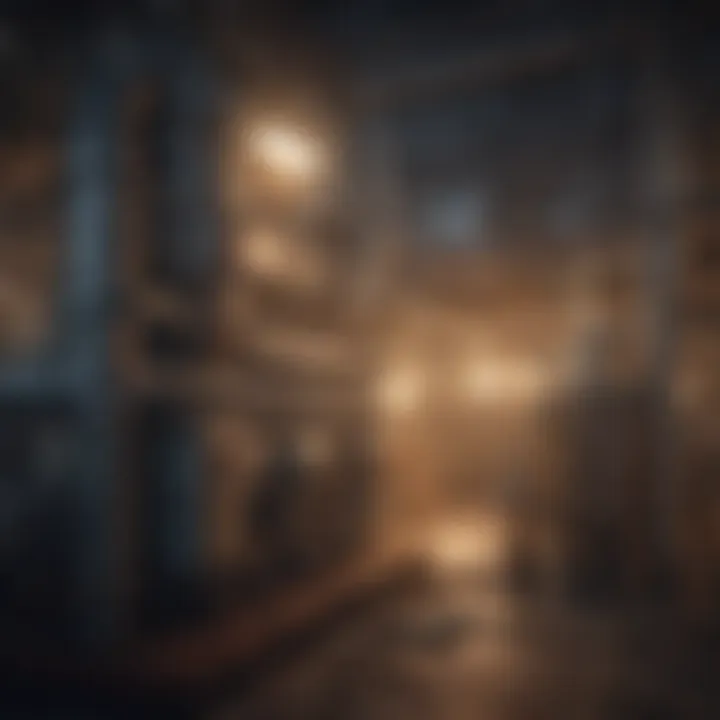
The oil and gas sector, notorious for significant emissions, has found in recuperative thermal oxidizers a valuable ally. With their capacity to handle fluctuating volumes and temperatures, they fit well in refineries and drilling operations. Here’s how they shine:
- Reduction of VOCs: Volatile organic compounds are commonplace in this industry. The oxidizers effectively split these compounds before they can escape into the atmosphere, fulfilling both operational efficiency and environmental protection goals.
- Adaptability: The varying nature of oil and gas production means that adaptable technologies are essential. Recuperative systems can be customized for specific operational needs, providing the flexibility required to maintain efficiency.
Automotive Industry
The automotive industry has increasingly adopted recuperative thermal oxidizers in their manufacturing processes, particularly in the paint and coating applications. The benefits are both practical and regulatory:
- Improved Paint Quality: By reducing the concentration of solvents in the air, these systems help achieve better paint finishes, decreasing defects that can arise from pollutant interference.
- Complying with Standards: With regulations becoming stricter around automobile emissions and manufacturing processes, the implementation of these oxidizers represents a commitment to sustainable practices. Companies not only enhance their public image but also avoid legal ramifications related to emissions violations.
Waste Management
Lastly, waste management companies benefit from recuperative thermal oxidizers primarily during the incineration process. At the heart of waste-to-energy strategies, these systems are instrumental in improving the effectiveness of waste disposal methods.
- Energy Recovery: As waste is burned, the heat generated can be harnessed to power other operations or even sold back to the grid, thus creating a dual revenue stream while minimizing environmental harm.
- Enhanced Safety: By ensuring the complete combustion of waste, these oxidizers help tackle the by-products that could be hazardous if not properly managed.
"The application of recuperative thermal oxidizers across multiple sectors demonstrates their versatility and essential role in modern emissions control strategies."
In summary, the applications of recuperative thermal oxidizers in diverse industries underline their importance not only in improving energy efficiency but also in enabling compliance with environmental standards, compelling companies to think long-term about sustainability and operational success.
Regulatory Compliance and Standards
In the realm of industrial processes, especially regarding emissions control, regulatory compliance plays a crucial role. Understanding the standards and regulations that govern the operation of recuperative thermal oxidizers can significantly impact not just the efficiency of these systems, but also their legal standing and operational viability. Adherence to regulations is not merely about ticking boxes; it’s about ensuring environmental responsibility and long-term sustainability in industrial practice. Here’s how this intricate web of compliance comes into play.
EPA Regulations
The Environmental Protection Agency (EPA) sets stringent guidelines targeted at mitigating air pollution. Comprehensive knowledge of EPA regulations is vital for operators of recuperative thermal oxidizers.
- National Emission Standards for Hazardous Air Pollutants (NESHAP): These regulations aim at reducing emissions of hazardous air pollutants from specific industries. Facilities using thermal oxidizers must ensure that their emissions meet or fall below the prescribed limits. Failure to comply not only attracts penalties but can lead to shutdowns until compliance is achieved.
- Title V Permits: Most states require facilities with significant emissions to secure Title V operating permits. These permits enforce compliance with both federal and state standards. Navigating the permitting process can be challenging, but it is necessary for legal operation. Engineers and compliance officers should stay abreast of any changes to these permits, as non-compliance can lead to significant financial implications.
- Continuous Emissions Monitoring Systems (CEMS): The EPA also mandates continuous monitoring systems for facilities emitting pollutants above certain thresholds. Implementing these systems can enhance operational transparency and give real-time data on emissions, helping facilities stay compliant.
It is essential that organizations conducting business within or impacted by these regulations invest in training their personnel on the latest EPA guidelines to remain compliant and responsible.
State and Local Compliance
While EPA sets the broad strokes, state and local regulations often paint the finer details. State environmental agencies may impose additional rules tailored to local conditions and specific pollutants prevalent in the region. This discrepancy can sometimes catch businesses off guard.
- State Implementation Plans (SIPs): States develop SIPs to outline how they will comply with the National Ambient Air Quality Standards (NAAQS). Businesses must familiarize themselves with their state’s unique rules and how they relate to thermal oxidizer operation.
- Local Ordinances: Municipal regulations can also have a significant impact. Some local governments may have stricter limits on pollutants, licensing requirements, or additional monitoring responsibilities. Staying attuned to local legislation can lead to more comprehensive compliance and can sometimes provide a competitive advantage.
"Understanding and complying with various regulatory frameworks is essential not only for avoiding penalties but also for fostering a culture of sustainability and responsibility within the industry."
Ultimately, regulatory compliance is not simply an obligation; it’s an integral part of operational strategy. Proactively engaging in these requirements can yield operational efficiencies while safeguarding the environment and the community. In a landscape where public scrutiny is at an all-time high, it’s imperative for industries utilizing recuperative thermal oxidizers to prioritize these standards not just as legal hurdles but as pivotal components in achieving sustainable practices.
Challenges and Limitations
Understanding the challenges and limitations surrounding recuperative thermal oxidizers is crucial for industry professionals and researchers alike. As effective as these systems are in managing air pollutants, they come with certain operational hurdles and other considerations that cannot be overlooked. Acknowledging these limitations ensures informed decisions are made regarding the implementation and maintenance of these technologies. This section provides insight into operational challenges, maintenance requirements, and market competition that influence the efficiency and practicality of these systems.
Operational Challenges
Operating a recuperative thermal oxidizer is not without its difficulties. One significant aspect is maintaining optimal operating conditions in the face of varying waste gas compositions and flow rates. For instance, when gases containing high moisture or particulate matter are introduced, the system's efficiency can be compromised. This variability can lead to increased wear and tear on components, as well as potential downtime for maintenance or recalibration. Moreover, the need for precise control of combustion conditions—like temperature and fuel-to-oxidizer ratio—adds another layer of complexity. If these parameters are not carefully monitored, it may result in incomplete combustion and increased emissions, running counter to the intended purpose of the system.
For operators, training personnel to handle these challenges effectively is paramount. An untrained workforce may lead to mistakes that could adversely affect operational efficiency. The learning curve can be steep, making it essential for organizations to invest in educational programs that deepen operational understanding and troubleshooting skills.
Maintenance Requirements
Regular maintenance is fundamental to ensuring the reliability of recuperative thermal oxidizers. Failures in this area can lead to unscheduled downtime, which is often costly, disrupting the overall production process. Components such as heat exchangers require periodic cleaning to prevent the buildup of deposits that can hinder performance and decrease efficiency.
Also, since these systems run at high temperatures, there is accelerated aging of certain parts. Burners, for example, may develop cracks due to thermal fatigue, necessitating timely inspections and replacements. Implementing a robust maintenance schedule, paired with real-time monitoring systems, can alleviate some of these burdens, allowing operators to anticipate issues before they become critical.
It's also essential for facility managers to understand the extent of maintenance involved. Some operators might underestimate the resources needed for upkeep, leading to surprise costs that impact budgeting. As such, an upfront assessment of these requirements can make the difference between seamless operations and costly interruptions.
Market Competition
The landscape surrounding recuperative thermal oxidizers is becoming increasingly competitive. With rising environmental regulations, many companies are seeking alternatives or upgrading existing systems. This competitiveness can spur rapid technological advancements, as companies strive to innovate and reduce operational costs.
However, the result can also create pressure on manufacturers of recuperative thermal oxidizers to keep up. New technologies, like advanced incineration alternatives and organic vapor control systems, may offer efficiency gains that challenge traditional oxidizers. Consequently, it is essential for manufacturers and operators to continuously assess their strategies and consider diversifying their product lines or services.
Moreover, clients may face a dilemma when choosing between established technologies like recuperative thermal oxidizers and emerging options. This competitive landscape may push risks, as some newer systems have yet to demonstrate long-term reliability or efficiency data.
In summary, while the recuperative thermal oxidizer market retains a strong position in air pollution control, it must navigate operational, maintenance, and competitive challenges to remain viable and effective.
Comparative Analysis with Alternative Technologies
Understanding the role of recuperative thermal oxidizers in emission control is crucial, but it is equally important to compare them against alternative technologies. Such a comparative analysis sheds light on their strengths and weaknesses, helping stakeholders make informed decisions about which option best suits their specific needs.
Examining different technologies allows for a clearer comprehension of cost-effectiveness, operational efficiency, and environmental impact. In industries where air quality management is paramount, such considerations can not only save money but also ensure compliance with stringent regulations. Without a comparative analysis, organizations might overlook viable alternatives that could perform better under certain circumstances.
Burner Technologies
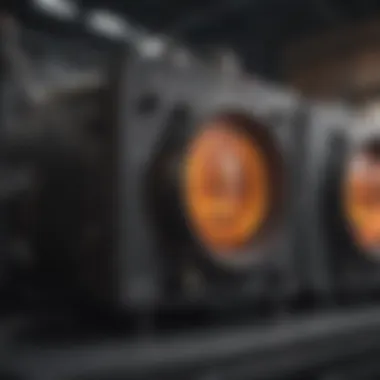
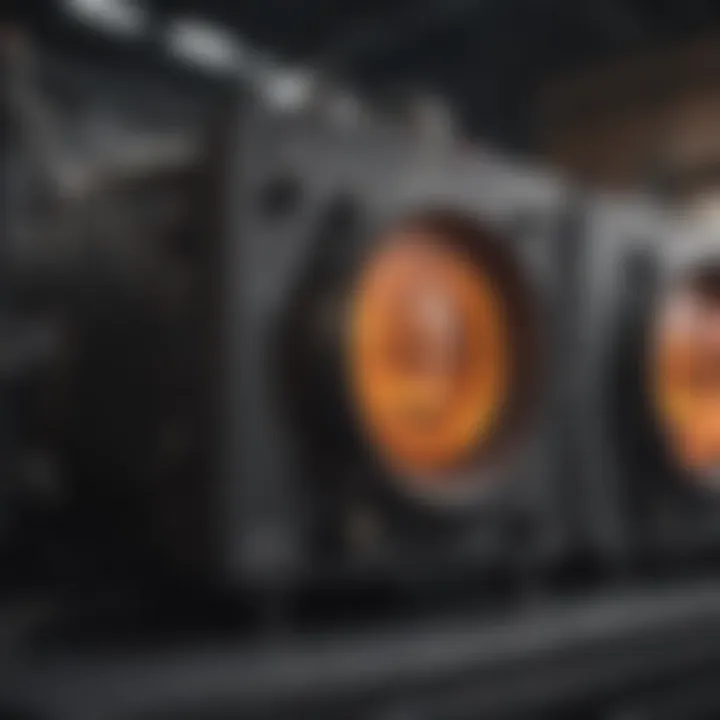
Burner technologies form the backbone of many combustion systems, including recuperative thermal oxidizers. These devices convert fuel into heat efficiently, but variations exist. For example, there are conventional burners, low-NOx burners, and oxy-fuel burners. Each of these has its own advantages. Conventional burners are straightforward but may emit more nitrogen oxides, while low-NOx burners help to control emissions but might have higher operational costs. The choice between these burners is often a balancing act of costs versus the emissions profile. Evaluating these technologies in conjunction with recuperative thermal oxidizers illustrates their interplay and importance. The efficiency of these systems plays a significant role in achieving both environmental goals and operational cost savings.
Organic Vapor Control Systems
Organic vapor control systems specialize in treating gaseous pollutants emitted during industrial processes. Technologies like activated carbon adsorption, thermal oxidizers, and bioreactors each provide unique methods of dealing with hazardous vapors. When compared to recuperative thermal oxidizers, organic vapor systems might excel in handling specific types of VOCs through absorption processes. For instance, activated carbon filters are highly effective in adsorbing certain vapors, but they come with their own set of maintenance and regeneration challenges.
Moreover, whereas recuperative thermal oxidizers are adept at breaking down many hazardous substances through combustion, they sometimes require pre-treatment to ensure efficiency. Therefore, analyzing these systems side by side clarifies the situations where one may be favored over the other—be it cost, material compatibility, or specific emissions reduction targets.
Incineration Techniques
Incineration is often a go-to solution for waste management and emission control. This technology burns waste to convert it into ash, flue gas, and heat, which can be harnessed as energy. While incineration is effective, particularly in reducing waste volume, it also brings forth critical considerations like the generation of greenhouse gases, and potential release of pollutants if not properly managed.
In contrast, recuperative thermal oxidizers can achieve a higher level of thermal efficiency and less greenhouse gas output when used optimally. They simply combust materials at high temperatures, breaking down contaminants into benign substances, while also recovering heat for reuse. This nuanced difference begs the question of sustainability and efficiency and encourages industries to explore the merits of both.
"When it comes to choosing between these technologies, understanding both their unique properties and the particular needs of your operation is key."
By tackling these alternatives head-on, one gains a comprehensive view of where recuperative thermal oxidizers stand in the grand scheme of emission control technologies. The decision hinges not only on technical capability but also on environmental stewardship and economic feasibility.
Case Studies of Successful Implementations
Case studies play a vital role in comprehending the real-world applications of recuperative thermal oxidizers. They provide concrete examples that can elucidate various aspects, such as operational efficiencies, cost-effectiveness, and environmental impact. By examining how different industries have successfully integrated these systems into their processes, we can extract valuable insights and lessons learned that inform best practices. Not only do these narratives highlight the versatility of recuperative thermal oxidizers, but they also demonstrate their effectiveness in meeting stringent emission regulations and achieving sustainability goals.
Industry-Specific Examples
The application of recuperative thermal oxidizers spans a variety of industries, showcasing their adaptive nature. For instance, the chemical manufacturing sector has seen remarkable success with these systems. Take a notable example from a large-scale chemical producer that implemented a recuperative thermal oxidizer. They replaced their older emission controls with a modern system, leading to a 50% reduction in volatile organic compound emissions. This improvement not only supported compliance with EPA regulations but also enhanced the overall efficiency of their production process.
In the oil and gas sector, an offshore drilling platform adopted recuperative thermal oxidation to manage waste gas emissions effectively. By leveraging this technology, they were able to recapture heat that would typically escape into the atmosphere. This innovation resulted in a significant reduction in fuel consumption, leading to cost savings along with lower greenhouse gas emissions. Such industry-specific examples underscore how tailored approaches to emission control can yield substantial benefits.
Performance Metrics
To truly understand the success of these implementations, analyzing performance metrics is essential. Metrics such as reduction rates of hazardous air pollutants, operational uptime, and capital costs compared to traditional systems provide a framework for evaluation.
For example, one chemical plant reported an impressive 80% reduction in emissions post-implementation, while maintaining a system availability of over 95%. It is also essential to look at economic factors; the aforementioned producer not only achieved compliance but also realized payback on their investment within three years.
"Successful case studies not only validate technology but also inspire confidence in its broader adoption across industries."
In another instance, an automotive manufacturer showcased a significant decrease in their carbon footprint after the integration of a recuperative thermal oxidizer. They documented not just lower emissions, but also a marked improvement in energy recovery efficiency. Such data is crucial, as it informs future projects and cultivates an understanding of how recuperative thermal oxidizers can be optimized further.
Research and scholarly articles can offer deeper dives into these case studies. Sources like en.wikipedia.org or britannica.com list scholarly work on the effectiveness of these technologies in various sectors. The exploration of successful implementations inspires innovation and points toward a promising future in emission control technologies.
Future Trends and Innovations
In the rapidly evolving sector of air pollution control, the advancements in recuperative thermal oxidizers are garnering much attention. This section aims to unpack the emerging trends and innovations that are shaping the landscape of thermal oxidizer technology. Understanding these changes is crucial for professionals, as they can greatly affect operational efficiency, compliance with stringent regulations, and overall environmental impact.
Advancements in Technology
Recent progress in recuperative thermal oxidizer technology shows significant promise. Engineers are now able to integrate advanced materials that withstand higher temperatures and corrosive environments. For instance, the use of silicon carbide in heat exchangers enhances durability and efficiency, helping to minimize energy use while maximizing heat recovery.
Moreover, automation and smart technology are becoming key players as well. Many facilities are adopting control systems that utilize artificial intelligence and machine learning algorithms. These systems analyze data in real-time to optimize operational parameters, leading to improved efficiency and reduced emissions.
- Energy Efficiency Gains: New systems are designed to operate at higher efficiencies. Modern recuperative thermal oxidizers can achieve up to 95% energy recovery.
- Emission Reduction: Ongoing research is focusing on enhancing combustion technology, aiming to lower NOx and CO emissions significantly.
These advancements are not just technical; they represent a paradigm shift in how industries manage harmful pollutants. Higher efficiency means less fuel consumption, making operations more sustainable.
Emerging Applications
As technology improves, the applications for recuperative thermal oxidizers are expanding into new sectors. One notable trend is their increasing use in the food processing industry. With tight regulations on volatile organic compounds, food manufacturers are turning to these systems to ensure compliance while keeping operational costs down.
Another promising application appears in the renewable energy sector. The capture and destruction of waste gases from biodigesters can benefit significantly from recuperative thermal oxidizers. By utilizing these systems, companies can turn potential emissions into energy, promoting a circular economy.
Specifically, industries that have stringent emission standards or produce high concentrations of harmful gases are likely to see the most benefit. Emerging applications could include:
- Pharmaceutical Manufacturing: Here, thermal oxidizers can help manage emissions from complex chemical processes.
- Electronics Production: As this industry grows, so does the need for substantial VOC management; recuperative thermal oxidizers provide a reliable solution.
- Energy Recovery from Biogas: Facilities utilizing biogas can enhance energy recovery while efficiently reducing pollutants.
"The trajectory of recuperative thermal oxidizers indicates a commitment to not only improving efficiency but also embracing newer sectors seeking sustainable solutions."
In summary, keeping an eye on the trends and innovations regarding recuperative thermal oxidizers is indispensable. It ensures a proactive approach to regulatory compliance and operational excellence. As we look forward, the integration of advanced technology and the diversification of applications will likely play pivotal roles in how industries tackle air pollution.
Finale
In wrapping up our exploration of recuperative thermal oxidizers, it’s crucial to emphasize their pivotal role in modern industrial practices, particularly in the realm of air pollution control. This technology is not merely an option; it has become a necessity for many sectors striving to comply with stringent regulatory frameworks while enhancing their operational efficiency. Through examining various facets such as operational principles, key components, and advantages, the article has unpacked the complex landscape surrounding these systems.
Summary of Key Insights
Recuperative thermal oxidizers stand out due to their ability to achieve high emission control efficiencies. They effectively break down hazardous pollutants, greatly reducing the impact on air quality. Highlights include:
- Energy Recovery: The heat recovery mechanism significantly lowers fuel consumption, marking a win-win for both environmental sustainability and cost savings.
- Versatile Applications: Their use spans across diverse industries including chemical manufacturing, oil and gas, and automotive sectors, showcasing their flexibility and broad applicability.
- Regulatory Compliance: Understanding and meeting EPA standards is simplified through employing these systems, making them a favored choice among industry leaders.
"The heart of a recuperative thermal oxidizer lies in its efficiency, both in performance and energy savings."
Future Implications
Looking ahead, the implications for recuperative thermal oxidizers are profound. As industries increasingly transition towards more sustainable practices, the technological advancements seen in this space are bound to accelerate. While today's models are efficient, future developments could focus on:
- Enhanced Automation: Smart technologies and real-time monitoring can further streamline operations, improving response times to fluctuating emissions.
- Innovative Materials: Ongoing research into catalytic materials may lead to even greater efficiency in pollutant breakdown.
- Broader Adoption: As awareness of climate change impacts grows, more industries are likely to embrace recuperative thermal oxidizers as a cornerstone of their emissions management strategies.