Exploring the Complex Landscape of Car Engine Manufacturing
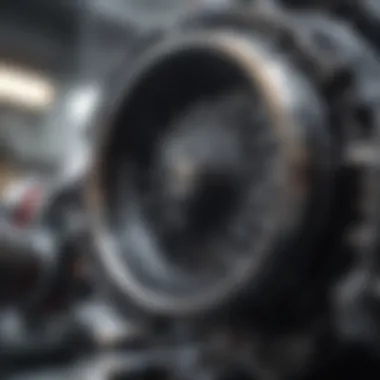
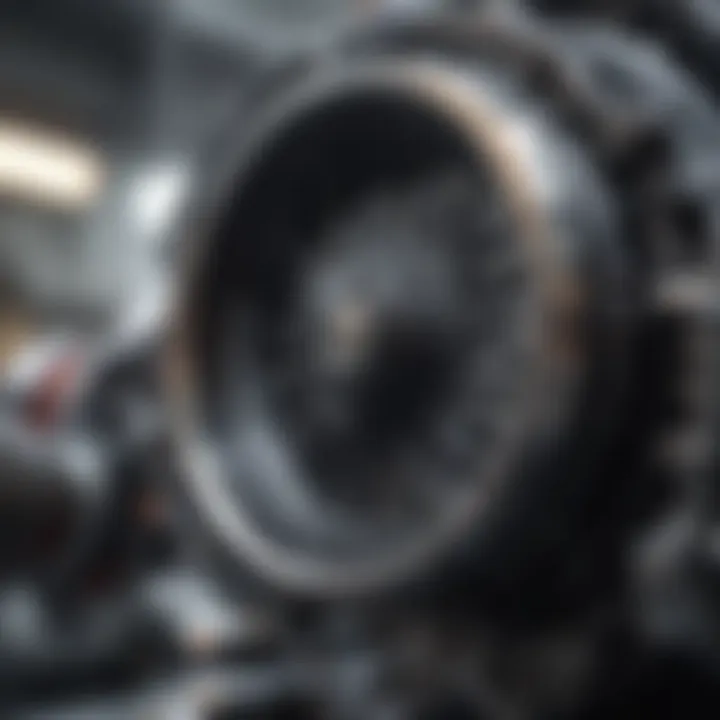
Intro
The realm of car engine manufacturing is not just a simple assembly of parts; rather, it is a complex, intricate web of technology, craftsmanship, and sustainability. As we stand on the brink of a multitude of advancements, it's crucial to grasp the essentials of this ever-evolving industry. From the roaring engines of combustion vehicles to the quiet hum of electric vehicles, the processes behind engine manufacturing have seen substantial transformation.
Understanding this landscape requires an examination of the various facets that come into play. Each component in an engine builds on decades of engineering expertise and innovation. Therefore, recognizing the key concepts in production, the materials utilized, and the shift towards greener methods provides a solid foundation upon which to explore the future of car engines. This article beckons you to journey through the elaborate mechanics of car engine manufacturing, illuminating the challenges and opportunities that shape the automotive world today.
Preamble to Car Engine Manufacturing
The realm of car engine manufacturing stands as a cornerstone in the automotive industry. This complex field not only affects the performance and efficiency of vehicles but shapes environmental impacts and consumer behaviors. By examining this intricate landscape, we can better appreciate the evolution of engine technologies and their implications on the market.
Historical Context
The journey of car engine manufacturing began in the late 19th century. Karl Benz is often credited with constructing the very first automobile powered by an internal combustion engine. From then, the field has steadily evolved. Early engines were rudimentary, often prone to failures and limitations. However, as the decades rolled on, technological innovations such as the four-stroke cycle improved reliability and efficiency. In the mid-20th century, mass production methods pioneered by figures like Henry Ford revolutionized manufacturing. This allowed for standardization and consistency, giving rise to ever more sophisticated engines that could be produced at scale. With each passing decade, developments such as turbocharging, fuel injection, and variable valve timing reshaped how engines operate, leading to vastly enhanced performance.
Importance in the Automotive Industry
Understanding the importance of car engine manufacturing is akin to recognizing the pulse of the automotive industry. Engines are, without a doubt, the heart of any vehicle. They dictate not only the power output and fuel efficiency but also emission levels and overall vehicle longevity. Here are a few key points that underscore the significance of this area:
- Consumer Expectations: In today’s market, car buyers expect both performance and economy from their vehicles. Engine manufacturing plays a vital role in meeting these demands through innovation.
- Regulatory Challenges: With stricter environmental regulations worldwide, manufacturers are pushed to design engines that comply with emission standards. This aspect highlights the need for continuous R&D to develop cleaner technologies.
- Economic Impact: The automotive sector contributes significantly to the global economy, providing millions of jobs. Engine manufacturing is at the heart of this, influencing everything from raw material procurement to assembly line production.
"The engine not only powers the vehicle; it represents a symbiosis of engineering precision and innovative design."
In summary, the introduction to car engine manufacturing lays the groundwork for understanding the intricacies of technology, consumer behavior, and the broader ecosystem of automotive production. As we explore further sections, we will unpick each layer, revealing the rich tapestry that embodies engine manufacturing.
Types of Car Engines
Understanding the different types of car engines is essential for grasping the full scope of automotive engineering. Each engine type contributes uniquely to vehicle performance, efficiency, and environmental impact. This section examines internal combustion engines, electric engines, and hybrid systems, highlighting their specific characteristics and relevance to contemporary automotive challenges.
Internal Combustion Engines
Gasoline Engines
Gasoline engines are one of the most prevalent types of internal combustion engines found in vehicles today, mainly due to their relatively simple design and widespread availability. These engines work on the four-stroke cycle model—intake, compression, power, and exhaust—effectively converting fuel into motion.
A key characteristic of gasoline engines is their ability to rev quickly, making them an appealing option for performance-oriented cars. This swift acceleration is often favored in sporty models where driver experience is paramount.
However, gasoline engines aren't without their downsides. Their efficiency tends to be lower compared to diesel engines, and they emit more carbon dioxide per mile traveled. This can be a double-edged sword: while their performance attracts many consumers, the environmental cost raises concerns, particularly as stringent regulations come into play.
"Gasoline engines balance between performance and accessibility, making them a staple in the automotive industry."
Diesel Engines
Diesel engines are known for their fuel efficiency and torque production, making them suitable for heavy-duty vehicles and long-distance travel. Unlike gasoline engines, these engines ignite fuel through compression rather than spark, leading to a different performance profile.
A major advantage of diesel engines is their superior fuel economy. They can travel further on a gallon of fuel, making them a popular choice for fleet vehicles and transport sectors. However, they have their drawbacks too. Diesel engines produce higher nitrogen oxide emissions and particulate matter, which pose challenges for air quality and public health.
In recent years, the automotive industry has faced increasing pressure to innovate diesel technology to meet environmental standards, which has led to investments in cleaner emissions technologies.
Electric Engines
Batteries
Batteries are the heartbeat of electric vehicles, providing the necessary power to drive electric motors. Lithium-ion batteries are the most commonly used, favored for their high energy density and longer life cycle.
The importance of batteries in electric engines cannot be overstated. They are often what defines an electric vehicle’s range and performance. As battery technology continues to advance, with newer chemistries being explored, it’s expected that the energy storage solutions will become lighter, cheaper, and more efficient.
Despite these advances, the cost and availability of batteries remain significant factors influencing the adoption of electric vehicles. The process of mining and refining the materials used in batteries has raised environmental concerns, necessitating a sustainable approach to battery production and disposal.
Charging Infrastructure
The charging infrastructure for electric vehicles is a critical aspect of their integration into daily life. An extensive network of charging stations is essential for reducing range anxiety among potential electric vehicle owners.
Fast chargers, in particular, are increasingly important as they can recharge a vehicle's battery in a fraction of the time compared to standard chargers. The expansion of charging stations in urban and rural areas alike is vital for facilitating the widespread adoption of electric vehicles. However, the variabilities in charging speed and compatibility depending on the manufacturer can complicate the charging landscape.
Investment in reliable charging infrastructure not only supports electric car users but also stimulates business opportunities for service providers. The challenge lies in balancing high demand and potential return on investment with the cost of installation and maintenance.
Hybrid Systems
Combination Powertrains
Hybrid systems that utilize combination powertrains leverage both internal combustion and electric engines to enhance overall efficiency. This flexibility allows vehicle design to switch between power sources or even utilize both simultaneously, optimizing performance while reducing fuel consumption.
One compelling feature of combination powertrains is their adaptability. Depending on driving conditions—like heavy traffic or steep inclines—the system can choose the most efficient source of power. This versatility often results in significant fuel savings and lower emissions compared to traditional combustion engines.
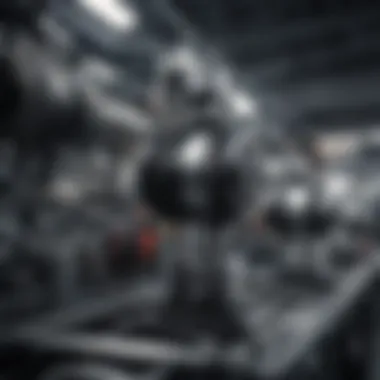
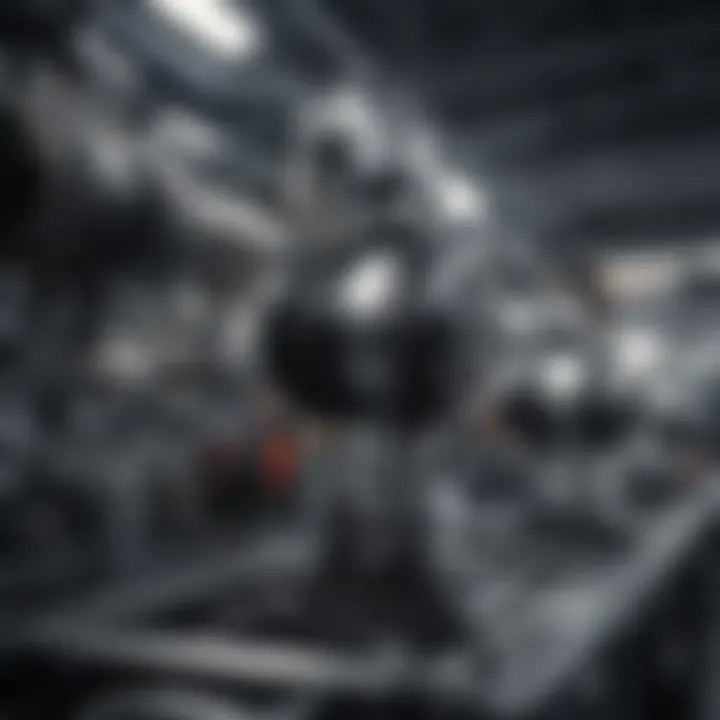
Nevertheless, hybrid systems can be more complex and might require special maintenance, which may deter some consumers.
Regenerative Braking
Regenerative braking is an innovative feature inherent in many hybrid and electric vehicles. Unlike conventional brakes that waste energy as heat, regenerative braking captures some energy during braking and converts it back into usable electricity, which can be used later to power the vehicle.
This system not only improves energy efficiency but also enhances brake life. By using the motor to drive the vehicle in reverse during braking, energy recovery becomes a smart addition to modern automotive engineering.
However, the effectiveness of regenerative braking can vary depending on driving habits and conditions. In scenarios where frequent stops occur, such as in city driving, the benefits are amplified, while in highway driving, the impact may be less pronounced.
In sum, the types of car engines available today play a vital role in shaping the future of transportation. As automotive manufacturers continue to innovate and adapt to societal demands, understanding these engine types helps frame the complexities of the ongoing evolution within the car engine landscape.
Manufacturing Processes
When diving into the world of car engine manufacturing, one cannot overlook the pivotal role that manufacturing processes play. These processes form the backbone of production, ensuring that every engine built meets strict specifications while adhering to time constraints and budget limitations. In an industry where precision is non-negotiable, having robust manufacturing processes is essential. They encompass various stages, from conceptual design to the final product, each contributing to the engine's performance, efficiency, and reliability.
Design and Engineering
Computer-Aided Design
One major aspect of design and engineering is Computer-Aided Design (CAD). CAD has revolutionized how engineers and designers envision engine components. By utilizing sophisticated software, teams can create detailed 3D models that simulate real-world behaviors and interactions. A key characteristic of CAD is its ability to produce complex geometries with pinpoint accuracy, which is crucial when thinking about the engine's performance.
The unique advantage of CAD lies in its iterative design process. Designers can easily modify their models based on testing results or feedback, streamlining the development process. However, while CAD significantly enhances efficiency, it does require skill and familiarity with the software, which could pose a barrier for some smaller manufacturers.
Prototyping Techniques
Prototyping techniques are equally vital in car engine manufacturing. The concept of creating physical representations of parts allows designers to identify flaws and improve systems before full-scale production. Rapid prototyping methods, such as 3D printing, have become increasingly popular because they allow for fast iterations and adjustments. This key characteristic can cut down on lead times while still ensuring product quality.
Moreover, prototypes are invaluable for testing various materials and assembly methods without committing to large production runs. Nonetheless, prototyping can also be costly and time-consuming, especially if multiple revisions are needed. In short, while some drawbacks exist, the benefits often outweigh the risks.
Production Techniques
Machining and Assembly
In the context of production techniques, machining and assembly are at the forefront. Machining involves removing material from a workpiece to achieve the desired shape and size, which is critical for components that require precise tolerances. The key characteristic of machining is its effectiveness in producing complex parts that can withstand the rigors of engine operation.
One unique feature of utilizing advanced CNC (Computer Numerical Control) machines is the level of automation and precision they offer. This technology minimizes human error and maximizes output quality. However, the initial investment in high-tech machinery can be significant, creating a piece of the puzzle that many smaller manufacturers might find challenging to navigate.
Quality Control Methods
Quality control methods are indispensable to ensure that each engine meets the expected standards. Various testing procedures, including non-destructive testing and performance evaluations, are used throughout the manufacturing process. The essential characteristic of rigorous quality control is its capacity to catch defects before they become costly mistakes down the line.
Methods like statistical process control allow engineers to monitor production in real time, adjusting as necessary to maintain quality. While implementing such processes might seem like an extra step, the long-term savings made possible by reducing returns and warranty claims make these practices a wise choice for any manufacturer.
Supply Chain Logistics
Material Sourcing
Effective material sourcing connects every phase of engine manufacturing. Securing the right materials at the right time influences quality, cost, and production timelines. The crucial aspect of material sourcing is not merely obtaining materials but establishing reliable networks that can consistently deliver high-quality components.
As markets fluctuate, manufacturers must be agile in their sourcing strategies. The advent of sourcing software that links manufacturers to a diverse array of suppliers has made this process simpler. Nevertheless, challenges such as geopolitical factors and supply chain disruptions can complicate sourcing, affecting overall production efficiency.
Inventory Management
Lastly, inventory management forms a cornerstone of production logistics. Effective inventory management maximizes efficiency by ensuring that every component is available when needed. A well-structured inventory system helps maintain a smooth workflow and minimizes waste.
The key feature of modern inventory management systems is their ability to provide real-time data on stock levels and production needs. While these systems can be expensive and require training to use effectively, the long-term benefits of reduced downtime and timely deliveries are significant.
"Manufacturing processes are not just about making parts; they are about weaving together technology, materials, and human skill to create something that powers the future."
Materials in Engine Construction
The choice of materials in car engine manufacturing plays a crucial role in defining engine performance, maintenance, and durability. This section dives into different materials, both traditional and innovative, looking closely at their characteristics, benefits, and limitations. As the automotive industry faces mounting pressure for efficiency and sustainability, understanding the materials that comprise engines becomes increasingly pertinent.
Traditional Materials
Aluminum Alloys
Aluminum alloys are a cornerstone in car engine construction, primarily due to their favorable strength-to-weight ratio. When it comes to reducing engine weight, aluminum is often the name of the game, allowing for better fuel efficiency without compromising structural integrity. A notable characteristic of aluminum alloys is their excellent thermal conductivity, making them ideal for heat dissipation in high-performance engines.
Advantages: One unique feature of aluminum alloys is their resistance to corrosion, ensuring longevity. This resistance often translates to lower maintenance costs and improved reliability over the engine's lifespan.
Disadvantages: Nevertheless, there's a catch; aluminum alloys can be more expensive compared to traditional steel components and may not hold up well under extreme stress, leading to potential deformation over time.
Steel Components
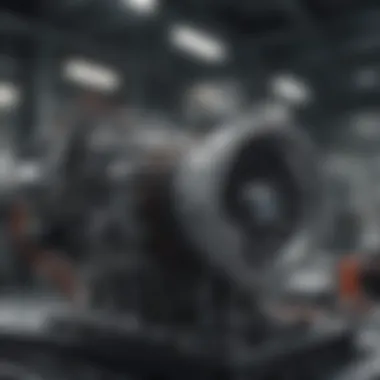
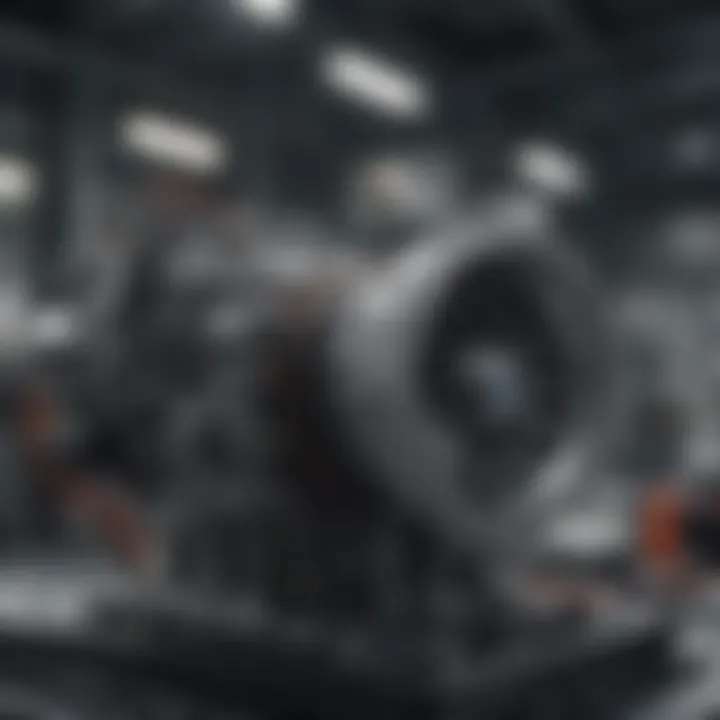
Steel components remain a staple in engine manufacturing due to their unmatched strength and durability. The robustness of steel allows for high-pressure environments, which is often a requirement in modern engines. Steel's key characteristic is its ability to withstand significant wear and tear, contributing to the engine’s overall longevity.
Advantages: A standout feature of steel is its cost-effectiveness, making it an economical choice for many manufacturers. Additionally, steel allows for precise machining, which can lead to better fitting components that contribute to enhanced overall engine performance.
Disadvantages: However, steel's heavier weight compared to aluminum leads to increased fuel consumption, which is counterproductive in light of current trends towards efficient energy use.
Innovative Materials
Composite Materials
The rise of composite materials marks a significant shift in car engine manufacturing. Composites, often made from a blend of different materials, provide a dynamic advantage by combining the best properties of each component for improved performance. A key characteristic of composites is their lightweight, which allows for better efficiency and speed in engine design.
Advantages: Their unique feature lies in the ability to tailor make composites for specific applications, offering durability without the weight penalty associated with metals. This adaptability is increasingly appealing as manufacturers seek to innovate.
Disadvantages: Nevertheless, composite materials can be rather costly to produce and require specialized techniques for shaping and maintenance, potentially leading to increased production times.
3D Printing Applications
3D printing applications are revolutionizing car engine manufacturing by enabling highly customizable production techniques. This process simplifies the creation of intricate designs that would be hard to achieve using traditional methods. A prominent characteristic of 3D printing is its ability to use various materials, from plastics to metals, depending on the application.
Advantages: The yearn for customization means manufacturers can create lightweight yet strong components. Moreover, 3D printing significantly reduces waste, aligning with sustainability goals in the industry.
Disadvantages: On the flip side, the technology might not yet provide the necessary scale for mass production or the durability required for high-stress engine parts, presenting a challenge for widespread adoption.
In summary, the choice of materials in engine manufacturing is a balancing act between performance, cost, and environmental responsibility. As technology evolves, the potential of innovative materials will undoubtedly reshape the landscape of car engines.
Environmental Considerations
Understanding the environmental considerations in car engine manufacturing is paramount. The automotive industry grapples with the dual challenge of meeting growing consumer demand while addressing environmental impact. As such, manufacturers are increasingly adopting practices that not only drive profit but also promote sustainability. This section delves into two key areas: sustainability practices and regulatory compliance, both of which play significant roles in shaping the future of engine manufacturing.
Sustainability Practices
Recycling of Materials
Recycling of materials is a crucial cog in the wheel of sustainable engine manufacturing. By reusing metals, plastics, and other materials, companies can significantly minimize waste. It reduces the demand for new raw materials, which, in turn, leads to less energy consumption in material extraction and processing. One of the key characteristics of recycling is its ability to lower production costs, thereby making it a more appealing choice for manufacturers amidst rising operational expenses.
A unique aspect of recycling is its impact on the carbon footprint. For instance, recycling aluminum can save up to 95% of the energy required to produce new aluminum from ore. This enables manufacturers to claim environmental benefits while often reducing their expenses as well. However, the challenge often lies in the sorting and cleaning of materials, which can be complex and costly.
Reducing Emissions
Reducing emissions is another critical element in the sustainability narrative of car engine manufacturing. The automotive sector has been under pressure to curb greenhouse gases produced during production and operation. This focus leads to innovations in cleaner technologies and fuels, pushing manufacturers to adopt methods that lower their emissions output.
A key characteristic of reducing emissions is its compliance with increasingly stringent regulations. By investing in cleaner technologies, manufacturers can not only create a positive public image but can also significantly reduce potential fines and compliance costs down the line. A unique feature here is that many manufacturers are also exploring alternative fuels, such as biofuels or hydrogen, which can dramatically decrease harmful emissions.
Nevertheless, transitioning to cleaner technologies often requires substantial upfront investment. For emerging companies, this could be a daunting barrier, but the long-term benefits, such as reduced operational costs and positive community impact, present a persuasive case.
Regulatory Compliance
Emission Standards
Emission standards stand as the legislative backbone protectin the environment from harmful pollutants. These regulations ensure that automotive manufacturers implement practices that keep emissions below specified limits. The key advantage of emission standards is that they push companies towards cleaner technologies, promoting research and innovation.
The unique feature of these standards is their adaptability; they evolve over time to incorporate new scientific insights. This means that manufacturers are always on their toes to stay ahead of regulations, which can be both a challenge and an opportunity. While this adaptability sometimes leads to increased costs, failing to comply can result in penalties, making adherence a critical aspect of operational strategy.
Safety Regulations
Safety regulations complement emission standards in reinforcing the integrity of manufacturing processes. These ensure that vehicles are not only efficient but also safe for consumers. Highlighting this aspect is vital since it reflects the industry's commitment to public safety alongside environmental commitments.
The unique characteristic of safety regulations is their comprehensive nature; they cover everything from design safety to operational protocols. Compliance not only helps to prevent accidents but also builds consumer trust—a crucial intangible asset in a highly competitive market. On the downside, stringent regulations can increase production costs and extend the time required for new models to hit the market.
"An environmentally conscious approach is no longer a choice; it's a mandate. The industry needs to adapt or be left behind."
In summary, environmental considerations in car engine manufacturing are not merely about compliance but also embody a profound opportunity for innovation and improvement. As the industry evolves, embracing sustainability practices and adhering to regulations can pave the way for a more responsible and future-ready automotive landscape.
The Role of Technology
In the ever-evolving arena of car engine manufacturing, technology serves as a linchpin, ushering in transformative changes that modify not only how engines are built but also how they perform. The integration of technology enhances production efficiency, ensures quality, and provides insights that were previously impossible to obtain. As manufacturers strive to meet regulatory demands and consumer expectations, the role of technology in this field becomes undeniably crucial.
Automation in Manufacturing
Robotics in Assembly Lines
The rise of robotics in assembly lines is perhaps one of the most significant developments in car engine manufacturing. These automated systems expedite the assembly process, reducing the time taken per engine while also minimizing human error. The unique characteristic of robotic arms—capable of precision movements—is particularly beneficial for tasks like welding and parts assembly.
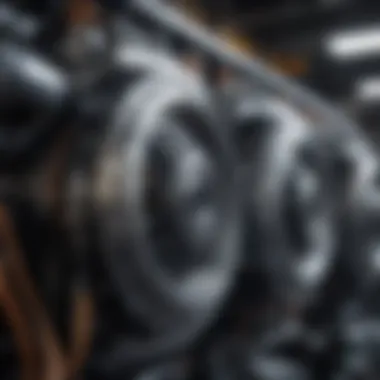
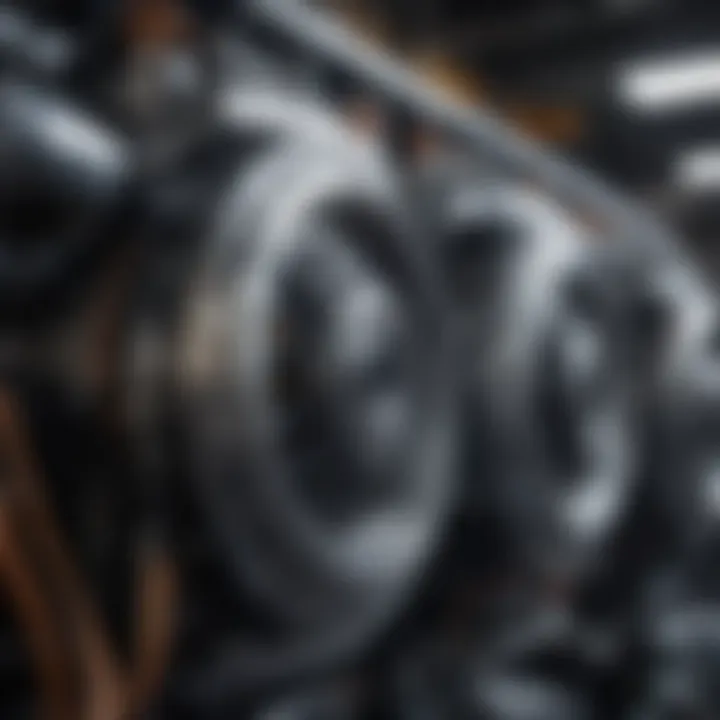
Implementing robotics not only boosts efficiency but also allows for a higher level of consistency across production batches. However, while the advantages are plentiful, one must consider the heavy initial investment and potential maintenance costs associated with such technology. For many manufacturers, the trade-off is worth the price tag, given the long-term benefits of increased output and quality.
Impact on Labor
The incorporation of automated technologies, notably robotics, significantly reshapes labor dynamics in car engine manufacturing. Traditionally labor-intensive tasks are now handled by machines, escalating questions about workforce sustainability and employment. While these advancements can lead to a more streamlined operation, they may also result in workforce reduction or necessitate reskilling of existing employees.
However, this shift isn’t purely negative. It creates opportunities for labor to evolve, with the demand for skilled operators and technicians rising. The technological change can pave the way for more rewarding jobs that focus on oversight and maintenance of sophisticated equipment. Thus, the impact on labor is decidedly a double-edged sword, where one sees both a challenge and a chance for growth in the available job market.
Data Analytics and Engine Performance
Performance Monitoring
Performance monitoring has become an indispensable aspect of engine development and manufacturing. Using advanced data analytics, manufacturers can now assess an engine's efficiency, power output, and emissions in real-time. This continuous feedback loop enables engineers to fine-tune performance parameters on the fly, leading to optimal engine designs.
The key characteristic of this process is its ability to gather vast amounts of data from a multitude of sensors embedded in engines. Not only does this inform product enhancements, but it also enables manufacturers to respond swiftly to performance anomalies, often before they escalate into serious issues. Still, the reliance on data analytics means manufacturers must invest commercially and in terms of training staff, creating a potential barrier for smaller firms that may not have the resources to keep pace.
Predictive Maintenance
Predictive maintenance stands at the forefront of technological advancement in car engine manufacturing. By utilizing sophisticated algorithms and machine learning, manufacturers can predict when parts may fail and require replacement—a significant leap forward compared to traditional scheduled maintenance plans.
The defining feature of predictive maintenance is its proactive approach, as it achieves cost savings and minimizes unplanned downtimes. An engine can spend more time on the road or in service rather than in repair. However, it isn't without challenges; the reliance on accurate data and the need for consistent monitoring create additional demands on data management resources.
"Automation is not just about replacing manual labor—it’s about augmenting our capabilities and enhancing the future of engine manufacturing."
In summary, the impact of technology spans across various dimensions of car engine manufacturing, from automation in the assembly lines to profound advancements in data analytics. This evolution marks a departure from traditional methods and approaches, highlighting a complex landscape where the interplay between machines and human intelligence continues to grow. Each change brings opportunities, yet it also necessitates a reevaluation of labor dynamics and resource allocation. As the industry heads into new territories, embracing technology remains a key consideration for both manufacturers and the overarching automotive sector.
Future Trends in Engine Manufacturing
The evolution of car engine manufacturing is at a crossroads today, rapidly shifting under the influence of changing consumer preferences, technological advancements, and environmental pressures. Understanding future trends in this sector is important because they will shape how manufacturers design, produce, and market engines. As we look ahead, several key elements emerge that will influence this landscape.
Shift Towards Electrification
Growth of Electric Vehicles
The rise of electric vehicles (EVs) marks a significant turning point in automotive engineering. As cities and governments push for greener initiatives, the growth of electric vehicles shows no signs of slowing down. The key characteristic of this trend is its potential to reduce carbon emissions, making EVs a popular choice amongst environmentally conscious consumers.
Unlike traditional combustion engines, electric vehicles utilize batteries that store energy, which can be harnessed for driving, leading to a notable decrease in air pollutants. One unique feature of EVs is their ability to perform regenerative braking, which allows them to harness energy that would otherwise be lost during braking. The advantages of this include increased efficiency and reduced wear on brake components. Yet, this shift toward electrification does come with challenges, such as battery production in terms of sustainability and the need for robust charging infrastructure.
Implications for Traditional Manufacturing
The implications for traditional manufacturing practices cannot be ignored. As the landscape shifts toward electric mobility, engine manufacturing will undergo top-to-bottom transformations. Traditional manufacturers will need to adapt their production lines or risk obsolescence. A critical aspect here is the need for skilled labor in electric vehicle technology, which diverges from the mechanical focus of internal combustion engines.
Moreover, the production processes will likely be streamlined to accommodate lighter, modular designs that are easier to manufacture and assemble. However, the unique feature of this adaptation means that manufacturers committed to traditional methods might face tough decisions about retooling or restructuring their facilities. The advantage lies in the opportunity for innovation, but it also risks significant investment and potential jobs loss as old ways become obsolete.
Emerging Markets and Global Dynamics
Market Demand Variations
Understanding market demand variations is crucial for the future of engine manufacturing. Different regions exhibit unique demands based on economic maturity, urbanization rates, and cultural preferences. For instance, in countries with robust middle-class growth, there's a notable spike in demand for affordable, efficient vehicles. This localization often results in desirably tailored engines that meet specific regulations and consumer needs, illustrating the advantage of versatile design and manufacturing.
The disadvantage, however, is the strain it places on global supply chains, making it a challenging juggling act for manufacturers to equate local preferences with global strategies. Not all markets will adapt to electric solutions equally, and manufacturers must remain agile in their response to these fluctuations.
Local vs. Global Production Strategies
The battle between local and global production strategies adds another layer of complexity. Local manufacturing can lead to reduced shipping costs and faster turnaround times, which is increasingly important in a world where quick response to consumer demands can set a company apart. A key characteristic of local strategies is their ability to cater specifically to regional markets, adapting to local regulations and customer preferences in a way global production often cannot.
However, the hallmark of global production strategies is their scale; they enable companies to benefit from economies of scale and potentially lower costs. The unique feature here lies in a trade-off between local adaptation and global efficiency. There's a delicate balance to strike, as offshoring manufacturing can expose companies to geopolitical risks and issues with long supply chains. Ultimately, success may hinge on the ability to merge both strategies effectively, responding to global trends while remaining rooted in local market understanding.
In summary, the future of engine manufacturing hinges on electrification and the complexities of global dynamics, which will shape the way cars are powered and produced for generations to come.
The End
The discussion of car engine manufacturing touches on various pivotal elements that shape the automotive industry today. This article outlines critical factors that influence the manufacturing process, from the historical context to the modern trends shaping the future. Understanding these dynamics is not trivial; it's vital for students, researchers, and professionals immersed in automotive technology.
Summary of Key Points
To really grasp the importance of car engine manufacturing, several key takeaways highlight the nuances of this extensive field:
- Historical Evolution: The journey of engine manufacturing has created foundations that inform current practices and innovations. The shift from steam engines to internal combustion and now to electrification marks major advancements.
- Diverse Engine Types: Understanding the difference among gasoline, diesel, electric, and hybrid systems offers insight into how manufacturers adapt to market trends and consumer preferences.
- Manufacturing Processes: Techniques like computer-aided design and prototyping have revolutionized productivity and precision, enabling manufacturers to produce engines that are both efficient and environmentally friendly.
- Material Innovations: The use of advanced materials, including composites and 3D printing technologies, enhances durability and performance of engines while addressing sustainability concerns.
- Environmental Framework: With the automotive industry facing scrutiny regarding its impact on the environment, adherence to sustainability practices is more than just a trend; it’s a necessity.
- Technological Positives: Automation and data analytics have changed the landscape of manufacturing, leading to optimized production lines and enhanced performance evaluations.
- Future Directions: The lean towards electric vehicles provides a clear indication of where automotive engineering is heading, coupled with changing market demands that transform established production strategies.
The Path Ahead
Looking ahead, the trajectory of car engine manufacturing is laden with opportunities and challenges. As electrification takes the front seat, traditional manufacturers may need to rethink their strategies. Transitioning to hybrid systems can serve as a bridge while fully electric systems are embraced more broadly.
Also, global dynamics play a critical role. Emerging markets may shift the center of gravity for production as manufacturers adapt to local demands while keeping an eye on global competitiveness. This situation reinforces the need for a robust supply chain that can handle both local and global pressures.
The shared knowledge about manufacturing practices will continue to evolve. Maintaining awareness of materials and processes—while pushing boundaries with new tech—will be pivotal. More research focused on performance and sustainability will play a vital role in shaping the next chapter of this complex landscape.
"Embracing innovation is not just about survival—it's about leading the charge into a more sustainable automotive future."
In summary, this exploration of car engine manufacturing not only provides insights into current practices but also hints at the transformations that lie ahead. Each of these aspects is essential in making informed decisions, fostering advancements, and preparing adequately for a rapidly changing environment.