The Comprehensive Guide to Micro End Mills
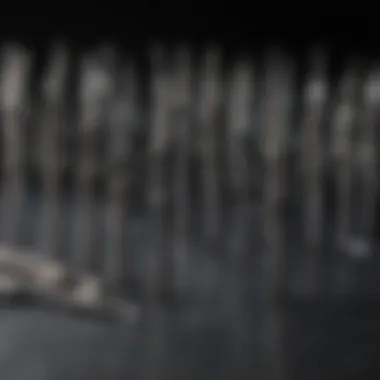
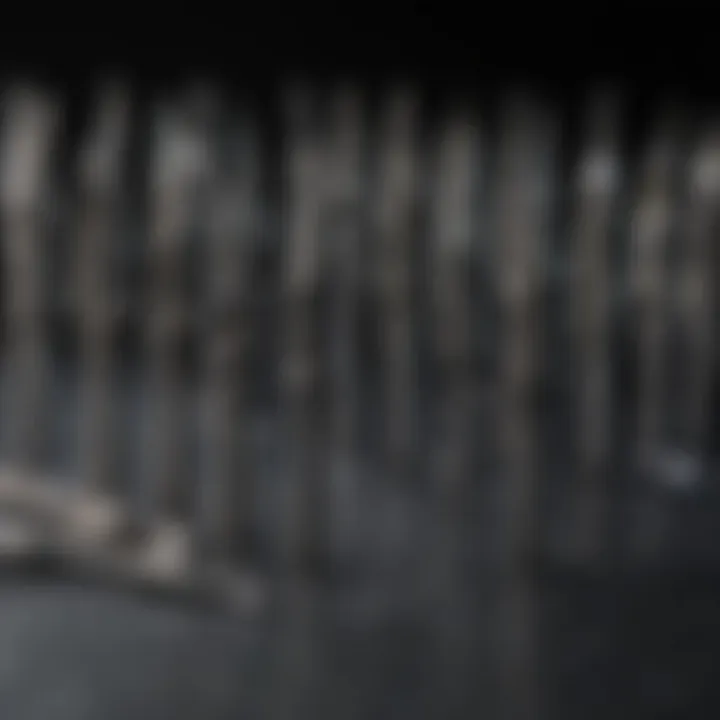
Intro
Micro end mills represent a crucial advancement in the field of machining, offering unparalleled precision for intricate designs. These cutting tools, typically less than 1 mm in diameter, are engineered to meet the demands of modern manufacturing. As industries increasingly shift toward finer precision and complexity, micro end mills have established themselves as indispensable tools in the machiner's toolkit.
The objective of this guide is to provide an in-depth understanding of micro end mills, exploring their definitions, various types, and applications, along with the essential material considerations and performance factors. Through this examination, one will see the significant advantages they hold over traditional end mills.
In the subsequent sections, topics will include key concepts, insights into current research gaps, and future directions for studies and applications. This comprehensive approach aims to equip students, researchers, and professionals with not just knowledge but also applicable insights into micro end mills and their role in contemporary machining processes.
Understanding Micro End Mills
Micro end mills play a crucial role in precision machining. These tiny cutting tools enable manufacturers to create complex parts with exceptional accuracy. Understanding micro end mills involves grasping not only their definitions but also their unique characteristics and applications.
By diving into this topic, readers can appreciate how micro end mills contribute to advancements in various industries. They enhance productivity and efficiency, offering benefits that allow for intricate designs not achievable with standard cutting tools. Moreover, this knowledge helps in selecting the right tools for specific jobs, which is essential in fields where precision is paramount.
Definition and Characteristics
Micro end mills are defined as miniature cutting tools with a diameter typically less than 1 millimeter. They are used in high-precision milling operations. The main characteristic setting them apart is their ability to achieve fine details and smooth finishes in materials, making them indispensable in fields like electronics and medical device manufacturing.
Key characteristics include:
- Precision: Micro end mills maintain tight tolerances, essential for intricate designs.
- Variety of geometries: They come in various shapes, enabling different milling operations.
- Material compatibility: Suitable for various materials from metals to plastics, which broadens their usage.
Due to their small size, micro end mills require advanced machinery capable of supporting their operation. This equipment provides the necessary stability and control.
Differences Between Micro and Standard End Mills
The distinctions between micro and standard end mills are significant. Standard end mills typically range from 1 to 20 millimeters, designed for bulk removal of material. In contrast, micro end mills excel in precision, performing intricate tasks that standard tools cannot handle.
Notable differences include:
- Size: The most obvious difference is the diameter. Micro end mills are much smaller.
- Applications: Micro end mills are used for fine detail work, while standard end mills serve larger projects.
- Tool life: Due to the nature of their work and the smaller geometries, micro end mills may wear out faster and need more frequent replacements.
Understanding these differences is vital for selecting the right tool for specific applications. Manufacturing processes that require both types of tools can benefit from the complementary use of micro and standard end mills to optimize productivity.
Types of Micro End Mills
Understanding the different types of micro end mills is essential for professionals in machining and manufacturing. Marrying tool design with the specific needs of various applications, the selection of the right type can significantly influence both performance and end product quality. This guide will explore solid micro end mills, coated micro end mills, the differences in flute designs, and the functionality of ball nose compared to flat end styles. Each type has its own advantages and considerations that can affect machining outcomes.
Solid Micro End Mills
Solid micro end mills are manufactured from high-speed steel or carbide which make them suitable for high precision machining tasks. These tools tend to exhibit improved rigidity and stability during operation. Solid construction allows for enhanced cutting capabilities, especially when machining materials like aluminum, copper, and various plastics. Some benefits of solid micro end mills include:
- High durability in challenging manufacturing environments.
- Better performance during dry machining tasks.
- Reduced risk of delamination in delicate materials.
Despite these advantages, solid micro end mills can be prone to wear, which may necessitate regular maintenance and eventual replacements. Therefore, understanding the expected tool life and wear patterns is crucial for achieving optimal results.
Coated Micro End Mills
Coated micro end mills feature a thin layer of material applied to the cutting edge, improving performance in specific applications. Coatings like titanium nitride (TiN) or diamond enhance surface hardness, reduce friction, and increase heat resistance. This leads to several key benefits:
- Lower cutting temperatures, extending tool life.
- Increased resistance to corrosion and wear.
- Improved surface finish on the workpiece due to smoother cutting action.
When selecting coated micro end mills, it’s important to match the coating with the material being machined. An improper match may lead to ineffective cutting and reduced tool efficiency.
Two-Flute vs. Four-Flute Designs
The flute count of a micro end mill has a direct impact on its performance characteristics. Two-flute designs are better suited for deeper cuts and provide more space for chip removal. This can help in improving the overall surface finish. On the other hand, four-flute designs cater to increased strength and stability during machining. Some points to consider include:
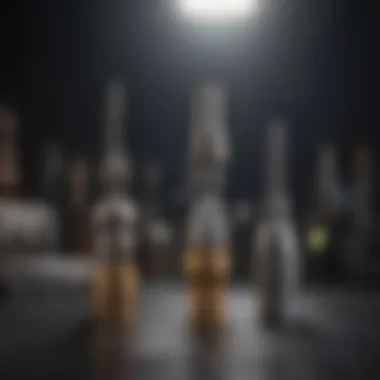
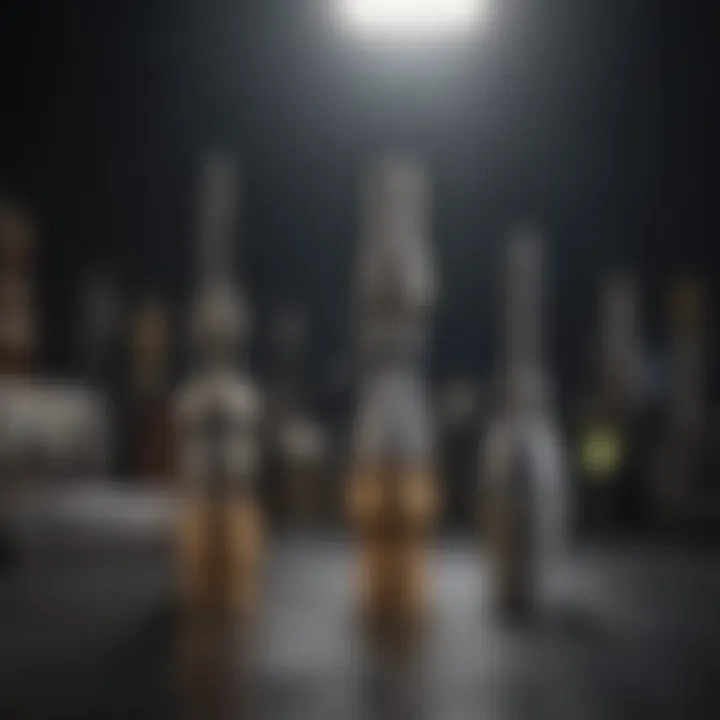
- Two-Flute Designs:
- Four-Flute Designs:
- Enhanced chip removal capability, ideal for softer materials.
- Better for plunge cutting operations, as they remove material efficiently.
- Provides great rigidity, benefiting harder materials.
- Offers smoother finishes due to higher cutting edges interacting with the material.
Choosing between these flute designs relies heavily on the specific application and material to be machined. Each option provides its unique solutions based on cutting requirements.
Ball Nose vs. Flat End Styles
Ball nose and flat end micro end mills serve different roles in machining operations. Ball nose end mills are ideal for creating contoured surfaces and complex shapes due to their rounded tips. They are particularly useful in:
- 3D machining tasks, where a smooth surface is essential.
- Creating molds and dies where precision is paramount.
Flat end mills, conversely, provide a larger surface area and are generally favored for:
- Horizontal surfaces and engraving tasks.
- Operations requiring flat-bottomed cuts in various materials.
Understanding the functional differences is critical. The choice should be determined by the specific requirements of the project, as one type may yield better results than another for a given task.
Overall, choosing the right type of micro end mill can make the difference in efficiency and outcome of machining processes. Mastering these tools is a step toward achieving precision and excellence in manufacturing.
Applications of Micro End Mills
Micro end mills are integral to many industries due to their ability to handle intricate designs and produce fine finishes. Their application extends across various fields, showcasing their versatility and importance in modern manufacturing. Understanding the specific applications of micro end mills is vital for professionals looking to enhance precision in machining processes.
Aerospace Engineering
In aerospace engineering, micro end mills play a critical role in the manufacturing of components that require high precision and durability. These tools enable the machining of complex shapes in materials such as titanium and aluminum, commonly used in aircraft structures. The lightweight nature of these metals, combined with the need for intricate designs, makes micro end mills suitable. They allow for tight tolerances and smooth finishes, overcoming manufacturing challenges inherent to this high-stakes field. Furthermore, the ability to machine small parts reduces material waste, contributing to cost-effectiveness in the production of aerospace components.
Medical Device Manufacturing
The medical device industry relies heavily on micro end mills for producing components that must meet strict regulatory standards. Parts like surgical instruments, implants, and diagnostics devices often require extreme precision and fine detailing. Micro end mills facilitate the creation of these items with high surface finish standards. In addition, their ability to machine complex geometries means that manufacturers can develop innovative products improving patient care. Selecting appropriate materials, such as stainless steel or biocompatible plastics, further enhances the efficacy of micro end mills in this sector.
Electronics Production
Electronics production is another area where micro end mills are indispensable. Components such as circuit boards, connectors, and housings benefit from the small-scale machining capabilities offered by these tools. The ability to achieve high accuracy in the production of intricate patterns on circuit boards enhances functionality and performance. With the rapid pace of technological advancements, micro end mills allow for quick prototyping and production of electronic components on a small scale, reflecting the industry's need for innovation and adaptability.
Prototyping and Custom Tooling
In prototyping and custom tooling, micro end mills enable designers and engineers to quickly create and iterate on new ideas. The precision offered by these tools means that prototypes can closely resemble final products, allowing for thorough testing and evaluation. This iterative process is crucial in industries where time is of the essence, and rapid product development can mean the difference between success and failure. Moreover, custom tooling resulting from micro end mill application can cater to specific needs, expanding the capabilities of manufacturing practices in diverse sectors.
Material Considerations for Micro End Mills
When discussing micro end mills, understanding the material used in their construction is crucial. The material fundamentally influences their performance, longevity, and suitability for various applications. Considering the demands of modern machining, it is essential for engineers and manufacturers to choose wisely. Selecting the right material affects cutting efficiency, tool wear, and precision. This section outlines common materials used for micro end mills and examines the impact that material selection has on overall performance.
Common Materials Used
Micro end mills are typically made from a range of materials, each chosen for specific properties that enhance their cutting ability. Here are some of the most common materials:
- High-Speed Steel (HSS): This material is known for its toughness and resistance to chipping. HSS micro end mills are often used for general machining tasks, offering a balance between performance and cost.
- Carbide: This is a dominant material in micro end mills due to its superior hardness and heat resistance. Carbide tools retain their cutting edge longer than HSS, making them ideal for high-speed machining.
- Cobalt Alloys: These materials share properties of both HSS and carbide, offering enhanced heat and wear resistance. Cobalt alloys are often used in applications requiring high strength and durability.
- Coated Tooling: Applying coatings such as Titanium Nitride (TiN) or Titanium Aluminum Nitride (TiAlN) can significantly increase wear resistance to oxidation and friction. Coated micro end mills enable longer tool life with improved surface finishes.
"The selection of material for micro end mills plays a pivotal role in their effectiveness and longevity in machining operations."
Impact of Material Selection on Performance
The material of a micro end mill heavily influences its operational characteristics. Here are some key factors affected by this choice:
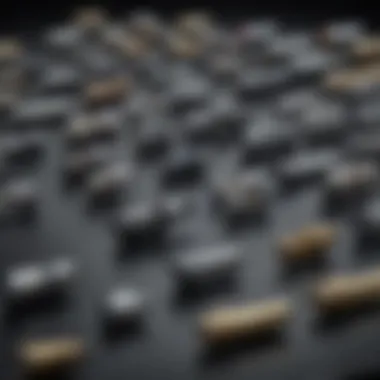
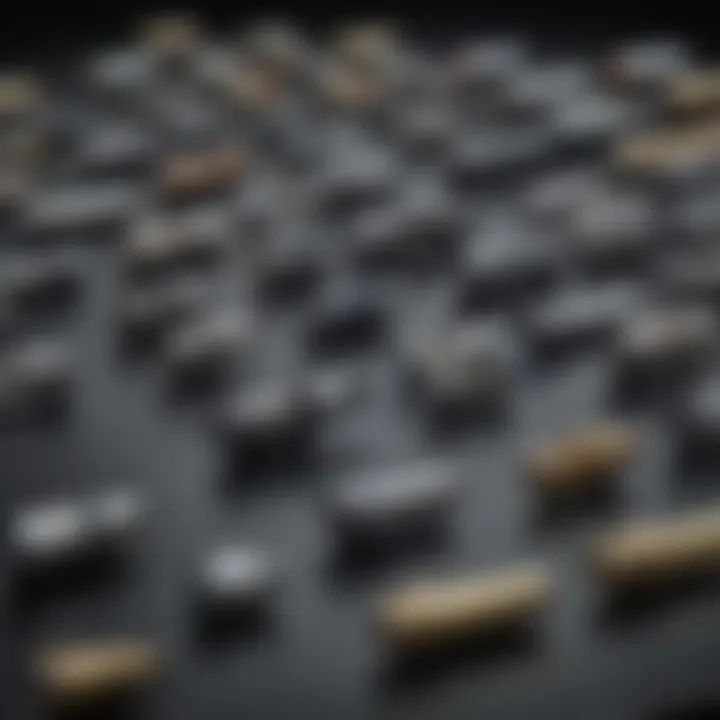
- Tool Life and Wear Resistance: Materials like carbide and cobalt alloys offer higher wear resistance compared to HSS. This resistance allows for longer tool life, reducing the frequency of tool changes, which can result in cost savings over time.
- Cutting Speed Capabilities: Carbide tools can generally withstand higher cutting speeds than HSS due to their thermal properties. This capability enhances productivity but often requires precise control to avoid overheating.
- Surface Finish Quality: The quality of the machined surface is critical in many applications. Coatings on tools can improve the quality of the finish by reducing tool friction, leading to a smoother, more precise cut.
- Chipping Risk: Toughness is important in high-stress applications. Materials like HSS may be more prone to chipping under extreme conditions compared to harder materials like carbide. Therefore, the risk of chipping can determine the suitable material choice for certain machining environments.
Performance Factors in Micro End Milling
Micro end milling involves precision machining where several performance factors are critical to achieving high-quality results. Understanding these factors ensures that machining meets desired specifications, enhances production efficiency, and maximizes tool life. Hence, this section addresses three specific elements: cutting speed and feed rate, tool geometry and design, and the usage of coolants and lubricants.
Cutting Speed and Feed Rate
Cutting speed refers to the linear speed at which the cutting edge of the tool engages with the material. It is typically measured in meters per minute. For micro end mills, cutting speed is vital. Choosing the right cutting speed can have significant implications. If the speed is too high, overheating may occur, leading to premature tool wear. Conversely, if the speed is too low, the process may result in inefficient material removal and extended machining time.
Feed rate is the speed at which the tool advances into the material being cut. This measurement, often expressed in millimeters per minute, essentially determines the depth of cut in one pass. Selecting the correct feed rate balances productivity with surface finish quality. A higher feed rate will increase material removal but may compromise precision and surface finish. Thus, it is essential to strike an appropriate balance between cutting speed and feed rate to optimize performance.
Tool Geometry and Design
The geometry of micro end mills includes several attributes, such as cutting edge angle, flute shape, and the number of flutes. Each of these elements plays a crucial role in how effectively the tool performs.
- Cutting Edge Angle: A sharper cutting edge can improve cutting efficiency but may reduce the tool's strength. This trade-off must be considered based on the material being machined.
- Flute Shape: The design of flutes affects chip removal. Flutes that facilitate effective chip evacuation prevent tool clogging and maintain cutting efficiency.
- Number of Flutes: Tools with more flutes can handle increased feed rates. However, fewer flutes provide better chip removal and cooling capabilities. The choice depends on the machining application.
Having the right tool geometry is critical for maximizing precision and minimizing wear.
Coolants and Lubricants Usage
Coolants and lubricants play an indispensable role in micro end milling. Their applications not only help to control temperature during machining but also provide lubrication to reduce friction between the tool and workpiece.
- Types of Coolants: There are various coolants, including water-based, oil-based, and synthetic. Choosing the right type impacts thermal control and surface finish.
- Benefits of Usage: Proper coolant application enhances tool life, minimizes the risk of thermal damage to the workpiece, and improves overall efficiency.
Incorporating the right coolants and lubricants creates a more efficient machining environment, facilitating better performance in micro end milling.
"Proper management of performance factors ensures not only tool longevity but also superior surface quality and precision, which are essential in advanced machining applications."
Understanding these performance factors is crucial for students, researchers, and professionals in the manufacturing field. It directly impacts the quality of work produced and optimizes the use of micro end mills.
Challenges and Limitations
Understanding the challenges and limitations of micro end mills is crucial for users seeking to achieve optimal results in machining applications. While micro end mills offer precise cuts and the ability to work on intricate designs, they also come with specific hurdles that must be addressed. These challenges can influence tool selection, machining strategies, and overall production efficiency. Entering this realm requires careful consideration of the distinct elements associated with wear, tolerances, and cost assessments, among other factors.
Wear and Tool Life
Wear and tool life are paramount factors affecting micro end milling. As compared to traditional end mills, micro end mills are inherently more susceptible to wear due to their smaller diameter and geometry. This result in increased friction and heat generation, which can hasten the degradation of the cutting edges. Micro end mills often have a limited lifespan, necessitating frequent replacements or re-sharpening. Consequently, users must monitor usage closely, often leading to increased workload during production planning. Optimal management of wear requires selecting appropriate parameters for speed, feed rates, and cutting conditions. Using the right materials and coatings can extend tool life significantly.
"Tool wear is a measure of the degradation of cutting tools, and understanding this phenomenon is essential for effective machining strategies."
Machining Tolerances and Precision
Maintaining machining tolerances and precision is an intricate process when using micro end mills. The finer the feature size, the more challenging it becomes to maintain accuracy. Due to their size, micro end mills can amplify any discrepancies in machining processes, leading to suboptimal results. Factors such as vibrations, tool deflection, and thermal expansion can distort the cutting path. To combat these issues, it is vital to implement stringent quality control measures and rigorous inspection protocols. Adopting advanced machining techniques, such as adaptive machining strategies, can also assist in enhancing precision, thus aligning the manufacturing output with expected tolerances.
Cost Considerations
Cost is an inherent challenge in employing micro end mills. The combination of a higher upfront tool cost and reduced tool life can lead to inflated production expenses. Understanding the total cost of ownership, which includes factors like maintenance and replacement, is essential for making informed purchase decisions. While cheaper options may seem appealing initially, they could lead to increased total costs due to frequent replacements and poorer performance. A thorough cost-benefit analysis is needed to evaluate micro end mills against traditional models, weighing the benefits of precision against their expenses. Moreover, investing in high-quality tools can yield longer-term savings, improved efficiency, and better end results.
Comparative Analysis
In the realm of precision machining, understanding the comparative dynamics between micro end mills and traditional end mills is crucial. This analysis serves not only to highlight differences in performance and application but also to provide insight into how each type of tool fits within the broader landscape of manufacturing. Comprehending these distinctions enables manufacturers and engineers to make more informed decisions aligned with their specific needs.
Micro End Mills vs. Traditional End Mills
Micro end mills possess unique features that differentiate them from their traditional counterparts. The most apparent distinction lies in their size; micro end mills typically possess a diameter of less than 1 millimeter. This precision allows for intricate cuts and detailed designs not achievable with standard end mills, which can have diameters up to several centimeters.
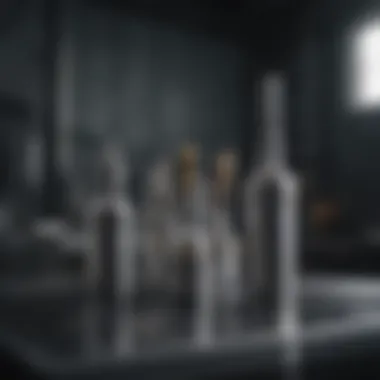
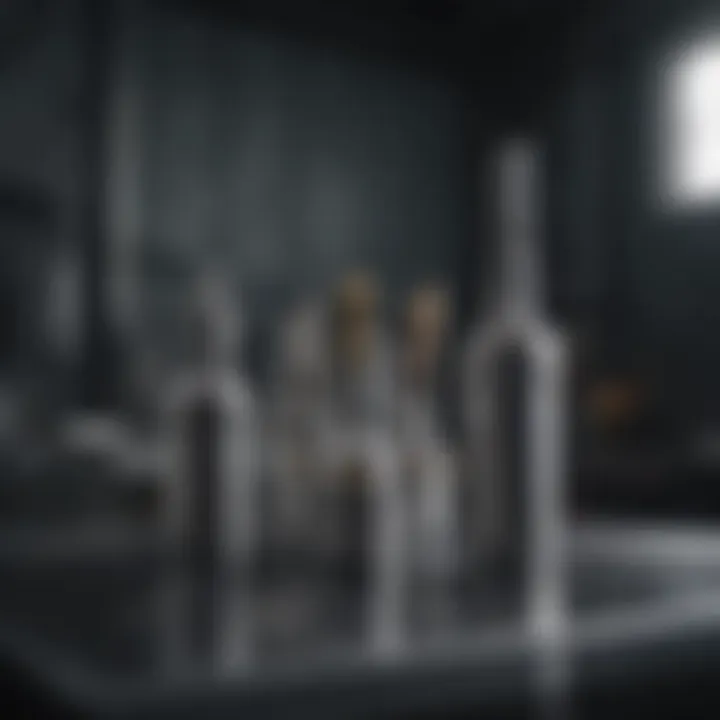
The design geometry of micro end mills is also distinct. They often feature finer flutes, allowing for better chip removal in tight spaces. This results in less material build up and improved surface finishes. In contrast, traditional end mills tend to have broader and deeper flutes conducive to handling more material at once, making them ideal for bulk operations.
Another important aspect is the application range. Micro end mills are predominantly used in sectors requiring high precision, such as electronics and medical device manufacturing. On the other hand, traditional end mills are more widely applied in general machining operations such as milling larger components without intricate details.
In terms of cost, micro end mills are generally more expensive than traditional models. The production techniques, such as tighter tolerances and better materials, contribute to this increased cost. However, the trade-off lies in the precision and quality of the finished product. It is essential to weigh these factors carefully.
"Micro end mills can tremendously enhance production capabilities by enabling complex geometries that were previously unattainable."
Advantages and Disadvantages
Both micro end mills and traditional end mills come with their sets of advantages and disadvantages, which is crucial in the comparative analysis.
Advantages of Micro End Mills:
- Precision: They achieve high precision in tight tolerances, essential for intricate designs.
- Detailing: Capable of creating complex geometries with defined features.
- Surface Finish: They often provide superior surface finishes, reducing the need for secondary operations.
Disadvantages of Micro End Mills:
- Cost: The initial investment is generally higher compared to traditional end mills.
- Durability: Micro end mills can be more susceptible to wear and tear, affecting tool life.
- Speed Limitations: They often require lower cutting speeds, limiting their overall productivity in some applications.
Advantages of Traditional End Mills:
- Cost-Effectiveness: Lower initial costs make them suitable for bulk operations.
- Durability: The construction can allow for longer tool life under certain conditions.
- Versatility: They can handle a broader range of materials and operations.
Disadvantages of Traditional End Mills:
- Lower Precision: Not optimal for highly detailed or intricate work.
- Surface Finish: Often requires additional processing for high-quality finish.
- Limited in Complexity: Not capable of achieving designs that micro end mills can produce efficiently.
The Future of Micro End Mills
The landscape of machining is rapidly changing, and micro end mills are at the forefront of these developments. Understanding the future of micro end mills means recognizing their potential impact on precision manufacturing, technological integration, and sustainable practices. As industries continue to evolve, the demand for more intricate designs and tighter tolerances will only increase. Thus, it is crucial to explore the advancements shaping these tools and how they will contribute to modern engineering and manufacturing solutions.
Technological Advancements
Technological innovation is a primary driver for the future of micro end mills. As research and development take center stage, newer technologies are continuously being integrated into tool manufacturing and application.
- CNC Machining Integration: Computer Numerical Control (CNC) technology enhances accuracy and repeatability in micro milling processes. Modern CNC systems allow for complex geometries to be machined effectively, surpassing the limitations of traditional methods.
- Additive Manufacturing Synergy: The confluence of additive manufacturing and micro end milling is promising. These processes can complement each other, allowing for the creation of complex parts and structures that were previously difficult to achieve.
- Advanced Coatings and Materials: New materials and coating techniques are emerging, enhancing the durability and functionality of micro end mills. Innovations such as diamond-like carbon (DLC) coatings significantly improve wear resistance and heat dissipation, extending tool life.
- Automation and AI: The incorporation of artificial intelligence into the manufacturing process can optimize operations by predicting tool wear and automatically adjusting parameters. This could lead to improved efficiency and cost-effectiveness.
"Technological advancements in micro end mills are paving the way for unprecedented precision and efficiency in modern manufacturing."
Sustainability Considerations
Sustainability is increasingly becoming a priority in manufacturing processes, and micro end mills hold a strategic position in these initiatives. As industries look for ways to reduce their environmental impact, several considerations emerge in the realm of micro milling.
- Material Efficiency: Micro end mills allow for greater material efficiency due to their precision. Minimizing waste in both raw materials and energy consumption is vital for sustainable practices.
- Recyclable Materials: The exploration of recyclable materials in tool production is essential. Manufacturers are investigating options that can be repurposed or recycled after their lifespan, reducing the overall environmental footprint.
- Reduced Energy Consumption: Tools designed for maximum efficiency help decrease energy use during machining. Innovations in tool geometry can result in lower cutting forces, leading to less energy required for operation.
- Eco-friendly Lubricants and Coolants: The development of biodegradable lubricants and coolants is also on the rise. These products can significantly reduce the ecological impacts associated with traditional options.
End
The conclusion of this article highlights the significance of micro end mills in the landscape of modern manufacturing. Through the insights gained in previous sections, it becomes clear that these precision tools are not just specialized instruments; they are pivotal in achieving high levels of accuracy and efficiency in various machining applications. By understanding their characteristics, types, and roles, professionals in the field can leverage their unique advantages to enhance production processes.
Summary of Key Points
Micro end mills are small but crucial in precision machining. Key points include:
- Definition: Micro end mills are cutting tools designed for intricate precision work.
- Applications: Widely used in aerospace, medical devices, and electronics among other industries.
- Design Variations: Availability of solid and coated options, and different flute designs suitable for specific applications.
- Performance Factors: Influenced by material selection, cutting speed, feed rate, and tool geometry.
- Challenges: They face issues related to tool wear, precision, and overall cost considerations, which must be navigated effectively.
The Role of Micro End Mills in Modern Manufacturing
In contemporary manufacturing, micro end mills fulfill an essential role by enabling the creation of complex features and fine details in parts. Unlike conventional tools, micro end mills provide opportunities for miniaturization in designs, which is increasingly important in industries such as electronics and medical devices. Their performance enhances production rates and quality controls, resulting in more efficient operations. Moreover, advancements in micro end mill design and materials continue to push boundaries, indicating a strong future for their application in high-tech areas.
"Micro end mills are not merely tools; they represent the convergence of precision and innovation in modern manufacturing."
As the demand for more complicated and precise components rises, micro end mills will continue to be instrumental in meeting these challenges, solidifying their role in the infrastructure of advanced manufacturing.