Understanding Gas Scrubber Vessels: Principles & Applications
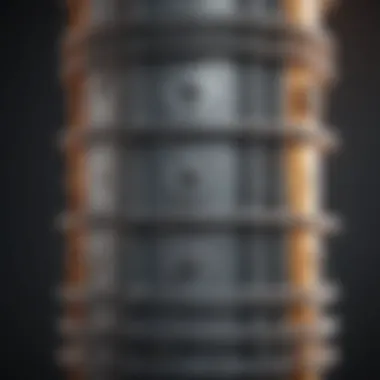
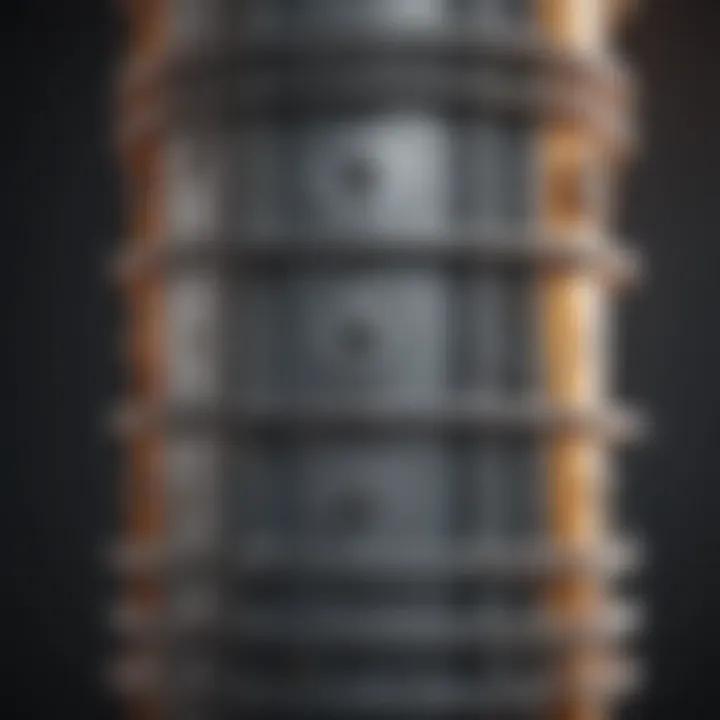
Intro
Gas scrubber vessels, a critical component in managing air quality, play an important role in reducing pollutants emitted into the atmosphere. These systems are designed to capture and remove harmful gases, ensuring compliance with environmental laws and protecting public health. As industries grow and regulations tighten, understanding the design, operation, and applications of gas scrubber vessels becomes increasingly essential. This article will delve into the fundamental principles of gas scrubbing, exploring how these vessels operate, their types, and the technological advancements that improve their effectiveness.
Key Concepts
Definition of Primary Terms
Gas scrubber: A device designed to remove contaminants from gaseous emissions, typically using liquid solutions to dissolve or absorb the harmful substances.
Pollutants: Substances that contaminate the air, leading to environmental harm and health risks.
Absorption: A process by which one material captures another substance, transferring it from the gas phase to a liquid phase.
Scrubbing solution: The liquid used in gas scrubber systems to react with or capture unwanted pollutants.
Related Concepts and Theories
Understanding gas scrubber vessels requires knowledge of several interrelated concepts.
- Environmental Regulations: Laws often dictate the emissions allowed from various industries, thus influencing the design and application of scrubber systems.
- Mass Transfer Principles: The effectiveness of a scrubber is based on mass transfer, which refers to the movement of substances between phases and how pollutants are absorbed or removed.
- Fluid Dynamics: The behavior of liquids and gases in the scrubbing process is governed by fluid dynamics, affecting the overall performance of gas scrubber systems.
"Gas scrubbers are not just mechanical devices; they reflect the ever-evolving standards of environmental responsibility and innovation."
Applications of Gas Scrubber Vessels
Gas scrubber vessels find application in various industries:
- Power Generation: They help reduce sulfur dioxide and nitrogen oxides from coal-fired power plants.
- Chemical Manufacturing: Scrubbers capture volatile organic compounds during chemical processing.
- Oil and Gas: In refineries, scrubbers remove harmful gases from extraction and processing operations.
- Waste Management: Gas scrubbers lessen emissions from waste incineration, protecting air quality.
Future Directions
Gaps Identified in Current Research
Further investigation is necessary to address several gaps in the understanding of gas scrubber vessels.
- Limitations in current designs often lead to inefficiencies.
- There is a lack of comprehensive studies on the long-term effects of different scrubbing solutions.
- Existing research does not fully explore the synergy between scrubbers and advanced monitoring systems.
Suggestions for Further Studies
Future studies should aim to
- Innovate in scrubber design to enhance efficiency.
- Analyze the environmental and economic impacts of next-generation scrubbing technologies.
- Investigate the integration of artificial intelligence in real-time monitoring and control of scrubber systems.
Foreword to Gas Scrubber Vessels
Gas scrubber vessels represent a crucial technology in mitigating air pollution. Their significance lies in their ability to remove various pollutants from gaseous emissions before they are released into the atmosphere. The article delves into the essentials of gas scrubber vessels, providing insights into their design, principles of operation, and various applications across multiple industries. Understanding these vessels is essential for students, researchers, educators, and professionals aiming to address environmental challenges effectively.
Definition and Purpose
Gas scrubber vessels are systems designed to clean gases by way of removing harmful substances. These vessels operate through scrubbing processes that typically involve liquid solutions. The main purpose of a gas scrubber is to protect both public health and the environment by reducing the concentration of pollutants, such as sulfur oxides, nitrogen oxides, volatile organic compounds, and particulate matter. In industrial settings, the implementation of scrubbers not only aligns with regulatory compliance but also enhances operational efficiency, contributing to sustainability efforts.
Historical Development
The concept of gas scrubbing traces back to the early 20th century when industries began recognizing the need to control emissions. Initially, scrubbers were rudimentary and primarily focused on controlling a limited range of pollutants. Over the decades, technological advancements led to diverse scrubbing methods, improving the efficacy and scope of these systems. The introduction of wet scrubbers in the mid-20th century marked a pivotal moment, allowing for more efficient removal of harmful gases from exhaust streams.
With increasing awareness of environmental issues, regulations began mandating higher standards for air quality. This catalyzed innovation in gas scrubber technologies, driving the development of dry and semi-dry scrubbers in various applications. Today, scrubber systems are integral in sectors such as power generation, waste management, and manufacturing, showcasing the evolution of these vessels from simple solutions to sophisticated technological apparatuses.
"Gas scrubbers have transformed from rudimentary tools into advanced systems pivotal for air quality control, adapting to the ever-changing regulatory landscape and environmental requirements."
The history of gas scrubbers illustrates the ongoing struggle between industrial growth and environmental protection, highlighting the importance of continuous innovation in scrubbing technologies.
Working Principles of Gas Scrubber Vessels
Understanding the working principles of gas scrubber vessels is essential for comprehending how they effectively reduce air pollutants. These mechanisms are not only fundamental for industrial compliance but also vital for maintaining environmental sustainability. An effective gas scrubber vessel minimizes the emission of harmful substances into the atmosphere. Hence, recognizing the working principles aids engineers and designers in optimizing systems to meet specific requirements.
Moreover, it allows industries to choose suitable scrubbing technologies that align with their operational and environmental needs. Each scrubbing vessel operates on certain basic mechanisms, which influence their efficiency and performance.
Basic Mechanisms
Gas scrubbers utilize a combination of physical and chemical principles to remove contaminants. These are the primary mechanisms at play:
- Absorption: This process involves the transfer of a pollutant from the gas phase into a liquid. The liquid phase could be water or another chemical solution. The gas interacts with the liquid, allowing soluble gases to dissolve.
- Adsorption: This mechanism relies on the adhesion of gas molecules to solid surfaces. Filters, charcoal, or zeolites are commonly used materials that provide a large surface area for pollutant capture.
- Chemical Reaction: In some scenarios, chemical scrubbers react the targeted gas with a reagent. This results in a new compound that is less harmful. For example, sulfur dioxide can react with an alkaline solution, forming a soluble sulfate.
These mechanisms are critical for determining the appropriate design and operational parameters of the scrubber vessels. Adjusting flow rates and the type of scrubbing solution can dramatically impact efficiency.
Types of Scrubbing Processes
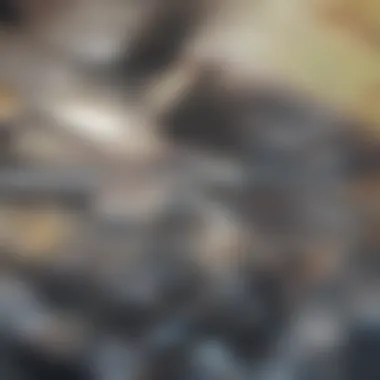

There are various processes that scrubbers can employ, each suited for different applications and contaminants:
- Wet Scrubbing: This method employs a liquid stream to capture pollutants. It is effective for gases that readily dissolve in water. Common applications include removing sulfur dioxide and particulate matter in flue gas.
- Dry Scrubbing: In this approach, dry reactants interact with the pollutants. Dry scrubbers are often utilized for gases like hydrochloric acid. They tend to have a lower operational cost than wet systems due to reduced water usage.
- Semi-Dry Scrubbing: Combining elements of both wet and dry scrubbing, this process uses a dry reagent and produces a mist of water to facilitate reactions. This method is suitable for various industries, especially those with moderate gas volumes.
Understanding these scrubbing processes enables industries to make informed decisions regarding technology selection. The effectiveness can depend significantly on the nature of the pollutants and the specific operational context.
"Gas scrubbers are not merely compliance tools; they are critical components of an integrated approach to air quality management."
Ultimately, gas scrubber vessels serve as a crucial line of defense against air pollution. A solid grasp of their working principles allows stakeholders to maximize their performance while minimizing environmental impact.
Types of Gas Scrubber Vessels
Understanding the types of gas scrubber vessels is crucial for grasping their role in managing air pollution. Each type has unique characteristics that influence their effectiveness in different applications. The choice of scrubber can significantly impact operational efficiency, maintenance, and compliance with environmental regulations. This section will detail three primary types of gas scrubber vessels: wet scrubbers, dry scrubbers, and semi-dry scrubbers.
Wet Scrubbers
Wet scrubbers use a liquid solution as a scrubbing medium to absorb or react with gaseous pollutants. They are enormously efficient in handling various contaminants, including acidic gases, particulate matter, and volatile organic compounds (VOCs). The liquid typically used is water, but depending on the pollution type, other chemical solutions may also be employed.
One of the biggest advantages of wet scrubbers is their ability to remove large volumes of pollutants, making them suitable for high-emission industrial processes. However, they also require significant water usage and can generate waste that must be treated before disposal.
Wet scrubbers can be classified into different configurations, such as packed bed scrubbers and venturi scrubbers, each tailored for specific applications. Moreover, performance metrics like absorption efficiency can vary depending on factors such as the scrubbing liquid's pH, temperature, and flow rate.
Dry Scrubbers
Dry scrubbers, in contrast, do not use liquid solutions; instead, they rely on solid sorbents to capture gaseous contaminants. Common materials used as sorbents include activated carbon, lime, and sodium bicarbonate. The primary benefit of dry scrubbers is their lower water consumption and consequently less waste byproduct creation compared to their wet counterparts.
These scrubbers are often used in situations where the scrubbing process needs to match the capabilities of a wet scrubber without the associated disposal problems of sludge. They can effectively mitigate the release of sulfur dioxide and other acidic gases. A challenge with dry scrubbers is that their effectiveness can depend heavily on the proper selection of sorbent material and maintaining optimal flow rates through the system.
Semi-Dry Scrubbers
Semi-dry scrubbers present a hybrid approach between wet and dry scrubbers. They use a slurry of solid sorbents and liquid that helps in capturing pollutants while minimizing wastewater generation. Semi-dry scrubbing technology efficiently removes not only acid gases but also particulate matter.
The operational flexibility of semi-dry scrubbers makes them suitable for various applications, including waste-to-energy plants and other industrial settings where both particulate matter and gas contaminants must be addressed. The balance of liquid and solid components is critical in optimizing performance. In general, these scrubbers can achieve high removal efficiencies without the extensive moisture issues seen in wet scrubbers.
When selecting a scrubber type, it is essential to consider not only the removal efficiency but also implications like operational costs, waste management, and specific environmental compliance needs. Each type of scrubber can be optimized for particular scenarios, highlighting their importance in industrial air pollution control.
Design Considerations for Gas Scrubber Vessels
The design of gas scrubber vessels is crucial for their efficiency and effectiveness in air pollution control. Each element in design plays a vital role in determining the overall performance of the scrubbing system. Specifically, material selection, sizing and capacity, and flow dynamics are significant aspects that must be addressed. Careful consideration of these factors can lead to improved pollutant removal, cost-efficiency, and long-term operational reliability.
Material Selection
Material selection for gas scrubber vessels directly affects their durability and resistance to chemical reactions. The materials used must withstand the corrosive properties of gases and the interactions with scrubbing solutions. Common materials include stainless steel and high-density polyethylene. Stainless steel is often preferred for its strength and ability to resist corrosion. However, the costs can be higher compared to other materials.
When selecting materials, environmental conditions must also be taken into account. For instance, the temperature of the gases being treated can influence the choice of material. Selecting the right material helps not only in enhancing the lifespan of the scrubber vessel but also reduces the frequency of replacements and repairs, leading to cost savings in the long run.
Sizing and Capacity
Sizing and capacity are fundamental to the design of any gas scrubber vessel. An under-sized scrubber may fail to effectively reduce pollutants, while an over-sized one can lead to unnecessary expenses. To determine the correct size, designers must consider the flow rate of the gases and the desired level of pollutant removal.
The capacity of the system also influenced by various factors such as peak pollution loads, operation time, and the characteristics of the pollutants. Adequate sizing and capacity planning ensure that the scrubber operates efficiently under varying operational conditions.
Flow Dynamics
Flow dynamics within the vessel are crucial for optimizing contact between the gas and scrubbing liquid. Understanding how gases flow through the scrubber affects its design and operation. Key factors include the velocity of the gas, turbulence, and how the scrubbing liquid interacts with the gas stream.
Effective flow dynamics ensure that gas molecules spend sufficient time in contact with the scrubbing liquid. This contact time is essential for the mass transfer processes to occur, significantly influencing the efficiency of pollutant capture. Designing for optimal flow patterns can lead to more uniform contact, maximizing the overall efficiency of the scrubber vessel.
"Design considerations for gas scrubber vessels play a pivotal role in ensuring compliance with environmental regulations while optimizing performance and cost-effectiveness."
In summary, the design of gas scrubber vessels demands a meticulous approach in material selection, sizing, and understanding flow dynamics. Each of these components contributes to achieving high performance and operational reliability in reducing air pollutants. Integrating these considerations into the design framework allows for the successful implementation of gas scrubber technologies across various applications.
Applications of Gas Scrubber Vessels
Gas scrubber vessels play a critical role in controlling air pollution in various sectors. Their applications are diverse and essential for ensuring compliance with environmental regulations, improving air quality, and protecting human health. In this section, we explore the specific applications of these vessels, providing insights into their benefits and the considerations involved in their implementation.
Industrial Processes
In industrial settings, gas scrubbers are indispensable for managing emissions produced from manufacturing operations. Industries such as chemical processing, pharmaceuticals, and food production generate volatile organic compounds and particulate matter that can harm the environment. Wet scrubbers are commonly used here to remove these pollutants through absorption and condensation.
Some important points regarding industrial applications include:
- Efficiency: Scrubbers can achieve high removal efficiencies for specific contaminants, ensuring that plants meet strict emission limits.
- Customizability: Systems can be tailored to fit the unique needs of different industrial processes, optimizing performance.
- Safety: With effective gas scrubbing, the risk of harmful exposure to workers is significantly reduced.
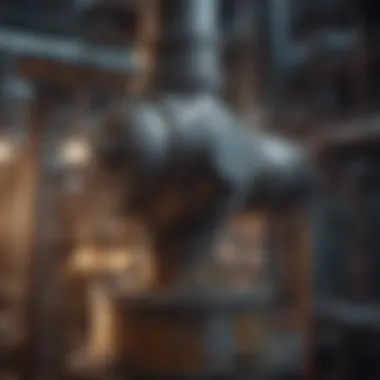
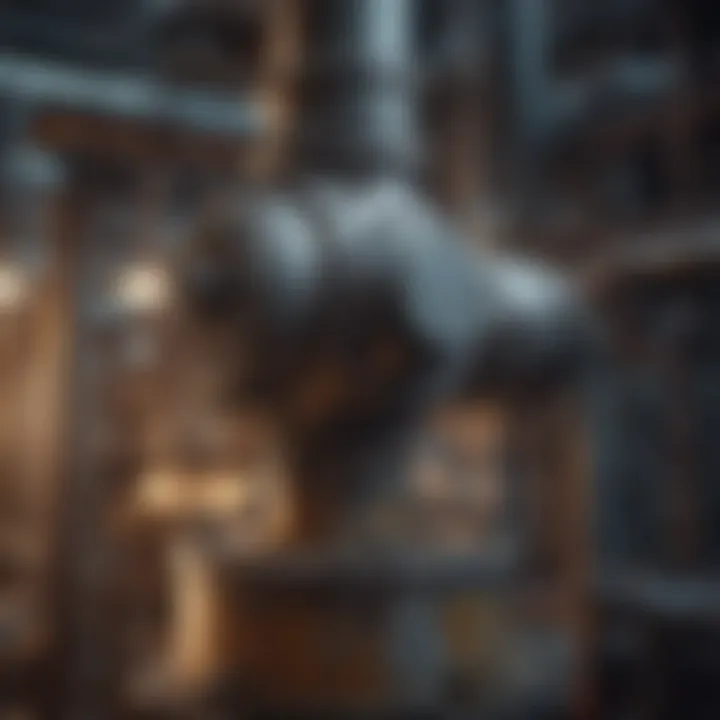
Waste Treatment
Gas scrubber vessels are also vital in waste treatment facilities. These facilities tackle the odors and harmful emissions generated from decomposing waste. Dry scrubbers are primarily utilized to capture gases that result from organic waste treatments, such as methane and hydrogen sulfide. This not only enhances the working conditions for personnel but also minimizes atmospheric pollution.
Key considerations include:
- Regulatory Compliance: Many regions impose stringent requirements on waste facilities regarding emissions. Gas scrubbers help meet these regulations.
- Public Health: Effective scrubbing reduces odors, thus improving the quality of life for nearby residents.
- Resource Recovery: The use of scrubbers can facilitate the recovery of valuable products from waste streams.
Power Generation
In the power generation sector, gas scrubber vessels serve a critical function in reducing emissions from fossil fuel combustion. Power plants emit sulfur dioxide, nitrogen oxides, and particulates, which must be controlled to comply with air quality standards. Both wet and dry scrubbers are employed in this field. For instance, flue gas desulfurization (FGD) units are a type of wet scrubber specifically designed to remove sulfur dioxide from exhaust gases generated by burning coal.
Essential factors to consider in power generation applications include:
- Environmental Impact: By significantly lowering harmful emissions, scrubbers play a vital role in mitigating climate change effects.
- Technological Integration: Advanced control systems enable real-time monitoring of scrubber performance, contributing to a more consistent and efficient operation.
- Economic Efficiency: While the initial investment in scrubbers may be high, the long-term savings from reduced fines, health costs, and improved efficiency can be considerable.
The application of gas scrubber vessels is not merely a regulatory obligation; it is an investment in sustainable practices that safeguard both the environment and public health.
With these examples, it becomes clear that gas scrubber vessels are crucial across various industries, aiding in emission control and enhancing overall operational safety. Their proper implementation can lead to a more sustainable industrial future.
Environmental Regulations and Compliance
The significance of environmental regulations and compliance cannot be overstated when discussing gas scrubber vessels. These regulations serve as the backbone for environmental protection, ensuring that industries mitigate their impact on air quality. The implementation of gas scrubbers aligns with these regulations, making them essential tools for companies striving to maintain compliance and reduce emissions.
Global Standards
Global standards on air quality management dictate strict emission limits for various pollutants. The World Health Organization (WHO) and the United Nations Environment Programme (UNEP) have established guidelines for air quality that many countries adopt as a baseline for their regulations. Compliance with these standards often requires industries to invest in advanced technologies such as gas scrubber vessels, which help to effectively remove harmful pollutants before they enter the atmosphere.
Governments worldwide monitor air quality, and industries found in violation of global standards may face severe penalties, including fines or operational shutdowns. For this reason, compliance is not just a regulatory formality; it is a critical framework guiding industry practices toward sustainability. High compliance reduces the likelihood of respiratory illnesses in communities surrounding industrial operations, thereby enhancing public health and wellbeing.
Local Regulations
Local regulations play a crucial role in shaping the operational landscape of gas scrubber vessels. Different regions may have specific air quality standards based on their unique environmental needs and challenges. Regulations can be influenced by factors such as population density, industrial activities, and geographical considerations.
Industry-specific regulations often outline the required technology, operational procedures, and monitoring practices. For instance, in the United States, the Environmental Protection Agency (EPA) enforces regulations that limit air emissions from various industrial sources, necessitating the use of effective scrubber systems for compliance.
Organizations must stay updated on local requirements to avoid compliance failures. This often involves diligent monitoring of emissions and regular reporting to regulatory bodies. By adhering to local regulations, companies contribute to greater air quality improvements, fostering healthier environments for residents.
"Meeting environmental regulations is not merely about compliance; it is about promoting the sustainability of our natural resources for future generations."
In summary, understanding environmental regulations and compliance is essential for the successful operation of gas scrubber vessels. Global and local standards guide industries in their objectives to minimize emissions. Compliance not only avoids penalties but also promotes a healthier environment and enhances the sustainability of operations. This interplay between regulation and technology continues to shape the evolution of gas scrubber systems.
Technological Advancements in Scrubbing Systems
Technological advancements in scrubbing systems are crucial, as they significantly enhance the efficiency and effectiveness of gas scrubber vessels. With the increasing focus on environmental protection and compliance with stringent regulations, innovations in this field lead to improved performance and reduced operational costs. As industries face growing pressure to minimize air pollutant emissions, integrating these advancements become imperative.
Innovative Materials
Innovative materials play a pivotal role in the development of gas scrubber systems. Recent research has led to the use of high-performance polymers and corrosion-resistant alloys. These materials can withstand harsh operating conditions while providing optimal absorption and reaction capabilities.
For instance, materials like polytetrafluoroethylene (PTFE) are well-known for their chemical resistance and durability. This resistance is important when handling various pollutants, such as sulfur dioxide and carbon dioxide. Moreover, advancements like the development of ceramic membranes offer high efficiency in separating pollutants.
Benefits of using innovative materials include:
- Enhanced durability: Reduces replacement frequency and maintenance costs.
- Improved absorption rates: Increases the efficiency of the scrubbing process.
- Lower weight: Reduces overall system stress and design complexity.
These advancements indicate a shift towards more sustainable and efficient solutions in emission reduction technologies.
Automation and Control Technologies
Automation and control technologies further revolutionize scrubbing systems. The integration of smart sensors and data analytics enables real-time monitoring and adjustments of operating parameters. This enhances the operational flexibility and reliability of gas scrubber vessels.
Smart automation systems can predict required adjustments based on data trends. For example, if emission levels exceed the set threshold, automated systems can increase the scrubbing liquid flow rate or adjust the temperature in the vessel.
Key aspects of automation and control technologies include:
- Real-time monitoring: Continual oversight of scrubbing efficiency and pollutant levels.
- Data analytics: Identification of patterns that can prompt proactive maintenance or system adjustments.
- Remote control: Allowing operators to manage systems from different locations, reducing the need for manual oversight.
"Integrating automation in scrubbing technologies is essential for optimizing performance and ensuring compliance with environmental standards."
Challenges in Implementing Gas Scrubber Technologies
Implementing gas scrubber technologies involves numerous challenges that can impact their effectiveness and efficiency. Understanding these challenges is crucial for ensuring operational success and compliance with environmental regulations. Addressing both technical and economic considerations can significantly enhance the performance of scrubber systems while also meeting industry standards.
Technical Limitations
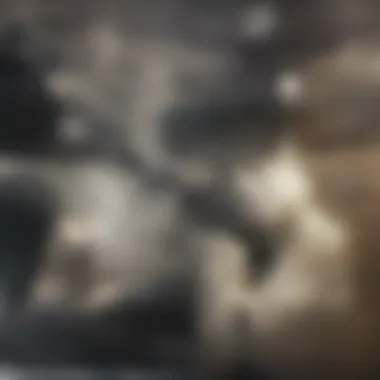
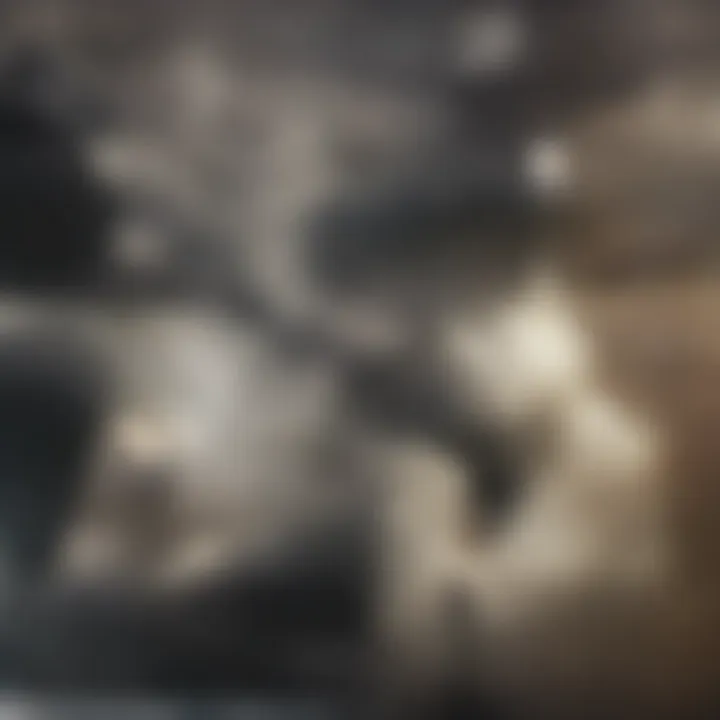
Technical limitations play a pivotal role in the effective application of gas scrubber systems. One major challenge is the variability in the composition of gases that need treatment. Different industrial processes produce different pollutants, which can require different scrubbing techniques. This variability can hinder the selection of an appropriate scrubber design that achieves optimal performance.
The efficiency of a gas scrubber also heavily depends on the physical and chemical properties of the scrubbing liquid or solid absorbent used. Some scrubbing agents may have limited capacity to remove specific contaminants, leading to reduced separation efficiencies. Moreover, scaling-up laboratory-scale designs to industrial levels often reveals unforeseen operational complexities, such as increased pressure drops and inadequate mass transfer rates.
In addition, the operation of gas scrubbers under varying temperature and flow conditions can lead to performance fluctuations. For instance, too high or too low temperatures can adversely affect the solubility of pollutants in the scrubbing solution, hindering effective gas treatment. Addressing these technical issues requires a thorough understanding of the specific operational environment and may necessitate additional research and development efforts.
Economic Considerations
Economic considerations are another significant challenge when implementing gas scrubber technologies. The initial investment required for purchasing and installing gas scrubber equipment can be substantial. Companies must weigh the capital expenditure against the projected benefits of improved air quality and regulatory compliance.
Operational costs represent another aspect that cannot be overlooked. Scrubber maintenance, chemicals for scrubbing solutions, and energy consumption contribute significantly to ongoing expenses. Companies must balance these costs with operational efficiencies and potential fines from non-compliance with environmental regulations.
Furthermore, fluctuating market conditions can affect the long-term viability of scrubber technology investments. For example, if new regulations lead to increased demand for cleaner technologies, companies that have already invested in gas scrubbers may find themselves at a competitive advantage. Conversely, sudden changes in regulatory frameworks can render new installations economically unfeasible.
Navigating the complexities of gas scrubber technologies is essential for ensuring environmental compliance while maintaining economic viability.
Maintenance and Operational Requirements
Maintaining gas scrubber vessels is critical for their effective performance and longevity. Proper maintenance ensures that these systems operate at peak efficiency, minimizing downtime and maximizing pollutant removal. The operational requirements are equally important, as they directly influence performance and compliance with environmental standards. Understanding these aspects helps stakeholders make informed decisions about installation, operation, and upkeep of gas scrubber systems.
Routine Maintenance Practices
Routine maintenance for gas scrubbers involves a series of planned actions aimed at keeping the system operational and efficient. The following practices are essential:
- Inspection: Regular visual inspections are necessary. They help identify any visible damages, leaks, or corrosion that could affect functionality.
- Cleaning: Periodic cleaning of the scrubber components is needed to prevent buildup of solids and residues, which can hinder the scrubbing process. This includes cleaning spray nozzles and demisters.
- Fluid Replacement: In wet scrubbers, the scrubbing liquid should be monitored and replaced as required. Over time, the liquid can become saturated with contaminants, reducing its effectiveness.
- Adjustment of Controls: Control settings need to be checked and calibrated regularly to maintain the desired operational parameters. Out-of-range settings can lead to inefficient scrubbing.
These maintenance practices not only ensure longevity but also enhance pollutant removal efficiency, contributing positively to overall air quality and compliance.
Performance Monitoring
Performance monitoring is essential to evaluate the effectiveness of gas scrubber systems. It involves continuously measuring operational parameters and pollutant removal efficiencies. Key elements of performance monitoring include:
- Emission Testing: Regular testing of emissions helps verify the system's efficiency in removing pollutants. Such tests ensure compliance with environmental regulations.
- Flow Rate Measurement: Monitoring the gas and liquid flow rates is crucial. Deviation from expected flow rates can indicate blockages or equipment malfunction.
- Pressure Differential: Measuring the pressure differential across various components enables operators to detect issues like clogging or malfunctioning parts.
- Data Logging: Implementing a data logging system can facilitate the tracking of operational conditions over time. This data helps identify trends and predict maintenance needs.
"Consistent performance monitoring allows for timely interventions, reducing operational costs and enhancing compliance with environmental regulations."
By integrating routine maintenance and diligent performance monitoring, the overall efficiency and reliability of gas scrubber vessels can be significantly improved. This is essential not only for meeting regulatory requirements but also for ensuring a sustainable operational environment.
Case Studies of Gas Scrubber Applications
The inclusion of case studies in the discussion about gas scrubber applications helps to show real-world impact and effectiveness. These practical examples illustrate how various industries implement scrubbing technologies to meet environmental standards and reduce air pollutants. Each case provides critical insights into the operating conditions, methodologies adopted, and the challenges faced by organizations during deployment.
Successful Implementations
Successful gas scrubber implementations demonstrate their capability to efficiently reduce emissions across multiple sectors. A notable example is the installation of wet scrubbers at pharmaceutical manufacturing plants. In these setups, scrubbing systems are capable of removing volatile organic compounds (VOCs) from exhaust gases. This is crucial given the stringent regulations imposed by environmental authorities.
In oil refineries, dry scrubbers are used to mitigate sulfur dioxide emissions. These scrubbers have a high degree of efficiency and reduce the environmental footprint of operations substantially. The implementation process involved thorough site assessments, leading to a tailored design that optimizes both cost and performance while ensuring compliance with regulations.
The installation of semi-dry scrubbers in cement plants has also proven successful. These facilities faced challenges due to the high dust load in the flue gas. Adopting semi-dry technology allowed for effective capture of particulates and measurement of acid gas emissions simultaneously. Data from operational assessments shows that these implementations not only reduced pollutant levels but also improved the overall efficiency of the plants.
Lessons Learned
Analyzing successful implementations offers valuable lessons that can guide future projects. One important lesson is the significance of initial feasibility studies. A comprehensive evaluation of the site conditions often uncovers potential obstacles beforehand. These studies can lead to better-targeted solutions that address specific requirements of the industry.
Another critical observation involves ongoing maintenance and monitoring. Facilities with robust performance monitoring systems can quickly address deviations from expected operation metrics. This proactive approach often leads to higher scrubbing efficiencies and longer equipment lifespan.
Furthermore, collaboration among multidisciplinary teams during the design and installation phases has shown to enhance the reliability of outcomes. Engaging engineers, environmental scientists, and regulatory experts helps to ensure that all aspects of compliance and operational efficiency are considered.
In essence, case studies provide a framework for understanding the tangible benefits and challenges associated with gas scrubbing technologies. They serve as essential reference points for industries looking to enhance their emission control systems.
Future Directions for Gas Scrubber Technologies
The future of gas scrubber technologies holds significant promise for enhancing environmental sustainability and operational efficiency. As industries face stricter regulations on air quality, companies are compelled to adopt advanced scrubbing solutions. Innovations in this field not only improve compliance with environmental standards but also enhance the overall performance of scrubber systems. Understanding these future directions is crucial for stakeholders such as engineers, policymakers, and environmental scientists.
Emerging Trends
Recent advancements in gas scrubber technologies reveal several key trends that are shaping their evolution:
- Integration of Smart Technologies: The adoption of IoT technologies is transforming how scrubbers operate. Real-time data collection and analysis enable better monitoring of emissions, which leads to more informed decision-making and enhanced performance.
- Sustainability Focus: There is increasing emphasis on using biodegradable and low-impact scrubbing media. Companies are exploring materials that reduce both operational costs and environmental harm, creating a win-win situation for market viability and ecological preservation.
- Hybrid Systems: The development of hybrid scrubbing technologies combines the advantages of wet, dry, and semi-dry scrubbers. These systems offer flexibility and can address a wider range of pollutants effectively.
- Modular Designs: Modular gas scrubber systems allow for easier installation, maintenance, and scalability. This trend caters to varying industrial needs, enhancing adaptability in different operational environments.
Research Opportunities
The quest for more effective gas scrubbing technologies opens numerous research avenues:
- Material Science: Research into new materials for scrubbing media and vessel construction is crucial. For instance, the exploration of advanced composites could lead to higher resistance against corrosive environments, thus extending the operational lifespan of scrubbers.
- Process Optimization: Investigating the dynamics of scrubbing processes is essential to improve efficiency. Studies on fluid dynamics and the chemical interactions within scrubbers could uncover new methods to enhance pollutant removal rates.
- Ecological Impact Studies: As scrubber technologies advance, evaluating their environmental impact becomes vital. Research focusing on the lifecycle assessment of different scrubbing systems can provide insights into their overall sustainability.
- Policy Analysis: Understanding the regulatory landscape is important for future developments in scrubber technologies. Research that analyzes regulatory changes could inform manufacturers about potential compliance challenges and opportunities for innovation.
"Investing in gas scrubber technologies not only supports regulatory compliance but also promotes a cleaner and more sustainable industrial future."
By focusing on these emerging trends and research opportunities, the industry can pave the way for a more sustainable and effective approach to air pollution control, driving innovation in gas scrubber technologies.