C-Scan Technology: Insights, Applications, and Future Trends
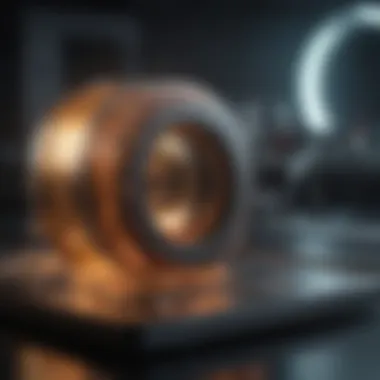
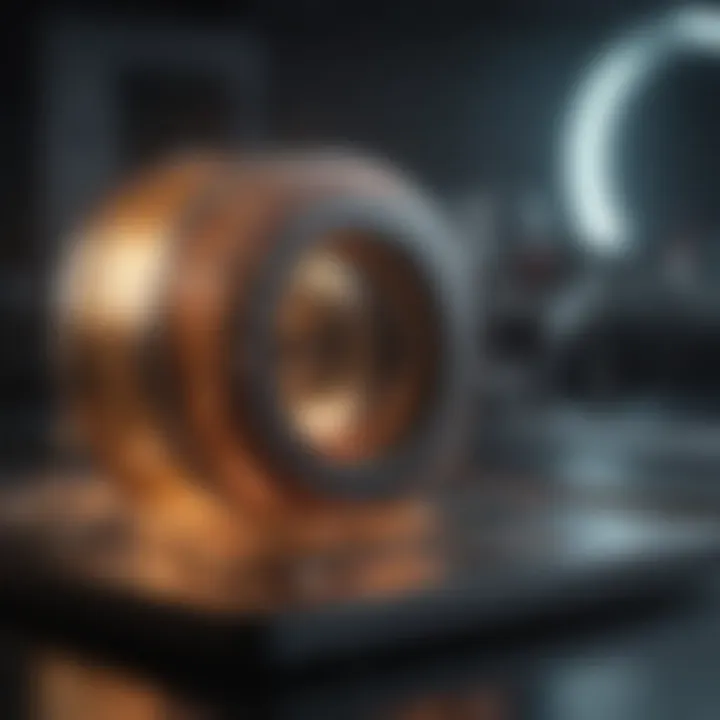
Intro
C-scan technology has carved a niche as a pivotal tool in the realm of non-destructive testing (NDT). This method stands out not just for its ability to assess material integrity without causing damage but also for its broad applicability across a spectrum of industries—from aerospace to automotive, and from civil engineering to manufacturing.
C-scan is based on the principles of ultrasonic testing, employing sound waves that penetrate materials to detect internal flaws or structural inconsistencies. Given the increasing demand for safety and durability in complex structures and systems, the importance of C-scan technology cannot be overstated. As we delve deeper into this subject, we'll explore the fundamental concepts, its operational mechanisms, and how it is reshaping the landscape of material inspection.
Key Concepts
Definition of Primary Terms
Understanding the terminology is crucial for grasping the intricacies of C-scan technology:
- C-scan: A method using ultrasound to create a two-dimensional image (or map) of the internal structure of a material. This technique highlights variations in thickness and identifies potential defects.
- Non-destructive Testing (NDT): Techniques used to evaluate material properties without causing any damage. C-scan is among the most effective NDT methods.
- Ultrasound: Sound waves with frequencies higher than the upper audible limit of human hearing, which is used in C-scan for detecting flaws.
Related Concepts and Theories
To appreciate the broader context of C-scan technology, it's important to consider several interrelated theories and concepts:
- Wave Propagation: The behavior of ultrasonic waves as they travel through various media, critical for interpreting results.
- Signal Processing: Techniques that enhance the data obtained from scanning, providing clearer and more precise results.
- Imaging Techniques: Various approaches, such as 2D and 3D imaging, that leverage C-scan data for advanced analysis.
As C-scan technology evolves, these related concepts will play increasingly significant roles in shaping effective evaluation methodologies.
Applications of C-Scan Technology
C-scan technology is not limited to a single field; its versatility allows for its application in diverse domains including but not limited to:
- Aerospace: Inspecting aircraft components for cracks or material fatigue, ensuring safety and compliance with stringent regulations.
- Automotive: Evaluating weld integrity in vehicle manufacturing, enhancing reliability and performance.
- Civil Engineering: Assessing the condition of bridges and buildings, identifying deterioration before it leads to catastrophic failures.
- Manufacturing: Checking the quality of manufactured products, from machinery parts to intricate assemblies.
Each of these applications showcases the critical role that C-scan technology plays in promoting safety and efficiency.
Future Directions
Gaps Identified in Current Research
Despite the advancements in C-scan technology, several gaps persist in current research. Notably:
- Integration with AI: There’s a growing potential for artificial intelligence to enhance the data analysis process, which remains underexplored.
- Real-Time Scanning: The ability to conduct scans in real-time and instantly analyze results warrants further investigation.
- Material Variability Studies: Additional research into how different materials affect C-scan results could lead to tailored solutions.
Suggestions for Further Studies
Future studies could aim to address these gaps by:
- Exploring the development and incorporation of sophisticated algorithms that empower real-time data interpretation.
- Conducting comparative studies of C-scan effectiveness across various industrial applications to establish best practices.
- Investigating advancements in transducer technology to improve sensitivity and resolution in detecting anomalies.
Intro to C-scan Technology
C-scan technology has grown into a crucial tool in various industries, forming the backbone of non-destructive testing methods. Its relevance cannot be overstated, as it provides a layer of safety and assurance in evaluating materials without compromising their integrity. Industries such as aerospace, automotive, and construction heavily rely on C-scan technology to identify potential issues before they escalate into costly problems. Understanding how C-scan functions and its historical context can enhance its application and integration into modern practices.
Definition and Overview
C-scan technology engages in extensive material evaluation by generating detailed images of subsurface structures. Unlike traditional methods, it allows for the visualization of internal defects, which might not be visible through conventional visual inspections. By employing different modes like ultrasonic or laser methods, C-scan systems create highly reliable and reproducible scans of test objects.
For example, using ultrasonic C-scan methods, high-frequency sound waves are transmitted into the material. The echoes reflected from internal flaws provide a visual representation through complex data processing techniques, often leading to clear graphical illustrations of the material's condition. This advantages operators by allowing them to make informed decisions based on the striking clarity of the data presented. C-scan's non-intrusive nature champions reliability for countless safety-critical applications.
Historical Development
The roots of C-scan technology spring from the early developments of non-destructive testing in the late 20th century. Initially, methods like radiography or magnetic particle testing were the go-to processes for flaw detection. However, with increased demand for safety and efficiency, the industry saw the advent of C-scan techniques in the 1970s.
As engineers faced the challenges of reliable inspections for materials with complex structures, they began adapting C-scan methods to various practices. The first notable advancements occurred in aerospace, where ensuring structural integrity was paramount. Engineers sought to enhance current defect-detection methods, leading to the development of automatic C-scan systems. This allowed operators to examine larger areas and gain comprehensive insights into materials' internal conditions much faster than before.
Eventually, the continuous improvements in imaging technology and data processing propelled C-scan into more realms, including civil engineering and automotive fields. Its methodology has consistently evolved; for example, modern C-scan systems incorporate digital processing, enhancing both accuracy and ease of interpretation.
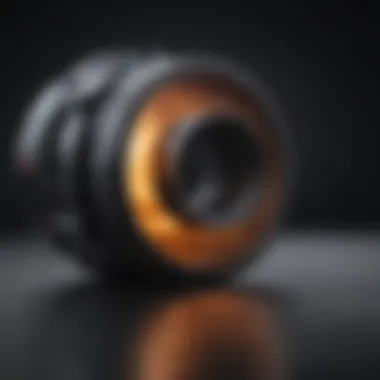
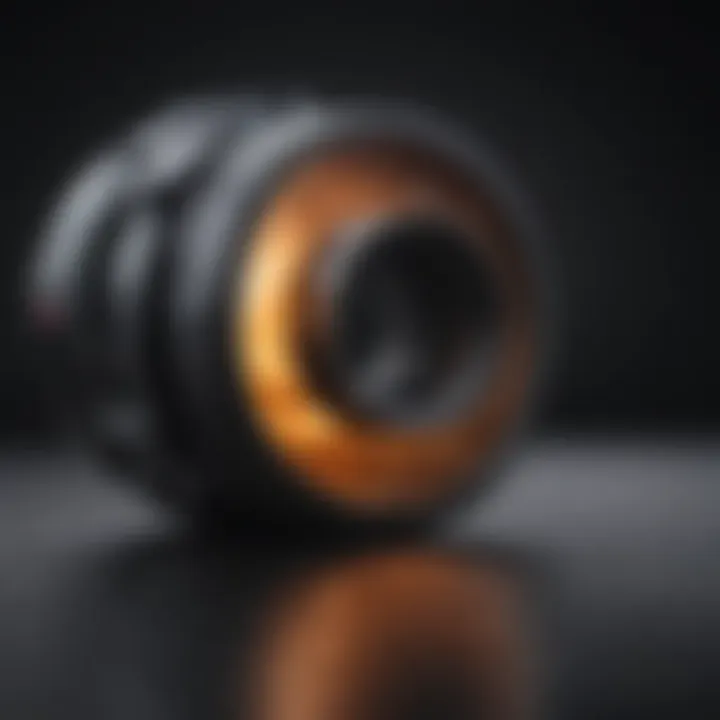
C-scan technology has paved the way for better safety standards, affirming material reliability across the board. As industries continue to evolve, understanding the technical nuances and historical significance of C-scan remains vital, not just for compliance but for pushing the envelope toward greater innovations in material evaluation.
Fundamentals of C-scan Operation
Understanding the fundamentals of C-scan technology is vital for anyone involved in material testing and evaluation. This section delves into the core principles that drive C-scan operation and explores the various types of C-scan technologies available today. By grasping these concepts, practitioners can leverage the benefits of C-scan effectively and address its challenges in real-world applications.
Principles of Imaging: How C-scan Works
C-scan operates on the principle of producing detailed images of a sample's internal structure by utilizing various forms of wave technology. Essentially, C-scan systems deploy a scanning mechanism that emits waves—be it ultrasonic, laser, or electromagnetic—into a material. The waves then reflect back to the sensor upon encountering different mediums or anomalies within the material. This creates an image that can be interpreted to evaluate material integrity.
The key to the operation lies in how these methods interpret the returned signals. The variation in the reflected waves—frequency shifts, amplitude changes, or phase changes—provides critical insights about the material's condition. Understanding how these signals correlate to structural issues is crucial for accurate analysis.
Types of C-scan Technologies
C-scan technology is not one-size-fits-all. Different types of C-scan methods cater to diverse needs depending on the material and inspection requirements. Below are three prevalent types of C-scan technologies:
Ultrasonic C-scan
Ultrasonic C-scan is regarded for its high precision in detecting internal flaws within materials, such as voids or cracks. Utilizing high-frequency sound waves, this method can penetrate deep into various substances, making it a favorite for industries where material integrity is paramount, such as aerospace and manufacturing.
The distinct characteristic of Ultrasonic C-scan is its ability to provide quantitative data on flaws, enabling engineers to assess not just the presence, but the size and significance of the defects. This capability is beneficial as it allows for informed decision-making about repairs or material degradation assessments. However, one limitation lies in its sensitivity to surface conditions, meaning operators must account for surface quality to achieve accurate results.
Laser C-scan
Laser C-scan introduces a fascinating approach by utilizing laser technology to evaluate surfaces. This method uses laser beams directed at the material's surface, which then measures the resulting wavelength variances to create a detailed map of surface integrity. Its key characteristic is the ability to achieve ultra-high resolution images, providing insights into even the smallest of surface defects.
Laser C-scan is often chosen for its minimal interaction with the material, which means it generally doesn't alter the material or cause damage during the inspection process. On the downside, it is typically less effective on thicker materials, as the laser may not penetrate deeply enough to assess subsurface conditions thoroughly.
Electromagnetic C-scan
Electromagnetic C-scan makes use of electromagnetic fields to inspect conductive materials. This method is particularly valuable in industries that work with metals, where it can detect surface and near-surface defects quickly. The fundamental aspect of Electromagnetic C-scan lies in its speed and efficiency; it can often cover large areas in a fraction of the time required by other methods.
One of the most notable features is its capability to function on a variety of material types without the need for direct contact. This makes it a preferred option in situations where access to the material is restricted or where traditional methods might cause damage. A challenge, however, is its limitation with non-conductive materials, where other C-scan technologies may have to be employed instead.
Overall, understanding these different C-scan technologies allows industries to choose the most favorable method based on their specific evaluation needs. Each method has its strengths and weaknesses, making it essential to analyze the particular application and required outcomes when selecting a C-scan approach.
C-scan technology continues to revolutionize non-destructive testing, ensuring materials are not just inspected, but thoroughly understood.
Industrial Applications of C-scan
C-scan technology holds immense significance across various industrial sectors. Servicing as a non-destructive testing method, C-scan is a valuable asset for maintaining the integrity and reliability of materials without compromising their utility. This section delves into the specific industries where C-scan is utilized, highlighting the advantages it brings and addressing considerations that companies must keep in mind.
Aerospace Industry
In the aerospace sector, the safety and reliability of components can never be overstated. C-scan technology plays a pivotal role here, allowing engineers and inspectors to assess materials for defects such as cracks or delaminations without inflicting damage. Airlines rely on C-scan to ensure that structural components like wing structures and fuselages are free from hidden flaws, which could lead to catastrophic failures.
- Robustness: Utilizing ultrasonic C-scan methods, which are adept at penetrating composite materials, inspectors can make accurate assessments.
- Regulatory Compliance: Compliance with safety regulations like FAA guidelines mandates rigorous testing, making C-scan not just beneficial but essential for certification.
With C-scan, faults can be detected swiftly, thus minimizing downtime and enhancing overall safety in aircraft operations.
Construction and Civil Engineering
Construction and civil engineering projects are profoundly influenced by C-scan technology, especially when inspecting welds and concrete structures. Given the immense stakes involved in building durable infrastructure, the importance of C-scan can't be overlooked.
- Quality Assurance: The ability to obtain clear images of internal structures and defects ensures that only quality materials are used in construction.
- Long-Term Cost Savings: Early fault detection saves costs in long-term maintenance and prevents costly overhauls or demolitions due to structural failures.
Additionally, as buildings and bridges age, C-scan helps engineers assess structural integrity, ensuring that they remain safe for public use.
Automotive Industry
In the automotive industry, where performance and safety directly correlate, C-scan technology is becoming increasingly vital. It’s used to evaluate everything from engine components to the structural integrity of the chassis.
- Material Evaluation: New advancements in C-scan, particularly with laser and electromagnetic methods, allow for thorough assessments of lightweight materials.
- Production Optimization: Automakers can streamline their production lines by incorporating C-scan testing to spot issues before they escalate into larger problems.
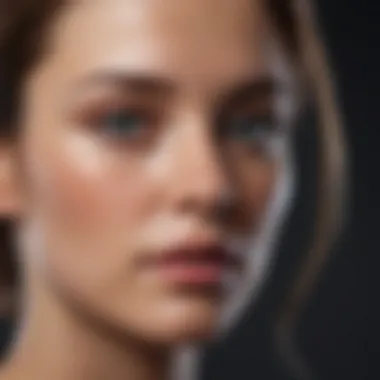
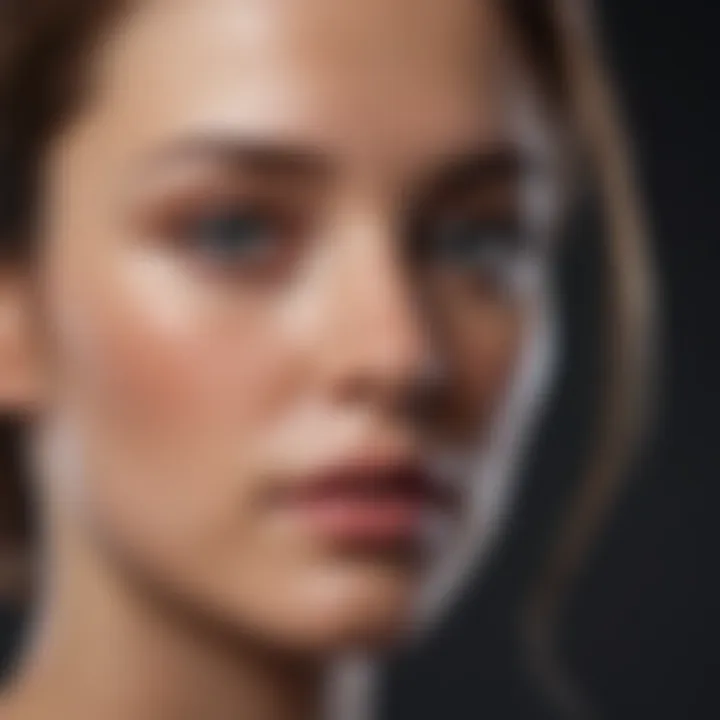
In a market driven by innovation and safety, C-scan offers a cutting-edge solution that fulfills both requirements with grace.
"C-scan technology empowers industries to not only detect faults effectively but to maintain the high standards expected in safety-critical operations."
Thus, as industries evolve, C-scan technology remains a cornerstone of non-destructive testing. The intersections between functional integrity and economic viability highlight its critical role in ensuring quality across different industrial applications.
Benefits of C-scan Technology
C-scan technology stands out in the field of material evaluation for its manifold benefits. The importance of these advantages cannot be overstated, especially in industries where safety and efficacy hinge on precise inspection protocols. The core benefits discussed here include non-destructive evaluation, enhanced efficiency and accuracy, as well as cost-effectiveness in long-term maintenance. Each of these aspects contributes to making C-scan a critical tool in contemporary industrial practices.
Non-Destructive Evaluation
The hallmark of C-scan technology is its non-destructive nature. Unlike traditional testing methods that may compromise the integrity of materials, C-scan allows for thorough examinations without causing any damage. This capability makes it particularly valuable in sectors such as aerospace and automotive, where the integrity of components is paramount.
To elaborate:
- It enables inspections to be conducted on assembled structures, such as aircraft fuselages, without cutting or deconstructing them.
- Operators can identify defects, such as delaminations or cracks, without removing or altering the tested part.
Hence, non-destructive evaluation plays a pivotal role in ensuring the reliability of components while concurrently extending their lifespan.
Increased Efficiency and Accuracy
In the fast-paced industrial world, time is often of the essence. C-scan technology significantly improves both the efficiency and accuracy of inspections. The automated scanning processes help in rapidly generating high-resolution images and data sets, which can be interpreted and analyzed with minimal delay.
The advantages include:
- The ability to detect defects with unprecedented precision - a step up from earlier methods that relied heavily on human judgment.
- Integration of advanced software analytics that can swiftly categorize the findings and highlight areas of concern, allowing for timely interventions.
Consequently, industries benefit immensely, minimizing downtime while maintaining rigorous safety standards.
Cost-Effectiveness in Long-Term Maintenance
While initial investments in C-scan technology might seem steep, the long-term financial benefits become apparent over time. Regular inspections using C-scan can highlight maintenance needs before they escalate into costly failures.
Key points to consider:
- Early detection of potential issues minimizes the risk of catastrophic failures, saving companies hefty repair bills and safety repercussions.
- The longevity of materials tested with C-scan technology reduces the frequency of replacements, thereby reducing waste and expense.
In a nutshell, integrating C-scan technology allows for significant savings and better resource management over an asset's lifespan.
"In industries where stakes are high, the right inspections can mean the difference between success and failure."
This summarization highlights the importance of embracing C-scan technology across various sectors. Emphasizing non-destructive evaluation ensures the safety of operations, while increased efficiency and long-term cost-effectiveness support sound financial practices. As industries grow ever more complex, C-scan technology remains a valuable ally in ensuring material integrity and operational excellence.
Challenges and Limitations of C-scan
Despite the myriad benefits of C-scan technology, it is not without its challenges and limitations. Understanding these aspects is crucial for practitioners, researchers, and industries that rely on this non-destructive testing method. Dissecting the hurdles C-scan faces can guide professionals in optimizing its use and finding solutions to these persistent issues.
Technical Limitations
C-scan technology, while innovative, comes with certain technical hurdles that can hinder its effectiveness. These limitations often manifest in the following areas:
- Material Compatibility: Not all materials react the same way under C-scan technology. For instance, certain composites may generate misleading signals that challenge accurate readings. Materials with complex internal structures can cause signal attenuation, obscuring important data.
- Calibration Requirements: Achieving and maintaining precise calibration is vital. Drift in sensors over time can lead to inaccuracies. Thus, regular maintenance and recalibration efforts are mandatory, consuming time and resources.
- Signal Noise: Environmental factors can introduce noise into the readings, leading to potential misinterpretations. C-scan systems might encounter interference from nearby electronic devices, which complicates data collection in industrial settings.
- Spatial Resolution: The spacing and resolution of the scanning process can hit a limitation. If the scanning grid is too wide, small but significant defects may slip under the radar. Conversely, a tighter resolution may result in data overload, making analysis a daunting task.
Those involved in implementing C-scan systems should keep these technical limitations in mind to adopt best practices that mitigate their impact.
"Recognizing and addressing the challenges within C-scan technology enhances the reliability of inspections and ultimately contributes to greater safety and performance in various industries."
Interpreting C-scan Data
C-scan technology generates a wealth of data during inspections. However, translating this data into actionable insights can prove to be a complex task.

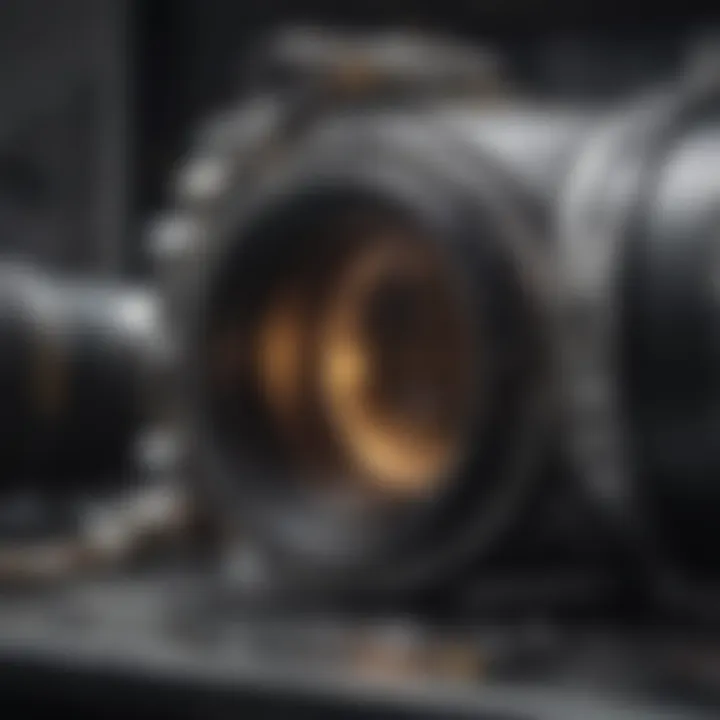
- Complex Data Format: The raw data output from C-scan devices can often appear convoluted. To the untrained eye, it may look like an abstract piece of art; thus, interpretation requires a solid understanding of the underlying principles. Analysts must be adept at recognizing patterns and anomalies, which is not always straightforward.
- Training and Expertise: Personnel must undergo extensive training to interpret C-scan outputs accurately. Without adequate knowledge, even seasoned engineers can misinterpret signals, which can lead to catastrophic decisions.
- Software Limitations: The tools used to visualize and analyze data may have their own limitations. Some software platforms struggle with handling large datasets or might lack advanced features needed for precise analysis. As a result, professionals may miss vital cues or trends in the data.
- Communication Challenges: Once analyzed, summarizing findings and conveying them to stakeholders in a digestible manner can be a significant challenge. Jargon-heavy reports may not reach the intended audience, leading to misunderstandings and sub-optimal decision-making.
Navigating the complexities involved in interpreting C-scan data is essential to harness the full potential of the technology. Industry practitioners must style their approaches to make interpretation possible for as many stakeholders as necessary, creating a bridge between data analysis and practical applications.
Regulatory Landscape and Standards
Understanding the regulatory landscape and standards governing C-scan technology is crucial for ensuring consistent quality and safety across various applications. Regulatory frameworks serve as a backbone in maintaining industry integrity while protecting both service providers and consumers from harm. This section highlights key components of these regulations, their benefits, and several important considerations.
Industry Standards for C-scan
Various organizations set industry standards to ensure that C-scan technology provides reliable results. These standards include protocols for calibration, data accuracy, and quality control. Some prominent standards are:
- ASTM E2876: Addresses comprehensive guidelines for automated ultrasonic testing, essential for industries like aerospace and construction.
- ISO 9712: Focuses on the qualification of personnel performing non-destructive testing, ensuring that operators are trained and capable of interpreting results accurately.
- ISO/ASTM 52900: Covers terminology for additive manufacturing but is increasingly relevant for scanning technologies used in conjunction with 3D printing methods.
These established standards help create a consistent framework, allowing manufacturers, service providers, and regulatory bodies to work harmoniously, ensuring that C-scan results are both precise and actionable.
Compliance with Safety Regulations
Safety regulations are another critical aspect of the C-scan landscape. When dealing with non-destructive testing methods, it is vital to adhere to safety guidelines designed to protect both personnel and the materials being tested. Key regulations that impact C-scan technology include:
- OSHA Standards: Occupational Safety and Health Administration provides regulations regarding workplace safety, including methodologies that minimize exposure to potentially harmful processes.
- NDT Safety Practices: Implementing non-destructive testing safety guidelines ensures that hazards related to equipment use, such as electromagnetic fields or high-energy sound waves, are minimized.
By complying with safety regulations, companies not only protect their employees but also gain trust from clients who rely on the accuracy and reliability of these tests.
Following industry standards and safety regulations ensures the integrity of C-scan technology while fostering advancements that contribute to safer and more efficient operating environments.
Future Directions in C-scan Technology
The realm of C-scan technology is poised at a significant juncture, where innovations and advancements could reshape various practices across industries. This section explores the future directions within this field, emphasizing the integration of emerging technologies and the potential for sophisticated innovations. By closely analyzing these factors, we can appreciate how they collectively enhance the functionality of C-scan methodologies and their applicability in modern contexts.
Integration with Artificial Intelligence
Integrating Artificial Intelligence (AI) into C-scan technology can herald a transformative era for this field. The application of AI algorithms can improve data analysis and interpretation, enabling faster and more reliable decision-making in material inspections.
For instance, AI can enhance **pattern recognition] capabilities, allowing C-scan systems to better identify anomalies or defects that might be overlooked through traditional methods. The strength of machine learning lies in its ability to learn from historical data, thus refining the accuracy of predictions over time.
Consider this example: if a C-scan device typically flags a certain type of defect in aircraft composites, AI can assess the likelihood of such defects based on a myriad of factors, including material age, environmental stresses, and prior wear. This leads to a more data-driven maintenance schedule that can ultimately save costs and improve safety.
Moreover, AI can assist in automating certain processes. The real-time data streaming from C-scan devices can be immediately analyzed, providing instant feedback during inspections. This reduces human error, accelerates reporting, and offers a level of predictive analytics that can preemptively address issues before they escalate.
Emerging Innovations
The frontiers of C-scan technology are not limited to AI alone; several emerging innovations hold considerable promise. One notable area is the advent of smart sensors that can seamlessly integrate with existing C-scan systems. These sensors are designed to be lightweight, portable, and incredibly sensitive. They can detect even the minutest changes in material properties, thus enhancing the granularity of inspections.
Additionally, advancements in multi-modal imaging technology are reshaping how C-scan operates. By harnessing various modalities, such as ultrasonic and electromagnetic scanning simultaneously, inspectors can compile comprehensive datasets that create detailed profiles of material integrity. This multidimensional approach not only enhances accuracy but also reduces inspection time and resource consumption.
Looking towards the future, the paradigm shift could also come from improved data visualization tools. As C-scan technology produces increasingly complex datasets, intuitive visualization platforms can empower users to interpret results quickly and effectively. These tools can incorporate augmented reality (AR), overlaying data on real-world images of structures, making it easier for technicians to identify and communicate issues to stakeholders.
"C-scan technology on its own is remarkable, but when combined with AI and innovative visualization, it creates a powerhouse for inspection and maintenance."
The future of C-scan technology indeed appears bright, driven by the fusion of AI and cutting-edge innovations. This transcendence not only improves efficiency in various applications but also reinforces the technology's pivotal role in ensuring safety and reliability in industrial operations. Understanding these evolving dynamics is essential for professionals keen on adopting next-generation C-scan practices.
Closure: The Role of C-scan in Modern Industries
C-scan technology is not just a tool; it's become an indispensable part of how industries ensure the integrity and safety of materials. Its role is intertwined with advances in technology and the increasing demands for quality assurance in various sectors. As we've navigated through earlier sections of this article, we've seen how C-scan has carved out a niche, offering precision and reliability in non-destructive testing.
The importance of C-scan can be boiled down into a few critical elements:
- Enhanced Safety: In fields like aerospace and construction, the implications of material failure can be catastrophic. C-scan helps detect flaws before they lead to structural failures, thereby safeguarding lives.
- Cost-Effectiveness: While the initial investment in C-scan technology might seem hefty, its ability to prevent failures saves companies money in the long run. Regular monitoring can avert costly repairs or replacements.
- Data-Driven Decisions: The ability to gather accurate data allows companies to make informed decisions about maintenance and replacements. C-scan does not just identify problems; it provides a roadmap for addressing them.
- Innovation and Integration: Modern industries are leaning towards smart technologies. The integration of artificial intelligence with C-scan could further enhance its capabilities, providing even deeper insights into material conditions.
As technology continues to evolve, so will the applications of C-scan. It is likely that newer variants will emerge, enhancing its resolution and applicability in more complex scenarios. Businesses that adopt these advancements will be better equipped to handle the challenges of tomorrow and maintain their competitive edge in a rapidly changing environment.
Society's growing emphasis on sustainability and efficiency also aligns with the benefits brought by C-scan technology. It supports maintenance strategies that prolong the life of materials, ultimately contributing to resource conservation.
In closing, the role of C-scan in modern industries is paramount. It offers a blend of safety, efficiency, and data-driven insights that are hard to overlook. For students, researchers, and professionals interested in material evaluation processes, understanding and advocating for the use of C-scan technology could pave the way toward future advancements in industries across the board. Embracing this technology is not merely a choice; it’s a necessity in today’s precision-oriented world.
"C-scan technology transforms the way industries view material integrity, making it an essential player in the modern industrial landscape."
By embracing the evolution of C-scan, industries are not just investing in a tool; they are paving a path towards a future marked by safety and innovation.