Welding Techniques and Innovations in Aerospace
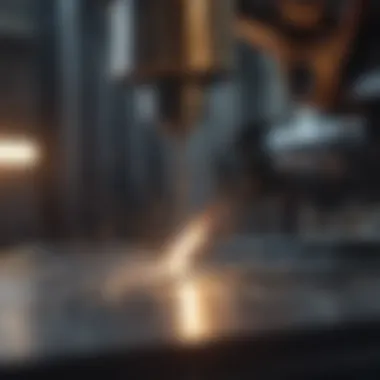
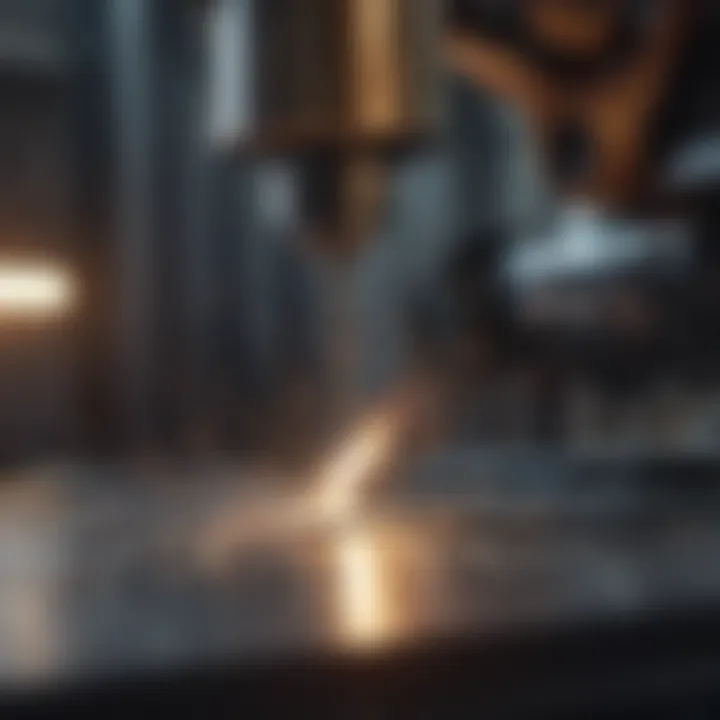
Intro
Welding holds a pivotal role in the aerospace industry, where the stakes are astoundingly high. It's not just about joining materials; it’s about ensuring that every fusion of metal meets rigorous safety standards. In an arena where precision matters more than anything, understanding the fundamental techniques, applications, and innovations in aviation welding becomes critical for students, scholars, and professionals alike. This article aims to untangle the intricate choreography of welding methods used in crafting aircraft, while also casting a light on the innovations that propel the field forward.
The scope of welding in aerospace is as vast as the sky itself. From manufacturing airframes to maintaining spacecraft, the welding processes utilized are diverse and ever-evolving. As we dive into the technical specifications and the materials that go into these processes, we’ll also reflect on the advancements that enlarge the horizons of what’s possible in aerospace welding. This intricate dance of technology and craftsmanship serves to remind us that behind every smooth flight, there exists a network of strong, resilient connections achieved through expert welding techniques.
The following sections will scaffold a comprehensive guide, detailing key concepts, current practices, and future directions in the welding domain within aerospace.
Prologue to Aerospace Welding
Welding in the aerospace field is more than just a technique; it's a vital cornerstone of modern aircraft design and maintenance. Focused on precision and safety, aerospace welding ensures the structural integrity of aircraft, which, in turn, affects not just the performance of the vehicle but ultimately the lives of those onboard. In this fast-paced domain, where every ounce of weight matters, the importance of reliable and effective welding cannot be overstated.
Understanding the Aerospace Sector
To grasp the significance of welding within aerospace, it's crucial to first understand the sector itself. The aerospace industry encompasses the design, development, and production of aircraft, spacecraft, and related systems. Functioning at the intersection of cutting-edge technology and rigorous safety standards, aerospace professionals must navigate a complex landscape characterized by innovation, regulation, and performance requirements.
Every segment within aerospace, from commercial airliners to military jets, demands high-quality manufacturing processes. Welding, therefore, holds a prominent place, contributing to everything from the lightweight frames of passenger aircraft to the intricate components of rocket systems. This industry thrives on precision, and welding technologies continually evolve to meet ever-changing challenges and opportunities in that regard.
Importance of Welding in Aerospace
The importance of welding in aerospace can be encapsulated in several key aspects:
- Structural Integrity: At its core, welding provides the essential bonds that hold various aircraft components together. Each weld must withstand immense forces and temperature variations during flight.
- Weight Reduction: Aerospace engineers are constantly on the lookout for ways to reduce weight. Advanced welding techniques, such as laser welding, allow for stronger, lighter joints that contribute to overall efficiency.
- Innovation: As new materials like composites and advanced alloys emerge, welding processes must adapt. Innovative welding technologies can enhance performance in areas like fuel efficiency and durability, which are critical in the aerospace arena.
- Safety Standards: Aviation is one of the safest modes of transport, largely due to stringent manufacturing processes. Welding is closely monitored to meet regulatory standards, ensuring that every weld contributes to an aircraft's safety.
"In the aerospace sector, a strong, reliable weld is not just a mechanical bond; it’s a commitment to ensuring safety and performance at 30,000 feet."
Understanding these points gives clarity regarding why welding techniques and choices in materials can have far-reaching implications in the aerospace landscape. This section sets the stage for exploring various welding processes and their applications, which are pivotal in driving the advancements that define the industry today.
Types of Welding Processes in Aerospace
Welding processes play a pivotal role in aerospace manufacturing, forming the backbone of how critical parts of aircraft come together. The selection of a welding technique is not simply a matter of preference but is deeply rooted in the materials used, the required precision, and the ultimate function of the components being fabricated. Each process offers distinct advantages, making it crucial for engineers and manufacturers to understand the nuances and applications of various techniques. This section dives into some of the most widely employed welding processes in the aerospace industry, providing detailed insights into their specific benefits, considerations, and suitability for complex aerospace applications.
Mig Welding
MIG welding, short for Metal Inert Gas welding, is one of the most prevalent methods utilized in aerospace applications. This process makes use of a continuously fed wire electrode which melts at high temperatures to create a weld. The efficiency of MIG welding is one of its primary advantages. It allows for high-speed welding and is particularly effective on thinner materials, which are commonly found in the aerospace industry.
The ability to weld a variety of materials, including aluminum and stainless steel, makes MIG welding highly versatile. However, it’s not without its challenges. One must carefully control the heat input to prevent overheating and warping of components. Furthermore, gas selection is critical; a mixture of argon and carbon dioxide is usually preferred to shield the weld area from contaminants.
- Benefits of MIG Welding:
- High deposition rate
- Versatile across various materials
- Less skilled labor required compared to other methods
Tig Welding
TIG welding, or Tungsten Inert Gas welding, presents another widely used technique in the aerospace sector. Unlike MIG, this method relies on a non-consumable tungsten electrode to produce a weld, while a filler rod is used separately. This method is renowned for its precision and ability to create strong, clean joints, making it suitable for high-strength applications, often required in aerospace architectures.
The major downside is its slower pace compared to MIG welding, making it less suitable for mass production. However, when it comes to aircraft fuselage, engine components, and other critical structures, the benefits of strength and durability are worth the time invested.
In terms of materials, TIG welding shines when working with tricky alloys, notably titanium and exotic metals, which are frequently found throughout aerospace design.
- Key Features of TIG Welding:
- Superior control of the weld puddle
- Ideal for thicker materials
- Produces minimal spatter
Spot Welding
Spot welding is particularly prominent in assembling the wings and fuselage of many aircraft, especially in the realm of aluminum and some stainless steel structures. This process fuses metal parts at specific points using electrical resistance, which provides quick and effective joining solutions.
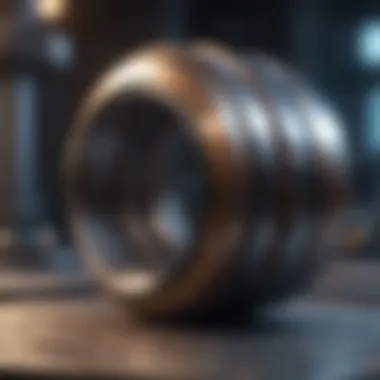
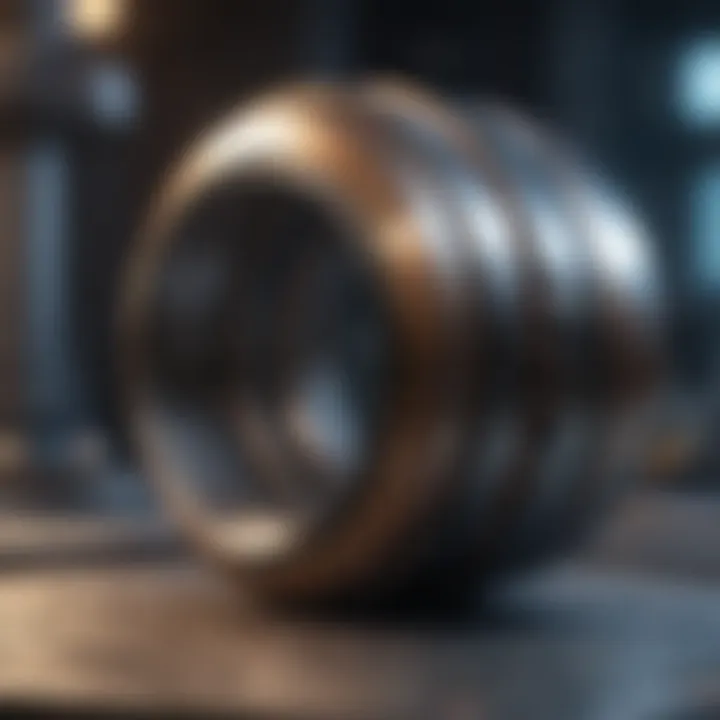
While spot welding isn't primarily regarded for its aesthetic, its speed and simplicity make it invaluable, especially in repetitive jobs where efficiency is key. However, its best applications are often limited to lap joints and tacking, leaving larger areas needing reinforcement or additional welding methods.
- Distinctive Aspects of Spot Welding:
- Ultra-fast operation
- Tack joints hold well under stress
- Requires specific tooling for efficiency
Laser Welding
Emerging as an advanced technique, laser welding is gaining traction due to its extraordinary precision and capability to work with minimal heat. Laser energy melts the material at very focused points allowing for clean and controlled welding of complex shapes. It is particularly useful for intricate designs, such as those found in aerospace gearboxes or sensor housing.
While it has considerable upfront costs due to equipment and setup, the resulting weld joints typically exhibit exceptional strength and quality, ensuring the longevity and safety of critical components in the aerospace landscape.
- Highlights of Laser Welding:
- High precision with minimal thermal distortion
- Flexibility to weld unique geometry shapes
- Suitable for automation in high-volume production
In the grand scheme of aerospace manufacturing, understanding the various welding processes and their implications helps in choosing the right technique for each specific application. The decision is influenced not only by the type of materials involved but also by the intended use and regulatory compliance requirements. As advancements continue, the tools and methods of welding in aerospace will likely evolve, leading to even greater efficiencies and innovations.
Welding Materials in Aerospace
Welding materials are the cornerstone of any aerospace application. The selection of appropriate materials determines not just the efficacy of the weld, but also the integrity and longevity of the component being created. Each type of welding material imparts unique characteristics, making it necessary for engineers and technicians to thoroughly understand these options. The significance here is twofold: first, there are stringent performance requirements in aviation, and second, the safety aspect cannot be overstated. A compromised weld could mean disaster in flight, which underscores the gravity of selecting the right welding materials.
Aluminum Alloys
Aluminum is often the metal of choice in aerospace manufacturing due to its lightweight yet strong properties. The most common alloys used in welding are 2024 and 7075. These alloys are prized for their strength-to-weight ratio, making them ideal for aircraft fuselage and wing structures. Notably, heats of strength from aluminum alloys can be enhanced with proper welding techniques such as pulsed TIG welding. This method reduces heat input and consequently minimizes distortion, preserving material properties.
Moreover, aluminum's natural resistance to corrosion makes it a sturdy choice for aerospace applications, yet using it requires consideration of factors like heat treatability and the potential for weld softening. A knowledgeable technician can make the most of these materials by understanding the metallurgy behind them and selecting the right filler, which plays a crucial role in achieving a strong bond.
Titanium Alloys
In recent years, titanium alloys have grown in prominence within the aerospace field. Alloys such as Ti-6Al-4V are particularly favored for their high strength and resistance to corrosion and fatigue. The high melting point of titanium presents unique challenges during welding. Techniques like GTAW (Gas Tungsten Arc Welding) or electron beam welding are often employed. These methods provide the precision needed to manage the reactivity of titanium, especially in the presence of oxygen, which can lead to detrimental effects on the weld quality.
One of the notable benefits of titanium is its strength when alloyed properly. This quality leads to reduced weight, ultimately enhancing fuel efficiency in aircraft. However, the cost of titanium and its alloys is generally higher than traditional materials; hence, applications tend to focus on critical components where performance is non-negotiable, such as in engines or landing gear.
Steel Grades
Steel is another staple in aerospace manufacturing, particularly for components that require notable strength and toughness. Different steel grades like 4130 and 4340 are used based on the structural requirements. Steel offers a balance of mechanical properties and is much more forgiving to weld than alloys such as titanium. However, it presents its own considerations, especially concerning the heat-affected zone (HAZ).
Welders must be cautious of potential warping and cracking that can arise from improper heat management during processing. Implementing pre-heating methods can significantly mitigate these risks, as it minimizes thermal shock during cooling. Steel's resilience makes it a go-to material for areas like landing gear assemblies where durability is key.
Composite Materials
Composite materials have gained traction in recent aerospace applications due to their unique properties, blending lightness with incredible strength. Carbon fiber and fiberglass composites are used in various aircraft structures, including wings and fuselages. However, the welding of composites requires specialized processes, typically involving adhesives or mechanical fastening rather than traditional welding methods.
Despite this limitation, the use of composites is transformative. They are not only lighter than metals but also exhibit excellent fatigue resistance and stiffness. Integrating composite materials can lead to significant improvements in fuel efficiency and the shifting of traditional design paradigms in aerospace engineering.
In summary, the materials used in aerospace welding dictate much more than just the end product. The alloys chosen impact weight, strength, and ultimately safety. As the aerospace sector pushes for advancements, understanding the nuances of these materials is paramount to progress.
Applications of Welding in Aerospace
Welding plays a pivotal role in the aerospace sector, as it connects various components that make up aircraft, missiles, and spacecraft. The applications of welding in this industry are diverse, reflecting the complexity and precision required to ensure the safety and functionality of aerospace vehicles. Understanding these applications offers insights not just into the manufacturing process but also into the operational integrity of these machines throughout their lifecycle. The benefits of welding in aerospace include enhancing structural integrity, enabling efficient production methods, and facilitating repairs and modifications.
Aircraft Structure Assembly
The assembly of an aircraft structure involves various welding techniques, crucial for ensuring the strength and durability of the airframe. Each weld contributes to the overall integrity, directly influencing an aircraft's performance and safety. For instance, during aircraft assembly, TIG welding is often favored for aluminum components due to its precision and control. The welder needs to pay attention to joint design, which demands high accuracy.
Moreover, the combination of aluminum alloys used in aircraft manufacturing makes welding more complex. Greater attention must be given to pre-weld treatments and post-weld inspections, ensuring that any residual stresses are managed effectively to minimize issues like warping or cracking. The perfection in these joints means the aircraft can withstand the enormous pressures experienced at altitude.
Engine Components Fabrication
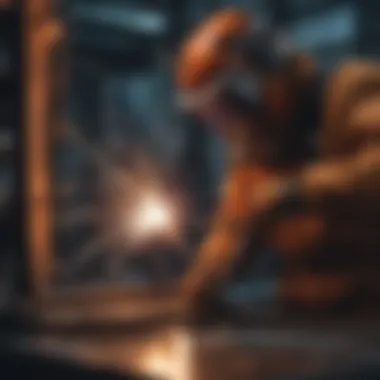
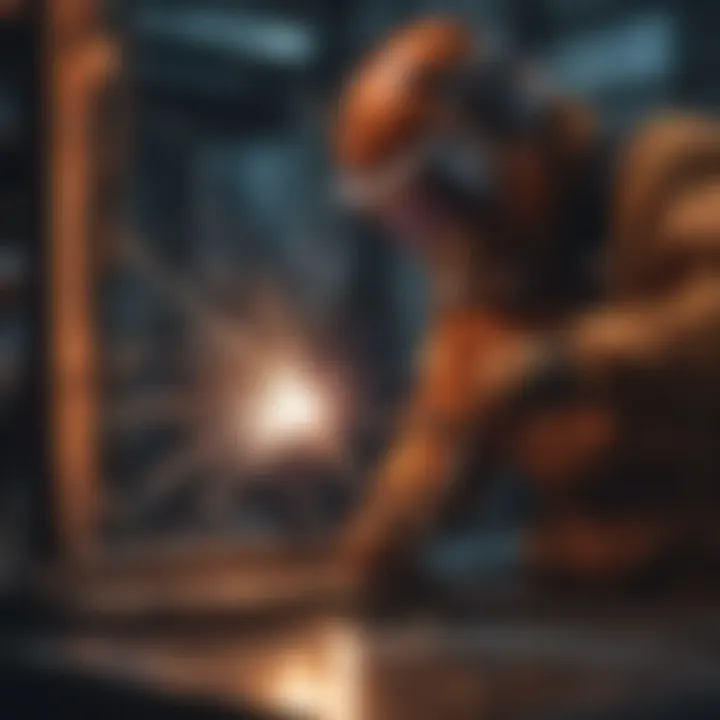
Welding contributes significantly in the fabrication of engine components, where the stakes are extraordinarily high. The materials used, such as titanium and high-strength steel, require precise welding techniques that can withstand extreme operating temperatures. Special processes like laser welding are increasingly employed for critical components. This technique not only provides stronger joints but also enables the assembly of intricate designs that traditional methods might struggle with.
Each part of an engine—from turbine blades to casings—must adhere to strict tolerances and specifications. These highly engineered components play a crucial role in the efficient operation of aircraft engines. The performance of these welds directly affects not just performance but also maintenance costs and safety, thus underscoring the importance of precision in the welding process.
Repair and Maintenance Procedures
In the life cycle of an aircraft, repair and maintenance are ongoing processes that are vital to ensuring operational readiness and flight safety. Welding surfaces often come into play here, whether it’s addressing stress fractures on aluminum skins or rectifying damages that occurred during operations.
Using techniques like MIG welding, aviators and maintenance crews can repair various structures relatively quickly. However, thorough assessments are critical before choosing to repair over replace, as the integrity of the weld must meet the original specifications. The importance of welding in maintenance cannot be understated; it’s not just about fixing an issue, but rather about restoring strength and safety.
"Proper welding practices in maintenance can extend an aircraft's lifespan significantly, making it a cost-effective solution for operators."
Innovative Designs and Prototyping
The innovative edge of aerospace applications is reflected in the way welding is leveraged not just for assembly but also for the creation of prototypes and unique designs. Techniques like additive welding are coming into play, where materials are added rather than subtracted, allowing for more radical design changes. This method opens doors to new concepts that may have been impractical with traditional methods. Prototyping in particular benefits from this, where rapid iterations can yield significant improvements in design and functionality.
Additionally, as aerospace engineers push for lightweight structures to improve fuel efficiency and performance, the choice and application of welding techniques become even more critical. New materials and innovative welding processes are constantly evolving, shaping the future of aircraft design and performance in a way previously thought impossible.
Challenges in Aerospace Welding
In the aerospace industry, welding is not just a routine operation; it plays a pivotal role in ensuring the integrity and functionality of aircraft components. However, the process is fraught with hurdles that can significantly impact the overall quality and safety of the finished product. Understanding these challenges is crucial for professionals engaged in welding operations and for those in engineering roles who oversee manufacturing processes.
Material Deformation
A major concern when welding in aerospace is material deformation. When subjected to high temperatures, metals can expand, which often leads to unwanted distortions during the cooling phase. In the context of aerospace, where precision is as critical as it gets, this deformation can have dire consequences.
For instance, consider an aircraft wing, which must maintain precise geometry to ensure aerodynamic efficiency. Deformation during the welding process can cause misalignment or inconsistencies in the wing structure. Thus, engineers may employ various strategies such as pre-heating the metal or implementing controlled cooling techniques to mitigate these risks. The key takeaway here is the necessity for meticulous planning and execution to minimize deformation and maintain tight tolerances required for aerospace applications.
Weld Quality Assurance
The second cornerstone of challenges in aerospace welding is weld quality assurance. The integrity of welded joints must meet remarkably high standards due to the operational demands placed on aircraft. A subpar weld can lead to catastrophic failures, and as a result, the industry mandates rigorous inspection processes.
In practical terms, this involves various testing methods, including:
- Non-destructive testing (NDT) to evaluate the integrity of the weld without damaging it.
- Visual inspections to catch any irregularities such as cracks or incomplete fusion.
- Metallographic examinations to understand the microstructure of the weld.
The importance of implementing a robust quality assurance protocol cannot be overstated. The airplane's performance and safety hinge on these inspections, ensuring that each weld meets aerospace specifications before the aircraft takes to the skies.
Heat Affected Zones
Another significant challenge in aerospace welding concerns the heat affected zones (HAZ). When welding occurs, the heat generated doesn't just affect the weld area but also the surrounding material. This results in a HAZ where the mechanical properties of the base material can be altered, potentially compromising strength and resilience.
Issues such as grain coarsening or changes in phase can create weak points, rendering parts more susceptible to failures. As such, it becomes essential to manage the welding parameters carefully—heat input must be controlled to limit the size of the HAZ.
"Every weld is a story; learning how to tell it accurately through careful control is key to safeguarding the future of our aerospace fleet."
The strategies to combat issues arising from HAZ can include selecting appropriate filler materials, using advanced welding methods that minimize heat exposure, or employing post-weld heat treatments. These are not just best practices; they're integral to achieving longevity and reliability in aerospace components.
In summary, the challenges associated with welding in aerospace cannot be taken lightly. Material deformation, maintaining weld quality assurance, and managing heat affected zones are critical areas that require ongoing attention. Addressing these challenges head-on leads to safer, more capable aircraft, which ultimately benefits both manufacturers and the flying public.
Regulatory Standards and Safety Requirements
Welding in the aerospace industry is not just a matter of skill with the torch; it’s also a strict adherence to regulatory standards and safety requirements. The complexity of aerospace structures and their demanding performance criteria require that every weld is executed with precision and within specified guidelines. This section delves into the importance of these standards and how they underpin the safety and reliability of aerospace components.
International Standards in Aerospace
In the realm of aerospace, international standards govern how welding tasks are performed. Regulatory bodies like the American Society for Testing and Materials (ASTM) and the International Organization for Standardization (ISO) specify criteria for weld quality, materials, and testing. For instance, ASTM standards dictate the chemical composition of aluminum used in aerospace components, ensuring consistency and reliability.
Adhering to these international standards guarantees:

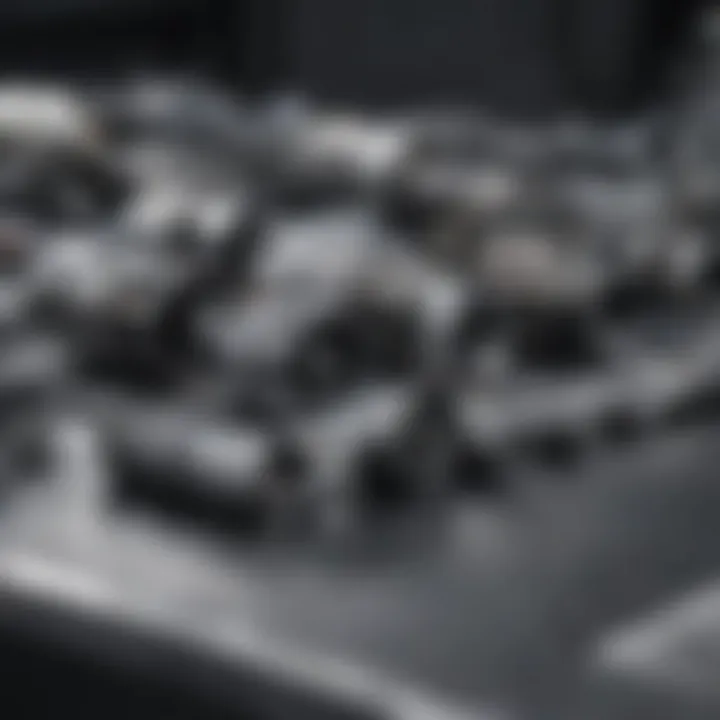
- Safety: The most crucial aspect of these standards is that they minimize the risk of failure, which can lead to catastrophic incidents. An inadequate weld could spell disaster when all that’s between a passenger and the sky is a structural component.
- Interoperability: Consistently applied standards allow for parts made by different manufacturers to fit together seamlessly, ensuring safety and operational efficiency.
- Traceability: Standards require thorough documentation. This not only facilitates quality assurance but also allows for tracing any weld back to its origins, vital in the case of a defect or failure.
These international regulations ensure a baseline level of quality and safety, allowing professionals in the field to have confidence that they are operating under best practices.
Quality Control Protocols
Quality control in aerospace welding is non-negotiable. Simply having standards isn’t sufficient; they must be actively enforced through rigorous protocols. Regular inspections, testing, and certifications are critical in maintaining the integrity of welds. Here are some key elements found within quality control protocols:
- Visual Inspections: Inspectors examine welds for immediate visible defects, such as cracks, undercuts, or incomplete fusion.
- Non-Destructive Testing (NDT): Techniques like ultrasonic testing or radiography are employed to unveil internal defects that the naked eye wouldn’t catch.
- Weld Procedure Qualifications (WPQs): Before welders can start on critical joints, their welding procedures must be tested and approved. This often includes validating the parameters that define the weld process.
- Continuous Monitoring: Using real-time sensors and data logging, aerospace companies can monitor welding processes as they happen, catching potential issues before they escalate.
Implementing solid quality control protocols not only meets regulatory demands but fosters a culture of safety and excellence within the workforce. As any seasoned professional in aerospace will tell you, cutting corners in quality controls can lead to dire consequences far beyond immediate costs.
"When it comes to aerospace welding, there’s no room for half-measures. Standards and safe practices are what keep the skies safe for everyone."
Overall, the interplay between regulatory standards and quality control protocols creates a robust framework that ensures aerospace welding is performed to the highest standards available. The commitment to these practices reflects the industry's dedication to safety and reliability in aircraft performance.
Future Trends in Aerospace Welding
In the rapidly evolving landscape of aerospace technology, the processes and technologies underpinning welding have become increasingly pivotal. As the demand for more advanced aircraft, heightened safety standards, and sustainable manufacturing practices rises, the future of welding in aerospace is geared toward innovation and efficiency. This section will shed light on the emerging trends that are set to transform the aerospace welding sector, focusing on automation, additive manufacturing, and advanced welding technologies.
Automation and Robotics
Automation is revolutionizing aerospace welding, bringing a host of benefits. The integration of robotic systems into welding processes can significantly enhance precision and consistency. Welding robots can repeat complex operations with a level of accuracy that is difficult for human hands to match. This is particularly crucial in aerospace, where even a slight variance can lead to major failures in structural integrity.
Moreover, these automated systems can operate continuously, reducing downtime and boosting production rates. This is a game changer when manufacturers need to meet stringent production deadlines while ensuring quality. For instance, a high-profile aerospace company has already implemented robotic welding systems that reduced production time by up to 40%, a striking improvement in efficiency.
The consideration of worker safety is another factor propelling automation. Robotic systems can take on tasks in hazardous environments, protecting human workers from exposure to harmful materials or conditions. This shift not only safeguards employees but also adheres to evolving safety regulations.
Additive Manufacturing Techniques
Additive manufacturing, often referred to as 3D printing, presents exciting possibilities for the aerospace industry. This method allows for the creation of complex geometries that traditional welding processes may struggle to achieve. Aerospace components can now be produced with lightweight, optimized designs, drastically reducing material waste.
Using techniques like directed energy deposition, manufacturers can weld metal layers directly onto pre-existing parts, effectively repairing damage or enhancing structures. This application has great implications for maintenance and repair operations, ensuring aircraft remain in airworthy condition without the need for complete part replacement.
However, incorporating additive manufacturing demands a thorough understanding of the materials and processes involved. Engineers need to navigate challenges related to weld quality and integrity of additively manufactured components to ensure they meet the rigorous standards of the aerospace sector.
Advanced Welding Technologies
As technologies advance, so too do the methods used for welding in aerospace applications. Techniques such as hybrid laser-arc welding are gaining traction due to their ability to combine the benefits of both laser and traditional arc welding. This approach provides deeper penetration and higher speed, allowing for faster join times without compromising quality.
The use of advanced welding technologies also emphasizes the need for continual training and adaptation of the workforce. Skilled welders must be familiar with these new techniques to fully leverage their potential. Potential companies are more likely to invest in training programs to ensure their workforce is knowledgeable about these advanced methodologies.
In summary, the future of aerospace welding is a convergence of automation, additive manufacturing, and advanced welding technologies. This intersection holds great promise for enhancing efficiency, safety, and innovation across the aerospace sector.
The emphasis on these forward-thinking trends is not just about keeping up with the competition; it's about setting the stage for groundbreaking advances in aircraft design, production, and maintenance. The integration of these technologies is destined to shape the future of the aerospace industry, leading to safer, more reliable, and more efficient aircraft.
The End
As we reach the end of our exploration into the intricate world of welding in aerospace, it’s pivotal to recognize the substantial role that welding plays in shaping the future of this industry. The article has detailed various aspects such as techniques, applications, and innovative trends that highlight the essence of welding.
Summary of Key Points
In this discussion, we underscored several critical components:
- Techniques: Various welding methods like MIG, TIG, spot, and laser welding, each with its own peculiarities, provide the backbone of assembly and fabrication in aerospace.
- Materials: The choice of materials—ranging from aluminum and titanium to advanced composites—reveal the intricate balance between weight, strength, and durability considerations.
- Applications: We noted how welding is not just pivotal in the construction of aircraft structures but also in engine components, repair, maintenance, and innovation in designing.
- Challenges: Material deformation, maintaining weld quality, and managing the heat-affected zones were highlighted as significant hurdles that engineers must tackle continuously.
- Future Trends: Automation and advancements in additive manufacturing technologies are sending ripples through the traditional processes, pushing boundaries in precision and efficiency.
The breadth of information provided equips professionals and enthusiasts alike with the necessary insights into the dynamics of aerospace welding.
Implications for the Aerospace Industry
The implications of effective welding practices are far-reaching:
- Safety Enhancement: With stringent standards in place, exemplary welding not only ensures structural integrity but also enhances overall safety for passengers and crew.
- Cost Efficiency: Streamlined welding processes contribute to reduced manufacturing times and costs, significantly affecting the bottom line while maintaining product quality.
- Innovation Drive: As aerospace projects increasingly embrace advanced technologies, welding methods must adapt to support innovations, ensuring competitive edge against global players.
- Sustainability: Environmentally forward-thinking techniques reduce waste and promote recycling of materials, aligning with broader industry goals for sustainability.
In summary, as the aerospace sector strives for better performance, safety, and efficiency, the significance of welding cannot be overstated. This article serves as a stepping stone for deeper exploration into welding's vital contributions and its transformative potential. The future of aerospace welding holds promise, and navigating this landscape requires an informed and adaptable approach.