Exploring Bonded Magnets: Features and Innovations
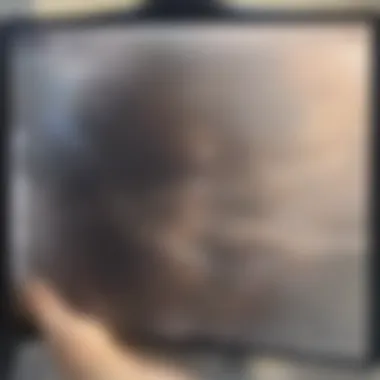
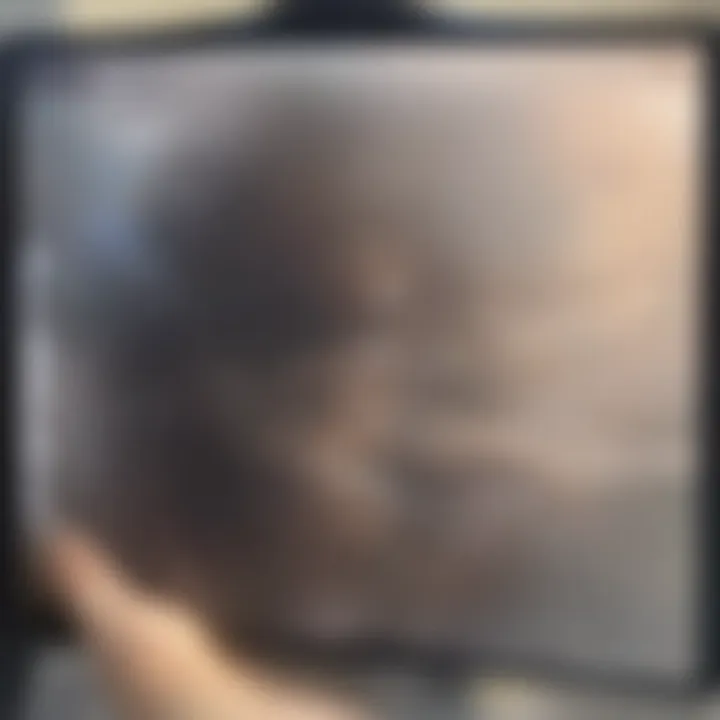
Intro
Bonded magnets are an essential component in many sectors, ranging from consumer electronics to industrial applications. Understanding their characteristics, production methods, and potential future developments is vital for leveraging their unique properties. In this piece, we aim to explore the intricate world of bonded magnets, emphasizing crucial scientific principles, practical applications, and the environmental factors associated with their lifecycle.
Key Concepts
Definition of Primary Terms
Bonded magnets are magnetic materials that are produced by combining magnetic powders with a polymer binder. This combination allows for the formation of magnets with specific shapes that can be both complex and precise. The magnetic properties are influenced by the type of magnetic powders used and the proportions in which they are blended. Types of bonded magnets include bonded neodymium, bonded ferrite, and bonded samarium-cobalt, each offering distinct characteristics suited for particular applications.
Related Concepts and Theories
The effectiveness of bonded magnets can be related to several underlying concepts, such as demagnetization, temperature stability, and magnetic anisotropy. Demagnetization refers to the process where a magnetic material loses its magnetism, significantly affecting performance in devices. Temperature stability is particularly important for applications exposed to varying thermal conditions. Understanding these concepts helps in optimizing the use of bonded magnets in real-world situations.
Applications
Bonded magnets have found a wide array of applications in modern technology. Here are some key areas where they play a pivotal role:
- Electronics: Used in microphones, speakers, and sensors, bonded magnets are essential for sound and data transmission.
- Automotive: They are utilized in motors and sensors, contributing to energy efficiency and improved performance.
- Medical Devices: In MRI machines and other medical technology, bonded magnets are crucial for accurate imaging.
- Renewable Energy: Wind turbines and solar applications benefit from the magnetic properties of bonded magnets to enhance energy conversion.
"Bonded magnets are not just components; they represent a fusion of material science and engineering ingenuity."
Future Directions
Gaps Identified in Current Research
Despite the advancements in bonded magnet technology, certain gaps remain in research, especially concerning sustainability practices. The environmental impact of magnetic powder production and the disposal of polymer binders are areas that require further investigation. Additionally, exploring novel materials could lead to better performance and lower environmental footprints.
Suggestions for Further Studies
Future studies should focus on:
- Developing eco-friendly binders
- Enhancing the efficiency of the fabrication process
- Investigating alternative materials that maintain or improve magnetic properties while minimizing environmental harm
Preamble to Bonded Magnets
Bonded magnets play a crucial role in various industries due to their unique properties and advantages. Understanding their characteristics is fundamental for professionals engaged in research, production, and application of magnetic materials. These magnets are made from a mixture of magnetic powders and binding agents, allowing for versatile applications ranging from electronics to healthcare.
In this section, we will explore the essence of bonded magnets, shedding light on their composition and the historical trajectory that shaped their development. Recognizing the importance of bonded magnets is indispensable because they bridge gaps in applications that require lightweight components with tailored magnetic properties.
What Are Bonded Magnets?
Bonded magnets are a type of permanent magnet that combine magnetic powder with a polymer binder. This dual-material approach allows for a diverse range of shapes and sizes, offering flexibility that traditional magnets cannot provide. The magnetic powders are typically made from rare-earth materials such as neodymium or ferrite, while the binding agents can be thermoplastic or thermosetting polymers.
The resulting magnet has specific magnetic properties, which depend on the type of materials used and the manufacturing process. Bonded magnets exhibit various advantageous traits, including lower weight, higher resistance to corrosion, and the ability to be molded into complex geometries. Such attributes make them suitable for applications that demand precision and efficiency.
Historical Development of Bonded Magnets
The evolution of bonded magnets can be traced back to the mid-20th century. Initially, traditional magnets dominated the market, largely limiting the applications due to their rigid compositions and production methods. However, as the demand for advanced materials increased, researchers began exploring new ways to create magnets with diverse properties.
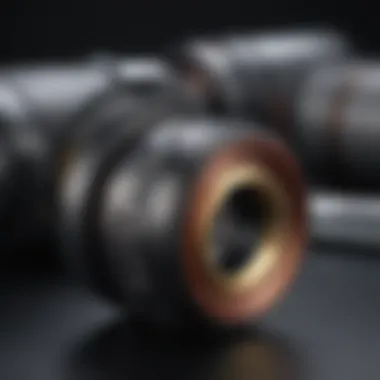
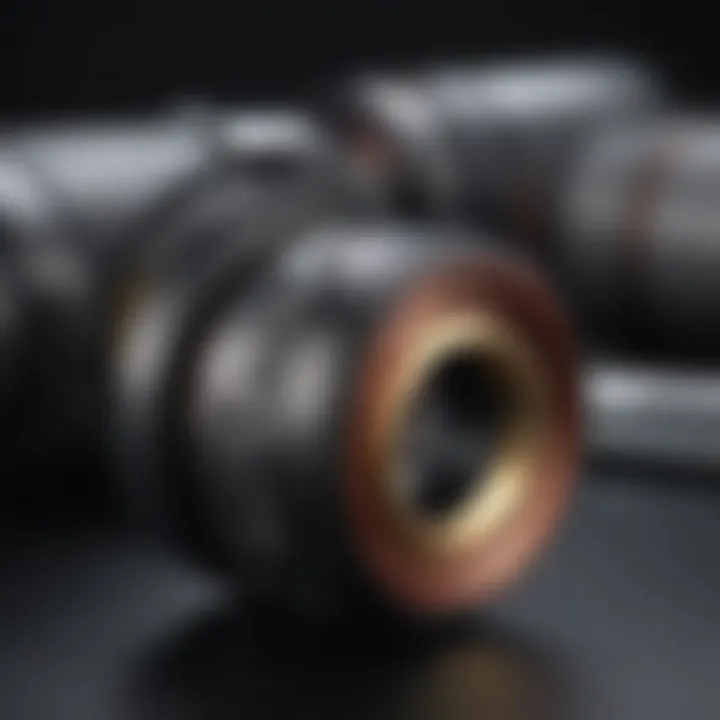
In the 1970s, significant advancements took place. The introduction of rare-earth magnetic materials revolutionized the field, leading to the development of bonded magnets. This era saw the combination of magnetic powder with different binders, allowing manufacturers to tailor their products to specific applications. Over the decades, innovations in production techniques, such as injection molding and compression bonding, have further refined the quality and capabilities of bonded magnets.
Today, bonded magnets serve critical roles in sectors like electronics, automotive, and medical technology. Their versatility and performance continue to expand, driven by ongoing research and technological developments. Understanding this historical context not only highlights the journey of bonded magnets but also underlines their significance in modern applications.
Composition and Manufacturing Processes
The composition and manufacturing processes of bonded magnets are crucial for understanding their effectiveness and versatility in various applications. Both elements not only govern the physical properties of the magnets, such as strength and durability, but also influence their production scalability and environmental impact. This section explores the essential materials, production techniques, and quality control measures that together play a significant role in the bonded magnet industry.
Materials Used in Bonded Magnets
Types of Magnetic Powders
The types of magnetic powders serve as the backbone for bonded magnets. These powders primarily originate from rare earth metals, ferrites, or other metal alloys. A key characteristic of these powders is their ability to generate strong magnetic fields while remaining lightweight. Their unique feature lies in how they can be tailored for specific applications, making them a favored choice in industries like electronics and automotive.
Advantages include the high-energy density, which allows for smaller and lighter components. However, disadvantages may involve cost and sourcing challenges due to reliance on specific minerals, particularly in the case of rare earth powders.
Binding Agents
Binding agents are vital in holding the magnetic powders together and shaping the final product. They often consist of resins or polymers that enhance the mechanical integrity of the magnets. A notable feature of binding agents is their capacity to provide flexibility in design, making it easier to mold the magnets into various shapes needed for specific applications. Furthermore, they significantly contribute to the magnet's durability against environmental factors.
The advantages of using binding agents include the ability to produce complex geometries and reducing manufacturing waste. However, they can affect the overall magnetic performance if not chosen correctly, introducing a trade-off between strength and flexibility that must be carefully managed.
Production Techniques
Injection Molding
Injection molding represents a prominent technique in the production of bonded magnets. It involves injecting a mix of magnetic powder and binding agents into a mold, where it is heated and cooled to form solid magnets. A key characteristic of this method is its efficiency, allowing for mass production with precise control over the magnets' shapes and sizes. This technique is extremely beneficial for industries requiring high volumes of consistent products.
Unique to injection molding is its capacity to reduce the manufacturing time significantly, which results in lower costs per unit. However, initial setup costs for molds can be high, making it less suitable for smaller production runs.
Compression Bonding
Compression bonding is another major manufacturing process for bonded magnets. This technique involves compactifying the magnetic powder with binding agents under high pressure in a mold, then applying heat to cure the binding agents. The key characteristic of compression bonding is its ability to produce magnets with higher density and strength compared to those produced by injection molding.
Its unique advantage is that it is less reliant on complex machinery and molds, which can make it more flexible for adjustments in production. However, achieving consistent quality can be challenging, requiring precise control over pressure and temperature during the process.
Quality Control in Manufacturing
Quality control is an essential phase in the manufacturing of bonded magnets. Various tests and inspections are implemented to ensure that the finished products meet industry standards. These measures include examining the magnetic properties, structural integrity, and potential defects in the materials used. Inconsistent quality can lead to magnets that fail in demanding applications, affecting overall performance.
Implementing rigorous quality control protocols enhances reliability and builds trust with customers, making it a fundamental aspect of the manufacturing process for bonded magnets.
Magnetic Properties and Performance
Understanding the magnetic properties and performance of bonded magnets is essential for evaluating their effectiveness in various applications. The magnetic attributes directly influence how these magnets can be utilized across different industries, impacting not only their efficiency but also their compatibility with other materials. This section will explore the key properties of bonded magnets, highlighting coercivity, remanence, and energy density. Each characteristic plays a significant role in the overall functionality of bonded magnets and their practical application.
Understanding Magnetic Properties
Coercivity
Coercivity refers to the ability of a magnet to withstand an external magnetic field without losing its magnetization. In the context of bonded magnets, high coercivity is often advantageous as it allows the magnet to maintain its strength under varying environmental conditions. A magnet with strong coercivity exhibits stability, making it particularly beneficial for applications requiring reliability. However, high coercivity can also mean that manufacturing processes must be closely controlled to ensure desired magnetic properties are achieved.
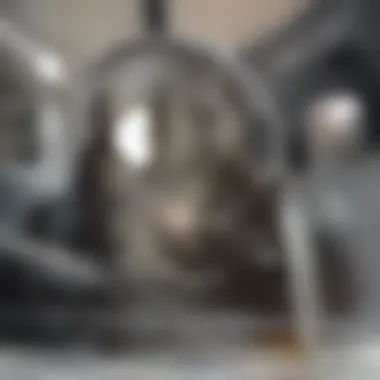
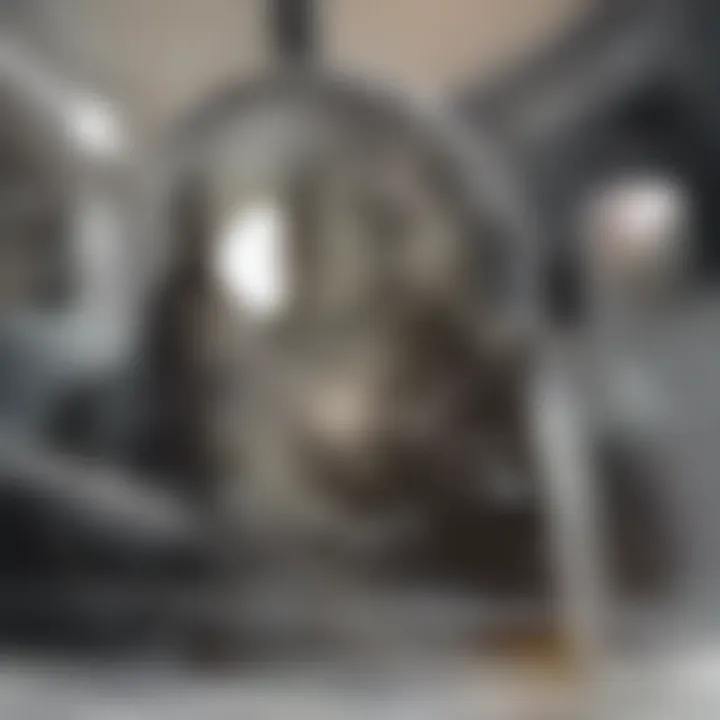
Remanence
Remanence is the measure of the magnetization left in a magnet once the external magnetic field is removed. This characteristic is crucial for bonded magnets because higher remanence levels indicate a more potent permanent magnet. This trait can be advantageous in applications where a strong, sustained magnetic force is necessary. However, the challenge with remanence lies in balancing it with other properties such as coercivity to maintain overall performance without compromising quality or applicability.
Energy Density
Energy density is a critical metric that combines both coercivity and remanence, reflecting the amount of magnetic energy stored in a given volume of the magnet. The significance of energy density in bonded magnets cannot be overstated, as a higher energy density allows for smaller, lighter magnets that still achieve required performance levels. This property makes bonded magnets particularly popular in compact electronic devices where space is limited, although achieving high energy density often involves complex manufacturing techniques.
Performance Comparison with Other Magnet Types
In order to appreciate the advantages of bonded magnets, it is important to compare their performance with other types of magnets. This comparison underscores how bonded magnets fit into the larger magnet landscape, facilitating an understanding of where they excel and where they may be less suitable.
Hard Ferrite Magnets
Hard ferrite magnets are known for their low cost and availability, which makes them a popular choice for various applications. Their significant characteristic is their moderate coercivity and remanence. Hard ferrite magnets can operate in high-temperature environments, which is advantageous in industrial applications. Despite their advantages, they typically have lower energy density compared to bonded magnets, which limits their use in space-constrained designs.
Neodymium Magnets
Neodymium magnets are renowned for their exceptional strength and high energy density, making them some of the most powerful permanent magnets available today. They exhibit high coercivity and remanence, leading to impressive performance in small sizes. However, they are more susceptible to thermal demagnetization, which could limit their application in high-temperature situations. Additionally, they require careful handling and a higher manufacturing cost compared to bonded magnets.
The choice between bonded magnets, hard ferrite magnets, and neodymium magnets ultimately depends on the specific requirements of the application, including size, strength, and environmental conditions.
Applications of Bonded Magnets
Bonded magnets have established themselves as a significant component in various industries due to their versatile applications. These magnets are not only efficient but also adaptable for different uses. The focus on bonded magnets' applications is crucial as it reveals the real-world relevance of this technology. By examining specific use cases, one can understand the benefits and considerations that these magnets offer across multiple sectors.
Electronics and Electrical Devices
Speakers
In the realm of audio technology, speakers utilize bonded magnets due to their lightweight and compact nature. The unique aspect of these magnets is that they provide a high magnetic strength without increasing the overall weight. This characteristic makes bonded magnets a beneficial choice for portable and high-performance audio equipment. The advantage lies in their ability to reproduce sound with clarity and efficiency, reducing distortion levels in various types of speakers. However, there can be concerns regarding durability under extreme conditions, as bonded magnets may not perform well in highly variable environments.
Microphones
Microphones employ bonded magnets primarily in their design to enhance sensitivity and sound quality. The key characteristic here is the response time; bonded magnets can produce superior acoustic responses, which are essential for high-fidelity recording. This feature allows for clearer voice capture and effective noise reduction. One disadvantage is the potential for reduced performance in certain high-frequency scenarios. Nonetheless, the benefits often outweigh the drawbacks, making bonded magnets a common choice in both professional and consumer microphones.
Automotive Industry
Electric Motors
Bonded magnets play a pivotal role in the electric motors of vehicles, particularly in electric and hybrid models. Their primary contributions include high efficiency and reduced size compared to traditional motor designs. The key characteristic of these motors is their ability to deliver considerable torque while maintaining low energy consumption. Consequently, they become a popular option in the automotive industry, aligning well with the push for more sustainable transportation solutions. A noted disadvantage might be the cost of production, but this is often mitigated by the overall savings in energy and operational costs over time.
Sensor Applications
In the automotive industry, sensors are essential for monitoring various systems. Bonded magnets are integrated into sensor designs for their precise magnetism and compact size. The unique feature here is their robustness, allowing for reliable performance in harsh environments and under high temperatures. This reliability is crucial for systems including braking and stability control. While the overall performance is highly rated, producing these sensors can sometimes be complex and costly, requiring attention to detail during manufacturing.
Medical Technology
Magnetic Resonance Imaging (MRI)
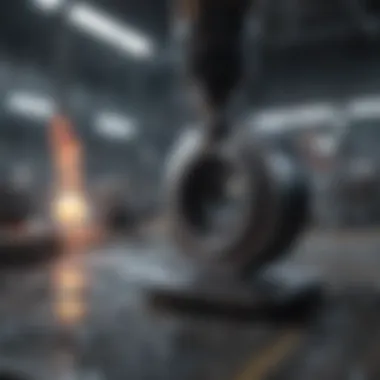
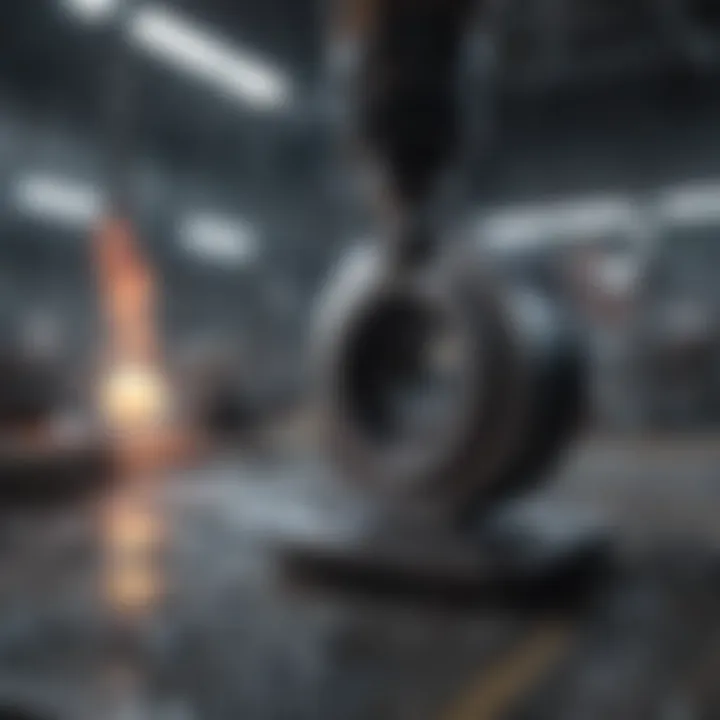
In the medical field, MRI machines depend on bonded magnets to create the necessary magnetic fields for imaging. The high magnetic strength of bonded magnets is essential for achieving clear images of soft tissues. The critical characteristic is their capability to maintain stable magnetic fields across a wide range of temperatures. This stability is advantageous as it enhances the quality of the diagnostic images produced. However, the complexity and cost related to scaling these magnets can be obstacles for some institutions.
Portable Devices
Portable medical devices have increasingly started to incorporate bonded magnets due to their lightweight and efficient performance. The key characteristic here is their portability without sacrificing the effectiveness of the devices. For example, portable ultrasound machines and handheld diagnostic tools use bonded magnets to optimize function and size. Advantages include improved patient mobility and ease of use in various environments. Yet, a challenge can be their susceptibility to wear over time, which may need consideration during the design phase.
Environmental and Sustainability Aspects
In today’s industrial landscape, the focus on sustainability is more critical than ever. This includes the production of bonded magnets, which are utilized in various applications. Understanding the environmental and sustainability aspects of bonded magnets has significant implications for their production and end-of-life management. Embracing sustainable manufacturing practices can lead not only to reduced environmental impact but also to increased operational efficiencies.
Challenges in Production
Producing bonded magnets comes with specific environmental challenges. The manufacturing process often involves materials that may have ecological consequences. For instance, the extraction of raw materials can result in habitat destruction, water pollution, and socio-economic issues in mining communities. Furthermore, the use of solvents in some production processes may release volatile organic compounds (VOCs) into the atmosphere.
- Energy Consumption: Manufacturing bonded magnets is energy-intensive. This leads to higher greenhouse gas emissions unless renewable energy sources are utilized. Reducing energy consumption during production can significantly decrease the carbon footprint associated with these magnets.
- Waste Generation: The production phases, particularly when creating magnetic powders, can generate substantial waste. It is essential to develop strategies to minimize waste and ensure that it is managed responsibly.
- Regulatory Compliance: Manufacturers must navigate complex and evolving regulations concerning environmental protection. Non-compliance can lead to penalties and harm public perception.
Addressing these challenges requires innovation and investment in cleaner technologies and practices, prioritizing sustainability in every step of the manufacturing process.
Recycling and Disposal
The life cycle of bonded magnets does not end with their use. Recycling and disposal strategies are essential for minimizing environmental impact.
- Recycling Opportunities: Currently, recycled magnets are still a developing area. The magnetic powders used in bonded magnets can be complex, making recycling a challenge. Yet, ongoing research aims to improve recycling technologies. When successful, this can lead to a valuable source of raw materials for new magnets.
- Safe Disposal Practices: Improper disposal can result in materials leaching into the environment. Therefore, manufacturers should implement safe disposal practices to mitigate risks. It is crucial for industries and consumers to be aware of proper end-of-life management for bonded magnets.
- Circular Economy: The concept of a circular economy emphasizes the continuous use of resources. Through effective recycling techniques and re-manufacturing programs, bonded magnets can contribute positively to a sustainable future.
“Sustainable practices not only benefit the environment but also enhance brand reputation and consumer trust.”
Innovations and Future Trends
Innovations in bonded magnets represent a crucial focus in the magnet industry, emphasizing advancements in technology and production. It is essential to understand how these innovations can enhance performance, efficiency, and sustainability. In recent years, the push towards smarter and lighter components in various applications has led to a wave of research and development in bonded magnet technology. This has implications not just for the efficiency of products but also for how industries can adapt to the growing demands of energy and performance.
Emerging Technologies in Magnet Industry
The emergence of new technologies in the magnet industry is fostering profound changes. One notable development is the integration of additive manufacturing techniques, such as 3D printing. This allows for the production of magnets with complex geometries that traditional methods cannot achieve. These innovative processes enable tailored magnetic properties and reduced material waste. Moreover, advancements in nanotechnology are paving the way for the enhancement of magnetic material properties, leading to higher efficiency in applications ranging from consumer electronics to automotive systems.
Another notable development involves the use of new magnetic materials, such as rare-earth-free compositions. This innovation aims to reduce dependency on scarce resources while maintaining performance. The research into alternative materials often involves collaboration among universities, private companies, and government agencies, indicating a collective effort toward sustainable solutions in manufacturing.
Potential Market Developments
The bonded magnet market is poised for significant growth in the coming years, largely due to increased demand in key sectors. Highlights of potential market developments include:
- Electronics: The proliferation of smart devices has increased the need for efficient bonded magnets. Manufacturers are likely to focus on miniaturization and increased power efficiency.
- Automotive: With the rise in electric vehicles, bonded magnets are becoming indispensable for drivers and other components. Future trends include the development of stronger and lighter magnets that improve efficiency.
- Medical Applications: The medical field demands precise and reliable components. Innovations in bonded magnets can lead to enhancements in devices like MRI machines, improving patient outcomes.
Finale
The topic of bonded magnets is fundamental for understanding modern magnet applications and technology. This article has explored various dimensions of bonded magnets, enhancing comprehension of their characteristics, manufacturing processes, properties, and implications in multiple industries.
Summary of Key Points
- Definition and Composition: Bonded magnets are made from powdered magnetic materials combined with a binding agent, shaping their unique properties.
- Manufacturing Techniques: Important methods such as injection molding and compression bonding play crucial roles in producing high-quality bonded magnets.
- Applications: Their versatile use in electronics, automotive, and medical fields illustrates their significance across sectors.
- Environmental Aspects: The challenges related to sustainability and recycling are key considerations for future development.
- Innovations: Emerging technologies are set to drive advancements, enhancing the effectiveness and applicability of bonded magnets.
"Understanding the specifics of bonded magnets opens doors to innovations in design and application, impacting various industries significantly."
The Future of Bonded Magnets
The future of bonded magnets looks promising. Continued research in material science may lead to improved magnetic properties and efficiencies. Emerging applications, particularly in green technology and renewable energy sectors, could redefine their usage. Sustainability efforts will also shape future processes, focusing on recycling and waste reduction.
As industries evolve, the integration of bonded magnets will likely expand. New manufacturing processes, such as additive manufacturing, may further enhance customization. The ongoing collaboration between academia and industry is essential for fostering innovation and adapting bonded magnet technologies to meet new challenges.