Understanding Reflective Optical Encoders: Principles and Progress

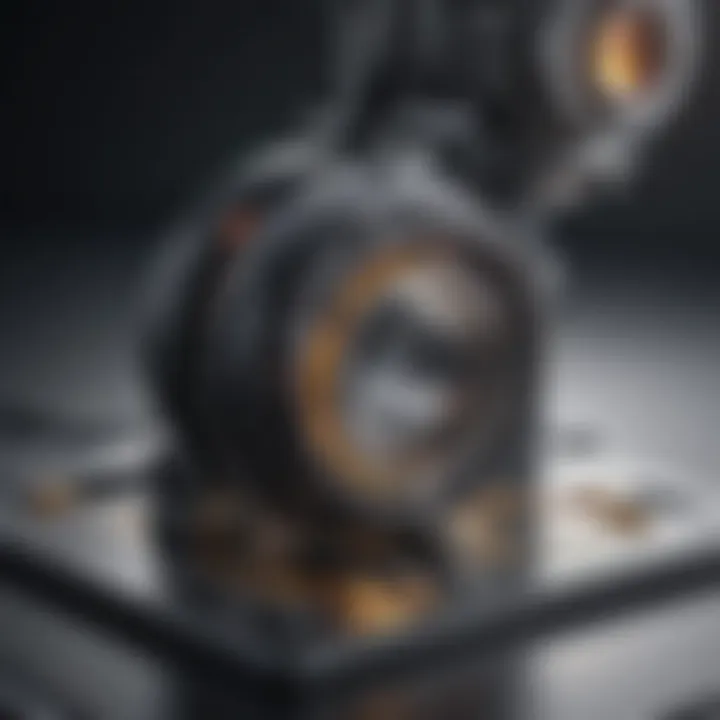
Intro
Reflective optical encoders play a crucial role in numerous electronic systems, serving as devices for measuring position, velocity, and other important metrics. The increasing reliance on automation and precision in industries such as robotics, manufacturing, and consumer electronics underscores the significance of these encoders. A proper understanding of their mechanics, applications, and advances is essential for professionals and enthusiasts in the field. By exploring what reflective optical encoders are, how they work, and where they are used, this article aims to illuminate their importance in modern technology.
Key Concepts
Reflective optical encoders utilize a light source and a photodetector to count angular or linear movement. As a component of feedback systems, they relay information about an object's position back to a controller or microprocessor.
Definition of Primary Terms
- Reflective Optical Encoder: A sensor that detects movement or position changes using light reflection.
- Light Emitting Diode (LED): A semiconductor device that emits light when current passes through it, often used in encoders as a light source.
- Photodetector: An electronic device that converts light into an electrical signal, crucial for interpreting the encoder's feedback.
- Incremental Encoder: A type of encoder that provides a series of pulses as output; these pulses represent changes in position.
- Absolute Encoder: Provides a unique value for each position, allowing for direct retrieval of location information.
Related Concepts and Theories
Understanding reflective optical encoders requires insight into various related concepts:
- Feedback Systems: Mechanisms that use outputs to adjust inputs, vital for control applications.
- Pulse Width Modulation (PWM): A technique used in encoding signals by varying the width of the pulses.
Operational Mechanics
The operational mechanics of reflective optical encoders are based on light reflection, where a light source illuminates a surface and the reflected light is detected. This reflection can change based on the surface's texture, presence of marks, or positioning of components. The encoder translates these changes into data that a machine can interpret to make decisions.
"Reflective optical encoders are essential for precision in tasks ranging from basic motor control to complex automated systems"
Applications Across Industries
Reflective optical encoders find use in a wide range of applications. Here are a few notable examples:
- Robotics: Position and speed control in robotic arms or mobile robots.
- Manufacturing: Used in assembly line machinery for precise operation.
- Consumer Electronics: Employed in computer mice and printer mechanisms.
Future Directions
Understanding potential advancements is key for engineers and researchers interested in reflective optical encoders.
Gaps Identified in Current Research
Despite the wealth of applications, there are gaps in research such as:
- Limitations in sensitivity in varying environmental conditions.
- Challenges in miniaturizing components for compact devices without losing performance.
Suggestions for Further Studies
Research into improving material quality, integrating artificial intelligence for smarter processing, and enhancing interoperability with other sensor systems is necessary. One possible direction could be the exploration of new photodetector technologies that can significantly improve response times and accuracy.
Preface to Reflective Optical Encoders
Reflective optical encoders are essential for precision measurement and control in various fields, from industrial automation to consumer electronics. Their role in modern technology cannot be overstated. As sensors that provide critical positional feedback, these encoders drive advancements in device accuracy and efficiency. Understanding their mechanics and applications is vital for students, researchers, educators, and professionals aiming to innovate or implement technology in their projects.
Defining Reflective Optical Encoders
Reflective optical encoders operate by utilizing light to detect motion and position. They typically consist of a light source, usually an LED, and a photodetector. The encoder works by reflecting light off a surface, with variations in light detected by the photodetector. This detection mechanism translates into positional data that informs other electronic systems. Because of their ability to provide high precision in measurements and feedback, reflective optical encoders have become a cornerstone in robotics, automation, and numerous consumer devices.
Historical Development and Evolution
The concept of optical encoders has undergone significant evolution. Early forms of encoders relied on mechanical systems that were limited in accuracy and durability. With advancements in optics and electronics, reflective optical encoders emerged, offering improved accuracy and lower costs.
Initially, the technology was primarily used in industrial machines, but its applications expanded as electronic devices became more sophisticated. The integration of reflective optical encoders into various products marked a shift towards more reliable and versatile technologies. Over decades, continual improvements in materials, design, and processing techniques have enhanced their functionality, making them integral to modern advancements in areas such as automation and consumer electronics.
Thus, understanding both the definition and historical context of reflective optical encoders is crucial for grasping their significance in today's technology landscape.
Basic Principles of Operation
Reflective optical encoders serve as vital components in many electronic systems. Understanding the basic principles of their operation is crucial to comprehending how they function and what applications they are suitable for. These encoders convert angular or linear displacement into electrical signals, which can be further processed for various applications. The principles discussed below outline how these devices achieve their functionality, highlight significant benefits, and explore important design considerations.
Optical Components
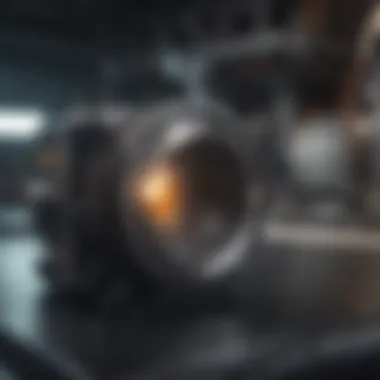
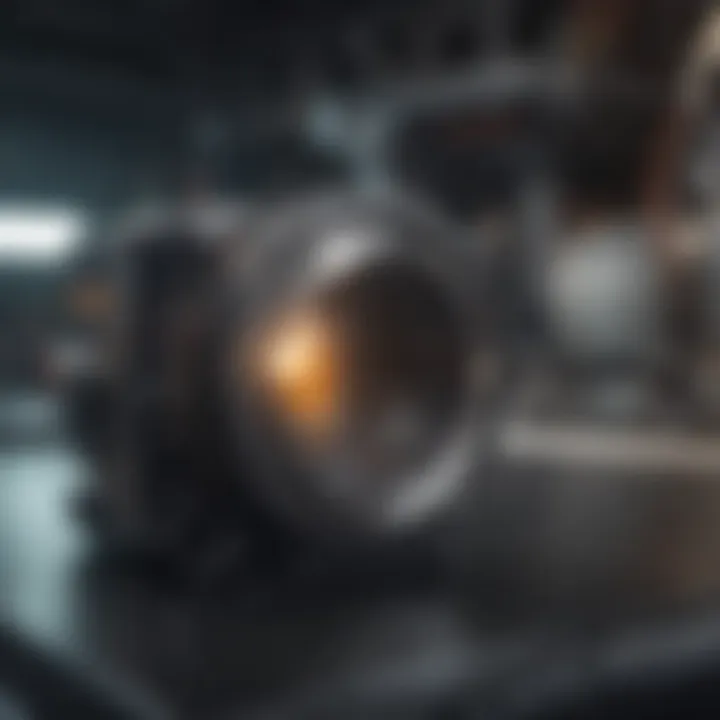
The heart of reflective optical encoders lies in their optical components. They typically consist of several key parts:
- Light Source: A light-emitting diode (LED) often serves as the source of light. It produces a beam that interacts with the reflective surfaces nearby.
- Reflective Surface: Marked surfaces, often a disk with alternating reflective and non-reflective segments, form the basis for measurement.
- Photodetector: This component detects the light reflected from the surface and converts it into electrical signals.
The light source and reflective surface's arrangement is crucial for accuracy. Variations in their design can influence the encoder's sensitivity and resolution. For instance, a more precise reflective pattern can enhance the encoder’s performance by allowing finer measurements over shorter distances.
Signal Processing Mechanism
The signal processing mechanism converts the detected light into usable information. When the light beam strikes the reflective surface, it bounces back toward the photodetector. The detector measures the intensity of the incoming light, yielding a digital signal representative of the rotation angle or linear position.
Each change in reflection caused by the movement of the encoded element results in a change in the photodetector’s response. This data is then processed through hardware or software algorithms to produce accurate position and movement measurements. The design of these algorithms is central to ensuring that the signal remains clear and free of noise. Thus, effective signal processing is essential for practical applications in industries requiring high precision.
Interpreting Encoder Outputs
Reflective optical encoders generate specific outputs that require correct interpretation for effective use. Generally, these outputs are represented in digital form, either as binary sequences or pulses, corresponding to the rotation or displacement.
To interpret these outputs:
- Count Pulses: Each pulse corresponds to a defined increment of movement. Knowing the pulse count allows for precise calculation of movement.
- Decoding Position: The encoder's output can be interpreted to reveal actual position, which can then be translated into a physical location or angle.
- Feedback Loops: In many systems, the output feeds back into controllers for real-time adjustments to performance, ensuring smooth operation.
Understanding these basics fosters a deeper appreciation of how reflective optical encoders operate. It highlights their role in a plethora of applications, from robotics to industrial automation, where precision and reliability in signal processing are paramount.
Understanding the basic principles underlying reflective optical encoders forms the foundation for leveraging their advantages in advanced applications across multiple industries.
Key Design Considerations
In the realm of reflective optical encoders, understanding key design considerations is imperative for ensuring optimal performance. These encoders are relied upon across various sectors due to their precision and efficiency. Therefore, focusing on aspects such as sensitivity, resolution, environmental factors, and mechanical integration plays a critical role in device efficacy.
Sensitivity and Resolution
Sensitivity in reflective optical encoders refers to the ability of the encoder to detect minute changes in position, which is critical for applications needing high precision. This is linked closely to resolution, defined as the smallest increment of movement that the encoder can reliably detect.
- For instance, in robotics, high resolution allows for smoother operation and improved control in tasks that demand precision, such as assembly or surgical procedures.
- The trade-off between sensitivity and environmental noise is another important aspect. Increased sensitivity can make encoders more susceptible to interference from external sources such as light, dust, or vibration.
Engineers must balance these factors during the design phase to produce encoders that maintain high performance levels without incurring excessive costs. The choice of materials and the configuration of optical components directly influence both sensitivity and resolution.
Environmental Factors
Reflective optical encoders are often deployed in challenging environments, such as factories, outdoor installations, and medical settings. Therefore, considering environmental factors is paramount.
- Temperature fluctuations can affect optical components, leading to performance degradation.
- Dust and moisture can obstruct optical pathways, resulting in signal loss and inaccurate readings.
- Vibration can cause physical instability, leading to erratic performance.
Designing encoders to resist these elements can enhance their reliability. Utilizing sealed enclosures, advanced filtering techniques, and selecting robust materials can mitigate these risks. Performing thorough environmental testing is essential prior to deployment to ensure long-term functionality.
Mechanical Integration
Mechanical integration involves ensuring that the encoder fits well within the broader system architecture of the device or platform in which it operates. This includes mounting arrangements, alignment with moving parts, and overall compatibility with surrounding technologies.
Achieving proper alignment is crucial. Misalignment can lead to inaccuracies, undermining the purpose of the encoder. Also, different application requirements may necessitate varying designs, such as size constraints or specific mounting configurations.
- Benefits of careful mechanical integration:
- Enhanced durability under physical stresses
- Improved accuracy due to correct alignment
- Streamlined assembly processes, reducing time and costs
When designing reflective optical encoders, comprehensive consideration of these designing elements ensures not only functionality but longevity in diverse applications. Building encoders with attention to sensitivity, environmental resilience, and mechanical fit ultimately leads to superior technology solutions that stand the test of time, serving demanding industries efficiently.
Applications Across Industries
Reflective optical encoders have found a diverse range of applications across various industries. Their ability to accurately measure position and movement makes them essential in numerous contexts. From manufacturing to consumer technology, these components play a critical role in enhancing functionality and precision. Understanding their applications offers insights into the benefits they bring and the considerations that need to be made for optimal use.
Industrial Automation
In industrial automation, reflective optical encoders are integral for control systems. They provide real-time feedback for automated machinery, ensuring precise positioning and movement tracking. This high level of accuracy is crucial in tasks such as robotic welding, assembly line product positioning, and conveyor belt management.
The regular feedback from these encoders allows for adjustments in speed and direction, which enhances efficiency and lowers operational errors. Their durability in harsh environments with vibrations and dust further solidifies their position in this field. The investment in optical encoders often leads to significant savings through reduced downtime and increased productivity.
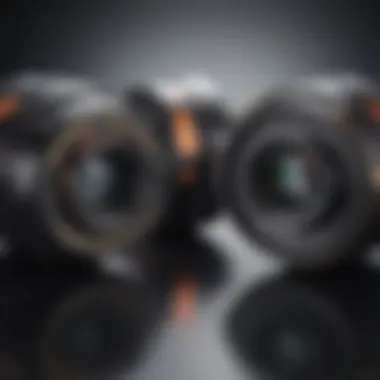
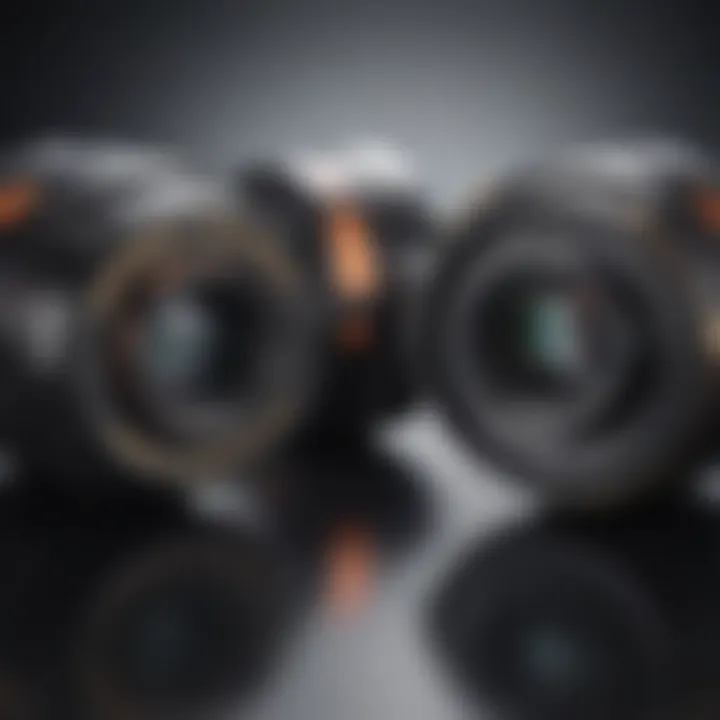
Consumer Electronics
Reflective optical encoders are commonly employed in consumer electronics. Devices such as printers, cameras, and gaming accessories utilize these encoders to improve user experience. In printers, the encoders track the position of the print head, ensuring accuracy in image reproduction. In gaming peripherals, they provide precise control for movements and actions, giving users a competitive edge.
The increasing demand for compact and high-speed electronic devices further drives the innovation in encoder technology. Manufacturers continuously explore new designs that balance size and performance to meet consumer expectations. As a result, reflective optical encoders are pivotal in advancing product capabilities in the consumer market.
Medical Devices
In the medical field, reflective optical encoders contribute to precision in device operation. Surgical robots and imaging equipment rely on accurate motion control to function effectively. For instance, an encoder ensures that a robotic arm moves with exactitude during a surgical procedure, minimizing the risk of human error.
Moreover, patient monitoring devices use these encoders to track position and data, helping in diagnostics and treatment planning. The reliability of reflective optical encoders plays a vital role in improving overall healthcare outcomes, ensuring that devices perform as intended in high-stakes situations.
Robotics
Reflective optical encoders are also essential in the field of robotics. They enable autonomous robots to navigate environments effectively by providing the necessary feedback for movement. In applications ranging from warehouse automation to domestic robotics, these encoders facilitate accurate positioning and speed regulation.
The advent of advanced robotics, where machine learning and artificial intelligence are integrated, has heightened the demand for better sensor capabilities. Reflective optical encoders support these innovations by delivering crucial navigation data. As robots evolve, the need for precise and reliable encoders continues to grow, reinforcing their vital role in future robotic designs.
Advantages of Reflective Optical Encoders
Reflective optical encoders stand out due to their distinct benefits, making them crucial for numerous applications in today's tech-driven landscape. The advantages discussed here highlight how they contribute to improved performance, efficiency, and reliability across various sectors. Understanding these benefits can aid in the selection of the right encoder for specific tasks.
High Accuracy
One of the most notable advantages of reflective optical encoders is their high accuracy. These devices can measure angular position with precision, typically reaching resolutions of thousands or even millions of pulses per revolution. This capability stems from their use of light as a sensing medium. The binary output produced by these encoders enables precise tracking of movements, making them ideal for applications that require exact positioning, such as robotics and automation systems.
The accuracy of a reflective optical encoder depends on both the quality of its components and the design of the optical system. Higher-quality lenses and reflective surfaces can enhance signal clarity, reducing errors in position detection. Moreover, a well-implemented signal processing mechanism ensures that noise is minimized, boosting performance in high-speed applications.
"Precision in measurements equates to efficiency in operation and reduced error margins in systems design."
Compact Size
Reflective optical encoders are also known for their compact form factor. Their small size allows for easy integration into various systems where space is a constraint. This quality is especially beneficial in fields like consumer electronics and embedded systems, where traditional encoders might not fit. Moreover, their compact nature does not compromise on performance; they maintain high accuracy and reliability despite being reduced in size.
The miniaturization of components continues to advance, pushing the boundaries of how small optical encoders can become. This translates to lighter, more portable systems without sacrificing functionality. In competitive markets, the ability to create sleek devices that perform at high levels provides a significant advantage.
Durability Under Varied Conditions
Reflective optical encoders excel in durability, making them suitable for diverse environments. Many models are built to withstand harsh conditions, including temperature fluctuations, moisture, and dust. This robustness is vital for industries like manufacturing, where equipment may face extreme exposure.
The construction of these encoders often includes protective casings and coatings that enhance their lifespan. Additionally, their optical sensing method is less susceptible to wear compared to mechanical encoders, which rely on physical contact. This characteristic reduces maintenance costs and increases overall system reliability.
In summary, the advantages of reflective optical encoders lie in their high accuracy, compact size, and remarkable durability. These qualities not only make them essential components in modern electronic systems but also highlight their significant role in shaping innovations in technology.
Limitations and Challenges
In understanding reflective optical encoders, it is essential to explore the limitations and challenges they present. While these devices are widely utilized for their accuracy and compact design, they are not without drawbacks. Professionals in the field must consider these elements seriously, particularly when selecting encoders for specific applications. Understanding their limitations helps in making informed decisions to enhance efficiency and reliability in various systems.
Environmental Sensitivity
Reflective optical encoders are susceptible to their operating environments. Factors such as temperature fluctuations, humidity, and dust can significantly impact their performance. For instance, high temperatures may affect the adhesive used in the optical components, leading to misalignment. Similarly, excessive moisture can introduce condensation, interfering with the signal processing mechanisms.
It is critical for engineers and technicians to evaluate the specific environmental conditions before choosing reflective optical encoders. Selecting models with housing that provides adequate protection against dust and moisture can mitigate such challenges. Furthermore, special attention should be given to the temperature ratings and operational tolerances of these devices.
"Environmental factors can either enhance or inhibit the functionality of reflective optical encoders. Proper understanding of these factors is vital for optimal device selection."
Cost-Effectiveness
Cost-effectiveness is another challenge faced when utilizing reflective optical encoders. While the initial investment may be low, the total cost of ownership includes factors such as maintenance, replacement, and the impact on overall system efficiency. Poor sensitivity or increased error rates can lead to additional expenses, outweighing the benefits initially perceived.
When considering cost, it is not just about the purchase price. Design teams must assess long-term performance and reliability. A more expensive encoder that offers greater precision and durability may yield better returns over time compared to cheaper alternatives that require frequent replacements.
To ensure cost-effectiveness, it is advisable to conduct thorough risk assessments and cost analyses during the selection process. Establishing a clear understanding of the total operational costs associated with an encoder can help organizations make informed decisions that align with budgeting goals and operational needs.
Recent Innovations in Reflective Optical Encoding Technology
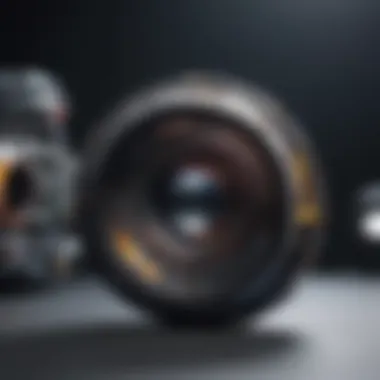
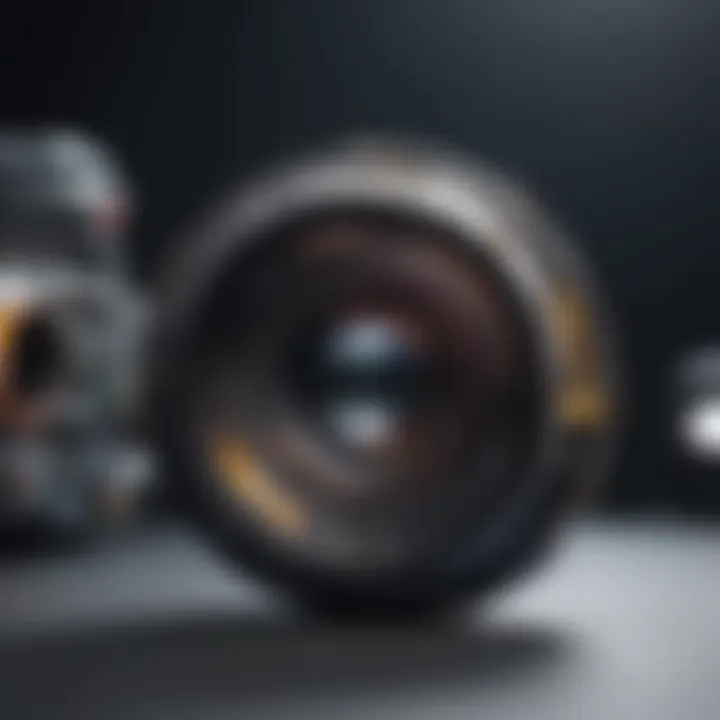
Innovations in reflective optical encoding technology not only enhance the capabilities of these devices but also expand their range of applications. The importance of advancements in this field cannot be overstated. As electronic systems become more complex and demanding, improvements in encoder technology are essential to ensure accurate feedback for motion and position control. Key elements pertaining to recent innovations include miniaturization and integration with digital systems. These trends contribute to improved performance, efficiency, and flexibility in various industrial and consumer applications.
Miniaturization Trends
Miniaturization is a significant trend affecting reflective optical encoders. With the push for smaller and lighter electronic devices, the need for compact encoder designs has increased. Achieving miniaturization involves advancements in optical components and materials. Manufacturers are now utilizing microscale optics and advanced fabrication techniques to create encoders that occupy less space.
The benefits of miniaturization include:
- Space-saving designs that allow integration in devices with strict size constraints.
- Increased efficiency, since smaller components often result in lighter systems, reducing the overall weight of the device.
- Cost-effectiveness due to reduced material usage during production.
"Miniaturization in optical encoders can lead to revolutionary changes in both design and functional efficiency, reshaping the landscape of electronic engineering."
This shift towards smaller encoders also necessitates careful consideration of heat dissipation and mechanical integrity. As encoders become more compact, ensuring reliable performance in varied environmental conditions remains a critical focus.
Integration with Digital Systems
The integration of reflective optical encoders with digital systems marks another pivotal advancement in their technology. As industries evolve, the need for seamless interaction between hardware and software becomes paramount. Reflective optical encoders are now being designed to interface directly with digital electronics, enhancing their functionality and ease of use.
Benefits of this integration include:
- Improved data processing, as digital systems can analyze encoder outputs more efficiently.
- Easier implementation in various applications, due to standardized digital protocols.
- Increased flexibility, enabling fast adaptation to new tasks or requirements in control systems.
Moreover, the shift towards digital systems facilitates the incorporation of advanced algorithms for data interpretation, increasing the accuracy and reliability of the output signals. Thus, reflective optical encoders are not just passive devices but active contributors to the functionality of modern digital systems.
In summary, innovations such as miniaturization and digital integration are driving the evolution of reflective optical encoders, enhancing their performance and broadening their application scope.
Future Prospects and Trends
The exploration of future prospects and trends in reflective optical encoders is fundamental not only for practitioners but also for those invested in technological advancements. This section aims to uncover how these devices will evolve in response to emerging demands in various sectors, particularly in industrial automation and smart technologies. Understanding these trends is essential for anticipating challenges and opportunities in design and application.
Advanced Robotics Applications
Reflective optical encoders are becoming increasingly crucial in the field of robotics. With advancements in robotic technologies, there is a growing requirement for precise positioning and navigation capabilities. For instance, industrial robots used in manufacturing rely on optical encoders to provide feedback on their position, allowing for accurate and repeatable movements. As robots are integrated into the workforce, the need for higher resolution and sensitivity in encoders will become more pronounced.
Research indicates that advances in encoding technology can result in smaller form factors while maintaining or enhancing performance. This miniaturization is key for the deployment of encoders in mobile robots, where space and weight constraints are critical. Furthermore, the use of reflective optical encoders in autonomous vehicles is on the rise. They play a vital role in providing real-time data for navigation systems, promoting spatial awareness in complex environments.
- Enhanced accuracy in robotic applications is facilitated by:
- Miniaturization of components.
- Robust signal processing mechanisms.
- Improved sensitivity to environmental changes.
Role in Smart Technologies
Reflective optical encoders will play a significant role in the development of smart technologies. The trend towards integrating these technologies into everyday objects signifies a shift in how we understand the concept of "smart." For example, in smart home devices, encoders can provide feedback for automated curtains or blinds, allowing users to control sunlight or privacy settings dynamically.
Moreover, the Internet of Things (IoT) ecosystem benefits from the reliability of reflective optical encoders. These devices enable a seamless connection between physical actions and digital responses. As systems become more interconnected, the need for precision in data capture will grow. In addition, the synchronization of devices will rely heavily on effective encoding technology to coordinate actions visibly.
"The integration of reflective optical encoders in smart systems enhances interoperability and functionality, making everyday tasks more efficient."
As smart technologies advance, the focus will include:
- Increased reliability in data transmission.
- Greater integration with cloud-based platforms.
- Continuous improvements in energy efficiency.
Epilogue
Reflective optical encoders play an essential role in contemporary technology. Their ability to precisely measure motion has made them indispensable in numerous fields. The advancements in this technology highlight its importance, not only in current applications but also in future developments.
Summarizing Key Insights
In reviewing reflective optical encoders, several pivotal insights emerge:
- Core Functionality: Reflective optical encoders utilize light to detect position and movement, making them incredibly effective for various applications.
- Diverse Use: They are integrated into systems across industrial automation, consumer electronics, medical devices, and robotics.
- Design Considerations: Sensitivity, resolution, and environmental factors are crucial in encoder design, directly affecting performance and reliability.
- Technological Advances: Trends such as miniaturization and integration with digital systems showcase how the technology is evolving to meet new challenges.
Reflective optical encoders combine precision with reliability, which is why they remain vital components in modern engineering and electronic design.
Final Thoughts on Future Directions
The future for reflective optical encoders appears bright. Key areas for advancement include:
- Integration with Smart Technologies: The rise of smart systems necessitates more sophisticated sensing capabilities. Reflective optical encoders will be critical in enhancing automation and intelligent systems.
- Advanced Robotics Applications: As robotics continues to evolve, the demand for high-accuracy positioning will increase. Future designs must accommodate these needs in areas such as autonomous vehicles and robotic surgery.
- Sustainability Considerations: Innovations will likely focus on reducing energy consumption and increasing durability to operate efficiently in harsh environments.
By embracing emerging trends and addressing limitations, reflective optical encoders have the potential to redefine their role across multiple sectors.
In closing, the reflective optical encoder's capacity to adapt and improve positions it as a cornerstone in future technological advancements.