Understanding Rebar Diameter in Construction
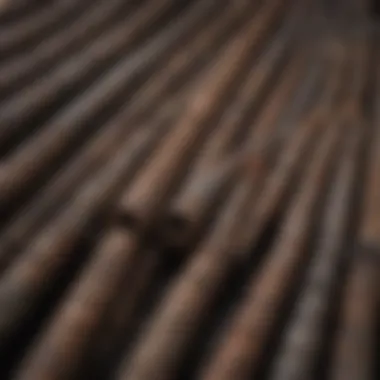
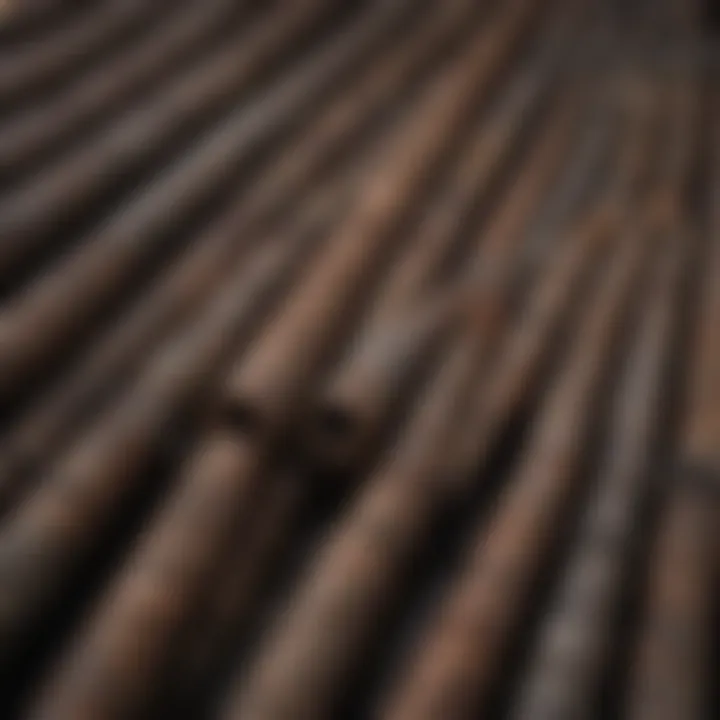
Intro
In construction and engineering, rebar, short for reinforcing bar, plays a pivotal role. It is the backbone of many structural elements, enhancing the strength and durability of concrete structures. Among the various characteristics that influence the performance of rebar, diameter stands out as a fundamental factor. This section unpacks the nuances of rebar diameter, detailing its significance, consequences for load distribution, and its relationship with structural integrity.
Understanding how diameter interacts with various forces can heighten safety measures in construction. When the right rebar diameter is selected, it enhances the load-bearing capacity of the concrete, ensuring that it does not crack or fail under pressure.
This introductory exploration sets the stage for a deeper dive into the specifics of rebar diameter, including its implications for both performance and safety in construction.
Key Concepts
Definition of Primary Terms
Rebar: A steel bar or mesh of steel wires used to reinforce concrete and masonry structures. It comes in various sizes, typically measured in millimeters or gauge.
Diameter: The measurement across the circular section of the rebar, directly influencing its ability to withstand tension and compression forces.
Load Distribution: The manner in which weight and forces are spread across a structure, affecting how evenly stress is transferred.
Related Concepts and Theories
The theory of load-bearing structures is crucial when discussing rebar diameter. As the dimensions of rebar change, so do the mechanics of tension and compression in concrete. For instance, thicker rebar offers greater resistance to cracking under pressure, and typically, the trade-off involves weight and material efficiency.
- Structural Integrity: Refers to the ability of a structure to withstand its intended load without experiencing failure. A well-optimized rebar diameter contributes to this integrity.
- Material Efficiency: Involves using the appropriate size of rebar to avoid over-engineering, which leads to unnecessary material use.
Understanding these concepts establishes a richer context for the subsequent analysis of rebar diameter and its implications in practical applications.
"Selecting the right diameter is not just about strength, it's about optimizing performance and ensuring safety."
Future Directions
Gaps Identified in Current Research
Despite the available knowledge about rebar diameter, there are still questions concerning optimal sizes for emerging materials and innovative construction technologies. Research exploring the performance of new composite materials integrated with rebar, or the impact of environmental factors on different diameters of rebar, could widen our understanding.
Suggestions for Further Studies
Further studies may involve comparing the efficiency of various rebar diameters across different types of concrete mixtures or assessing the long-term durability of structures as a function of rebar diameter. Exploring varying international standards for rebar sizes can also offer insights that are beneficial for global applications.
With these discussions in mind, it is essential to have a well-rounded grasp of rebar diameter's role in construction to make informed choices that prioritize both safety and progression in engineering applications.
Prolusion to Rebar
The world of construction hinges on various materials, and among them, rebar stands tall as a cornerstone. This introduction to rebar outlines its critical role in ensuring that buildings, roads, and bridges hold up against the test of time. From its composition to its uses, understanding rebar is not just an academic exercise but a practical necessity for professionals engaged in construction and civil engineering.
Rebar, or reinforcing bar, is a key component that provides tensile strength to concrete structures. Concrete itself, while strong in compression, lacks the ability to withstand tensile forces. Thus, rebar compensates for this weakness, allowing concrete to perform optimally under various load conditions. Understanding rebar's characteristics isn't merely of academic interest; it's essential for safety and compliance in various projects.
Definition of Rebar
Rebar typically refers to long steel bars that are used in concrete and masonry structures. But it's not just any steel. The bars are usually ribbed or textured to help them bond with concrete and resist slippage. This bond is vital because it helps the rebar distribute loads evenly throughout the structure, minimizing the risks of cracks and failures.
When we dig deeper into the definition, we find that rebar comes in various grades and sizes. These variations enable engineers and architects to select the right type of rebar for specific applications, ranging from residential homes to mega-bridges. For instance, high-strength steel rebar can be close to twice as strong as mild steel, providing enhanced structural support while using less material.
Historical Context
The use of rebar dates back to the 19th century when engineers began looking for ways to augment the structural integrity of concrete. Early adopters of reinforced concrete, such as Joseph Monier in France, demonstrated that embedding iron rods in concrete revolutionized building practices. Monier's design led to the development of modern concrete as we know it today.
As time marched on, different types of rebar were developed, including epoxy-coated rebar for corrosion resistance and stainless steel rebar for areas exposed to harsh environments. Historical events, such as the construction of the Eiffel Tower, showcased how rebar could transform architectural possibilities and create structures that were not only strong but also aesthetic.
"The story of rebar is one of innovation and adaptation, crucial not just in construction but also in how we perceive modern architecture."
From its roots in early engineering practices to contemporary applications, rebar continues to be a subject of research and development. As we move forward in this article, we will explore various aspects of rebar, focusing particularly on diameter, its implications, and how it shapes the structural integrity of the projects it supports.
Rebar Diameter Explained
Understanding the diameter of rebar is not just a technical requirement; it has profound implications for the structural integrity of any project. A well-selected rebar diameter can mean the difference between a building standing tall for decades or crumbling due to inadequate support. Weighing factors like load-bearing capacity, stress distribution, and material efficiency is essential when making diameter choices.
Importance of Diameter
Diameter matters—it’s really as simple as that. The size of the rebar directly correlates to its strength and performance under various conditions. Using the right diameter is crucial for ensuring that a structure can withstand imposed loads, such as those from traffic, weather, and even seismic activity. It’s not just about following the rules or sticking to traditional practices; understanding the engineering principles behind diameter selection opens doors to innovations in design and application.
There are several key benefits tied to selecting an appropriate rebar diameter:
- Load Capacity: A larger diameter often means increased capacity to carry heavier loads. In situations where vehicles or equipment might exert significant force, thicker rebar could be critical.
- Flexibility: In designs that require bending or regional tension, the right diameter can affect how rebar responds. A thicker rebar, for instance, may constrain movement more than a smaller one.
- Cost Efficiency: While larger diameters might seem to offer more strength, they also cost more. Understanding which diameter suffices for specific project demands can minimize expenses while ensuring safety.
Common Diameters Used
In the diverse world of construction, certain rebar diameters are far more prevalent than others. Familiarizing oneself with these common sizes is essential for both novice and seasoned practitioners.
Here are some widely used rebar diameters:
- #3 Rebar (10 mm): Commonly used for light applications, like residential concrete slabs.
- #4 Rebar (12 mm): Often found in sidewalks, driveways, and smaller structural components.
- #5 Rebar (16 mm): A favorite in medium-sized structures, often employed in beams or floor slabs due to its strength.
- #6 Rebar (20 mm): Common in high-load conditions, including roadways and large commercial buildings.
This isn’t a comprehensive list, as diameters can range from tiny #1 (6 mm) for specialty uses to significantly thicker bars like #11 (35 mm) for critical tension applications. The choice of diameter often reflects the specific engineering requirements of each project. Careful consideration must be given to environmental challenges, load expectations, and regional building codes when determining which diameter fits best.
Understanding these aspects of rebar diameter is key to successful project outcomes, ensuring not just compliance, but excellence in engineering design.
Material Properties and Their Impact
Understanding the material properties of rebar is fundamental to grasping its overall effectiveness in construction. Rebar serves not just as a supplementary reinforcement, but as a critical element that directly influences structural performance and longevity. The right material choices can enhance durability and resistance to various environmental stresses and loads. This section explores the intricate relationship between material composition and strength metrics, providing robust insights into how these properties affect their application in construction.
Material Composition
The composition of rebar primarily encompasses the blend of materials used to produce it. Commonly, this includes steel—often enhanced with additives to bolster certain attributes such as flexibility, tensile strength, and resistance to corrosion. For example, many manufacturers utilize recycled steel, attracting commendation for sustainability measures that can also tap into cost savings.
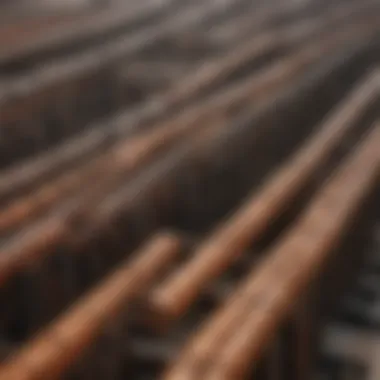
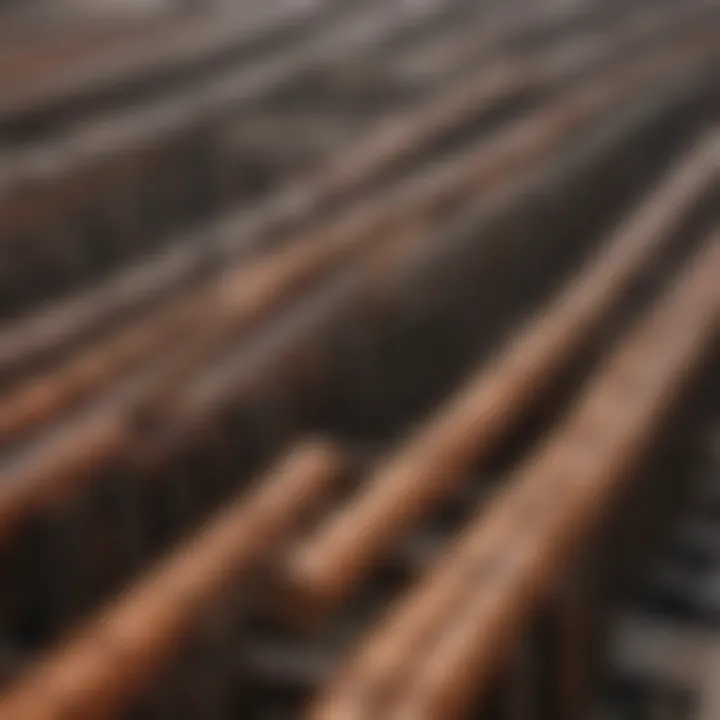
Additionally, the varying grades of steel are significant when talking about rebar. For instance, standard steel bars (like Grade 40 and Grade 60, indicating the yield strength in ksi) form the backbone of most rebar applications. However, as construction technology evolves, we observe an ongoing trend toward alternative materials such as fiberglass or epoxy-coated bars that cater to specific environmental conditions, such as areas with high salt exposure, where traditional steel might rust rapidly.
Here’s a glimpse of typical compositions:
- Carbon Steel: Predominantly used due to its excellent strength-to-weight ratio.
- Epoxy-Coated Steel: Provides protection against corrosion, ideal for harsh weather.
- Glass Fiber Reinforced Polymer (GFRP): Lightweight and highly resistant to chemical attack, useful in special settings.
Understanding these composite materials can greatly influence design decisions, especially in projects where environmental conditions pose significant challenges. Selecting the right material composition can mean the difference between a sound structure and one plagued with maintenance issues from the get-go.
Strength Metrics
Strength metrics play a crucial role in determining appropriate rebar usage. Essentially, this includes evaluating yield strength, tensile strength, and modulus of elasticity. In simple terms, yield strength refers to the load at which rebar begins to deform permanently. For instance, Grade 60 rebar demonstrates a yield strength of 60,000 psi, which is generally considered adequate for medium-traffic structures.
Furthermore, the tensile strength—referring to the maximum load the rebar can withstand before breaking—factors prominently into load analysis. The tensile strength of commonly used rebar grades can vary:
- Grade 40: Approximately 40,000 psi.
- Grade 60: Roughly 60,000 psi.
- Grade 80: Reaching up to 80,000 psi, often used in specialized applications.
Lastly, the modulus of elasticity gives insight into how much a rebar will deform under load. This is vital for engineers to assess how much flexibility and stiffness a structure may require. Incorporating these strength metrics allows professionals to perform precise calculations, thereby optimizing the rebar selection process based on specific project demands.
"The efficacy of rebar extends beyond simple utility; its material properties dictate the resilience and safety of any constructed entity."
Understanding these aspects draws clearer connections between theoretical principles and practical applications, enabling designers and contractors to strike a fine balance between safety and performance.
Loading and Stress Considerations
Understanding loading and stress considerations is pivotal in the realm of rebar applications. This section dives deeper into how these factors not only affect the integrity of a structure but also guide the decision-making process when selecting rebar diameters and types. In construction, anticipating loads and stresses can mean the difference between a sturdy edifice and one that may face critical failure. The emphasis here is on understanding how varying loads interact with rebar to ensure safety and durability.
Types of Loads
When it comes to construction, loads can be categorized into several types. Each of these plays a significant role in determining how rebar should be used within structures. Here’s a brief overview:
- Dead Loads: These are the permanent static forces acting on the building, such as the weight of the materials used in the construction itself. It’s like trying to balance a heavy box on top of a table; should the table be weak, the box might bring the whole structure down eventually.
- Live Loads: These loads vary over time, such as occupants, furniture, and equipment movement. They change constantly, much like how the crowd in a stadium shifts as fans come and go.
- Environmental Loads: This includes forces from nature, such as wind, snow, and earthquakes. Think about a tree bending in a storm; it’s necessary for the tree to have strong roots, just like buildings require reliable rebar to withstand such forces.
Understanding these load types is crucial, as different diameters may be better suited to handle specific kinds of stress. An improper choice can lead to issues like cracking or eventual structural collapse.
Stress Distribution Analysis
The behavior of a concrete structure under load isn’t straightforward. Stress distribution plays a key role in how even the strongest materials perform. Stress doesn’t just go one way – it travels and distributes along the rebar, which can be understood through several vital elements.
The following points outline the core aspects involved in stress distribution:
- Shear Stress: Happens when forces are applied directly to a material's cross-sectional area. For instance, a properly sized rebar divides the load evenly across its length. If the rebar is too small, it could buckle under pressure, much akin to the way a thin straw bends when you try to suck through it harder than usual.
- Bending Moments: These occur when loads are applied off-center. Here, the diameter of the rebar becomes crucial; a thicker rebar can ideally counteract greater bending moments. Structures like bridges hinge on this understanding— thinned rebar can create vulnerabilities that lead to greater anxieties.
"The right diameter isn’t just about strength; it’s about ensuring every inch of rebar does its part under load."
- Critical Stress Points: Identifying where maximum stress occurs in a structure allows engineers to adjust the rebar diameter to optimize safety. Much like a football team looks at its weak spots before a game, a structural engineer ensures that no point is overlooked.
By analyzing these stress distributions, one can make well-informed decisions about which diameter of rebar to use in various scenarios, ensuring that structures can weather the tests of time and load without crumbling under pressure.
Selection Criteria for Rebar Diameter
The selection criteria for rebar diameter can be a game changer in any construction project. Choosing the right diameter isn’t just about the numbers on a spec sheet; it influences overall structural integrity, load capacity, and even the long-term durability of the project. Essentially, the diameter of rebar you choose plays a crucial role in how successfully the whole structure can withstand the everyday forces it faces.
Getting the diameter right means balancing between safety and cost-efficiency. With the wrong decisions, you risk overspending or, worse, endangering future occupants. To this end, it’s vital to assess several factors that will guide you in making informed choices.
Project Specifications
When starting a construction project, one of the key documents you’ll refer to is the project specifications. Each project comes with unique demands based on its design, purpose, and anticipated loads. For instance:
- Load Requirements: A high-rise building needing to carry heavy loads may require larger diameter bars to ensure safety and compliance with safety regulations.
- Environmental Considerations: Structures in coastal areas may need thicker rebar with protective coatings to combat corrosion from saltwater.
- Design Specifications: Architectural elements, including beams, slabs, and columns, dictate the size and spacing of rebar to efficiently handle tension and compression forces.
In simpler terms, aligning the selection of rebar diameter with project specifications is like tailoring a suit; it must fit just right to perform as expected.
Environmental Factors
Environmental conditions can significantly influence the choice of rebar diameter. Different climates, soil types, and other external factors may necessitate varied approaches:
- Weather Conditions: Locations prone to extreme weather events might require thicker rebar to withstand stress from high winds or snowfall.
- Soil Quality: Certain soils, like expansive clays, can exert pressure that affects the structural load; thus, larger diameters may be prudent.
- Exposure Risks: In seismic zones, you would want to ensure ample flexibility and strength, which could lead to opting for bigger rebar to help absorb shock waves from earthquakes.
Adapting to such environmental conditions is essential for maximizing safety and longevity of the structure, ensuring that it won’t just shine on opening day but will hold steadfast as time marches on.
"Selecting the correct rebar diameter is not merely a choice; it's a strategic decision that can affect the entire lifecycle of your project."
In short, both project specifications and environmental factors serve as your compass, guiding you through the critical landscape of rebar diameter selection. Tread carefully and consult as needed; your diligence pays off in the end.
Regulatory Standards and Guidelines
The world of construction and engineering is rife with rules and regulations that aim to ensure safety and quality in structures. The Regulatory Standards and Guidelines serve as vital benchmarks in the realm of rebar usage, influencing not only how materials are selected but also the methods of implementation. These guidelines dictate the expectations for performance, longevity, and safety in building practices. It is imperative for professionals in the field to grasp these components as they directly impact the dependability and welfare of structures built upon them.
International Standards
At the international level, various organizations have established standards that govern the use of rebar in construction. The most notable among these is the International Organization for Standardization (ISO). The standards set forth by ISO provide a framework that helps ensure consistency and quality among materials. This includes considerations for strength, ductility, and corrosion resistance, which are essential for any project.
When adhering to international standards, companies benefit from:
- Enhanced Reliability: Structures built following these standards tend to have a longer lifespan, as they’re reinforced with material designed for optimum performance.
- Global Acceptance: Compliance with international standards can simplify the project approval process across borders. For companies working internationally, this can significantly reduce time-to-market and complication in logistics.
- Safety Assurance: Rigorous testing and certification processes help in identifying any deficiencies upfront, thus preventing potential failures before they manifest during construction.
Using the ISO 10070 standard, for instance, various grades and types of rebar are classified according to their mechanical properties. This ensures that only the most suitable materials are selected for particular environments or structural requirements.
Local Building Codes
While international guidelines provide a broad scope, local building codes are where the rubber truly meets the road. These codes are often influenced by regional considerations such as climate, geology, and the specific demands of local construction practices. They specify everything from the type and grade of rebar that must be used to the exact spacing and placement requirements.
The role of local building codes includes:
- Tailored Solutions: Local codes adapt the overarching standards to better suit the unique challenges faced by a given area. For example, when dealing with seismic zones, codes may require a different approach to rebar diameter and placement, ensuring structures can withstand earthquakes.
- Compliance Enforcement: These codes are enforced by local authorities, ensuring that builders adhere to safety protocols. Non-compliance can lead to fines, project delays, or even complete halting of operations, making adherence essential.
- Public Trust: By complying with these codes, construction entities build a reputation for safety and reliability. Clients are more likely to trust contractors who respect local regulations, fostering business growth and stability.
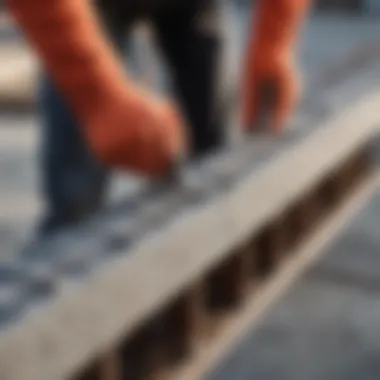
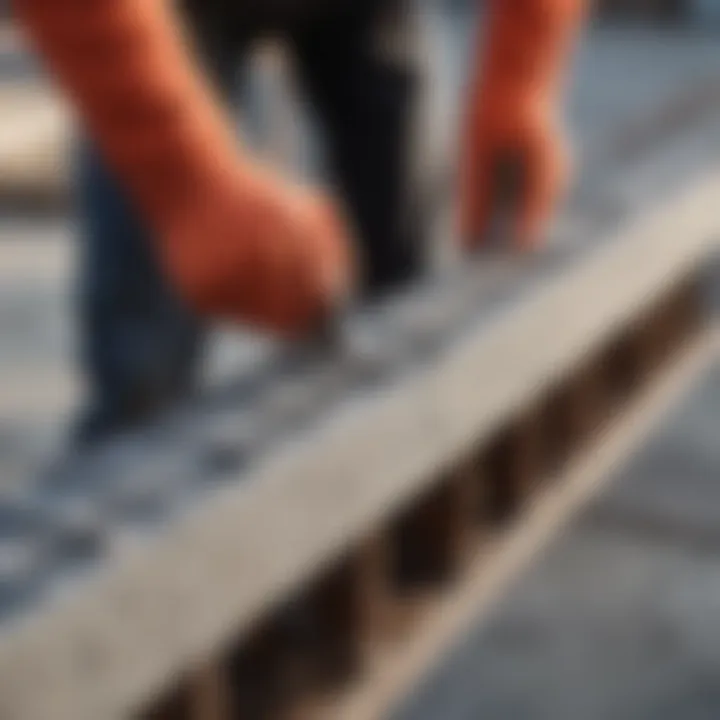
"When it comes to construction, cutting corners can lead to catastrophic outcomes. Standards and guidelines are not just a suggestion—they're our first line of defense against failure."
Ultimately, the adherence to Regulatory Standards and Guidelines is vital in shaping the future of rebar usage in construction. They dictate not only the materials utilized but also the methods employed, balancing safety, durability, and functionality. Understanding these frameworks equips professionals and students alike with the knowledge to navigate and excel in the intricate world of structural engineering.
Comparative Analysis of Rebar Types
When it comes to rebar in construction, a meticulous comparative analysis of rebar types becomes vital. Understanding the differences between materials and how they interact with specific project requirements can greatly affect a structure's durability, cost-effectiveness, and overall performance. The choice of rebar isn't merely academic; it has practical ramifications that can determine the success or failure of a construction project.
Steel vs. Alternative Materials
Steel has long been the traditional go-to for rebar in construction. This metal boasts an impressive strength-to-weight ratio, making it ideal for bearing heavy loads. Moreover, steel can resist high temperatures better than many alternatives, which is crucial in fire-prone environments. However, it also has downsides, mainly its susceptibility to rust when exposed to moisture without proper treatment.
In contrast, materials such as fiberglass reinforced polymer (FRP) and epoxy-coated bars have begun to carve out their niche in more specialized applications. For instance, FRP is non-corrosive and thus excels in projects near bodies of water or in coastal areas where salt can pose a threat to the integrity of steel. However, while it can withstand challenging conditions, FRP often falls short in terms of tensile strength compared to its steel counterpart.
Here are a few considerations when contrasting these materials:
- Strength: Steel generally wins for load-bearing applications.
- Corrosion Resistance: FRP and epoxy-coated rebar are better suited for environments where corrosion is a concern.
- Cost: Steel tends to be more affordable than alternative materials, although long-term savings may be realized with corrosion-resistant options due to lower maintenance costs.
- Weight: While both steel and FRP are manageable, FRP is much lighter, making it easier to handle and transport.
Cost Implications
The financial aspect of choosing rebar types can have rippling effects across project budgeting. Steel is often the most economical choice upfront, but lifecycle costs are important too. Corrosion can significantly shorten the lifespan of steel rebar, leading to expensive repairs and potential replacements. If you consider the total cost of ownership, alternatives like epoxy-coated bars or even FRP might present longer-term savings despite a higher initial investment.
Key Cost Considerations:
- Initial Cost: Steel is cheaper, but alternatives require evaluation of long-term expenses.
- Maintenance: Non-corrosive options can lower maintenance and replacement costs.
- Long-Term Stability: Weigh the extended service life of premium materials against their upfront price.
In essence, the choice of rebar type filters down to understanding the specific needs of your project and balancing them against the costs. Getting it right means avoiding a headache down the line, both financially and structurally.
Installation Practices
Installation practices are pivotal in ensuring that rebar performs optimally within concrete structures. The way rebar is handled and placed can significantly impact the structural integrity, load-bearing capacity, and long-term durability of the construction. Therefore, it is crucial for professionals to understand the protocols and best methods associated with rebar installation.
Handling Techniques
When it comes to handling rebar, a few key techniques stand out that can greatly reduce the risk of damage and ensure safety during installation:
- Use of Proper Gear: Personnel should always wear protective gear, including gloves and steel-toed boots. These ensure safety when working with heavy and sharp steel bars.
- Safe Lifting Practices: It's essential to lift rebar using both hands while keeping the load close to the body. This practice minimizes strain and prevents accidental drops.
- Avoiding Damage During Transit: Rebar should be stacked securely when transported. Loose piles can easily shift, causing damage to the bars or injury to workers.
- Preventing Rust and Corrosion: Handling should be done in a way that minimizes exposure to moisture, dirt, and chemicals that can lead to rust. Storing rebar in a dry place and covering it can help prolong its life.
Implementing these handling techniques not only protects the material but also contributes to a safer working environment.
Placement Methods
Proper placement of rebar within concrete forms is vital. The following points highlight effective strategies for placing rebar:
- Correct Spacing: Following the design specifications for spacing ensures optimal load distribution. Misplacing bars can lead to weak points in the concrete.
- Use of Rebar Ties: Employing ties ensures that rebar stays in position throughout the pouring of concrete. Without ties, rebar might shift, compromising structural integrity.
- Clear Positioning: Keep bars at the specified cover distance from the forms. This prevents issues with corrosion and ensures the rebar does its intended job of enhancing tensile strength.
- Consideration of Temperature: It's also important to consider temperature changes that may expand or contract rebar. Adequate spacing allows for this movement without causing damage to the concrete.
In summary, the integrity of a concrete structure heavily relies on diligent installation practices. Understanding the right handling techniques and placement methods is crucial for achieving safe and effective results.
Common Mistakes in Rebar Usage
In the world of construction, even a small error can lead to significant consequences. When it comes to rebar, understanding the common mistakes can save time, money, and ensure structural integrity. Some people might think that rebar is straightforward, but its diameter plays a crucial role in the strength and performance of any project. Recognizing potential pitfalls helps professionals make informed decisions. Let's take a closer look at two major areas where mistakes often arise: oversizing and undersizing, and misinterpretation of specifications.
Oversizing and Undersizing
When selecting rebar, diameters often get misjudged. Oversizing can sound like a reliable approach—after all, a bigger piece should offer better support, right? Wrong. Using rebar that is too large for the project can lead to issues such as increased costs and complicated placement. Plus, larger diameters often add unnecessary weight to the structure, potentially resulting in the need for more robust support systems.
On the other end of the spectrum, undersizing rebar can present an even more serious risk. Insufficiently sized rebar may not withstand the intended loads, leading to structural failure over time. It’s a bit like trying to build a bridge with toothpicks; it might look good on the surface, but it sure won't hold up under pressure.
"Choosing the right diameter is not just a matter of preference; it’s about understanding the loads and stresses that will be at play in the structure."
It’s essential to remember that the right diameter should align with project specifications and engineering calculations. A good rule of thumb is to consult with structural engineers who can provide expertise and insight tailored to specific project needs.
Misinterpretation of Specifications
Another prevalent mistake in rebar usage stems from misunderstanding specifications. Project documents may list various requirements, but how often does one pause to decipher them thoroughly? It’s not just about the numbers. Misinterpretations can lead to selecting the wrong diameter, which can have severe repercussions.
Here’s where the fine print matters. For instance, if specifications omit details on load types or stress distributions, assumptions might be made that steer one in a wrong direction. Misreading these crucial elements can lead to safety issues that shouldn't be taken lightly. Individuals must take specifications seriously, always seeking clarification when in doubt.
When dealing with specifications:
- Always double-check numbers.
- Consult involved parties like engineers or architects to ensure full understanding.
- Pay attention to site-specific requirements, as regulations can vary by region.
Doing thorough homework avoids the trap of costly mistakes that could compromise not just the project but also the safety of future users.
Emerging Trends in Rebar Technology
The construction industry is witnessing remarkable advancements in technology, and rebar is no exception. This section delves into the emerging trends in rebar technology that are shaping the future of construction. Understanding these trends is vital for engineers, architects, and construction managers to stay ahead of the game. The benefits of embracing these innovations include enhanced performance, better sustainability, and improved safety.
Smart Rebar Innovations
Innovations in smart rebar technology have taken center stage. Smart rebar goes beyond the traditional steel reinforcement by integrating sensors that can monitor various factors inside the concrete. For instance, smart rebar can track strain, temperature, and moisture levels, providing real-time data that enhances the decision-making process during construction.
Some advantages of using smart rebar include:
- Improved Structural Integrity: Real-time monitoring helps identify potential issues before they escalate. This ensures that any structural weaknesses are addressed promptly, minimizing risks.
- Data-Driven Decisions: With continuous monitoring, construction teams can make informed decisions rather than relying on assumptions. This aspect is particularly useful when dealing with complex projects.
- Long-Term Maintenance: Since smart rebar provides ongoing data even after the structure is complete, it aids in long-term maintenance and upfront repairs, potentially saving costs in the long run.
However, integrating smart technology into rebar does come with considerations, such as additional installation costs and the need for familiarity with data analysis tools among the workforce. Nevertheless, the potential gains often outweigh these hurdles.
Sustainability Practices
As the world leans more towards sustainable practices, rebar technology is evolving to meet these demands. Sustainable rebar not only reduces the environmental impact of construction but also helps in achieving green building certifications.
Some notable practices include:
- Recycled Materials: The use of recycled steel in manufacturing rebar preserves natural resources and saves energy. Using scrap metal to produce rebar can reduce the carbon footprint significantly.
- Low Carbon Footprint Products: Emerging brands are developing rebar that is produced with lower emissions during its lifecycle. This technology is gaining traction as companies strive to align with global sustainability goals.
- Alternative Materials: Research into materials like fiber-reinforced polymers (FRP) is on the rise. These materials offer excellent corrosion resistance and are lighter than traditional steel rebars, adding another dimension to sustainable building practices.
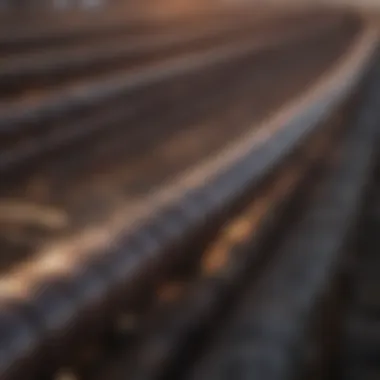
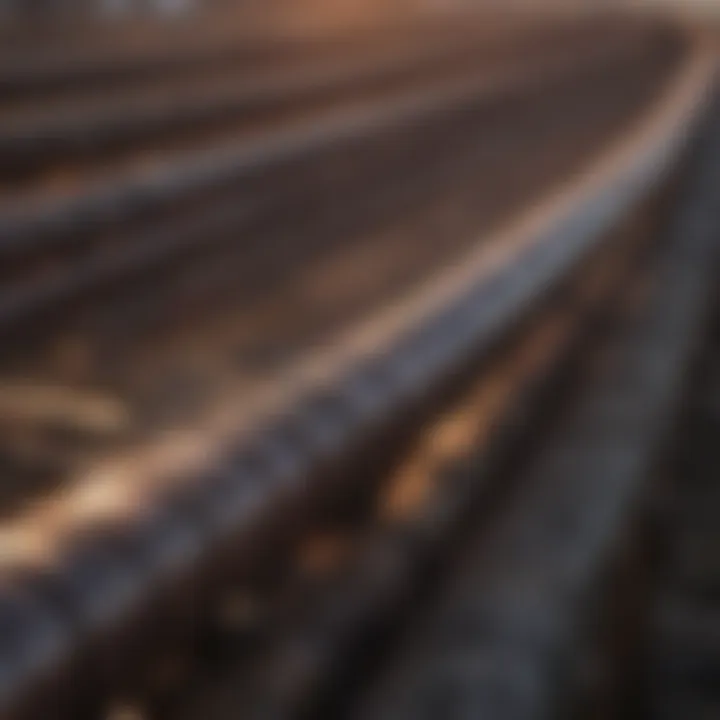
These sustainability practices align with a broader vision of reducing environmental impact and enhancing long-term performance.
"The future of rebar technology hinges on integrating advanced materials and techniques that align with sustainability and climate goals."
Case Studies
Case studies are more than just narratives; they serve as crucial evidence in understanding the complex dynamic of rebar diameter selection. In the construction world, they bridge the gap between theory and practical application. By examining real-world examples, we can observe how different diameters perform under varied conditions, the effects on structural integrity, and how they align with specific project goals. Evaluating case studies enables us to glean valuable insights into best practices while also identifying pitfalls.
Successful Projects Utilizing Specific Diameters
Successful projects often highlight the careful balance between rebar diameter and the structural demands placed upon it. For instance, the Golden Gate Bridge employed a specific rebar size that allowed it to withstand not just its own weight but the additional stresses from heavy traffic and environmental factors. Engineers identified a diameter that maximized strength while keeping costs manageable. Ultimately, this case underscores the importance of selecting the right size:
- Load Capacity: Larger diameters generally offer increased strength, making them suitable for high-load applications. However, it's essential to ensure the diameter aligns with the overall design to avoid excessive material use.
- Project Norms: Some construction projects, like tall skyscrapers, might favor thicker rebar due to the significant vertical loads encountered, illustrating how context influences diameter choice.
These decisions aren't made in a vacuum; they require comprehensive understanding of both the materials and the intended usage.
Lessons Learned from Failures
On the flip side, lessons from failures provide equally important insights. The collapse of the Ronan Point tower in London is a stark reminder of the consequences of improper rebar diameter selection. Investigations revealed that inadequate rebars were used concerning the weight of vertical loads. This incident imparted several lessons:
- Risk of Undersizing: Insufficient rebar diameter can lead to structural weaknesses, making buildings vulnerable to unforeseen stresses. It becomes a lesson in ensuring that the selected diameter is not just compliant with standards but capable of accommodating practical variables.
- Importance of Compliance: Building codes are there for a reason. Adhering to established standards ensures resilience. Failure to do so can lead to catastrophic results.
- Need for Continuous Monitoring: Analyzing the performance of existing structures with varying diameters can inform future designs. Structures should be evaluated regularly to assess the effectiveness of rebar choices.
Case studies, whether they demonstrate success or failure, become catalyst for evolution in design practices. They reflect the collective learning experiences of the engineering community, emphasizing the importance of informed decisions in every aspect of rebar diameter selection.
Best Practices for Rebar Diameter Selection
Choosing the right rebar diameter is critical in construction and engineering projects. The selection process goes beyond mere aesthetics; it impacts safety, longevity, and cost efficiency in a big way. When using rebar, the diameter must match the specific requirements of the project, considering not just load-bearing capacities but also environmental conditions and material interactions. Understanding and implementing best practices in rebar diameter selection can lead to significant advantages, ensuring that structures are built to last and perform as designed.
Consultation with Experts
The world of rebar is complex, and relying solely on personal intuition can lead to errors that might compromise project integrity. Engaging with seasoned professionals who specialize in structural engineering is a wise move. These experts can offer tailored suggestions based on the specific details of your project – from seismic conditions to anticipated loads.
Some key benefits of consulting experts include:
- Optimized Performance: They can assess whether the diameter chosen will handle stress and weight efficiently, thereby enhancing overall structural performance.
- Regulatory Compliance: Experts are well-versed in local building codes and regulations. They can ensure that your project meets all legal requirements, avoiding potential fines or delays.
- Advanced Knowledge: Many professionals keep abreast of innovations in rebar technology and material science. Their insights might lead you to options you weren’t even aware existed.
Tips for Effective Consultation:
- Prepare Questions: List specific concerns to maximize the productivity of meetings.
- Request Case Studies: Understanding how similar projects approached measuring their rebar can provide clarity.
- Follow-Up: Always seek a follow-up session if new issues arise during implementation.
Utilizing Software Tools
In today’s fast-paced construction environment, taking advantage of technology gives any project a substantial edge. Software programs specifically geared toward structural engineering can assist in the selection of the appropriate rebar diameter effectively. These tools not only allow for complex calculations but also save time and boot efficiency.
Some well-known software tools incorporate capabilities like:
- Load Calculations: Estimate how much load the structure will bear under different conditions. This capability helps in determining the right diameter.
- Design Visualization: 3D modeling capabilities can provide visual guidance, ensuring that engineers and contractors are on the same page.
- Scenario Testing: Modeling different configurations helps to predict how various diameters affect the performance of the entire structure under varying conditions.
Recommended Software Tools:
- SAP2000: Known for its versatile modeling capabilities and user-friendly interface.
- Revit: Popular among architects and structural engineers alike for its collaborative tools.
- AutoCAD: While primarily a drafting tool, it includes features that can assist in rebar layout and specification.
Utilizing these resources together promotes a comprehensive approach to rebar diameter selection, ensuring your project stands up to scrutiny and functions reliably for years to come.
In essence, consulting experts and incorporating software tools are vital best practices. They greatly contribute to informed decision-making regarding rebar diameter, helping you to avoid costly mistakes while enhancing structural integrity.
Future Directions in Rebar Research
As we look ahead, the field of rebar research is moving in leaps and bounds, and understanding its future directions is vital not just for engineers, but also for those impacting sustainability and efficiency in construction. The exploration of these avenues opens doors to new methodologies and innovations that promise improved outcomes in structural integrity and performance.
Innovative Materials Research
The quest for innovative materials in rebar research is integral to advancing construction practices. Traditional steel rebar has served us well, but the evolving landscape of materials science suggests that alternatives may provide both strength and sustainability. For instance, researchers are investigating fiber-reinforced polymers and other composite materials that could reduce weight without compromising load-bearing capacity. This could lead to structures that are tougher yet lighter—ideal for overcoming the stressors of natural disasters like earthquakes and floods.
Benefits of exploring new materials include:
- Enhanced Durability: New materials can offer superior resistance to corrosion, bending, and cracking, thus extending the lifespan of structures.
- Sustainability Advantages: From reduced environmental impact due to fewer resources required for production to the possibility of recycling materials more efficiently, the push toward sustainable rebar options is strong.
- Cost-Effectiveness: While the initial investment might be higher, long-term savings due to reduced maintenance and increased lifespan present a compelling case for innovative materials.
Furthermore, the collaboration between material scientists and structural engineers is critical in this area. Enhanced dialogue between these disciplines can ensure that material breakthroughs directly align with engineering capabilities and objectives.
Advancements in Performance Testing
As new materials emerge, the need for rigorous performance testing becomes paramount. The safety and functionality of rebar in structures hinge on our ability to accurately assess how these materials behave under different conditions. Advancements in performance testing methodologies are reshaping how we understand and implement rebar in projects.
Techniques such as large-scale testing, finite element analysis (FEA), and non-destructive evaluation (NDE) are bringing significant improvements to our testing regimens. Each of these methods allows for a detailed examination of how rebar performs in real-world conditions, ensuring that any newly developed material stands up to the rigors of everyday usage.
Key advantages of these advancements include:
- Precision: Improved testing techniques lead to an accurate understanding of stress distribution and failure points, allowing engineers to make more informed choices.
- Reproducibility: As testing methods become standardized, the reliability of data increases, enhancing confidence in material performance claims.
- Speed: With advanced technologies, testing times can be reduced, enabling quicker project timelines without sacrificing safety.
"As engineers and researchers continue to innovate, the future of rebar research promises a paradigm shift that could redefine construction standards and efficiencies."
In summary, the future landscape of rebar research is bright, driven by innovative materials and enhanced testing methodologies. Keeping pace with these advancements will not only influence structural integrity but also elevate the standards of sustainability in construction. Understanding these trends is crucial for anyone invested in safe, effective, and environmentally responsible building practices.
Epilogue
Summary of Insights
Throughout this discussion, we have covered various insights, such as:
- The Connection Between Diameter and Load-Bearing Capacity: Larger diameters generally contribute to greater strength, but this must be balanced with economic considerations.
- Material Composition's Role: The interactions between different materials and their diameters affect overall robustness and durability. Understanding these dynamics is crucial.
- Standards and Regulations: Familiarizing oneself with international standards and local building codes can safeguard against costly mistakes on the job site.
- Best Practices in Selection: Engaging experts and employing analytical software tools can significantly elevate decision-making when it comes to choosing the right diameter for specific projects.
Final Thoughts on Rebar Diameter's Role
Rebar diameter plays a more significant role in construction than many might initially assume. It is intertwined with safety, performance, and cost-effectiveness. When project specifications are developed, considering the diameter alongside other factors is paramount. The right diameter choice can lead to better stress distribution, minimized risk of failure, and enhanced longevity of structures.
Ultimately, as construction practices continue to evolve, staying informed about advancements—including innovative materials and performance testing methods—will remain essential for all stakeholders involved. Keeping abreast of these changes ensures that the lessons learned today can fuel better decisions in future projects.
"Success in construction is built on careful planning and consideration—especially when it comes to selecting the right materials like rebar. Ensuring every detail, including diameter, is accounted for leads to stronger, safer outcomes."
With the insights provided in this article, readers can approach their projects with a newfound understanding of how rebar diameter can profoundly impact overall construction quality.