Exploring Gas Pipe Steel: Applications and Innovations
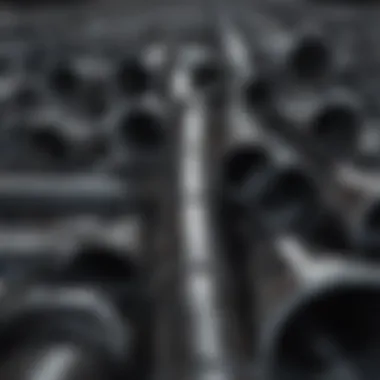
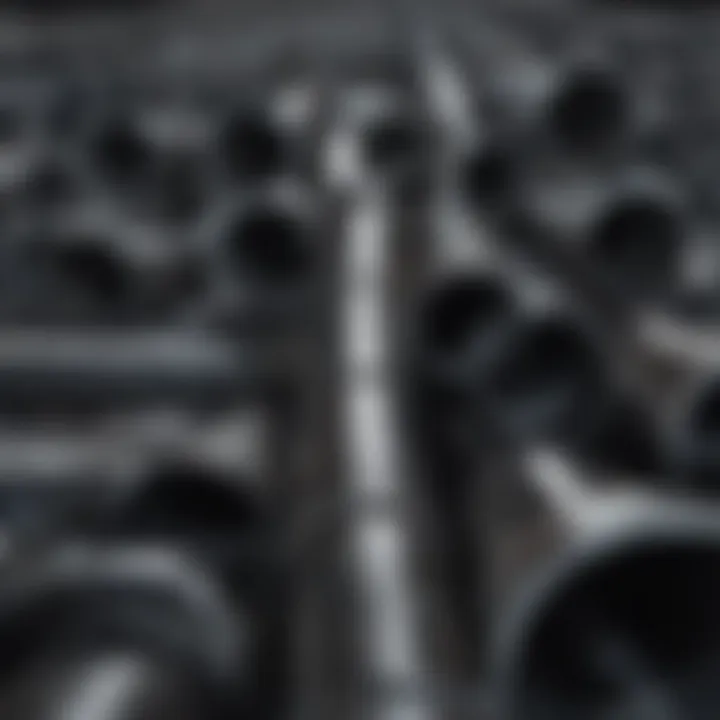
Intro
Gas pipe steel is a critical component in the energy and construction sectors. As hidden yet essential elements, these pipes facilitate the safe transport of natural gas and other gases, underlining the importance of high-quality materials and stringent standards. This exploration aims to shed light on the applications and innovations surrounding gas pipe steel, providing both foundational definitions and forward-looking insights.
In many industries, the reliability of gas pipe steel can’t be overstated. From ensuring household heating needs to supporting heavy industrial operations, its role resonates far and wide. As you read on, let’s dive deeper into this subject and uncover the nuances that define gas pipe steel, ensuring a solid understanding of its multifaceted significance in today’s infrastructure.
Key Concepts
Definition of Primary Terms
To effectively understand gas pipe steel, it’s crucial to grasp some key terminology:
- Gas Pipe Steel: This refers to steel specifically designed and manufactured for the construction of pipelines that carry gases, such as natural gas, methane, and others.
- API Standards: The American Petroleum Institute has established specific norms and guidelines to ensure the quality and safety of gas pipes.
- X-grade Steel: A designation indicating higher strength and toughness, which is essential for gas transport, often seen in pipes made for challenging conditions.
Related Concepts and Theories
One must consider the metallurgical principles governing gas pipe steel. The mechanical properties - including tensile strength, ductility, and impact resistance - are paramount. These properties are influenced by the steel’s composition and the treatments it undergoes during manufacturing. For instance, the inclusion of alloys like chromium can improve corrosion resistance, a key factor when pipelines traverse diverse environments.
Another significant aspect is the environmental impact of gas transportation. The carbon footprint of production and transportation processes raises pertinent questions about sustainability within the industry.
Future Directions
Despite the extensive research, gaps still exist in understanding how emerging techniques may enhance the durability and efficiency of gas pipe steel. Addressing these gaps can lead to stronger, safer, and more environmentally-friendly solutions.
Gaps Identified in Current Research
- Long-term performance in extreme conditions: While current standards address many parameters, how do pipes perform over decades in harsh conditions?
- Impact of new materials: What role might advanced composites or smart materials play in enhancing the functionality of gas pipelines?
Suggestions for Further Studies
- Conduct extensive field tests across diverse conditions and geographical settings.
- Investigate recycling methods for gas pipe materials, focusing on sustainability and material recovery.
Understanding these concepts not only broadens the current knowledge landscape but also charts a path for innovations that can redefine the standards of gas pipe steel.
Preface to Gas Pipe Steel
Gas pipe steel stands as a cornerstone in the infrastructure that supports modern societies. This material isn't just a simple alloy; it embodies the strength and resilience needed for transporting natural gas across vast distances safely and efficiently. As industries push for more sustainable energy solutions, understanding gas pipe steel becomes even more crucial. It encompasses various alloys and grades, each tailored to meet specific requirements in the field of pipeline engineering.
The importance of gas pipe steel goes beyond its practical applications. It's integral to ensuring the integrity of pipelines that serve as lifelines for energy delivery. Imagine a bustling city powered by the gas that moves through these pipelines. Any failure in this system can have dire consequences. Thus, gas pipe steel has stringent standards governing its production and application, helping mitigate risks associated with leaks, explosions, and other hazards.
A key element of gas pipe steel is its ability to withstand environmental challenges. Hot summers, frigid winters, and everything in between can affect pipeline performance. Engineers carefully select materials to enhance durability while adhering to regulatory frameworks. This selection is especially critical as companies aim for compliance with evolving environmental standards, which incorporate advanced testing and evaluation of materials.
Moreover, innovations in gas pipe steel technology showcase the ongoing developments in this sector. New materials and manufacturing techniques are constantly being introduced, offering potential improvements in performance and safety. As research continues, the future of gas pipe steel promises to blend traditional practices with cutting-edge science, ensuring that our means of transporting gas remains both efficient and secure.
"The reliable function of gas pipelines is pivotal for energy distribution, and understanding the materials that underpin this infrastructure is essential for all stakeholders."
In summary, grasping the fundamentals of gas pipe steel is not merely an academic exercise; it's a necessity for engineers, policymakers, and anyone involved in the energy sector. The text that follows will explore this material's properties, manufacturing processes, applications, safety measures, innovations, and the challenges it faces as we move toward a more sustainable future.
Historical Context
The historical context of gas pipe steel is pivotal to comprehend its evolution and significance in contemporary infrastructure. This narrative can be traced back to the very inception of pipeline technology, where the demand for efficient gas transportation prompted innovations in materials and engineering methods. Understanding how gas pipe steel has evolved over the decades sheds light on its current applications and the standards set to ensure safety and efficiency.
Development Through Time
Gas pipe steel has undergone numerous transformations since the early days of pipeline construction. Initially, materials such as wood and wrought iron were utilized, but as demand increased, there was a clear necessity for stronger, more resilient materials. The advent of seamless steel pipes in the early 20th century marked a turning point, allowing for a safer and more reliable way to transport natural gas and other fluids.
The technological leaps didn't stop there. Following World War II, advancements in metallurgy and welding techniques vastly improved the quality and performance of gas pipe steel. The adoption of automated manufacturing processes further streamlined production, giving rise to pipes that could withstand higher pressures and hostile environments.
Throughout the years, the standards governing gas pipe steel have evolved in tandem with these developments. For instance, the introduction of API and ASTM standards in the United States established benchmarks for quality control and safety, vital for industries that rely on safe gas transportation.
Milestones in Pipeline Engineering
Several milestones have punctuated the journey of pipeline engineering, each representing a significant leap towards modernizing infrastructure.
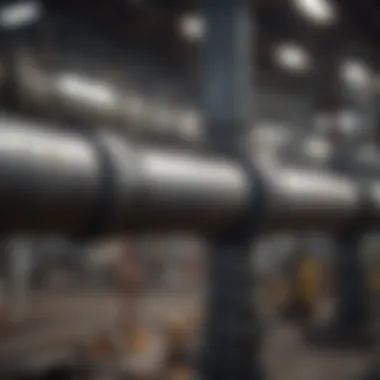
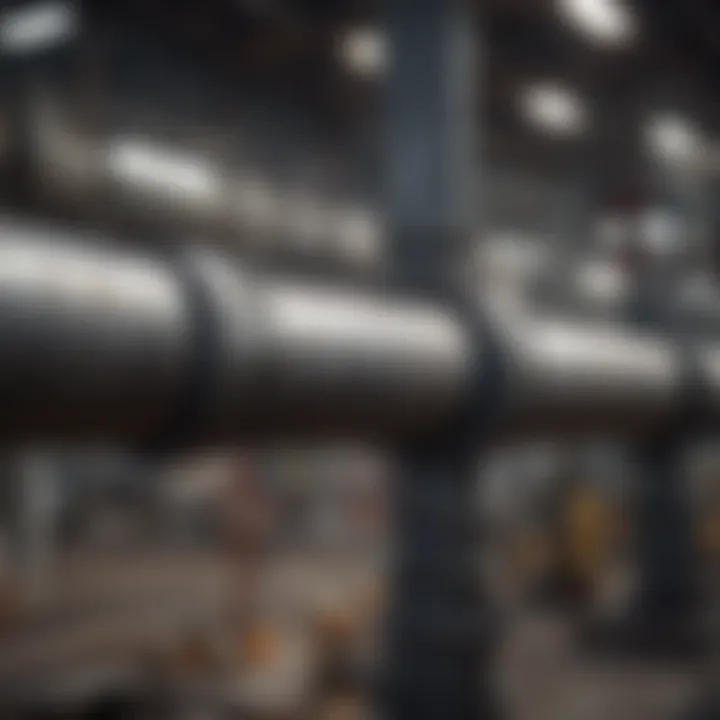
- 1920s - The Birth of Long-Distance Pipelines: The first long-distance pipelines emerged, making gas transportation viable over vast distances. This revolution not only changed the landscape of energy distribution but also spurred economic growth in regions previously lacking gas access.
- 1970s - The Shift to High-Strength Steel: As global energy needs rose, the industry shifted towards high-strength steels, enabling the construction of larger diameter pipes designed to handle increased loads. This shift paved the way for efficiency and cost-effectiveness in pipeline projects.
- 1990s - Introduction of Advanced Materials: The integration of advanced materials and coatings, such as polymer-based linings, began in the 90s. These innovations aimed to enhance corrosion resistance and extend the lifespan of pipelines, underscoring the industry’s commitment to safety and sustainability.
The evolution of gas pipe steel is a testament to the intersection of innovation and necessity. As societies advance, so too must the materials we depend upon to support them.
The narrative of historical context surrounding gas pipe steel highlights an ongoing trend of adaptation and improvement. This not only serves current demands but lays the groundwork for future innovations that will further enhance the safety and reliability of gas transportation systems.
Material Properties of Gas Pipe Steel
The material properties of gas pipe steel are pivotal, forming the backbone of its utility across various industries. Understanding these properties provides insights into not only the performance but also the safety and longevity of pipelines. Key material characteristics determine how a pipe will handle the stress of gas transportation under different environmental conditions. Durability, flexibility, and resistance to degradation are essential factors that companies consider before selecting gas pipe steel for their projects. These properties ultimately influence operational costs and risks associated with gas transport.
Types of Steel Alloys Used
Different steel alloys bring unique advantages to the table, hence their specific applications in pipeline installation. Carbon steel is often touted for its weldability and relatively low cost, making it a popular choice. On the other hand, alloy steels, which may contain elements like chromium or molybdenum, enhance strength and performance under high temperatures and pressures. Stainless steel is another contender, favored for its corrosion resistance, particularly in environments that present a risk of rust and corrosion.
Mechanical and Chemical Properties
Yield Strength
Yield strength is a critical measure in gas pipe steel, indicating the maximum stress a material can endure without permanent deformation. This property plays a significant role in preventing pipeline failure during extreme conditions. A high yield strength generally signifies that the steel can withstand forces that would deform lesser materials. This is particularly beneficial in scenarios like high-pressure gas transport where structural integrity is paramount. However, it’s important to remember that extremely high yield strength can lead to brittleness, which must be managed through careful engineering techniques.
Tensile Strength
Tensile strength measures how much pulling force a material can handle before breaking. The importance of tensile strength in gas pipe steel cannot be overstated; it directly correlates with the ability to handle the internal pressure during gas transit. Strong tensile values ensure that a pipeline remains intact even under stress, proving vital for safety in operations. While high tensile strength is advantageous, it's also vital to balance it with ductility, which allows the material to deform without breaking under sudden stress.
Corrosion Resistance
Corrosion resistance is a key material property that safeguards against environmental threats. Gas pipe steel often operates in conditions that expose it to corrosive substances, including moisture, acids, and other chemicals. High corrosion resistance means the pipeline will have a longer service life, reducing maintenance efforts and costs. However, achieving this resistance may involve additional costs, such as special coatings or using alloyed steels, which could deter some budget-conscious projects.
Standard Specifications
Standards provide a benchmark in the industry for material quality, safety, and performance.
ASTM Standards
The ASTM (American Society for Testing and Materials) standards offer guidelines on the manufacturing and testing of materials used in pipelines. They ensure that specific mechanical and chemical properties are met, enhancing the reliability of gas pipe installations. Their wide acceptance in the industry underscores their importance, considering rigorous testing measures are involved. While ASTM standards are well-regarded, compliance can increase production costs, which might affect smaller enterprises more significantly.
API Standards
API (American Petroleum Institute) standards are crucial for ensuring the effectiveness and safety of gas transport systems. These standards also help to harmonize operations across different organizations and regions. API focuses on specific performance criteria that align with safety practices for transportation industries. Implementing these standards may require more investments in manufacturing processes, but the resultant quality assurance can lead to fewer failures and incidents, ultimately benefiting companies in the long run.
Manufacturing Processes
The manufacturing processes involved in gas pipe steel are crucial in determining the final product's quality and performance. These processes not only dictate how the steel is shaped and formed but also influence its strength and durability, which are essential when transporting gases under high pressures. Understanding these intricate methods provides insight into the standards that the gas pipeline industry upholds and helps ensure safety and efficiency.
Steel Pipe Production Techniques
Welding Methods
Welding methods play a vital role in the production of steel pipes. This technique involves joining together metal pieces by melting the edges and adding a filler material. The key characteristic of welding is its versatility; it allows manufacturers to fabricate complex shapes and sizes of pipes, suitable for varied applications. Notably, the process can be adapted to use different types of filler materials, which enhances the strength of the weld joint.
Welding is a popular choice in the gas pipe steel industry because it facilitates the construction of long sections of pipeline without the need for additional joints, reducing potential failure points. However, one must consider the distinctive feature that while welding can produce strong joints, improper techniques can lead to defects, such as cracks or weaknesses in the weld. These imperfections could potentially compromise the integrity of the entire pipeline, leading to dangerous situations. Therefore, the success of welding methods entirely depends on the skills of the operators and the quality of materials used during the process.
Seamless vs. Welded Pipes
When we look at seamless versus welded pipes, both have unique aspects that contribute to their functionality in gas pipe applications. Seamless pipes are created by pushing heated steel through a mold, ensuring no weld seams exist, which often results in stronger, more durable pipes. The significant advantage of seamless pipes lies in their resistance to pressure; they can often handle higher internal forces than their welded counterparts. This makes them a choice for applications that demand high reliability, such as high-pressure gas systems.
On the other hand, welded pipes come at a reduced cost and can be produced in a wide variety of sizes. Their flexibility makes them ideal for varied industrial uses where specific dimensions and shapes are needed. Nevertheless, the welds themselves can be weak points, and, if not manufactured carefully, may lead to potential failure under stress conditions. Thus, the choice between seamless and welded pipes essentially boils down to the specific needs of the project at hand, weighing factors like cost, strength, and ease of installation.
Quality Control in Production
Ensuring that the gas pipe steel meets required standards necessitates rigorous quality control in the production process. This not only assures manufacturers of the product's safety but also provides confidence to end users relying on these materials for critical applications.
Testing Methods
Testing methods serve as a crucial backbone in quality control. These methods validate the physical properties and performance of the pipes. Common testing strategies include ultrasonic, radiographic, and hydrostatic tests. Each method offers a unique insight into the pipe structure. For example, hydrostatic testing involves filling the pipe with water and increasing the pressure to ensure that the seams hold. This method is preferred as it mimics real-life operating conditions.
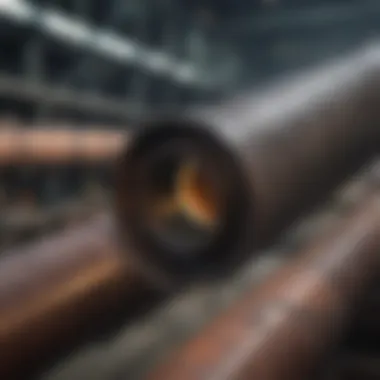
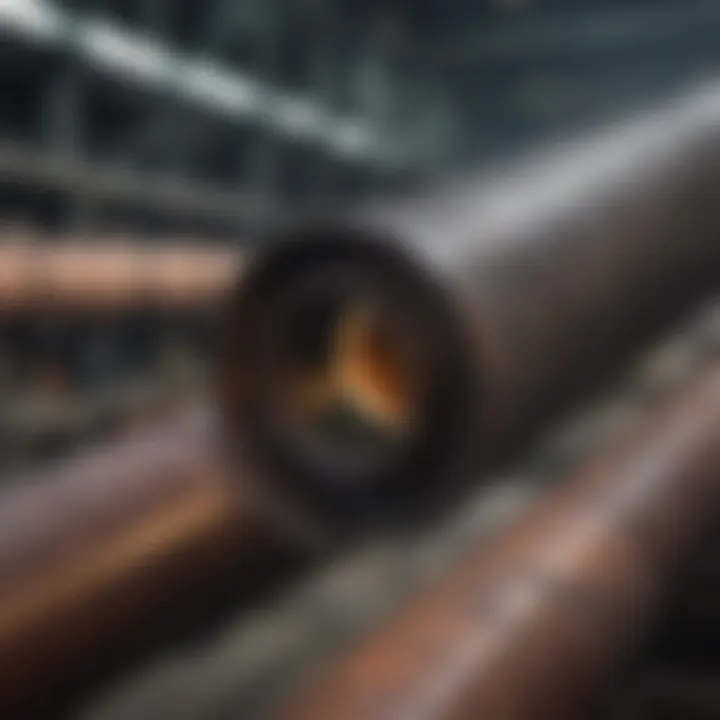
The benefit of employing various testing methods is that they highlight any flaws or imperfections prior to installation, preventing costly failures in the field. However, reliance on multiple tests can extend the production timeline, posing challenges for manufacturers under tight deadlines.
Certification Processes
Certification processes entail the evaluation and validation of the manufacturing process and materials used in gas pipe production. This may involve third-party inspections to confirm adherence to industry standards, such as those established by ASTM or API.
A key feature of certification processes is that they provide a surefire way to ensure quality that meets regulatory requirements. This is particularly beneficial for projects that require compliance with stringent safety standards, making it easier to secure contracts and project approvals. However, this process can also be resource-intensive, requiring advanced documentation and compliance checks, which could lead to increased costs for manufacturers.
In summary, the manufacturing processes related to gas pipe steel play a significant role in performance, safety, and compliance with industry standards. Understanding the intricacies of welding techniques, the pros and cons of seamless versus welded pipes, and the vital role of quality control assures stakeholders of the reliability in pipeline infrastructures.
Applications of Gas Pipe Steel
Gas pipe steel serves as a backbone across various industries, acting as more than just a conduit for fluid transfer. It symbolizes safety, efficiency, and reliability in operations that range from domestic heating to large-scale manufacturing processes. Its relevance cannot be overstated, as it ensures that natural gas and other hydrocarbons reach their intended destinations without leaks or safety incidents.
One significant application is in gas transportation, where specific steel grades are selected for their strength, ductility, and corrosion resistance. Companies trust these materials for long-distance pipelines, knowing that they can withstand high-pressure environments and harsh external conditions. The ability of gas pipe steel to adapt to varying temperatures and pressures makes it invaluable in the transportation sector.
Additionally, gas pipe steel is present in industrial uses, serving essential functions in both manufacturing and the energy sector. This versatility positions it as a key ingredient in modern infrastructure. Let’s dive deeper into these crucial applications and why they matter in today’s world.
Gas Transportation
Transporting gas is like navigating the arteries of a city—each pipeline is vital to ensuring fluid movement and energy distribution. Gas transportation networks rely heavily on high-quality steel pipes that not only facilitate the flow of gas but also endure the dangers associated with high pressure. The design and implementation of these pipelines undergo rigorous testing, owing to the potential implications of system failures.
Key Benefits:
- Durability: Piping systems resist deformation and environmental wear.
- Safety: Steel pipes reduce the chances of leaks compared to other materials.
- Efficiency: High-grade steel offers thermal efficiency, ensuring minimal energy loss during transit.
Given the remote locations of many gas reserves, the ability to construct and maintain lengthy pipelines effectively is critical. Advanced welding techniques and automated machinery play a significant role in enhancing the quality of installations.
Industrial Uses
In the industrial realm, gas pipe steel finds its place in numerous sectors. Its attributes fulfill the functional needs of several industries, with manufacturing being a primary player.
Manufacturing
The manufacturing sector's reliance on gas pipe steel is substantial. The material's ability to withstand extreme conditions makes it a popular choice in facilities where gas is used for heating processes, machinery operation, and even in some chemical reactions.
Key Characteristic: Strength Under Pressure
Gas pipe steel can handle significant pressure changes without compromising integrity. This characteristic is essential when moving materials through various stages of production, ensuring uninterrupted operations.
Why It's Beneficial:
Manufacturers favor gas pipe steel for its cost-effectiveness and longevity. Frequent replacement due to wear and tear can be financially draining; therefore, investing in reliable pipe solutions leads to long-term savings and enhanced operational efficiency.
Unique Feature:
One notable feature is the adaptability of steel pipes to different production layouts, allowing for flexible design and installation. This adaptability offers manufacturers the freedom to configure their operations without worrying about pipeline failure.
Energy Sector
Gas pipe steel is indispensable in the energy sector as well. This field demands not only reliability but also enhanced performance under challenging conditions, perfect for gas transportation systems that reach power plants and refineries.
Key Characteristic: Resistance to Corrosion
Given the aggressive nature of materials moved through pipelines, resistance to corrosion is paramount. Steel pipes come treated with protective coatings that shield against environmental damage, extending their lifespan significantly.
Why It's Beneficial:
For energy companies, choosing gas pipe steel translates to lower operational risks and reduced maintenance costs. The technology behind these pipes ensures that companies adhere to stringent regulations while benefiting from enhanced safety and efficiency in their processes.
Unique Feature:
The integration of smart technologies can enhance pipeline monitoring. Sensors applied to steel pipes can detect potential issues before they escalate, ensuring that the integrity of the entire system is maintained.
"Gas pipe steel is not just a material; it's a commitment to safety, efficiency, and the future of energy distribution."
In summary, the applications of gas pipe steel in gas transportation and industrial uses underline its importance in maintaining infrastructure integrity. From manufacturing to energy production, its versatility and strength make it a pivotal choice in various applications. The significance of proper material selection cannot be overstated, especially in an era that prioritizes sustainability and operational efficiency.
Safety and Environmental Considerations
The discussion around gas pipe steel transcends beyond its mere physical and chemical properties; it elbow nudges its way into the realms of safety and environmental responsibility. An industry that relies heavily on gas transportation must place utmost priority on safety protocols and environmental practices. These two factors not only influence regulatory compliance but also commendably affect public perception and trust.
Regulatory Frameworks
In any discussion about safety and environmental impacts, regulatory frameworks take center stage. Regulatory bodies, both national and international, have established stringent guidelines to manage how gas is stored, transported, and eventually utilized. Agencies like the Pipeline and Hazardous Materials Safety Administration (PHMSA) in the United States spearhead the enforcement of safety standards for pipeline systems. They focus on a variety of regulations concerning material weaknesses, operational protocols, and mandatory inspections.
Additionally, different countries have their own detailed regulations that govern pipeline safety standards; these can differ significantly. For instance:
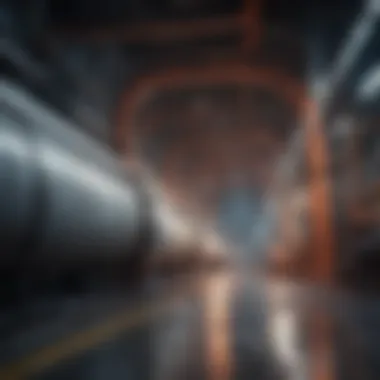
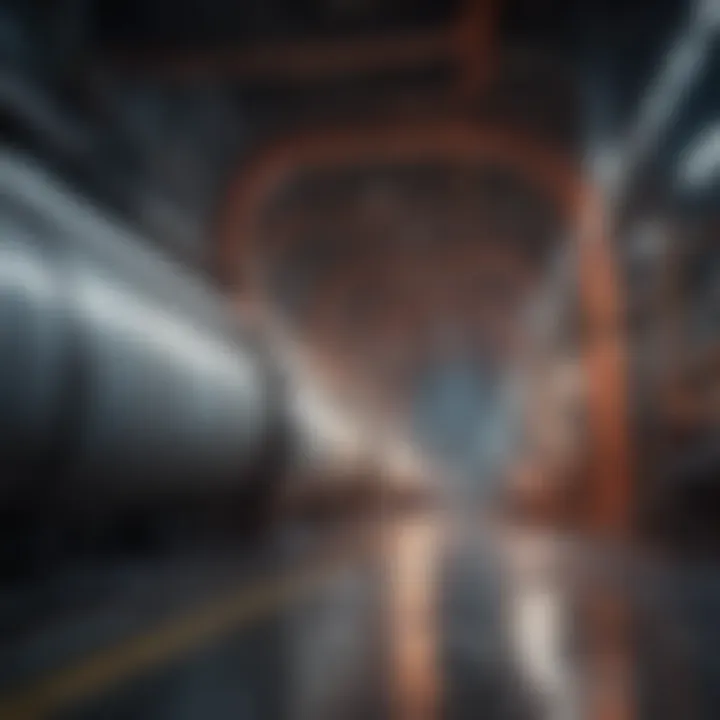
- In Europe, the European Union's regulations emphasize not only safety but also the environmental impact assessments needed for gas project approvals.
- In Canada, the National Energy Board (NEB) oversees safety regulations specific to pipelines.
These frameworks aim to mitigate risks associated with transporting explosive and volatile substances. By adhering to these_, organizations ensure they comply with legal requirements, thereby reducing the likelihood of accidents, leaks, or any environmental degradation.
Environmental Impact Assessments
Environmental Impact Assessments (EIAs) serve as a critical tool in understanding how pipeline projects can affect local ecosystems. Before any major project gets off the ground, it is essential to evaluate potential environmental consequences. The EIA process typically includes:
- Identifying the potential environmental impacts associated with the project.
- Evaluating alternatives that might reduce or eliminate negative effects.
- Involving public opinion and local communities in discussions about risks and benefits.
These assessments regard factors such as soil erosion, water quality, and biodiversity. One of the significant aspects of these evaluations is that they can promote the adoption of innovative developments in gas pipe steel technologies tailored to minimize harm. For example, advanced coatings and treatments discussed earlier not only enhance the longevity of the pipes but also reduce the chances of corrosion, which can lead to leaks.
By tackling both safety and environmental concerns proactively, industries can protect the environment while maintaining operational efficiency.
"Investing in safety and environmental compliance is investing in a sustainable future for gas transportation."
Innovations in Gas Pipe Steel Technology
In a rapidly evolving industrial landscape, innovations in gas pipe steel technology play a pivotal role. These advancements are not just about enhancing the materials used in gas pipelines; they directly influence the efficiency, safety, and sustainability of gas transport systems globally. As economic and environmental pressures mount, stakeholders are pushed to seek better solutions that stand the test of time while minimizing adverse effects.
Advanced Coatings and Treatments
One of the foremost innovations in gas pipe steel technology is the development of advanced coatings and treatments. These enhancements are designed to improve the longevity and performance of gas pipelines.
- Corrosion Resistance: Modern coatings can effectively prevent corrosion, a primary threat to the integrity of steel pipes. For instance, the application of fusion-bonded epoxy or polyurethane coatings provides a robust barrier against moisture and contaminants that may lead to corrosion.
- Thermal Insulation: Some treatments focus on enhancing thermal insulation properties. This is crucial for transporting gases at specific temperatures, thereby aiding in the maintenance of operational efficiency. Enhanced thermal insulation can help in reducing energy loss and maintaining gas quality throughout transportation.
- Nanotechnology Applications: The use of nanomaterial-based coatings is another emerging area. These coatings can dramatically improve surface properties, ensuring that pipes are less prone to damage and wear. As research advances, the potential for significantly elevated performance standards becomes clear.
"Innovative coatings not only prolong the lifespan of gas pipes but also boost overall system efficiency. The future of gas transportation depends on such technologies."
Smart Pipeline Technologies
As technology progresses, integrating smart pipeline technologies into the gas industry is becoming increasingly prevalent. These innovations are reshaping how pipelines are monitored, managed, and maintained.
- Sensors and Monitoring Systems: Using IoT (Internet of Things) technology, sensors can be embedded within pipelines, providing real-time data on pressure, temperature, and chemical composition of the gas. This data allows for timely interventions if any anomalies are detected, reducing risks associated with leaks or ruptures.
- Predictive Maintenance: With the help of machine learning algorithms and predictive analytics, stakeholders can accurately determine when maintenance is needed, preventing potential failures before they occur. This proactive approach can save both time and money in the long run, and it minimizes the risks of unexpected downtime.
- Data Integration and Analysis: These smart technologies often encompass sophisticated data integration systems, which compile information from various sources. This allows for comprehensive analyses of pipeline performance, enabling better decision-making regarding maintenance and upgrades.
Challenges and Future Directions
In the realm of gas pipe steel, the landscape is constantly evolving, fraught with challenges and brimming with opportunities for advancements. An understanding of these challenges is imperative, as it ensures the integrity of infrastructure and the safety of those who depend upon it. From mitigating risks associated with pipeline integrity to embracing future research, the field is at a critical juncture.
Pipeline Integrity Issues
Ensuring pipeline integrity presents a formidable challenge. Aging infrastructure often leads to vulnerabilities that can cause leaks, ruptures, and environmental hazards. The effects of these issues are not merely theoretical; incidents such as the well-publicized pipeline leaks have underscored their real-world impacts. For instance, an incident in Kalamazoo, Michigan, demonstrated how a single failure can trigger environmental catastrophes and public outcry.
Addressing these concerns involves several key measures:
- Regular Inspections: Technologies such as smart pigs—devices that travel through pipes to gather data—play a vital role in monitoring the condition of gas pipelines.
- Corrosion Management: Understanding the mechanisms behind corrosion is essential. Innovations in coatings and inhibitors can prolong the life span of pipelines and maintain their integrity.
- Pressure Management: Keeping an eye on pressure levels is crucial. Imbalances can compromise pipe strength over time, necessitating stringent pressure regulation protocols.
The importance of tackling integrity issues cannot be overstated. Maintaining the structural soundness of pipelines protects not only the environment but also public safety and corporate reputations. The reliable delivery of gas depends upon a attention to these looming integrity risks.
Future Research and Developments
Looking ahead, the field of gas pipe steel stands ready for extensive research and development. Innovations are on the horizon, aimed at enhancing performance and sustainability. The following areas are ripe for exploration:
- Material Science Advancements: Research into high-strength, lightweight materials could lead to revolutionary changes in pipe design, reducing transportation and installation costs.
- AI and Predictive Maintenance: Implementing data analytics and machine learning can facilitate predictive maintenance strategies. Such approaches can foresee issues before they escalate into serious failures.
- Sustainable Practices: The push for sustainability compels researchers to focus on eco-friendly production methods. Developing pipes from recycled materials or utilizing biocompatible coatings may present viable paths forward.
"Investing in research is like planting seeds for future forests. What we nurture today can yield resources to revolutionize the industry tomorrow."
The challenges of today are indeed the stepping stones for the innovations of tomorrow. By confronting pipeline integrity issues head-on and embarking on promising research paths, the field of gas pipe steel can support a resilient and sustainable infrastructure for future generations.
Finale
In wrapping up our discussion on gas pipe steel, it’s crucial to take a step back and appreciate the intricate tapestry woven by its applications, standards, and innovations. Gas pipe steel stands as a backbone for various industries, playing an essential role in ensuring safety, efficiency, and reliability in gas transportation.
One takeaway is the sheer diversity of applications. From the energy sector to manufacturing, the versatility of gas pipe steel showcases its engineered properties designed to withstand harsh environments and stresses. The strength and durability of these materials not merely fulfill regulatory requirements; they exceed them, thanks to advancements in technology and production methods. This, in turn, offers industries a safety net against failures that can prove catastrophic.
Furthermore, adherence to established standards, like ASTM and API, ensures that safety measures are up to scratch and that production processes maintain high quality. These frameworks, while sometimes seen as mere bureaucratic hurdles, are actually pillars holding up the integrity of pipelines and protecting not just infrastructure but also the communities surrounding these installations. For instance, a failure in pipeline integrity could lead to environmental damage, economic loss, and even loss of life. Therefore, rigorous adherence to these standards cannot be overstated.
Moreover, as we look towards the future, innovative advancements in gas pipe steel technologies—such as smart pipeline technologies—are paving the way for enhanced monitoring, maintenance, and overall performance. The potential for integrating digital solutions offers exciting prospects for real-time data analysis and proactive measures in pipeline management. This isn’t just a nice-to-have but a necessity in an era where efficiency and sustainability are paramount.
"Safety is never an accident; it is always the result of intelligent planning and execution."
Thus, this article serves not merely as an educational piece but as a call to action for students, researchers, and industry professionals alike to engage deeply with this essential material and its implications in modern infrastructure. By fostering a robust dialogue around these topics, we can pave the path toward safer, more effective methods of gas transportation.