Understanding Tungsten Carbide Quality: A Comprehensive Guide
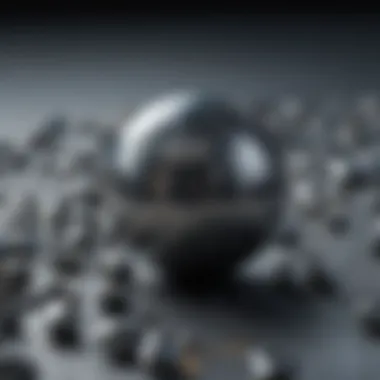
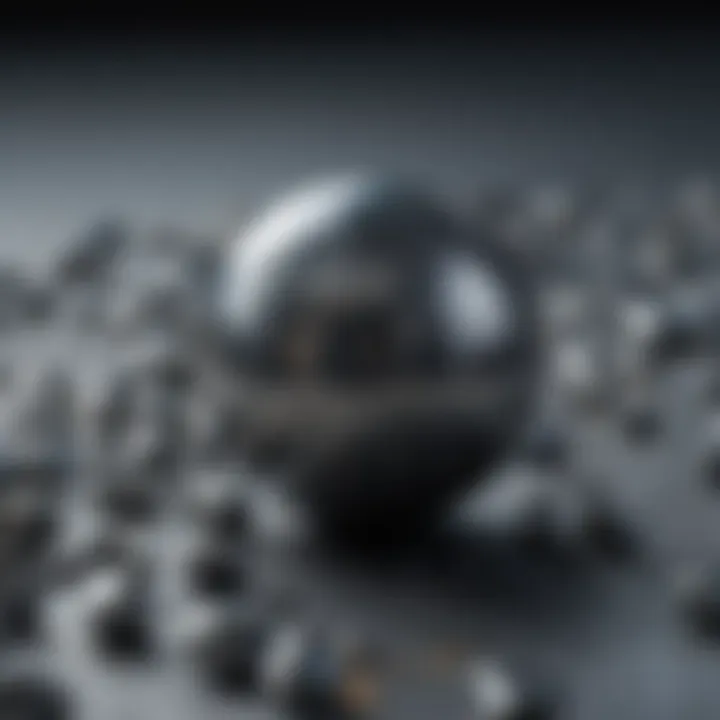
Intro
Tungsten carbide is a compound made from tungsten and carbon. It is known for its exceptional hardness and wear resistance, which makes it a popular material in various industries. Understanding the quality of tungsten carbide is essential for both manufacturing and jewelry applications. This article will explore the components that define quality, including composition, purity, hardness, and resistance to wear. Through a detailed examination, we will clarify common misconceptions and provide tools for quality assessment in different contexts.
Key Concepts
Definition of Primary Terms
To effectively discuss tungsten carbide, it is important to define some primary terms:
- Tungsten Carbide: A binary chemical compound composed of equal parts of tungsten and carbon atoms. It is used for cutting tools and industrial machinery due to its superior hardness.
- Purity: Refers to the absence of impurities within the material. High purity levels are crucial for optimal performance.
- Hardness: A measure of a material's resistance to deformation. Tungsten carbide has a high hardness rating, making it suitable for demanding applications.
- Wear Resistance: This property reflects the ability of a material to withstand wear from friction and other mechanical actions. Tungsten carbide offers excellent wear resistance.
Related Concepts and Theories
Understanding tungsten carbide also involves exploring related concepts. These include:
- Composite Materials: Materials made from two or more constituent materials with different physical or chemical properties that, when combined, produce a material with characteristics different from those of the individual components.
- Metal Matrix Composites: Comprising a metal matrix combined with other materials to enhance mechanical properties.
- Quality Control Standards: Procedures and guidelines established to ensure that products meet specific performance criteria.
Future Directions
Gaps Identified in Current Research
Although much is known about tungsten carbide, gaps remain in certain areas of research.
- Variability in Manufacturing Processes: Different manufacturers employ various methods that may impact the final product's quality.
- Long-term Performance Studies: Research focusing on how tungsten carbide performs under prolonged stress and different environmental conditions is limited.
Suggestions for Further Studies
Future research should aim to address these gaps. Suggested areas include:
- Studies on the effect of different carbon contents on tungsten carbide's physical properties.
- Assessment of the sustainability of tungsten carbide production methods and their environmental impact.
"Understanding the nuances of tungsten carbide quality is crucial for both manufacturers and consumers, as it directly impacts performance in critical applications."
Prologue to Tungsten Carbide
Tungsten carbide is a remarkable material that has gained prominence across several industries. Understanding its significance is essential for anyone involved in manufacturing, engineering, or even jewelry design. Tungsten carbide is not just another alloy; it represents a fusion of two elements: tungsten and carbon. This combination results in a compound known for its exceptional hardness and durability.
Benefits of Tungsten Carbide
One of the most notable benefits of tungsten carbide is its resistance to wear and tear. This makes it ideal for various applications such as cutting tools, industrial machinery, and even jewelry. In industries where precision and longevity are crucial, tungsten carbide can provide a reliable solution. Its ability to maintain sharpness and resist deformation under high pressure is unmatched compared to other materials.
Another consideration is its high melting point. Tungsten carbide can endure extreme conditions without degradation. This property is particularly important in industries like aerospace and oil drilling, where components are subjected to intense heat and stress.
"Tungsten carbide's unique properties enable it to outperform many conventional materials in demanding applications."
Moreover, the material is available in various grades, giving manufacturers the flexibility to choose a type that best fits their needs. These grades differ in composition and processing, which can significantly affect performance characteristics.
Considerations When Workng With Tungsten Carbide
When considering the use of tungsten carbide, one must also be aware of its brittleness when compared to some other metals. While it is tough, it can be prone to chipping or cracking when faced with sudden impacts. Therefore, careful handling and application are important.
Chemical Composition of Tungsten Carbide
The chemical composition of tungsten carbide is fundamental in determining its quality and performance in various applications. Understanding the elements that make up this material can provide insights into its durability, hardness, and overall effectiveness. Tungsten carbide is primarily composed of tungsten (W) and carbon (C), and the ratios of these elements can greatly influence the final product's characteristics.
In manufacturing processes, achieving the right composition is crucial. The purity levels of tungsten and carbon significantly impact the material's wear resistance and toughness. High-quality tungsten carbide typically contains a near stoichiometric ratio, which means optimum amounts of tungsten and carbon are present. Deviations from this ratio can lead to a decrease in performance.
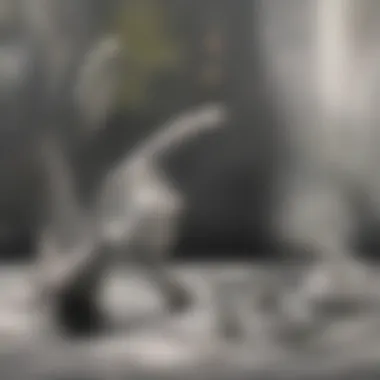
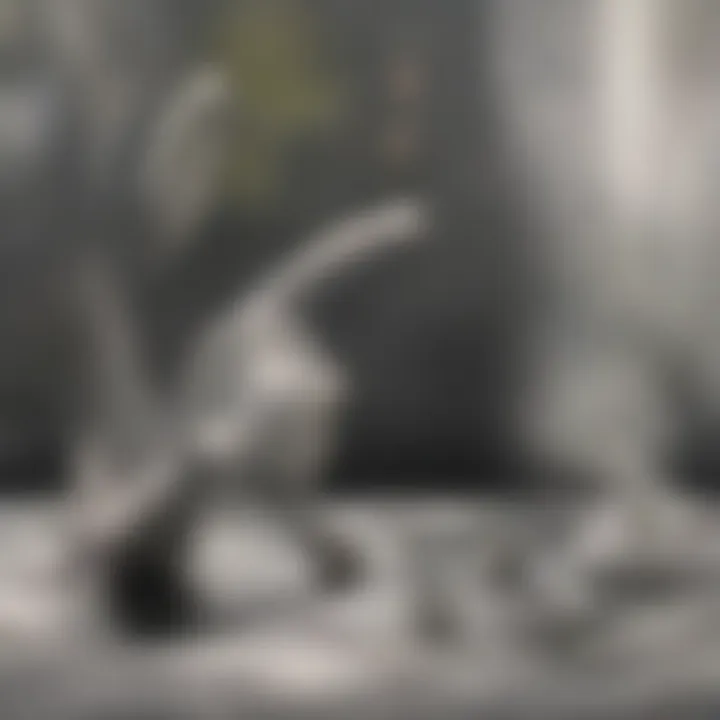
Furthermore, the presence of additives in production can enhance specific properties of tungsten carbide. Understanding each component's role allows manufacturers to tailor the properties of tungsten carbide for specialized applications, making it versatile and widely applicable in industries such as machining, mining, and jewelry production.
Tungsten and Carbon Elements
Tungsten and carbon are the primary elements in tungsten carbide. Tungsten is known for its exceptional hardness and high melting point, making it particularly valuable in extreme environments. When combined with carbon, tungsten forms a compound that exhibits remarkable hardness.
The ratio of tungsten to carbon in tungsten carbide typically hovers around 6:1. This ratio is optimal for obtaining the best mechanical properties. When the balance shifts too far toward either element, it may result in excessive brittleness or reduced hardness, affecting the integrity of the finished product.
Common Additives in Production
While tungsten and carbon are essential, various additives can be included in the production process to alter the properties of tungsten carbide based on specific application needs. Common additives include cobalt, nickel, and chromium.
- Cobalt acts predominantly as a binder in tungsten carbide, enhancing toughness and durability. This is vital in applications where impact resistance is critical.
- Nickel can improve corrosion resistance, which is beneficial in environments where moisture and chemicals are present.
- Chromium may enhance the wear resistance of tungsten carbide, further extending its lifespan in demanding conditions.
Understanding the role of these additives helps manufacturers produce tungsten carbide with qualities that align precisely with the requirements of various industries. Their strategic use illustrates the complexity behind the creation of high-quality tungsten carbide products.
Manufacturing Processes
The manufacturing processes underlying tungsten carbide are essential to understanding its quality and performance. Quality largely relies on how tungsten carbide is produced, emphasizing the crucial steps involved. Each manufacturing process impacts the final properties, such as hardness, wear resistance, and overall reliability. Thus, grasping these processes illuminates the path from raw materials to high-performing tungsten carbide products.
Sintering Techniques
Sintering is a pivotal process in tungsten carbide manufacturing. It involves compacting fine tungsten carbide powders and applying heat without reaching the melting point. This procedure joins the particles at a molecular level, leading to a dense final product that possesses excellent hardness. Various sintering methods exist, including:
- Pressure Sintering: Utilizes hydraulic or mechanical pressure, enhancing density.
- Vacuum Sintering: Conducted in a vacuum to eliminate oxidation and contaminants, improving purity.
- Hot Isostatic Pressing (HIP): This method applies heat and uniform pressure, further maximizing density and mechanical properties.
The choice of technique influences the material’s microstructure, which directly correlates with its performance in applications.
Cementation Process
The cementation process complements sintering in the creation of tungsten carbide. It involves infusing cobalt or nickel into tungsten carbide, which acts as a binder. The analysis of the cementation process emphasizes its role in enhancing toughness and fracture resistance. Key points include:
- Material Selection: A high-quality binder is crucial for the performance of tungsten carbide. Cobalt is preferred for its superior binding capabilities.
- Temperature Control: Precise temperature management is vital during cementation to prevent excessive grain growth, which can weaken the final product.
- Monitoring Proportions: The ratio of tungsten carbide to the binder determines the final characteristics, affecting wear resistance and hardness.
Mastering the cementation process ensures a balance of hardness and toughness, making it versatile in various applications.
Impact of Temperature on Quality
Temperature plays a significant role in both sintering and cementation processes. Variations can alter the microstructure, affecting overall product quality. Understanding the implications of temperature is essential:
- Sintering Temperature: Elevated temperatures can enhance densification, but too high can lead to grain coarsening, diminishing hardness.
- Cementation Temperature: The right temperature ensures optimal dispersion of the binder, while excessive heat can cause unwanted phase changes.
- Cooling Rates: After sintering or cementation, controlled cooling is necessary to prevent thermal stresses that can lead to cracks.
Properties Characterizing Quality
The properties of tungsten carbide play a crucial role in determining its overall quality. Understanding these properties is essential for industries that rely on tungsten carbide components. Key characteristics include hardness, wear resistance, and impact toughness. Each of these elements contributes to the performance, longevity, and suitability of tungsten carbide for various applications. Therefore, examining these properties allows consumers and manufacturers to make informed decisions about the materials they choose.
Hardness Metrics
Hardness is one of the most significant properties of tungsten carbide. It measures the material's resistance to localized deformation, typically caused by mechanical indentation. Tungsten carbide ranks high on the Mohs hardness scale, usually between 8.5 and 9.5, depending on its composition.
Measuring the hardness helps predict how a material will perform under different conditions. For example, tools made from harder tungsten carbide can be more effective in cutting and drilling applications. Common testing methods include the Rockwell and Vickers tests, both of which provide valuable data concerning the hardness levels. A higher hardness metric often correlates to improved performance and longevity.
Wear Resistance Analysis
Wear resistance is another vital factor when assessing tungsten carbide quality. It reflects how well the material can withstand abrasive actions over time. Tungsten carbide exhibits exceptional wear resistance, making it ideal for tools and applications that endure high levels of friction and wear. Since wear can lead to costly replacements and downtime, selecting materials with higher wear resistance ensures durability and efficiency in operations.
The evaluation of wear resistance usually involves standardized tests, such as the ASTM G65 test, which measures the material's response to abrasion. Higher performance in this area means reduced maintenance costs and extended product lifespans. Tungsten carbide's wear resistance, combined with its hardness, makes it a valuable choice in industries such as mining and manufacturing.
Impact Toughness and Its Relevance
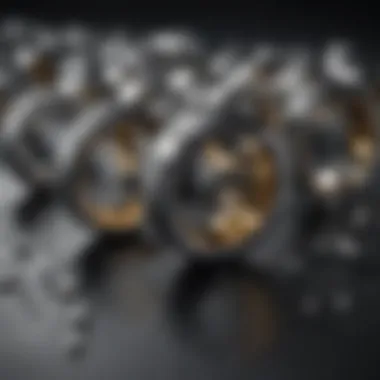
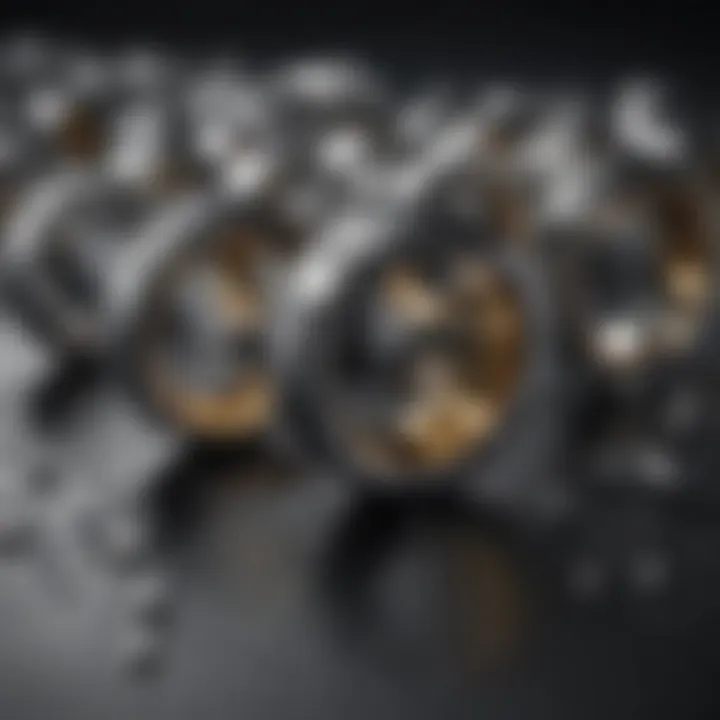
Impact toughness defines a material’s ability to absorb energy during deformation. It is a critical consideration, especially in applications where machinery faces sudden shocks or loads. Tungsten carbide has some limitations in this area due to its rigidity and density. While it excels in hardness and wear resistance, it may be prone to brittle fracture under extreme impact.
Understanding impact toughness is essential when designing tools and components. For specific applications, reinforcing tungsten carbide with other materials can help improve its toughness. This addition can create a balance between hardness and durability, ensuring the material performs optimally under various conditions. The relevance of impact toughness thus cannot be overlooked, as it plays a significant role in safety and reliability across different industries.
Quality Standards in Tungsten Carbide Production
Quality standards in tungsten carbide production are crucial for ensuring that the end product meets specific performance requirements. These standards guide manufacturers in producing reliable materials essential for various applications. Understanding these quality benchmarks helps both producers and consumers assess the reliability and performance of tungsten carbide products.
In the realm of tungsten carbide, the presence of quality standards not only guarantees specific properties like hardness and wear resistance but also ensures consistency and safety. Customers rely on these standards to make informed decisions regarding their purchases. Adhering to these norms also fosters a culture of quality within organizations, promoting accountability during manufacturing processes.
International Standards
International standards play a vital role in tungsten carbide production, establishing universally accepted criteria for quality assurance. Organizations such as the International Organization for Standardization (ISO) set guidelines that influence manufacturing processes across the globe. Standards such as ISO 9001 ensure that companies adopt effective quality management systems.
These standards encompass a wide range of criteria, including:
- Material Specifications: Guidelines governing the composition and purity of tungsten carbide.
- Testing Methods: Protocols for evaluating material properties like hardness and wear resistance.
- Documentation: Requirements for record-keeping to demonstrate compliance with quality processes.
By adhering to these international standards, manufacturers can guarantee that their products meet the necessary performance expectations, helping them gain trust within their customer base.
Certifications and Compliance
Certifications serve as tangible proof that a manufacturing process aligns with established quality standards. Various entities offer certifications that signal compliance. For instance, compliance with ISO standards or specific industrial certifications can reassure customers about product quality.
Certifications often require rigorous testing and evaluation. Manufacturers must undergo periodic audits to maintain their certified status. This ongoing scrutiny helps ensure continuous improvement in quality practices.
Key benefits of pursuing certifications include:
- Increased Credibility: A certification enhances the reputation of the manufacturer, bolstering consumer trust.
- Market Access: Many industries require specific certifications before products are accepted in the market.
- Operational Excellence: Organizations that focus on compliance often experience improved operations and reduced waste.
Assessing Tungsten Carbide Quality
Assessing tungsten carbide quality is fundamental to understanding its performance and applications. The integrity of this material plays a pivotal role in industries ranging from manufacturing to aerospace. Therefore, it is crucial to have clear standards and methods for evaluating the quality of tungsten carbide.
A consistent assessment process helps manufacturers ensure that their products meet industry requirements. It creates a framework for quality control, which is vital for maintaining the safety and reliability of end products.
Testing Methods and Techniques
Evaluating tungsten carbide quality typically involves various testing methods. These methods can be categorized into non-destructive and destructive techniques. Non-destructive testing is preferred for maintaining the material integrity while assessing its properties.
- Visual Inspection: This is often the first step. Inspectors look at surface abnormalities like cracks or pits. This method is simple but effective.
- X-ray Diffraction: This technique helps determine the crystalline structure in tungsten carbide. It can assess any phase changes that might affect quality.
- Hardness Testing: Tools like Vickers and Rockwell testers are used to measure hardness. These tests determine how well the material can withstand abrasion.
- Microstructure Analysis: Using scanning electron microscopy, one can observe the microstructure of tungsten carbide. This method provides insight into both composition and uniformity.
Each method offers unique insights that contribute to a comprehensive understanding of the material's quality. Integrating these tests leads to more informed decisions within manufacturing processes.
Evaluating Purity Levels
Purity levels are another crucial aspect when assessing tungsten carbide quality. Impurities can significantly influence the performance characteristics of the material. Therefore, knowing the composition is essential.
- Chemical Analysis: Techniques like mass spectrometry can ascertain the elemental composition. High-purity tungsten carbide typically contains 94% tungsten and 6% carbon, with few impurities.
- Contaminant Testing: Tests can detect other metallic contaminants that may affect mechanical properties. This is vital to ensure a high standard of quality.
- Sintering Analysis: The sintering process can be altered by the presence of impurities. Proper evaluation post-sintering can provide insights into the overall quality of the material.
A well-evaluated purity level of tungsten carbide not only enhances performance but also extends the material life-span in applications.
Accurate evaluation techniques for purity and performance metrics are essential for ensuring that tungsten carbide meets the high standards expected in various industries. Emphasizing rigorous testing and analysis will improve product performance and safety.
Applications of Tungsten Carbide
Tungsten carbide stands as one of the most valuable materials across multiple industries. Its unique properties, such as high hardness, excellent wear resistance, and resilience to high temperatures, make it a material of choice for various applications. Understanding these applications not only highlights the versatility of tungsten carbide but also provides insight into its critical role in manufacturing processes and the production of durable goods.
Aerospace Industry Uses
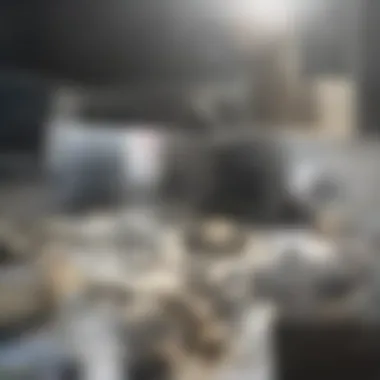
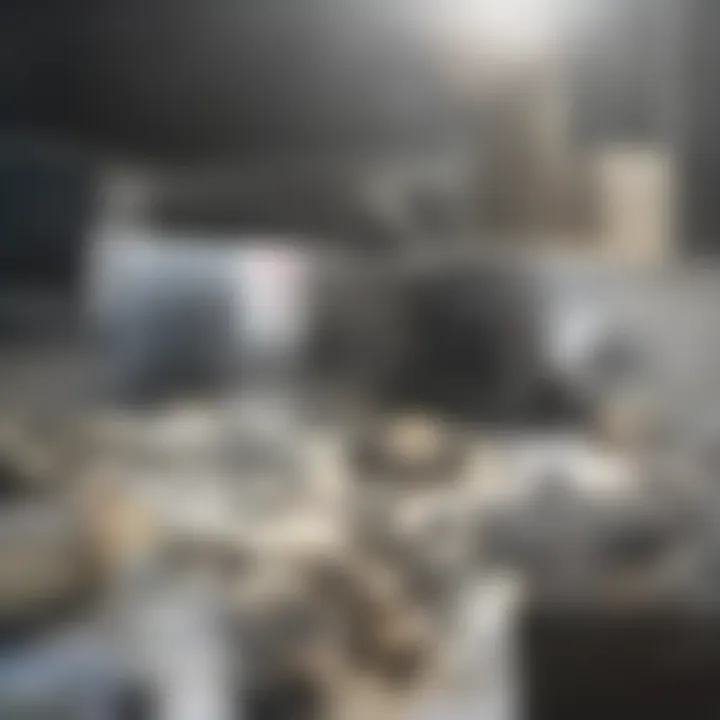
In the aerospace sector, tungsten carbide is instrumental in enhancing the performance of different components. Turbines, landing gear, and various fasteners benefit from tungsten carbide's strength-to-weight ratio.
- Durability: Components made from tungsten carbide can withstand substantial wear and tear during operation, which is crucial in high-speed flight situations.
- Heat Resistance: With its ability to endure extreme conditions, tungsten carbide parts are less likely to fail due to thermal stress. This is a significant advantage in aerospace applications where engine temperatures can reach daunting levels.
- Precision Engineering: Aerospace demands high precision and reliability. Tungsten carbide enables the production of tight-tolerance components, ensuring operational safety.
The adoption of tungsten carbide in aerospace shows how the material can both improve performance and extend the lifespan of vital components.
Cutting Tools and Machinery
One of the most prominent uses of tungsten carbide lies in cutting tools and machinery. Industries rely on its exceptional hardness and ability to retain a sharp edge. This material enhances the efficiency and effectiveness of manufacturing processes.
- Tool Longevity: Tungsten carbide tools last longer than traditional steel tools, significantly reducing the cost and frequency of replacements.
- Increased Cutting Speed: Thanks to its hardness, tungsten carbide allows for faster cutting speeds without compromising on quality. This efficiency is vital in production environments where time is money.
- Versatility: Cutting tools can vary in applications, from drilling to milling and turning, all benefiting from tungsten carbide's properties. As a result, manufacturers enjoy the flexibility of using a single, incredibly durable material in various tools.
Jewelry and Aesthetic Applications
The aesthetic qualities of tungsten carbide have made it popular in the jewelry sector, particularly in wedding bands and fashion pieces. Its unique appearance, along with its durability, attracts a wide range of consumers.
- Design Variety: Jewelers can create intricate designs due to tungsten carbide's malleability when heated. Different finishes and textures are possible, enhancing aesthetic appeal.
- Hypoallergenic Qualities: Tungsten carbide is a suitable option for those with sensitive skin. It does not react with the body, making it an appealing choice for jewelry that must be worn daily.
- Scratch Resistance: Unlike traditional gold or silver, tungsten carbide jewelry resists scratching. This feature maintains the piece's integrity and appearance over time.
The multifaceted applications of tungsten carbide underline its importance across various industries. From aerospace to industrial tools and jewelry, its unique properties provide a profound advantage, ensuring that products are both reliable and long-lasting.
Common Myths and Misconceptions
In the realm of tungsten carbide, various misconceptions can cloud its true nature and quality. Addressing these myths is essential for understanding its real benefits and applications. Recognizing these misunderstandings can help both users and producers make informed choices when selecting or working with tungsten carbide products. This section will explore two of the most common inaccuracies that surface in discussions about tungsten carbide: the durability myths and the assumptions about cost versus quality.
Durability Myths
One prevalent myth is that tungsten carbide products are completely scratch-proof or indestructible. While tungsten carbide does boast high hardness and excellent wear resistance, it is not immune to damage. For instance, impacts or extreme conditions can lead to chipping or breakage. Despite its impressive durability, a user’s expectations should be grounded in reality. Understanding that no material is truly impervious is vital.
Another related misconception suggests that tungsten carbide is suitable for all applications. While it excels in various industries, it may not be the best choice for all uses. Some applications requiring flexibility or specific performance under varying conditions may find other materials more advantageous. Therefore, opting for tungsten carbide should come after evaluating the material against the specific demands of the intended application.
Cost vs. Quality Assumptions
Many individuals assume that a higher price tag directly equates to superior quality in tungsten carbide products. While price can reflect quality, it is not an absolute indicator. Costs may vary for many reasons, including brand reputation and manufacturing processes. It is quite possible to find high-quality products at competitive prices if one looks beyond mere branding.
Moreover, there's a belief that lower-cost options imply inferior performance. This is not always true. Several manufacturers offer reliable tungsten carbide products that meet industry standards without engaging in premium pricing strategies. Thus, consumers should focus on specific characteristics and certifications rather than just the price.
Quality should be evaluated on tangible attributes rather than perceptions based solely on cost.
Future Trends in Tungsten Carbide Manufacturing
The landscape of tungsten carbide manufacturing is evolving rapidly. Understanding future trends is crucial to staying ahead in industries that rely on this material. Innovations in technology and sustainability are at the forefront of these trends. These developments not only enhance the quality and performance of tungsten carbide but also address environmental concerns.
Advancements in Technology
New technologies are reshaping how tungsten carbide is produced. Advanced manufacturing techniques, such as additive manufacturing, are becoming more prevalent. This method allows for creating complex shapes and designs with minimal waste. By using techniques like 3D printing, manufacturers can achieve higher precision. This leads to more efficient use of materials and reduces overall production costs.
Moreover, innovations in coating technologies are noteworthy. Enhanced coatings can significantly improve the wear resistance and longevity of tungsten carbide products. This is particularly valuable in applications where abrasiveness is a concern, like cutting tools.
The transition to automated systems also indicates the industry's movement towards increased efficiency and reduced human error in production.
Sustainability Considerations
Sustainability is becoming a critical factor in tungsten carbide manufacturing. The industry is under increasing pressure to minimize its environmental impact. This has led to a stronger focus on recycling and reusing tungsten carbide materials. Many companies are now implementing programs to reclaim used carbide for reuse in new products. This not only conserves resources but also reduces waste significantly.
Furthermore, exploring alternative raw materials and more energy-efficient processes can lessen the carbon footprint associated with tungsten carbide production. Investment in research for more sustainable mining practices is also crucial. Developing a clear plan to address these considerations leads to better regulatory compliance and improved public perception.
End
In summary, tungsten carbide is not merely a strong material; it also offers various qualities that are vital for its effectiveness. The discussions on purity levels, hardness metrics, and wear resistance have highlighted how lean material compositions can lead to superior performance in tools, jewelry, and even aerospace components.
Adhering to international standards ensures that products made from tungsten carbide meet necessary specifications. This opens avenues for its use in both high-stakes industrial applications and fine aesthetic pieces.
Besides, recognizing common myths and misconceptions surrounding tungsten carbide solidifies its reputation. By addressing the durability and cost versus quality debates, one can make informed choices when selecting tungsten carbide products.
Moreover, the foresight into future trends prepares stakeholders for advancements that may reshape the industry. Sustainable practices combined with technological innovation point to a promising horizon.