Understanding Renishaw Probe Codes for Precision Measurement
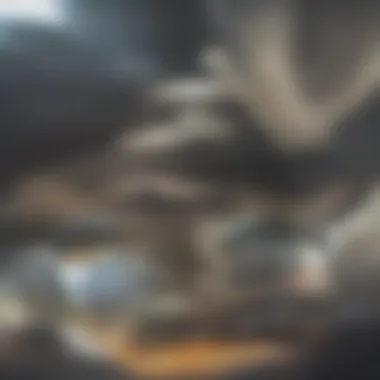
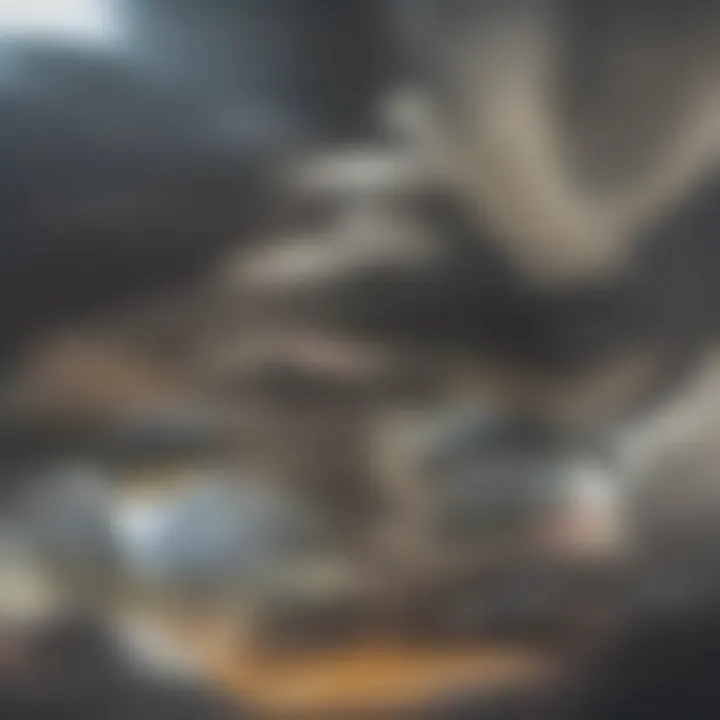
Intro
Key Concepts
Definition of Primary Terms
To grasp Renishaw probe codes, it is crucial to first understand some key terms.
- Probe: A device used to measure physical attributes of workpieces in manufacturing. Renishaw probes are often utilized in CNC machines to gather data accurately.
- Code: In the context of Renishaw technology, codes are sequences that dictate the specific functions and behaviors of the probes. These codes enable the machines to interpret the data from the probes correctly.
- Measurement: Refers to the process of quantifying a physical characteristic. The accuracy and precision of these measurements can significantly impact production quality.
Related Concepts and Theories
Several related concepts underpin the functioning of Renishaw probes.
- Automation: The use of technology to perform tasks with minimal human intervention. Probes play a vital role in automating the measurement process, enhancing operational speed and reliability.
- Precision Engineering: This discipline focuses on creating systems and components with high levels of accuracy. Renishaw probes are integral in achieving the desired precision in various engineering applications.
Understanding these concepts creates a foundation for exploring the intricacies of Renishaw probe codes.
Prologue to Renishaw Probe Codes
Renishaw probe codes are fundamental to the fields of precision measurement and automation, especially in manufacturing. Understanding these codes is not just beneficial; it is essential for anyone involved in quality control, process automation, or CNC machining. This section introduces the importance of Renishaw probe codes, setting the stage for a deeper exploration of their functionality and applications.
The use of probe codes enhances measurement accuracy by providing specific instructions to the machinery. They allow machines to communicate effectively with probing systems, ensuring that the data collected is reliable and actionable.
Definition and Purpose
Renishaw probe codes serve as a standardized language that allows probing systems to perform measuring tasks. These codes tell the machine how to interact with the probe, dictating the type of measurement to be taken and collecting data accordingly. They contribute to the precision and efficiency of manufacturing processes, making them a crucial element in any advanced manufacturing setup. These codes are vital in assuring that parts meet exact specifications, thus minimizing errors.
Historical Background
The development of Renishaw probe codes correlates with advancements in automated manufacturing technologies. Initially, measurement systems were predominantly manual and heavily reliant on operator skill. With the introduction of CNC machines, the need for standardized codes emerged, allowing operators to program and automate complex measurement processes.
Renishaw, a pioneer in probe technology, recognized this demand. The company's early innovations in optical and laser probe technologies prompted the necessity for a coding system that would unify various measurement tasks. Over time, these codes evolved to support a broader range of applications, adapting to the complexities of modern manufacturing. Thus, the establishment of a robust framework for Renishaw probe codes was a significant milestone in the journey toward automation in precision engineering.
This article will further explore how these codes operate, their programming nuances, and their applications across diverse industries. By grasping the essence of Renishaw probe codes, readers can appreciate their significance in enhancing measurement accuracy and industrial efficiency.
Types of Renishaw Probes
Types of Renishaw probes are critical to understanding the broader context of Renishaw probe codes. Each type has unique features and operational benefits that contribute to precision measurement in various applications. By exploring these types, one can better appreciate the significance of coding systems and their impact on efficiency and accuracy in engineering tasks.
Touch Probes
Working Principle
The working principle of touch probes is straightforward yet effective. These probes operate by physically making contact with the workpiece surface to collect measurement data. The key characteristic is their ability to provide immediate feedback regarding position and surface features. This is essential for achieving high levels of accuracy in manufacturing. Touch probes are a popular choice in many industries due to their simplicity and reliability. However, the contact nature can cause minor surface damage to delicate materials, which can be a disadvantage in specific contexts.
Applications
Touch probes find applications mainly in the manufacturing industry. Their robustness makes them effective for quality control tasks. They ensure that components meet specified dimensions with precision. The unique feature of touch probes is their versatility in different environments, including both CNC and manual setups. While these probes excel in validity checks, their real-time data acquisition can slow production if not managed correctly, posing challenges in time-sensitive production lines.
Optical Probes
Characteristics
Optical probes offer a non-contact alternative for measurement tasks. They use light to assess dimensional accuracy, making them suitable for fragile or soft materials. A standout characteristic is their capability of generating high-resolution measurements without physical intrusion. This quality makes optical probes beneficial in scenarios where surface damage must be minimized. However, they can be sensitive to environmental conditions such as dust or temperature variations, which may affect their accuracy.
Benefits
The benefits of optical probes include their high speed and precision. They perform well in applications requiring continual measurement without interruption. This non-contact approach allows for quicker workflows, which is advantageous in fast-paced manufacturing environments. However, reliance on lighting quality and environmental stability can limit their use in some settings. Users must also be trained to interpret optical data correctly, which can present challenges for operators.
Laser Probes
Functionality
Laser probes utilize laser technology to obtain extremely precise measurements. Their functionality is grounded in the principle of triangulation, where the probe detects a laser beam reflected off the target surface. The key characteristic is their speed; laser probes can cover large areas rapidly while delivering accuracy. This makes them advantageous particularly in large-scale industrial applications. However, their performance can vary based on the surface finish of the measured item.
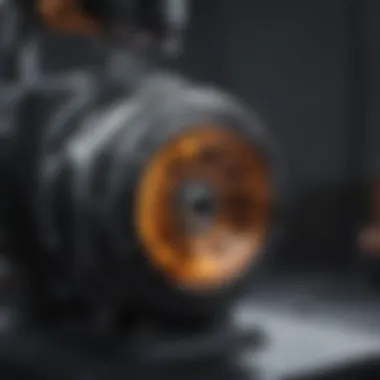
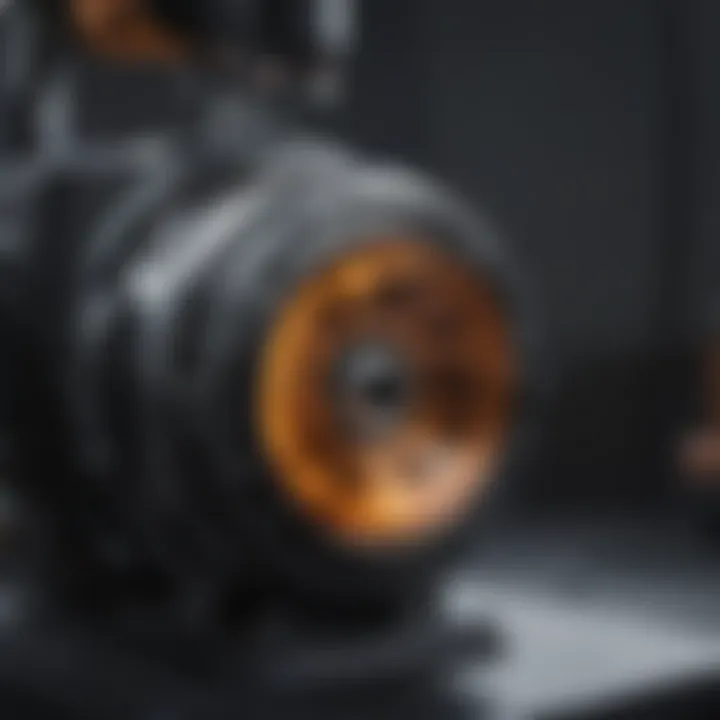
Use Cases
Laser probes are employed in a wide range of applications, from aerospace to automotive industries. Their unique feature is the ability to measure objects from a distance, which enables measurement of components that are otherwise difficult to reach. They excel in tasks requiring high-speed data collection and are particularly valuable in quality assurance protocols. One disadvantage is their susceptibility to accuracy fluctuations based on surface conditions, necessitating careful calibration for consistent results.
Understanding Probe Codes
Renishaw probe codes are essential for the accurate operation of probe systems. They provide instructions for how to measure and navigate a given workspace. Understanding these codes facilitates improved efficiency in manufacturing processes. Technicians and engineers can better leverage these tools, enhancing their operations with precision and automation. Interpreting the structure and nuances of these codes is vital for maximizing the benefit these technologies offer. In this section, we delve deeper into the components that make up these codes and how they function in practice.
Code Structure
Syntax
The syntax of a Renishaw probe code defines its layout and rules. A well-structured syntax allows operators to quickly understand the commands without confusion. It is crucial in ensuring that the probe executes tasks efficiently. Key characteristics of the syntax include its clarity and conciseness. This makes it a popular choice among operators who need to implement commands swiftly and accurately.
One unique feature of the syntax is its standardized format across various probe types. This consistency aids operators in transitioning between different tools without extensive retraining. However, it can also pose disadvantages, such as limitations in customization or adaptability for unique applications.
Components
Components of the probe codes illustrate the individual elements that comprise each command. These components are pivotal for understanding how instructions translate into actions executed by the probes. A key characteristic of the components is that they include parameters that guide measurement processes. Familiarity with these components allows engineers to tailor instructions to specific measurement tasks.
The clarity of these components is beneficial for reducing errors during operation. However, complexity can arise if operators do not fully grasp the relationships and functions of each component. This can lead to misinterpretations and errors during setup or operation.
Commonly Used Codes
Code Examples
Code examples provide a glimpse into the various types of commands typically employed in Renishaw probes. Familiarization with these codes is essential for anyone using the technology. A defining feature of these code examples is their commonality in industrial applications. This characteristic showcases the reliability and consistency of Renishaw systems. For instance, commands for initiating measurements or adjusting probe position are frequently used across different contexts.
An important element of these examples is their role in training new users. Novices can refer to these examples to understand typical operations. However, over-reliance on examples without contextual understanding can result in operational errors.
Usage Context
The usage context of Renishaw probe codes relates to the specific environments or scenarios where they are most applicable. Each context may present unique challenges and requirements that influence how codes are deployed. A significant feature of the usage context is its adaptability across various industries, from automotive to aerospace.
Understanding the usage context enables operators to apply the correct codes effectively. This understanding can help optimize measuring processes and ensures that the right settings are employed for particular materials or instruments. Yet, the varied contexts can also pose risks if operators are not adequately aware of the environments they are working within, potentially leading to errors in measurement or process execution.
"Clarity in probe code structure and components is vital for achieving measurement accuracy and efficiency. Misunderstanding can lead to costly errors in manufacturing processes."
With this understanding of the syntax, components, commonly used codes, and their relevant contexts, operators can navigate the technical landscape of Renishaw probe codes with greater confidence.
Programming Renishaw Probes
Effective programming of Renishaw probes is essential for achieving high precision and efficiency in various applications. This section examines the two main programming languages used: G-Code and Macro Programming. Understanding these languages helps ensure proper communication between the probe and the CNC system, which ultimately determines the success of measurement tasks.
Programming Languages
G-Code
G-Code is a fundamental programming language widely used in CNC machining and probe operations. Renishaw probes utilize G-Code to facilitate instructions for tool movement and measurement tasks. The primary characteristic of G-Code lies in its systematic approach to directing machine activities through recognizable codes. It is a beneficial choice for programming Renishaw probes due to its ability to succinctly convey machine commands, making it efficient for operators to implement.
One of the unique features of G-Code is its versatility. Operators can dictate various parameters, including speed and axes movement, according to specific measurement requirements. G-Code also supports a wide range of functions, which allows for intricate and detailed probe operations. However, the learning curve for G-Code may be steep for beginners, as understanding all the commands requires practice. Nevertheless, its established nature makes it a preferred language in many industrial settings.
Macro Programming
Macro Programming represents a more advanced programming style that allows for automation and customization in operations. This method is particularly advantageous for repetitive tasks commonly performed by Renishaw probes. The core characteristic of Macro Programming is its ability to create complex sequences that enhance operational efficiency, making it a popular choice in environments where precision and repeatability are critical.
Unique to Macro Programming is the use of variables. This feature allows programmers to write more flexible and adaptable codes that can respond to varying measurement tasks. Furthermore, macros can save significant time, as they eliminate the need to re-enter commands for similar measurements. However, the complexity of writing macros can pose a challenge, especially for those less familiar with programming concepts. Overall, when well-implemented, Macro Programming vastly improves workflow and operational capabilities.
Common Programming Commands
Common programming commands serve as the building blocks for successful probe operations. They facilitate various essential tasks, such as setup and measurement. Understanding these commands is crucial for anyone working with Renishaw probes.
Setup Commands
Setup Commands are instrumental in preparing the system for measurement activities. They dictate how the probe should be positioned and calibrated before measurements begin. The key characteristic of Setup Commands is their role in establishing initial conditions, which ensures accurate and repeatable results.
One significant benefit of utilizing Setup Commands is their straightforward implementation. These commands allow operators to quickly configure the system without requiring extensive programming knowledge. Additionally, establishing a proper setup minimizes the risk of user error during subsequent measurement phases. However, inadequate setup can lead to inaccuracies, underlining the importance of attention to detail in this phase.
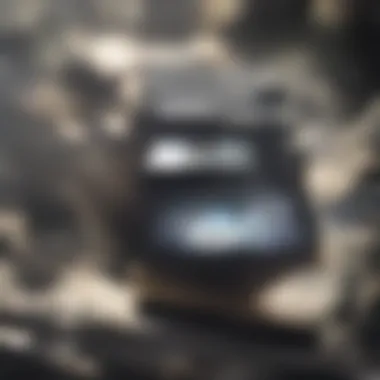
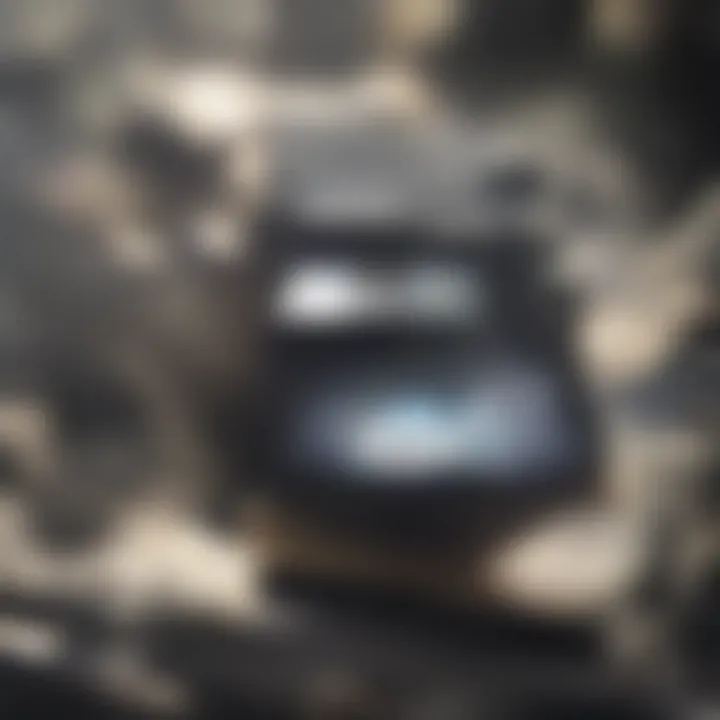
Measurement Commands
Measurement Commands are vital for instructing the probe on how to execute specific measurement tasks. These commands outline the actions the probe must take during the measurement process, ensuring the captured data is accurate and reliable. A key characteristic of Measurement Commands is their specificity. Each command is tailored for various measurements, enhancing the precision of the operation.
Measurement Commands offer significant advantages, such as improving accuracy and efficiency. They allow for streamlined processes, which is critical in time-sensitive environments. Although the complexity of some commands might require training or prior experience, proficient operators can leverage these commands to achieve impressive results. Overall, well-defined Measurement Commands act as a cornerstone for optimal probe performance.
Applications of Renishaw Probe Codes
The applications of Renishaw probe codes are significant across multiple sectors. Their usage is foundational to improving measurement processes and ensuring high precision in various tasks. This section aims to explore how probe codes cater to distinct fields, emphasizing their value and the considerations around them.
Manufacturing Industry
Quality Control
Quality control in manufacturing is intertwined with Renishaw probe codes. The primary aspect of quality control is to ensure products meet defined specifications and standards. Renishaw probes are crucial in capturing accurate measurements during the production process. A key characteristic of quality control is its systematic approach to detecting defects. This systematic process is beneficial as it minimizes waste and enhances efficiency.
The unique feature of using Renishaw probes for quality control is their ability to deliver high accuracy in measurements. The probes can assess dimensions, shapes, and other critical features that must conform to design requirements. Advantages include reduced variability in production and improved product reliability. However, there are challenges, such as the need for trained personnel to interpret results effectively and integrate them into the production line.
Automation
Automation has transformed manufacturing paradigms. Renishaw probe codes play a pivotal role in this transformation by optimizing processes. The aspect of automation focuses on reducing human intervention while maintaining or improving quality. One key characteristic of automation is its reliance on technology to perform repetitive tasks efficiently. This reliance is particularly beneficial to reduce errors and enhance speed in operations.
The unique feature of automation with Renishaw probes is their ability to integrate seamlessly with CNC machines, allowing for real-time adjustments. This capability leads to better production efficiency and consistency. However, the initial setup and ongoing maintenance of automated systems can be costly and require expert knowledge.
Research and Development
Experimental Design
In the realm of research and development, experimental design acts as a blueprint for investigations. Renishaw probes enhance this process by ensuring the accuracy of various measurements crucial for experiments. A specific aspect of experimental design is its focus on structuring methods to derive reliable data. This structure is advantageous as it allows researchers to replicate experiments effectively.
The unique feature of incorporating Renishaw probes is their high precision and ability to capture data in real time. This feature supports rigorous experimental protocols, enhancing the reliability of outcomes. Nevertheless, complexities in probe programming may pose challenges for researchers unfamiliar with the equipment.
Precision Measurement
Precision measurement is a vital component of R&D. It facilitates meticulous analysis of materials, components, and processes. Renishaw probes are essential here, enhancing the accuracy of measurements taken during experiments. One key characteristic of precision measurement is its direct impact on the quality of findings. The high level of precision makes Renishaw probes a preferred tool in academic and industrial research.
A unique feature of precision measurement with Renishaw probes is their ability to function across various scales, from micro to macro levels. This versatility is a significant advantage, providing consistent data across different applications. However, the sophistication of these tools can lead to steep learning curves for users.
Medical Applications
Surgical Instruments
In medical settings, the role of surgical instruments cannot be overstated. Renishaw probes enhance surgical precision significantly. A specific aspect of surgical instruments is their design to operate seamlessly in sterile environments, crucial for patient safety. This quality makes probes integral to many medical procedures.
The unique feature here is the high accuracy of Renishaw measurements, allowing for precise instrument calibration. These benefits lead to improved patient outcomes. However, any reliance on technology also poses risks, such as technical failures that could lead to complications.
Diagnostics
Diagnostics is pivotal in healthcare, providing necessary data for patient assessment. Renishaw probe codes contribute immensely to improving diagnostic accuracy. The emphasis in diagnostics is on collecting precise data quickly. This characteristic provides healthcare professionals better insights into patient health, making it a beneficial choice.
Furthermore, the ability of Renishaw probes to integrate with various diagnostic equipment enhances their functionality. They offer reliable data that is essential for informed decision-making. Nonetheless, the complexity of some diagnostic tools may create barriers to effective use without adequate training.
Integration with CNC Systems
The integration of Renishaw probe codes with CNC systems is a crucial aspect of modern manufacturing processes. This integration ensures that precision measurement tools operate seamlessly within automated environments. The significance of this integration lies in several elements, including enhanced accuracy, streamlined workflows, and improved data collection for quality assurance.
Compatibility Issues
Compatibility issues can complicate the integration of Renishaw probes with CNC systems. Each CNC machine may have specific requirements regarding software versions and hardware interfaces. Ensuring the correct matching of these elements is vital for successful integration.
- Hardware Compatibility: Probes need to work with the CNC machine’s existing hardware to prevent operational disruptions.
- Software Versions: Using the right versions of control software can determine how effectively the probe codes function.
- Manufacturing Variability: Different models of CNC machines have unique adaptations that may lead to issues if not properly aligned with the probe codes.
Addressing these compatibility issues is essential to maximizing performance and minimizing downtime in manufacturing settings.
Setup Process
The setup process of integrating Renishaw probes with CNC systems comprises critical phases that determine the efficiency and precision of the measurement capabilities. Two noteworthy aspects of this process are Initial Configuration and Calibration.
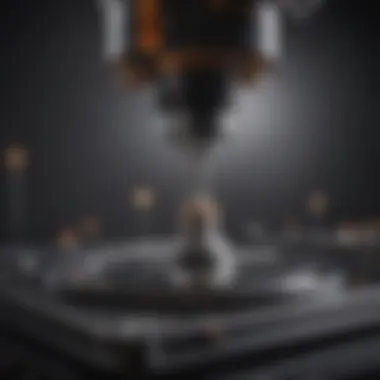
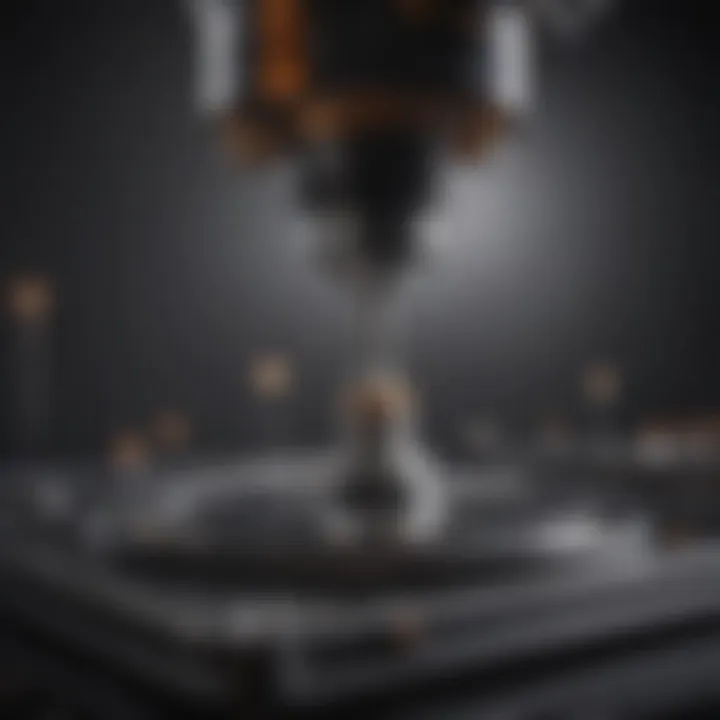
Initial Configuration
Initial Configuration involves establishing settings that allow the CNC machine to communicate effectively with the Renishaw probe. This step is fundamental because it sets the stage for subsequent operations. A key characteristic of Initial Configuration is its ability to ensure the probe is recognized by the CNC system.
- User-Friendly Interfaces: Many CNC systems now feature intuitive settings screens. This ease of use makes Initial Configuration a popular choice.
- Communication Protocols: The unique feature of Initial Configuration is its reliance on established communication protocols such as RS-232 or Ethernet. This capability has significant advantages, enabling faster data transmission rates and improving overall responsiveness. However, improper settings can lead to communication errors, complicating the initial setup process.
Calibration
Calibration is another critical step in the setup process, ensuring that the probe delivers accurate and reliable measurements. This step is indispensable for maintaining quality control in manufacturing. The key characteristic of Calibration is its focus on aligning the measured values with known standards.
- Regular Adjustments: Calibration is often a routine task. Its regular application contributes significantly to long-term efficiency.
- Measurement Accuracy: The unique feature of Calibration lies in its ability to detect systematic errors. Such detection is essential for rectifying issues before they impact production quality. Despite being advantageous, Calibration demands a significant investment of time and resources, which may deter some users.
Challenges in Using Renishaw Probe Codes
Renishaw probe codes greatly enhance measurement capabilities in various fields, but their application is not without complexities. Understanding the challenges involved can help users innovate solutions and minimize errors. Knowledge of these challenges is crucial for professionals who utilize Renishaw probes, as it directly impacts efficiency and accuracy in measurement.
Technical Limitations
Although Renishaw probes are designed for precision, they face certain technical limitations that can affect performance. For example, not all CNC machines are compatible with specific probe models or types. This can limit functionality and lead to suboptimal utilization. Additionally, the range of measurable parameters might be restricted. Users need to understand the specifications of their equipment to ensure that they do not exceed the limitations of their chosen probes.
Furthermore, technical constraints such as environmental conditions can hinder the efficiency of probe operations. High temperatures and vibrations can disrupt measurement accuracy. Therefore, it is paramount to maintain optimal working conditions to achieve reliable measurements. Users should consider the following aspects when dealing with technical limitations:
- Compatibility with existing systems
- Environmental conditions affecting performance
- Range and accuracy specifications
Understanding these issues enables users to make informed decisions on the best tools and techniques for their measurement needs.
User Errors
User errors represent a significant challenge when operating Renishaw probes. These mistakes can arise from improper programming, misunderstandings of code syntax, or inadequate training. A lack of familiarity with the software used for programming can lead to the misapplication of probe codes, resulting in inaccurate data capture.
Training is essential to mitigate these errors. Operators should receive in-depth instruction on both the theoretical aspects of Renishaw technology and practical applications. This training should encompass:
- Overview of probe types and their coding systems
- Hands-on programming exercises
- Simulation scenarios to practice error identification
Even with training, errors can still occur due to human oversight. Regular auditing of measurement processes can help identify patterns of mistakes. By addressing these issues directly, organizations can significantly reduce user-related errors, improving the overall integrity of their measurement operations.
"By understanding the technical limitations and potential user errors associated with Renishaw probe codes, professionals can enhance their effectiveness and ensure high-quality outcomes in measurement and automation."
Future Trends in Probe Technology
As technology advances, the field of probe technology is also evolving. This evolution is crucial for maintaining relevance in precision measurement and automation. Understanding future trends in probe technology allows professionals to adapt and leverage these innovations for improved performance and efficiency in their operations.
Innovations in Probes
The development of new technologies leads to notable innovations in probe design and functionality. These innovations include enhanced measurement capabilities, improved data processing, and more versatile applications.
- Miniaturization: Probes are becoming smaller. This reduction enables integration into tighter spaces without sacrificing accuracy.
- Wireless Communication: The shift to wireless technology improves flexibility and reduces the need for cumbersome cables.
- Advanced Sensor Technology: Sensors are evolving with higher precision and faster response times, allowing for more accurate readings in various environments.
- Smart Probes: Integration of AI algorithms enables probes to adapt to different measurement conditions, enhancing usability.
These innovations not only improve the efficiency of measurement processes but also accommodate a broader range of applications across industries. They exemplify the ongoing quest for precision and accuracy in measurement tasks, which is fundamental to quality control in manufacturing.
Market Demand and Evolution
The market for probe technology is influenced by various factors, including industrial growth, technological advancements, and changing consumer needs. Understanding market demand helps stakeholders identify opportunities and challenges in the field.
- Increased Automation: As industries move toward automation, the demand for reliable probe technology grows. Probes are critical in automated quality assurance processes, ensuring products meet specified tolerances.
- Diverse Applications: With probes being used in sectors such as aerospace, automotive, and healthcare, the versatility of probe technology becomes increasingly significant. This diversity helps stimulate market growth.
- Sustainability Trends: The emphasis on sustainable practices drives the need for effective measurement solutions that minimize waste and optimize production processes.
- Custom Solutions: Clients now require more tailored solutions in terms of functionality and capability, pushing manufacturers to innovate continually.
In summary, the future of probe technology is shaped by the interplay of innovation and market demand. These elements predict an exciting trajectory toward more sophisticated, efficient, and adaptable probe systems. Understanding these trends is essential for professionals aiming to navigate the complexities and harness the potential of Renishaw probe technology.
Closure
In this article, we explored the critical significance of Renishaw probe codes within various industries. Their role in precision measurement and automation is not only vital but also expanding rapidly with advancements in technology. Understanding the codes is fundamental for professionals engaged in engineering, manufacturing, and research.
Renishaw probe codes offer several benefits:
- Efficiency: The codes streamline processes, reducing measurement time while enhancing accuracy.
- Flexibility: They accommodate various applications across industries, from manufacturing to medical diagnostics.
- Integration: The ability to work seamlessly with CNC systems enhances the overall machinery capabilities.
An important consideration when applying these codes is training. Professionals need to be knowledgeable about programming languages, common commands, and the integration with CNC systems. This knowledge minimizes user errors and technical limitations that can arise in practical scenarios.
Moreover, as we look to the future, staying updated on innovations in probe technology and changes in market demand will be crucial. The evolving landscape underscores the necessity for continued education and adaptation for those utilizing Renishaw technologies.
"Understanding and leveraging Renishaw probe codes can lead to significant improvements in measurement precision and overall productivity in various sectors."
In summary, the insights gained from this article not only highlight the importance of Renishaw probe codes but also emphasize the need for continuous learning and adaptation to harness their full potential. As the demand for accuracy in measurement grows, so too does the relevance of understanding these codes and their applications.