Production 4.0: The Future of Smart Manufacturing
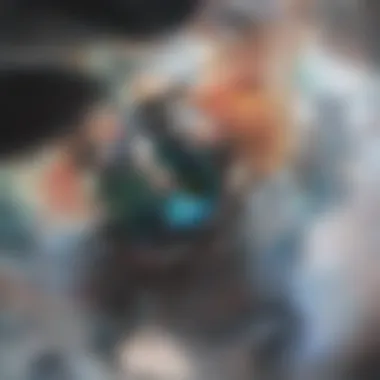
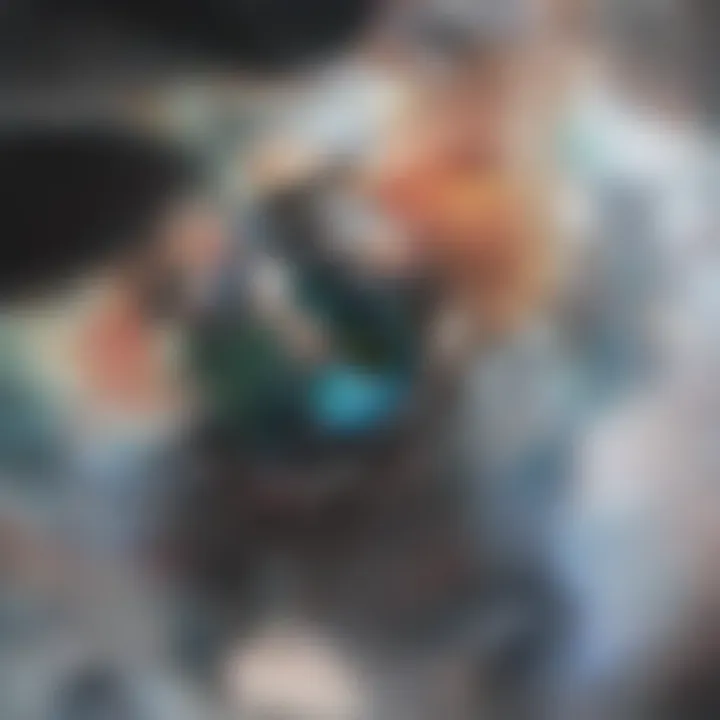
Intro
The rapid advancement of technology has been reshaping various sectors, but manufacturing is undergoing a unique transformation. The term Production 4.0 encapsulates this shift towards a more digital and interconnected manufacturing ecosystem. In an era defined by digitization, automaton and data analytics, traditional practices face significant changes. This article aims to provide a deeper understanding of Production 4.0, primarily by examining its concepts, technologies, and its extensive implications on the manufacturing sector.
Key Concepts
Definition of Primary Terms
Production 4.0 represents a paradigm shift in manufacturing. This concept revolves around the integration of cyber-physical systems, the Internet of Things (IoT), and cloud computing within production processes. The objective is to create smart factories, where machines communicate with one another and data drives decision-making.
- Cyber-Physical Systems (CPS): These are integrations of computation, networking, and physical processes. They enable real-time monitoring and control of manufacturing systems.
- Internet of Things (IoT): A network of physical devices connected to the internet, which allows them to gather and exchange data.
- Cloud Computing: Utilizing remote servers to store, manage, and process data, enabling flexibility and scalability in manufacturing operations.
Related Concepts and Theories
Production 4.0 is deeply linked to several broader concepts in the realm of technological advancement.
- Industry 4.0: The fourth industrial revolution, characterized by smart production, integrating various technologies.
- Lean Manufacturing: A systematic approach to minimizing waste within manufacturing systems, which can be enhanced through digital tools.
- Automation and Robotics: These technologies streamline processes, improve efficiency, and reduce human error, complementing Production 4.0 initiatives.
Each of these concepts contributes to the foundation upon which Production 4.0 builds upon. They highlight the relevance of innovation and adaptability in today's manufacturing landscape.
"The integration of advanced technologies in manufacturing is not just a trend but a necessary evolution to stay competitive."
Future Directions
Gaps Identified in Current Research
While there is significant discourse on Production 4.0, some facets remain underexplored. For instance, the full impact of cybersecurity risks associated with IoT devices in manufacturing is still being understood. Moreover, research on the effects of worker adaptation to automated systems is limited.
Suggestions for Further Studies
To fortify the understanding of Production 4.0, future research should consider:
- In-depth Analysis of Cybersecurity Issues: Investigating how to safeguard smart factories against potential threats.
- Human-Machine Interaction Studies: Observing how workers adapt to and interact with increasingly automated environments.
- Sustainability and Eco-Efficiency Research: Assessing how these technologies impact environmental sustainability in manufacturing.
Research in these areas could bridge the gaps currently present and pave the way for a more resilient production landscape.
Understanding Production 4.
Understanding Production 4.0 is crucial for anyone interested in the current and future landscape of manufacturing. This era marks a significant evolution, where traditional processes integrate seamlessly with advanced technologies. The implications of this shift extend beyond mere efficiency; they encompass changes in business models, workforce dynamics, and sustainability practices. In this context, grasping the core elements of Production 4.0 is essential for stakeholders to remain competitive.
Defining the Industrial Revolutions
The history of manufacturing can be divided into several major industrial revolutions. The First Industrial Revolution began in the late 18th century, introducing mechanical production systems powered by water and steam. The Second Industrial Revolution occurred in the late 19th century, characterized by mass production enabled by electricity. Later, the Third Industrial Revolution emerged in the late 20th century, marked by digital technologies and automation.
Production 4.0 represents the Fourth Industrial Revolution, characterized by the fusion of advanced digital technologies. It combines concepts like the Internet of Things (IoT), artificial intelligence, and big data into one cohesive framework. The distinction of this period lies in how these technologies interact with manufacturing processes, creating a smart, interconnected environment.
Key Characteristics of Production 4.
Several notable characteristics define Production 4.0:
- Connectivity: All devices and systems are interconnected, enabling real-time data exchange.
- Decentralization: Decision-making is distributed across various devices, allowing for autonomy in production processes.
- Smart Manufacturing: Machines are equipped with intelligence, enhancing their capabilities to optimize processes.
- Customizability: Production can be adjusted in real-time to meet specific customer demands, promoting agile responses to market changes.
These features enhance efficiency, reduce errors, and permit greater flexibility within manufacturing operations. They allow organizations to adapt quickly to shifting market conditions while maintaining high levels of productivity.
The Evolution from Production 3.
Production 3.0 significantly relied on automation and computers to enhance manufacturing capabilities. However, this framework often remained siloed, with limited data sharing between machines, leading to inefficiencies. In contrast, Production 4.0 builds on this foundation by promoting interconnectedness among devices and systems.
The leap from Production 3.0 to 4.0 is evident in the following aspects:
- Integration of Technologies: Instead of isolated systems, Production 4.0 encourages a holistic approach where all elements work together.
- Enhanced Data Utilization: Organizations leverage data analytics to gain insights previously hidden in data silos.
- Proactive Maintenance: The shift towards predictive maintenance enhances the efficacy of production operations, reducing downtime significantly.
Understanding these evolutions is vital for companies to navigate the complexities of this new era effectively.
"The future of manufacturing is not just about machines, but the integration of technologies and data-driven decisions that shape how we produce and innovate."
Embracing these components is not optional but a necessity for those aspiring to thrive in the digitally transformed landscape of manufacturing.
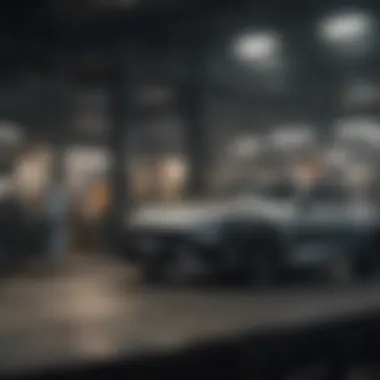
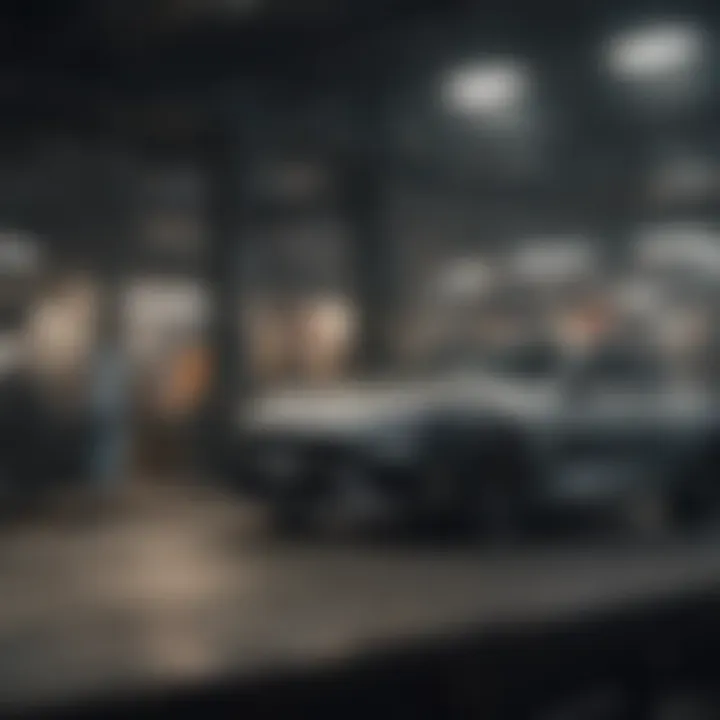
Technological Innovations Driving Production 4.
The emergence of Production 4.0 is heavily influenced by technological innovations that reshape traditional manufacturing. Digital transformation integrates technologies in unprecedented ways. As a result, industries must adapt to maintain competitiveness. Technological innovations propel this shift, enhancing efficiency, productivity, and flexibility.
IoT and Smart Manufacturing
The Internet of Things (IoT) is a cornerstone of Production 4.0. It connects devices, enabling seamless communication. This connectivity allows for real-time monitoring of production processes. Sensors gather data, providing insights into operational efficiency. Manufacturers can identify bottlenecks promptly, reducing downtime.
With smart manufacturing, production lines become more adaptive. Systems can respond to changes in demand swiftly. For instance, adjustments in machine settings can occur automatically based on real-time analytics. Such flexibility leads to optimized resource usage and minimized waste.
A significant advantage of IoT is predictive maintenance. Devices can self-diagnose issues before they escalate. By addressing potential failures early, companies can avoid costly downtime and extend equipment lifespan. The overall result is a more resilient and efficient manufacturing environment.
Artificial Intelligence in Production
Artificial Intelligence (AI) plays a transformative role in manufacturing. It enhances decision-making through advanced data analysis. AI systems can process vast amounts of data, uncovering patterns and trends that humans might overlook. This capability enables smarter forecasting and inventory management.
Moreover, AI-driven robots can improve production processes. They adapt to changes in real-time, optimizing workflows based on current conditions. This adaptability leads to increased output and lower operational costs.
In addition, AI enhances quality control. Machine learning algorithms can analyze products in real-time, detecting defects and ensuring consistent quality. This level of monitoring reduces waste and rework, creating a more sustainable approach to production.
Robotics and Automation
Robotics and automation are integral to the evolution of manufacturing. Automated systems reduce human intervention, increasing speed and precision in production lines. This automation minimizes errors, which leads to higher quality products.
Robotics technology has advanced significantly. Collaborative robots, or cobots, work alongside human operators. This partnership enhances productivity while ensuring workplace safety. By taking over repetitive tasks, cobots allow humans to focus on more complex and strategic roles.
Furthermore, the integration of robotics with AI creates intelligent automation systems. These systems learn from their surroundings and continuously improve their performance. The benefits include lower operating costs, increased efficiency, and the ability to scale operations without significant overhead.
"Technological innovations are not just tools; they are the foundation for the next generation of manufacturing."
In summary, the technologies driving Production 4.0 provide manufacturers with unprecedented capabilities. The integration of IoT, AI, and robotics not only enhances efficiencies but also prepares industries for future challenges. As these technologies continue to evolve, the manufacturing landscape will witness substantial transformations, fostering innovation and growth.
Integrating Data Analytics in Manufacturing
In the context of Production 4.0, integrating data analytics into manufacturing processes emerges as a vital component. The intersection of data analytics and manufacturing enables organizations to harness the potential of data generated across various stages of production. This integration facilitates improved efficiency, cost reduction, and informed decision-making.
Data analytics allows manufacturers to collect and interpret vast amounts of data. This entails understanding production patterns, resource usage, and equipment performance. By analyzing this data, companies can identify trends, predict outcomes, and implement solutions tailored to specific challenges. The benefits include enhanced operational efficiency and the ability to respond quickly to market changes.
The Role of Big Data
Big data refers to the immense volume of data collected during manufacturing processes. This data can originate from sensors, machines, and employee input. The significance of big data lies in its ability to provide insights that were previously unattainable.
When manufacturers analyze big data, they gain a granular understanding of their operations. This knowledge can lead to improvements in several areas:
- Operational efficiency: Identifying bottlenecks and inefficiencies can streamline processes.
- Quality assurance: Tracking product defects helps in maintaining high quality standards.
- Market responsiveness: Real-time data allows businesses to adapt to customer demands immediately.
Predictive Maintenance Applications
Predictive maintenance is another essential aspect of data analytics in manufacturing. By utilizing data collected from machinery, manufacturers can predict when equipment is likely to fail. This approach mitigates the risk of unexpected downtimes that can lead to hefty costs.
Predictive maintenance employs algorithms and machine learning to analyze patterns in equipment performance. By doing so, manufacturers can schedule maintenance during non-peak hours, minimizing operational disruptions. This data-driven approach contributes significantly to cost savings and maximizes equipment lifespan.
"Prioritizing predictive maintenance transforms reactive practices into proactive strategies in the manufacturing sphere."
Data-Driven Decision Making
In the age of Production 4.0, data-driven decision making stands as a pillar for business success. Traditional decision-making processes often relied on intuition or past experiences, which can lead to inefficiencies. With data analytics, manufacturers have access to concrete evidence supporting their choices.
Data-driven decision-making encompasses various facets:
- Resource allocation: Understanding which resources yield the best results ensures strategic investments.
- Customer preferences: Analyzing buyer trends aids in tailoring products that meet market needs.
- Risk management: Predictive analytics can identify potential risks, enabling proactive management solutions.
Through integrating data analytics effectively into their operations, manufacturers are not only optimizing their processes but also positioning themselves competitively in an evolving market landscape.
Impacts on Workforce Dynamics
The concept of Production 4.0 reshapes the traditional manufacturing landscape, and inevitably, this transformation impacts workforce dynamics. As machines become smarter and processes more automated, the skills required of workers are also evolving. This section aims to dissect how these changes affect the workforce, highlighting the new skill requirements, the necessity of reskilling and upskilling, and the collaborative nature between humans and machines.
Changing Skill Requirements
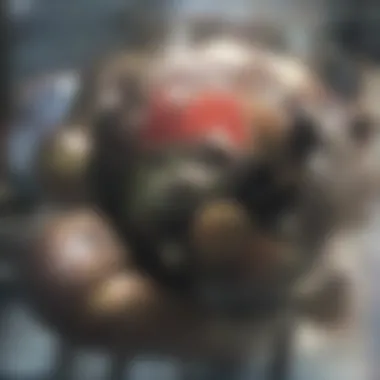
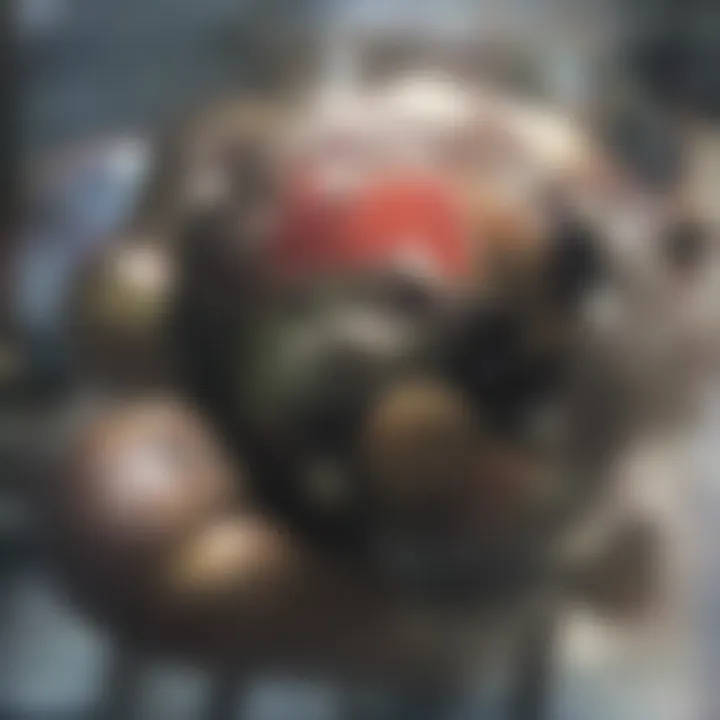
The transition to Production 4.0 demands a shift in the skill set of the workforce. Traditional manufacturing skills may no longer suffice. Workers now need to have a grasp of technology, particularly tools involving data analytics, artificial intelligence, and the Internet of Things.
The following skills are becoming essential:
- Technical proficiency in operating advanced machinery.
- Analytical skills to interpret data from automated systems.
- Adaptability, as workers will face ongoing changes in technology and processes.
In essence, industries must prepare employees not just for current roles but for future innovations that are yet to emerge. Skills that enable them to engage with technology effectively will be crucial in this new era.
Reskilling and Upskilling for the Future
Organizations are now obligated to invest in comprehensive training programs to equip their employees with necessary skills. Reskilling and upskilling methods are paramount to ensure workers can handle new technologies. Companies like Siemens and Bosch have implemented successful training initiatives focused on digital skills. Through hands-on workshops and online learning platforms, they help employees transition smoothly into roles that require more sophisticated knowledge.
"The future of manufacturing is not just about machines, but about people adjusting to machines."
Moreover, providing ongoing education fosters loyalty and engagement within the workforce. Employees who receive regular training feel valued and are more inclined to contribute meaningfully to their organizations. In this context, continuous education becomes a strategic advantage.
The Role of Human-Machine Collaboration
As automation rises, the interaction between humans and machines becomes more important. In the realm of Production 4.0, workers often collaborate with sophisticated machines that assist in various tasks. This synergy promotes efficiency and precision in manufacturing processes.
Benefits of human-machine collaboration include:
- Enhanced productivity, as machines handle repetitive tasks and allow workers to focus on more complex issues.
- Reduced error rates, as machines consistently perform tasks with high accuracy.
- The fostering of a creative environment, where humans can apply their problem-solving skills alongside advanced technology.
Manufacturers need to rethink their operational strategies to harness the full potential of this relationship. Training programs should emphasize not only how to work alongside machines but also how to leverage these technologies to augment human capabilities.
Supply Chain Resilience in the Digital Age
Supply chain resilience has become a crucial focus for manufacturers as they navigate the complexities of today's market. The rise of digital transformation has reshaped how businesses manage their supply chains. In this context, resilience refers to the ability to anticipate, prepare for, respond to, and recover from disruptions. The benefits of a resilient supply chain include enhanced operational efficiency, reduced costs, and improved customer satisfaction. Organizations that cultivate resilience can withstand unexpected changes, such as geopolitical issues, natural disasters, and global pandemics.
Blockchain for Supply Chain Transparency
Blockchain technology offers a promising solution for enhancing supply chain transparency. By creating a decentralized ledger, blockchain enables all parties to share and verify data securely. This technology ensures that every transaction is recorded and traceable. As products move through the supply chain, stakeholders can access real-time information about origin, quality, and compliance. For instance, companies can track the path of raw materials from suppliers to the end consumer, minimizing the risk of fraud and assuring product authenticity. Moreover, transparency leads to better decision-making, as data is accessible and verifiable by all partners involved.
Agile Manufacturing Practices
Agile manufacturing practices have emerged as a method to enhance supply chain resilience. These practices focus on flexibility and responsiveness to market demands. By adopting agile methodologies, manufacturers can quickly adapt to changes in production volumes and product offerings. This approach reduces lead times and enhances the ability to meet customer needs. Key to agile manufacturing is the integration of advanced technologies such as IoT, which enables real-time monitoring of processes. This data helps organizations fine-tune their operations and respond promptly to disruptions.
Global Sourcing and Localized Production
Global sourcing and localized production strategies help companies balance efficiency with resilience. Global sourcing involves procuring materials from a variety of international suppliers to reduce costs. However, this approach can lead to vulnerabilities, especially in times of crisis. Localized production, on the other hand, encourages manufacturers to establish production facilities near their key markets. This strategy allows for quicker response times and reduces transportation costs. Striking the right balance between these two strategies can also mitigate risks associated with supply chain disruptions. By diversifying their sourcing options and establishing local production capabilities, companies can build a more robust supply chain that can adapt to changing conditions.
"In today's interconnected world, supply chain resilience is not just an advantage; it is a necessity for long-term survival and growth in the manufacturing sector."
Cultivating supply chain resilience through these strategies equips manufacturers to tackle current and future challenges. As the digital age progresses, companies must continually evaluate their approaches to ensure that their supply chains remain not only functional but also adaptable to a rapidly evolving landscape.
Sustainability in Production 4.
Sustainability has become a critical focus in manufacturing in the context of Production 4.0. It integrates technological innovation with environmentally responsible practices. As the demand for sustainable products increases, businesses must adapt their approaches to mitigate negative impacts on the environment. In doing so, they not only comply with regulations but also meet the expectations of consumers who are increasingly aware of ecological issues. Transitioning towards sustainable practices fosters resilience in supply chains and promotes long-term growth.
Environmentally Responsible Manufacturing
Environmentally responsible manufacturing is essential in the era of Production 4.0. This concept involves minimizing waste, reducing emissions, and enhancing energy efficiency throughout the production process. Moreover, manufacturers are now embracing cleaner technologies that limit harmful discharges. Implementations such as closed-loop systems, which recycle waste materials, are becoming more common. Companies can adopt eco-friendly materials and production methods to lessen their environmental footprint.
Investing in environmentally responsible practices can lead to significant cost savings and improved brand reputation.
This shift not only benefits the planet but also opens new markets, as consumers tend to prefer sustainably produced goods.
Circular Economy Practices
Circular economy practices play a crucial role in reshaping manufacturing strategies under Production 4.0. In contrast to the traditional linear model, the circular economy focuses on resource efficiency and product lifecycle management. It encourages designing products for longevity and reusability. Companies are now exploring ways to repurpose materials, thus minimizing waste. This transition fosters innovation and requires collaboration across the supply chain. By doing so, organizations can turn products at the end of their life into valuable resources.
Key principles of the circular economy in manufacturing include:
- Reducing resource consumption
- Encouraging recycling and reuse
- Implementing modular designs
These practices contribute to sustainable development goals and ensure a more resilient economy.
Regulatory Compliance in Sustainability
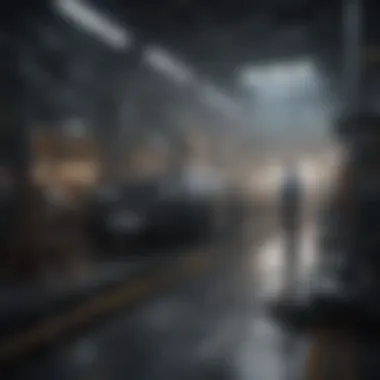
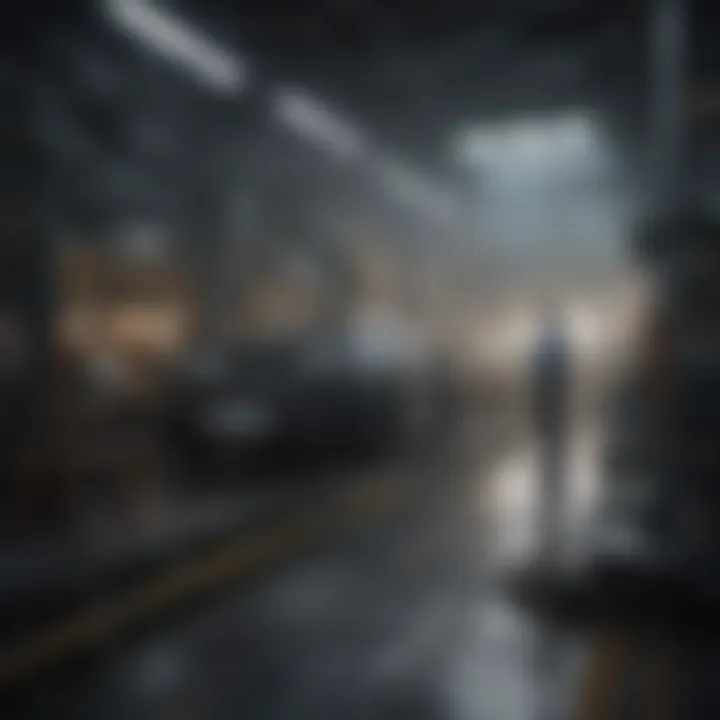
Regulatory compliance is another important aspect of sustainability in Production 4.0. As governments worldwide enforce stricter environmental regulations, companies must stay ahead of compliance to avoid penalties and reputational damage. Adopting proactive measures is crucial. Organizations should regularly assess their processes for adherence to existing regulations while anticipating future legal requirements.
Compliance not only safeguards against legal repercussions but also enhances operational efficiency. By aligning with regulatory frameworks, manufacturers can streamline their processes and reduce waste. Furthermore, sustainability certifications can serve as a competitive advantage, attracting consumers who prioritize eco-friendly practices. In essence, integrating sustainability into manufacturing is not only about meeting laws but also about nurturing a responsible business ethos.
Challenges and Risks in Transitioning to Production 4.
The transition to Production 4.0 is not without its challenges and risks. As organizations strive to adopt modern technologies and processes, they face several potential obstacles that can impede their progress. Understanding these challenges is essential for organizations that wish to leverage the benefits of the digital transformation in manufacturing. It not only helps in planning but also in mitigating risks associated with the transition.
Cybersecurity Threats
Organizations must pay close attention to cybersecurity as they integrate new technologies. The increased connectivity of devices in smart manufacturing systems creates more entry points for cyber threats. Data breaches and ransomware attacks can lead to substantial financial losses and damage to reputation. Therefore, manufacturers should implement robust cybersecurity measures, including firewalls, encryption, and regular security audits. Personnel should receive extensive training in security protocols to recognize and mitigate risks.
Investment and Cost Considerations
Transitioning to Production 4.0 demands significant financial investment. Companies need to allocate budgets for new technologies such as Internet of Things devices, artificial intelligence solutions, and advanced robotics. Additionally, ongoing costs for maintenance and updates can strain resources. Organizations must conduct thorough cost-benefit analyses to justify these investments. Sustainability in budgeting should also be considered, ensuring enough capital is available to scale solutions over time.
Resistance to Change within Organizations
Resistance to change is a prevalent challenge when adopting new practices and technologies. Employees may feel apprehensive about learning new skills or altering their workflows. This resistance can stem from fears of job loss or inadequacy in using new systems. It is crucial for organizations to foster a culture of openness and support. This includes transparent communication about the benefits of the transition and involving staff in the change process. Providing ongoing training and upskilling opportunities can also alleviate fears, encouraging a smoother transition.
The successful implementation of Production 4.0 depends largely on how well organizations navigate these challenges.
In summary, while challenges and risks exist in the transition to Production 4.0, proactive strategies can facilitate a smoother process. Addressing cybersecurity threats, carefully managing investments, and overcoming internal resistance are essential to fully realize the potential of the fourth industrial revolution.
Case Studies in Production 4.
Case studies are crucial for understanding the practical applications and implications of Production 4.0 in various industries. They provide tangible evidence about how digital transformation reshapes manufacturing processes and enhances competitiveness. By examining specific instances of implementation, companies can draw insights into successful strategies, recognizing the challenges and solutions that arise during the transition to a more integrated and automated production system.
Successful case studies reveal not just the outcomes but also the methodologies employed. They can serve as a guide for organizations aiming to embrace similar changes. Moreover, these examples highlight innovative practices around automation, data utilization, and workforce adaptation. They underscore the reality that, while technology plays a significant role, human factors are equally important in achieving successful outcomes in Production 4.0.
Successful Implementation in the Automotive Industry
The automotive industry exemplifies a sector that has successfully adopted Production 4.0 principles. Companies like Toyota and Tesla have integrated IoT and AI into their manufacturing processes, leading to increased efficiency and reduced waste. Automakers now utilize real-time data to optimize production lines, as well as to monitor the health of machines, reducing downtime significantly.
A critical component of these implementations is the ability to collect and analyze vast amounts of data generated during manufacturing. Advanced analytics empower manufacturers to make faster, data-driven decisions, aligning production closely with demand. Furthermore, human resources have been upskilled to effectively work alongside machines, leading to superior outcomes.
Lessons from Electronics Manufacturing
In the electronics sector, companies such as Samsung and Apple have leveraged the principles of Production 4.0 to innovate rapidly and efficiently. By incorporating advanced robotics and automation, these firms have streamlined their production lines, allowing for greater responsiveness to market changes.
One lesson learned from these implementations is the importance of flexibility. Production systems designed to be adaptable play a critical role in meeting the diverse needs of consumers. Prioritizing modular production and customizable workflows has proven beneficial. Additionally, the integration of supply chain management with real-time tracking ensures transparency and enhances collaboration among stakeholders.
Pharmaceutical Innovations Driven by Data
The pharmaceutical industry is another domain where Production 4.0 has demonstrated remarkable advancements. Companies such as Pfizer and Novartis have embraced data analytics to enhance research and development processes. Applying AI in drug discovery not only accelerates development time but also improves outcomes.
Moreover, the implementation of digital twin technology in manufacturing processes allows for simulations that can predict the performance of drugs. This method ensures high quality and compliance with regulatory standards. The shift towards data-driven methodologies in this field illustrates the power of technology to transform traditional practices, leading to better patient outcomes and streamlined operations.
"Case studies in Production 4.0 provide insights into innovative practices and reveal the nuanced pathways organizations can take to transition successfully into the future of manufacturing."
Understanding these case studies offers a roadmap for industries aiming to harness the benefits of digital transformations. They highlight the need for alignment between technology and workforce strategies to ensure a comprehensive approach to manufacturing challenges.
Future Trends in Production 4.
As we look toward the future, the concept of Production 4.0 continues to evolve. Understanding the upcoming trends is essential to grasp how they will shape the manufacturing landscape. The integration of emerging technologies influences not only productivity but also how businesses relate to consumers and respond to market demands. Future trends can lead to substantial benefits, including increased efficiency, reduced costs, and enhanced customer satisfaction. Additionally, it’s crucial to consider the implications of these trends on the workforce and organizational structures.
The Rise of Hyper-Personalization
Hyper-personalization is becoming a significant trend in manufacturing. As consumers seek products tailored to their specific preferences, businesses must adapt their production strategies. Through the use of advanced data analytics and Artificial Intelligence, companies can analyze consumer behavior to create customized solutions. This level of personalization fosters a connection between consumers and brands, leading to stronger customer loyalty. Moreover, companies using hyper-personalization can optimize their inventory, minimizing waste and enhancing operational efficiency.
Organizations adopting this model must invest in technologies that facilitate data collection and analysis. For instance, the deployment of Internet of Things (IoT) devices can provide real-time feedback, allowing manufacturers to adjust production processes rapidly.
Growth of Decentralized Manufacturing
Decentralized manufacturing has gained traction. The idea is to move production closer to end-users, minimizing logistics complexities and costs. By utilizing local resources and technologies, businesses can respond quickly to market changes and customer demands. This model enhances resilience by reducing dependency on global supply chains, making operations more agile.
In practice, decentralized manufacturing can leverage 3D printing technology, enabling small-scale production and customization. Companies like Local Motors demonstrate how decentralized manufacturing can be successfully implemented. Companies can harness innovation while ensuring a more sustainable approach to their production processes, promoting environmental stewardship.
Potential for Advanced Biotechnology Applications
Another key trend is the integration of advanced biotechnology into manufacturing processes. Biotechnological innovations can lead to increased production efficiencies and sustainable practices. For example, biomanufacturing can create products using renewable resources, reducing environmental impact and costs.
The application of biotechnology can also enhance product quality. Through genetic engineering and synthetic biology, manufacturers can develop superior materials and products with tailored properties. Industries such as pharmaceuticals have already begun to capitalize on these emerging technologies. The potential for growth in this area is vast, as businesses aim to innovate while addressing pressing global challenges like sustainability and resource scarcity.
The future of Production 4.0 is not just about efficiency but also addresses consumer preferences and sustainability.