Exploring Small Industrial Servo Motors: Insights & Applications
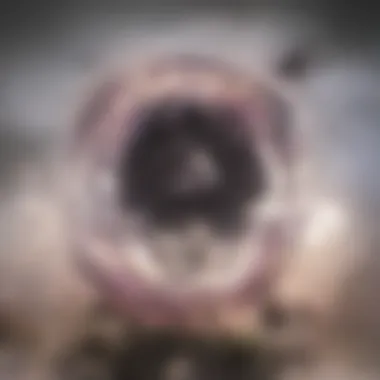
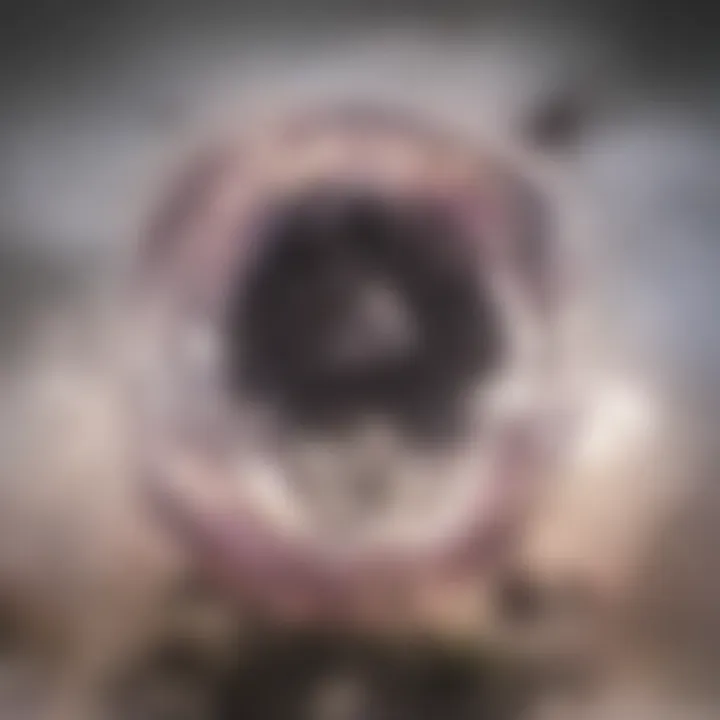
Intro
Small industrial servo motors play a critical role in various manufacturing and automation processes. These motors are essential when precision and control are paramount. Their unique design and operational characteristics enable them to perform tasks that standard motors cannot handle effectively. This discussion will cover essential concepts related to small industrial servo motors, including their definitions, applications, and technical insights.
A servo motor is a rotary actuator that provides precise control of angular or linear position, velocity, and acceleration. In smaller industrial contexts, these motors are integral in robotics, CNC machinery, and conveyor systems. By understanding the fundamental features of these motors, one can appreciate their growing importance in modern industry.
Key Concepts
Definition of Primary Terms
When discussing small industrial servo motors, it is crucial to define some key terms.
- Servo Motor: A motor that receives feedback and adjusts its operations accordingly, ensuring accurate positioning and motion control.
- Closed-Loop Control: A system that uses feedback to compare the actual output with the desired output to reduce errors.
- Open-Loop Control: A simpler system that operates without feedback. It sends commands without adjusting to current conditions.
Understanding these terms helps clarify how small servo motors work and their applications in different scenarios.
Related Concepts and Theories
Servo motors function based on principles of control theory. This science deals with how systems react and adjust based on input. The relationship between input and output is essential for achieving precision. Additionally, concepts such as torque and speed are vital when discussing motor performance and applications.
- Torque: The rotational force produced by a motor, vital for determining how effectively it can perform tasks.
- Speed: Refers to how quickly the motor can achieve desired positions or movements, crucial for applications demanding rapid response.
Small servo motors often integrate with various control systems. These include programmable logic controllers (PLCs) and computer numerical control (CNC) systems. This integration allows for enhanced accuracy and efficiency, leading to better overall performance.
"Understanding the intricacies of how small industrial servo motors operate can lead to improved designs and applications across numerous fields in automation and manufacturing."
Future Directions
Gaps Identified in Current Research
While significant advancements have been made in small industrial servo motors, there are still challenges and gaps in current research. The need for improved energy efficiency is an ongoing concern. Additionally, the development of smarter motor control systems can enhance performance.
Suggestions for Further Studies
Future studies may explore the integration of AI and machine learning in the control of servo motors. This could lead to more adaptive systems capable of learning from their environments and improving their operational efficiency. Additionally, research focusing on advancing materials used in motor construction can lead to lighter, more effective designs.
By addressing these aspects, the industry can continue evolving, meeting the demands of ever-changing technological landscapes.
Intro to Small Industrial Servo Motors
Small industrial servo motors play a crucial role in modern automation and robotics. Their precise control and capability to respond to commands make them indispensable in various manufacturing sectors. The significance of understanding these motors lies not only in their functional advantages but also in their application versatility.
They provide significant benefits such as improved efficiency and reduced energy consumption. As industries continue to evolve, the demand for accurate, reliable, and efficient control systems increases. Small industrial servo motors meet these demands effectively.
From CNC machines to assembly lines, these motors are pivotal components that enhance production accuracy and speed. Understanding their operations and capabilities is essential for students, researchers, and professionals aiming to optimize manufacturing processes. It can also guide decisions about technology investments in equipment.
"As automation advances, the role of small industrial servo motors becomes more pronounced in driving efficiency and productivity in manufacturing."
Definition and Overview
A small industrial servo motor is an electromechanical device that receives and processes commands to produce precise rotational motion. These motors primarily utilize feedback systems, allowing them to correct any deviations from their desired position quickly. The key components typically include a motor, a drive, and a feedback unit.
These motors can vary in size and power, but all share common abilities such as high torque-to-weight ratios and precise positioning. They are essential in sectors that prioritize accuracy and repeatability, thereby facilitating high-quality production standards.
Historical Context and Development
The history of small industrial servo motors dates back to the mid-20th century when the demand for automation in factories began to rise. Early servo mechanisms were large and cumbersome, limited in application scope. However, advancements in electronics and materials science led to the development of more compact, efficient servo motors.
In recent decades, the integration of digital control systems and microprocessors has revolutionized the industry. Today, small industrial servo motors feature enhanced capabilities, including greater precision, response speed, and connectivity. This evolution has made them suitable for a wide range of applications, significantly contributing to the growth of automated processes across various industries.
Understanding the development of these motors offers insights into how they have transformed modern manufacturing and the potential for future advancements.
Construction of Small Industrial Servo Motors
The construction of small industrial servo motors is crucial to understanding their functionality and effectiveness. The design and components utilized in these motors greatly impact their performance, durability, and application suitability. By examining the various elements that make up these motors, one gains insight into how they operate and the benefits they provide in industrial settings.
Components and Materials
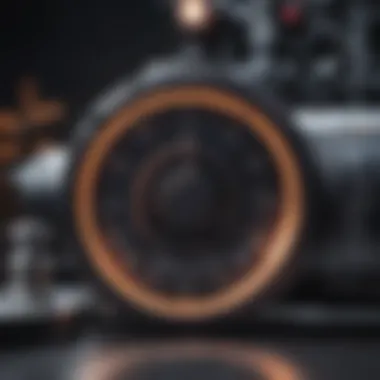
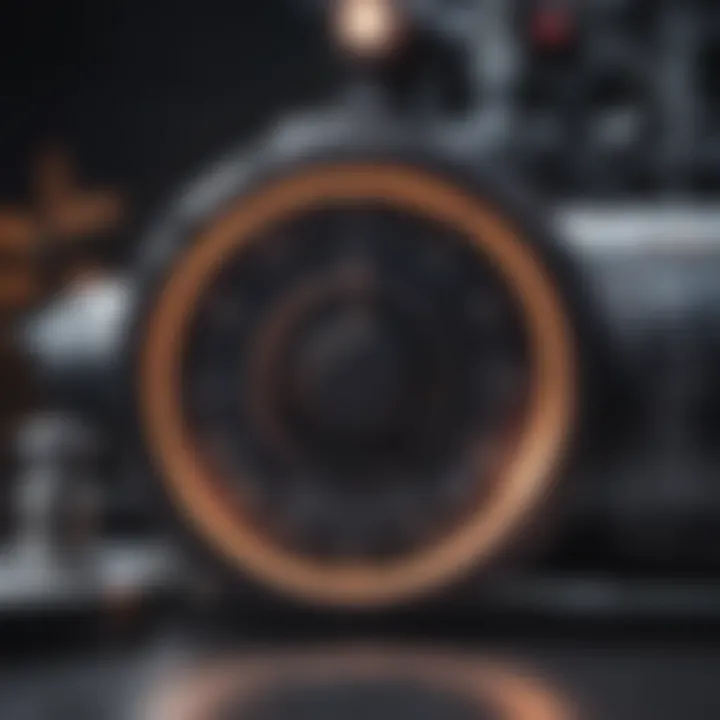
The primary components of a small industrial servo motor include the stator, rotor, gearbox, power supply, and controller.
- Stator: This component generates the magnetic field necessary for rotation. Typically, it is constructed using high-quality steel laminations to minimize losses.
- Rotor: The rotor moves in response to the magnetic field. Its design usually involves permanent magnets or winding coils, depending on the motor type.
- Gearbox: Although this is not included in every design, gearboxes are often used to enhance torque and speed control. Precision gears help achieve the desired motion.
- Power Supply and Controller: The controller ensures the motor operates as intended, adjusting parameters such as speed and direction in real-time, while the power supply provides the needed energy.
The materials used in creating these components also play a significant role. Common materials include:
- Copper for electrical windings due to its excellent conductivity.
- High-strength steel for rotors and gearboxes, ensuring durability under stress.
- Rare earth magnets in permanent magnet designs for enhanced magnetic properties.
Selecting the right combination of materials contributes to efficiency and performance. A well-constructed servo motor can provide precise movements and withstand heavy-duty applications, which makes understanding these components vital for anyone involved in the field.
Motor Types: vs. AC
There are primarily two types of small industrial servo motors: DC servo motors and AC servo motors. Each has its unique construction and operating principles that suit different applications.
DC Servo Motors
DC servo motors are often simpler in design. They convert direct current into mechanical motion.
- They typically offer better torque at lower speeds, making them suitable for applications requiring rapid starts and stops.
- Maintenance of DC motors can be higher due to brushes that wear out over time and need replacement.
AC Servo Motors
AC servo motors, on the other hand, utilize alternating current and are often considered more advanced.
- They usually have higher efficiency and longer operational life compared to their DC counterparts.
- Their design includes complex control systems, which allow for higher precision and smoother operation at variable speeds.
Choosing between DC and AC servo motors depends largely on the application requirements. Each type offers specific advantages, and understanding these can guide better decision-making in industrial settings.
The Role of Feedback Systems
Feedback systems are integral to the successful operation of small industrial servo motors. They enable high levels of accuracy and control over movement. These systems work by continuously monitoring the motor performance and making real-time adjustments.
- Types of Feedback: The most common types include position feedback from encoders and velocity feedback from tachometers. These devices provide crucial data about the motor's actual position and speed compared to the desired settings.
- Advantages of Feedback Systems:
- Improved Precision: By continuously receiving data about its performance, a servo motor can achieve desired motion with remarkable accuracy.
- Enhanced Stability: Feedback allows the control system to make adjustments, ensuring smooth operation even in dynamic environments.
- Fault Detection: Real-time monitoring can help identify potential issues early, facilitating timely maintenance and minimizing downtime.
Feedback systems revolutionize the functionality of servo motors by providing them with the necessary data to function effectively.
Operational Principles of Small Industrial Servo Motors
Understanding how small industrial servo motors operate is crucial for their effective application in various industries. This section discusses the fundamental concepts that underlie the functionality of servo motors, focusing on their motion control capabilities, the feedback mechanisms that enhance their performance, and the specific characteristics related to torque and speed. Knowing these operational principles helps engineers and technicians optimize the integration of servo motors into systems, leading to enhanced productivity and precision.
How Servo Motors Function
Servo motors work using a closed-loop system that ensures controlled movement. The core components include the motor itself, a feedback sensor, and a controller. When a command is inputted, the controller sends a signal to the motor to initiate movement. As the motor operates, feedback sensors continuously monitor its position and send this information back to the controller. By comparing the actual position with the intended position, adjustments are made in real time to ensure accuracy.
For example, if a servo motor is instructed to rotate to a specific angle, the feedback system allows it to make corrections if it deviates from that angle due to load changes or other factors. This level of precision is why servo motors are favored in applications requiring high accuracy and responsiveness.
Control Systems and Signal Processing
The control systems for servo motors are typically built on PID (Proportional, Integral, Derivative) algorithms. These systems process signals from the feedback components to calculate the necessary adjustments in motor operation. Each component of the PID controller plays a distinct role:
- Proportional Control: It adjusts the motor's output proportional to the error, which is the difference between the desired output and the actual output.
- Integral Control: This helps eliminate the residual steady-state error by adjusting the system based on the accumulated past errors.
- Derivative Control: It predicts future error based on current rates of change, thus improving stability and response times.
Using such control systems means that servo motors can adapt dynamically to changing conditions, making them suitable for a wide array of applications from simple machine movement to complex robotic arms.
Torque and Speed Characteristics
Torque and speed are vital performance metrics for servo motors. Torque refers to the rotational force the motor can exert, while speed indicates how quickly it can achieve the desired position. The balance between these two characteristics is critical for effective operation.
A servo motor is rated for specific torque and speed values, which affects its suitability for particular tasks. For instance, in applications where rapid movements are needed, like pick-and-place robotics, the emphasis might be on achieving higher speeds. Conversely, tasks requiring precise control at low speeds might prioritize torque.
In more technical terms:
- Torque can be visualized as the strength that allows a motor to overcome resistance. High torque enables a motor to handle heavier loads without stalling.
- Speed, measured in revolutions per minute (RPM), determines how fast a motor can complete its rotation. For many applications, a balance between these two metrics translates into operational efficiency.
Optimizing torque and speed is essential for enhancing the overall performance of systems utilizing small industrial servo motors. A mismatch can lead to inefficiencies or equipment failures, highlighting the importance of careful selection and tuning during the design phase.
In summary, the operational principles of small industrial servo motors revolve around sophisticated control mechanisms, precise feedback systems, and the balance of torque and speed. Understanding these elements provides a solid foundation for leveraging servo technology effectively in varied applications.
Performance Metrics for Small Industrial Servo Motors
Performance metrics are essential for evaluating the efficacy and suitability of small industrial servo motors. These metrics provide insights into various operational characteristics that can influence the performance of automated systems. Understanding these parameters will help users make informed decisions about the right servo motors for specific applications.
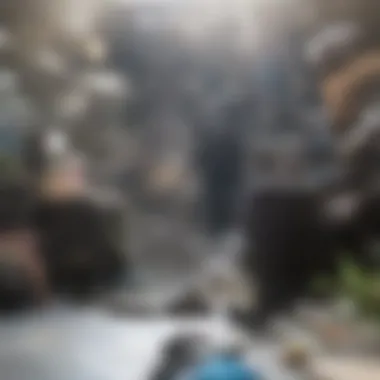
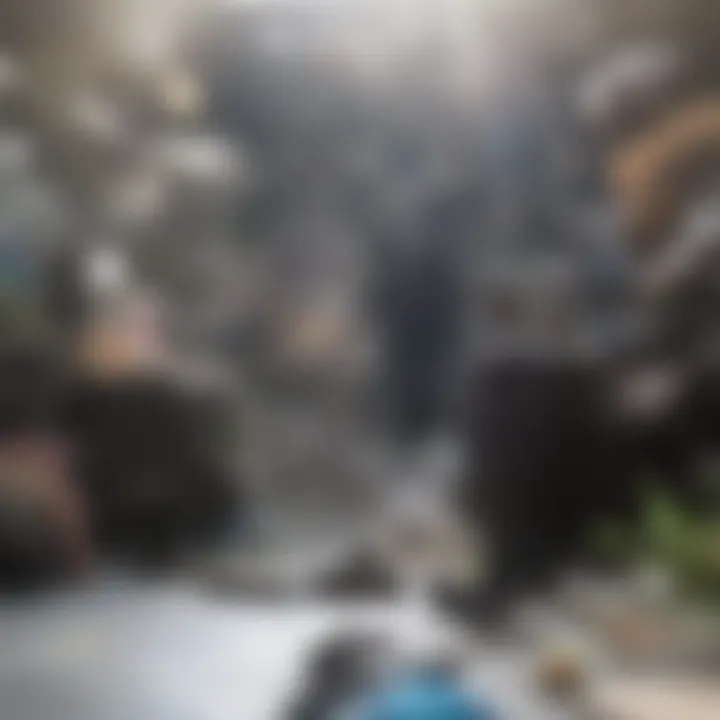
Efficiency Factors
Efficiency in small industrial servo motors hinges on several components, including energy conversion rates and thermal management. High efficiency reduces operational costs and minimizes heat generation, which can lead to longer motor life. Some factors to consider are:
- Power Rating: This is the maximum output power the motor can provide. Motors with high power ratings tend to operate more efficiently under load.
- Losses: These include copper losses caused by resistance in the windings and iron losses from the magnetic circuit. Calculating these losses allows for a better understanding of overall efficiency.
- Speed-Torque Characteristics: The relationship between speed and torque can indicate how efficiently a servo motor can perform under various conditions. Motors optimize their efficiency within specific speed and load ranges.
Load Capacity and Durability
Load capacity refers to the maximum weight or force that a servo motor can handle effectively without compromising performance. A motor must be selected based on the specific load characteristics of the application. Factors to consider include:
- Rated Load: This is the standard load a motor can handle continuously without overheating. Exceeding rated load can lead to motor failure.
- Durability: This refers to the material construction and design of the motor. Durability is tested through various cycles of operation, which can indicate how well the motor will hold up over time.
- Environmental Resistance: Motors that operate in harsh environments may require additional protection, such as sealed enclosures, to prevent damage from dust, moisture, or temperature extremes.
Response Time and Precision
Response time and precision are critical for applications requiring quick and accurate movements. Response time is the duration it takes for the motor to react to input commands, while precision refers to how closely the motor can achieve the desired position or speed. Key considerations are:
- Control Algorithms: The type of control system employed can impact both response time and precision. Advanced algorithms can enhance performance by ensuring tighter control over the motor operation.
- Feedback Mechanisms: Many servo motors utilize feedback systems like encoders or resolvers. These devices provide real-time data on position and speed, allowing for rapid adjustments and improved accuracy.
- Testing Standards: Adhering to specific testing protocols can ensure that motor performance meets industry standards for response time and position precision.
Understanding these performance metrics allows engineers and technicians to select the most appropriate servo motors that suit their needs, reducing the risk of operational failures and ensuring efficiency in production.
By carefully evaluating efficiency factors, load capacity and durability, and response time and precision, users can enhance the performance of industrial applications leveraging small servo motors.
Applications of Small Industrial Servo Motors
The applications of small industrial servo motors are numerous and varied, reflecting their versatility and functionality. These motors play a crucial role in a wide range of industries, driving innovations and efficiencies that are essential in today’s fast-paced manufacturing environment. Understanding their applications provides insights not only into their practical benefits but also into the technical considerations that these systems demand.
Manufacturing and Automation
In manufacturing, small industrial servo motors are central to automation processes. They provide the precision required for tasks such as material handling, assembly, and packaging. For instance, in automated assembly lines, precision is vital. Servo motors enable accurate positioning and consistent repeatability, enhancing productivity.
The use of servo motors in robotics is particularly noteworthy. Robotic arms often rely on these motors for tasks requiring delicate movements, such as assembly or quality control. Electromechanical systems benefit greatly from the torque and speed control that servo motors offer. Improved cycle times and reduced operational costs are key advantages.
Consider the case of CNC machining. Here, servo motors control tools with high accuracy. This ensures that parts are produced to exact specifications, reducing waste and improving overall product quality. In automated warehouses, servo motors manage storage and retrieval systems seamlessly, enhancing operational efficiency.
Robotics and Mechatronics
Within the realm of robotics and mechatronics, small industrial servo motors are indispensable. These motors are pivotal for mobile robots and robotic limbs. They provide the necessary movement and stability required for tasks like navigation and manipulation.
Servo motors in* the field of mechatronics allow for the integration of mechanical systems with electronic control systems. This interaction enables more complex movements and operations. For example, in surgical robots, servo motors are utilized to perform intricate procedures with human-like precision.
Moreover, the adaptability of servo motors to different applications is another advantage. They can be tuned for high torque applications or high-speed operations based on specific requirements. This flexibility supports many advanced applications, such as drones and underwater robots, where precision and control are paramount.
Aerospace and Automotive Industries
The aerospace and automotive sectors also benefit significantly from small industrial servo motors. Their ability to operate efficiently under strict regulatory standards makes them suitable for applications such as flight control systems and automated vehicle components.
In aerospace, servo motors are used in actuators for controlling flight surfaces like flaps and rudders. These components require precise control, where servo motors excel. Their reliability and responsiveness enhance the overall safety and performance of aircraft.
Similarly, in the automotive industry, they are used for various applications ranging from power steering assist to robotic assembly of cars. The need for high accuracy and responsiveness aligns perfectly with the advantages of servo motors. Automation of assembly lines has also led to cost reductions and improved safety.
In summary, small industrial servo motors play an integral role in transforming how industries operate. Their applications not only streamline processes but also address the growing demand for precision and efficiency across manufacturing environments. Understanding these applications highlights their relevance in innovation and industry evolution.
Advantages of Small Industrial Servo Motors
Understanding the advantages of small industrial servo motors is crucial for evaluating their role in modern machinery and automation systems. These motors offer a range of benefits that cater to the needs of various industries, enhancing their operational efficiency and effectiveness. Below, we delve into key aspects that underline their importance in manufacturing and robotics.
Compact Size and Lightweight Design
One of the leading advantages of small industrial servo motors is their compact size and lightweight construction. This makes them ideal for applications where space is at a premium. In manufacturing settings, machines often require multiple components to operate efficiently, and the integration of small servo motors allows for denser configurations without sacrificing performance.
The lightweight nature also contributes significantly to ease of installation and handling. Technicians can manage these motors more conveniently, reducing the overall downtime during repairs or upgrades. This feature is particularly beneficial in robotics and automation where agility and speed are essential.
High Accuracy and Control
High accuracy and control are paramount in applications that rely on precise movements. Small servo motors excel in providing consistent positional accuracy due to their closed-loop control systems. These systems not only enhance performance but also minimize errors in various operations.
Servo motors can achieve high torque at low speeds while maintaining accurate position control. This capacity is significant in processes such as CNC machining, where meticulous precision is a requirement. Furthermore, the ability to fine-tune their performance through programming offers engineers great flexibility in designing automation setups.
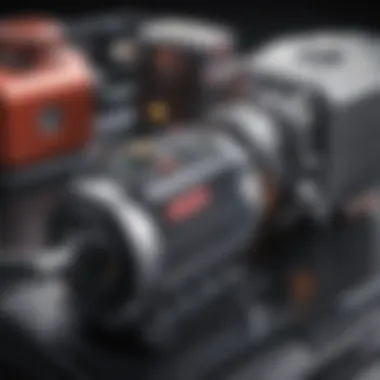
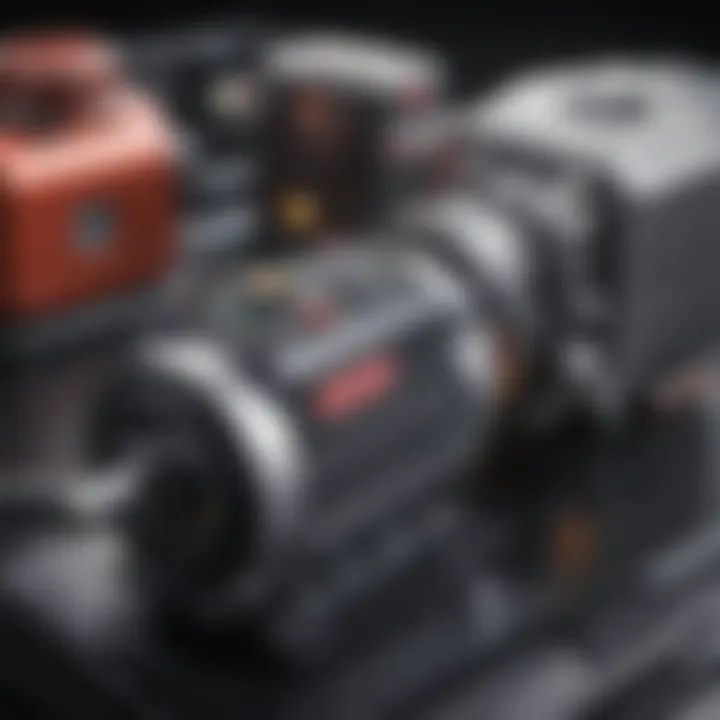
Energy Efficiency
Energy efficiency is another compelling advantage of small industrial servo motors. Their operational design reduces energy consumption compared to traditional motors. This lower energy use not only decreases operational costs but also enhances sustainability within manufacturing processes.
Many models utilize energy recovery features, where excess energy generated during operation can be redirected or stored, thus contributing to overall system efficiency. During peak operation, these motors help in maintaining performance without requiring high energy inputs. This aspect is increasingly becoming a consideration for industries aiming to meet strict energy regulations or those pursuing green initiatives.
"The transition to more energy-efficient technologies is not just about compliance; it's about rethinking operational strategies in an eco-sensitive world."
Challenges in Using Small Industrial Servo Motors
The integration of small industrial servo motors into various applications presents unique challenges. Understanding these challenges is crucial for engineers, designers, and decision-makers involved in automation and robotics. This section explores significant obstacles that users may encounter, focusing on how these challenges affect implementation and operational efficiency.
Cost Considerations
The initial investment required for small industrial servo motors can be significant. The unit cost of high-performance servo motors often surpasses that of traditional motors. This higher upfront cost is primarily due to their advanced technology and precision components. Additionally, supporting equipment such as controllers and feedback systems can further inflate costs.
Many companies must carefully evaluate their budget and the expected return on investment. The need for specialized knowledge and skills can also contribute to hidden costs. Training staff and maintaining these systems requires additional resources. It is essential to factor these costs into project budgeting to prevent overspending.
Technical Complexity of Implementation
Implementing small industrial servo motors involves intricate design and configuration. The setup may require specialized knowledge in control systems and signal processing. Many users face challenges when integrating these motors with existing equipment. Complicated wiring and programming can lead to extensive downtime during implementation.
In addition, the varying specifications and standards can complicate the selection process. Without thorough understanding, mismatches between components can occur, resulting in inefficiencies. Projects often suffer delays and increased costs if initial setups are not carefully planned and executed. Proper training and education about the hardware and software involved are critical for a successful deployment.
Maintenance and Reliability Issues
While designed for durability, small industrial servo motors still require regular maintenance. Over time, wear and tear can affect performance and reliability. Routine inspections and timely repairs are essential to prolong the service life of these motors. It is important for technicians to be familiar with common failure modes and how to mitigate them.
Moreover, sourcing replacement parts can become a challenge. The specific nature of servo technology means parts may not be locally available. This can lead to extended downtime while waiting for components to arrive. Companies must implement preventive maintenance programs to keep systems running efficiently.
"To optimize the performance of small industrial servo motors, organizations must develop comprehensive maintenance strategies that anticipate common issues."
Future Trends in Small Industrial Servo Motors
The future trends in small industrial servo motors are vital for understanding their evolving role in manufacturing and automation. These trends indicate how the industry may change due to advancements in technology, increasing integration with artificial intelligence, and the need for sustainability. Awareness of these trends provides insight into what to expect for small servo motor applications in the coming years.
Advancements in Motor Technology
Technological progress in small industrial servo motors focuses primarily on enhancing performance and efficiency. Innovations in materials and manufacturing processes lead to lighter and more robust motors. For example, the introduction of high-energy density magnets improves torque and speed performance significantly. New rotor and stator designs facilitate better thermal management, allowing for higher operating temperatures and prolonged lifespans.
Additionally, the development of miniature servo motors fits increasing demands for compact solutions in automated systems. Features like improved feedback systems, such as high-resolution encoders, enable finer control and precision. These advancements not only optimize operation but also expand applications in industries like robotics and medical technologies.
Integration with AI and Machine Learning
The integration of artificial intelligence and machine learning into small industrial servo motors introduces a paradigm shift in operational control. Enhanced data analytics can improve decision-making processes in real-time, allowing for predictive maintenance and reducing downtime. AI algorithms can optimize motion control and adapt the motor's performance based on varying conditions and loads.
Moreover, smart servo motors that communicate with other devices in an IoT framework enable seamless integration within complex systems. This connectivity results in enhanced automation that can maximize productivity. The importance of AI does not only lie in process efficiency but also in its potential to provide insights into performance metrics. These insights can guide the design of future servo systems, leading to more intelligent manufacturing solutions.
Sustainability and Eco-Friendly Designs
The emphasis on sustainability in manufacturing extends to small industrial servo motors. As environmental concerns grow, so does the initiative to create eco-friendly designs. Manufacturers are now focusing on energy-efficient motors that consume less power without compromising performance. This leads to reduced operational costs as well as lowered carbon footprints.
In addition, implementing recyclable materials in servo motor construction has become a priority. Manufacturers aim to create products that contribute to circular economy principles. This means designing motors that can be easily disassembled for repair or recycling. Strategies for sustainable design not only comply with regulations but also reflect a commitment to responsible manufacturing practices.
By focusing on advancements in technology, AI integration, and sustainability, the future of small industrial servo motors looks promising, confirming their essential role in modern manufacturing.
Clearly, trends in small industrial servo motors indicate a vibrant future, shaped by the synergy between technological advancement and sustainability efforts. Understanding these trends is crucial for professionals not just for adaptation but also for driving innovative solutions in industrial applications.
Epilogue
The conclusion serves as a crucial component of this article. It encapsulates the key discussions around small industrial servo motors, reinforcing their significance in modern technology. The insights drawn throughout the article highlight the multifaceted nature of these motors and their impact across diverse industries.
Summary of Key Points
This article has elaborated on several fundamental aspects of small industrial servo motors:
- Definition and Overview: Understanding what small industrial servo motors are and their role in automation.
- Construction: Delving into components, materials, and the differences between DC and AC motors.
- Operational Principles: How these motors function, including control systems and performance metrics.
- Advantages and Challenges: Discussing benefits like compact design and energy efficiency, as well as operational challenges.
- Future Trends: Noting advancements in technology and integration with AI.
These points collectively inform about the current and potential future landscape of small industrial servo motors. The continuous advancements and growing applications across various sectors underscore their importance.
Implications for Industry and Research
The insights derived from understanding small industrial servo motors carry significant implications. For industry practitioners, integrating these motors can enhance productivity and efficiency in manufacturing processes. On the research front, the emphasis on sustainability and the latest technological advancements offers fertile ground for further studies. This can lead to innovations that not only optimize performance but also reduce the ecological footprint of manufacturing.
In summary, small industrial servo motors are pivotal in shaping future technologies. Recognizing their potential cements their role as critical components in advancing industrial practices.