In-Depth Insights on Polyurethane Fabric Coating Spray
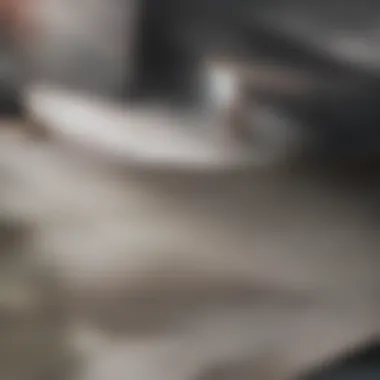
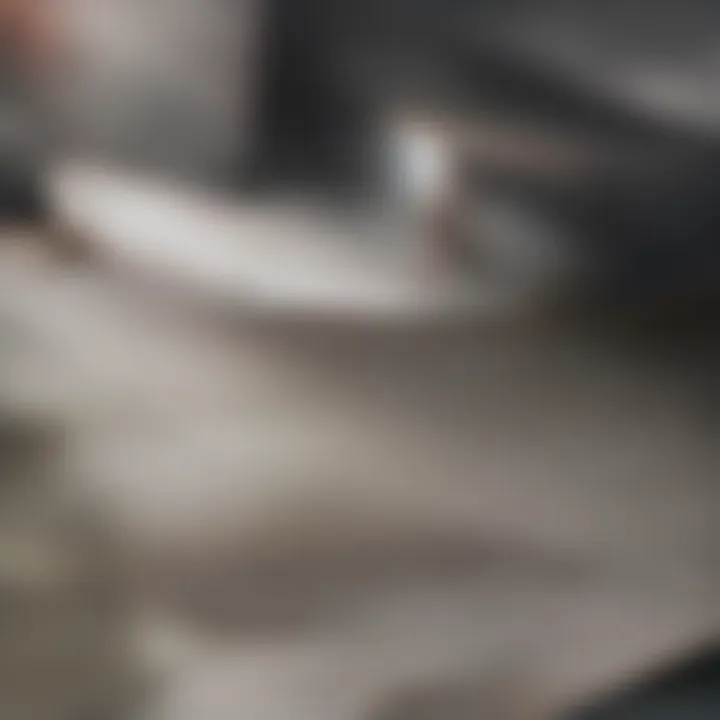
Intro
The importance of polyurethane fabric coating spray cannot be overstated in today's textile landscape. This material has become central to numerous applications, from outdoor gear to various protective clothing items. Understanding its properties, effectiveness, and environmental implications is crucial for students, researchers, and professionals involved in materials science and textile engineering. By exploring various facets of polyurethane fabric coating spray, we aim to equip readers with knowledge that aids in informed decision-making and further discussion in relevant fields.
Key Concepts
Understanding polyurethane starts with a few foundational concepts that frame its utility.
Definition of Primary Terms
Polyurethane is a polymer composed of organic units joined by carbamate links. When used in fabric coatings, it enhances water resistance while allowing the material to retain its breathability. This unique combination has made polyurethane a popular choice in a variety of applications.
Fabric Coating Spray refers to the application process of a coating material onto textiles to impart certain properties such as durability, waterproofing, and resistance to abrasions. This method is particularly advantageous due to its ease of application and uniform coverage, which is essential in manufacturing and outdoor recreation industries.
Related Concepts and Theories
The utility of polyurethane fabric coating begins with its chemical structure, which is versatile and adaptable. The following concepts are related:
- Waterproofing Mechanisms: Polyurethane's effectiveness is derived from its hydrophobic properties that prevent water molecules from penetrating the fabric fibers, making it ideal for outdoor uses.
- Breathability: Polyurethane coatings can be engineered to allow moisture vapor to escape, which is critical in fabrics for active wear.
- Environmental Impact: Examination of the life-cycle of polyurethane is crucial. The production, use, and disposal processes introduce significant environmental considerations.
Polyurethane fabric coatings serve not just functional needs but also raise questions regarding sustainability and environmental effects throughout their life cycle.
Future Directions
As industries evolve, the need for further investigation into polyurethane coatings remains evident.
Gaps Identified in Current Research
While there is substantial information on polyurethane's effectiveness, gaps exist in understanding its long-term environmental impacts, particularly post-consumer disposal and degradation processes. More comprehensive studies that evaluate the sustainability of the coatings and advances in bio-based alternatives would be beneficial.
Suggestions for Further Studies
Future research should focus on the following aspects:
- Reduced Environmental Impact: Explore methods to produce polyurethane coatings that minimize environmental harm and optimize recycling options.
- Innovative Applications: Investigate the potential for new uses of polyurethane in emerging markets, such as smart textiles and medical applications.
- User Safety Evaluations: Conduct thorough assessments to ensure user safety in different environments, particularly in industrial and outdoor settings.
Prologue to Polyurethane Fabric Coating Spray
Polyurethane fabric coating spray is an essential topic in today's material science and textile industry. Understanding its properties, methods of application, and contexts of use enhances its significance across various sectors. This introduction sets the stage by foregrounding the importance of polyurethane coatings for fabrics, as they offer durability and versatility.
The benefits of using polyurethane coatings are manifold. They provide enhanced water resistance, UV protection, and abrasion resistance, which are essential for both outdoor and indoor applications. Given the increasing demand for durable and sustainable materials, polyurethane coatings meet the needs of a market that is increasingly focused on performance and longevity.
Moreover, since innovation drives much of today’s manufacturing processes, a deeper understanding of polyurethane fabric coating spray equips professionals and researchers with the knowledge to develop functional and innovative materials. This is particularly relevant for sectors like textiles, medical applications, and outdoor gear manufacturing. Researchers and industry professionals will find the in-depth insights beneficial for bridging gaps between product development and consumer expectation.
Definition and Overview
Polyurethane fabric coating spray refers to a synthetic polymer that is applied to fabric surfaces to enhance their properties. The coating process involves spraying a polyurethane mixture onto the fabric, which upon curing, forms a flexible and durable layer. This layer can significantly improve the material's resistance to wear, water, and chemicals.
Polyurethane coatings can be tailored for various applications, making them versatile across industries. For instance, they can be found in automotive upholstery, outdoor gear, and even clothing designed for medical purposes. The flexibility and strength of the coating allow the base fabric to maintain its original characteristics, enhancing its lifespan without compromising comfort.
Historical Context and Development
The development of polyurethane coatings began in the mid-20th century, with significant strides made during the 1960s and 1970s. Innovations came from the need for materials that could withstand harsh environmental conditions while providing comfort and usability.
Initially, the use of polyurethane coatings was primarily limited to industrial applications. However, as the technology progressed and manufacturing techniques improved, the applications expanded to consumer goods. Today, we see polyurethane coatings widely used in fashion, outdoor equipment, and protective clothing.
The evolution of this material reflects the changing needs of society, pushing for more durable, eco-friendly fabric options. The historical advancements continue to influence current practices, emphasizing the importance of ongoing research and development in this field.
Chemical Composition of Polyurethane Coatings
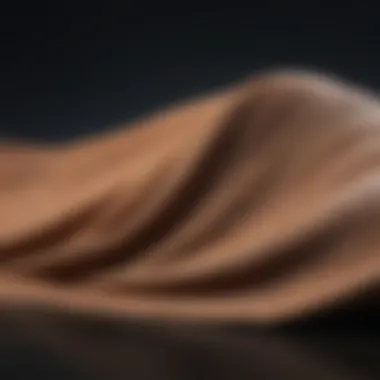
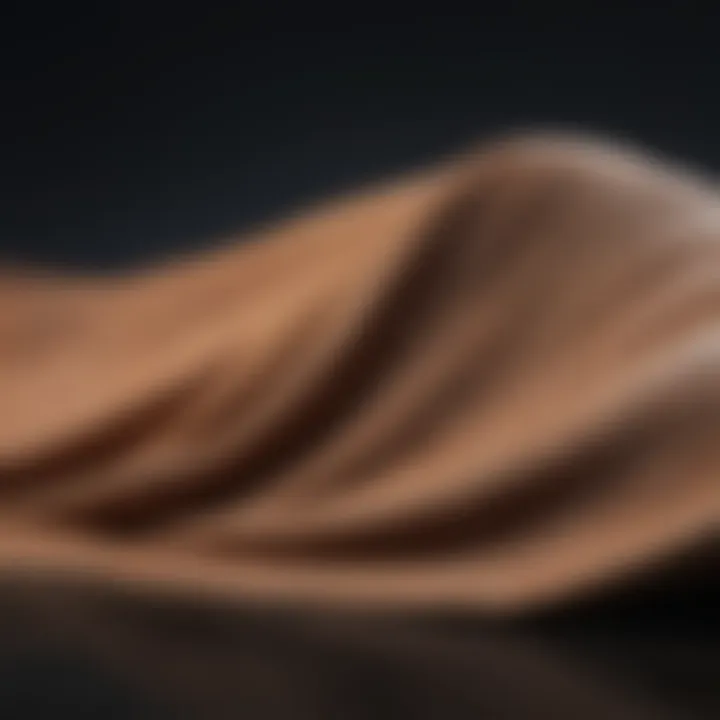
The chemical composition of polyurethane coatings is paramount to understanding their functionality and effectiveness. Polyurethane coatings are engineered to provide a blend of durability and flexibility, making them suitable for various applications. The specific composition influences the performance characteristics, including adhesion, resistance to abrasion, and overall longevity. Grasping the fundamentals of these materials allows researchers and professionals to make informed decisions when selecting coatings for different uses.
Base Materials
Base materials for polyurethane coatings primarily consist of polyols and isocyanates. Polyols are hydroxyl-containing compounds that react with isocyanates to create the backbone of the polyurethane structure. Various types of polyols can be used, including polyether polyols and polyester polyols. Each type imparts different properties to the final product. For instance, polyether polyols usually offer good flexibility and resistance to hydrolysis, while polyester polyols enhance the coating's durability against mechanical stress.
The choice of base materials significantly influences the final characteristics of the coating. Users must consider factors like application surface, required performance, and environmental exposure when selecting these base materials to ensure ideal results.
Curing Agents
Curing agents, also known as hardeners, are essential for the chemical reaction that transforms the polyurethane from a liquid state to a solid form. Typical curing agents include aliphatic or aromatic isocyanates, which react with the hydroxyl groups present in polyols. The type of curing agent chosen directly affects the film's hardness and chemical resistance. For example, toluene diisocyanate (TDI) is commonly used for applications where flexibility is desired, while hexamethylene diisocyanate (HDI) provides high durability and weather resistance.
Moreover, the amount and ratio of curing agent to base material can influence the coating’s final properties. Too little curing agent may lead to incomplete bonding, resulting in a weaker coating, while excessive amounts can produce a brittle film. The balance is crucial for achieving optimal performance.
Additives and Enhancers
Additives and enhancers play a critical role in modifying the performance of polyurethane coatings. These include thickeners, surfactants, and curing accelerators. Thickeners adjust viscosity, making the coating easier to apply. Surfactants improve wetting and adhesion to the substrate, enhancing application efficacy. Additionally, certain additives can provide specific effects like improved UV resistance or enhanced antimicrobial properties.
Common additives include dimethylpolysiloxane, which can increase flexibility and hydrophobicity, and light stabilizers that reduce degradation caused by ultraviolet light. The careful selection of these additives can further tailor the polyurethane coating to meet specific industrial or ecological requirements.
"Understanding the individual components and their interactions is crucial for maximizing the benefits of polyurethane coatings. This knowledge leads to better decisions in production and application."
Mechanisms of Application
The mechanisms of application for polyurethane fabric coating spray play a critical role in ensuring that the end product meets the desired performance characteristics. In this section, we will look into the various steps involved in applying the spray, emphasizing the importance of each stage. A proper application process can enhance durability, ensure optimal adhesion, and improve the overall functionality of the coating.
Surface Preparation
Surface preparation is a foundational step in the coating application process. It involves cleaning and treating the surface to be coated to ensure good adhesion of the polyurethane spray. If the surface is not properly prepped, the coating may fail to adhere correctly, which can lead to peeling or flaking over time.
Several key techniques are used for surface preparation:
- Cleaning: Remove any dirt, grease, dust, and old coatings that could affect adhesion. Common cleaning agents include solvents or detergents.
- Sanding: Lightly sand the surface to create a rough texture. This texture improves mechanical bonding of the coating.
- Priming: In some cases, applying a primer can enhance adhesion. This step is especially important for surfaces that may not bond well with polyurethane, such as certain types of plastics.
Attention to detail during surface preparation can lead to a significant increase in performance and longevity of the coat. A well-prepared surface provides a clean and rough enough profile for the coating to adhere efficiently, ensuring a more durable finish.
Spray Techniques
Next, the application method itself is crucial. Spray techniques can vary, and the choice depends on the specific application and the type of equipment used. Proper technique impacts the uniformity and thickness of the coating.
Key aspects of effective spray techniques include:
- Consistency in Distance: Maintaining a consistent distance between the spray nozzle and surface helps achieve an even coat. An ideal distance is usually between 6 to 12 inches.
- Overlap: Overlapping each stroke by 50% prevents areas of uneven coverage. This ensures uniform application and reduces the chances of drips or runs.
- Speed and Movement: Smooth, steady strokes result in an even distribution. Quick movements can lead to thin spots, while slow motion can oversaturate certain areas.
Understanding these spraying techniques allows for a refined application, which is essential for achieving optimal performance and aesthetic qualities in the finished product.
Drying and Curing Processes
Finally, the drying and curing processes are vital for the success of the coating application. After applying the polyurethane fabric coating spray, the coating needs time to dry and cure properly. This step can significantly affect the durability and performance of the coating.
- Drying Time: This is usually the first phase, where the solvent evaporates. Factors like temperature, humidity, and air circulation influence drying time, which can vary depending on product specifications.
- Curing Time: Different from drying, curing is the chemical process where the coating achieves its final hardness and adhesion. Curing can take several hours to days, and conditions need to be controlled for optimal results.
- Post-Curing Treatments: In some advanced applications, additional heat or UV exposure can be employed to expedite curing and enhance final properties.
To conclude, understanding the mechanisms of application is key for those involved in utilizing polyurethane fabric coating sprays effectively. Each of these stages contributes to the coating's performance, and thorough consideration at every step is crucial for success.
Applications of Polyurethane Coating
Polyurethane coatings have gained significant traction in various industries due to their diverse applications and beneficial properties. Understanding their role helps in grasping their importance in enhancing both functionality and aesthetic appeal across different sectors. This section delves into three prominent applications of polyurethane coatings: the textile industry, outdoor equipment manufacturing, and medical and protective clothing. Each subsection highlights the unique advantages that these coatings offer and the considerations that come with their use.
Textile Industry
In the textile industry, polyurethane fabrics have transformed the way materials are manufactured and treated. These coatings serve multiple purposes, including providing water resistance, enhancing durability, and improving overall fabric performance. Manufacturers often apply polyurethane finishes to garments such as jackets, sportswear, and functional apparel, where longevity and resistance to the elements are crucial.
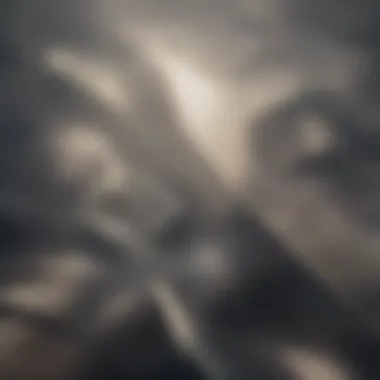
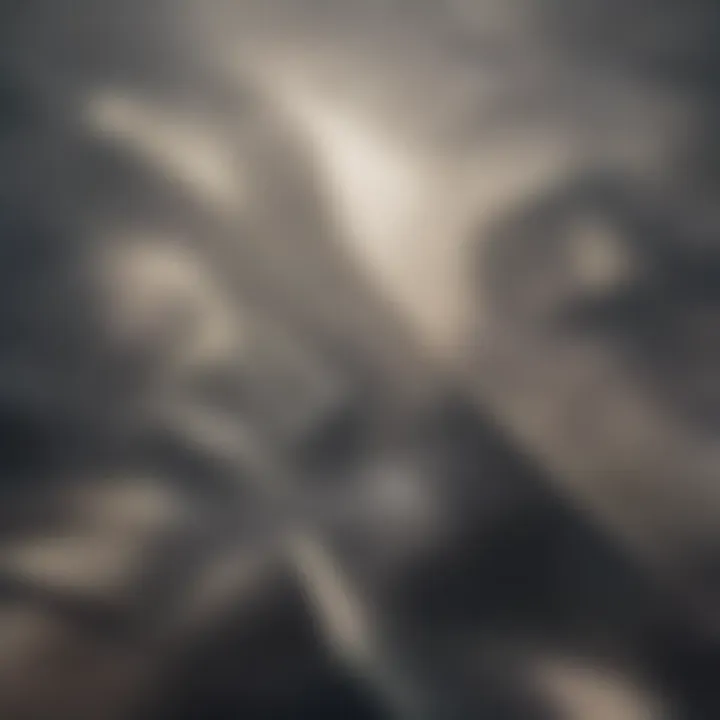
The permeability and elasticity of polyurethane also play crucial roles in textile functionality. They contribute to breathability while ensuring that the fabric remains soft and comfortable against the skin. Many sports brands capitalize on these characteristics, allowing athletes to perform optimally under varying weather conditions. Additionally, the variety of textures available with polyurethane coatings allows for endless design possibilities, further enriching the market with innovative products.
Outdoor Equipment Manufacturing
The outdoor equipment industry heavily relies on the properties of polyurethane coatings for durability and weather resistance. Items such as tents, backpacks, and outdoor apparel often utilize these coatings to withstand harsh environmental conditions. Product longevity is vital in this segment, as consumers expect gear that lasts long term and performs creditably.
Columbia's tents and North Face backpacks are examples of products benefiting from this technology. The addition of polyurethane dramatically increases their ability to repel water, resist abrasion, and maintain structural integrity. Given the ever-increasing awareness around environmental sustainability, many companies are also exploring eco-friendlier options within polyurethane manufacturing, adding another layer of attractiveness for environmentally conscious consumers.
Medical and Protective Clothing
Polyurethane coatings are also essential in the field of medical and protective clothing. The versatility of these coatings allows protective garments to be lightweight while still providing robust safety features, such as chemical resistance and antimicrobial properties. This is especially important in environments where exposure to hazardous substances is a concern.
For instance, healthcare professionals rely on polyurethane-coated uniforms that not only offer protection but are also easy to clean and maintain. The softness of the fabric, combined with its protective qualities, ensures comfort during long working hours. Furthermore, the transparency of some coatings allows for aesthetic choices without sacrificing functionality.
In summary, polyurethane coatings find extensive applications in sectors where performance, durability, and safety are crucial. Their unique characteristics enhance both product function and user experience, making them indispensable in contemporary manufacturing.
Performance Characteristics
The performance characteristics of polyurethane fabric coating spray are crucial for assessing its functionality across various applications. These characteristics help in understanding how well the coating performs in terms of durability, resistance, and feel. It is essential for industry professionals and product users to recognize these key traits, as they directly influence the material's effectiveness and suitability for specific uses.
Durability and Longevity
Durability is a primary factor when considering any type of fabric coating. Polyurethane coatings are known for their strong adhesion properties which contribute significantly to their longevity. Once cured, the coating forms a robust layer that protects the underlying fabric from wear and tear. This makes it ideal for outdoor gear, such as tents and jackets, which must withstand harsh environmental conditions.
Additionally, the longevity of polyurethane coatings is enhanced by their resistance to UV radiation and water damage. Unlike some alternatives, polyurethane does not easily degrade under sunlight, which is a common cause of material failure. Users can expect these coatings to maintain their integrity and appearance through multiple uses and exposures, offering more value over time compared to less durable options.
Resistance Properties
Resistance properties encompass a range of attributes, making polyurethane coatings a preferred choice in various contexts. They are particularly effective against moisture, chemicals, and abrasions. The water-resistant nature of polyurethane prevents water from soaking into the fabric, which helps to maintain the comfort and functionality of outdoor wear.
On top of that, the chemical resistance is significant for applications in environments that involve exposure to oils, solvents, and cleaning agents. This ensures that the coated fabric remains intact and functional even when subjected to challenging conditions. Moreover, the abrasion resistance is vital for items that face regular friction, like work gear, ensuring the materials can last without significant damage.
Feel and Aesthetic Properties
In addition to functional performance, the feel and aesthetic properties of polyurethane coatings matter. Users often seek materials that not only perform well but also provide a pleasant tactile experience. The coating can be engineered to maintain the softness and flexibility of the fabric, which enhances comfort, especially in clothing applications.
From an aesthetic viewpoint, polyurethane coatings can be produced in various finishes and colors, allowing for customization. This adaptability meets consumer preferences in different markets, from fashion to industrial applications. Furthermore, coatings can impart a sleek appearance, appealing to users looking for both practicality and style in their fabric products.
To summarize, the performance characteristics of polyurethane fabric coating spray—its durability, resistance properties, and overall feel—play a vital role in the decision-making process for end-users and manufacturers. Understanding these factors can guide informed choices regarding the use of this versatile material.
Environmental Considerations
Environmental considerations are vital when discussing polyurethane fabric coating spray. As industries adopt this technology, understanding its environmental impact emerges as a key topic. The focus lies not only on the benefits provided by these coatings but also on the implications they carry in terms of sustainability.
The application of polyurethane coatings can provide protection to materials, prolonging their lifecycle. However, the effects on the environment cannot be overlooked. Developing a balanced perspective involves acknowledging both the advantages of enhanced durability and the potential ecological repercussions.
Biodegradability and Recycling Issues
One significant aspect of environmental impact is the biodegradability of polyurethane coatings. These materials are often criticized for their slow decomposition rates, leading to worries about landfills filling up with non-biodegradable substances. Unlike natural materials that break down relatively quickly, polyurethane can persist in the environment for many years, posing long-term disposal issues.
To address this dilemma, several companies are exploring formulations that include biodegradable components. These alternatives may reduce environmental harm by enabling easier decomposition in waste management systems.
The recycling of polyurethane coatings also presents challenges. Unlike metals or glass, which are typically recycled with established protocols, the recycling processes for polyurethane remain underdeveloped. This creates barriers for effectively reusing these materials after their primary function has ended. An increase in recycling infrastructure and initiatives would be essential to improve the sustainability of polyurethane applications.
Toxicity Concerns
Toxicity is another critical environmental consideration when using polyurethane fabric coating spray. The chemical composition of certain polyurethane materials can release volatile organic compounds (VOCs) during application and curing. These emissions can contribute to air pollution and might cause health risks among workers and end users.
Regulatory agencies emphasize the need for materials with lower VOC content. The adoption of water-based options has gained traction in recent years due to their reduced toxicity levels. Also, ensuring safe handling and application minimizes exposure to harmful substances.
It is crucial for industries to prioritize the use of safer formulations and to follow guidelines for proper use. This emphasizes the importance of staying informed about the risks associated with different polyurethane coatings.
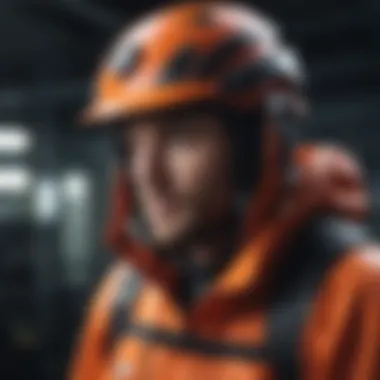
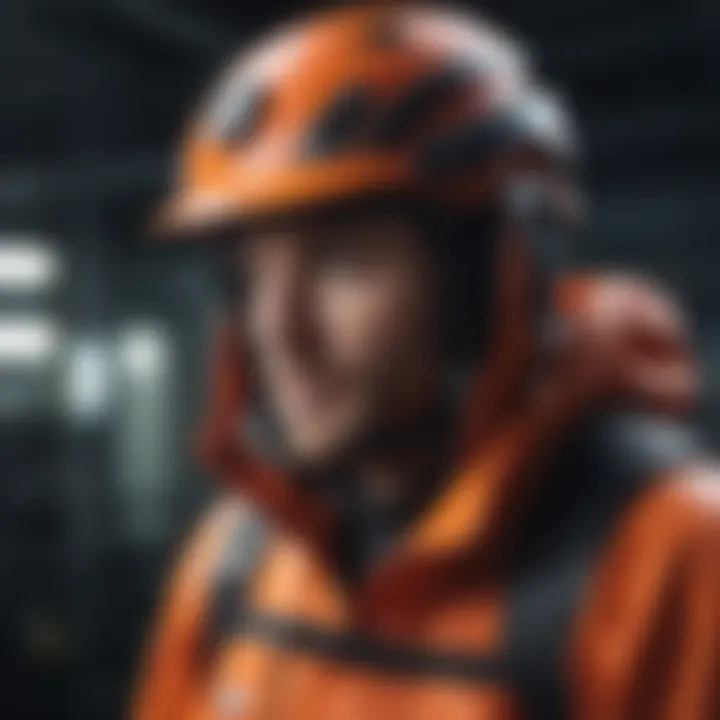
Understanding the environmental considerations surrounding polyurethane coatings ensures that their benefits are not overshadowed by potential negative impacts.
By fostering dialogue around these issues, stakeholders can motivate progress towards more sustainable practices in the employing of polyurethane fabric coating spray. This ensures that the needs of both industry and environment can be reasonably balanced.
Health and Safety Precautions
Understanding the health and safety precautions when working with polyurethane fabric coating spray is crucial. These materials can pose risks if not handled properly. Knowing how to mitigate these hazards not only ensures the safety of individuals using the spray but also enhances the overall effectiveness of the application process.
Material Safety Data Sheets (MSDS)
Material Safety Data Sheets, or MSDS, offer vital information regarding the properties of polyurethane coatings. These sheets provide details on the chemical composition, potential health effects, and necessary precautions. Familiarity with MSDS helps users to:
- Identify Hazards: The MSDS outlines the potential risks associated with exposure to the substances involved, enabling informed decision-making about their use.
- Implement Safety Measures: Each data sheet include recommended personal protective equipment (PPE) and handling procedures that must be followed.
- Understand First Aid Procedures: In the event of exposure or an accident, the MSDS offers guidance on first aid measures.
In short, MSDS is a necessary resource. It protects users by offering essential details about components in the spray, and ensuring safe usage in various environments.
Personal Protective Equipment (PPE)
Personal Protective Equipment is imperative when working with polyurethane coatings. Using appropriate PPE minimizes exposure to harmful chemicals. Key components of effective PPE for this context include:
- Respirators: Protects lungs from inhaling toxic vapors.
- Gloves: Nitrile or latex gloves serve as barriers against skin contact, which can lead to irritation or allergic reactions.
- Goggles: Safety goggles prevent eye contact and safeguard against splashes during application.
- Protective Clothing: Wearing long sleeves and pants made from resistant materials can further minimize direct skin exposure.
The importance of PPE cannot be overstated. It reduces risk and enhances confidence when applying polyurethanes, ensuring a safer working environment.
Always refer back to the MSDS for specific PPE requirements related to the particular polyurethane product you are using.
Market Trends and Future Directions
The polyurethane fabric coating spray industry is experiencing significant changes that reflect broader shifts in technology and consumer expectations. The growing emphasis on sustainability and innovation is reshaping product development. Understanding these trends is crucial for stakeholders, as they navigate a landscape that increasingly prioritizes eco-friendly solutions while still addressing performance demands.
Future directions in this market hinge upon several critical elements. These include the advancement of coating technologies, increasing consumer awareness regarding material sustainability, and evolving preferences for more durable and functional products.
Emerging Innovations in Coating Technologies
Recent developments in coating technologies are transforming how polyurethane fabrics are created and applied. Novel formulations are being designed to improve adhesion, flexibility, and resistance to elements, enhancing the overall performance of coated textiles. Some notable innovations include:
- Waterborne Polyurethane Coatings: These are being favored due to their lower environmental impact compared to solvent-based counterparts. They emit fewer volatile organic compounds (VOCs) during application.
- Nano-coatings: The incorporation of nanotechnology is increasing the durability and water resistance of coatings. These coatings can provide excellent protection without adding significant weight.
- Self-cleaning and Antimicrobial Properties: Emerging technologies include coatings that not only enhance the fabric's longevity but also make it easier to maintain.
These advancements underscore the importance of research in developing polyurethane coatings that meet both performance and sustainability criteria. They allow manufacturers to deliver products that not only satisfy current market demands but also anticipate future needs.
Consumer Preferences and Sustainability Demand
As awareness of environmental issues grows, consumer preferences are increasingly directed toward sustainable products. The demand for eco-friendly polyurethane coatings is rising. Consumers now actively seek transparent information about the materials and processes involved in fabric coating. Some factors driving this preference include:
- Sustainability Certifications: Products with recognized eco-labels or certifications tend to attract more attention and trust.
- Local Sourcing: Consumers show a preference for products sourced locally, which reduces carbon footprint associated with transportation.
- Durability and Lifespan: Buyers are more inclined to invest in higher-quality materials that minimize waste over time, favouring durable polymers.
This shift presents both challenges and opportunities for manufacturers in the polyurethane fabric coating spray market. Companies are encouraged to adapt their practices, focusing on sustainability while still addressing practical performance requirements. The rise of this demand represents a pivotal moment; businesses must consider strategies that combine innovation with environmental responsibility.
Closure and Final Thoughts
In this article, the discussion around polyurethane fabric coating spray highlighted its importance in various sectors, its advantages, and the considerations that come with its usage. This topic is not merely technical; it has real implications for industries reliant on durable and functional materials. The diverse applications, from textiles to protective clothing, showcase how critical this material is in enhancing product longevity and performance.
Polyurethane coatings offer numerous benefits. Their durability, resistance to water, and overall effectiveness make them a favored choice for many manufacturers. Moreover, as sustainability becomes a focal point in product development, the implications of polyurethane coatings on the environment are vital. This article has endeavored to cover both the practical and theoretical aspects of polyurethane application, drawing connections between user needs and industry trends.
"Understanding the intricacies of polyurethane fabric coating is essential for innovation and sustainability in material applications."
Summary of Key Points
- Definition and Understanding: Polyurethane fabric coating sprays are essential for enhancing material properties, providing durability and waterproofing.
- Composition and Mechanics: Understanding the chemical makeup and application techniques is crucial for optimal use.
- Broad Applications: From fashion to medical, various industries benefit significantly from these coatings.
- Performance Evaluation: Evaluating durability, aesthetics, and resistance properties ensures the right choice for specific applications.
- Environmental and Safety Considerations: Awareness of the ecological impact and health risks cannot be overstated.
- Market Trends and Innovations: Keeping abreast of emerging technologies is vital for staying competitive.
Implications for Future Research
Further research in the area of polyurethane fabric coating spray can lead to substantial benefits for both manufacturers and consumers alike. The exploration of biodegradable alternatives is one avenue that requires attention. As industries shed light on sustainability, seeking materials that are not only effective but also environmentally friendly l is crucial. Improving formulations to reduce toxicity while maintaining performance is another area worthy of deeper exploration.
In addition, innovative application methods that increase efficiency and reduce waste could reshape how polyurethane coatings are utilized across various sectors. Future studies may also look into the long-term effects of these coatings on health and the environment, thereby serving as a reference for safer practices in application.
All of these research avenues can contribute to a better understanding of polyurethane coating materials, optimizing their application while being mindful of ecological and health factors.